FMEA 分析模板
1-1 FMEA新版模板(AIAG-VDA R1)
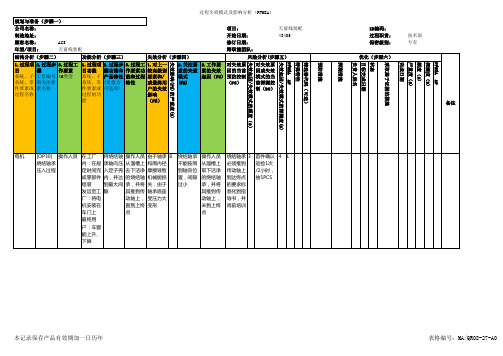
失效分析(步骤四)
风险分析(步骤五)
1.过程项 2.过程步 3.过程工
目
骤
作要素
系统,子 工位编号 4M类型
系统,零 和关注要
件要素或 素名称
过程名称
1.过程项 2.过程步 3.过程工 1.对上一
目功能 骤功能和 作要素功 较高级别
系统、子 产品特性 能和过程 要素和/
系统、零 (量值为 特性
或最终用
年型/项目:
天窗线装配
跨职能团队:
结构分析(步骤二)
功能分析(步骤三)
失效分析(步骤四)
风险分析(步骤五)
1.过程项 2.过程步 3.过程工
目
骤
作要素
系统,子 工位编号 4M类型
系统,零 和关注要
件要素或 素名称
过程名称
1.过程项 2.过程步 3.过程工 1.对上一
目功能 骤功能和 作要素功 较高级别
失效起因/失效模式的频度(O)
失效影响(FE)的严重度(S)
ID编码: 过程职责: 保密级别:
优化(步骤六)
技术部 专有
备注
本记录保存产品有效期加一日历年
表格编号:MA/QR08-27-A0
过程失效模式及影响分析(PFMEA)
规划与准备(步骤一)
公司名称:
项目:
天窗线装配
制造地址:
开始日期:
43405
影响
能
(FE)
2.关注要 3.工作要 对失效原
素的失效 素的失效 因的当前
模式
起因(FC) 预防控制
(FM)
(PC)
对失效原 因或失效 模式的当 前探测控 制(DC)
ID编码: 过程职责: 保密级别:
FMEA(精典范例)

5.4 “潜在失效后果的严重度(S)”、“潜在失效起因/机理的频度(O)”、“现行设计(过程)控制的探测度(D)”三者 均用1-10的计分方式为评分标准,其评价标准详见附表1、附表2的评价准则;
“风险顺序数(RPN=S×O×D)”,项目小组进行FMEA活动时,对RPN值>80(顾客另有要求时按其要求)或S值>7时的失效模 式及后果优先采取纠正措施,并在采取措施栏内记入改善的状况并记入新的RPN值。
产品开发(APQP)过程
《潜在失效模式及后果分析》参考手册
3. 术语和定义
3.1潜在失效模式及后果分析(FMEA):
在产品的设计阶段和过程设计阶段,对构成产品的子系统、零件、对构成过程的各道工序逐一进行分析,找出所有潜在的 失效模式,并分析其可能的后果,从而预先采取必要的措施,以提高产品的质量和可靠性的一种系统化的活动。
并执行。
研发部项目组
项目小组对改进措施的有效性进行确认,并进行标准 化,纳入相应的文件中予以执行。
及时更新FMEA
质量部
1.当有顾客投诉时由质量部通知研发项目组修改 FMEA资料。2.新设备、过程变更、工程更改、过程 能力不稳定或能力不足(Cpk≤1.33)时由项目负责 人更新FMEA资料。
5.3 FMEA的制作 5.3.1 FMEA制作必须具备以下资料: 5.3.1.1 DFMEA必须的资料: a) 明确设计要求 b) 产品可靠性和质量目标 d) 产品的功能、使用环境 e) 类似产品的失效分析(FMA);以往类似产品的DFMEA f) 初始工程标准 g) 初始特殊特性明细表 h) 系统方框分析图、设计草图等 5.3.1.2 PFMEA必须的资料: a) 过程流程图、过程特殊特性矩阵图 b) 风险评估分析
fmea及对应控制计划的模板

