BMA208_10_tutorial_5
3500系列_中文手册
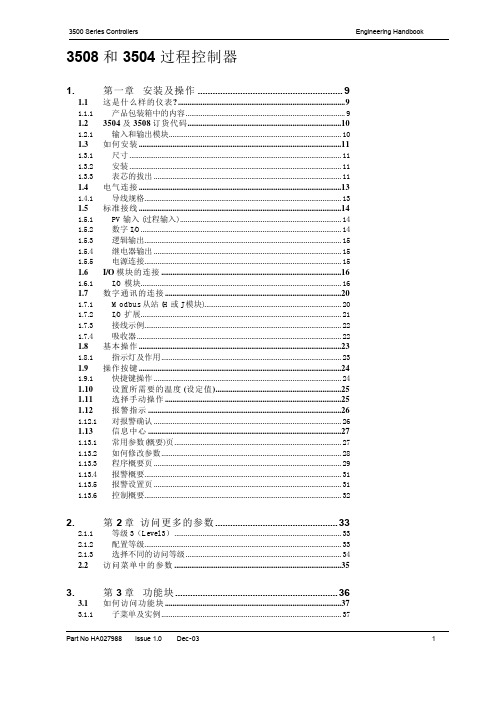
1.13.3 程序概要页 .................................................................................................... 29
1.13.4 报警概要......................................................................................................... 31
2.
2.1.1 2.1.2 2.1.3 2.2
第 2 章 访问更多的参数 .................................................33
等级 3(Level 3)......................................................................................... 33 配置等级......................................................................................................... 33 选择不同的访问等级................................................................................... 34 访问菜单中的参数 .........................................................................................35
1.1 这是什么样的仪表? .........................................................................................9
M218基础培训试验教材

M218 基础培训示例教材
M218 高速计数器示例
内容简介: 本文介绍如何通过M218的高速计数器功能实现冷弯成型机的定长裁剪控制。 1. 冷弯成型机控制系统描述: 冷弯成型机最基本的控制要求是将滚压成型完成的材料送到指定位置,然后进行压膜或 者裁切动作。 材料的输送电机由变频器控制。 在靠近压膜或者裁剪机构的滚轮上安装有用于 计长的旋转编码器,PLC实时检测该编码器的脉冲信号并换算成长度数值。当机器启动时, PLC将实际检测的长度数值与设定数值进行比较,控制变频器进行多段速定位。即当长度到 达阀值0时,变频器切换到低速;当长度到达阀值1时变频器输出0速。
Modicon M218 培训试验教材
植根中国 化繁为简的 SoMachine 平台
施耐德电气(中国)有限公司 LECA 市场部
M218 培训试验教程
目录
M218 基础培训示例教材 ................................................................................................................ 3 M218 高速计数器示例 ............................................................................................................ 3 PTO 使用示例 ......................................................................................................................... 17 PWM 示例 ............................................................................................................................... 47 串口 Modbus 通讯示例 ......................................................................................................... 52 自由协议通讯 ......................................................................................................................... 62 以太网通讯示例 ..................................................................................................................... 69 PID 示例 .................................................................................................................................. 77 RTC 实现示例 ......................................................................................................................... 84 M218 基础培训试验教材 ............................................................................................................ 103 试验一-SoMachine 软件入门 ............................................................................................ 103 试验二-开关量和模拟量试验 ........................................................................................... 113 试验三-PTO 试验 ............................................................................................................... 118 试验四-串口通信试验 ....................................................................................................... 128 试验五-以太网通信试验 ................................................................................................... 134
Moxa EDS-208系列产品说明书

P/N: 1802002080016*1802002080016*EDS-208 Series Quick Installation GuideMoxa EtherDevice SwitchVersion 5.2, January 2021Technical Support Contact Information/support2021 Moxa Inc. All rights reserved.OverviewThe EDS-208 series of Moxa EtherDevice™ Switches are entry-level8-port Ethernet Switches that provide a cost-effective solution for industrial Ethernet connections. EDS-208 provides a choice of 12 to 48 VDC power input. The switches can operate reliably in a temperature range of -10 to 60°C, and the rugged hardware design makes EDS-208 perfect for ensuring that your Ethernet equipment can be used in demanding industrial environments.Package ChecklistMoxa EDS-208 is shipped with the following items. If any of these items is missing or damaged, please contact your customer service representative for assistance.• 1 EDS-208 or EDS-208-M-SC or EDS-208-M-ST•Quick installation guide (printed)•Warranty cardFeaturesHigh Performance Network Switching Technology•10/100BaseT(X) (RJ45), 100BaseFX (SC/ST type, Multi-mode) •IEEE 802.3/802.3u/802.3x•Store and Forward switching process type, 1024 address entries Industrial Design•Operating temperature ranges from -10 to 60°C•Power inputs: 12 to 48 VDC•IP30, plastic case•DIN-Rail mounting abilityPanel Layout of EDS-2081.Heat dissipation orifices2.Terminal block for power inputand grounding3.Moxa Logo4.Power input LED5.10/100BaseT(X) Port6.TP port’s 100 Mbps LED7.TP port’s 10 Mbps LED8.DIN-Rail kitPanel Layout of EDS-208-M-SC/ST1.Heat dissipation orifices2.Terminal block for power inputand grounding3.Moxa Logo4.Power input LED5.10/100BaseT(X) Port6.TP port’s 100 Mbps LED7.TP port’s 10 Mbps LED8.FX port’s 100 Mbps LED9.100BaseFX Port10.DIN-Rail kitMounting Dimensions (unit = mm)DIN-Rail MountingThe plastic DIN-Rail attachment plate should already be fixed to the rear panel of EDS-208 when you take it out of the box. If you need to reattach the DIN-Rail attachment plate to EDS-208, make sure the DIN-Rail kit is situated towards the top, as shown in the figures below.STEP 1: Insert the top of the DIN-Rail into the slot. STEP 2:The DIN-Rail attachment unit will snap into place as shown below.To remove Moxa EDS-208 from theDIN-Rail, insert a flat-blade screwdriver horizontally into the DIN-Railkit under the EDS-208, and thenpull it upwards and releaseEDS-208 towards you away fromthe DIN-Rail.You may also take the following steps to remove the EDS-208 from the DIN-Rail.STEP 1: Press the middle of the flat side of the mounting kit as indicated. Pull the EDS-208 downwards.STEP 2:Release it towards you and away from the DIN-Rail.Wiring RequirementsYou should also pay attention to the following items:• Use separate paths to route wiring for power and devices. If powerwiring and device wiring paths must cross, make sure the wires are perpendicular at the intersection point.NOTE: Do not run signal or communications wiring and power wiring in the same wire conduit. To avoid interference, wires with different signal characteristics should be routed separately.• You can use the type of signal transmitted through a wire todetermine which wires should be kept separate. The rule of thumb is that wiring that shares similar electrical characteristics can bebundled together.• Keep input wiring and output wiring separated.