水泥生产工艺熟料煅烧
水泥的生产工艺流程
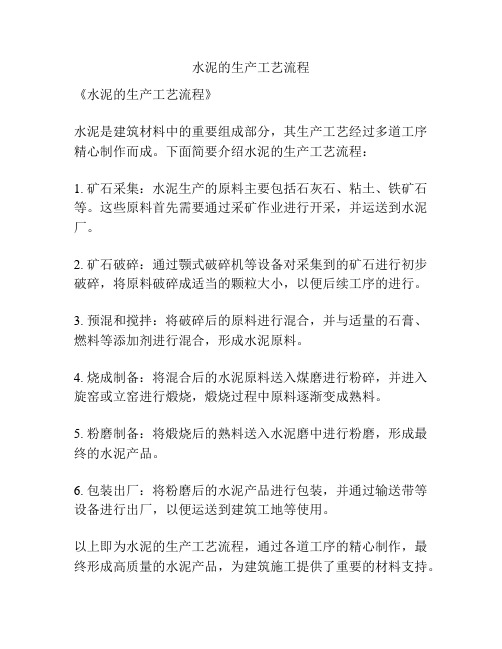
水泥的生产工艺流程
《水泥的生产工艺流程》
水泥是建筑材料中的重要组成部分,其生产工艺经过多道工序精心制作而成。
下面简要介绍水泥的生产工艺流程:
1. 矿石采集:水泥生产的原料主要包括石灰石、粘土、铁矿石等。
这些原料首先需要通过采矿作业进行开采,并运送到水泥厂。
2. 矿石破碎:通过颚式破碎机等设备对采集到的矿石进行初步破碎,将原料破碎成适当的颗粒大小,以便后续工序的进行。
3. 预混和搅拌:将破碎后的原料进行混合,并与适量的石膏、燃料等添加剂进行混合,形成水泥原料。
4. 烧成制备:将混合后的水泥原料送入煤磨进行粉碎,并进入旋窑或立窑进行煅烧,煅烧过程中原料逐渐变成熟料。
5. 粉磨制备:将煅烧后的熟料送入水泥磨中进行粉磨,形成最终的水泥产品。
6. 包装出厂:将粉磨后的水泥产品进行包装,并通过输送带等设备进行出厂,以便运送到建筑工地等使用。
以上即为水泥的生产工艺流程,通过各道工序的精心制作,最终形成高质量的水泥产品,为建筑施工提供了重要的材料支持。
水泥生料易烧性与熟料煅烧效率

引言在水泥生产的过程当中,熟料煅烧是非常重要的一部分内容。
提高水泥熟料煅烧的质量,保证水泥的质量,提高水泥的产量,降低生产水泥的消耗对于企业的发展来说具有非常重要的意义,然而要做到这三方面的内容不仅要控制水泥生产的过程以及相关技术的应用,也要控制水泥生产原料的质量。
对于水泥生产来说,生产原料的质量包括三大内容,分别是生料的易烧性,生料的均匀性以及生料的细度,在这三方面内容当中生料的易烧性会直接影响到水泥熟料的煅烧效率,直接影响到水泥的生产。
1、生料的易烧性基本概念在水泥的生产过程当中,原材料的燃烧过程会受到原材料本身的物质组成,颗粒大小,化学成分等因素的影响。
原材料的燃烧程度会直接影响到窑的产量,熟料的煤耗以及熟料的质量。
实际上水泥生料的易烧性是指水泥在煅烧的过程当中形成熟料的难易程度。
水泥生料的易烧性会受到原材料的物质组成,颗粒大小化学成分等因素的影响,如果易烧性好,则煅烧过程中所需要的温度较低,如果易烧性不好,则煅烧过程当中所需要的温度较高。
一般通过对水泥的原材料进行灼烧后,检验原材料当中的氧化钙含量来测定该原材料的易烧性的高低。
如果灼烧后氧化钙的含量过高,则说明原材料的易烧性很低,如果氧化钙的含量低则说明原材料的易烧性高。
2、影响生料易烧性的因素实际上对于水泥的灼烧来说,原材料的易烧性被材料的矿物组成、化学组成、颗粒组成、材料煅烧的温度和时间、材料出现的液相量、材料的塑料的相组成、煤灰的灰分以及窑的气氛这八个因素影响。
但是在这八个因素当中,原材料的矿物组成,化学组成和颗粒组成这三个因素会直接影响到材料的易烧性,其它因素的影响并非是由原材料本身的原因产生的。
而是在煅烧的过程当中煅烧的环境和煅烧的条件决定的。
在以往的研究过程当中,仅仅重视了原材料的化学组成和熟料的相液组成,这两方面的原因,而忽视了原材料的矿物质组成和颗粒组成。
