钢铁料消耗攻关总结
转炉钢铁料消耗分析与对策
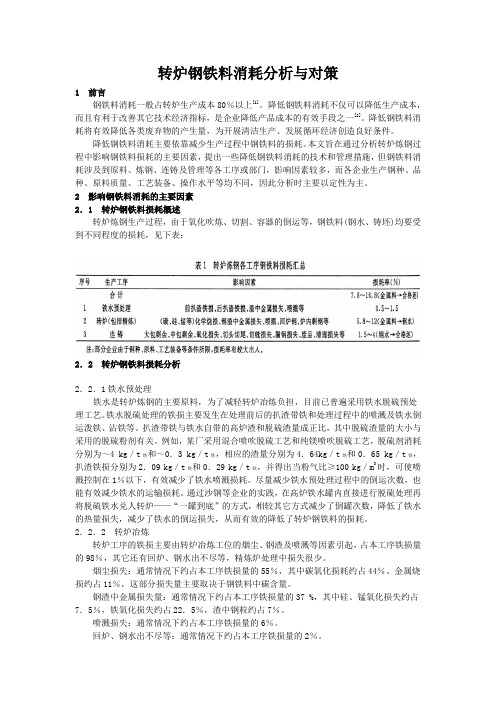
转炉钢铁料消耗分析与对策1 前言钢铁料消耗一般占转炉生产成本80%以上[1]。
降低钢铁料消耗不仅可以降低生产成本,而且有利于改善其它技术经济指标,是企业降低产品成本的有效手段之一[2]。
降低钢铁料消耗将有效降低各类废弃物的产生量,为开展清洁生产、发展循环经济创造良好条件。
降低钢铁料消耗主要依靠减少生产过程中钢铁料的损耗。
本文旨在通过分析转炉炼钢过程中影响钢铁料损耗的主要因素,提出一些降低钢铁料消耗的技术和管理措施,但钢铁料消耗涉及到原料、炼钢、连铸及管理等各工序或部门,影响因素较多,而各企业生产钢种、品种、原料质量、工艺装备、操作水平等均不同,因此分析时主要以定性为主。
2 影响钢铁料消耗的主要因素2.1 转炉钢铁料损耗概述转炉炼钢生产过程,由于氧化吹炼、切割、容器的倒运等,钢铁料(钢水、铸坯)均要受到不同程度的损耗,见下表:2.2 转炉钢铁料损耗分析2.2.1铁水预处理铁水是转炉炼钢的主要原料,为了减轻转炉冶炼负担,目前已普遍采用铁水脱硫预处理工艺。
铁水脱硫处理的铁损主要发生在处理前后的扒渣带铁和处理过程中的喷溅及铁水倒运泼铁、沾铁等。
扒渣带铁与铁水自带的高炉渣和脱硫渣量成正比,其中脱硫渣量的大小与采用的脱硫粉剂有关。
例如,某厂采用混合喷吹脱硫工艺和纯镁喷吹脱硫工艺,脱硫剂消耗分别为~4 kg/t铁和~0.3 kg/t铁,相应的渣量分别为4.64kg/t铁和0.65 kg/t铁,扒渣铁损分别为2.09 kg/t铁和0.29 kg/t铁,并得出当粉气比≥100 kg/m3时,可使喷溅控制在1%以下,有效减少了铁水喷溅损耗。
尽量减少铁水预处理过程中的倒运次数,也能有效减少铁水的运输损耗。
通过沙钢等企业的实践,在高炉铁水罐内直接进行脱硫处理再将脱硫铁水兑人转炉——“一罐到底”的方式,相较其它方式减少了倒罐次数,降低了铁水的热量损失,减少了铁水的倒运损失,从而有效的降低了转炉钢铁料的损耗。
2.2.2 转炉冶炼转炉工序的铁损主要由转炉冶炼工位的烟尘、钢渣及喷溅等因素引起,占本工序铁损量的98%,其它还有回炉、钢水出不尽等,精炼炉处理中损失很少。
钢铁企业上半年降本增效经验小结_降本增效工作总结
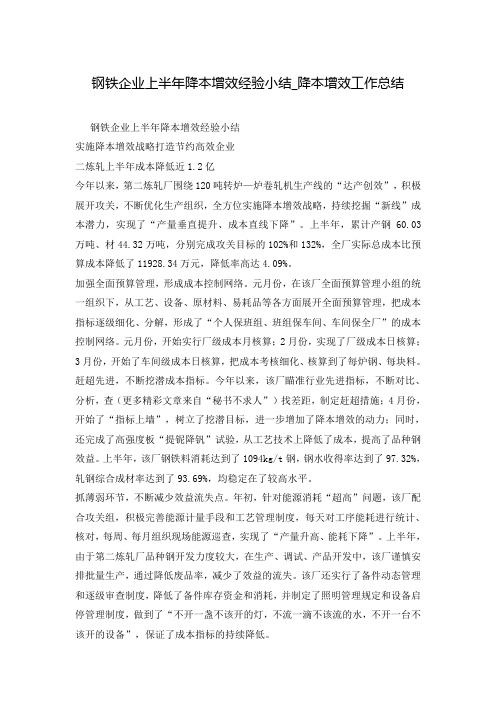
钢铁企业上半年降本增效经验小结_降本增效工作总结钢铁企业上半年降本增效经验小结实施降本增效战略打造节约高效企业二炼轧上半年成本降低近1.2亿今年以来,第二炼轧厂围绕120吨转炉—炉卷轧机生产线的“达产创效”,积极展开攻关,不断优化生产组织,全方位实施降本增效战略,持续挖掘“新线”成本潜力,实现了“产量垂直提升、成本直线下降”。
上半年,累计产钢60.03万吨、材44.32万吨,分别完成攻关目标的102%和132%,全厂实际总成本比预算成本降低了11928.34万元,降低率高达4.09%。
加强全面预算管理,形成成本控制网络。
元月份,在该厂全面预算管理小组的统一组织下,从工艺、设备、原材料、易耗品等各方面展开全面预算管理,把成本指标逐级细化、分解,形成了“个人保班组、班组保车间、车间保全厂”的成本控制网络。