•It is strongly advised that you label wiring to all devices in the system when necessary.Grounding EDS-208Grounding and wire routing help limit the effects ofnoise due to electromagnetic interference (EMI).Run the ground connection from the right mostcontact of the 3-contact terminal block to thegrounding surface prior to connecting devices.Wiring the Power InputsThe two left-most contacts of the 3-contact terminal block connector on EDS-208’s top panel are used for the DC input. Top and front views of one of the terminal block connectors are shown here.STEP 1: Insert the negative/positive DC wires intothe V-/V+ terminals.STEP 2: To keep the DC wires from pulling loose,use a small flat-blade screwdriver to tighten thewire-clamp screws on the front of the terminalblock connector.STEP 3: Insert the plastic terminal block connectorprongs into the terminal block receptor, which islocated on EDS’s top panel.Communication ConnectionsEDS-208 has 7 or 8 10/100BaseT(X) Ethernet ports, and 1 or 0 (zero) 100BaseFX (SC/ST-type connector) multi-mode fiber ports.10/100BaseT(X) Ethernet Port ConnectionThe 10/100BaseT(X) ports located on EDS-208’s front panel are used to connect to Ethernet-enabled devices.Below we show pinouts for both MDI (NIC-type) ports and MDI-X (HUB/Switch-type) ports, and also show cable wiring diagrams for straight-through and cross-over Ethernet cables.MDI Port PinoutsMDI-X Port Pinouts 8-pin RJ45 PinSignal 1Tx+ 2Tx- 3Rx+ 6 Rx- PinSignal 1Rx+ 2 Rx- 3 Tx+ 6 Tx-RJ45 (8-pin) to RJ45 (8-pin) Straight-Through Cable WiringRJ45 (8-pin) to RJ45 (8-pin) Cross-Over Cable Wiring100BaseFX Ethernet Port ConnectionThe concept behind the SC/ST port and cable is quite straightforward. Suppose you are connecting devices I and II. Contrary to electrical signals, optical signals do not require a circuit in order to transmit data.Consequently, one of the optical lines is used to transmit data from device I to device II, and the other optical line is used to transmit data from device II to device I, for full-duplex transmission.All you need to remember is to connect the Tx (transmit) port of device I to the Rx (receive) port of device II, and the Rx (receive) port of device I to the Tx (transmit) port of device II. If you make your own cable, we suggest labeling the two sides of the same line with the same letter (A-to-A and B-to-B, as shown below, or A1-to-A2 and B1-to-B2). SC-Port Pinouts SC-Port to SC-Port Cable WiringST-Port Pinouts ST-Port to ST-Port Cable WiringLED IndicatorsThe front panel of EDS-208 contains several LED indicators. The function of each LED is described in the table below.LED Color State DescriptionP AMBER OnPower is being supplied to the powerinputOffPower is not being supplied to thepower input10(TP) GREENOn TP port’s 10 Mbps link is active Blinking Data is being transmitted at 10 Mbps Off TP Port’s 10 Mbps link is inactive100(TP) GREENOn TP port’s 100 Mbps link is active BlinkingData is being transmitted at 100MbpsOff 100BaseTX Port’s link is inactive100M(FX) GREENOn FX port’s 100 Mbps link is active BlinkingData is being transmitted at 100MbpsOff 100BaseFX Port’s link is inactiveAuto MDI/MDI-X ConnectionThe Auto MDI/MDI-X function allows users to connect EDS-208’s10/100BaseTX ports to any kind of Ethernet device, regardless of how the Ethernet cable is wired. This means that you can use either astraight-through cable or cross-over cable to connect EDS-208 to Ethernet devices.Dual Speed Functionality and SwitchingEDS208’s 10/100 Mbps switched RJ45 port auto negotiates with the connected device for the fastest data transmission rate supported by both devices. All models of EDS-208 are plug-and-play devices, so that software configuration is not required at installation, or during maintenance. The half/full duplex mode for the switched RJ45 ports is user dependent and changes (by auto-negotiation) to full or half duplex, depending on which transmission speed is supported by the attached device.Switching, Filtering, and ForwardingEach time a packet arrives at one of the switched ports, a decision is made either to filter or to forward the packet. Packets with source and destination addresses belonging to the same port segment will be filtered, constraining those packets to one port, and relieving the rest of the network from the need to process them. A packet with destination address on another port segment will be forwarded to the appropriate port, and will not be sent to the other ports where it is not needed. Packets that are used in maintaining the operation of the network (such as the occasional multi-cast packet) are forwarded to all ports.EDS-208 operates in the store-and-forward switching mode, which eliminates bad packets and enables peak performance to be achieved when there is heavy traffic on the network.Switching and Address LearningEDS-208 has an address table that can hold up to 1,000 node addresses, which makes it suitable for use with large networks. The address tables are self-learning, so that as nodes are added or removed, or moved from one segment to another, EDS-208 automatically keeps up with new node locations. An address-aging algorithm causes the least-used addresses to be deleted in favor of newer, more frequently used addresses. To reset the address buffer, power down the unit and then power it back up. Auto-Negotiation and Speed SensingAll of EDS-208’s RJ45 Ethernet ports independently supportauto-negotiation for speeds in the 10BaseT and 100BaseTX modes, with operation according to the IEEE 802.3u standard. This means that some nodes could be operating at 10 Mbps, while at the same time, other nodes are operating at 100 Mbps.Auto-negotiation takes place when a “live” RJ45 cable is connected to the switch, and then each time a LINK is enabled. EDS-208 advertises its capability for using either 10 Mbps or 100 Mbps transmission speeds, with the device at the other end of the cable expected to similarly advertise. Depending on what type of device is connected, this will result in agreement to operate at a speed of either 10 Mbps or 100 Mbps.If an EDS-208 RJ45 Ethernet port is connected to a non-negotiating device, it will default to 10 Mbps speed and half-duplex mode, as required by the IEEE 802.3u standard.SpecificationsTechnologyStandards IEEE802.3, 802.3u, 802.3xProcessing Type Store and Forward, with IEEE802.3x fullduplex, non-blocking flow controlAddress Table Size 1,000 uni-cast addressesInterfaceRJ45 Ports 10/100BaseT(X) auto negotiation speed, F/Hduplex mode, and auto MDI/MDI-X connection Fiber Ports 100BaseFX ports (SC/ST connector)LED Indicators Power, 10/100 M (TP port), 100 M (FX port) PowerInput Voltage 12 to 48 VDCInput Current @ 24 VDC 0.07 A (EDS-208)0.1 A (EDS-208-M-SC/EDS-208-M-ST) Connection Removable 3-contact Terminal Block Overload CurrentPresentProtectionPresentReverse PolarityProtectionMechanicalCasing IP30 protection, plastic caseDimensions 40 x 109 x 95 mm (W x H x D)Weight 170 gInstallation DIN-RailEnvironmentOperating Temperature -10 to 60°C (14 to 140°F) Storage Temperature -40 to 70°C (-40 to 158°F)5 to 95% (non-condensing) Ambient RelativeHumidityRegulatory ApprovalsSafety UL 508EMI FCC Part 15, CISPR 32 class A EMS EN61000-4-2 (ESD),EN61000-4-3 (RS),EN61000-4-4 (EFT),EN61000-4-5 (Surge),EN61000-4-6 (CS)Shock IEC 60068-2-27Free Fall IEC 60068-2-32Vibration IEC 60068-2-6 WARRANTY 5 years。
MPLAB Code Configurator v2.25 1 产品说明书
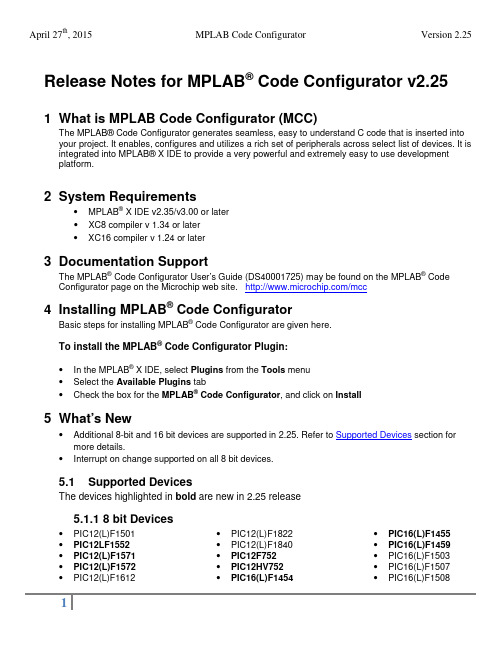
Release Notes for MPLAB® Code Configurator v2.251 What is MPLAB Code Configurator (MCC)The MPLAB®Code Configurator generates seamless, easy to understand C code that is inserted into your project. It enables, configures and utilizes a rich set of peripherals across select list of devices. It is integrated into MPLAB®X IDE to provide a very powerful and extremely easy to use development platform.2 System Requirements•MPLAB® X IDE v2.35/v3.00 or later•XC8 compiler v 1.34 or later•XC16 compiler v 1.24 or later3 Documentation SupportThe MPLAB® Code Configurator User’s Guide (DS40001725) may be found on the MPLAB® Code Configurator page on the Microchip web site. /mcc4 Installing MPLAB® Code ConfiguratorBasic steps for installing MPLAB® Code Configurator are given here.To install the MPLAB® Code Configurator Plugin:•In the MPLAB® X IDE, select Plugins from the Tools menu•Select the Available Plugins tab•Check the box for the MPLAB® Code Configurator, and click on Install5 What’s New•Additional 8-bit and 16 bit devices are supported in 2.25. Refer to Supported Devices section for more details.