通过实际的调查研究,能够明显的发现原材料的易烧性除了会受到化学组成的影响之外,材料的矿物质组成和颗粒组成也会影响到原材料的易烧性。
水泥熟料生产工艺及设备

湿法窑
熟料
硅质原料
石灰石
校正原料
破碎
单段锤式破碎机 预均化堆场
配料站 (新型水泥干法生料工艺流程图)
立式生料磨
生料均化库
贮库 干法窑
熟料
二、水泥熟料生产工艺
• 新型干法水泥生产技术,就是以悬浮预热和预分解技术为核心,把现代科学技术和工 原料矿山计算机控制网络化开采,原料预均化,生料均化,挤压粉磨,新型耐热、耐 以及IT技术等广泛应用于水泥干法生产过程,使水泥生产具有高效、优质、节约资源 保护要求和大型化、自动化、科学管理特征的现代化水泥生产方法。
Page 17
三、具体工艺流程-----煤粉磨
• 煤粉磨指从原煤仓、喂料控制、烘干粉磨、收尘到煤粉仓等生产贮存环节。其简要的
• 原煤 破碎机
煤预均化堆场
原煤仓
粉输送
分别到窑和分解炉燃烧器。
喂煤计量控制 煤粉烘干粉Page 18来自18Page 19
19
三、具体工艺流程-----熟料煅烧
• 熟料煅烧过程是指生料出均化库后的预热、煅烧和熟料冷却等环节。其简要生产流程
• 石灰石均化堆场 生料均化库储存。
原料计量配料系统及输送原料磨
空气输送斜槽
提升
Page 12
12
三、具体工艺流程-----生料制备
• 破碎:水泥生产过程中,大部分原料要进行破碎, • 破碎物料的目的在于提高烘干和粉磨的效率,同时亦便于物料的均化、运输和储存。
Page 13
三、具体工艺流程-----生料制备
干燥、预热 分解(85%~95%)
部分分解、固相反应、 烧结反应
熟料的冷却
预分解窑是20世纪70年代发展起来的一种煅烧工艺设备。它是在悬浮预 热器和回转窑之间,增设一个分解炉或利用窑尾烟室管道,在其中加入 30~60%的燃料,使燃料的燃烧放热过程与生料的吸热分解过程同时在悬 浮态或流化态下极其迅速地进行,使生料在入回转窑接受基本上完成碳 酸盐的分解反应,因而窑系统的煅烧效率在幅度提高。这种将碳酸盐分 解过程从窑内移到窑外的煅烧技术称窑外分解技术,这种窑外分解系统 简称预分解窑。
水泥熟料生产工艺及设备

1一物料层;2一漏斗;3一库底中心锥;4一收尘器 ;5-钢 制减压锥;6一充气管道;7一气动流量控制阀;8一电动流 量控制阀;9一套筒式生料计量仓;lO一固体流量计
干法生产:将原料先烘干后粉磨或同时烘干与粉磨成生料粉,而后喂 入干法窑内煅烧成熟料。但也有将生料粉加入适量水制成生料球,送 入立波尔窑内煅烧成熟料的方法,称之为半干法,仍属干法生产之一 种。
Page 5
LOGO
黏土堆场 泥浆库
Page 6
石灰石
单段锤式破碎机 碎石库
生料湿法粉磨系统
铁粉堆场 铁粉库
LOGO
三、具体工艺流程-----生料制备
原燃材料的储存设施一般为各种储存库,也有的为露天堆场或堆棚、 预均化设施兼储存等。
Page 14
LOGO
三、具体工艺流程-----生料制备
