橡胶知识
橡胶基础知识
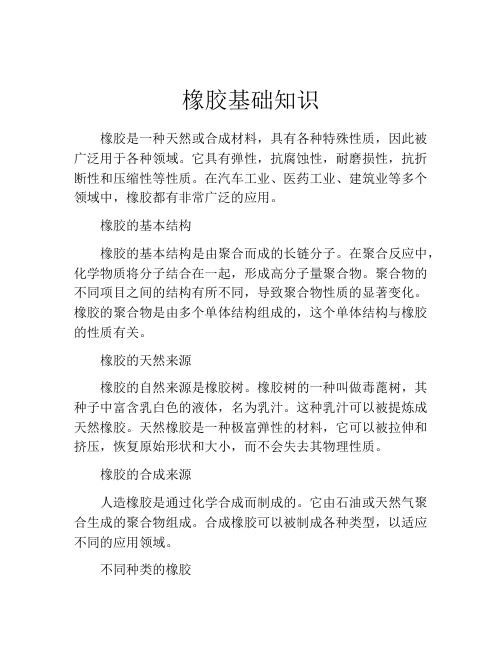
橡胶基础知识橡胶是一种天然或合成材料,具有各种特殊性质,因此被广泛用于各种领域。
它具有弹性,抗腐蚀性,耐磨损性,抗折断性和压缩性等性质。
在汽车工业、医药工业、建筑业等多个领域中,橡胶都有非常广泛的应用。
橡胶的基本结构橡胶的基本结构是由聚合而成的长链分子。
在聚合反应中,化学物质将分子结合在一起,形成高分子量聚合物。
聚合物的不同项目之间的结构有所不同,导致聚合物性质的显著变化。
橡胶的聚合物是由多个单体结构组成的,这个单体结构与橡胶的性质有关。
橡胶的天然来源橡胶的自然来源是橡胶树。
橡胶树的一种叫做毒蓖树,其种子中富含乳白色的液体,名为乳汁。
这种乳汁可以被提炼成天然橡胶。
天然橡胶是一种极富弹性的材料,它可以被拉伸和挤压,恢复原始形状和大小,而不会失去其物理性质。
橡胶的合成来源人造橡胶是通过化学合成而制成的。
它由石油或天然气聚合生成的聚合物组成。
合成橡胶可以被制成各种类型,以适应不同的应用领域。
不同种类的橡胶1. 天然橡胶天然橡胶是通过从橡胶树的乳汁中提取制得的。
这种橡胶具有很高的弹性,弯曲和扭曲性能,但其机械性能很低,不能经受高温和高压。
2. 丁基橡胶丁基橡胶是一种合成橡胶,具有很好的抗温性和耐油性能。
因此,这种橡胶通常用于机械密封和管道密封等高温和高压环境。
3. 丁腈橡胶丁腈橡胶具有良好的耐油和抗性能,可以在低温环境环境下表现出色。
4. 氟橡胶氟橡胶是一种用于温度范围较广的高性能橡胶。
它具有良好的耐化学性,耐高温性和耐油性能,因此经常应用于制造高性能密封件和管道。
5. 氯丁橡胶氯丁橡胶通常用于制造工业密封件和橡胶板。
由于它的耐化学性和耐油性能较高,可以在苛刻的环境和化学物质下工作。
6. 丙烯酸酯橡胶丙烯酸酯橡胶通常用于制造长寿命和高强度的橡胶制品。
它具有良好的抗切割性和高弹性,因此经常用于制造轮胎和其他高重负荷的制品。
总之,橡胶是用于各个领域的关键材料。
了解橡胶的基本知识对于正确使用橡胶及其性能的确定均是非常重要的。
橡胶知识整理
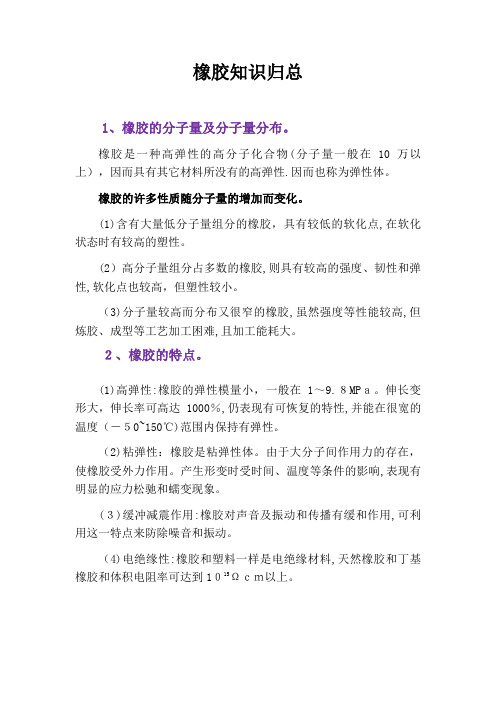
橡胶知识归总1、橡胶的分子量及分子量分布。
橡胶是一种高弹性的高分子化合物(分子量一般在10万以上),因而具有其它材料所没有的高弹性.因而也称为弹性体。
橡胶的许多性质随分子量的增加而变化。
(1)含有大量低分子量组分的橡胶,具有较低的软化点,在软化状态时有较高的塑性。
(2)高分子量组分占多数的橡胶,则具有较高的强度、韧性和弹性,软化点也较高,但塑性较小。
(3)分子量较高而分布又很窄的橡胶,虽然强度等性能较高,但炼胶、成型等工艺加工困难,且加工能耗大。
2、橡胶的特点。
(1)高弹性:橡胶的弹性模量小,一般在1~9.8MPa。
伸长变形大,伸长率可高达1000%,仍表现有可恢复的特性,并能在很宽的温度(-50~150℃)范围内保持有弹性。
(2)粘弹性:橡胶是粘弹性体。
由于大分子间作用力的存在,使橡胶受外力作用。
产生形变时受时间、温度等条件的影响,表现有明显的应力松驰和蠕变现象。
(3)缓冲减震作用:橡胶对声音及振动和传播有缓和作用,可利用这一特点来防除噪音和振动。
(4)电绝缘性:橡胶和塑料一样是电绝缘材料,天然橡胶和丁基橡胶和体积电阻率可达到1015Ωcm以上。
(5)温度依赖性:高分子材料一般都受温度影响。
橡胶在低温时处于玻璃态变硬变脆,在高温时则发生软化、熔融、热氧化、热分解以至燃烧。
(6)具有老化现象:如同金属腐蚀、木材腐朽、岩石风化一样,橡胶也会因环境条件的变化而发生老化,使性能变坏,使寿命缩短。
(7)必须硫化:橡胶必须加入硫黄或其它能使橡胶硫化(或称交联)的物质,使橡胶大分子交联成空间网状结构,才能得到具有使用价值的橡胶制品。
3、橡胶的分类。
