压铸工艺及模具设计:第7章 成型零件和模架设计
第7章成型零件及模架设计详述

成型尺寸的计算要点如下: ①型腔磨损后尺寸增大,计算型腔尺寸时应使压铸件外 形接近于最小极限尺寸。 ②型芯磨损后尺寸减小,计算型芯尺寸时应使压铸件内 形接近于最大极限尺寸。 ③两个型芯或型腔之间的中心距离和位置尺寸与磨损量 无关,应使压铸件尺寸接近于最大和最小两个极限尺寸的 平均值。
2.成型尺寸标注形式及偏差分布的规定 上述三类成型尺寸,分别采用三种不同的计算方法。
镶块壁厚尺寸推荐值见表7-7。
2.整体镶块台阶尺寸 整体镶块台阶尺寸推荐值见表7-8
3.组合式成型镶块固定部分长度 组合式成型镶块固定部分长度推荐值见表7-9
4.圆形型芯结构尺寸 圆形型芯结构尺寸推荐值见表7-10
7.2成型零件成型尺寸的计算 7.2.1压铸件的收缩率 1.实际收缩率
压铸件的收缩率是指室温时,模具成型尺寸与压铸件对 应尺寸的相对变化率。又称为实际收缩率。即
L模 L铸 100%
L模
常用压铸合金的计算收缩率见表7-11。
2.计算收缩率(室温下压铸件尺寸与模具尺寸的相对差值) 设计模具时,计算成型零件成型尺寸所采用的收缩率为
计算收缩率。它包括了压铸件收缩值及模具成型零件在工作 温度时的膨胀值,即
计
L模 L铸 L铸
100%
L模 L铸(1%)
3.收缩率的确定 压铸件的收缩率应根据压铸件的结构特点、收缩条件
φ50的尺寸要换算成单向公差尺寸,其结果是: 49.900.22
计算结果如下表:
序号 类别
压铸件 尺寸
计算公式
模具尺寸
1
型 径向 腔
500.10 0.32
2
尺 深度
寸
2000.12
50.0500.055
20.04
压铸模设计及成型零件制造工艺与压铸工艺设计
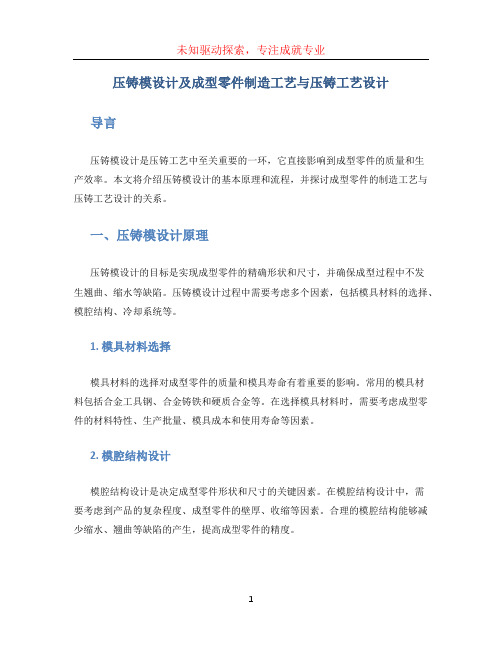
压铸模设计及成型零件制造工艺与压铸工艺设计导言压铸模设计是压铸工艺中至关重要的一环,它直接影响到成型零件的质量和生产效率。
本文将介绍压铸模设计的基本原理和流程,并探讨成型零件的制造工艺与压铸工艺设计的关系。
一、压铸模设计原理压铸模设计的目标是实现成型零件的精确形状和尺寸,并确保成型过程中不发生翘曲、缩水等缺陷。
压铸模设计过程中需要考虑多个因素,包括模具材料的选择、模腔结构、冷却系统等。
1. 模具材料选择模具材料的选择对成型零件的质量和模具寿命有着重要的影响。
常用的模具材料包括合金工具钢、合金铸铁和硬质合金等。
在选择模具材料时,需要考虑成型零件的材料特性、生产批量、模具成本和使用寿命等因素。
2. 模腔结构设计模腔结构设计是决定成型零件形状和尺寸的关键因素。
在模腔结构设计中,需要考虑到产品的复杂程度、成型零件的壁厚、收缩等因素。
合理的模腔结构能够减少缩水、翘曲等缺陷的产生,提高成型零件的精度。
3. 冷却系统设计冷却系统的设计对模具寿命和生产效率有着重要的影响。
合理的冷却系统能够快速降低模具温度,提高成型速度,减少成本。
冷却系统的设计需要考虑到模腔形状、成型零件的特性、模具材料等因素。
二、成型零件制造工艺与压铸工艺设计成型零件的制造工艺和压铸工艺设计是紧密相关的。