原燃料在储存、取用过程中,通过采用特殊的堆、取料方式及设施, 使原料或燃料化学成分波动范围缩小,为入窑前生料或燃料煤成分趋 于均匀一致而做的必要准备过程,通常称作原燃料的预均化。
粉磨:将各种原料(石灰石、粘土、铁粉)配料的混合物后在磨机内 磨成适合窑煅烧的的生料。
Page 17
LOGO
三、具体工艺流程-----煤粉磨
煤粉磨指从原煤仓、喂料控制、烘干粉磨、收尘到煤粉仓等生产贮存 环节。其简要的生产流程:
原煤 破碎机 煤预均化堆场 原煤仓 喂煤计量控制 煤 粉烘干粉磨 煤粉仓 煤粉输送 分别到窑和分解炉燃烧器。
水泥生产工艺及水泥熟料的形成
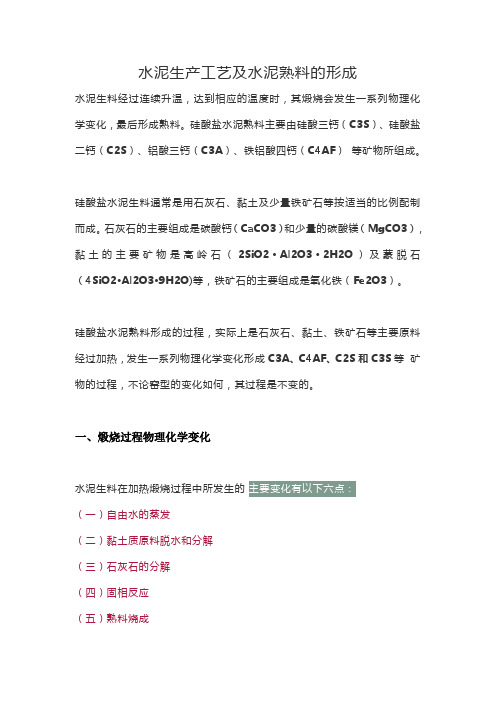
水泥生产工艺及水泥熟料的形成水泥生料经过连续升温,达到相应的温度时,其煅烧会发生一系列物理化学变化,最后形成熟料。
硅酸盐水泥熟料主要由硅酸三钙(C3S)、硅酸盐二钙(C2S)、铝酸三钙(C3A)、铁铝酸四钙(C4AF)等矿物所组成。
硅酸盐水泥生料通常是用石灰石、黏土及少量铁矿石等按适当的比例配制而成。
石灰石的主要组成是碳酸钙(CaCO3)和少量的碳酸镁(MgCO3),黏土的主要矿物是高岭石(2SiO2·Al2O3·2H2O)及蒙脱石(4SiO2·Al2O3·9H2O)等,铁矿石的主要组成是氧化铁(Fe2O3)。
硅酸盐水泥熟料形成的过程,实际上是石灰石、黏土、铁矿石等主要原料经过加热,发生一系列物理化学变化形成C3A、C4AF、C2S和C3S等矿物的过程,不论窑型的变化如何,其过程是不变的。
一、煅烧过程物理化学变化水泥生料在加热煅烧过程中所发生的(一)自由水的蒸发(二)黏土质原料脱水和分解(三)石灰石的分解(四)固相反应(五)熟料烧成(六)熟料的冷却(一)自由水的蒸发无论是干法生产还是湿法生产,入窑生料都带有一定量的自由水分,由于加热,物料温度逐渐升高,物料中的水分首先蒸发,物料逐渐被烘干,其温度逐渐上升,温度升到100~150℃时,生料自由水分全部被排除,这一过程也称为干燥过程。
(二)黏土质原料脱水和分解黏土主要由含水硅酸铝所组成,其中二氧化硅和氧化铝的比例波动于2:1~4:1之间。
当生料烘干后,被继续加热,温度上升较快,当温度升到450℃时,黏土中的主要组成高岭土(Al2O3·2SiO2·2H2O)失去结构水,变为偏高岭石(2SiO2·Al2O3)。
高岭土进行脱水分解反应时,在失去化学结合水的同时,本身结构也受到破坏,变成游离的无定形的三氧化二铝和二氧化硅,其具有较高的化学活性,为下一步与氧化钙反应创造了有利条件。
在900-950℃,由无定形物质转变为晶体,同时放出热量。
水泥制作流程
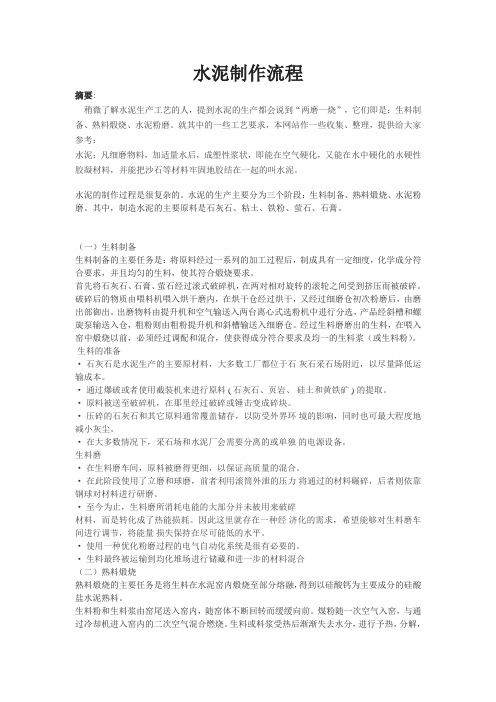
水泥制作流程摘要:稍微了解水泥生产工艺的人,提到水泥的生产都会说到“两磨一烧”,它们即是:生料制备、熟料煅烧、水泥粉磨。
就其中的一些工艺要求,本网站作一些收集、整理,提供给大家参考:水泥:凡细磨物料,加适量水后,成塑性浆状,即能在空气硬化,又能在水中硬化的水硬性胶凝材料,并能把沙石等材料牢固地胶结在一起的叫水泥。
水泥的制作过程是很复杂的。