天然橡胶丁苯橡胶SBR顺丁橡胶BR 橡胶ﻩ通用合成橡胶异戊橡胶IR氯丁橡胶CR合成橡胶乙丙橡胶EPDM丁橡胶NBR特种合成橡胶硅橡胶SiR氟橡胶FPM、聚氨酯橡胶FU(1)天然橡胶(NR):成分以橡胶烃(聚异戊二烯)为主,含少量蛋白质、水分、树脂酸、糖类和无机盐等。
橡胶基础知识

4.老化现象:如金属腐蚀、木材腐朽、岩石风化一样,橡胶也会因为 环境条件的变化而产生老化现象,使性能变坏,寿命下降。
5.必须进行硫化才能使用,热塑性弹性体除外。
6.必须加入配合剂。
其它如比重小、硬度低、柔软性好、气密性好等特点, 都属于橡胶的宝贵性能。
2
Polymer Materials
10
Polymer Materials
3.国内橡胶工业的发展概况
我国从1904年开始在雷州半岛等地种植NR,50年代将橡胶树北移种 植成功,并在云南、广西等地大面积种植,现在,我国NR产量占世界第 四位。
1915年,在广州建立第一个橡胶加工厂—广州兄弟创制树胶公司,生产鞋底 1919年,在上海建立清和橡皮工厂
1)塑炼:降低生胶的分子量,增加塑性,提高可加工性。
2)混炼:使配方中各个组分混合均匀,制成混炼胶。
3)压延:混炼胶或与纺织物、钢丝等骨架材料通过压片、压型、贴合、 擦胶、贴胶等操作制成一定规格的半成品的过程。
4)压出:混炼胶通过口型压出各种断面的半成品的过程,如内胎、胎面、 胎侧、胶管等。
5)硫化:橡胶加工的最后一道工序,通过一定的温度、压力和时间后, 使橡胶大分子发生化学反应产生交联的过程。
11
Polymer Materials
我国橡胶工业从50年代后开始飞速发展,逐渐形成了以上海的正泰、 大中华,青岛的橡胶二厂,黑龙江的桦林橡胶厂为中心的橡胶工业 格局号称橡胶界的四大家族。其中正泰、大中华生产胶鞋、胶带, 胶二和桦林生产轮胎。到1990年止,全国县级以上的橡胶企业就有 1000多家,产值180亿元,约占全国工业总产值的1.5%,约占化工工 业总产值的25%。90年代,我国橡胶工业得到了蓬勃发展,个体、 私营橡胶企业如雨后春笋般发展起来,仅山东省大小橡胶企业就有 1000多家,青岛市有几百家,96年以后由于受气候等因素的影响, 世界NR的产量锐减,致使NR的价格飞涨,橡胶工业的发展受到一 定程度的影响,但在国内工业总产值、化工工业总产值中仍然占有 相当比重。橡胶企业主要集中在北京、上海、山东、沈阳、贵阳、 重庆、牡丹江等地。我院为我国橡胶工业的发展作出了突出贡献, 为橡胶工业培养了近万名人才,许多毕业生已成为各个橡胶企业的 负责人和骨干技术人员。
橡胶基本知识

1.耐老化性能差:不饱和程度高 2.耐热性不是很好:长期使用温 度为90℃,短期最高使用温度为 110℃。粘流温度Tf =130℃ 3.气密性中下等 4.耐化学介质性: NR 具有良好 的耐化学药品性及一般溶剂作用, 耐稀酸酸、稀碱,不耐浓酸、油、 耐水性差
天然橡胶的应用
轮胎:胎面、胎体、胎侧 工业橡胶制品:如胶管、胶带 日常生活用品:鞋底
丁苯橡胶的用途
输送带
汽车零件
胶管和胶鞋
乳聚丁苯橡胶主要厂家及牌号
公司名称
产品名称 主要产品牌号
中国 美国
齐鲁石化 申华化学
吉林化学 Ameripol Synpol 固特异 DSM
齐鲁牌 TAIPOL 双力牌 Ameripol
Plioflex COPO
1500、1502、1712、1778 1500、1502、1712、1778
合成塑料 合成橡胶 合成纤维 合成粘合剂 合成涂料
天然橡胶(NR) 通用合成橡胶
合成橡胶 特种合成橡胶
丁苯橡胶(SBR) 顺丁橡胶(BR) 丁腈橡胶(NBR) 氯丁橡胶(CR) 乙丙橡胶(EPM、EPDM) 丁基橡胶(IIR) 异戊橡胶(IR) 氟橡胶(FPM) 硅橡胶(MVQ或Q) 聚氨酯橡胶(PU) 丙烯酸酯橡胶(ACM) 聚硫橡胶(T) 氯化聚乙烯(CPE) 氯磺化聚乙烯(CSM) 氯醚橡胶或氯醇橡胶(CO、ECO) 环氧化天然橡胶(ENR)
产品名称 长寿
卧虎
主要产品牌号
CR1211, CR1212, CR1222,CR2321, CR2441,CR2442, CR3211,SCR2122