成型零件的制造工艺包括材料准备、熔炼、浇注、固化、清理等过程;而压铸工艺设计包括模具设计、模具制造、成型参数设置等过程。
1. 材料准备材料准备是成型零件制造工艺的第一步。
在压铸工艺中,常用的材料包括铝合金、锌合金、镁合金等。
材料的准备需要考虑到成型零件的要求和使用环境,选择合适的材料,并进行加热、熔化等处理。
2. 熔炼熔炼是将原材料加热至熔点并进行熔化的过程。
在熔炼过程中,需要控制温度、时间和熔炼速度等参数,确保材料的均匀性和纯度。
熔炼后的材料会通过浇注口注入压铸模中进行成型。
3. 浇注与固化浇注是将熔融的材料注入压铸模中的过程。
在浇注过程中,需要控制浇注速度、浇注压力和浇注位置等参数,以确保材料均匀填充模腔。
压铸工艺与模具设计

压铸工艺与模具设计压铸是一种常见的金属成型工艺,通过将熔融金属注入到预先设计的模具中,经过冷却与固化,得到所需形状的金属制品。
压铸工艺具有高效、精度高、生产周期短等优点,广泛应用于汽车、机械、电子等领域。
而模具设计是实现压铸工艺的关键环节,决定了产品的质量和生产效率。
下面将从压铸工艺和模具设计两个方面进行详细阐述。
一、压铸工艺1.压铸工艺流程:首先,将金属加热至熔点,并注入到模具中;然后,通过高压注射机构,将熔融金属迅速注入模具中,并保持一段时间;待金属冷却并固化后,打开模具,取出成品。
2.压铸工艺特点:①高效、精度高:压铸通过模具的高速填充和快速冷却,能够实现高效率、高精度的生产;②生产周期短:相比其他金属成型工艺,压铸生产周期较短,适用于大批量生产;③生产成本低:压铸可以实现自动化生产,减少人工成本;④可复杂成型:压铸可以实现复杂形状、薄壁、高强度的金属制品成型。
二、模具设计模具设计是实现压铸工艺的关键环节,影响产品的质量和生产效率的重要因素。
以下是模具设计的主要考虑因素:1.模具材料选择:模具材料要具有耐磨性、耐腐蚀性、热传导性和高温强度,常用的模具材料包括铸钢、合金钢等。
2.模具结构设计:模具结构设计要考虑产品的形状、尺寸及要求,尽可能减少产品缺陷和铸件结构应力,提高生产效率和产品质量。
3.模具冷却系统设计:模具冷却系统的设计直接影响到成品的质量和生产效率。
合理的冷却系统设计可以加快铸件凝固速度,减少缺陷的产生。
4.模具排气系统设计:排气系统的设计对于排除铸件中的气体孔洞和缺陷非常重要,合理的排气系统设计能够提高产品质量。
5.模具表面处理:模具表面处理可以提高成品的表面质量和延长模具寿命,常见的表面处理方式包括硬镀铬、熔融硬化、电镀等。
总结:综上所述,压铸工艺与模具设计是密切相关的。
压铸工艺具有高效、精度高、生产周期短等优点,模具设计是实现压铸工艺的关键环节,包括模具材料选择、模具结构设计、模具冷却系统设计、模具排气系统设计和模具表面处理。
压铸成型工艺与模具设计

压铸成型工艺与模具设计一、引言压铸成型工艺是一种常见的金属零件制造方法,它通过将熔融金属注入模具中,经过冷却凝固后获得所需形状的零件。
模具设计是压铸成型工艺的关键环节,合理的模具设计可以保证产品质量和生产效率。
本文将介绍压铸成型工艺的基本原理以及模具设计的要点。