水泥的生产主要分为三个阶段:生料制备、熟料煅烧、水泥粉磨。
其中,制造水泥的主要原料是石灰石、粘土、铁粉、萤石、石膏。
(一)生料制备生料制备的主要任务是:将原料经过一系列的加工过程后,制成具有一定细度,化学成分符合要求,并且均匀的生料,使其符合煅烧要求。
首先将石灰石、石膏、萤石经过滚式破碎机,在两对相对旋转的滚轮之间受到挤压而被破碎。
破碎后的物质由喂料机喂入烘干磨内,在烘干仓经过烘干,又经过细磨仓初次粉磨后,由磨出部御出。
出磨物料由提升机和空气输送入两台离心式选粉机中进行分选,产品经斜槽和螺旋泵输送入仓,粗粉则由粗粉提升机和斜槽输送入细磨仓。
经过生料磨磨出的生料,在喂入窑中煅烧以前,必须经过调配和混合,使获得成分符合要求及均一的生料浆(或生料粉)。
生料的准备·石灰石是水泥生产的主要原材料,大多数工厂都位于石灰石采石场附近,以尽量降低运输成本。
·通过爆破或者使用截装机来进行原料 ( 石灰石、页岩、硅土和黄铁矿 ) 的提取。
·原料被送至破碎机,在那里经过破碎或锤击变成碎块。
·压碎的石灰石和其它原料通常覆盖储存,以防受外界环境的影响,同时也可最大程度地减小灰尘。
·在大多数情况下,采石场和水泥厂会需要分离的或单独的电源设备。
生料磨·在生料磨车间,原料被磨得更细,以保证高质量的混合。
·在此阶段使用了立磨和球磨,前者利用滚筒外泄的压力将通过的材料碾碎,后者则依靠钢球对材料进行研磨。
·至今为止,生料磨所消耗电能的大部分并未被用来破碎材料,而是转化成了热能损耗。
水泥的制作流程(精)

水泥的制作流程水泥的制作过程是很复杂的。
水泥的生产主要分为三个阶段:生料制备、熟料煅烧、水泥粉磨。
其中,制造水泥的主要原料是石灰石、粘土、铁粉、萤石、石膏。
制造水泥的主要原料是石灰石(80%~90%,为质量分数,以下同)、粘土(10%~15%)和铁矿粉(1%~2%)。
为了控制凝结速率),还要在熟料中加入3%以下的石膏。
(1)水泥生料煅烧成熟料的物理、化学变化过程混合生料进入回转窑的上端,受热到100℃时,主要是水分蒸发,这一段叫干燥带。
干燥的生料继续在窑中前进,在与更热的气体相遇时,被加热到600℃左右,这时发生有机物燃烧和高岭土脱水。
此时,由于粘土可塑性减低,块料粉碎成粉料,这一带叫做“预热带”。
温度升高到900℃,石灰石发生分解,生成的CaO和粘土组成里的二氧化硅、氧化铝开始发生固态反应,这一段叫“分解带”。
当温度升高到1100℃以上,CaO和酸性氧化物的反应大为加快,反应主要是:3CaO+Al2O3—→3CaO·Al2O3(铝酸三钙)(1200℃时)这一段叫做“煅烧带”或称“放热反应带”。
温度到达1400℃左右,窑内物料开始烧结,部分开始熔融。
这时硅酸二钙仍保持为固态,它熔于熔融液里,与游离的CaO继续反应生成硅酸三钙(3CaO·SiO2)。
硅酸三钙以微小的结晶析出,即成熟料。
这一段称为“烧结带”。
经过烧结带后,熟料开始冷却而出窑,这一段叫做“冷却带”。