•Interrupt on change supported on all 8 bit devices.5.1 Supported DevicesThe devices highlighted in bold are new in 2.25 release5.1.1 8 bit Devices•PIC12(L)F1501 •PIC12LF1552 •PIC12(L)F1571 •PIC12(L)F1572 •PIC12(L)F1612 •PIC12(L)F1822•PIC12(L)F1840•PIC12F752•PIC12HV752•PIC16(L)F1454•PIC16(L)F1455•PIC16(L)F1459•PIC16(L)F1503•PIC16(L)F1507•PIC16(L)F1508•PIC16(L)F1509 •PIC16(L)F1512 •PIC16(L)F1513 •PIC16(L)F1516 •PIC16(L)F1517 •PIC16(L)F1518 •PIC16(L)F1519 •PIC16(L)F1526 •PIC16(L)F1527 •PIC16(L)F1574 •PIC16(L)F1575 •PIC16(L)F1578 •PIC16(L)F1579 •PIC16(L)F1613 •PIC16(L)F1614 •PIC16(L)F1615 •PIC16(L)F1618 •PIC16(L)F1619 •PIC16(L)F1703 •PIC16(L)F1704 •PIC16(L)F1705 •PIC16(L)F1707 •PIC16(L)F1708 •PIC16(L)F1709 •PIC16(L)F1713 •PIC16(L)F1716 •PIC16(L)F1717 •PIC16(L)F1718 •PIC16(L)F1719 •PIC16(L)F1764•PIC16(L)F1765•PIC16(L)F1768•PIC16(L)F1769•PIC16(L)F1782•PIC16(L)F1783•PIC16(L)F1784•PIC16(L)F1786•PIC16(L)F1787•PIC16(L)F1788•PIC16(L)F1789•PIC16(L)F1823•PIC16(L)F1824•PIC16(L)F1825•PIC16(L)F1826•PIC16(L)F1827•PIC16(L)F1828•PIC16(L)F1829•PIC16(L)F1847•PIC16(L)F1933•PIC16(L)F1934•PIC16(L)F1936•PIC16(L)F1937•PIC16(L)F1938•PIC16(L)F1939•PIC16(L)F1946•PIC16(L)F1947•PIC16F753•PIC16HV753•PIC16LF1554•PIC16LF1559•PIC18(L)F13K22•PIC18(L)F14K22•PIC18(L)F23K22•PIC18(L)F24K22•PIC18(L)F24K50•PIC18(L)F25K22•PIC18(L)F25K50•PIC18(L)F26K22•PIC18(L)F23K20•PIC18(L)F43K22•PIC18(L)F44K22•PIC18(L)F45K22•PIC18(L)F45K50•PIC18(L)F46K22•PIC18(L)F23K20•PIC18(L)F23K20•PIC18(L)F24K20•PIC18(L)F25K20•PIC18(L)F26K20•PIC18(L)F23K20•PIC18(L)F43K20•PIC18(L)F44K20•PIC18(L)F45K20•PIC18(L)F46K20April 27th, 2015 MPLAB Code Configurator Version 2.255.1.2 16 bit Devices•PIC24F08KA101 •PIC24FJ128GB202 •PIC24FJ64GA006•PIC24F08KA102 •PIC24FJ128GB204 •PIC24FJ64GA008•PIC24F(V)08KM101 •PIC24FJ128GB206 •PIC24FJ64GA010•PIC24F(V)08KM102 •PIC24FJ128GB210 •PIC24FJ64GA102•PIC24F(V)08KM202 •PIC24FJ128GC006 •PIC24FJ64GA104•PIC24F(V)08KM204 •PIC24FJ128GC010 •PIC24FJ64GA106•PIC24F(V)16KM102 •PIC24FJ16GA002 •PIC24FJ64GA108•PIC24F(V)16KM104 •PIC24FJ16GA004 •PIC24FJ64GA110•PIC24F(V)16KM202 •PIC24FJ192GA106 •PIC24FJ64GA202•PIC24F(V)16KM204 •PIC24FJ192GA108 •PIC24FJ64GA204•PIC24F16KA101 •PIC24FJ192GA110 •PIC24FJ64GA306•PIC24F16KA102 •PIC24FJ192GB106 •PIC24FJ64GA308•PIC24F(V)16KA301 •PIC24FJ192GB108 •PIC24FJ64GA310•PIC24F(V)16KA302 •PIC24FJ192GB110 •PIC24FJ64GB002•PIC24F(V)16KA304 •PIC24FJ256DA106 •PIC24FJ64GB004•PIC24F(V)32KA301 •PIC24FJ256DA110 •PIC24FJ64GB106•PIC24F(V)32KA302 •PIC24FJ256DA206 •PIC24FJ64GB108•PIC24F(V)32KA304 •PIC24FJ256DA210 •PIC24FJ64GB110•PIC24FJ128DA106 •PIC24FJ256GA106 •PIC24FJ64GB202•PIC24FJ128DA110 •PIC24FJ256GA108 •PIC24FJ64GB204•PIC24FJ128DA206 •PIC24FJ256GA110 •PIC24FJ64GC006•PIC24FJ128DA210 •PIC24FJ256GB106 •PIC24FJ64GC010•PIC24FJ128GA006 •PIC24FJ256GB108 •PIC24FJ96GA006•PIC24FJ128GA008 •PIC24FJ256GB110 •PIC24FJ96GA008•PIC24FJ128GA010 •PIC24FJ256GB206 •PIC24FJ96GA010•PIC24FJ128GA106 •PIC24FJ256GB210•PIC24FJ128GA108 •PIC24FJ32GA002•PIC24FJ128GA110 •PIC24FJ32GA004•PIC24FJ128GA202 •PIC24FJ32GA102•PIC24FJ128GA204 •PIC24FJ32GA104•PIC24FJ128GA306 •PIC24FJ32GB002•PIC24FJ128GA308 •PIC24FJ32GB004•PIC24FJ128GA310 •PIC24FJ48GA002•PIC24FJ128GB106 •PIC24FJ48GA004•PIC24FJ128GB108 •PIC24FJ64GA002•PIC24FJ128GB110 •PIC24FJ64GA0046 Repairs and Enhancements# ID Description Device(s)1. MCC-1456 Pin Names with special characters give warnings ingenerated code All devices2. MCC-1457 System Module EC Value does not reload All 16 bit devices3. MCC-1458 When ADC enabled and uses VREF+ and VREF- pinsmcc generates a source code where TRISA0 and TRISA1bits are cleared so it overwrites the connected referencevoltagePIC24FJ128GA204 andPIC24FJ128GB204 family4. MCC-1459 Pin 44 is not available as a PPS pin for SPI1 PIC24FJ128GC006April 27th, 2015 MPLAB Code Configurator Version 2.25 # ID Description Device(s)5. MCC-1460 Primary Oscillator range is incorrect PIC24FJ128GA204 and PIC24FJ128GB204 family6. MCC-1461 At SPI1 module SPI1_ExchangeBuffer() function uses theenhanced buffer mode of SPI but SPI1CON1L.ENHBUFbit is cleared.PIC24FJ128GA204 andPIC24FJ128GB204 family7. MCC-1284 Interrupt on change (IOC) not available All 8 bit devices8. MCC-910 Timer 0 – Incorrect Variables declared K20\K22 devices9. MCC-1290 Seed Value not getting loaded in the initializer function PIC16F161910. MCC-1470 RTCC module is missing PIC24FJ64GB004 family 7 Known IssuesThe following are enumerated issues for the MPLAB® Code Configurator.# ID Description Device(s)1. MCC-1419 Does not support both commas and periods entered in atextbox as decimal separator. Currently MCC accepts inputsonly with a period as decimal separator.All devices2. MCC-1190 Configuration setting ZCD compatible with XC8 v1.33 only PIC16(L)F161x devices3. MCC-1250MCC-1253 I2C driver errors when multiple initializer are used All 8 bit devices4. MCC-1259 Timer 2/4/6 input pins not configured as digital PIC16(L)F161x devices5. MCC-1295 I2C slave driver does not fit in RAM PIC12(L)F18226. MCC-1466 I2C PPS register value incorrect for RC3 PIC16(L)F161x devices7. MCC-1321 PPS register configuration is wrong. PIC16F17078. MCC-1102 CN\IOC functionality not supported All 16 bit devices9. MCC-1462 MCCP Compare Alert does not go away on selecting outputpin(s) All PIC24F KM devices 10. MCC-1455 Cannot set PWM2 on RA5 through APFCON PIC16(L)F1454/911. MCC-1434 Changing oscillator selection from INTOSC oscillator toexternal clock in Config1 bits does not show up 'ExternalClock' text box (in 'Clock' label) to input external clockfrequency values.PIC12LF1552,PIC16(L)F176xPIC16(L)F157x,PIC16(L)F161xApril 27th, 2015 MPLAB Code Configurator Version 2.25 8 Customer Support8.1 The Microchip Web SiteMicrochip provides online support via our web site at . This web site is used as a means to make files and information easily available to customers. Accessible by using yourfavorite Internet browser, the web site contains the following information:•Product Support – Data sheets and errata, application notes and sample programs, design resources, user’s guides and hardware support documents, latest software releases and archivedsoftware• General Technical Support – Frequently Asked Questions (FAQs), technical support requests, online discussion groups/forums (), Microchip consultant programmember listing• Business of Microchip – Product selector and ordering guides, latest Microchip press releases, listing of seminars and events, listings of Microchip sales offices, distributors and factoryrepresentatives8.2 Additional SupportUsers of Microchip products can receive assistance through several channels:•Distributor or Representative•Local Sales Office•Field Application Engineering (FAE)•Technical SupportCustomers should contact their distributor, representative or field application engineer (FAE) forsupport. Local sales offices are also available to help customers. A listing of sales offices andlocations is available on our web site.Technical support is available through the web site at: 。
PT208使用手册

6
数字化·智能压力/差压变送器
测量开口容器液位时,变送器装在靠近容器的底部,以便测量其上方液面高度所对应的压力。容器液 位的压力,作用于变送器的高压侧,而低压侧通大气。如果被测液位变化范围的最低液位,在变送器安装 处的上方,则变送器必须进行正迁移。 密闭容器的液位测量 在密闭容器中,液体上面容器的压力 P0 影响容器底部被测的压力。因此,容器底部的压力等于液面 高度乘以液体的比重再加上密闭容器的压力 P0。为了测得真正的液位,应从测得的容器底部压力中减去容 器的压力 P0。为此,在容器的顶部开一个取压口,并将它接到变送器的低压侧。这样容器中的压力就同时 作用于变送器的高低压侧。结果所得到的差压就正比于液面高度和液体的比重乘积了。 导压连接方式 1)干导压连接 如果液体上面的气体不冷凝,变送器低压侧的连接管就保持干的。这种情况称为干导压连接。决定变 送器测量范围的方法与开口容器液位的方法相同。 2)湿导压连接 如果液体上面的气体出现冷凝, 变送器低压侧的导压管里就会渐渐地积存液体, 从而引起测量的误差。 为了消除这种误差,预先用某种液体灌充在变送器的低压侧导压管中,这种情况称湿导压连接。 上述情况,使变送器的低压侧存在一个压头,所以必须进行负迁移。 测量误差 导压管使变送器和流程工艺管道连在一起,并把流程工艺道上取压口处的压力传输到变送器。在压力 传输过程中,可能引起误差的原因如下: 1)泄漏; 2)摩擦损失(特别使用洁净剂时) ; 3)液体管路中有气体(引起压头误差) ; 4)气体管路中存积液体(引起压头误差) ; 5)两边导压管之间因温差引起的密度不同(引起压头误差) ; 减少误差的方法 1)导压管应尽可能短些; 2)当测量液体或蒸汽时,导压管应向上连到流程工艺管道,其斜度应小于 1/12 ; 3)对于汽体测量时,导压管应向下连接到流程工艺管道,其斜度应不小于 1/12 ; 4)液体导压管的布设要避免中间出现高点,气体导压管的布设要避免中间出现低点; 5)两导压管应保持相同的温度; 6)为避免摩擦影响,导压管的口径应足够大; 7)充满液体导压管中应无气体存在; 8)当使用隔离液时,两边导压管的液体要相同;
