铝合金轧制工艺
铝合金轧制工艺

铝合金轧制工艺一. 实验目的:1.掌握板带轧机工作原理及设备操作过程。
2.学会轧制变形量的计算方法及安排道次变形量。
二. 轧制原理:轧制法是应用最广泛的一种压力加工方法,轧制过程是靠旋转的轧辊及轧件之间形成的摩擦力将轧件拖进轧辊缝之间并使之产生压缩,发生塑性变形的过程,按金属塑性变形体积不变原理,通过轧制,轧件厚度变薄同时长度伸长,宽度变宽。
见图1所示。
图1轧制前后轧件厚度的减少成为绝对压下量,用△h 表示,△h =h 1-h 2绝对压下量与原厚度之比成为相对压下量,用ε表示,ε=△h /h 1×100%, 轧制时轧件的长度明显增加,轧后长度与轧前长度的比值称为延伸系数用λ表示,λ=l 1/l 2。
由于轧带时轧件宽度变化不大,一般略而不计(Δb=b 2-b 1)。
ε、Δh和λ是考核变形大小的常用指标。
三. 实验内容:使用两辊板带轧机轧制AlCu合金试件,试件铸态毛坯尺寸:120×15.00×7(mm)。
经多道次轧制使熔铸台毛坯形成轧制态工件,轧制厚度由7mm轧至2mm,将其中一半轧件送到马弗炉时效处理,为下一实验做准备。
四.实验步骤:1.根据轧机传动系统图和轧制原理图结合轧机了解板带轧机的组成,熟悉其结构和轧制机理。
2.润滑各运动部件,启动电源空车运转。
3.按总变形量分配道次压下量,并调整压下装置。
4.喂料轧制,按道次测量并记录相关数据。
5.轧制加工完成关闭电源,快速退回压下装置。
6.清理轧机和工作地点。
7.拟写实验报告。
五.实验装置:图2 轧机基本结构六.实验数据及处理:七. 思考题:1.试述齿轮座(分动箱)的作用?齿轮箱位于辊与减速箱中间起连接传动作用,同时用它控制上下轧辊转速保 持一致2.分析压下量与咬入角之间关系。
]/)(1arccos[21D h h --=α为轧辊直径为咬入角、即为压下量、其中D )( 21αh h -根据实验原理的图示可知.。
铝合金铸轧工艺
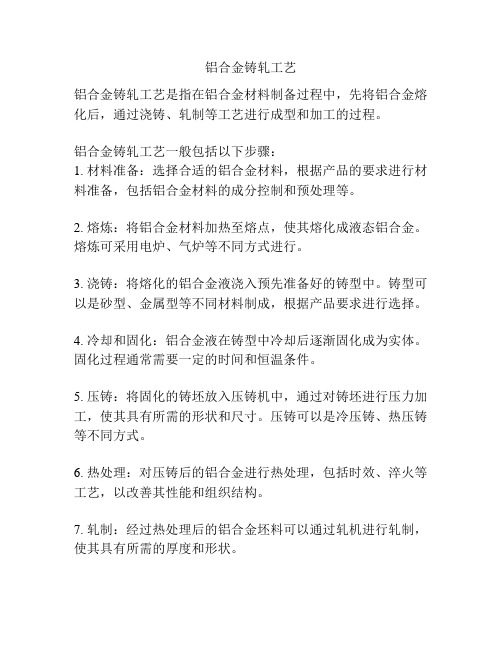
铝合金铸轧工艺
铝合金铸轧工艺是指在铝合金材料制备过程中,先将铝合金熔化后,通过浇铸、轧制等工艺进行成型和加工的过程。
铝合金铸轧工艺一般包括以下步骤:
1. 材料准备:选择合适的铝合金材料,根据产品的要求进行材料准备,包括铝合金材料的成分控制和预处理等。
2. 熔炼:将铝合金材料加热至熔点,使其熔化成液态铝合金。
熔炼可采用电炉、气炉等不同方式进行。
3. 浇铸:将熔化的铝合金液浇入预先准备好的铸型中。
铸型可以是砂型、金属型等不同材料制成,根据产品要求进行选择。
4. 冷却和固化:铝合金液在铸型中冷却后逐渐固化成为实体。
固化过程通常需要一定的时间和恒温条件。
5. 压铸:将固化的铸坯放入压铸机中,通过对铸坯进行压力加工,使其具有所需的形状和尺寸。
压铸可以是冷压铸、热压铸等不同方式。
6. 热处理:对压铸后的铝合金进行热处理,包括时效、淬火等工艺,以改善其性能和组织结构。
7. 轧制:经过热处理后的铝合金坯料可以通过轧机进行轧制,使其具有所需的厚度和形状。