元月份,开始实行厂级成本月核算;2月份,实现了厂级成本日核算;3月份,开始了车间级成本日核算,把成本考核细化、核算到了每炉钢、每块料。
赶超先进,不断挖潜成本指标。
今年以来,该厂瞄准行业先进指标,不断对比、分析,查(更多精彩文章来自“秘书不求人”)找差距,制定赶超措施;4月份,开始了“指标上墙”,树立了挖潜目标,进一步增加了降本增效的动力;同时,还完成了高强度板“提铌降钒”试验,从工艺技术上降低了成本,提高了品种钢效益。
上半年,该厂钢铁料消耗达到了1094kg/t钢,钢水收得率达到了97.32%,轧钢综合成材率达到了93.69%,均稳定在了较高水平。
抓薄弱环节,不断减少效益流失点。
年初,针对能源消耗“超高”问题,该厂配合攻关组,积极完善能源计量手段和工艺管理制度,每天对工序能耗进行统计、核对,每周、每月组织现场能源巡查,实现了“产量升高、能耗下降”。
上半年,由于第二炼轧厂品种钢开发力度较大,在生产、调试、产品开发中,该厂谨慎安排批量生产,通过降低废品率,减少了效益的流失。
该厂还实行了备件动态管理和逐级审查制度,降低了备件库存资金和消耗,并制定了照明管理规定和设备启停管理制度,做到了“不开一盏不该开的灯,不流一滴不该流的水,不开一台不该开的设备”,保证了成本指标的持续降低。
影响钢铁料消耗因素探讨与实践

2017年第2期LYS Science-Technology& Management・8・影响钢铁料消耗因素探讨与实践一炼轧厂黄伟豪摘要本文对影响钢铁料消耗的因素进行了具体分析。
通过改进入炉料结构、优化造渣工艺、减少转炉喷溅率、加强内部含铁资源回收,有效提高了转炉钢水收得率,降低了钢铁料消耗。
1 引言目前钢铁行业竞争日益激烈,钢材利润空间急剧压缩,为应对市场带来的挑战,必须采取措施来降本增效。
而钢铁料消耗占转炉炼钢生产成本的70%以上,且钢铁料指标的好坏直观体现了该厂综合技术水平、管理水平的高低,它关系到炼钢厂以挖潜增效为主的竞争活动的成败,因此降低钢铁料消耗对炼钢企业来说显得尤为迫切。
本文综合分析了涟钢一炼轧厂转炉线的实际生产情况,提出针对性的改进措施,付诸实施后,钢铁料消耗取得了明显进步。
2 炼钢线生产现状涟钢一炼轧厂转炉线现有公称容量100t氧气顶底复吹转炉3座,铁水预处理一座,吹氩站3座,2台6机6流弧形连铸机。
年产钢390万吨。
主要品种有HRB系列、CSP低碳钢、CSP普碳钢、低碳合金钢、高碳高强钢及其它新钢种。
3 钢铁料消耗计算口径与现状3.1 钢铁料消耗计算方法钢铁料消耗(kg/t)=入炉钢铁料(kg)÷合格钢产量(t);钢铁料消耗量(t)=铁水量(t)+生铁量(t)+废钢量(t)+矿石(t);废钢从来源上分为外购废钢和自产废钢,加生铁是由于炼钢能力大于高炉生产能力,铁水量不足,靠采购生铁块来发挥转炉产能。
3.2 钢铁料消耗现状2016年一炼轧厂的钢铁料实物消耗1079.31kg/t,较往年明显好转。
4 影响钢铁料消耗的主要因素涟钢6#高炉处于炉役后期,铁水质量较差,入炉铁水渣量、温度、成分波动大,转炉炉容比小,受入炉原材料质量以及入炉料结构的影响较大。
转炉冶炼过程易喷溅、喷溅渣含铁量大,熔剂消耗高,终渣TFe高,终点温度、成分控制较差导致回炉与中断连铸次数较多,过吹、高温现象较严重;连铸操作稳定性差,铸余钢水流失多,严重影响着钢铁料消耗的降低。