二、压铸成型工艺原理压铸成型工艺是将金属材料加热至液态,然后通过高压将熔融金属注入模具中,待冷却后获得所需形状的零件。
压铸成型工艺具有以下特点:1. 精度高:压铸成型工艺可以制造出形状复杂、尺寸精确的零件,满足不同行业的需求。
2. 生产效率高:压铸成型工艺具有高度自动化的特点,可以实现连续生产,提高生产效率。
3. 材料利用率高:压铸成型工艺可以减少废料产生,提高材料利用率。
4. 表面质量好:压铸成型工艺可以制造出光滑平整的表面,减少后续加工工序。
三、模具设计要点1. 材料选择:模具的材料应具有良好的热导性和耐磨性,常用的材料有冷作工具钢、热作工具钢和硬质合金等。
根据零件的要求,选择合适的模具材料。
2. 模具结构设计:模具的结构设计应考虑到零件的形状、尺寸和工艺要求,确保零件的成型质量。
模具的结构主要包括模腔、模芯、导向机构和冷却系统等。
3. 浇注系统设计:浇注系统的设计直接影响到熔融金属的流动和充填情况,应合理布置浇口、冲压头和溢流槽等。
同时,应考虑熔融金属的冷却和凝固过程,避免产生缺陷。
4. 铸件脱模设计:铸件脱模设计应考虑到零件的形状、表面质量和模具的结构,以确保零件的完整性和光洁度。
可以采用顶出机构、斜顶和分模等方式来实现铸件的脱模。
5. 冷却系统设计:冷却系统的设计对于模具寿命和零件质量有着重要影响。
应根据零件的形状和厚度,在模具中设置合适的冷却水路,以加快冷却速度,避免产生缺陷。
6. 模具加工工艺:模具的加工工艺应选用适当的加工方法和工艺参数,以确保模具的精度和表面质量。
常用的加工方法包括数控加工、电火花加工和线切割等。
7. 模具试模调试:模具制造完成后,需要进行试模调试,以验证模具的性能和调整工艺参数。
压铸工艺与模具设计
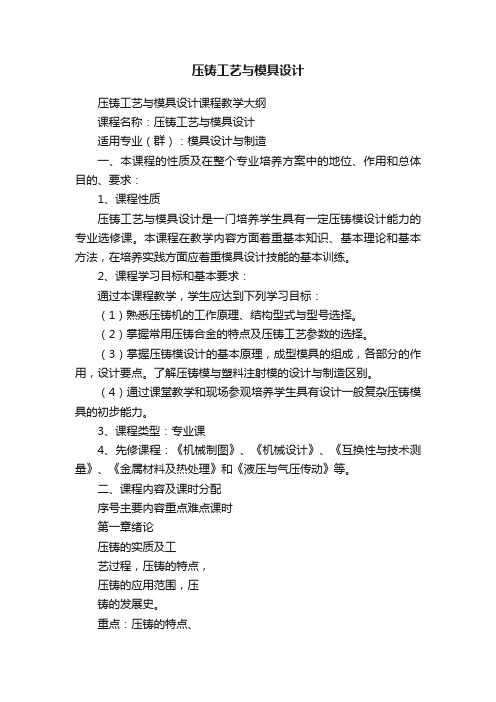
压铸工艺与模具设计压铸工艺与模具设计课程教学大纲课程名称:压铸工艺与模具设计适用专业(群):模具设计与制造一、本课程的性质及在整个专业培养方案中的地位、作用和总体目的、要求:1、课程性质压铸工艺与模具设计是一门培养学生具有一定压铸模设计能力的专业选修课。
本课程在教学内容方面着重基本知识、基本理论和基本方法,在培养实践方面应着重模具设计技能的基本训练。
2、课程学习目标和基本要求:通过本课程教学,学生应达到下列学习目标:(1)熟悉压铸机的工作原理、结构型式与型号选择。
(2)掌握常用压铸合金的特点及压铸工艺参数的选择。
(3)掌握压铸模设计的基本原理,成型模具的组成,各部分的作用,设计要点。
了解压铸模与塑料注射模的设计与制造区别。
(4)通过课堂教学和现场参观培养学生具有设计一般复杂压铸模具的初步能力。
3、课程类型:专业课4、先修课程:《机械制图》、《机械设计》、《互换性与技术测量》、《金属材料及热处理》和《液压与气压传动》等。
二、课程内容及课时分配序号主要内容重点难点课时第一章绪论压铸的实质及工艺过程,压铸的特点,压铸的应用范围,压铸的发展史。
重点:压铸的特点、实质和工艺过程。
本章属介绍性内容,不存在难点2第二章压铸过程原理及常用压铸合金压铸压力和压铸速度,液态金属充填铸型的理论(喷射充填、全壁厚充填、三阶段充填),常用压铸合金的要求(压铸合金的分类、主要性质和选用)。