8. 退火处理:通过对轧制后的铝合金进行退火处理,消除残余应力,改善其机械性能。
9. 表面处理:对轧制后的铝合金进行酸洗、氧化等表面处理,以提高其表面质量和耐腐蚀性能。
10. 检验和包装:对成品进行检验,包括外观检查、尺寸测量、性能测试等,然后进行包装和贮存。
铝合金铸轧工艺可以根据具体产品的要求进行调整和改进,在不同的铝合金材料、铸型和轧制设备等条件下,工艺参数和工艺流程也会有所差异。
铝热轧工艺流程

铝热轧工艺流程铝热轧是一种常见的金属加工工艺,用于制造各种铝合金材料。
热轧是指将铝坯加热到一定温度后,在轧机上进行塑性变形,从而得到所需的板材、带材或形状复杂的铝材产品。
下面将介绍铝热轧的工艺流程。
1. 铝坯准备铝坯是铝热轧的原材料,通常为铝合金坯料。
首先,需要对铝坯进行清洁处理,去除表面的氧化物和杂质。
然后,根据需要的材料规格,将铝坯切割成适当的尺寸。
切割后的铝坯应进行表面清洁,以确保热轧过程中的质量。
2. 加热加热是铝热轧的关键步骤之一。
铝坯经过清洁后,需要将其加热到合适的温度。
加热温度取决于铝合金的成分和所需的板材性能。
通常,加热温度在400°C至500°C之间。
加热的目的是使铝坯达到塑性变形的条件,减小轧制力和提高产品的成形性能。
3. 轧制在加热后,铝坯被送入轧机进行塑性变形。
轧机主要包括一对或多对辊子,通过对铝坯进行挤压和拉伸,使其产生塑性变形。
轧制过程中,铝坯会逐渐变薄,形成所需的铝板或带材。
轧制过程中需要控制轧制力和轧制速度,以确保产品的尺寸精度和表面质量。
4. 冷却轧制后的铝板或带材需要进行冷却处理。
冷却可以通过自然冷却或水淬来实现。
冷却的目的是使铝材快速降温,固化其内部晶体结构,提高产品的机械性能和物理性能。
冷却后的铝材需要进行拉伸矫直,消除轧制过程中产生的应力和变形,使其达到平整度和尺寸精度的要求。
5. 表面处理冷却后的铝板或带材需要进行表面处理,以提高其表面质量和耐腐蚀性。
常见的表面处理方法包括酸洗、氧化和涂层等。
酸洗可以去除铝材表面的氧化物和杂质,提高其表面光洁度。
氧化可以形成一层氧化膜,增强铝材的耐腐蚀性。
涂层可以在铝材表面形成一层保护层,提高其耐磨性和耐腐蚀性。
6. 产品检验轧制和表面处理后的铝板或带材需要进行产品检验,以确保其质量符合要求。
常见的检验项目包括尺寸精度、表面质量、力学性能和化学成分等。
产品检验可以通过各种检测设备和方法进行,如尺寸测量仪、表面检测仪、拉伸试验机和光谱分析仪等。
铝合金冷轧及薄板生产技术
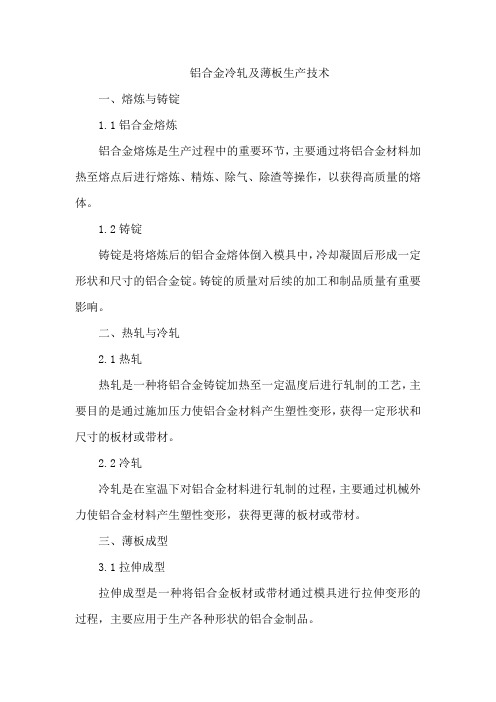
铝合金冷轧及薄板生产技术一、熔炼与铸锭1.1铝合金熔炼铝合金熔炼是生产过程中的重要环节,主要通过将铝合金材料加热至熔点后进行熔炼、精炼、除气、除渣等操作,以获得高质量的熔体。
1.2铸锭铸锭是将熔炼后的铝合金熔体倒入模具中,冷却凝固后形成一定形状和尺寸的铝合金锭。
铸锭的质量对后续的加工和制品质量有重要影响。
二、热轧与冷轧2.1热轧热轧是一种将铝合金铸锭加热至一定温度后进行轧制的工艺,主要目的是通过施加压力使铝合金材料产生塑性变形,获得一定形状和尺寸的板材或带材。
