镍基高温合金切削加工技术
镍基高温合金的切削加工

镍基高温合金的切削加工CuttingofNickel-BasedHighTemperatureAlloy沈阳黎明航空发动机(集团)有限责任公司山东大学机械工程学院赵秀芬高级工程师.现主要从事航空发动机难加材料的匹配刀具选择.高效加工.切削参数优化.刀具国产化等方面的研究。
现在的涡扇发动机的材料中难加工材料占绝大部分,其中高温合金有65%,其相对加工性很低。
同时,航空航天发动机中叶片、机匣件等形状复杂,表面完整性要求又高,使镍基高温合金零件的切削加工更为困难。
航空发动机零件结构复杂,而高温合金等难加工材料加工难度更大。
对工件来说,复杂型面数控程序优化难,高温合金材料容易造成加工变形和让刀,使加工精度不符合要求;对46航空制造技术・2010年第11期赵秀芬王玉华刘阳王兴林万熠航空发动机零件结构复杂。
而高温合金等难加工材料加工难度更大。
对工件来说。
复杂型面数控程序优化难,高温合金材料容易造成加工变形和让刀,使iju-r精度不符合要求;对刀具来说,JjⅡ"r镍基高温合金零件,容易造成刀具快速磨损。
刀具消耗大。
刀具来说,加工镍基高温合金零件,容易造成刀具快速磨损,刀具消耗大。
镍基高温合金材料的主要成分为镍,以GH4169为例,其镍的含量为50%.55%,其余主要元素有Fe、Cr、Nb等。
它是以体心立方Ni3Nb(1,,)和面心立方Ni3(A1,Ti,Nb)(^y’)强化的镍铁基合怠通常称为镍基合金),从低温到700oc以下具有高的屈服强度、拉伸强度和持久强度。
在650。
C~7600C具有良好的塑性,一般认为GH4169的组织是由1基体和NbC、1’、1,,、8相组成。
NbC(Ti、Nb)(CN)等碳化物数量很少,比较稳定。
^y”相数量最多,是合金的主要强化相。
晶格常数为a0=3.642A,c0=7.406A,呈圆盘状在基体中弥散析出,强化作用是通过1,,的共格畸变而实现。
7’相数量次之,呈球状弥散析出,对合金起一部分强化作用,此外还有一些碳化物起强化相作用。
高温合金的切削加工分析

为了获得刃 口锋利 的刀片 , 采用合理刀片 刃磨 的方法 , 要
提 高 刀 片 的 刃 磨质 量 。
切 削高温 合金 时 , 为了减小 塑性 变形 , 减小切 削力 , 降低
温合金的推广和使用 十分重要 。
1 高温 合金 的切 削特 点
高温合金在切削过程 中有 以下特点 : () I 塑性变形大 。 由于高温合金 中有大量 的奥 氏体组织存 在 , 以高温合金 的塑性变形很大 。 所 () 2 切削力大 。高温合金在 较高温度下 , 仍有较高的物理 机械性 能 , 使切 削力增 大 。通常 , 切削高温合金 的单位 切削力 要 比切 削中碳钢 高 1 ~3倍 。
0.5 ~ 0. mm 。 0 2
() 4 切削温度高 , 刀具易磨损 。 削高温合金 时, 切 产生较大
的塑性变形 , 刀具 与工件 间的摩擦 加剧 , 削力增大 , 切 因此产
生 大量 的切削热 。因高温合金 的导热 系数低 , 以高温合金的 所
散热性很差 , 使切 削温度升高 。由于高温合金的高温强度高 ,
为 了减 小刀具后刀面与加工表面间酌磨擦 ,后角应稍 大 些, 粗加工一般取 8 。~1 。, 2 精加工取 1 。一1 。 2 8。
刀具宜采用大工作 主偏 角 , 以减小背 向切削力 。主偏角 6 。一7 。; 0 5 副偏角 5 。~1。; 0 刃倾 角 0。—一 0 刀尖 圆角半 1 。;
其中, 采用 Y G类 硬质合金 是常用 的牌 号 ; 6 3切削高 温合 用 4 金效 果较好 ;其余几种牌 号切削效果 明显优 于 Y G类硬质合
