关于PCB钻孔的综述
PCB雷射钻孔技术介绍
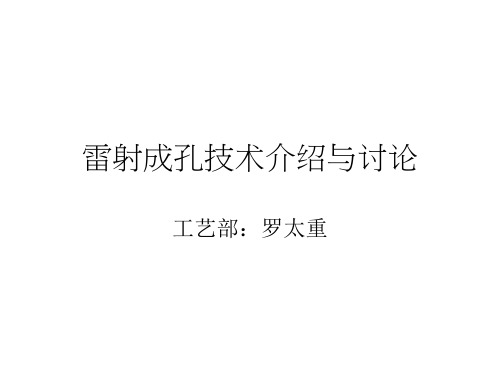
• 2.4
超薄铜皮直接烧穿法 内层核心板两面压贴背胶铜箔后,可采“半蚀法” (Half Etching)将其原来0.5OZ(17um)的铜皮咬薄 到只剩5um左右,然后再去做黑氧化层与直接成孔。 因在黑面强烈吸光与超薄铜层,以及提高CO2雷射的光 束能量下,将可如YAG雷射般直接穿铜与基材而成孔, 不过要做到良好的“半蚀”并不容易。於是已有铜箔业 者在此可观的商机下,提供特殊的“背铜式超薄铜皮” (如日本三井之可撕性UTC)。其做法是将UTC棱面压 贴在核心板外的两面胶层上,再撕掉厚支持用的“背铜 层‘,即可得到具有超薄铜皮(UTC)的HDI半成品。 随即在续做黑化的铜面上完成雷射盲孔,并还可洗耳恭 听掉黑化层进行PTH化铜与电铜。此法不但可直接完成 微孔,而且在细线制作方面,也因基铜之超薄而大幅提 升其良率,当然这种背铜式可撕性的UTC,其价格一定 不会便宜。
• 1. 雷射成孔的原理 雷射光是当:“射线”受到外来的刺激,而增大 能量下所激发的一种强力光束,其中红外光或可 见光者拥有热能,紫外光则另具有化学能。射到 工作物表面时会发生反射(Refliction)吸收 (Absorption)及穿透(Transmission)等三种 现象,其中只有被吸收者才会发生作用。而其对 板材所产生的作用又分为热与光化两种不同的反 应,现分述於
• 2. 二氧化碳CO2雷射成孔的不同制程 2.1 开铜窗法Conformal Mask 是在内层Core板上先压RCC然后开铜窗,再以雷射 光烧除窗内的基材即可完成微盲孔。详情是先做FR-4的 内层核心板,使其两面具有已黑化的线路与底垫 (Target Pad),然后再各压贴一张“背胶铜箔” (RCC)。此种RCC(Resin Coated Copper Foil)中 之铜箔为0.5 OZ,胶层厚约80~100um(3~4mil)。可 全做成B-stage,也可分别做成B-stage与C-stage等两 层。后者於压贴时其底垫上(Garget Pad)的介质层厚 度较易控制,但成本却较贵。然后利用CO2雷射光,根 据蚀铜底片的座标程式去烧掉窗内的要树脂,即可挖空 到底垫而成微盲孔。此法原为“日立制作所”的专利, 一般业者若要出货到日本市场时,可能要小心法律问题。
pcb 钻孔参数

pcb 钻孔参数PCB(Printed Circuit Board)钻孔参数是指在PCB制造过程中,钻孔的相关参数设置,包括钻孔直径、钻孔深度、钻孔位置等。
这些参数的合理设定对于保证PCB质量和性能至关重要。
钻孔直径是指钻孔的孔径大小。
在PCB制造中,钻孔直径通常由PCB设计要求确定。
根据不同的应用需求,钻孔直径可以有多种选择。
较小的钻孔直径适用于高密度元件布局,而较大的钻孔直径适用于较大尺寸元件的布局。
在钻孔直径选择时,需要考虑到元件引脚的直径、焊盘的尺寸等因素,以确保钻孔与元件引脚或焊盘的匹配度。
钻孔深度是指钻孔的深度。
钻孔深度的设定应根据PCB设计要求以及板材的厚度来确定。
一般来说,钻孔深度应略大于PCB板材的厚度,以确保在钻孔过程中不会损坏PCB板。
此外,还需要考虑到钻孔深度对后续工艺操作的影响,如插件焊接、贴片等。
钻孔的位置也是钻孔参数中的重要内容之一。
钻孔的位置信息由PCB设计师在设计过程中确定,并在制造过程中准确控制。
钻孔位置的准确性对于保证PCB元件的布局、引脚与焊盘的匹配度以及电路连接的可靠性非常关键。