(2)熟料中加入石膏,为什么可以延缓水泥硬化速率?首先来分析一下水泥的硬化过程:水泥配上适当分量的水后,调和成浆,经过相当时间,凝固成块,最后成为坚硬如石的物体,这一过程叫做水泥的硬化。
硬化时发生下列反应3CaO·SiO2+2H2O=2CaO·SiO2·H2O+Ca(OH)2(水解)2CaO·SiO2+H2O=2CaO·SiO2+H2O(水化)3CaO·Al2O3+6H2O=3CaO·Al2O3·6H2O(水化)第一个反应生成的Ca(OH)2由于开始时量少而溶解,随着量的增多,变成饱和溶液而后析出胶体Ca(OH)2,引起水合硅酸钙和水合铝酸钙凝成凝胶状胶体,这时水泥具有可塑性。
水泥熟料的煅烧
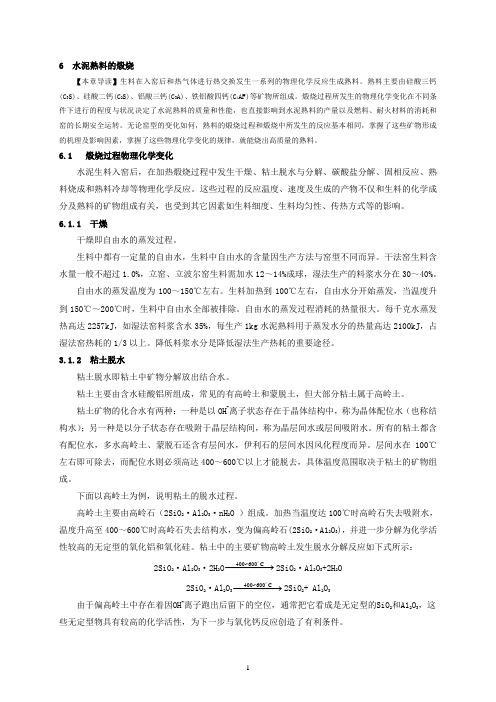
6 水泥熟料的煅烧【本章导读】生料在入窑后和热气体进行热交换发生一系列的物理化学反应生成熟料。
熟料主要由硅酸三钙(C 3S)、硅酸二钙(C 2S)、铝酸三钙(C 3A)、铁铝酸四钙(C 4AF)等矿物所组成。
煅烧过程所发生的物理化学变化在不同条件下进行的程度与状况决定了水泥熟料的质量和性能,也直接影响到水泥熟料的产量以及燃料、耐火材料的消耗和窑的长期安全运转。
无论窑型的变化如何,熟料的煅烧过程和煅烧中所发生的反应基本相同,掌握了这些矿物形成的机理及影响因素,掌握了这些物理化学变化的规律,就能烧出高质量的熟料。
6.1 煅烧过程物理化学变化水泥生料入窑后,在加热煅烧过程中发生干燥、粘土脱水与分解、碳酸盐分解、固相反应、熟料烧成和熟料冷却等物理化学反应。
这些过程的反应温度、速度及生成的产物不仅和生料的化学成分及熟料的矿物组成有关,也受到其它因素如生料细度、生料均匀性、传热方式等的影响。
6.1.1 干燥干燥即自由水的蒸发过程。
生料中都有一定量的自由水,生料中自由水的含量因生产方法与窑型不同而异。
干法窑生料含水量一般不超过1.0%,立窑、立波尔窑生料需加水12~14%成球,湿法生产的料浆水分在30~40%。
自由水的蒸发温度为100~150℃左右。
生料加热到100℃左右,自由水分开始蒸发,当温度升到150℃~200℃时,生料中自由水全部被排除。
自由水的蒸发过程消耗的热量很大。
每千克水蒸发热高达2257kJ ,如湿法窑料浆含水35%,每生产1kg 水泥熟料用于蒸发水分的热量高达2100kJ ,占湿法窑热耗的1/3以上。
降低料浆水分是降低湿法生产热耗的重要途径。
3.1.2 粘土脱水粘土脱水即粘土中矿物分解放出结合水。
粘土主要由含水硅酸铝所组成,常见的有高岭土和蒙脱土,但大部分粘土属于高岭土。
粘土矿物的化合水有两种:一种是以OH -离子状态存在于晶体结构中,称为晶体配位水(也称结构水);另一种是以分子状态存在吸附于晶层结构间,称为晶层间水或层间吸附水。
- 1、下载文档前请自行甄别文档内容的完整性,平台不提供额外的编辑、内容补充、找答案等附加服务。
- 2、"仅部分预览"的文档,不可在线预览部分如存在完整性等问题,可反馈申请退款(可完整预览的文档不适用该条件!)。
- 3、如文档侵犯您的权益,请联系客服反馈,我们会尽快为您处理(人工客服工作时间:9:00-18:30)。