2.2冷轧冷轧是在室温下对铝合金材料进行轧制的过程,主要通过机械外力使铝合金材料产生塑性变形,获得更薄的板材或带材。
三、薄板成型3.1拉伸成型拉伸成型是一种将铝合金板材或带材通过模具进行拉伸变形的过程,主要应用于生产各种形状的铝合金制品。
3.2弯曲成型弯曲成型是一种将铝合金板材或带材通过模具进行弯曲变形的过程,主要应用于生产各种弯曲形状的铝合金制品。
四、表面处理4.1抛光抛光是通过机械或化学方法对铝合金表面进行加工,以获得光滑、亮泽的表面效果。
常用的抛光方法包括机械抛光、化学抛光和电化学抛光等。
4.2喷涂与电镀喷涂和电镀是在铝合金表面涂覆或镀覆其他金属或非金属材料,以提高铝合金制品的耐腐蚀性、美观度和功能性。
常用的喷涂和电镀材料包括油漆、塑胶、金属等。
五、质量检测5.1外观检测外观检测是对铝合金制品的表面质量进行检测的过程,主要通过目视、触觉等方法对制品的外观缺陷进行检查。
5.2尺寸检测尺寸检测是对铝合金制品的尺寸精度进行检测的过程,主要通过测量工具对制品的尺寸进行精确测量。
5.3力学性能检测力学性能检测是对铝合金制品的力学性能进行检测的过程,主要包括硬度、抗拉强度、屈服强度、延伸率等指标的检测。
六、环保与安全6.1有害物质控制铝合金冷轧及薄板生产过程中会产生一些有害物质,如废气、废水、废渣等,需要进行有效的控制和处理,以减少对环境和人体的危害。
5052铝合金板带材冷轧工艺的制定方法

5052铝合金板带材冷轧工艺的制定方法
制定5052铝合金板带材的冷轧工艺方法,可以按照以下步骤
进行:
Step 1: 材料准备
首先准备5052铝合金板带材,确保材料的质量符合要求。
Step 2: 实验设计
根据5052铝合金板带材的特性和要求,设计合适的实验方案。
考虑到冷轧机的参数和设备特点,确定冷轧的工艺参数。
Step 3: 实验测试
根据实验设计的方案,进行冷轧工艺参数的实验测试。
可以根据不同的冷轧机设备,调整不同的参数,如轧制温度、轧制压力、入模速度等。
Step 4: 分析结果
根据实验测试的结果,对冷轧工艺参数进行分析。
评估冷轧过程中板带材的质量和性能。
Step 5: 优化工艺
在实验测试结果的基础上,进行工艺参数的优化。
根据优化的结果,确定最佳的冷轧工艺参数。
Step 6: 生产应用
将优化后的冷轧工艺参数应用于5052铝合金板带材的生产中。
确保生产过程中的稳定性和可靠性。
Step 7: 质量控制
对生产的5052铝合金板带材进行质量检测和控制。
监测产品的物理性能和化学成分,以确保产品的质量符合要求。
以上是制定5052铝合金板带材冷轧工艺的一般方法。
具体的制定过程可能还需要根据实际情况进行调整和改进。
铝板的铸轧工艺

铝板的铸轧工艺
铝板的铸轧工艺是指将铝合金熔化后,通过铸造和轧制工艺制成不同尺寸和形状的铝板,以满足不同领域的使用需求。
铝板的铸造工艺包括连铸和直铸两种,其中连铸工艺是通过将熔化的铝合金倒入连续铸造机中进行连续铸造,制成厚度较薄的板材;而直铸工艺则是通过将熔化的铝合金倒入铸模中进行单次铸造,制成厚度较厚的板材。