AB-208灯光智能控制使用说明

智能报警联动控制器安装指南
智能报警联动控制器只需一个常闭或常开输入:如红外探头,对射,紧急按钮等常闭端,即可联动另一端的强电开关(常开同样效果)。
1. 性能特点:
输出即时跟随输入功能(输入关输出也关;输入开输出也开)
输出延时跟随输入功能时间可由用户通过拨码设定(精确到5秒),最长10分钟
3.指示灯说明
●电源指示灯: 通电后就会亮
●状态指示灯: 即时联动(未拨码)情况下,快速闪烁;延时联动(拨码)情况下,1秒钟闪烁1次
●高压操作指示灯:高压继电器操作时变换指示
●低压操作指示灯:低压继电器操作时变换指示
4.使用说明
输出即时跟随输入功能不拨码,即2--8位拨码开关都是OFF
输出延时跟随输入功能拨码(见拨码开关对应时间表),最短延时为5秒,最长10分钟
具体的时间=下表的秒数* 基数(基数为5秒)
例:用户希望延时为30秒,应当拔开关数设成6,则实际继电器的闭合延迟时间将为:6 *5=30秒。
其它以此类推。
;用户想采用其他基数请在定购产品时说明。
拨码开关第1位用来设置输入端接法,1为OFF输入端接常闭,1为ON输入端接常开。
AVer Document Camera Setup Guide

Setup your AVer Document Camera from home!Please first identify which AVer document camera you are using to know what software to install.A+ Suite (Sphere2 on Win10/Mac) or Sphere Lite (Chromebooks): AVer U70+, AVer U50, AVer M70HD, AVer 300AFHD, AVer F70W, AVer F50-8M, AVer F17-8M, M17-13MAVerTouch (Win10/Mac): AVer M15W, AVer M15-13M, AVer M70WA+ Interactive Software (Old Version on Win/Mac): V300AF ASIC, SPC300 ASIC, SPC300 +, CP130, CP150, CP300, SPB350, SPB370, CP135, CP155, CP355, V355AF, V310AF, SPB350+, V300AF+, F30, F50, U10, U15, AP20,M50, W30Sphere (Old Version on Win/Mac): PL50, SPB350, SPB370, SPB350+, M50, M70, V300AF+, F50, F30, F15 U15, W30A+ Suite (Sphere2):1.Download the A+ Suite software on your computer, go to:https:///education/support/aplus-suiteSelect the OS you are using to download the software (we will use Win10 in this tutorial)2.Open the downloaded .exe file to start the installationFollow the setup wizard to install the A+ Suite software3.After installation is completed, open the Sphere2 software4.Plug in the power adapter to your document camera and turn it on by pressing the power button (does notapply to U-series doc cams, your document camera may look different than the one pictured)5.Locate a USB port on your computer and connect your camera to it via USB cable that is included6.Select the visualizer icon on the top right of the Sphere2 software and select your camera7.You are now connected to your AVer document camera and can begin teaching!If you own an AVer F70W and wish to connect to your computer wirelessly, please follow this guide: https:///education/downloads/F70WV2-Quick-Guide-EN-v5-2020-02-24.pdfSphere Lite (Chromebook):1.Download the Sphere Lite software on your Chromebook, go to:https:///webstore/detail/sphere-lite/bhmibpbadaengbikmoglphhlhioajdjn?hl=enunch Sphere Lite app after installing3.Plug in the power adapter to your document camera and turn it on by pressing the power button (does notapply to U-series doc cams, your document camera may look different than the one pictured)4.Locate a USB port on your Chromebook and connect your camera to it via USB cable that is included5.Select your camera on the bottom left. You are now connected to your AVer document camera and can beginteaching!AVerTouch:1.Download the AVerTouch software on your computer, go to:https:///education/support/avertouchSelect the OS you are using to download the software (we will use Win10 in this tutorial)2.Unzip the downloaded .zip file3.Open the extracted folder and run the .exe to start the installation4.Follow the setup wizard to install the AVerTouch software5.After installation is completed, open the AVerTouch software6.Plug in the power adapter to your document camera and turn it on by pressing the power button (yourdocument camera may look different than the one pictured)7.Locate a USB port on your computer and connect your camera to it via USB cable that is includedNote: For M15W/M70W users, please make sure WiFi is turned off when trying to do a USB connection 8.The connected visualizer will appear within the AVerTouch software. Click the play icon to connect to thecameraIf you own an AVer M15W/M70W and wish to connect to your computer wirelessly, please follow this guide: M15W: https:///education/downloads/M15W-instruction-manual-EN-2019-12-20.pdfM70W: https:///education/downloads/M70W-instruction-manual-EN-v1-2019-12-20.pdfA+ Interactive Software:1.Download the A+ Interactive Software on your computer, go to:https:///education/support/averplusSelect the OS you are using to download the software2.Unzip the downloaded .zip file3.Open the extracted folder and run the .exe to start the installation4.Follow the setup wizard to install the A+ Interactive Software5.After installation is completed, open the A+ Interactive Software6.Power on and connect your doc cam to your computer via USB cable7.Select your visualizer within the software and you are now connected!Sphere:1.Download the Sphere on your computer, go to:https:///education/support/sphereSelect the OS you are using to download the software2.Run the downloaded .exe to start the installation3.Follow the setup wizard to install the Sphere software4.After installation is completed, open the Sphere Software5.Power on and connect your doc cam to your computer via USB cable6.Select your visualizer within the software and you are now connected!Using your AVer Document Camera with other platforms (Zoom, Skype, Google Hangout).Open up your software of choice and connect your AVer document camera to your computer via USB cable.Select your AVer document camera as your visualizer and you are successfully connected!(Please refer to Zoom, Skype, or Hangout user guides to navigate through their software)Zoom:https:///hc/en-us/articles/201362033-Getting-Started-on-Windows-and-MacSkype:https:///en/skype/windows-desktop/start/Hangout:https:///hangouts/?hl=en#topic=6386410Note: The following AVer doc cams are not UVC compliant and are not compatible with other platforms: F50, M70, PL50, W30, W30HD, Tabcam, 355AF, M50More HelpFor FAQs, technical support, software and instruction manual download, please visit:https:///education/support/Contact InformationAVer Information Inc.668 Mission Ct. Fremont, CA 94539, USAToll-free: 1(877)528-7824Local: 1(408)263-3828********************。
AN208

Rev. 0.2 9/06Copyright © 2006 by Silicon LaboratoriesAN208AN208S E N S O R L E S S B R U S H L E S S DC M O T O R R E F E R E N C E D E S I G N1. IntroductionThis reference design provides a hardware and software solution for Sensorless Brushless dc motors. This document includes complete schematics, printed circuit board layout, and firmware. The Sensorless Brushless dc motor reference design may be used as a starting point for motor control system designers using Silicon Laboratories MCUs, significantly reducing the design time and time to market.Brushless dc motors consist of a permanent magnet rotor with a three-phase stator winding. Brushless dc motors evolved from conventional dc motors where the function of the brushes is replaced by electronics. Brushless dc motors offer longer life and less maintenance than conventional brushed dc motors.Most Brushless dc motor designs historically use Hall effect sensors to measure the position of the rotor. Hall effect sensors provide absolute position information required to commutate the motor. Using Hall effect sensors provides simple, robust commutation and performance roughly comparable to brushed dc motors. One of the major barriers limiting the market penetration of Brushless dc motors has been the cost of using Hall effect sensors. The Hall effect sensors themselves are not particularly expensive. However, the Hall effect assembly adds significant expense to the cost of manufacturing