在PCB制造过程中,通常使用CNC钻床进行钻孔操作,通过控制钻头的位置和移动轨迹,实现对钻孔位置的精确控制。
钻孔参数的合理设定对于保证PCB质量和性能至关重要。
合理选择钻孔直径、钻孔深度和钻孔位置,可以确保PCB板的结构强度、电气特性和可靠性。
过小的钻孔直径可能会导致焊盘质量下降、电气连接不可靠等问题;过大的钻孔直径可能会导致元件安装困难、布线不规整等问题。
钻孔深度不足可能导致元件插入不牢固,影响PCB的可靠性;钻孔深度过深则会增加制造成本,同时也可能对PCB板的结构性能造成不利影响。
钻孔位置的精确控制可以保证电路连接的可靠性,避免因钻孔位置偏差而导致的电路故障。
PCB钻孔参数的合理设定对于保证PCB的质量和性能至关重要。
钻孔直径、钻孔深度和钻孔位置的选择应根据PCB设计要求、元件的尺寸和布局以及制造工艺要求等因素进行综合考虑。
pcb背钻孔工艺流程

pcb背钻孔工艺流程
PCB背钻孔工艺流程是指在PCB板的背面钻孔的工艺流程,一般包括以下几个步骤:
1. 材料准备:准备好需要钻孔的PCB板和背钻孔用的钻头。
2. 设计钻孔布局:在PCB设计时,在背面的相应位置安排好需要钻孔的位置和大小。
3. 钻孔定位:使用精确的钻孔机来对PCB板进行定位。
可以使用自动对位系统或者人工对位。
4. 钻孔加工:将PCB板放置在钻孔机上,根据钻孔布局,使用钻头对PCB背面进行钻孔操作。
钻孔机可以是CNC钻孔机或者半自动钻孔机,根据生产需求选择。
5. 清洁处理:钻孔完成后,需要进行清洁处理,以便去除可能产生的残渣和污染物。
6. 检查质量:对钻孔的质量进行检查,包括孔径、孔壁平整度和孔位置偏差等。
7. 防腐处理:有些需要防腐的PCB板,在背部钻孔完成后,需要进行防腐处理,以防止氧化和腐蚀。
8. 清洁再检查:最后,对PCB板进行再次清洁和检查,确保钻孔工艺完成后的质量符合要求。
这是一个基本的PCB背钻孔工艺流程,具体的操作方法和设备选择还会因实际情况而有所不同。
PCB钻孔工艺详解

PCB板钻孔制程简介目的:了解钻孔制程及品质要求内容点:①PCB钻孔的作用②PCB钻孔板的品质缺陷及解决对策③钻孔品质及其鱼骨图分析④钻咀及相关辅料阐述⑤钻、锣带制作知识的介绍一、PCB钻孔的作用1、PCB板制作流程以双面板喷锡板工艺流程为例:开料→钻孔→沉铜→板电(加厚铜)→图形转移→电铜电锡→蚀刻退锡→检验→印阻焊→印字符→喷锡→成形→测试→成品检查→包装一、PCB钻孔的作用2、钻孔的作用钻孔就是在覆铜板上钻出所需的过孔。
PCB过孔按金属化与否,分为a、电镀孔( PTH ),也叫金属化孔b、非电镀孔(NPTH),也叫非金属化孔按工艺制程分为a、盲孔(多层板)b、埋孔(多层板)c、通孔过孔主要提供电气连接与用作器件的固定或定位的作用。
二、PCB钻孔板的品质缺陷及解决对策二、PCB钻孔板的品质缺陷及解决对策二、PCB钻孔板的品质缺陷及解决对策二、PCB钻孔板的品质缺陷及解决对策二、PCB钻孔板的品质缺陷及解决对策偏孔:二、PCB钻孔板的品质缺陷及解决对策二、PCB钻孔板的品质缺陷及解决对策三、钻孔品质及其鱼骨图分析1、钻孔的品质要求孔径:+0/-1mil孔位:≤2mil孔壁粗糙度:≤1mil钉头:≤1.5三、钻孔品质及其鱼骨图分析2、钻孔品质鱼骨分析图四、钻咀及相关辅料阐述1、钻咀ST型钻咀(用于普通FR-4、CEM-3板及环保板加工)四、钻咀及相关辅料阐述UC型钻咀(具有耐磨性能好、排尘能力强、孔壁质量好、孔位精度高。