钢铁生产过程中的能源消耗如何降低

钢铁生产过程中的能源消耗如何降低钢铁行业作为国民经济的重要支柱产业,在为社会发展提供重要基础材料的同时,也面临着能源消耗巨大的挑战。
降低钢铁生产过程中的能源消耗,不仅对于企业降低成本、提高竞争力具有重要意义,也是实现可持续发展、应对全球能源危机和环境压力的必然要求。
在钢铁生产的各个环节中,都存在着不同程度的能源消耗。
首先是原料准备阶段,包括矿石开采、选矿和运输等。
矿石的开采需要消耗大量的电能和燃料,而选矿过程中的破碎、磨矿等作业也需要消耗不少能源。
在运输环节,长距离的运输会增加能源的消耗。
接下来是炼铁环节,这是钢铁生产中能源消耗最大的部分之一。
高炉炼铁需要消耗大量的焦炭作为还原剂和燃料,同时还需要消耗大量的热风来提供热量。
此外,高炉的鼓风系统、炉顶煤气余压回收装置等设备的运行也需要消耗电能。
炼钢环节同样消耗大量能源。
转炉炼钢需要消耗氧气、电能等,电炉炼钢则主要消耗电能。
在精炼过程中,如 LF 炉、RH 炉等设备的运行也需要消耗电能和热能。
轧钢环节的能源消耗主要来自加热炉,用于将钢坯加热到合适的轧制温度。
此外,轧机的运行也需要消耗电能。
为了降低钢铁生产过程中的能源消耗,可以从以下几个方面入手:一是采用先进的生产工艺和技术。
例如,推广使用高炉喷煤技术,可以减少焦炭的使用量,从而降低能源消耗。
在炼钢环节,采用转炉负能炼钢技术,通过回收转炉煤气和蒸汽等,实现能源的再利用。
另外,连铸连轧技术的应用,可以减少钢坯的加热次数,降低能源消耗。
二是优化设备运行和管理。
定期对设备进行维护和保养,确保设备处于良好的运行状态,减少设备故障和停机时间,提高设备的运行效率。
同时,采用先进的自动化控制系统,对生产过程进行精确控制,实现能源的合理分配和利用。
三是加强能源管理。
建立完善的能源管理体系,对能源的使用进行监测和分析,找出能源消耗的重点环节和部位,采取针对性的节能措施。
例如,通过安装能源计量仪表,对能源的消耗进行实时监测和统计,为能源管理提供数据支持。
影响钢铁料消耗的主要因素分析

影响钢铁料消耗的主要因素分析1前言钢铁料消耗指标是炼钢厂重要的经济技术指标,一般占生产成本的80~85%,对炼钢厂的成本有重要的意义。
钢铁料消耗国家规定的统计标准:转炉钢铁料消耗(kg/t钢)=[铁水+生铁+废钢铁量(kg)]/转炉合格产出量(t),其中:生铁包括高炉铁块、还原铁;废钢铁包括各种废钢、废铁等。
(行业惯例目前都以合格铸坯量代替转炉合格产出量)以下对影响钢铁料的主要因素进行梳理,由于涉及的因素较多,以定性分析为主。
2影响钢铁料消耗的主要因素2.1铁水预处理铁水脱硫处理的钢铁料损失主要发生在处理前后的扒渣带铁和处理过程中的喷溅及铁水倒运铁损失等。
扒渣带铁与铁水自带的高炉渣和脱硫渣量成正比,其中脱硫渣量的大小与采用的脱硫剂有关。
如复合喷吹脱硫工艺,脱硫剂消耗为4 kg/t铁,渣量为4.64kg/t铁,扒渣铁损为2.09 kg/t铁。
2.2转炉冶炼转炉的钢铁料损失主要由冶炼的烟尘、钢渣及喷溅等因素引起,占本工序损失量的98%,回炉、钢水出不尽等占一部分。