压铸压力、压铸速度和充填形态对压铸质量的影响,合金的选用。
压铸压力和压铸速度。
4第三章压铸机压铸机的分类,压铸机的压铸过程及特点,压铸机的合模机构和压射机构,压铸机的选用。
压铸机的选用,压室容量的估算,开模行程的核算压铸机的选用。
6第四章压铸件结构设计及压铸工艺压铸件结构设计,压铸工艺参数选择(包括压力、速度、温度和时间),压铸涂料的作用、要求和选用,压铸件的清理、浸渍、后处理和表面处理,半固态压铸的特点、成形方法及应用,其他特殊压铸工艺(包括真空压铸、充氧压铸、精速密压铸等)压铸件结构设计和压铸工艺参数选择。
压铸模成形零件设计
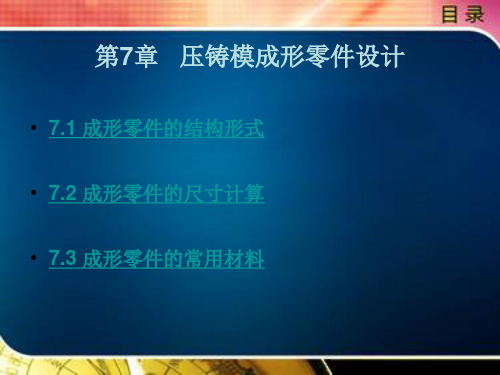
7.1 成形零件的结构形式
• 7.1.4
• • 1. • 模套组合式的结构形式如图7-7所示。 • 图7-7(a)所示的型腔外形结构比较复杂,采用整体结构很难加工,所
以将其分拆成几块镶件:底拼块1、端面拼块2和侧拼块3,分别加工 后,装入模板的模套4中, 组合成形腔,保证了成形件的精度,降低 了加工难度。
上一页 下一页 返回
7.1 成形零件的结构形式
• 7.1.3
• • 图7-4为局部组合式型腔的结构实例。 • 图7-4(a)为压铸件底部有较为复杂的成形形状,很难加工,因此在型
腔底部铣出形状简单的模套,将加工好的成形底芯压入,在背面用螺
• 图7-4(c)~(f) • 局部组合式型腔多用于局部形状较为复杂,整体加工较为困难的场合。
上一页 下一页 返回
7.1 成形零件的结构形式
• 图7-7(b)为直角型腔的拼接形式。 图7-7(c)是圆角型腔的拼接形式, 为避免明显的接缝痕迹,应将拼接处设在圆角的切点处。加工研合后,
• 图7-7(d) • 为了增强各拼块间相互拼接的强度和刚度,均采用T字槽的连接方式,
上一页 下一页 返回
7.1 成形零件的结构形式
• 图7-2(b)是模板用线切割机床,切割成贯通的模套,将矩形型腔镶块 从背面装入模框,并设置台肩,用螺栓固定在垫板上。
• 图7-2(c)是另一种组合形式,在模腔镶块中心用螺栓将其固定在垫板
上,为防止转动,需设置止转销。
上一页 下一页 返回
7.1 成形零件的结构形式
• 整体组合式型芯的基本结构和固定形式如图7-3 • 图7-3(a)是将模板加工成与型芯相对应的安装孔,采用H7/h6的
第7章 压铸模成形零件设计
压铸成型零件与模架设计

压铸工艺及模具设计
影响压铸件收缩率的因素较多,主要如下: (1) 铸件结构越复杂,型芯数量越多,收缩率就小,反 之收缩率就大。 (2) 薄壁铸件收缩率小,厚壁铸件收缩率大。 (3) 包住型芯的径向尺寸收缩受阻,收缩率较小,而轴 向尺寸收缩自由,收缩率较大。 (4) 浇注温度高时收缩率大,反之收缩率小。 (5) 有镶嵌件的铸件收缩率变小。 (6) 在模具中停留时间越短,脱模温度越高,铸件的收 缩率越大,反之收缩率则越小。 因此,要精确确定收缩率很困难,在计算成型尺寸时, 往往综合上述诸多因素的影响,选用综合收缩率进行计算, 可参考表6-2进行选取。