CR1211, CR1212, CR1222,CR2322, CR2442, CR2461, CR3211,SCR2121
橡胶有关知识点总结

橡胶有关知识点总结一、橡胶的基本概念橡胶是一种高分子聚合物,主要成分是聚异戊二烯,常温下呈胶状。
橡胶具有优良的弹性、耐磨、耐寒和耐酸碱的特性,因而广泛地用于工业和日常生活中。
二、橡胶的性质1. 弹性:橡胶具有良好的弹性,可以拉伸成线状,然后回弹成原状。
2. 耐磨性:橡胶具有很好的耐磨性,适合用于制作汽车轮胎等耐磨耗的产品。
3. 耐寒性:橡胶在低温下仍然保持良好的弹性,不易变硬变脆。
4. 耐酸碱性:橡胶具有一定的耐酸碱性,适合用于化工行业的管道和容器等。
三、橡胶的生产工艺橡胶的生产主要包括天然橡胶和合成橡胶两种,其中合成橡胶是以石油为原料经过聚合反应而得到的,而天然橡胶是从橡胶树中提取而来的。
橡胶的生产包括原料的采集、精炼、聚合等多个环节,生产工艺较为复杂。
四、橡胶的应用领域1. 汽车轮胎:橡胶是汽车轮胎的主要原材料,其良好的弹性和耐磨性能够提高汽车行驶的稳定性和安全性。
2. 鞋底:橡胶制成的鞋底耐磨耗,具有良好的抓地力,适合于户外活动和运动场所。
3. 工业制品:橡胶也被广泛用于工业领域,比如密封件、管道、阀门等。
4. 家居用品:橡胶也被用于制作家居用品,如橡皮泥、橡皮筋等。
五、橡胶的发展趋势1. 高性能化:随着科技的进步,人们对橡胶产品的性能要求越来越高,未来橡胶制品将朝着更高强度、更耐磨耗、更耐老化的方向发展。
2. 绿色环保:在生产过程中,应该尽量减少对环境的污染,采用节能环保的生产工艺,生产出更环保的橡胶产品。
3. 智能化:未来橡胶制品可能会加入智能芯片,实现对产品的智能化管理,提高产品的安全性和可靠性。
六、橡胶的保养与维护1. 温度:橡胶产品不宜放置在高温下,以免变硬变脆。
2. 防水:在橡胶制品长时间浸泡在水中后,要及时晒干,避免发霉和变质。
3. 防腐:橡胶制品在长时间不使用时,应保持干燥,避免霉菌的滋生。
4. 避免接触酸碱物质:橡胶制品不宜接触强酸和强碱,以免发生化学反应而损坏产品。
七、橡胶的环保问题1. 废橡胶的处理:废橡胶的处理一直是一个环保难题,目前主要有回收再利用和焚烧处理两种方式。
橡胶知识整理
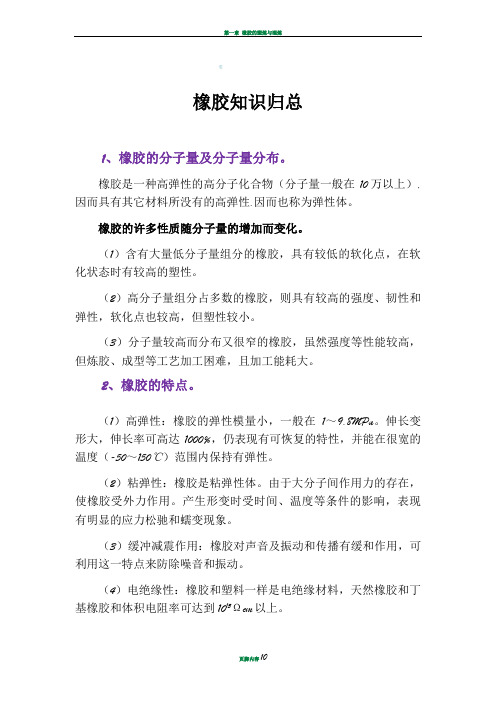
橡胶知识归总1、橡胶的分子量及分子量分布。
橡胶是一种高弹性的高分子化合物(分子量一般在10万以上),因而具有其它材料所没有的高弹性.因而也称为弹性体。
橡胶的许多性质随分子量的增加而变化。
(1)含有大量低分子量组分的橡胶,具有较低的软化点,在软化状态时有较高的塑性。
(2)高分子量组分占多数的橡胶,则具有较高的强度、韧性和弹性,软化点也较高,但塑性较小。
(3)分子量较高而分布又很窄的橡胶,虽然强度等性能较高,但炼胶、成型等工艺加工困难,且加工能耗大。
2、橡胶的特点。
(1)高弹性:橡胶的弹性模量小,一般在1~9.8MPa。
伸长变形大,伸长率可高达1000%,仍表现有可恢复的特性,并能在很宽的温度(-50~150℃)范围内保持有弹性。
(2)粘弹性:橡胶是粘弹性体。
由于大分子间作用力的存在,使橡胶受外力作用。
产生形变时受时间、温度等条件的影响,表现有明显的应力松驰和蠕变现象。
(3)缓冲减震作用:橡胶对声音及振动和传播有缓和作用,可利用这一特点来防除噪音和振动。
(4)电绝缘性:橡胶和塑料一样是电绝缘材料,天然橡胶和丁基橡胶和体积电阻率可达到1015Ωcm以上。
(5)温度依赖性:高分子材料一般都受温度影响。
橡胶在低温时处于玻璃态变硬变脆,在高温时则发生软化、熔融、热氧化、热分解以至燃烧。
(6)具有老化现象:如同金属腐蚀、木材腐朽、岩石风化一样,橡胶也会因环境条件的变化而发生老化,使性能变坏,使寿命缩短。
(7)必须硫化:橡胶必须加入硫黄或其它能使橡胶硫化(或称交联)的物质,使橡胶大分子交联成空间网状结构,才能得到具有使用价值的橡胶制品。