适用于一般板材加工,尤其适合高Tg、环保板等硬度较高板材的加工)四、钻咀及相关辅料阐述2、盖板PCB钻孔用盖板的要求是:有一定表面硬度防止钻孔上表面毛刺,但又不能太硬而磨损钻头。
常用的有:a.铝箔b.酚醛纸胶盖板c.环氧玻璃布盖板3、垫板要求垫板本身树脂成分不能过高,否则钻孔时将会形成熔融的脂球黏附在孔壁。
常用的有:a.普通纸质垫板b.高密度纸质垫板c.酚醛垫板五、钻锣带制作知识的介绍1、钻孔档(Drill File)介绍a.常见格式:Exel系S&m系b.坐标格式LEADING ZERO 省前0补后0 例:12.3→12300TRAILING ZERO 补前0省后0 例:12.3→0123NONE ZERO 前后0补齐例:12.3→012300 五、钻锣带制作知识的介绍●Exel系格式钻带●M48●T1C0.125●T2C0.028●T3C0.035●T4C0.0394●T5C0.04●T6C0.0433●%●T1●X0Y114222●X0025Y114222●X06417Y114722●X12584Y114222●X12834Y114222●X12834Y-002●X12584Y-002●X06417Y-0025●X005Y-002●X0025Y-002●X0Y-002●T2●X0311Y00788●X03425Y00788●X02913Y00788●X01575Y00406●X07008Y0317●M30五、钻锣带制作知识的介绍●S&m系格式钻带●X-5.Y-7.5T01●XY-7.5●X293.Y-7.5●X-5.Y246.5●X293.Y246.5M30●X5.58Y-36T02M31●X3.53Y2.81●X133.85Y-2.08●XYM50●X.01Y62.M50●X.03Y124.07M50●X.04Y186.09M50●X149.18Y186.07M50●X149.21Y124.04M50●X149.19Y62.01M50●X149.2Y-.04M50M30●X10.Y-7.5M30●X16.01Y3.3T04M31●X61.67Y3.28●X76.95Y3.28●XYM50●X.01Y62.M50●X.03Y124.07M50●X.04Y186.09M50●X149.18Y186.07M50●X149.21Y124.04M50●X149.19Y62.01M50●X149.2Y-.04M50M30●X20.Y-7.5M30五、钻锣带制作知识的介绍c.单位制公制(METRIC) mm英制(ENGLISH) inch or mild.单位换算1 inch=1000 mil=2.54 cm=25.4 mm1 mm=0.03937inch=39.37 mil五、钻锣带制作知识的介绍2、钻(锣)带文件头介绍(以常用的EXEL格式为例)一般以M48 开头,排列在钻孔文件的前面,以%结束。
pcb激光钻孔标准
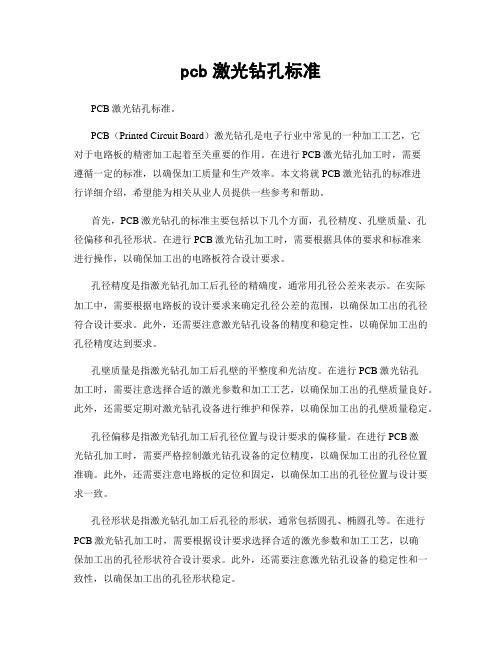
pcb激光钻孔标准PCB激光钻孔标准。
PCB(Printed Circuit Board)激光钻孔是电子行业中常见的一种加工工艺,它对于电路板的精密加工起着至关重要的作用。
在进行PCB激光钻孔加工时,需要遵循一定的标准,以确保加工质量和生产效率。
本文将就PCB激光钻孔的标准进行详细介绍,希望能为相关从业人员提供一些参考和帮助。
首先,PCB激光钻孔的标准主要包括以下几个方面,孔径精度、孔壁质量、孔径偏移和孔径形状。
在进行PCB激光钻孔加工时,需要根据具体的要求和标准来进行操作,以确保加工出的电路板符合设计要求。