(1) 不通孔形式,套板结构简单,强度较高,可用螺钉 和套板直接紧固,不用座板和支承板。但当动、定模均为不 通孔时,对多型腔模具要保证动、定模镶块安装孔的同轴度 和深度尺寸全部一致比较困难。不通孔形式用于圆柱形镶块 或型腔较浅的模具,如为非圆形镶块,则只适用于单腔模具。
(2) 通孔形式,套板用台阶固定或用螺钉和座板紧固。 在动、定模上,镶块安装孔的形状和大小应一致,以便加工 和保证同轴度。
(3) 通孔台阶式用于型腔较深的或一模多腔的模具,以 及对于狭小的镶块不便使用螺钉紧固的模具。通孔无台阶式 用于镶块与支承板(或座板)直接用螺钉紧固的情况。
压铸工艺及模具设计
6.1.4 型芯的固定形式 型芯固定时,必须保持与相关构件
之间有足够的强度和稳定性,便于加工 和装卸,在金属液的冲击下或铸件卸除 包紧力时不发生位移、弹性变形和弯曲 断裂现象。型芯普遍采用台阶式固定 图6-4 型芯固定形式 方式。型芯靠台阶的支撑固定在镶块、滑块或动模套板内, 制造和装配比较简便,应用广泛。另外,台阶用座板压紧 后,适用于推板推出结构模具中的活动型心的使用,如图 6-4所示。
第7章 压铸模成形零件设计13spring1
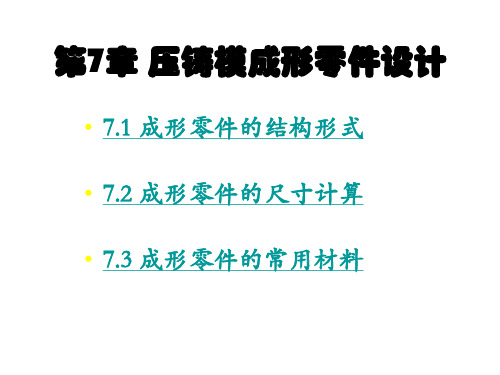
式中Cm—模具上型腔或型芯的中心距尺寸; Cz—压铸件凸台或凹槽的中心距尺寸。
• 4.模内中心线到某一成形面的尺寸 • 在设计成形零部件时,经常会遇到模具上凸台或凹槽 的一些局部成形结构的中心线到某一成形面的距离尺 寸。 • (1)凹槽或型芯中心线到凹模侧壁的尺寸 模具上成 形零件的凹槽或型芯中心线到凹模侧壁的尺寸
3、组合(镶拼)式结构的应用
型腔较深或较大型的模具; 多型腔模具; 成型表面比较复杂的模具。
4、组合式结构的设计要点
1、便于机械加工,以保证压铸件的尺寸精度和组合 部分的配合精度。
直角较深的型腔
两端小、中间大的半圆形型腔
异形圆弧形型腔
环形套内的球体镶块
C型深腔局部镶块
2、保证镶块和型芯的强度以及提高镶块、 型芯与模块间相对位置的稳定性。
一、压铸件的收缩率
(一)实际收缩率 压铸件的实际收缩率φ实是指室温时的模具成型尺 寸减去压铸件实际尺寸与模具成型尺寸之比,即:
式中 A型—室温下模具的成型尺寸(mm)
A实—室温下压铸件的实际尺寸(mm)
(二)计算收缩率
设计模具时,计算成型零件所采用的收缩率
为计算收缩率φ,它包括了压铸件收缩值和成型零
通孔套板台阶固定形式
通孔套板时镶块固定形式
1. 套板 2. 镶块 4. 导套
(2)通孔套板无台阶式固定形式
通孔套板无台阶形式
• 整体组合式型芯的基本结构和固定形式
• 7.1.3 局部组合式结构
• 型腔或型芯由整块材料制成,局部镶有成形镶块。
局部组合式型腔的结构。多用于局部形状较为复杂, 整体加工较为困难的场合。
局部组合式型芯的结构形式
• 7.1.4 完全组合式结构 • 1.模套组合式
- 1、下载文档前请自行甄别文档内容的完整性,平台不提供额外的编辑、内容补充、找答案等附加服务。
- 2、"仅部分预览"的文档,不可在线预览部分如存在完整性等问题,可反馈申请退款(可完整预览的文档不适用该条件!)。