3、橡胶的分类。
天然橡胶丁苯橡胶SBR顺丁橡胶BR 橡胶通用合成橡胶异戊橡胶IR氯丁橡胶CR合成橡胶乙丙橡胶EPDM丁橡胶NBR特种合成橡胶硅橡胶SiR氟橡胶FPM、聚氨酯橡胶FU(1)天然橡胶(NR):成分以橡胶烃(聚异戊二烯)为主,含少量蛋白质、水分、树脂酸、糖类和无机盐等。
橡胶基础知识
第一章概论一、橡胶的作用橡胶是一种高分子弹性体,是重要的战略物资和经济物质。
橡胶与国民经济与人民生活密切相关,对我国农业、工业、国防、科学技术、交通运输、人民生活都起着极为重要的作用。
二、橡胶工业开展史人类使用橡胶已有二百多年历史。
1770年,人们开始用橡胶树上自然凝固的橡胶来制造文具橡皮等。
1823年在英国建立了世界上第一个橡胶工厂,它将橡胶溶于有机溶剂中,然后涂在布上,生产发防水胶布。
1826年汉考克〔Hancock〕发现橡胶反复通过两个转动圆筒的缝隙后,弹性下降,易于加工,从而诞生了专用橡胶设备,为现代橡胶加工方法奠定了根底。
直到1839年美国科学家固特异〔Goodyear〕发现了橡胶可用硫黄硫化方法改善其强度、弹性与耐温性后,橡胶才真正进入工业化生产阶段,开辟了橡胶制品广泛应用的前景。
1880年邓录普〔Dunlop〕发明了充气轮胎,利用橡胶制造轮胎,使橡胶制品从雨衣、雨鞋等日常用品转入以轮胎、胶带等工业用品为主,使橡胶工业突飞猛进地开展起来。
我国橡胶工业仅有几十年的历史,1917年萌芽于##,建立起第一个小型橡胶厂,以后相继在##、##、##等地建立起小型橡胶工厂。
经过几十年的开展,到今天橡胶工业已成为我国化学工业的重要组成局部,橡胶消耗量居世界首位,产品品种已达到四万种以上,是世界上橡胶制品的生产大国。
三、橡胶制品的分类橡胶制品通常分五大类,即轮胎、管带、工业用品、胶鞋与其他〔文化、医疗卫生、日常用品等〕。
四、橡胶制品生产根本工艺高弹性是橡胶特有的性质,这种高弹性增加了产品制造的困难,生胶需要经过加工,才能制成各种各样的制品。
同时,单纯的橡胶,其性能是不十分完善的,为了提高制品的使用性能,改善加工性能,节约生胶,降低本钱,必须在生胶中参加各种配合剂。
其胶料的组成,可概括五个体系。
主体材料:生胶、橡胶代用品硫化体系:硫化剂、促进剂、活性剂、防焦剂补强与填充体系:补强剂、填充剂增塑与软化体系:增塑剂、塑解剂、软化剂防护体系;化学防老剂、物理防老剂其他性能体系:着色剂、发泡剂、芳香剂、其他专用配合剂橡胶制品生产的根本工艺过程包括塑炼、混炼、压延、压出、成型、硫化六个根本工序,如下图。
橡胶基础知识
橡胶基础知识橡胶是一种不断发展的工程材料。
从自然橡胶发展到合成橡胶,再到高分子弹性体,橡胶的种类越来越多,应用范围也越来越广。
橡胶的定义是一种高分子化合物,具有高度的可拉伸性和可回弹性。
橡胶在应用中广泛地使用在密封、减震、气垫、橡胶软管、轮胎、橡胶地垫、橡胶管道、橡胶破碎机橡胶零件等方面。
其中,汽车轮胎、皮革、印刷墨汁、自行车胎和人造橡胶等应用最为广泛的橡胶产品。
橡胶的分类有两种,一种是天然橡胶,另一种是合成橡胶。
天然橡胶是由橡胶树中的乳液提取而来,是一种高分子有机成分,其中又包含了约98%的高分子碳水化合物及少量的蛋白质、油脂和灰分。
而合成橡胶则是通过人工合成的高分子化合物,具有与天然橡胶相似的性质,但是比天然橡胶优良的特性是合成橡胶的种类和特性更灵活,可以根据需要进行改良和提高,不仅能适用于不同的业务领域,而且具有更广泛的市场需求。
关于橡胶的物理性质,其品质与物水的机械性能、耐热性和抗老化性能有关。
而橡胶的化学性能则和各类有机溶剂、硝酸、氢氧化物等有关。
一般来说,橡胶的耐候性能、抗紫外线、抗氧化、抗臭氧、耐酸碱性较大程度上取决于其化学构成,这个特性对长期使用的橡胶制品具有非常重要的意义。
橡胶由于其高分子化学构成,具有许多特殊性质,如在变形时可以恢复原来的形状,也可以随变形而变形,在机械应力作用下表现出接近弹性的性质。