fmea及对应控制计划的模板FMEA(Failure Mode and Effects Analysis)是一种用于识别和评估潜在故障模式及其对系统性能和安全性的影响的方法。
对应的控制计划是为了降低或消除潜在故障模式的风险而制定的一系列控制措施。
下面是一个常见的FMEA及对应控制计划的模板,供参考:1. FMEA模板:- 故障模式(Failure Mode):列出可能的故障模式。
- 故障原因(Failure Cause):对每个故障模式列出可能的原因。
- 故障影响(Failure Effect):描述每个故障模式对系统性能和安全性的影响。
- 严重度(Severity):评估每个故障模式的严重程度,通常使用1-10的评分,10表示最严重。
- 发现性(Detection):评估当前探测到故障模式的能力,通常使用1-10的评分,10表示最容易发现。
- 发生性(Occurrence):评估每个故障模式发生的可能性,通常使用1-10的评分,10表示最容易发生。
- RPN(Risk Priority Number):根据严重度、发现性和发生性计算出的风险优先级数值,用于确定优先处理的故障模式。
2. 对应控制计划模板:- 控制措施(Control Measures):针对每个故障模式,列出相应的控制措施,以降低或消除风险。
- 负责人(Responsible):指定负责实施和监督控制措施的人员。
- 实施期限(Implementation Deadline):规定控制措施的实施期限。
- 实施状态(Implementation Status):记录控制措施的实施状态,例如已实施、正在实施或未实施。
- 效果验证(Effectiveness Verification):评估控制措施的有效性,可以记录验证方法和结果。
举例说明:假设我们正在开发一款电子产品,其中一个潜在的故障模式是电池过热。
故障原因可能是电池过充、电路设计问题或温度过高等。
fmea格式 (2)
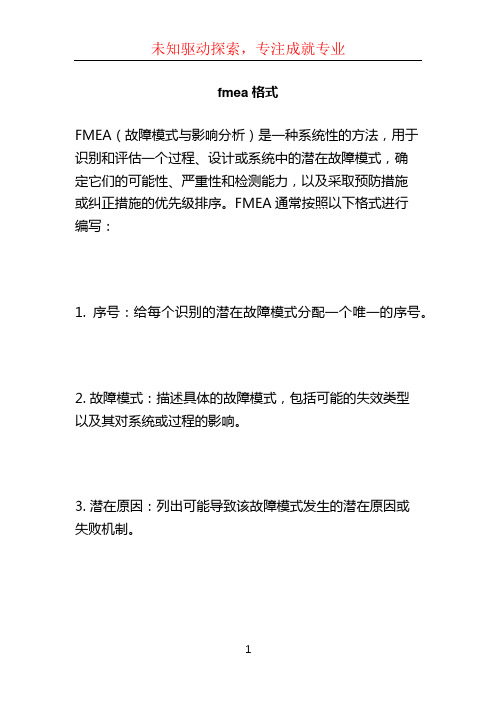
fmea格式
FMEA(故障模式与影响分析)是一种系统性的方法,用于识别和评估一个过程、设计或系统中的潜在故障模式,确
定它们的可能性、严重性和检测能力,以及采取预防措施
或纠正措施的优先级排序。
FMEA通常按照以下格式进行
编写:
1. 序号:给每个识别的潜在故障模式分配一个唯一的序号。
2. 故障模式:描述具体的故障模式,包括可能的失效类型
以及其对系统或过程的影响。
3. 潜在原因:列出可能导致该故障模式发生的潜在原因或
失败机制。
4. 后果:描述故障模式对系统、过程或产品的可能影响,包括质量、安全和可靠性方面的损失。
5. 严重性:根据影响的严重程度,对故障模式进行分级,通常使用一个1-10的数值等级。
6. 可能性:对故障模式发生的可能性进行评估,通常使用一个1-10的数值等级。
7. 检测能力:评估系统中的控制措施或设计特性是否可以及时检测该故障模式的发生。
8. 现有控制:列出已经存在的预防控制措施或设计特性,防止或减轻故障模式的发生。
9. 推荐控制:根据严重性、可能性以及检测能力的评估,推荐采取的纠正措施或改进措施。
10. 负责人:指定负责执行推荐控制措施的责任人。
11. 优先级:根据严重性、可能性和检测能力的评估,对推荐控制措施进行优先级排序。
这个格式是常见的FMEA表格的一种示例,具体的表格格式可以根据需求进行调整和定制。
FMEA 模板