镍基单晶高温合金DD5_磨削成屑机理研究

镍基单晶高温合金DD5磨削成屑机理研究*于贵华1, 朱 涛1, 蔡 明1, 安志欣1, 王成静2, 罗书宝1(1. 辽宁石油化工大学 机械工程学院, 辽宁 抚顺 113001)(2. 辽宁石油化工大学 石油化工学院, 辽宁 抚顺 113001)摘要 为研究镍基单晶高温合金DD5的磨削去除机理,提高其加工效率,针对镍基单晶高温合金具有显著各向异性的特点,建立基于Hill 模型的三维有限元磨削模型,研究镍基单晶高温合金DD5的表面加工形貌和切屑形貌,分析切屑形貌演变过程及其磨削力变化,探究磨削速度对切屑形貌和切屑形成频率的影响。
研究表明:在磨削参数范围内,加工DD5容易出现锯齿形切屑;磨削力呈稳定增加并伴有一定的周期性波动,其波动情况与锯齿形切屑相对应;随着磨削速度的增大,磨粒能更快进入切削阶段,其临界成屑厚度由0.225μm 最终降为0.158 μm ,成屑阶段占比由85.0%提高到89.5%;临界划擦厚度受磨削速度变化影响不大;随着磨削速度的增加,DD5切屑形貌由锯齿分节密集堆叠的单元节状向连续型锯齿状转变,最后发展为条形带状切屑。
关键词 磨削;切屑形貌;镍基单晶高温合金DD5;有限元分析中图分类号 TG58; TH161 文献标志码 A 文章编号 1006-852X(2023)06-0760-12DOI 码 10.13394/ki.jgszz.2022.0169收稿日期 2022-10-11 修回日期 2023-01-16作为航空发动机涡轮盘、转子叶片、涡轮导向叶片等关键零部件的主要材料,镍基单晶高温合金具有优异的物理和化学性能,例如抗蠕变性能、耐高温性能、抗冲击性能等[1-2]。
然而,这些优异的力学性能也给其加工制造带来了巨大困难,使其出现加工质量差、加工成本高等缺点[3]。
和其他传统加工方式相比,磨削加工具有加工质量好、精度高等特点,能够满足镍基单晶高温合金在特殊工况下的使用条件[4]。
但是,在磨削过程中镍基单晶高温合金仍出现磨削温度高、磨削力大、能量损耗高、加工效率低等难点[5]。
高温合金材料及其切削加工性

高温合金材料及其切削加工性随着科学技术和人类文明进步的需要,机械产品高性能、多功能、高质量要求非常剧烈,产品结构要求也更加紧凑,零件尺寸向微细化进展。
为满意上述要求,具有高硬度、高韧性和高耐磨性的难加工材料在产品中使用得越来越多。
以发电设备为例,汽轮机从30万一般机组到超超临界100万以及燃机等大功率高参数设备,耐高温、耐磨、耐酸的零部件材料采纳镍基高温合金或其它难加工材料的比例正在快速增加。
据不完全统计,十余年前企业以常规机组为主导产品时,所涉及的高温合金等难加工材料仅GH132等极少数的零件材料。
而目前,因火电、气电、核电、风电等新产品的特别要求,高强度不锈钢、抗低温脆性金属、高温耐热合金等十余种材料给切削加工带来了很大难题,其中高温合金就有近十个牌号,所涉及零件有十余种。
这里只就镍基高温合金孔加工问题进行技术探讨。
与一般钢材相比,高温合金的切削加工难点主要表现在以下几个方面:加工硬化倾向大。
比如GH4169未强化处理的基体硬度约HRC37,切削后表面产生0.03毫米左右的硬化层,硬度增加到HRC47左右,硬化程度高达27%。
加工硬化现象对刀具寿命有很大影响,通常会产生严峻的边界磨损。
2)切削力大。
高温合金强度比汽轮机常用合金钢材料高30%以上,在600℃以上的切削温度下,镍基高温合金材料的强度仍高于一般合金钢材料。