橡胶还具有非常高的抗寒性,因为在低温下还可以保持较大的伸长量。
此外,橡胶也具有耐化学腐蚀和耐高温性的特点,使得他们在航空、飞行器和汽车等领域得到了广泛的应用。
关于橡胶的加工过程,橡胶一般不适用于单独作为材料来应用,需要经过一定的加工过程后才能使用到它的全部优良特性。
橡胶加工主要包括几个过程,如混炼、成型、硫化和后处理等。
其中混炼是指将橡胶与其他添加剂(如填料和增塑剂)混合在一起,使之成为胶体。
橡胶经过混炼之后,可以被用于成型,如挤出成型、压缩成型、注射成型等,使之成为所需要的产品,而硫化过程则是将成型后的橡胶制品加热,在硫化质量控制下使其形成三维网络结构,这个过程使得橡胶制品具有出色的耐用性和抗热性。
橡胶的知识
橡胶知识橡胶------高分子化合物. 它具有其他材料所没有的高弹性:A分子量巨大,上百万.B.分子量多分散性.基本特征:1.高回弹性-----伸张变形很大,伸张率可以高达1000%.当外力撤消后橡胶可恢复的弹性形变的大小.是橡胶网状结构对外加应力反抗特性的表征.2.引伸出高拉伸强度和高撕裂强度抵抗(拉伸)破坏的极限能力.这是橡胶制品普遍要求的性能.撕裂强度是指单位厚度的试样产生裂纹所需要的能量.3.耐磨性:摩擦\滚动\冲击和反复形变产生的疲劳.4.耐侯性能;是指橡胶的理化性能对温度的敏感性,也就是橡胶在高温或低温时的理化性能与室温时的差别大小..5.耐油性; .耐化学性;耐水性是指橡胶抗介质作用的能力.(溶胀\硬化等力学性能) 通常用效能△m质量变化率, △V体积变化率.6.导电性能7.阻燃性能氟橡胶F2311Q氟橡胶F2311Q. (俗称1#氟橡胶). 性能. 具有优良的耐强腐蚀介质和强氧化剂的性能,如耐发烟硝酸、盐酸和过氧化氢等,较突出的是耐酸性较好;还有良好的耐热性和较好的物理机械性能,电绝缘性能。
长期工作温度为200 ...氟橡胶F2311Q(俗称1#氟橡胶)性能具有优良的耐强腐蚀介质和强氧化剂的性能,如耐发烟硝酸、盐酸和过氧化氢等,较突出的是耐酸性较好;还有良好的耐热性和较好的物理机械性能,电绝缘性能。
长期工作温度为200℃,在250℃下则可短期使用;玻璃化温度为0℃左右,脆点为-20— -40℃,耐寒性能一般。
主要用途该胶可用普通橡胶成型方法和设备加工成胶带、胶管、胶布、薄膜、垫片、油箱和浸渍制品。
广泛应用在航空工业、汽车工业、石油工业、化学工业等领域。
氟橡胶FPM26(俗称2#氟橡胶)性能具有良好的耐热、耐油和耐溶剂性能,尤其是耐油性能突出。
同时,还具有良好的物理机械性能、电绝缘性和抗辐射性能。
在250℃下较长时间使用,短时间可耐300℃高温。
耐低温性能尚可,玻璃温度-17±2℃,脆点温度-40—-55℃,但不耐低分子酮类、酯类、某些醚灯、无水氨和活泼胺类。
橡胶选材知识点总结大全
橡胶选材知识点总结大全一、橡胶的种类1. 天然橡胶:天然橡胶是由橡胶树分泌的乳液经过加工制备而成的橡胶。
它具有优异的弹性和耐磨性,但耐热性和耐油性较差。
2. 合成橡胶:合成橡胶是通过人工合成的橡胶材料,根据不同的合成方法和配方可以得到不同性能的合成橡胶,如丁腈橡胶、丁晴橡胶、丁苯胶、氯丁胶、硅胶等。
二、橡胶的性能1. 弹性:橡胶具有很好的弹性,可以在一定的应力作用下产生变形,当去除外力时又能恢复原状。
2. 耐磨性:橡胶具有很好的耐磨性,能够在摩擦和挤压作用下保持较好的稳定性。
3. 耐老化性:橡胶在长期受热、受光、受氧化作用下会发生老化,使其性能下降。
4. 耐油性:橡胶在油品的作用下会发生膨胀、软化、断裂等现象。
5. 耐溶剂性:橡胶在有机溶剂的作用下会发生膨胀、变形、软化等现象。
三、橡胶选材的考虑因素1. 使用环境:不同的使用环境对橡胶材料的性能要求不同,如室内、室外、高温、低温、潮湿、干燥等。
2. 使用介质:橡胶材料在不同的介质中表现出不同的耐磨性、耐化学性等性能。
3. 使用寿命:产品的使用寿命要求决定了橡胶的耐老化性能和耐磨性能。