the motor. Hall effect sensors also typically require 5 additional wires, adding to the installation costs.A “Sensorless” Brushless dc motor does not have Hall effect sensors. Sensorless Brushless dc motors employ more sophisticated electronics using some alternative scheme to control the commutation of the motor. The most common scheme involves measuring the back EMF of the motor and using this information to control the commutation of the motor.Most computer hard disc drives use a sensorless brushless dc motor. However, these small motor drives use a linear regulator to control the voltage applied to the motor. This works well for small motors, but is too inefficient to use for motors greater than a few watts. Larger motors require PWM control for efficient operation. Using PWM control makes the task ofmeasuring the back EMF of the motor more difficult, due to noise coupled from the active windings.Sensorless Brushless dc motors are well suited for fans and rotary pumps from a few watts up to about 1 kW. Fans and pumps’ loads are predictable and fairly well behaved. Most Sensorless Brushless dc motors do notprovide the same level of dynamic speed control available from Hall effect controlled BLDC motors or dc motors. While it is theoretically possible to achieve high-performance from a sensorless BLDC motor using sophisticated vector control, most practical sensorless BLDC implementations address the much simpler fan and pump applications. This reference design is targeted for simple fan applications.Sensorless BLDC motor drives often compete against ac induction motors for certain applications. A system designer must consider the power level, efficiency requirements, and starting requirements when choosing between BLDC motors and ac induction motors. BLDC motors are most often used for small motors rangingfrom 1 watt to 1 kW. AC induction motors are readily available from 250 W to 10 kW or more. BLDC motors offer potentially higher efficiency than ac induction motors. This is due to the fact that ac motors have high rotor losses while BLDC motors do not waste energy in magnetizing the rotor. AC induction motors are much easier to start than sensorless BLDC motors. Thecomplexity of starting a fully loaded BLDC motor often makes the ac induction motor a better choice, particularly for piston pumps and compressors.AN2082Rev. 0.22. Theory of OperationBrushless dc motors have a dual personality. To fully understand Sensorless Brushless dc motor control it is necessary to understand both dc motor characteristics and Stepper motor characteristics. When commutated using Hall effect sensors, the torque speed characteristics of the Brushless dc motor are virtually identical to a conventional dc motor. The ideal no load speed is a linear function of the applied voltage. The torque and motor current are at a maximum at zero speed and decrease to zero at the maximum speed. The torque-speed characteristics of a dc motor are shown in Figure 1. Under ideal conditions, the characteristics of a sensorless BLDC motor are similar.The characteristics of a stepper motor are quite different. The motor current in a stepper motor is not proportional to the load torque. The motor winding resistance typically limits the current in a stepper motor. The motor winding resistance of a stepper motor is normally an order of magnitude higher than a BLDC motor. An ideal model for a stepper motor is shown in Figure 2.Figure 2. Stepper Motor ModelThe motor is driven with a constant voltage. When the motor is at a standstill, the back EMF is zero and the current is at its maximum value. As the motor speed increases the back EMF will increase, reducing the voltage across the motor resistance, and the motorcurrent will decrease. The available torque for a stepper motor is proportional to the current forced through themotor windings. The available torque is at its maximum value when the motor is at a standstill. The available torque decreases as the motor speed increases. If the load torque ever exceeds the available torque the motor will stall. Figure 3. Stepper Motor CharacteristicsThe performance of the stepper motor may be improved using a variable voltage drive. By increasing the voltageapplied to the stepper motor in proportion to the velocity,the available torque will remain constant and the fancan be driven to a higher velocity before stalling as shown in Figure 3.A BLDC motor can also be considered as an unusual stepper motor. A 4-pole 12 V BLDC motor is functionally equivalent to a 12-step per revolution stepper motor with a voltage rating of about 1 V. A typical Stepper motor has a much higher step count, higher voltage, and higher resistance. A typical hybrid permanent-magnet stepper motor has a step angle of 1.8º, or 200 steps per revolution. A 12 V stepper motor might have a resistance of 30 Ω, compared to less than 1 Ω for a similar size BLDC motor. The stepper motor is optimized for precise angular positioning and constant voltage drive. The BLDC motor is optimized for Hall effect commutation and variable voltage drive.2.1. PWM SchemeMost Hall effect BLDC motors use a three-phase bridge to drive the motor windings. A Three-Phase bridge isshown in Figure 4.AN208Rev. 0.23Figure 4. Three-Phase BridgeThe most common drive method is to use blockcommutation and apply a PWM signal to only thebottom transistors as shown in Table 1. Depending onthe position of the motor and the Hall effect code, theappropriate step pattern is applied to the motor. As themotor rotates, the step pattern will increment throughthe table entries. Using this method, at any point in timethere is only one top transistor in the continuous ONstate and only one bottom transistor being driven by thePWM signal.Considering the motor phases, one phase is drivenhigh, one phase is being pulse-width modulated, andone phase is open. The open phase is noted in thetable. However, there is a problem using the open-phase to sense the back EMF when pulse-widthmodulating only the bottom transistors.Figure 5. Low-Side PWM Back EMFConsider the BLDC motor winding shown in Figure 5. Inthis case the motor is at the first state of thecommutation table. A pulse-width modulated signal isapplied to phase A, phase B is driven high, andphase C is open. The back EMF that we are interestedin is actually the voltage from phase C to the centerconnection labeled point Y. The problem is that thecenter of the Y connection is not a constant dc voltage.Assuming that the resistance and inductance ofwindings A and windings B are the same, the voltage atpoint Y will be halfway between phase A and phase B.The voltage at point Y will be approximately half thesupply voltage when phase A is driven low. Whenphase A is high, the center point Y will be approximatelyequal to the upper supply voltage. The voltage on theopen phase C is now the voltage at center-point Y plusthe back EMF of the motor. The voltage at phase C isalso clamped to the upper rail by the MOSFET bodydiodes in the inverter bridge. The result is a pulse widthmodulated waveform where the minimum voltage levelis equal to the back EMF of the motor. While it ispossible to filter out the PWM signal or sample thevoltage during the PWM on-time, working with thiswaveform is problematic.A better approach is to use a symmetric PWM scheme.A symmetric PWM scheme is any PWM scheme wherethe active top and bottom transistors are turned on andoff together. The simplest method is to apply identicalPWM signals to the top and bottom transistorsaccording to Table 2. This commutation table is