刻蚀
集成电路工艺:刻蚀

1. 引 言
1.1刻蚀的概念
刻蚀:它是半导体制造工艺,微电子IC制造工 艺以及微纳制造工艺中的一种相当重要的步骤。 是与光刻相联系的图形化(pattern)处理的一 种主要工艺。所谓刻蚀,实际上狭义理解就是 光刻腐蚀,先通过光刻将光刻胶进行光刻曝光 处理,然后通过其它方式实现腐蚀处理掉所需 除去的部分。随着微制造工艺的发展;广义上 来讲,刻蚀成了通过溶液、反应离子其它机 械方式来剥离、去除材料的一种统称,成为微 加工制造的一种普适叫法。
4.2常用材料的湿法刻蚀
1.二氧化硅湿法刻蚀 采用氢氟酸溶液加以进行。因为二氧化硅可与室
温的氢氟酸溶液进行反应,但却不会蚀刻硅基材 及多晶硅。反应式如下:
SiO2 + 6HF= H2[SiF6] + 2H2O 由于氢氟酸对二氧化硅的蚀刻速率相当高,在制
程上很难控制,因此在实际应用上都是使用稀释 后的氢氟酸溶液,或是添加氟化铵(NH4F)作 为缓冲剂的混合液,来进行二氧化硅的蚀刻。
下层的Ti ➢ 金属铝的刻蚀步骤多,工艺复杂
4. 湿法刻蚀
4.1 湿法刻蚀的原理
湿法刻蚀是将被刻蚀材料浸泡在腐蚀液内进行腐蚀 的技术
这是各向同性的刻蚀方法,利用化学反应过程去除 待刻蚀区域的薄膜材料
湿法刻蚀,又称湿化学腐蚀法。半导体制造业一开 始,湿法腐蚀就与硅片制造联系在一起。现在湿法 腐蚀大部分被干法刻蚀代替,但在漂去氧化硅、除 去残留物、表层剥离以及大尺寸的图形腐蚀应用方 面起着重要作用。尤其适合将多晶硅、氧化物、氮 化物、金属与Ⅲ-Ⅴ族化合物等作整片的腐蚀。
干法刻蚀是各向异性刻蚀,用物理和化学方法, 能实现图形的精确转移,是集成电路刻蚀工艺的 主流技术。
各向同性刻蚀:侧向与纵向腐蚀速度相同 各向异性刻蚀:侧向腐蚀速度远远小于纵向腐蚀
第14章 刻蚀
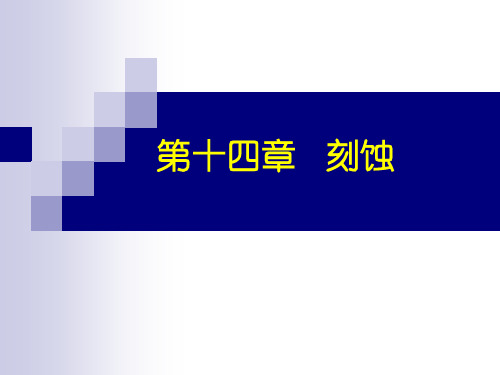
刻蚀类型 湿法刻蚀
干法刻蚀
侧壁剖面
各向同性
各向同性性 (depending on equipment &
parameters) 各向异性 (depending on equipment & parameters) 各向异性
锥形
硅槽
示意图
各种刻蚀剖面
三.刻蚀偏差
刻蚀偏差是指刻蚀以后线宽或关键尺 寸间距的变化。它通常是由于横向钻蚀 (undercut)引起的,但也能由刻蚀剖面 引起。
在表面
应
各向异性 刻蚀
衬底
各向同性刻蚀
阴极
化学和物理的干法刻蚀机理
物理刻蚀
溅射的表面材料
反应正离子轰 击表面
化学刻蚀
原子团与表面膜的表面 反应
副产物的解吸 附
各向异性刻蚀
各向同性刻蚀
12.2.1 刻蚀作用
作用方式:
化学:高活性基团与硅片发生化学反应,类似湿法刻蚀。 物理:带能离子通过电场加速,轰击硅片,类似溅射。 化学+物理:二者结合。
表面反应
反应
在干法刻蚀中, 刻蚀包括离子 溅射和活性元素 与硅片表面的反 应
各向异性
差/难以提高 (1:1) 高 一般/好
各向同性
一般/好(5:1 至100:1) 中等 差
各向同性
各向同性至 各向异性
好/很好
一般/高(5:1
(高于500:1) 至100:1)
低 非常差 -
中等 好/非常好
【例2】电子在反应离子刻蚀(RIE)和高密度等
式中,R0是空腔刻蚀的速率,A是刻蚀薄膜暴露 的面积,k是跟工艺有关的常数。
六.残留物
刻蚀残留物常覆盖在腔体内壁或被刻蚀图形 的底部。
刻蚀工艺名词解释