4. 成本考虑:不同种类和品牌的橡胶材料价格、性能、品质等都不同,成本也是橡胶选材的重要考虑因素。
四、橡胶选材的常用方法1. 实验室测试:通过拉伸试验、硬度测试、老化测试、耐油性测试等实验室测试方法,评估橡胶材料的性能指标。
2. 比对品牌资料:参考橡胶供应商提供的资料,了解不同品牌、不同种类的橡胶材料性能和适用范围。
3. 实际应用经验:借鉴行业内同行的经验,了解在具体应用领域中哪种橡胶材料表现更为优异。
五、橡胶材料应用领域1. 工程机械:橡胶轮胎、橡胶履带、橡胶密封件等是工程机械中常见的橡胶材料应用。
2. 汽车制造:汽车轮胎、汽车密封件、汽车减震器等都是橡胶材料的重要应用领域。
3. 食品加工:橡胶输送带、橡胶密封圈等在食品加工行业中广泛应用。
4. 医疗器械:医用橡胶手套、医用橡胶管等都是医疗器械中必不可少的橡胶材料。
- 1、下载文档前请自行甄别文档内容的完整性,平台不提供额外的编辑、内容补充、找答案等附加服务。
- 2、"仅部分预览"的文档,不可在线预览部分如存在完整性等问题,可反馈申请退款(可完整预览的文档不适用该条件!)。
- 3、如文档侵犯您的权益,请联系客服反馈,我们会尽快为您处理(人工客服工作时间:9:00-18:30)。
三、硫化1. 硫化对橡胶性能和影响1)、定伸强度通过硫化,橡胶单个分子间产生交联,且随交联密度的增加,产生一定变形(如拉伸至原长度的200%或300%)所需的外力就随之增加,硫化胶也就越硬。
对某一橡胶,当试验温度和试片形状以及伸长一定时,则定伸强度与MC(两个交联键之间橡胶分子的平均分子量)成反比,也就是与交联度成正比。
这说明交联度大,即交联键间链段平均分子量越小,定伸强度也就越高。
2)、硬度与定伸强度一样,随交联度的增加,橡胶的硬度也逐渐增加,测量硬度是在一定形变下进行的,所以有关定促强度的上述情况也基本适用于硬度。
3)、抗张强度抗张强度与定伸强度和硬度不同,它不随交联键数目的增加而不断地上升,例如使硫磺硫化的橡胶,当交联度达到适当值后,如若继续交联,其抗张强度反会下降。
在硫黄用量很高的硬质胶中,抗张强度下降后又复上升,一直达到硬质胶水平时为止。
4)、伸长率和永久变形橡胶的伸长率随交联度的增加而降低,永久变形也有同样的规律。
有硫化返原性的橡胶如天然橡胶和丁基橡胶,在过硫化以后由于交联度不断降低,其伸长率和永久变形又会逐渐增大。
5)、弹性未硫化胶受到较长时间的外力作用时,主要发生塑性流动,橡胶分子基本上没有回到原来的位置的倾向。
橡胶硫化后,交联使分子或链段固定,形变受到网络的约束,外力作用消除后,分子或链段力图回复原来构象和位置,所以硫化后橡胶表现出很大的弹性。
交联度的适当增加,这种可逆的弹性回复表现得更为显著。
2. 硫化过程的四个阶段胶料在硫化时,其性能随硫化时间变化而变化的曲线,称为硫化曲线。
从硫化时间影响胶料定伸强度的过程来看,可以将整个硫化时间分为四个阶段:硫化起步阶段、欠硫阶段、正硫阶段和过硫阶段。
1)、硫化起步阶段(又称焦烧期或硫化诱导期)硫化起步的意思是指硫化时间胶料开始变硬而后不能进行热塑性流动那一点的时间。
硫起步阶段即此点以前的硫化时间。
在这一阶段内,交联尚未开始,胶料在模型内有良好的流动性。
胶料硫化起步的快慢,直接影响胶料的焦烧和操作安全性。
这一阶段的长短取决于所用配合剂,特别是促进剂的种类。
用有超速促进剂的胶料,其焦烧比较短,此时胶料较易发生焦烧,操作安全性差。
在使用迟效性促进剂(如亚磺酰胺)或与少许秋兰姆促进剂并用时,均可取得较长的焦烧期和良好的操作安全性。
但是,不同的硫化方法和制品,对焦烧时间的长短亦有不同要求。
在硫化模压制品时,总是希望有较长的焦烧期,使胶料有充分时间在模型内进行流动,而不致使制品出现花纹不清晰或缺胶等到缺陷。
在非模型硫化中,则应要求硫化起步应尽可能早一些,因为胶料起步快而迅速变硬,有利于防止制品因受热变软而发生变形。
不过在大多数情况下仍希望有较长的焦烧时间以保证操作的安全性。