未强化处理的高温合金单位切削力在4000N/mm2以上,而一般合金钢仅2500N/mm2。
3)材料导热性差。
切削高温合金时产生的大量切削热由刀具承受,刀尖承受了高达800~1000℃的切削温度,在高温柔大切削力作用下,将导致切削刃产生塑性变形、粘结与集中磨损。
4)镍基合金主要成份为镍和铬,另外还添加有少量其它元素:钼、钽、铌、钨等,值得留意的是,钽、铌、钨等也是用来制造硬质合金(或高速钢)刀具的主要成分,用这些刀具加工高温合金会产生集中磨损和磨料磨损。
高温合金高速切削性能分析及参数优化

( h n iUnv ri fS in e& T c n lg ,X ’ n 7 0 ,C ia Sax ies y o ce c t e h oo y i a 2 1 1 hn ) 0
络 建 模 , 析 了切 削 速 度 、 给 量 、 削 深 度 、 削 时 分 进 切 切
究 。在各类 难 加 工 材 料 当 中 , 基 高 温 合 金 是 最 难 镍
加 工 的 材 料 之 一 , 有 硬 质 点 多 、 热 性 极 差 、 工 具 导 加
间及 冷却 液 等 因 素 对 切 削 过 程 的影 响 , 通 过 涂 层 并 刀具 的 高 速 切 削试 验 对 人 工 神 经 网 络 模 型 进 行 验 证 , 到 与 试 验 相 符 的 结 果 ; 尔 滨 工 业 大 学 梁 作 得 哈 斌 等 对 G 4 6 H 19进 行 了高速 铣 削试 验 , 出 了切 削 得 力 随切削 速度 V 每齿 进 给 量 . 铣 削 深 度 a 、 、 和 铣 削 宽度 a 的变化 规律 。
T eep r n rsl lb sdt esnby sl t h i s edmahnn ut gp rm tr. h x ei t eu swi eue orao a l e c teh曲-p e c i gctn aa ees me t l e i i
K e r s:h g s e u tn ;c ti rm e es e e i lo ih ;o i i y wo d ih-pe d c tig u tngpaa t r ;g n tc ag rt m ptm ze
参数 的选择提 供 了参 考和依 据 。 关键词 : 高速切 削 ; 削参数 ; 切 遗传 算 法 ; 优化
Inconel600的切削加工
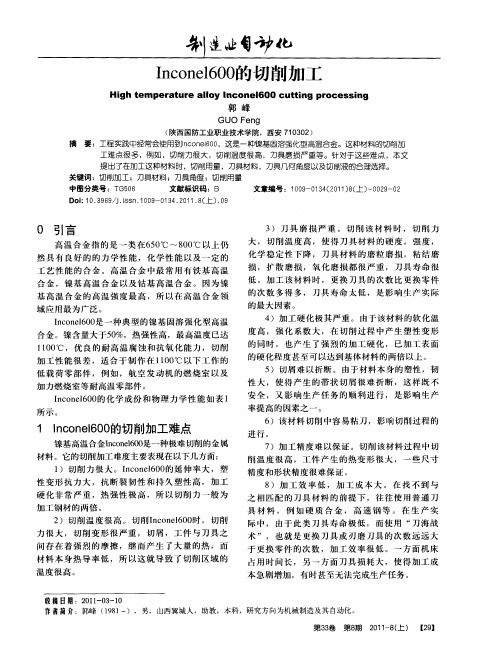
Icnl0 的切 削加工 no e60
H i em per ur l y n gh t at e alo I conel 600 cut i ocess n t ng pr i g
郭 峰
GU0 e g F n
( 陕西国防工业职业技术学院 ,西安 7 0 0 ) 13 2
之 相 匹 配 的刀 具 材 料 的 前 提 下 , 往 往 使 用 普通 刀
材料 。它的切 削加 工难度主 要表现在 以下几方面 : 1 )切 削 力很 大 。Ic n l0 的延 伸 率 大 ,塑 n o e6 0
性 变 形 抗 力 大 ,抗 断 裂 韧 性 和 持 久 塑 性 高 ,加 工 硬 化 非 常 严 重 ,热 强 性 极 高 ,所 以 切 削 力 一般 为
进行。
1 Ic n l0 的切 削加 工难点 n o e6 0
镍基高 温合 金Icnl0 是一种极难切 削 的金属 no e 0 6
7 )加 工 精 度 难 以保证 。切 削该 材 料过 程 中切 削 温 度 很 高 ,工 件 产 生 的 热 变 形 很 大 ,一 些尺 寸 精度 和 形状 精度 很难 保证 。 8 )加 工 效 率 低 ,加 工 成 本 大 。在 找 不 到 与