铝板的轧制工艺包括热轧和冷轧两种,其中热轧工艺是将连铸或直铸的铝板在高温下进行轧制,以减小板材厚度并提高其力学性能;而冷轧工艺则是将热轧后的铝板在常温下进行轧制,以提高其表面质量和精度。
此外,还可以采用涂层、拉伸等工艺对铝板进行进一步加工,以满足特定的使用需求。
总的来说,铝板的铸轧工艺是一个复杂的过程,需要精密的设备和技术,并需要根据不同的需求和使用环境选择适合的工艺和材料。
铝板的应用范围广泛,包括航空航天、汽车制造、建筑装饰、电子产品等多个领域。
- 1 -。
铝加工热轧和冷轧工艺流程
铝加工热轧和冷轧工艺流程
铝加工热轧和冷轧的工艺流程如下:
热轧工艺流程:
1.材料剪切:按照所需尺寸剪切铝合金材料,为后续加工做准备。
2.预处理:
●清洗:去除剪切好的铝合金材料表面的污垢和氧化物。
●酸洗:将清洗后的材料浸泡在酸液中,以除去材料表面的氧化铝层。
●涂油:酸洗处理后,对铝板或铝卷进行涂油处理,防止表面氧化。
3.加热:
●加热炉:将预处理好的铝板或铝卷送入加热炉中,使材料达到适合轧制的温度。
●温度控制:确保材料在轧制过程中保持适宜的温度。
4.热轧:
●轧机设备:包括粗轧机、精轧机和细轧机,将加热后的铝板或铝卷送入轧机中进行轧制。
●轧制辊道调整:通过调整轧机辊道的间距和轧制力度,控制铝板或铝卷的厚度和表面质量。
●过程冷却:轧制过程中对铝板或铝卷进行冷却处理,保证产品性能和形状。
而冷轧工艺流程相对热轧要简单一些,通常包括:
1.开卷:将热轧后的铝卷开卷,送入冷轧机进行加工。
2.冷轧:通过冷轧机对铝材进行进一步加工,达到所需的厚度和精
度。
3.卷取:将冷轧后的铝材卷取成卷,方便后续的运输和储存。
请注意,具体的工艺流程可能因材料种类产品要求以及生产设备的不同而有所差异。
在生产过程中,还需要根据具体情况进行工艺参数的调整和优化,以确保产品质量和生产效率。
制表:审核:批准:。
5052铝合金板带材冷轧工艺的制定方法
5052铝合金板带材冷轧工艺的制定方法一、确定冷轧工艺流程1.1选择适合的原料:5052铝合金是一种常用的铝合金材料,具有优良的机械性能和耐腐蚀性。
在选择原料时,应确保其成分、组织和性能符合相关标准。
1.2确定变形程度:冷轧工艺的变形程度应根据产品规格、原料状态和轧机能力等因素来确定。
变形程度过小,产品质量不稳定;变形程度过大,产品易出现裂纹或断裂。
1.3控制加工速率:冷轧工艺的加工速率应根据原料状态、轧机能力和产品质量等因素来确定。
加工速率过快,产品质量不稳定;加工速率过慢,生产效率低下。
二、计算压下率2.1确定变形量:变形量应根据原料状态、产品规格和轧机能力等因素来确定。
变形量过小,产品质量不稳定;变形量过大,产品易出现裂纹或断裂。
2.2计算压下率数值:压下率是指单位时间内金属在轧制过程中的变形量与原始厚度的比值。
压下率数值应根据原料状态、产品规格和轧机能力等因素来确定。
2.3调整压下率以确保质量:在轧制过程中,应根据产品质量情况及时调整压下率。
当产品质量出现问题时,可通过调整压下率来改善产品质量。