2)、欠硫阶段(又称预硫阶段)硫化起步与正硫化之间的阶段称为欠硫阶段。
在此阶段,由于交联度低,橡胶制品应具备的性能大多还不明显。
尤其是此阶段初期,胶料的交联度很低,其性能变化甚微,制品没有实用意义。
但是到了此阶段的后期,制品轻微欠硫时,尽管制品的抗张强度、弹性、伸长率等尚未达到预想的水平,但其抗撕裂性耐磨性和抗动态裂口性等则优于正硫化胶料。
因此,如果着重要求后几种性能时,制品可以轻微欠硫。
一、塑炼橡胶受外力作用产生变形,当外力消除后橡胶仍能保持其形变的能力叫做可塑性。
增加橡胶可塑性工艺过程称为塑炼。
橡胶有可塑性才能在混炼时与各种配合剂均匀混合;在压延加工时易于渗入纺织物中;在压出、注压时具有较好的流动性。
此外,塑炼还能使橡胶的性质均匀,便于控制生产过程。
但是,过渡塑炼会降低硫化胶的强度、弹性、耐磨等性能,因此塑炼操作需严加控制。
橡胶可塑度通常以威廉氏可塑度、门尼粘度和德弗硬度等表示。
1、塑炼机理橡胶经塑炼以增加其可塑性,其实质乃是使橡胶分子链断裂,降低大分子长度。
断裂作用既可发生于大分子主链,又可发生于侧链。
由于橡胶在塑炼时,遭受到氧、电、热、机械力和增塑剂等因素的作用,所以塑炼机理与这些因素密切相关,其中起重要作用的则是氧和机械力,而且两者相辅相成。
通常可将塑炼区分为低温塑炼和高温塑炼,前者以机械降解作用为主,氧起到稳定游离基的作用;后者以自动氧化降解作用为主,机械作用可强化橡胶与氧的接触。
塑炼时,辊筒对生胶的机械作用力很大,并迫使橡胶分子链断裂,这种断裂大多发生在大分子的中间部分。
塑炼时,分子链愈长愈容易切断。
顺丁胶等之所以难以机械断链,重要原因之一就是因为生胶中缺乏较高的分子量级分。
当加入高分子量级分后,低温塑炼时就能获得显著的效果。
氧是塑炼中不可缺少的因素,缺氧时,就无法获得预期的效果。
生胶塑炼过塑炼时,设备与橡胶之间的摩擦显然使得胶温升高。
热对塑炼效果极为重要,而且在不同温度范围内的影响也不同。
由于低温塑炼时,主要依靠机械力使分子链断裂,所以在像章区域内(天然胶低于110℃)随温度升高,生胶粘度下降,塑炼时受到的作用力较小,以致塑炼效果反而下降。
相反,高温塑炼时,主要是氧化裂解反应起主导作用,因而塑炼效果在高温区(天然胶高于110℃)将随温度的升高而增大,所以温度对塑炼起着促进作用。
各种橡胶由于特性不同,对应于最低塑炼效果的温度范围也不一样,但温度对塑炼效果影响的曲线形状是相似的。
由前已知,不论低温塑炼还是高温塑炼,使用化学增塑剂皆能提高塑炼效果。
接受剂型增塑剂,如苯醌和偶氮苯等,它们在低温塑炼时起游离基接受剂作用,能使断链的橡胶分子游离基稳定,进而生成较短的分子;引发剂型增塑剂,如过氧化二苯甲酰和偶氮二异丁腈等,它们在高温下分解成极不稳定的游离基,再引发橡胶分子生成大分子游离基,并进而氧化断裂。
此外,如硫醇类及二邻苯甲酰胺基苯基二硫化物类物质,它们既能使橡胶分子游离基稳定,又能在高温下引发橡胶形成游离基加速自动氧化断裂,所以,这类化学增塑剂称为混合型增塑剂或链转移型增塑剂。
2、塑炼工艺生胶在塑炼前通常需进行烘胶、切胶、选胶和破胶等处理。
烘胶是为了使生胶硬度降低以便切胶,同时还能解除结晶。
烘胶要求温度不高,但时间长,故需注意不致影响橡胶的物理机械性能;例如天然胶烘胶温度一般为50~60℃,时间则需长达数十小时。
生胶自烘房中取出后即切成10~20公斤左右的大块,人工选除其杂质后再用破胶机破胶以便塑炼。
按塑炼所用的设备类型,塑炼可大致分为三种方法。
1、开炼机塑炼其优点是塑炼胶料质量好,收缩小,但生产效率低,劳动强度大。
此法适宜于胶料变化多和耗胶量少的工厂。
开炼钢机塑炼属于低温塑炼。
因此,降低橡胶温度以增大作用力是开炼机塑炼的关键。
与温度和机械作用有关的设备特性和工艺条件都是影响塑炼效果的重要因素。
为了降低胶温,开炼钢机的辊筒需进行有效的冷却,因此辊筒设有带孔眼的水管,直接向辊筒表面喷水冷却以降低辊筒需进行有效的冷却,这样可以满足各种胶料塑炼时对辊温的基本要求。