产品名称:法兰盘过程责任部门:技术部、生产部,质量部FMEA编号:04-006 Part Name: Process Responsibility: Technical Dept., Production Dept. FMEA No: 04 –006产品图号:RC66218 关键日期: 页次1of 5Part No. Key Date: Pages: 1of5主要参加人:Team:编制:编制日期:修订日期:Prepared by: Date (Orig.) Date (Rev.)产品名称:法兰盘过程责任部门:技术部、生产部,质量部FMEA编号:04-006 Part Name: Process Responsibility: Technical Dept., Production Dept. FMEA No: 04 –006产品图号:RC66218 关键日期: 页次1of 5Part No. Key Date: Pages: 1of5主要参加人:Team:编制:编制日期:修订日期:Prepared by: Date (Orig.) Date (Rev.)产品名称:法兰盘过程责任部门:技术部、生产部,质量部FMEA编号:04-006 Part Name: Process Responsibility: Technical Dept., Production Dept. FMEA No: 04 –006产品图号:RC66218 关键日期: 页次1of 5Part No. Key Date: Pages: 1of5主要参加人:Team:编制:编制日期:修订日期:Prepared by: Date (Orig.) Date (Rev.)产品名称:法兰盘过程责任部门:技术部、生产部,质量部FMEA编号:04-006 Part Name: Process Responsibility: Technical Dept., Production Dept. FMEA No: 04 –006产品图号:RC66218 关键日期: 页次1of 5Part No. Key Date: Pages: 1of5主要参加人:Team:编制:编制日期:修订日期:Prepared by: Date (Orig.) Date (Rev.)产品名称: 法兰盘 过程责任部门: 技术部、生产部,质量部 FMEA 编号: 04-006Process Responsibility: Technical Dept., Production Dept. FMEA No: 04 –006 RC66218 关键日期: 页 次 1 of 5 Key Date: Pages: 1 of 5编制日期: 修订日期: Prepared by: Date (Orig.) Date (Rev.)。
FMEA标准模板

严 重 度 S
潜在失效起因/机理 级别 Origin/Mechanism of Class Potential Failure
频 度 O
探 现行预防过 现行探测过程 测 度 程控制 控制 D
措施执行结果 Executive Results of Actions R O N 建议措施 Recommended Actions 责任和目标完 成日期 Responsibility & Target Date 严 重 度 S 探 测 度 D
7
★
Molding process or mold dim. Or mould temp.