孔径精度是指激光钻孔加工后孔径的精确度,通常用孔径公差来表示。
在实际加工中,需要根据电路板的设计要求来确定孔径公差的范围,以确保加工出的孔径符合设计要求。
此外,还需要注意激光钻孔设备的精度和稳定性,以确保加工出的孔径精度达到要求。
孔壁质量是指激光钻孔加工后孔壁的平整度和光洁度。
在进行PCB激光钻孔加工时,需要注意选择合适的激光参数和加工工艺,以确保加工出的孔壁质量良好。
此外,还需要定期对激光钻孔设备进行维护和保养,以确保加工出的孔壁质量稳定。
孔径偏移是指激光钻孔加工后孔径位置与设计要求的偏移量。
在进行PCB激光钻孔加工时,需要严格控制激光钻孔设备的定位精度,以确保加工出的孔径位置准确。
此外,还需要注意电路板的定位和固定,以确保加工出的孔径位置与设计要求一致。
孔径形状是指激光钻孔加工后孔径的形状,通常包括圆孔、椭圆孔等。
在进行PCB激光钻孔加工时,需要根据设计要求选择合适的激光参数和加工工艺,以确保加工出的孔径形状符合设计要求。
此外,还需要注意激光钻孔设备的稳定性和一致性,以确保加工出的孔径形状稳定。
总之,PCB激光钻孔标准对于电路板的加工质量和生产效率起着至关重要的作用。
在进行PCB激光钻孔加工时,需要严格遵循相关标准和要求,以确保加工出的电路板符合设计要求。
希望本文能为相关从业人员提供一些参考和帮助,让他们能够更好地掌握PCB激光钻孔的标准和技术要点。
PCB制造工艺综述

PCB制造工艺综述PCB即印制电路板,是电子电路、机械设备中必备的一部分。
它是一种单面或双面的面板,通常是由有机材料或玻璃纤维纸板等制成,在表面附着有一层铜质电极,它是电路连接器的基础。
PCB制造是一项非常重要的任务,因为它是电子设备的核心部分之一。
PCB制造工艺的关键是设计和制造过程的精确性,因此在制造前需要进行一系列的测试和调试,以确保最终制造出的PCB满足产品的需求。
下面就介绍一下常见的PCB制造工艺:一、设计阶段PCB制造的第一步是设计。
在电路板上标记电子器件的布局和连接方式,使用设计软件绘制电路板原型,然后将其转换成硬件图像。
设计人员需要仔细研究电路用途、区分不同信号类型和分析电路性能,以便使得设计符合所需参数。
二、印刷阶段印刷是PCB制造的二个主要步骤之一。
印刷包括制造胶片和制作UV曝光机模版。
制造胶片是电路原型转换成制图工程的最后步骤。
将原型的轮廓投射到胶片,胶片结构反转,最后转换为表面铜质电极结构图。
这种结构图只留下需要焊接端口的电路板部分。
制作UV曝光机模版是将硬件图像输出为纸张,然后使用镏铜工艺将图案转换到电路板表面。
三、切分阶段在这个阶段,按需求的尺寸和要求将电路板切成所需尺寸。
常用的方法有铣、锯和CNC方式等。
四、钻孔阶段PCB制造的另一个重要步骤是钻孔。
钻孔需要精准的定位和方向。
得益于可编程控制的工具,在钻孔中还需考虑机器如何为每个孔口定位、标示孔口位置、以及移动到下一个合适的位置。
五、电镀阶段电镀是PCB制造中的关键步骤。
电镀包括在电路板表面镀一层保护性铜材料,以避免氧化和腐蚀。
在此之后,需要将印刷图案反转,外层镀铜结构被切割出来,准备焊接。
六、焊接阶段焊接是PCB制造的最后一个步骤。
将元器件设置到PCB上,用热风吹或电阻炉加热(取决于焊接方式)制作焊点。
大多数PCB使用表面安装技术(SMT)进行焊接,而有些PCB则使用插式技术(THT)焊接。
焊接结束后,PCB会得到最后精液所需的形状和连接。
PCB钻孔工艺详解
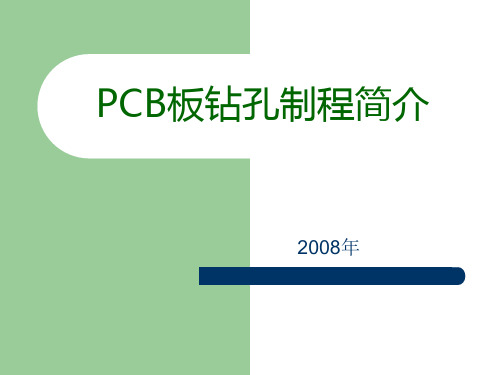