similarto the low side PWM commutation table except that thehigh side transistors are pulse-width modulated insteadof just being turned on.Table 1. Low-Side PWM CommutationTop Bottom OpenA B C A B C Phase0ON PWM C1ON PWM B2ON PWM A3ON PWM C4ON PWM B5ON PWM AAN2084Rev. 0.2During the first state of Table 2, an identical PWM signal is applied to both the A bottom transistor and the B top transistor. The result is that Phase A will go low when Phase B goes high and visa versa. If the A and B windings are balanced, the center point Y will remain mid-rail even though phase A and phase B are being pulse-width modulated. The voltage on phase C is now roughly equal to the back EMF voltage. There may be some residual PWM noise due to the second order effects of unbalanced windings and capacitive coupling. However, the unwanted PWM signal is reduced by at least an order of magnitude, as shown in Figure 6.Figure 6. Symmetric PWM Back EMF3. Back EMF WaveformsMost sensorless BLDC control systems use the back EMF zero crossing time as a control variable for a phase locked loop. Instead of using the zero-crossing time, this reference design measures the back EMF voltage at middle of the commutation period using the ADC and uses the voltage measurement to control the commutation. This method provides higher resolution and always provides a robust feedback signal even asthe motor approaches a stall condition. When using the zero-crossing time as a feedback signal, special measures must be taken when a zero crossing does not fall within the measurement window.The back EMF voltage for three different cases is shown in Table 3. If the voltage and speed are just right the voltage ramp will be centered within the commutation period and the midpoint voltage will measure half of the supply rail. If the voltage is too low or the speed is too fast the voltage ramp will be shifted up and to the right. If the voltage is too high or the speed is too slow, the voltage ramp will be shifted down and to the left. The feedback loop should work to keep the mid-point voltage at mid-rail.3.1. Safe Operating RangeWhen driving a Sensorless BLDC motor from a MCU there are two output variables, the motor Voltage V and the motor speed ω. Figure 7 shows the output voltage verses speed characteristics for a sensorless BLDC motor. Three lines are labeled in Figure 7. The middle line is the ideal “no load” line with V equal to ω times the motor constant K E . This line represents the optimum voltage for a perfect motor with no friction.Table 2. Symmetric PWM CommutationTop Bottom Open A B CA BCPhase 0PWMPWMC 1PWM PWM B 2PWMPWM A 3PWM PWMC 4PWM PWM B 5PWM PWMATable 3. Back EMF ControlAN208Rev. 0.25 Figure 7. Output Voltage and SpeedThe maximum current is normally limited by thecapability of the power transistors. The maximum boostvoltage is then the maximum inverter current times thewinding resistance. The upper line in Figure 7 is theideal voltage plus the maximum boost voltage. This linedefines the maximum bounds for safe operation. Thelower line is the ideal voltage minus the maximum boostvoltage. This line defines the minimum bounds for safeoperation. While not intuitive, it is quite possible to getan over-current condition by driving the motor with avoltage that is too low for a particular speed.Figure 8. Safe Operating AreaThe Safe Operating Area for the Sensorless BLDCmotor is shown in Figure 8. Above the maximum line thevoltage is dangerously too high. Below the minimum linethe voltage is dangerously too low. The area betweenthe ideal line and the max line is labeled the positivetorque region. In normal steady state operation, theoutput variables will operate in the positive torqueregion.The area below the ideal line is labeled the negativetorque region. While most simple fan and pumpapplications do not require negative torque, operation inthe negative area is permitted. If the motor speedcommand is decreased, the control system will outputvalues in the negative torque region until the operatingpoint is re-stabilized. While it is possible to prohibitoperation in the negative torque region, this mayadversely affect the stability of the control system.The safe operating area is important because it is veryeasy to exceed the limit using conventional controltechniques. If we ignore the safe operating area anduse a simple PI controller to regulate the output voltage,the control loop will output excessive voltage and thepower transistors may be damaged.If we drive the motor with a voltage corresponding to themaximum line, we are forcing maximum current into themotor at all times. This will provide the maximumavailable torque at all times and it is unlikely that themotor will stall. However, the no load efficiency will bevery low and cogging torque may be a problem.Cogging torque is the variation in torque caused by apulsating electromotive force. Stepper motors aredesigned to operate on the max line with low coggingtorque. Most BLDC motors are not designed for thiskind of operation. Excessive cogging torque can causevibration, noise, and stability problems.This reference design uses a novel control techniqueentitled “Constant Voltage Control with SpeedDependent Limiting”. The goal of this controlmethodology is to provide a simple and robust controlalgorithm using a single control loop while keeping theoutput speed and voltage within the Safe OperatingArea.The control technique is illustrated in Figure 9. Theinput speed control potentiometer controls the targetoperating point indicated by the dot on the ideal line. Ifthe error signal is zero, the output voltage and speedare set according to the speed potentiometer. As thespeed control is varied, the target operating point willvary along the ideal line.The bold line indicates variation in the output voltageand speed due to the error signal. A small positive errorsignal from the feedback control system will result in adecrease in speed while the voltage remains constant.The voltage will remain constant until the speed reachesthe limit set by the maximum line. If the error signal islarge enough to exceed the limit, both voltage andspeed are reduced according to the maximum limit.In a similar fashion, a small negative error signal willresult in an increase in speed. If the negative error isincreased beyond the bounds set by the minimum line,the voltage will be increased.The resulting control loop is very stable. The motor isdriven with a constant voltage, as long as the loadAN2086Rev. 0.2torque and acceleration are within the bounds set by the minimum and max limits. In this region the motor behaves like a dc motor with a constant voltage drive. A small increase in load torque will result in a small decrease in speed.For large positive errors signals, the motor voltage is reduced to keep the current below the maximum limits. In this region the motor behaves as a constant current or constant torque drive.Figure 9. Constant-Voltage with Limiting3.2. Starting One major problem with using the back EMF to control the commutation of a sensorless BLDC motor is that the back EMF is not present or is too small to be useful until the motor is rotating at some minimum speed. Thecommon solution is to drive the BLDC motor like astepper motor to align the motor and accelerate themotor up to some nominal speed. This requires that the control system have multiple modes of operation. While it is generally undesirable to have a control system withmultiple modes of operation, it is unavoidable in thiscase. A common pitfall of systems with multiple modesof operation