烟尘损失:通常情况下占转炉工序损失量的55%,其中碳氧化损耗约占44%、金属烧损约占11%,这部分损失量主要取决于钢铁料中碳含量。
钢渣中金属损失量:通常情况下占损失量的37 %,其中硅、锰氧化损失约占7.5%,铁氧化损失约占22.5%,渣中钢粒约占7%。
喷溅损失:通常情况下约占6%。
回炉、钢水出不尽等:通常情况下约占2%。
转炉冶炼是一个氧化过程,减少氧化损失是减少钢铁料损失的关键。
氧化损失中,一类为必要损失,无法避免,如碳、硅、锰等元素氧化,以获得化学热,这部分损失为必要损失。
另一类氧化损失是可以避免或减少的,如转炉后吹。
2.3 连铸连铸的钢铁料损失主要包括氧化铁皮、切割损失、切头切尾、中包注余、大包注余、漏钢、废品、清理损失等。
其中中包注余、切头切尾、切割损失等因素,占连铸工序钢铁料损失量的80%。
中包注余:通常约占连铸工序损失量的40%。
钢铁企业达产创效攻关总结(2篇)

钢铁企业达产创效攻关总结____吨转炉/炉卷轧机生产线“达产创效”攻关组自元月____日正式成立以来,各专业攻关小组都能严格按照公司要求、主动融入到第二炼轧厂的系统管理中去,不分彼此、精诚团结,相互配合、形成合力,围绕“达产创效”这一中心任务,全方位开展攻关工作,制订实施了详细、准确、可操作性强的管理措施和考核办法,理顺了各环节之间的相互关系,确保了各项攻关措施落到实处,圆满完成了攻关任务。
主要攻关成绩如下:--实现了达产攻关目标。
____-____月份炼钢系统产钢____万吨,平均月产达到____万吨,其中____月份产钢____万吨,实现了达产目标,____月份产钢达到____万吨,____月份产钢达到____万吨,均超过设计月产能力。
轧钢系统累计入库钢板____万吨,平均月产钢____万吨,其中____月份入库量达到____万吨,超过了____万吨的达产目标。
--提前实现正边际贡献。
经财务部按____m3高炉成本水平计算,第二炼轧厂元月份边际贡献为-____万元,____月份即实现正边际贡献____万元,____月份实现正边际贡献____万元;____月份实现正边际贡献____万元;____月生产经营形势更好于____月份、预计边际贡献可达到____万元。
____-____月份全厂可累计实现正边际贡献____亿元以上,提前完成了公司要求的上半年实现正边际贡献的攻关目标。
--____月份开始实现盈利。
经财务核算按外购原材料实际采购价格和____m3高炉铁水实际成本计算,第二炼轧厂____月份吨材实现毛利____元,全月实现销售毛利润____万元;____月份吨材实现毛利润____元,实现总销售毛利润____万元;预计____月份可实现总销售毛利润____万元;并且吨材盈利水平已不低于兄弟单位。
即使按____m3高炉铁水实际成本计算,____月份仍可实现销售毛利润____万元,____月仍可实现销售毛利润____万元,____月仍可实现销售毛利润____万元。
影响钢铁料消耗主要原因学习和总结

影响钢铁料消耗主要原因学习和总结影响钢铁料消耗主要原因学习和总结在炼钢生产中,钢铁料消耗是炼钢生产总成本的关键,而转炉冶炼过程的钢铁料消耗在总的钢铁料消耗中也占有很大的比例。
因此抓好转炉冶炼的钢铁料成本对控制总成本起关键性的作用。