1
IPQC
Dim 2, 3, 4 are controlled during process
3
21
PM mould, check molding Xu Zhenglin parameter /Amelia regularly
3
o
Wrong insert/嵌入错误
1
Order start release Dim check/尺 plan/订单开 寸确认 始出计划
2
6
PM mould /点检 磨具
Production supervisor, WW26/生产主 管
Review PM mould personnel instruction, incoming inspection optical inserts/人员回顾 作业指导,来料检验光学 尺寸
2
PM mould, check molding Xu Zhenglin 60 parameter /Amelia regularly PM mould, check molding Xu Zhenglin 60 parameter /Amelia regularly PM mould, QC check molding 60 parameter regularly Xu Zhenglin /Amelia
fmea报告模板范例
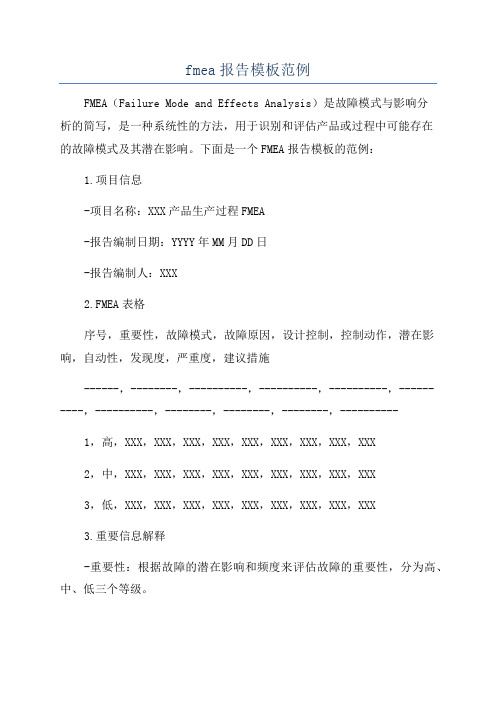
fmea报告模板范例FMEA(Failure Mode and Effects Analysis)是故障模式与影响分析的简写,是一种系统性的方法,用于识别和评估产品或过程中可能存在的故障模式及其潜在影响。
下面是一个FMEA报告模板的范例:1.项目信息-项目名称:XXX产品生产过程FMEA-报告编制日期:YYYY年MM月DD日-报告编制人:XXX2.FMEA表格序号,重要性,故障模式,故障原因,设计控制,控制动作,潜在影响,自动性,发现度,严重度,建议措施------,--------,----------,----------,----------,----------,----------,--------,--------,--------,----------1,高,XXX,XXX,XXX,XXX,XXX,XXX,XXX,XXX,XXX2,中,XXX,XXX,XXX,XXX,XXX,XXX,XXX,XXX,XXX3,低,XXX,XXX,XXX,XXX,XXX,XXX,XXX,XXX,XXX3.重要信息解释-重要性:根据故障的潜在影响和频度来评估故障的重要性,分为高、中、低三个等级。
-故障模式:记录故障出现的模式或类型,例如机器停机、设备损坏等。
-故障原因:识别导致故障的根本原因,例如零部件磨损、操作错误等。
-设计控制:标记故障模式是否由设计决策引起。
-控制动作:记录已经或将要采取的控制措施来减少或消除故障模式。
-潜在影响:分析故障可能带来的影响,如生产延误、产品质量下降等。
-自动性:描述人工检查效果,区分人工检查的故障发现自动性高低。
-发现度:根据控制措施可能发现的故障数量进行评估。
-严重度:根据故障带来的影响评估故障的严重性,分为高、中、低三个等级。
-建议措施:记录针对每个故障模式采取的应对措施和改进建议。
4.分析结果总结-根据FMEA表格中的评估和分析,我们可以得出以下结论:-高重要性的故障模式需要优先处理,并采取相应措施进行风险控制。
FMEA表格讲解【范本模板】
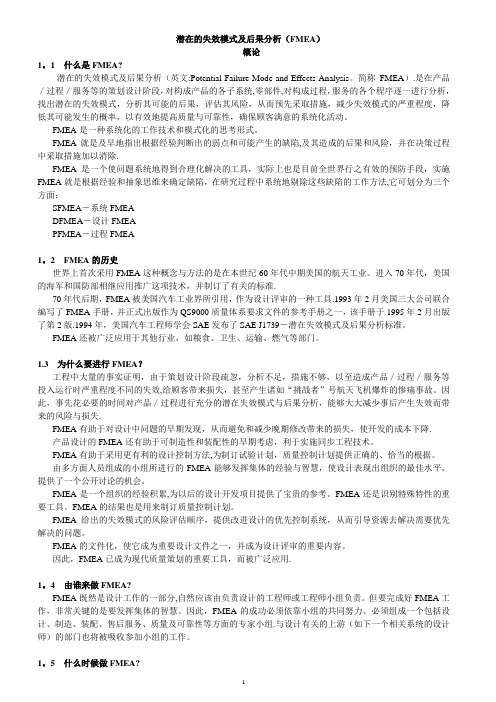
潜在的失效模式及后果分析(FMEA)概论1。