中图分类号 :T 5 6 @ 0 文献标识码 :B 文章编号 :1 0 —0 3 ( 0 1 8上 ) 0 9 2 9 1 4 2 1 ) ( ~0 2—0 0
D i1 .9 9 Jis .0 9 1 4 21 .( ) 0 o : 3 6/ . n 1 0 -0 3 .0 1 8上 . 9 0 s
温度 很高 。
本 急剧增 加 ,有 时甚 至无 法完 成生 产任务 。
镍基高温合金的切削性能及切削参数优化

镍基高温合金的切削性能及切削参数优化镍基高温合金是一种在高温环境下具有优异性能的材料,被广泛应用于航空、航天和能源等领域。
然而,由于其高硬度、高强度和高热稳定性,切削镍基高温合金是一项具有挑战性的任务。
因此,研究镍基高温合金的切削性能并优化切削参数对于提高切削效率和工件质量具有重要意义。
首先,镍基高温合金的切削性能受材料本身的特性影响。
镍基高温合金具有较高的硬度和强度,因此切削过程中会产生较大的切削力和切削温度。
同时,高温合金还具有一定的塑性变形能力,这会导致切削刃具的磨损加剧。
因此,切削镍基高温合金需要选择合适的切削刃具和切削液,并采取适当的切削策略,以减小切削力和切削温度,延长刀具寿命。
其次,切削参数的选择对镍基高温合金的切削性能具有重要影响。
切削速度、进给速度和切削深度是常用的切削参数。
在切削速度方面,较高的切削速度有助于提高切削效率,但过高的切削速度会导致刀具磨损加剧和切削表面质量下降。
进给速度的选择应考虑到切削力和切削温度的控制,较低的进给速度可以减小切削力和切削温度,但会降低切削效率。
切削深度的选择应根据工件的要求和刀具的承载能力进行合理确定。
为了优化切削参数,可以采用试验和数值模拟相结合的方法。
通过切削试验,可以获得切削力、切削温度和切削表面质量等关键参数,并评估切削性能。
同时,利用数值模拟方法,可以对切削过程进行仿真,预测切削力和切削温度的变化规律,为切削参数的优化提供依据。
综上所述,镍基高温合金的切削性能及切削参数优化对于提高切削效率和工件质量具有重要意义。
通过选择合适的切削刃具和切削液,以及合理调整切削参数,可以降低切削力和切削温度,延长刀具寿命,同时提高切削效率和工件表面质量。
未来的研究还应进一步探索切削机理和切削参数的优化方法,以满足高温合金在不同应用领域的需求。
镍基合金的加工和热处理

镍基合金的加工和热处理
首先,镍基合金的加工包括锻造、热轧、冷拔、热处理等工艺。
在加工过程中,要注意控制温度、变形速率和变形量,以确保材料
的组织和性能得到良好的保持。
特别是在高温合金的加工过程中,
要注意防止过热和过冷,避免产生裂纹和变形不均匀的情况。
其次,镍基合金的热处理是影响材料性能的重要环节。
常见的
热处理工艺包括固溶处理、时效处理等。
固溶处理可以消除材料中
的过饱和固溶相,提高材料的塑性和韧性;时效处理则可以在固溶
处理的基础上,进一步沉淀出合金元素的弥散相,提高材料的强度
和耐久性。
此外,镍基合金的加工和热处理还需要考虑到材料的成分、工
艺参数和设备条件等因素。
合理的工艺设计和严格的工艺控制可以
有效地提高镍基合金的加工质量和产品性能。
总之,镍基合金的加工和热处理是一个复杂而关键的工艺过程,对于材料的性能和使用寿命有着重要的影响。
通过合理的工艺设计
和严格的工艺控制,可以有效地提高镍基合金的加工质量和产品性能,满足不同领域对于高温合金材料的需求。
- 1、下载文档前请自行甄别文档内容的完整性,平台不提供额外的编辑、内容补充、找答案等附加服务。
- 2、"仅部分预览"的文档,不可在线预览部分如存在完整性等问题,可反馈申请退款(可完整预览的文档不适用该条件!)。