三、判断是否需要中间退火3.1确定退火温度:退火温度应根据原料状态、产品规格和轧机能力等因素来确定。
退火温度过高或过低都会影响产品质量。
3.2控制退火时间和退火速率:退火时间和退火速率应根据原料状态、产品规格和轧机能力等因素来确定。
退火时间过长或过短都会影响产品质量。
3.3评估退火对产品性能的影响:在确定退火工艺参数时,应充分考虑其对产品性能的影响。
退火后产品的力学性能、耐腐蚀性等指标应符合相关标准。
四、计算各道次轧制后板带材的厚度4.1确定初始厚度:初始厚度应根据原料状态、产品规格和轧机能力等因素来确定。
初始厚度过小或过大都会影响产品质量和生产效率。
4.2计算各道次轧制后的厚度:在每道次轧制后,应及时测量并记录板带材的厚度。
各道次轧制后的厚度应符合相关标准或设计要求。
综上所述,制定5052铝合金板带材冷轧工艺时,应充分考虑原料状态、产品规格、轧机能力和产品质量等因素。
铝合金连续铸轧和连铸连轧技术
铝合金连续铸轧和连铸连轧技术
铝合金连续铸轧和连铸连轧技术
铝合金连续铸轧和连铸连轧技术是一种新兴的材料加工技术,它结合
了铸造和轧制的技术,可以实现铝合金材料的连续加工。
连续铸轧工艺,是把铝合金浇液料加热熔融,然后将熔体倒入熔体模,经过一段时间冷却固化后即可得到铸件,并经过轧制加工,从而提高
了铝合金的力学性能和外观质量。
连铸连轧技术,则是将熔体倒入铸轧机中,一次完成浇注和轧制,实
现熔体的连续加工,从而提高了产量和效率,并可以直接改变铸件的
尺寸和形状,并可以提高质量,降低生产成本。
连续铸轧和连铸连轧技术,不仅可以改善铝合金的力学性能,提高外
观质量,而且可以提高产量,降低成本,一定程度上满足大批量生产
的要求。
它已经被广泛应用于车辆制造、航空航天、电力行业等众多
领域,受到了社会的广泛认可。
总之,铝合金连续铸轧和连铸连轧技术是一种新兴的材料加工技术,
它的应用范围广泛,可以改善铝合金的力学性能,提高外观质量,提
高产量,降低成本,有助于提高生产能力和效率,更好地满足社会对
高品质铝合金产品的需求。
铝合金轧制工艺
铝合金轧制工艺嘿,咱今儿就来唠唠铝合金轧制工艺这档子事儿!你说铝合金这玩意儿,那可真是了不起啊!就好像是我们生活中的一位超级英雄,无处不在又神通广大。
从汽车到飞机,从建筑到日常用品,哪儿都有它的身影。
那铝合金是咋来的呢?这就得说到轧制工艺啦!想象一下,铝合金就像是一块面团,而轧制工艺呢,就是那双神奇的大手,把这块面团揉啊揉、擀啊擀,最后变成我们需要的各种形状和厚度。
这可不是随随便便就能搞定的事儿哦!就好像你做面条,得掌握好力度和技巧,不然那面条可就粗细不均啦!在轧制过程中,温度可是个关键因素呢!要是温度不合适,那铝合金可能就不乐意啦,要么硬得像块石头,要么软得像摊烂泥。
这就好比你做饭时火候没掌握好,不是烧焦了就是没熟。
所以啊,得把温度控制得恰到好处,就像哄孩子一样,得顺着它的脾气来。
还有啊,轧制的速度也很重要呢!太快了不行,太慢了也不行。
太快了就像你跑步时冲刺过猛,容易摔倒;太慢了呢,又好像蜗牛在爬,效率太低啦。
所以得找到那个最合适的速度,让铝合金乖乖地听话,变成我们想要的样子。