1 什么是FMEA?潜在的失效模式及后果分析(英文:Potential Failure Mode and Effects Analysis。
简称FMEA).是在产品/过程/服务等的策划设计阶段,对构成产品的各子系统,零部件,对构成过程,服务的各个程序逐一进行分析,找出潜在的失效模式,分析其可能的后果,评估其风险,从而预先采取措施,减少失效模式的严重程度,降低其可能发生的概率,以有效地提高质量与可靠性,确保顾客满意的系统化活动。
FMEA是一种系统化的工作技术和模式化的思考形式。
FMEA就是及早地指出根据经验判断出的弱点和可能产生的缺陷,及其造成的后果和风险,并在决策过程中采取措施加以消除.FMEA是一个使问题系统地得到合理化解决的工具,实际上也是目前全世界行之有效的预防手段,实施FMEA就是根据经验和抽象思维来确定缺陷,在研究过程中系统地剔除这些缺陷的工作方法,它可划分为三个方面:SFMEA-系统FMEADFMEA-设计FMEAPFMEA-过程FMEA1。
2 FMEA的历史世界上首次采用FMEA这种概念与方法的是在本世纪60年代中期美国的航天工业。
进入70年代,美国的海军和国防部相继应用推广这项技术,并制订了有关的标准.70年代后期,FMEA被美国汽车工业界所引用,作为设计评审的一种工具.1993年2月美国三大公司联合编写了FMEA手册,并正式出版作为QS9000质量体系要求文件的参考手册之一,该手册于1995年2月出版了第2版.1994年,美国汽车工程师学会SAE发布了SAE J1739-潜在失效模式及后果分析标准。
FMEA还被广泛应用于其他行业,如粮食、卫生、运输、燃气等部门。
1.3 为什么要进行FMEA?工程中大量的事实证明,由于策划设计阶段疏忽,分析不足,措施不够,以至造成产品/过程/服务等投入运行时严重程度不同的失效,给顾客带来损失,甚至产生诸如“挑战者”号航天飞机爆炸的惨痛事故。
- 1、下载文档前请自行甄别文档内容的完整性,平台不提供额外的编辑、内容补充、找答案等附加服务。
- 2、"仅部分预览"的文档,不可在线预览部分如存在完整性等问题,可反馈申请退款(可完整预览的文档不适用该条件!)。
- 3、如文档侵犯您的权益,请联系客服反馈,我们会尽快为您处理(人工客服工作时间:9:00-18:30)。
和产品特性
系统、子系统 工序号和关 (人、机、料-非直 (厂内、至外厂、
、产品单元, 注要素名称 接、环,等等) 过程步骤、车辆用 (可用量化数据)
或过程名称
户,如果信息可获
取的话) 过程:按控制信号
转化电能为机械
能;
厂内:在周期时间
内装配,无报废和 在电机壳里压入球
玻璃升降电机 总成
OP# 30 压 入球面轴承
制;
用户:升降车窗玻
璃
过程失效模式及影响分析 - PFMEA
PFMEA项目名称 PFMEA开始日期 最新修订日期 小组名单
:功能分析
3. 作业要素的功 能和过程特性
1. 失效影响 (FE)
(厂内、至外厂、过程步骤、 车辆用户,如果信息可获取的
话)
步骤4:失效分析
2. 过程步骤的失效模式 (FM)
3. 作业要素的失效原因 (FC)
据
进行 中
更新严重度 (S) 更新发生度 (O) 更新探测度 (D) 更新DFMEA AP
备注
持续改进
历史/变更授权 (如适用)
至外厂:无;
用户:车窗玻璃升降困难 (7)
手册(草案)中例子不清晰
8
轴承轴向位置没有达 到,间距过小
压机在还没压到位就停止 了(压力太小)
- PFMEA
PFMEA编号: 按公司内部规定 过程负责人: 即PFMEA负责人
保密等级: 例如:对外/机密/内部使用