PCB板钻孔制程简介2008年目的:了解钻孔制程及品质要求内容点:①PCB钻孔的作用②PCB钻孔板的品质缺陷及解决对策③钻孔品质及其鱼骨图分析④钻咀及相关辅料阐述⑤钻、锣带制作知识的介绍一、PCB钻孔的作用1、PCB板制作流程以双面板喷锡板工艺流程为例:开料→钻孔→沉铜→板电(加厚铜)→图形转移→电铜电锡→蚀刻退锡→检验→印阻焊→印字符→喷锡→成形→测试→成品检查→包装一、PCB钻孔的作用2、钻孔的作用钻孔就是在覆铜板上钻出所需的过孔。
PCB过孔按金属化与否,分为a、电镀孔( PTH ),也叫金属化孔b、非电镀孔(NPTH),也叫非金属化孔按工艺制程分为a、盲孔(多层板)b、埋孔(多层板)c、通孔过孔主要提供电气连接与用作器件的固定或定位的作用。
二、PCB钻孔板的品质缺陷及解决对策品质缺陷原因分析解决对策断钻(孔损)下钻速或回刀速过快更改加工参数压脚问题检查或更换压脚机床不稳定检查固定座钻咀有缺陷或超孔限更换钻咀类型或检查钻咀叠板过厚或叠板过松减少叠板数或叠紧盖板材料不对更换盖板加工深度过深更改合理的深度胶纸未贴好将胶纸贴好贴牢固二、PCB钻孔板的品质缺陷及解决对策品质缺陷原因分析解决对策断钻(孔损)板间有杂物保持板面及板间清洁孔壁粗糙,毛刺,钉头钻头钝或钻头有缺口更换钻头压脚压力过小检查压脚及气压设置加工参数过快或过慢调整参数设置叠板太松或太厚贴紧板或更改叠板厚度板间有杂物保持板面及板间清洁多层板层压固化不良需层压或板材协助解决盖板不平、太薄等更换盖板材料烤板时间或温度不够按要求重新烤板二、PCB钻孔板的品质缺陷及解决对策品质缺陷原因分析解决对策塞孔钻咀刀刃不够长或螺旋角不对更换钻咀叠板太厚减少叠板数吸尘堵塞或吸力不够清除堵塞,清理吸尘机增加吸力下钻深度过深更改合理的深度钻头过度磨损更换钻咀静电吸附灰尘增加温度垫板材料不对更换垫付板加工参数过快更改参数层压板固化不足更换更好的板材二、PCB钻孔板的品质缺陷及解决对策品质缺陷原因分析解决对策偏孔钻轴退刀过量检查并清洗钻轴夹嘴钻床精度不好检查并维修钻床切屑载荷太大降低横切量切割速度太慢增加转速钻孔同心度不好检查钻头与垫板叠板太厚减少叠板数板间有杂物清洁板面二、PCB钻孔板的品质缺陷及解决对策品质缺陷原因分析解决对策偏孔内层焊盘不硬检查内层板材厚板不均匀更换更好的板材压力脚不平或压力不足更换压脚或调整气压烤板时间或温度不够重新烤板钻床不稳定检查钻床固定座主轴偏摆过大清洗夹嘴或维修主轴钻咀类型不附或有缺口更换钻咀盖板不好更换盖板偏孔:二、PCB钻孔板的品质缺陷及解决对策品质缺陷原因分析解决对策移位定位销松动更改定位销或重新定位钻孔零位改变更正零位压脚过低抬高压脚钻孔机器故障维修机器孔大、孔小钻咀用错更换钻咀钻咀崩缺或磨损过度更换钻咀钻带指示错误更改钻带孔变形钻咀有缺陷检查并更换钻咀钻带有重孔更改钻带二、PCB钻孔板的品质缺陷及解决对策品质缺陷原因分析解决对策槽纹钻咀磨损过度更换钻咀板材问题更换板材切割速度过快降低转速或下钻速未钻穿钻头断或钻咀长度不够更换钻咀重新补孔台面不平调整台面平整度下钻深度设置错误更改合理设置多孔、少孔、飞孔操作失误补孔或报废钻带出错或格式用错用正确格式的钻带生产三、钻孔品质及其鱼骨图分析1、钻孔的品质要求孔径:+0/-1mil孔位:≤2mil孔壁粗糙度:≤1mil钉头:≤1.5三、钻孔品质及其鱼骨图分析2、钻孔品质鱼骨分析图板料环境及加工条件机器性能技术加工参数辅助材料清洁度板厚均匀度层压重合度烤板光滑度对机器的熟练度专业技能钻咀盖板垫板地基吸尘温度湿度叠板数气压深度进刀速回刀速转速刀具寿命压脚平整度主轴偏摆度台面平整度静态定位精度动态精度品质四、钻咀及相关辅料阐述1、钻咀ST型钻咀(用于普通FR-4、CEM-3板及环保板加工)四、钻咀及相关辅料阐述UC型钻咀(具有耐磨性能好、排尘能力强、孔壁质量好、孔位精度高。