而且哦,轧制设备就像是个大力士,得足够强壮有力才能把铝合金制服。
要是设备不给力,那可就糟糕啦,就像一个虚弱的人想搬动大石头,根本不可能嘛!所以啊,得保证这些设备像钢铁侠一样厉害,才能搞定那些厉害的铝合金。
你说这铝合金轧制工艺是不是很神奇?它就像是一场魔术表演,把普通的铝合金变成了各种神奇的宝贝。
咱生活中的好多好东西可都离不开它呢!它让我们的生活变得更加丰富多彩,更加便捷舒适。
所以啊,咱可不能小瞧了这铝合金轧制工艺。
它虽然看起来不起眼,但实际上却是幕后的大功臣呢!它就像是一位默默奉献的工匠,用自己的双手打造出了无数的美好。
咱得好好感谢它,感谢它为我们的生活带来的这些改变和惊喜。
咋样,现在你是不是对铝合金轧制工艺有了更深的认识和了解啦?哈哈!原创不易,请尊重原创,谢谢!。
- 1、下载文档前请自行甄别文档内容的完整性,平台不提供额外的编辑、内容补充、找答案等附加服务。
- 2、"仅部分预览"的文档,不可在线预览部分如存在完整性等问题,可反馈申请退款(可完整预览的文档不适用该条件!)。
- 3、如文档侵犯您的权益,请联系客服反馈,我们会尽快为您处理(人工客服工作时间:9:00-18:30)。
铝合金轧制工艺
一. 实验目的:
1.掌握板带轧机工作原理及设备操作过程。
2.学会轧制变形量的计算方法及安排道次变形量。
二. 轧制原理:
轧制法是应用最广泛的一种压力加工方法,轧制过程是靠旋转的轧辊及轧件之间形成的摩擦力将轧件拖进轧辊缝之间并使之产生压缩,发生塑性变形的过程,按金属塑性变形体积不变原理,通过轧制,轧件厚度变薄同时长度伸长,宽度变宽。
见图1所示。
图1
轧制前后轧件厚度的减少成为绝对压下量,用△h 表示,△h =h 1-h 2绝对压下量与原厚度之比成为相对压下量,用ε表示,ε=△h /h 1×100%, 轧制时轧件的长度明显增加,轧后长度与轧前长度的比值称为延伸系数用λ表示,
λ=l 1/l 2。
由于轧带时轧件宽度变化不大,一般略而不计(Δb=b 2-b 1)。
ε、Δh
和λ是考核变形大小的常用指标。
三. 实验内容:
使用两辊板带轧机轧制AlCu合金试件,试件铸态毛坯尺寸:120×15.00×7(mm)。
经多道次轧制使熔铸台毛坯形成轧制态工件,轧制厚度由7mm轧至2mm,将其中一半轧件送到马弗炉时效处理,为下一实验做准备。
四.实验步骤:
1.根据轧机传动系统图和轧制原理图结合轧机了解板带轧机的组成,熟悉其结构和轧制机理。
2.润滑各运动部件,启动电源空车运转。
3.按总变形量分配道次压下量,并调整压下装置。
4.喂料轧制,按道次测量并记录相关数据。
5.轧制加工完成关闭电源,快速退回压下装置。
6.清理轧机和工作地点。
7.拟写实验报告。
五.实验装置:
图2 轧机基本结构
六.实验数据及处理:
七. 思考题:
1.试述齿轮座(分动箱)的作用?
齿轮箱位于辊与减速箱中间起连接传动作用,同时用它控制上下轧辊转速保 持一致
2.分析压下量与咬入角之间关系。
]/)(1arccos[21D h h --=α
为轧辊直径为咬入角、即为压下量、其中D )( 21αh h -
根据实验原理的图示可知.。