通过改进原料结构和炉前冶炼工艺,采用少渣炼钢工艺,控制喷溅,减少倒渣带钢减少后吹,降低吹损,提高一次拉碳率等有效措施来降低钢铁料消耗。
进7月份以来我对影响我车间钢铁料消耗的主要原因学习和总结如下;影响转炉钢铁料消耗的主要原因影响转炉钢铁料消耗的主要因素包括炉渣中的铁损失、降低吹损、喷溅及倒渣带钢的铁损失等。
为了减少转炉炼钢拉碳时出现的碳低磷高和碳高磷低成分不合后吹的造成吹损,降低钢铁料损耗,应采取合理的原料结构,稳定的装入量及合适的渣量和稳定的操作。
1.优化入炉原料结构在合适的用量范围内,通过增加矿石和铁皮球的用量,也就说的含铁冷料,可有效地减少铁水的消耗,从而降低钢铁料消耗,因此在实际操作中可加大含铁冷料的加入。
因为吹炼前期为满足前期脱磷条,需要大量的氧化铁,吹炼中期为避免反干,要求渣中含有适当的氧化铁,增加矿石消耗的工艺措施,降低钢铁料消耗。
实际生产中,由于铁皮球中SIO2含量较高,因此使用铁皮球产生的渣量大,造成渣中铁消耗较高,但是价格相对便宜,也可以少量食用。
为了尽量增加矿石的用量,提高矿石还原效果和减少吹炼过程中矿石加入量过多对冶炼稳定性的影响,在实际生产中,根据矿石的反应程度,在吹炼前、中期全部加完,在保证化渣效果和避免喷溅的情况下尽量早加和均匀加入矿石,以保证矿石化渣还原时间和效果。
吹炼中期矿石应分批次少量加入,避免集中加入,导致积聚过多的氧化铁造成的喷溅;吹炼后期严禁加入矿石,避免矿石加入过晚造成还原效果差和钢水的氧化性强脱氧不到位和对脱氧合金化的影响。
2.减少喷溅,降低终渣氧化铁(1)控制好熔池温度,吹炼前期温度不要过低,并防止突然的温降,保持熔池均匀升温,碳氧反应均衡进行,避免碳氧反应失衡造成爆发性的喷溅。
炼钢节能总结范文

炼钢节能总结范文引言炼钢是钢铁生产过程中最关键的环节之一。
随着全球资源的日益匮乏以及环境污染问题日益突出,炼钢过程中的能源消耗和碳排放已经成为一个重要的问题。
因此,炼钢节能已经成为钢铁行业的重要课题。
本文将从技术和管理两个方面,对炼钢节能进行总结,并提出相应的解决方案。
技术方面的节能措施1. 优化高炉燃料配比优化高炉燃料配比是最有效的炼钢节能措施之一。
通过合理调整燃料的种类和比例,可以提高高炉燃烧效率,减少能源消耗。
例如,可以增加高炉煤气的利用率,减少煤粉的使用量,达到节能减排的效果。
2. 使用高效节能的炼钢设备现代炼钢厂应当采用高效节能的炼钢设备,例如高炉煤气余热发电装置、脱硫装置、余热回收器等。
这些设备可以将炼钢过程中产生的热能和废气进行有效利用,从而减少能源消耗和环境污染。
3. 炼钢过程的自动化控制炼钢过程中的自动化控制可以提高炉况的稳定性,减少能源的浪费。
通过引入先进的控制系统,可以实现对炼钢过程各个环节的精确控制,从而减少炼钢过程中的能源损耗。
管理方面的节能措施1. 完善节能管理制度建立完善的节能管理制度是炼钢企业实施节能措施的前提。
制定科学的能源消耗标准、能源测量和统计方法,以及相应的考核机制,可以使企业的节能管理工作更加科学和有效。
2. 节能技术培训和推广加强炼钢技术培训和推广工作,提高员工对新节能技术的认识和掌握程度,能够更好地应用节能技术,进一步提高炼钢节能效果。