pcb整孔原理 -回复

pcb整孔原理-回复PCB整孔原理导语:印刷电路板(Printed Circuit Board,简称PCB)是电子产品中的重要组成部分,用于实现电子元器件之间的连接。
而整孔则是PCB制造过程中的一个重要步骤,用于安装元器件并进行焊接。
本文将从PCB整孔的原理出发,详细介绍整孔的步骤和过程。
一、PCB整孔的概述PCB整孔是指在印刷电路板上开设导通孔或贴片孔,用于插装或焊接元器件。
整孔的种类包括贴片孔、圆孔和长方孔等。
在整孔过程中,需要考虑到孔的位置、孔径、孔距等参数,以确保后续元器件的安装和电路的连接正常进行。
二、PCB整孔的步骤PCB整孔的步骤主要包括孔位设计、孔加工和孔修剪三个过程。
下面我们将逐一介绍这些步骤:1. 孔位设计孔位设计是整孔的第一步,它是根据电路原理图和元器件布局来确定孔的位置和数量。
首先,根据电路原理图确定哪些元器件需要焊接或插装,然后根据元器件布局将它们放置在PCB板上,最后确定孔的位置。
在进行布局时,还需要考虑到元器件之间的间距和电路板上的规则约束条件。
2. 孔加工孔加工是整孔的核心步骤。
在这一步骤中,主要有两种方法用于开孔,分别是机械钻孔和激光钻孔。
(1)机械钻孔:机械钻孔是最常用的孔加工方式之一。
它通过机械钻头在PCB板上钻孔。
钻孔机根据预先设定的参数进行自动加工,包括孔径、孔类型(贴片孔、圆孔或长方孔)和孔距等。
(2)激光钻孔:激光钻孔是一种非常精确的加工方法。
它通过激光束在PCB板上瞬间加热,然后利用高热蒸发板材的方式来形成孔洞。
激光钻孔具有高精度、高速度和无接触等特点,适用于高密度PCB板。
3. 孔修剪孔修剪是整孔的最后一步。
在整孔过程中,钻孔或激光加工会留下残留物,这些残留物需要进行修剪。
孔修剪采用的方法有机械去毛刺、化学腐蚀和激光去毛刺等。
这些方法都能去除孔周围的残留物,使孔壁光滑,以便良好的插装和焊接。
三、PCB整孔的原理PCB整孔的原理是通过开设导通孔或贴片孔,实现元器件的连接和焊接。
- 1、下载文档前请自行甄别文档内容的完整性,平台不提供额外的编辑、内容补充、找答案等附加服务。
- 2、"仅部分预览"的文档,不可在线预览部分如存在完整性等问题,可反馈申请退款(可完整预览的文档不适用该条件!)。
- 3、如文档侵犯您的权益,请联系客服反馈,我们会尽快为您处理(人工客服工作时间:9:00-18:30)。
先
进
加
工
技
术
作
业
学院:机电工程学院
姓名:王琳芳
学号:2111101052
关于PCB钻孔的综述
1 PCB的发展历程
摘要
近年来,由于电子产品的高密度、多功能、小型化的要求,促进了PCB工
业向高密度布线和多层板薄形化技术的发展[1],故印刷电路板(PCB)在人们的
生活中运用的越来越广泛,成为了电子组件制造业的最大支柱产业之一,它用于
组装电子元器件之前的基板、形成电子线路以及连接电子元器件,发挥整体功能。
PCB钻孔的过程中需要研究钻削力和钻削热对刀具寿命和孔质量的影响。
关键词 PCB 材料性能 钻孔质量 刀具使用寿命
1.1 PCB基板材料
PCB板基板材料业已累积了近百年的历史。基板材料业的每一阶段的发展,
都受到电子整机产品、半导体制造技术、电子安装技术、电子电路制造技术的革
新所驱动。20世纪初至20世纪40年代末,是PCB基板材料业发展的萌芽阶段。