- 3、如文档侵犯您的权益,请联系客服反馈,我们会尽快为您处理(人工客服工作时间:9:00-18:30)。
目录•镍基合金的特点和用途•硬质合金刀具加工镍基合金研究•陶瓷刀具加工镍基合金研究•CBN刀具加工镍基合金研究镍基合金的特点和用途•镍基合金性能特点–镍含量>50%,一般在固溶状态使用,基体为致密的固溶体,同时含有大量金属碳化物硬质点以及金属间化物的沉淀相;–室温强度>1400MPa,900°C时仍>300MPa,在137MPa应力下1000小时的蠕变温度达到1100°C,具有良好的相稳定性,良好的抗疲劳、腐蚀、氧化能力,导热系数低于45钢的1/3;镍基合金的特点和用途•镍基合金用途及工况–主要应用于航空发动机及燃气轮机的热端部件,如涡轮叶片、涡轮盘、机匣等部件:•涡轮前温度达1700~1750K,旋转速度达13000~16000rpm,叶尖速度300m/s以上,零件既要轻又在高温下承受极端载荷镍基合金的特点和用途•发动机镍基合金零件毛坯种类–锻造毛坯:涡轮盘、转子叶片等主承力零件;–板焊毛坯:机匣、火焰筒等–铸造毛坯:叶片、静子叶环、机匣–粉末冶金:涡轮盘–定向结晶、单晶铸件:涡轮叶片。
镍基合金的特点和用途•镍基合金的加工要求–强度高,尤其是高温强度高,固溶体组织加工硬化严重,弥散的硬质点提高变形抗力,造成刀具磨料磨损,导热系数低,加工难度高,对刀具性能要求极高;–由于航空发动机轻量化的要求,安全系数接近甚至等于1,材料强度利用到极致,制造精度有严格要求;–工作在高温、大应力、动载荷条件下,对零件表面质量有极高要求,零件表面粗糙度、加工残余应力、组织和缺陷对零件寿命极其重要;–薄壁机匣、薄壁盘、薄叶片容易产生加工变形,变形控制成为制造过程的关键技术之一;–单晶叶片的加工对刀具、切削用量有特殊要求,以防加工产生多晶化倾向。
硬质合金刀具加工镍基合金研究•实验条件–刀具:•PVD-TiAlN涂层;基体成分:94% WC+6% Co;–工件:•镍基高温合金GH4169棒料,固溶时效,40HRC;–切削液:•水溶性切削液,浓度:8%–切削用量•切削速度v (m/min):58,82,115;•进给量f(mm/r):0.1,0.13,0.2;•切削深度a p(mm):1.2,1.9,2.4。
硬质合金刀具加工镍基合金研究•磨损曲线硬质合金刀具加工镍基合金研究•磨损机理–磨料磨损•工件材料的硬质点划擦刀具,产生磨料磨损,以平行于划擦方向的并列沟槽为特征。
•GH4169对刀具较强的粘附倾向,切削过程中在刀具表面经常覆盖着稳定的粘结层,保护了刀具,抑制了磨料磨损;•只有在前刀面上偶尔观察到沟槽,但后刀面难见磨料磨损的证据。
硬质合金刀具加工镍基合金研究–扩散磨损•跨越刀-工界面的线扫描显示出两侧成份的梯度变化,工件材料中的Ni、Fe,Cr元素以及刀具材料中的W元素浓度的变化发生在界面附近1~2µm左右;•在距离界面更远的部位进行区域能谱分析,也发现了W的存在;•上述证据表明刀-工界面确实发生了元素扩散,光滑的刀具表面也表征了扩散磨损的穿晶破坏特征。
硬质合金刀具加工镍基合金研究–粘接磨损•当粘接在刀具表面的工件材料脱落时,将刀具材料带走,产生粘接磨损;•发生粘接磨损的刀具表面呈现沿晶破坏的粗糙形貌;•切削理论认为,在中等切削速度下粘接磨损较大。
硬质合金刀具加工镍基合金研究•前、后刀面粘接层–EDS检测表明,粘结层的主要元素均来自于镍基高温合金硬质合金刀具加工镍基合金研究•不同切削速度下的粘接层–速度越高粘接越严重,而不是中等速度粘接严重切削速度82m/min切削速度115m/min硬质合金刀具加工镍基合金研究•粘接层沿刀刃变化–中部薄,均匀;边缘厚,不均匀。