当前针对FC的 预防性控制措施
(PC)
步骤5:PFMEA 风险分析
过程:机械能损失,因为球面
轴承与转子间摩擦过大,球面
作业员从料箱拿取 正确型号的清洁的 球面轴承,并放到 压机的上止位
轴承与轴承座过紧使得球面轴 承内尺寸变形(8); 厂内:由于间距小,转子装配 困难(报废)(7),周期时)
8
轴承轴向位置没有达 到,间距过小
步骤1:范围定义
公司名称: 负责PFMEA的公司 工厂地点: 地理位置 顾客名称: 顾客名或过程族名称 车型年/平台: 顾客车型年型/平台/款型
任务描述: PFMEA开始日期: PFMEA修订日期:
跨职能小组:
Issue #
步骤2:结构分析
步骤3:功能分析
1. 过程 2. 过程步骤 3. 作业要素
1. 过程功能 2. 过程步骤的功能
到车门不会出现停 围内
线/停顿、拣选、遏
制;
用户:升降车窗玻
璃过程:按控制信号
转化电能为机械
能;
厂内:在周期时间
内装配,无报废和 在电机壳里压入球
玻璃升降电机 总成
OP# 30 压 入球面轴承
机器(压机)
返工;
面轴承,轴向位置
至外厂:电机安装 在图纸公差允许范
到车门不会出现停 围内
线/停顿、拣选、遏
无
10
轴承与电机座的间 距,用绿色和红色记
3
H CC
使用掉到地 上的轴承,
号笔标记OK/NOK
并培训相关
件,再由作业员筛选
人员
。
批次放行要求
(100%有效),检
料箱门根据轴承 型号自动打开; 作业指导书;作 业员培训
验员用检具检查球面 轴承与电机座的间 1 距,用绿色和红色记 号笔标记OK/NOK 件,再由作业员筛选
作业员拿了错误型号的轴 承
间距过小的程度可能是不一样的,这样 的话,对应的影响、发生度、探测度也
过程:机械能损失,因为球面
轴承与转子间摩擦过大,球面
轴承与轴承座过紧使得球面轴
压机把球面轴承压 承内尺寸变形(8);
入电机壳至规定的 厂内:由于间距小,转子装配
轴向位置
困难(报废)(7),周期时间超
时(7);
作业员
返工;
面轴承,轴向位置
至外厂:电机安装 在图纸公差允许范
到车门不会出现停 围内
线/停顿、拣选、遏
制;
用户:升降车窗玻
璃过程:按控制信号
转化电能为机械
能;
厂内:在周期时间
内装配,无报废和 在电机壳里压入球
玻璃升降电机 总成
OP# 30 压 入球面轴承
作业员
返工;
面轴承,轴向位置
至外厂:电机安装 在图纸公差允许范
当前针对FC或FM的 探测性控制措施 (DC)
PFMEA预 PFMEA 责任
防性行动措 探测性 人
施
行动措
施
步骤6:优化
期限
FC发生度 (O) FC/FM 探测度
(D) PFMEA AP (行
动优先级) 特殊特性 过滤代码 (可选)
批次放行要求
(100%有效),检
作业指导书
验员用检具检查球面
规定不允许
1
L
。
无法继续装配
批次放行要求
(100%有效),检
使用带有压力和 位置传感器的压
机
3
验员用检具检查球面 轴承与电机座的间
距,用绿色和红色记 号笔标记OK/NOK
3
L
件,再由作业员筛选
。
John Doe (生产 工程 师)
步骤6:优化
状态 采取 完成
(进 的措 日期
行中/ 施和
完成/ 取
消)
降低 分值 的证
FE严重度 (S)
过程:机械能损失,因为球面
作业员从料箱拿取 正确型号的清洁的 球面轴承,并放到 压机的上止位
轴承与转子间摩擦过大,球面 轴承与轴承座过紧使得球面轴 承内尺寸变形(8); 厂内:无 至外厂:无;
用户:车窗玻璃升降困难 (7)
8
轴承轴向位置没有达 到,间距过小
作业员使用之前掉到过地 上的轴承(轴承上有异 物)