它的发展特点主要表现在:此时期基板材料用的树脂、增强材料以及绝缘基板大
量涌现,技术上得到初步的探索。这些都为印制电路板用最典型的基板材料——
覆铜板的问世与发展,创造了必要的条件。另一方面,以金属箔蚀刻法(减成法)
制造电路为主流的PCB制造技术,得到了最初的确立和发展。它为覆铜板在结构
组成、特性条件的确定上,起到了决定性的作用。
覆铜板在PCB生产中真正被规模地采用,最早于1947年出现在美国PCB业。
PCB基板材料业为此也进入了它的初期发展的阶段。在此阶段内,基板材料制造
所用的原材料——有机树脂、增强材料、铜箔等的制造技术进步,对基板材料业
的进展予以强大的推动力。正因如此,基板材料制造技术开始一步步走向成熟。
集成电路的发明与应用,电子产品的小型化、高性能化,将PCB基板材料技
术推上了高性能化发展的轨道。PCB产品在世界市场上需求的迅速扩大,使 PCB
基板材料产品的产量、品种、技术,都得到了高速的发展。此阶段基板材料应用,
出现了一个广阔的新领域——多层印制电路板[2]。同时,此阶段基板材料在结构
组成方面,更加发展了它的多样化。
1.2 印刷电路板的分类
按印刷电路板的层数,我们可以将其分为三类:单层(面)印刷电路板、双
层(面)印刷电路板以及多层印刷电路板。
单层电路板是指导线分布在绝缘基板的一面上,几乎都采用纸质酚醛基材。
双层电路板即双面都印有线路图形,即绝缘基板两面都有电路,再通过孔的
金属化进行双面互连形成的印刷电路板。
多层印刷电路板是利用传统多层板逐次压合的观念,在以双层和四层板为基
础的核心基板的板外,逐次增加绝缘层和导体层,一层一层个别制作,在绝缘层
上制造导体线路,达到多层结构的功能。
另外,电路板也可以根据基板的硬度分为刚性基板电路板和柔性基板电路
板,根据基材的材料可以分为纸质基板、复合基板、玻璃纤维布基等等。
2 PCB机械钻孔的研究方法
在线路板上钻孔的常用方法有数控机械钻孔方法和激光钻孔方法等,现阶段
以机械钻孔方法使用最多。随着高密度增层法线路板的普及,对盲孔的需求增加,
激光钻孔加工方法应用有增加的势头。但是激光钻孔加工对被加工材料适应性较
差、设备成本高及孔壁质量较低等原因,使得目前近90%的PCB孔由机械钻孔机
来实现[3]。
在对印刷电路板的钻削过程中,钻头需要经过盖板、多层PCB电路板以及垫
板,不同的层的材料不同,所以,在钻削过程中,钻头的磨损以及孔的质量是不
同的,综合各种因素,以其找到最优的钻削方法,故对其钻削过程应进行深入的
研究。
2.1 印刷电路板钻削过程中的钻削力[4]
钻削力是印刷电路板钻削过程中的重要物理参数之一,它的大小决定了钻削
过程中所消耗的功率,切削变形,它还导致了钻削热的产生,并进一步影响钻头
的磨损,对加工精度和加工质量有着重要的影响。
在钻削过程中通过安装的测试系统来测试不同的加工参数和钻头的几何参
数对钻削力的影响,进而导出钻削力的经验公式。根据钻削力的经验公式,综合
刀具使用寿命,孔加工质量,成本等因素,得出最优的钻削方案。
2.2 印刷电路板钻削过程中钻屑的显微观察
切屑分为带状切屑、挤裂切屑、单位切屑和崩碎切屑等[5],不同的切屑形状
包含了不同的加工信息,影响因素有加工参数的不同、刀具几何参数的不同等。
由于在钻削过程中,钻头需要通过盖板、多层电路板和垫板,每层的材料不同,
故钻屑的形状也不同,通过高速显微观察不同时期不同材料的钻屑的形状和毛刺
情况,并分析钻屑对钻削过程的影响。
2.3 印刷电路板钻削过程中钻头的磨损研究
观察高速钻削印刷电路板时钻头磨损,比较不同的进给速度对钻头磨损的影