切削速度82m/min硬质合金刀具加工镍基合金研究•缺口磨损–磨损带边缘产生大缺口,是刀具失效的主要原因;•粘接磨损(加氧缓解、加氩加剧)•温度梯度大,造成极大热应力;•切屑边缘划擦碰撞;•前次走刀加工硬化。
硬质合金刀具加工镍基合金研究•缺口的粘接磨损分析–大部份刀刃温度大于800°C,致使工件材料强度显著降低,塑性显著提高;–刀刃边缘温度急剧下降至700°C以下,工件强度升高,塑性变差;硬质合金刀具加工镍基合金研究•缺口的粘接磨损分析–刀刃中部的工件材料强度低、塑性好、剪切流动性好,易于形成薄粘接层,保护刀刃;–缺口部位温度急剧下降,强度升高,塑性降低,流动性变差,粘接层变厚,剪切力造成较大弯矩,界面产生拉应力;硬质合金刀具加工镍基合金研究–薄粘接层处剪切流动性好,剪切抗力低,刀具应力较小;–厚粘接层处剪切力大,还有弯矩的共同作用,刀具承受较大的剪应力和拉应力,容易产生晶粒团脱落,形成沿晶破坏的粗糙表面。
硬质合金刀具加工镍基合金研究•硬质合金刀具磨损机理小结–磨料磨损特征不明显,刀具大部分磨损区被工件材料粘接层复盖,保护刀具免受磨料磨损;–粘接磨损特征明显,可能是硬质合金刀具加工镍基合金时最主要的磨损机理;–扩散磨损有发生的迹象,稳定的粘接层有助于扩散磨损的发生。
–缺口磨损主要是由于边缘温度下降,工件材料强度提高而塑性降低,粘接层变厚,刀具在剪应力和拉应力共同作用下发生晶粒团的整体脱落。
•根据磨损机理分析提出对刀具材料的要求–粘接磨损是主要磨损机理,应该着力提高刀具材料晶界强度,抵抗晶粒团的沿晶破坏;–磨料磨损不明显,为提高强度可以适度牺牲刀具材料硬度。
陶瓷刀具加工镍基合金研究•陶瓷刀具分类–氧化铝基、氮化硅基、氧化铝+氮化硅、晶须增韧;–四种刀具材料在镍基合金加工中均有研究应用的报导,但以氧化铝+氮化硅、晶须增韧二种居多;•陶瓷刀具性能特点–常温硬度、高温硬度、耐磨性高于硬质合金;–与大多数工件材料化学亲和力小;–强度、韧性低于硬质合金,导热系数低;–抵抗机械冲击和热振的能力差;•应用条件–负前角、负倒棱,加强刃口强度;–高速度:200m/min~1000m/min,是硬质合金的数倍至数十倍;–多数情况采用干切削。
陶瓷刀具加工镍基合金研究•实验条件–刀具•氧化铝+氮化硅(Sialon):SX9,KY1540•晶须增韧(Al2O3+SiC w):WG300,KY4300•氧化铝+碳化钛(Al2O3+TiC):LX21–工件:•镍基高温合金GH4169棒料,固溶时效,40HRC;–切削用量•切削速度为150m/min~370m/min,•进给量0.1~0.15mm/r•切削深度1mm陶瓷刀具加工镍基合金研究•磨损过程–后刀面VB磨损状况:Al2O3+SiC w好于SialonWG300-VB SX9-VB陶瓷刀具加工镍基合金研究•磨损过程–切深线磨损VN状况:Al2O3+SiC w差于SialonWG300-VN SX9-VN陶瓷刀具加工镍基合金研究•磨损机理–磨料磨损–刃部微崩–切深线沟槽磨损SX9v=200m/minf=0.15mm/r陶瓷刀具加工镍基合金研究•磨损机理–粘接磨损–破碎–剥落WG300v=370m/minf=0.1mm/r陶瓷刀具加工镍基合金研究•磨损机理–扩散磨损:粘接层Ni 、Fe 、Cr 含量远低于工件材料母材;–化学磨损:磨损带边缘富钛区,Ti 含量接近50%。