此外,采用冷却胶片的方法也是有效的,例如使塑炼形成的胶片通过一较长的运输带(或导辊)经空气自然冷却后再返回辊上,以及薄通塑炼(缩小辊距,使胶片变薄,以利于冷却)皆可。
分段塑炼的目的也是为了降低胶温,其操作是将全塑炼过程分成若干段,来完成,每段塑炼后生胶需充分停放冷却。
塑炼一般分为2~3段,每段停放冷却4~8小时。
胶温随塑炼时间的延长而增高,若不能及时冷却,则生胶可塑性仅在塑炼初期显著提高,随后则变化很少,这种现象是由于生胶温度升高而软化,分子易滑动和机械降解效率降低所致。
胶温高还会产生假可塑性,一旦停放冷却后,可塑性又降低。
两个辊筒的速比愈大则剪切作用愈强;因此,塑炼效果愈好。
缩小辊间距也可以增大机械剪切作用,提高塑炼效果。
2、密炼机塑炼(高温、间断)密炼机塑炼的生产能力大,劳动强度较低、电力消耗少;但由于是密闭系统,所以清理较难,故仅适用于胶种变化少的场合。
密炼机的结构较复杂,生胶在密炼室内一方面在转子与腔壁之间受剪应力和摩擦力作用,另一方面还受到上顶栓的外压。
密炼时生热量极大,物料来不及冷却,所以属高温塑炼,温度通常高于120℃,甚至处于160~180℃之间。
依据前述之高温塑炼机理,生胶在密炼机中主要是借助于高温下的强烈氧化断链来提高橡胶的可塑性;因此,温度是关键,密炼机的塑炼效果随温度的升高而增大。
天然胶用此法塑炼时,温度一般不超过155℃,以110~120℃最好,温度过高也会导致橡胶的物理机械性能下降。
3、螺杆机塑炼(高温、边续)螺杆塑炼的特点是在高温下进行连续塑炼。
在螺杆塑炼机中生胶一方面受到强烈的搅拌作用,另一方面由于生用受螺杆与机筒内壁的摩擦产生大量的热,加速了氧化裂解。
用螺杆机塑炼时,温度条件很重要,实践表明,机筒温度以95~110℃为宜,机关温度以80~90℃为宜。
因为机筒温度高于110℃,生胶的可塑料性也不会再有大的变化。
机筒温度超过120℃则排胶温度太高而使胶片发粘,粘辊,不易补充加工。
机筒温度低于90℃时,设备负荷增大,塑炼胶会出现夹生的现象。
合成胶塑炼较天然胶困难。
为改进合成胶塑炼工艺性能,最好在合成过程中注意控制和调节分子量大小和分子量分布,以便制得门尼粘度较低和工艺性能良好的品种,如软丁苯和软丁腈胶等。
这些品种可直接用于混炼。
顺丁胶分子量较低,易冷流,塑炼效果不好,因此顺丁胶和适宜门尼粘度也应在合成过种中获得。
氯丁胶门尼粘度低,一般不需塑炼,只要经过3~5次薄通就可进行混炼。
硬丁腈胶门尼粘度为90~120,塑性低,工艺性能差,只有经过充分塑炼才能进行进一步加工。
但是,由于丁腈胶韧性大,塑炼生热大、收缩剧烈,塑炼特别困难。
欲提高丁腈胶的塑炼效果,应采用低温薄通法,即尽可能降低塑炼温度和强化机械作用力,加入增塑剂虽可提高丁腈胶的塑炼效果。
但对混炼胶可塑度的提高不利,因此,不宜采用。
丁基胶、乙丙胶的化学性质稳定,因此缺乏塑炼效果,前者门尼粘度一般为38~75,可不经塑炼而直接混炼,后者加工所必需的可塑性应在合成过程中获得。
二、混炼1、混炼的目的为了提高橡胶产品使用性能,改进橡胶工艺性能和降低成本,必须在生胶中加入各种配合剂。
混炼就是通过机械作用使生胶与各种配合剂均匀混合的过程。
混炼不良,胶料会出现配合剂分散不均,胶料可塑度过低或过高、焦烧、喷霜等到现象,使后续工序难以正常进行,并导致成品性能下降。
控制混炼胶质量对保持半成品和成品性能有着重要意义。
通常采用检查项目有:1、目测或显微镜观察;2、测定可塑度;3、测定比重;4、测定硬度;5、温室物理机械性能和进行化学分析等。
进行这些检验的目的是为了判断胶料中的配合剂分散是否良好,有无漏加和错加,以及操作是否符合工艺要求等。
2、混炼理论由于生胶粘度很高,为使各种配合剂均匀混入和分散,必须借助炼胶机的强烈机械作用进行混炼。
各种配合剂,由于其表面性质的不同,它们对橡胶的活性也各不一致。
按表面特性,配合剂一般可分为二类:一类具有亲水性,如碳酸盐、陶土、氧化锌、锌钡白等;另一类具有疏水性,如各种炭黑等。