is instability during the transition from one control mode to another. Special considerations are required in the running stage to ensure system stabilityduring the transitions.The motor state diagram is shown in Figure 10. The system is initially in the STOP state. Pressing the Start button will advance to the ALIGN state. The motor willthen advance automatically to the START and RUNstates. An over-current error will reset the motor to the STOP state. Figure 10. SBLDC State Diagram3.3. AlignmentThe alignment state consists of two stages—the Alignment Ramp and the Alignment Delay. During the Alignment Ramp, one of the motor windings is excited by PWMing the top of one phase and the bottom of another phase. The PWM duty cycle is initially at zero percent and is ramped up to 50% plus the starting boost voltage. The voltage is increased using a linear ramp with a fixed delay time between voltage increments. The current in the motor winding will depend on the motor inductance and winding resistance. For duty cyclesbelow 50% the current will be discontinuous. The current will increase while the transistors are on and decrease to zero after the transistors turn off as shown in Figure 11. The peak and average dc current for duty cycles equal to or less than 50% can be calculated using Equation 1.The PWM duty cycle will always be above 50% while running.I avg I peak VL---d×==AN208Rev. 0.27Equation 1. Peak and Average CurrentFor duty cycles above 50% the current will be continuous. Usually a higher current is desired for alignment. Above 50%, a small change in duty cycle will result in a much large change in average dc current. The starting boost voltage is typically a very small number.The second part of the alignment phase consists of asimple delay. The voltage is held constant for a period oftime. The alignment delay time should be long enough to allow the motor to align to the excited pole position. A one second ramp time and a two second delay time works well for the test motor with no fan. When using a large fan, a time of several seconds may be required. Finding the optimal delay time requires some experimentation.The alignment stage ensures that the motor starts froma known position. Without the alignment stage the motormight miss the first several critical commutations in the starting acceleration ramp. If the motor does not align during this stage a motor stall is more likely in the starting phase.During the alignment stage the system is in a relativelybenign state. The dc current is predictable and wellregulated. The power dissipated in the motor can becalculated from the motor winding resistance. A currentmeasurement is only needed to protect against wiringerrors.Most BLDC motors are optimized for high-speedoperation and have very limited torque in the alignmentphase. This is not too much of a problem for small fans,but it does preclude the use of sensorless control insome other applications. The torque is limited by theinverter current and motor design. Over-sizing the inverter or using a lower speed motor can increase the starting torque.3.4. Starting During the starting phase the BLDC motor is driven like a stepper motor. The motor is commutated at first very slowly and then velocity is increased linearly using a linear velocity ramp table. The voltage is also increasedin proportion to the velocity with additional boost voltageto keep the current at a constant value. The motor winding resistance normally limits the boost voltage.The acceleration ramp table ramps the motor speedover a 30:1 range from 25 to 750 rpm. The maximumvalue of 750 rpm was chosen to be one tenth of the maximum speed of the motor. The closed loop sensorless control will then operate over a 10:1 range from 750 to 7500 rpm. The back EMF at 750 rpm will be one tenth of the rated voltage.The key to getting the motor up to 750 rpm is to use alarge enough acceleration ramp table with a sufficiently large ratio of minimum to maximum. A ratio of 30:1 can be achieved using a table with only 192 bytes of data. This also permits the efficient use of an 8-bit table index. Experimental results using a smaller 16-byte table withan 8:1 range proved unsatisfactory. If the table is too small, the initial velocity will be too fast or the finalvelocity will be too slow.The voltage of the motor is also ramped during the acceleration phase. If the voltage were held constant at the alignment value, the current would decrease during the motor acceleration. Initially the current is only limited by the motor resistance. As the motor starts turning, the back EMF of the motor will subtract from the voltageacross the motor resistance. This results in a decrease in motor current and a corresponding decrease in theamount of available torque.Assuming the motor will accelerate in step with the commutation period, the back EMF will be proportional to the motor velocity and inversely proportional to themotor period. The motor voltage ramp may be calculated by dividing a constant by the value in theramp table. By increasing the voltage during theacceleration phase the motor current can be held at aconstant value. This ensures maximum available torqueduring the acceleration phase.If the motor stalls at any point, the back EMF will be zero, and the assumption of motor velocity is no longervalid. The resulting motor voltage will be too high andthe current may be much higher than expected. This isproblematic for small motors and can be disastrous forlarge motors.The solution is to monitor the dc motor current during acceleration and to shut down if the motor current getstoo high. The back EMF is not sufficiently large to detect if the motor is moving. A current limit is not neededduring the starting phase if the motor voltage is limited to the maximum inverter current times the motor resistance, though this will severely limit the starting torque on all but the smallest motors.3.5. RunningThe minimum Running speed and voltage are dictatedby the starting parameters. In this example, the minimum speed is 750 rpm. The minimum voltage is10% plus the boost voltage. At the lower operatingAN2088Rev. 0.2point, the motor is being over-driven by a voltage that is intentionally higher than necessary for stable closed loop operation. Since the motor is being driven like a stepper motor, the cogging torque and motor vibration will be higher in the starting phase.3.6. Back EMF MeasurementsThe back EMF is measured at three points, as shown in Figure 12. The midpoint voltage is the primary control variable for closed loop control. The two voltage measurements at one quarter and three fourths are used for stall detection. The current measurement is used for over current detection. The time slots are discussed in further detail in the software description.Stall detection is achieved by measuring the voltage at quarter points over two cycles. The difference betweenthe minimum and maximum of these four points is anindication of the back EMF of the motor. If the back EMFis greater than a certain value, we can deduce withreasonable certainty that the motor is indeed running. Ifthe back EMF is too small to give a usefulmeasurement, we cannot know for certain if the motor isstalled or running. Thus, the stall detection operatesonly in the running phase. The example implementationilluminates an LED when a stall condition is detected.4. Hardware DescriptionThe schematic diagram for the Sensorless BLDC Motor reference design is in Appendix A. The circuit consists of the C0851F310 Microcontroller, three-phase power MOSFET