响,分析钻头磨削机理,采用单因素实验,选择不同的刀具几何参数,逐个分析
其对刀具磨损的影响,用显微镜对刀具的磨损情况进行分析,得出刀具磨损图形,
综合不同的刀具磨损参数的特征,确定磨损机理。
2.4 印刷电路板钻削过程中的钻削温度的测量以及孔加工
质量的研究
采用非接触式红外测温的方法来测量印刷电路板在钻削过程中钻削加工区
域的温度场变化。应用测温软件,测量不同时刻温度场中各点或各区域的温度,
绘制等温线。
研究印刷电路板钻削加工中,孔径超差、毛刺、孔壁粗糙度等加工质量问题。
印刷电路板钻削加工中,孔径超差、毛刺、孔壁粗糙度均是钻孔质量的评价指标。
3 我国PCB工业的发展现状和发展前景
PCB工业的发展与进步主要是受世界主导经济而决定(制约)着的,也就是
说,当前和今后的世界主导经济——知识经济的状况将决定着PCB工业的发展与
进步!尽管世界经济多次反复的波动(经济危机、特别是2008年发生的金融海啸,
至今还处在缓慢“复苏”之中)会给PCB工业带来市场和生产上的很大起落变化。
但是,当今世界的主导经济——知识经济仍然没有改变,这意味着PCB工业仍将
继续大力(特别是PCB生产工业技术、产品结构和升级等)向前发展着[6]。
随着电子工业的迅速发展, 特别是表面安装技术和计算机的飞速进展, 我
国印制电路技术已逐渐进入成熟时期.当然,也应该看到我国印制电路技术同世
界先进水平相比, 还有不少差距[7]。尽管改革开放30多年来使我国PCB工业从小
到大走上了世界产量首位、产值第一的大国,但是仍然属于中、低档产品为主体
的“劳动密集型”的产业。同时,我国PCB工(产)业和其它工(产)业一样,
面临着发达国家走过的“刘易斯转变点”——无限提供劳动力到有限提供劳动力
变化的问题,在这种情况下。我国PCB工业要积极应对:转变生产方式提高生产
效率;进行产品结构调整和优化升级;创新生产工艺和产品体系等,使我国PCB
工业从生产大国走向生产强国!
世界PCB的发展技术以日本和英国为领袖,日本的电子设备产品以采用高密
度安装和轻薄短小化的方向性而著称于世,处于高度优势。。实现各种功能的电
子设备安装中,PCB是决定电子设备特性的重要部件之一。今后高性能化的要求
仍将继续,特别是在便携型电子设备的安装中,各种功能并行发展,适应各种功
能的PCB开发支撑和高性能的实现[9]。相比于这些发展国家,我国的发展技术稍
显青涩,过去我国PCB产业的状大和发展主要是依靠广大农村的“剩余劳动力”,
由于现在劳动力相对短缺,也就造成了我国PCB行业的滞后,在未来的日子我们
采用自动化的方法。这样做既可增加产品自动化生产程度,又能够提高产品质量
与生产效率,达到降低生产成本、提高企业效益!
参考文献
[1]蔡云鹏,曾黎明,陈雷,王俊海.纳米材料在印刷电路板基材中的应用.原材
料与设备.2010年第五期
[2]祝大同编译.积层法多层板的最新技术发展.印制电路资讯.2004年
[3]王星,宋福民,肖俊君.PCB数控钻孔机开发与应用综述.制造工艺与设备.2009
年4月
[4]黄立新.印刷电路板定位安装孔钻削研究.广东工业大学.2011年
[5]任家隆.机械制造基础.北京:高等教育出版社,2003.
[6]林金堵.我国PCB工业的发展趋势——结构调整、创新发展.印制电路信息第一
期.2011年
[7]吴水清.印制电路技术发展方向的探索.中科院高能物理研究所五专论
[8]王成勇,黄立新,郑李娟等.印刷电路板超细微孔钻削加工及其关键技术.工
业技术.2010年4月
[9]蔡积庆 编译.PCB的关联技术.印制电路信息.2011年第三期