➢ 3.1 新型干法煅烧工艺技术
➢ 3.1.1 悬浮预热技术
➢ 悬浮预热技术是在水泥中空窑的尾部(生料喂入端) 装设悬浮预热器(也称旋风预热器),使出窑废热气体 在预热器内通过,同时使入窑的低温生料粉分散于废热 气流之中,在悬浮状态下进行热交换,使物料得到迅速 加热升温后再入窑煅烧的一项技术。
➢ 传统的回转窑煅烧水泥熟料过程完全是在窑内进行 的,即生料喂入到窑内后的干燥→预热→碳酸盐分解→ 放热反应→熟料矿物的形成→冷却这六个过程完全是在 回转窑内完成的(见下图),使得窑体长度相对较长, 热量损失较大,窑的产量不高。
新型干法(现代水泥)回转窑
悬浮或立筒预热器
干法回转窑
加热机
立波尔回转窑(已被淘汰)
普通干法回转窑(逐渐被淘汰)
湿法回转窑(逐渐在改造成为新型干法窑)
二次风入窑 出窑熟料
不同类型回转窑各带划分
➢ 3.1.1.1 悬浮预热器单元组成
➢ 悬浮风预热器单元由换热管道、预热器、衬料、出风 管(废热气体将热量传给生料后排出)、下料管和锁风阀 (重锤)组成,见下图(C1代表第一级旋风预热器,以下 类推)。悬浮预热器系统由上述多个(四级串联的称为四 级旋风预热器,五级串联的称为五级旋风预热器)单元组 合构成:
热电偶 重锤
分解后的 生料入窑
窑体(窑尾)
分解炉、第四级预热器、 回转窑窑尾之间的关系
分解炉
重锤
喷煤嘴(3个) 三次风来自冷却机
窑体(窑尾)
物气料体放温温热度度反::应~~带11370000CC
回转窑
物气料体温温度度::13烧0~01成70带104C5~0~130冷0 C却物带料温度: ~1000 C
煤粉三次风
火焰
去分解炉
去煤磨烘干及 余热锅炉发电
➢ ④下料管及锁风阀:生料在上一级预热器内预热后, 经下料管进入下一级预热器,下料管口处装有撒料装置, 使物料迅速分散悬浮,加快换热速度。卸料阀具有锁风性 能,摆动灵活。
废热气体排出:350 C 生料
气体进入C2
换热管道
撒料板
内筒
来自的C2生料
C1(两个) 换热管道
C2
来自C4的
废热气流
C3
下料管
窑体 ZAB型立筒预热器
立筒(两个)
窑体 普列洛夫型逆流悬浮预热器
➢ 3.1.2 预分解技术
➢ 预分解技术(也称窑外分解技术)是在在悬浮预 热器和回转窑之间增加一个分解炉,将已经过悬浮预 热后的水泥生料,在达到碳酸盐分解温度之前进入到 分解炉内,与进入到炉内的燃料混合,在悬浮状态下 迅速吸收燃料的燃烧热,使生料中含量最多的碳酸盐 (主要是CaCO3及少量MgCO3)迅速分解成为氧化钙 (CaO及少量MgO)并放出二氧化碳(CO2)。在预 分解窑系统中,熟料煅烧所需要的60%~65%的燃料送 到分解炉内,并将其燃烧热迅速应用于生料中碳酸盐 的分解,分解率可达85%~95%。窑内只承担着放热反 应、熟料矿物的形成和冷却过程(见下图),减少了 窑内燃烧带的热负荷,大幅度提高了窑系统的生产效 率。
锁风阀
C4
生料预热后的
去增湿塔
温度:约800 C
预热后的生料进
入C4进一步预热
第三级预热器(C3)放大图
回转窑
旋风预热器及生料 和废热气流的走向