切削速度190m/min切削速度310m/minWG300陶瓷刀具加工镍基合金研究•磨损机理–采用310m/min切削速度,经过30S切削后的后刀面磨损WG300 KY4300 LX21 SX9 KY1540陶瓷刀具加工镍基合金研究•磨损特点–经过短期切削,晶须增韧陶瓷已形成显著缺口磨损,但后刀面其它位置磨损较小;–氧化铝-氮化硅陶瓷具有良好抗缺口磨损能力,但是其后刀面整体磨损较大;–氧化铝-碳化钛陶瓷的缺口磨损介于二者之间陶瓷刀具加工镍基合金研究–Sialon的导热系数、热膨胀系数、弹性模量较低,断裂韧性、强度较高;–同样热边界时温度更均匀,同样温差时胀缩更小,同样胀缩变形时应力更小,同样应力下更不易断裂和脆性破坏;–从Sialon陶瓷没有缺口磨损推论出:切深线处高温度梯度导致热应力增大,产生裂纹和脆性破坏,造成缺口磨损。
陶瓷刀具加工镍基合金研究•陶瓷刀具加工镍基合金小结–陶瓷刀具加工镍基合金的合理切削速度>200m/min,加工效率是硬质合金的3~6倍;–但加工镍基合金时陶瓷刀具的使用寿命较短,许多情况下为几分钟,虽然金属去除量不少,但仍影响陶瓷刀具的选用;–陶瓷刀具加工镍基合金时,磨料磨损、粘接磨损、扩散磨损、化学磨损都有发生,但影响寿命的主要原因是微崩、破碎、剥落等脆性损坏;–Sialon陶瓷具有良好抵抗切深线缺口磨损能力,但其磨损带整体磨损较大;Al2O3+SiCw陶瓷缺口磨损强度远大于磨损带其它部位;–切深线处高温度梯度导致热应力增大,产生裂纹和脆性破坏,造成缺口磨损。
CBN刀具加工镍基合金研究•CBN刀具特点–晶格结构与金刚石相似,硬度仅次于金刚石,晶体硬度8000~9000HV,聚晶体硬度3000~5000HV,高于陶瓷;–与Fe的化学亲和性低于金刚石,是可以加工黑色金属的最硬刀具;•CBN刀具的分类–按CBN含量分:CBN含量45~95%;–按粘接剂种类:金属粘接剂、陶瓷粘接剂、金属-陶瓷复合粘接剂–晶粒尺寸:普通晶粒、细晶粒、超细晶粒CBN刀具加工镍基合金研究•实验条件–工件材料:•GH4169,热处理状态为固溶时效,42HRC;–刀具:•郑钻KB91:PCBN+硬质合金基底•Sumitomo BNS800:整体PCBN•刀片RNGN 120400T02020,•前角为-6°;后角为6°,倒棱宽度0.2mm,倒棱角度-20°;–切削用量(铣削):•V=515, 615, 740, 890, 1065m/min•f z=0.03, 0.06, 0.09, 0.12 mm/z•a p=0.5, 0.7, 1.0 mm•a e=31.5 mm–测量值•VB、VN和缺口磨损宽度WCBN 刀具加工镍基合金研究•磨损实验:切削速度对刀具磨损的影响–在1065m/min 以下,速度升高,刀具磨损总体下降;–切深线磨损VN 低速下不十分明显,KB91高速下显示出缺口,BNS800始终不出现缺口;–KB91刀具的磨损总体小于BNS800;a p =0.5mm,a e =31.5mm0.61.21.82.433.64.24.85157408901065刀具磨损量(m m )v (m/min)VB VN W0.30.60.91.21.51.82.12.42.75156157408901065刀具磨损量(m m )v (m/min)VB VN W0.30.60.91.21.51.82.12.42.75156157408901065刀具磨损量(m m )v (m/min)VB VN WBNS800,f z =0.06mmKB91,f z =0.06mm KB91,f z =0.09mmCBN 刀具加工镍基合金研究•磨损实验:进给量对刀具磨损的影响–进给量增大,刀具磨损总体下降;–低速下缺口磨损不明显,高速下明显;–速度达到1065m/min 时磨损下降。