3. 加强能源监测和数据分析通过对能源的监测和数据分析,可以了解炼钢过程中的能源消耗情况,并找出能源消耗高的环节,采取相应的节能措施。
同时,对炼钢过程中的能源消耗进行动态跟踪,及时发现和纠正问题,提高能源利用效率。
结论炼钢节能是钢铁行业可持续发展的重要方向。
通过技术和管理的措施的综合运用,可以有效提高炼钢节能效果。
在技术方面,优化高炉燃料配比、使用高效节能的炼钢设备以及炼钢过程的自动化控制是有效的节能措施。
在管理方面,建立完善的节能管理制度、加强节能技术培训和推广以及加强能源监测和数据分析都能够进一步提高炼钢节能效果。
- 1、下载文档前请自行甄别文档内容的完整性,平台不提供额外的编辑、内容补充、找答案等附加服务。
- 2、"仅部分预览"的文档,不可在线预览部分如存在完整性等问题,可反馈申请退款(可完整预览的文档不适用该条件!)。
- 3、如文档侵犯您的权益,请联系客服反馈,我们会尽快为您处理(人工客服工作时间:9:00-18:30)。
钢铁料消耗攻关总结
目标设定:全年完成钢铁料消耗1087kg/t钢。
项目负责人:魏天会(转炉车间主任)
攻关过程介绍:
(1)任务来源:
钢铁料消耗是炼钢重要的一项经济技术指标,也是炼钢成本构成的主体,在一定程度上反应了炼钢厂技术操作和生产组织的水平,也直接体现了炼钢厂现代化程度和科学管理水平。
所以炼钢厂将降低钢铁料消耗作为一项攻关项目,降低生产成本。
此项攻关主要应用于转炉炼钢,通过对影响钢铁料消耗的原因分析,找出制约钢铁料消耗的因素,通过调整过程枪位和终点氧压,减少吹损,采用留渣操作,减少渣中铁量损失,增加过程含铁物料,提高金属收得率,改进连铸火焰切割机,减少铸坯切口,减少切损,降低钢铁料消耗。
(2)性能指标:
2011年全年,炼钢厂完成钢铁料消耗为1089kg/t钢。
通过本次攻关后,2012年
通过本次攻关活动,最终实现2012年1-11月份钢铁料消耗累计达到t钢,达到并超额完成了最初制定的1087kg/t钢的目标。
(3)攻关过程采取的主要措施:
①改善入炉铁水质量,采取留渣操作工艺;
②减少洒铁、洒钢、喷溅现象的发生;
③提高入炉冷料质量,增加自循环料的回收量;
④增加过程含铁物料数量,降低钢铁料消耗;
⑤提高连浇炉数,改造设备减少切损;
通过以上各项措施的实施,多措并举,最终实现了2012年钢铁料消耗较2011年的1089kg/t钢下降了t钢,使本次攻关取得圆满成功。
(4)项目经济效益计算:
2012年1-11月平均钢铁料消耗为t钢,较去年降低t钢。
按铁水占装入量的96%,废钢占装入量的4%,铁水单价为元,废钢单价为元,全年钢产量200万吨进行计算。
实际降本创效额=[1000*96%*+1000**4%)]*2000000
=1337万元
(5)攻关成功意义:
通过推广改技术,炼钢厂钢铁料消耗在稳步下降,该技术在转炉车间的应用已达到成熟程度。
降低钢铁料消耗是一项系统工程,炼钢厂通过扒渣和炉外脱S、P工艺,改善了入炉铁水条件;通过增加过程含铁物料的加入量,提高了金属收得率;通过对自循环料的控制等措施,实现了降低钢铁料消耗的目的,为企业的挖潜创效作出了较大的贡献。
至此,本次降低钢铁料消耗的攻关工作取得圆满成功,攻关成果对本厂意义重大,今后将继续坚持不懈的贯彻相关攻关工作,以促进炼钢厂生产工艺的不断完善。