➢ 3.1.1.3 悬浮预热器的分类
➢ 悬浮预热器的种类较多,一般用三种方法进行分类, ➢ 见下表并参照下面的5个图:
按制造厂商命名分类 按热交换方式分类 按预热器组成分类
生料喂入
生料喂入
去增湿塔
去增湿塔 风机
多波尔型悬浮预热器
窑体
去增湿塔 风机
窑体
米亚格型悬浮预热器
窑体
维达格型悬浮预热器
废热气体排出去增湿塔
生料喂入
二级旋风筒 (1个)
一级旋风筒 (两个)
废热气体排出去增湿塔 除尘器(四个)
生料喂入
旋风筒(两个)
第一级立筒
去增湿塔 风机
第二级立筒
第三级立筒
去增湿塔
风机
新型干法水泥生产工艺
3.水泥熟料的煅烧
➢ 3 水泥熟料的煅烧
➢ 水泥熟料煅烧是生料制备之后的一道最重要的工序。 符合煅烧要求的水泥生料,从窑炉尾部的最上一级预热器 进入,沿着曲曲折折的路径、不断地与来自回转窑内部的 高温废气流进行热交换而得到预热后,进入分解炉内煅烧 至大部分碳酸盐分解,再经过最后一级预热器进入回转窑 中进行高温煅烧,至部分熔融后所得以硅酸钙为主要成分 的为硅酸盐水泥熟料;至完全或部分熔融所得以铝酸钙为 主要成分的为铝酸盐水泥熟料;所得以无水硫酸钙和硅酸 钙为主要成分的为硫铝酸钙水泥熟料;所得以无水硫酸钙 和硅酸二钙为主要成分的为铁铝酸钙水泥熟料;所得以氟 铝酸钙和硅酸钙为主要成分的为氟硫铝酸钙水泥熟料。熟 料煅烧的过程是一个连续加热、不断发生一系列的物理化 学反应的变化过程,最终将水泥生料煅烧成为熟料,经冷 却后送入储库,完成水泥熟料的煅烧任务。
干燥带 气体温度: 250~400 C 物料温度: ~200°C
废热气体排出 生料
预热带 碳酸盐分解带 ~800 C ~1600 C 750°C ~1000 C
放热反应带 ~1700 C ~1300 C
烧成带 ~1700 C~ 1300~1450~1300 C
冷却带 ~1000
窑头罩 煤粉
悬浮预热器 分解炉
生料
废热气体 C1
C2 C3
去增湿塔
分解炉
喷煤嘴 C4
三次风
入窑
回转窑 (窑尾)
物料
热气流
碳酸盐分解带 气体温度:~1600 C 物料温度:~1000 C
预热带 气体温度: ~800 C 物料温度:~750 C
气流C3
来自C3的生料
气流去C3
生料来自C3
分解炉
C4 喷煤嘴
热电偶
重锤
三次风
第四级 预热器(C4)
➢ ①预热器:也称旋风筒,是将气、料分离和影响预热 效率的主要部件。
➢ ②出风管:在第一级预热器(即C1)的顶部中心处, 通向增湿塔、除尘器的管道。
➢ ③换热管道:在第二、三、四级预热器的顶部连接管 道通向相对应的上一级预热器的管道,它承担着物料分散、 均布、锁风和换热的任务,管道内合适的风速可保证物料 悬浮于气流中更好的换热。
洪堡( )型
史密斯(F.L.Smidth)型
EVS/SVS型
以同流热交换为主 数级旋风筒组合
维达格(Wedag)型
盖波尔(Gepol)型 ZAB型 普列洛夫(Prepov)型
多波尔(Dopol)型 米亚格(Miag)型
以逆流热交换为主 以立筒组合为主
混
生料喂入