- 3、如文档侵犯您的权益,请联系客服反馈,我们会尽快为您处理(人工客服工作时间:9:00-18:30)。
(一)主型芯的结构及固定形式 • 图7-6
(二)小型芯的结构及固定形式 • 图7-7,图7-8。
(二)小型芯的结构及固定形式
六、镶块和型芯的止转形式。
七、镶块和型芯的结构尺寸
(一)镶块壁厚尺寸
(二)整体镶块台阶尺寸
表7-8 整体镶块台阶尺寸推荐值
(三)组合式成型镶块固定部分长度
• 表7-9 组合式成型镶块固定部分长度推荐值
铸件实际尺寸的差与模具成型尺寸之比。即:
• A型-----室温下模具的成型尺寸(mm), • A实-----室温下压铸件的实际尺寸(mm)。
一、压铸件的收缩率 • (二)计算收缩率
• A’-----计算得到的模具成型零件的尺寸(mm), • A-----压铸件的公称尺寸(mm)。
常用压铸合金的计算收缩率腔尺寸(包括型腔深度尺寸) ②型芯尺寸(包括型芯高度尺寸)
③成型部分的中心距离和位置尺寸
(一)成型尺寸的分类及计算要点
成型尺寸计算的要点: • 因型腔磨损后尺寸增大,故计算型腔尺寸时应使得压
铸件外形接近于最小极限尺寸。
• 因型芯磨损后尺寸减小,故计算型腔尺寸时应使得压
铸件内形接近于最大极限尺寸。
• 1.壳体压铸件的成型尺寸分类
压铸件的①、②、③属于型腔尺寸;④、⑤、⑥属于 型芯尺寸;⑦、⑧属于中心距离、位置尺寸。另外, ②、⑤受到分型面的影响,高压、高速的金属液充填 型腔时,闭合的动、定模会出现微小的分离倾向,使 与分型面有关的尺寸略微增大。为消除这种影响,通 常将计算所得的公称尺寸减去0.05mm。
第七章 成型零件和模架设计(P118)
• 成型零件是构成型腔以形成压铸件形状的零件。通常 浇注系统、溢流和排气系统也在成型零件上加工而成。 成型零件的结构、尺寸和质量直接影响着压铸件的精 度、质量和模型的寿命。
• 成型零件主要指型芯和镶块
§1. 成型零件的结构及分类
• 成型零件的结构形式分为:整体式和镶拼式 。
(三)中心距离、位置尺寸的计算
• 压铸件的中心距离、位置尺寸采用双向等值正、负偏 差,公称尺寸为平均值;与之相应的模具中心距尺寸 也采用双向等值正、负偏差,公称尺寸为平均值。
(四) 制造偏差的选取
型腔和型芯尺寸的制造偏差△’按下列规定选取: • 当压铸件尺寸精度为IT11~IT13时, △’取△ /5。 • 当压铸件尺寸精度为IT14~IT16时, △’取△ /4。
一、整体式结构
二、镶拼式结构
三、镶拼式结构的设计要点
1、便于机加工,以保证成型部位的尺寸精度和组合部位的配合精度。 其结构形式:
2、保证镶块和型芯的强度及提高镶块、型芯与模块间相 对位置的稳定性。
3、镶块及型芯不应有锐角和薄壁,以防止镶块及型芯在 热处理及压铸生产时产生变形和裂纹。
4、镶拼间隙处产生的飞边方向应与脱模方向一致。
(四) 圆型芯结构尺寸 • 圆型芯尺寸推荐值见表7-10。
八、型腔镶块在分型面上的布置形式
• (一)卧式冷室压铸机用模具型腔镶块的布置形式。 见图7-10。
八、型腔镶块在分型面上的布置形式
• (一)卧式冷室压铸机用模具型腔镶块的布置形式。