bridge, three dual gate drivers, sense voltage resistive dividers, current amplifier, speed control potentiometer, two function switches, USB-UART bridge, and voltage regulator.Port P1 is configured as push-pull outputs and is connected to the three dual gate drivers. The P1 port pins are sequenced, alternating between bottom and top starting with phase A in the least significant bit. P1.0-1.5 corresponds to A bottom, A top, B bottom, B top, C bottom, and C top respectively. This sequence facilitates commutation using a simple pattern with the Crossbar pin skip register.Each of the three output phases are connected to a simple resistive divider. The resistive divider will divide the phase output voltage by six. This ratio permits accurate ADC measurements up to 19.8 volts. The 5 V tolerant port pins offer protection against phase voltages up to 30 Volts. The motor supply is 12 V nominal when loaded with the motor turning at full-speed. The unloaded voltage may climb as high as 18 V for the recommended wall mounted transformer.A capacitor across the lower resistor of each divider forms simple single-pole low-pass RC filter. Each filter is tuned approximately one decade below the PWM frequency. Three test points are provided for the scaled voltages labeled VA, VB, and VC.A forth resistive divider is used to sense the voltage of the motor supply. This resistive divider has a ratio of one to twelve. A test point is provided on the scaled motor supply voltage labeled VM. A phase voltage of 12 volts will produce voltage of 2 V on the respective ADC input, while a supply voltage of 12 V will produce a sense voltage of 1.0 V on the VM ADC input. A differential ADC voltage measurement will be used relative to the VM ADC input. The resulting ADC reading will be a signed 16-bit value with 0x0000 corresponding to mid-rail.The sensorless BLDC motor reference design boardincludes a current sense resistor R25 and currentamplifier U7A. The sense resistor is a 20 m Ω surfacemount resistor in an 1812 package. The sense resistorwas chosen for a maximum RMS current of 5 amps witha power dissipation of 500 mW. The resulting sensevoltage of only 100 mV requires amplification to achievemore than 5 bits of resolution from the 10-bit ADC.The current amplifier is a variation of the classic differential amplifier circuit. In the classic circuit configuration, the second resistors on the non-inverting input would be connected to ground. In this variation,resistor R17 is connected to a 400mV voltage reference. The 0.4V reference compensates for the variation in the input offset voltage of the op amp and also keeps the output within the recommended output voltage range. The gain of 26 was chosen to fully utilize the output voltage span of the amplifier allowing forvariation in the input offset voltage. The op amp chosen for this circuit is the LMV358. This is a low-voltage version of the industry standard LM358 dual CMOS op amp. The second op amp in the dual。
- 1、下载文档前请自行甄别文档内容的完整性,平台不提供额外的编辑、内容补充、找答案等附加服务。
- 2、"仅部分预览"的文档,不可在线预览部分如存在完整性等问题,可反馈申请退款(可完整预览的文档不适用该条件!)。
- 3、如文档侵犯您的权益,请联系客服反馈,我们会尽快为您处理(人工客服工作时间:9:00-18:30)。
}
People
• Part of the 7 Ps - related to the interaction of staff with customers and stakeholders • What skills and experience do your staff need to service your customers • How do you integrate your human resources with your automated processes
______ refers to a model for assessing the quality of the online customer experience.
• • • • • The Long Tail SERVQUAL The Tipping Point -Price transparency None of the above.
• Promotion 1.personal promotion 2. direct marketing
• Place 1.Direct distribution channel 2. new intermediary
2. Critically evaluate the impact of the Internet on the marketing mix for an industry sector of your choice.
Tipping point 倾卸点
Ghosh (1998) describes methods of creating digital value by adding to the ______ element of the mix by asking questions such as, "can I offer additional information or transaction services to my existing customer base?" • • • • • Place Product Promotion Price None of the above.
Processes
• Part of the 7 Ps – related to methods and procedures companies use to achieve its marketing functions • Increase customer’s satisfaction and to minimise costs by increase efficiency, productivity and moral/motivation
Physical evidence
• Part of the 7 Ps – often referred to as the tangible expression of a product and how it’s purchased and used • In an online context – it’s refers to as the customer’s experience of the company through the website
The ______ customer concern from the 4Cs is equivalent to the Price element of the marketing mix.
• • • • • needs and wants convenience cost communications techniques None of the above.
• How customer interactions are managed
process
• Where the products are delivered or distributed to place • Different product pricing for different categories
______ refers to how word of mouth communication has a tremendous impact on the rate of adoption of new products • • • • • The Long Tail SERVQUAL The Tipping Point -Price transparency None of the above
______ refers to the impact of comparison websites and aggregator intermediaries.
• • • • • The Long Tail SERVQUAL The Tipping Point 倾卸点 Price transparency None of the above.
Extended Product
Additional
DHL
1.Core benefit: 2.deliver parcels 3.Basic product: 4.collect parcels form sender and deliver parcels to receivers 5.extened product: 6.tracking system make the customers know where their parcels have been delivered.
• Product: new digital products and valueadds. • Price: price reduction, new pricing models. • Place: new representation on intermediaries, direct-selling. • Promotion: integration of online and offline techniques.
price
The ______ customer concern from the 4Cs is equivalent to the Place element of the marketing mix
• • • • • needs and wants convenience cost communications techniques None of the above.
4C
• • • • Customer needs and wants (from product) Cost to the customer (price) Convenience (relative to place) Communication (promotion)
1. Select the two most important changes introduced by the Internet for each of the 4Ps.
• • • • • Disintermediation Countermediation Star Alliance Localisation None of the above.
Match the definition to the issue relating to Place in the online marketing mix. ______ refers to 'cutting out the middleman' through selling-direct.
Explain two applications of dynamic pricing on the Internet.
• selling ‘distressed inventory’, for example, flight tickets, which must be used by a fixed date. • varying prices for different segments.
BMA208
Tutorial 5 Toby
What is marketing mix?
• • • • • • • • • Traditional marketing mix is 4P But for internet marketing mix is 7P Product How are the marketing mix Promotion varied online? Price Place People better reflect Process service delivery Physical evidence
How word of mouth communication has a tremendous impact on the rate of adoption of new products, Using the science of social epidemics explains principles that underpin the rapid spread of ideas, products through a population. Domino effect
Match the definition to the issue relating to Place in the online marketing mix. ______ refers to the creation of country or region-specific content (often involving translation).
Product Price Place Promotion People Physical evidence Process
• A. How the brand is presented. Physical evidence • B. The mix of traditional and online Promotion communications • C. Opportunities for modifying the core or extended product Product • D. How customer service affects the experience people