八、型腔镶块在分型面上的布置形式
• (二)热室或立式冷室压铸机用模具型腔镶块的布置形式。
压铸件的中心距离、位置尺寸的制造偏差△’按下列规 定
选取: • 当压铸件尺寸精度为IT11~IT13时, △’取△ /5。 • 当压铸件尺寸精度为IT14~IT16时, △’取△ /4。
• 成型尺寸计算举例
• 壳体压铸件如图所示。取Ⅰ-Ⅰ为分型面,采用扩张 式外侧浇口,型腔设在定模镶块内。壳体材料为压铸 铝合金Y102,查表7-11(P110),选定平均 计算收缩率为0.6%。
孔两种。
四、 镶块的固定形式
• 图7-3.盲孔套板镶块的固定形式。
四、 镶块的固定形式
• 通孔套板分为:通孔台阶式和通孔无台阶式两种。
四、 镶块的固定形式
五、型芯的结构及固定形式 • 成型压铸件内形的零件-----型芯。 • 成型压铸件整体内形的零件-----主型芯。 • 成型压铸件局部内形的零件-----小型芯。
八、型腔镶块在分型面上的布置形式
(二)热室或立式冷室压铸机用模具型腔镶块的布置形 式。见图7-11。
§2. 成型零件成型尺寸的计算
成型部分的尺寸和精度是保证压铸件尺寸和精度的主要因素。当零 件结构与模具结构确定后,影响压铸件尺寸精度的主要因素有: ① 成型零件的制造精度; ② 设计压铸模时,合金计算收缩与实际收缩率的差异; ③ 压铸模在使用过程中的磨损,使得同一模型在新和旧的时候所生
• 两个型芯或型腔之间的中心距离和位置尺寸与磨损无
关,故应使其尺寸接近于最大和最小两个极限尺寸的 平均值。
(二)成型尺寸标注形式及偏差分布的规定
• 压铸件的外形尺寸采用单向负偏差,公称尺寸为最大 值;与之相应的型腔尺寸采用单向正偏差,公称尺寸 为最小值。
(二)成型尺寸标注形式及偏差分布的规定
• 压铸件的内形尺寸采用单向正偏差,公称尺寸为最小 值;与之相应的型芯尺寸采用单向负偏差,公称尺寸 为最大值。
5、镶块和型芯的个别凸凹易损部分、圆弧部分以及局部尺寸精度
要求高的成型零件,受金属液直接冲击的部位,应设计成单独的 镶块以便能用时更换和维修。
6、不影响压铸件的外观,便于去除飞边。
四、 镶块的固定形式
• 镶块固定时必须保持与相关的零件有足够的稳定性, 还要求便于加工和装卸。
• 镶块通常安装在模具的套板内。套板分为:通孔和盲
产的制品各不相同; ④分型面对压铸件的影响; ⑤压铸工艺和生产操作; ⑥ 压铸机性能影响等。 • 只有当所有这些累积误差在压铸件规定公差范围内时才能生产出
合格的压铸件。因此确定成型部分尺寸时要全面考虑影响压铸件 尺寸的因素,使计算时假设条件尽量接近实际情况。
一、压铸件的收缩率 • (一)实际收缩率 • 压铸件的实际收缩率----是指室温下模具成型尺寸与压
(三)收缩率的确定
一般规律: • 压铸件结构复杂,型芯多,收缩受阻大时,收缩率较
小;反之,收缩率较大。 • 薄壁件的收缩率较小;厚壁件收缩率较大。 • 压铸件出模温度越高,则收缩率越大,反之则小。 • 靠近浇道处型腔温度高,此处的收缩率较大。
三、成型零件尺寸的分类、计算要点及标注形式
• 成型零件中直接决定压铸件几何形状的尺寸---成型尺寸。 (一)成型尺寸的分类及计算要点