刻蚀工艺名词解释
把未被抗蚀剂掩蔽的薄膜层除去,从而在薄膜上得到与抗蚀剂膜上完全相同图形的工艺。
在集成电路制造过程中,经过掩模套准、曝光和显影,在抗蚀剂膜上复印出所需的图形,或者用电子束直接描绘在抗蚀剂膜上产生图形,然后把此图形精确地转移到抗蚀剂下面的介质薄膜(如氧化硅、氮化硅、多晶硅)或金属薄膜(如铝及其合金)上去,制造出所需的薄层图案。
刻蚀就是用化学的、物理的或同时使用化学和物理的方法,有选择地把没有被抗蚀剂掩蔽的那一部分薄膜层除去,从而在薄膜上得到和抗蚀剂膜上完全一致的图形。
刻蚀技术主要分为干法刻蚀与湿法刻蚀。
干法刻蚀主要利用反应气体与等离子体进行刻蚀;湿法刻蚀主要利用化学试剂与被刻蚀材料发生化学反应进行刻蚀。
半导体器件工艺学之刻蚀

下游式刻蚀系统
离子束铣( Ion Milling) 是近年来发展较快的一种离 子剥离技术。该技术主要利用携带能量的离子轰 击靶材料所产生的物理溅射刻蚀效应
离子刻蚀速率表示如下: dh( H) / dt = R( H) / cos(H) = R( H) [ 1 + tan2( H) ]1/2
当离子束入射的角度较大时, 材料表面反射的离子束也增 多。因此, 随着角度H的增大 , 越来越少的离子渗入到材 料的有效表面。为保证离子 的有效渗入, 定义临界角Hc 。 离子束的溅射场与靶材料的 原子数Z 有关, 材料的原子数 Z 越高, 刻蚀速率越高; 反之 则越低。
本产品通过物理与化学相结合的方法,对很细的线条(亚微米以下)进行刻 蚀以形成精细的图形。 主要用于微电子、光电子、通讯、微机械、新材料、能源等领域的器件 研发和制造。
深层反应离子刻蚀(DRIE)
系统己经足以刻蚀深宽比超过50 的深槽硅结构,对于光阻的刻蚀 选择比己超过100:1,刻蚀深度均 匀度也可以控制在±3%以内。
中微发布Primo D-RIE刻蚀设备,面向22 纳米及以下工艺
中微半导体设备(上海)有限公司(以下简称“ 中微”)日前发布面向22纳米及以下芯片生产 的第二代300毫米甚高频去耦合反应离子刻 蚀设备--Primo AD-RIE。 2011年7月
Primo AD-RIE在促进中微第一代刻蚀设备技术创 新的同时,又大大扩大了其自身的加工领域。 该设备的主要部分是一组创新的少量反应台反应 器的簇架构,可以灵活地装置多达三个双反应台 反应器,以达到最佳芯片加工输出量。每个反应 器都可以实现单芯片或双芯片加工。独特的反应 器腔体设计融合了中微专有的等离子体聚焦和喷 淋头技术,确保了芯片加工的质量。Primo ADRIE的一些基本特征使其更具备28纳米以下关键刻 蚀加工的能力
刻蚀
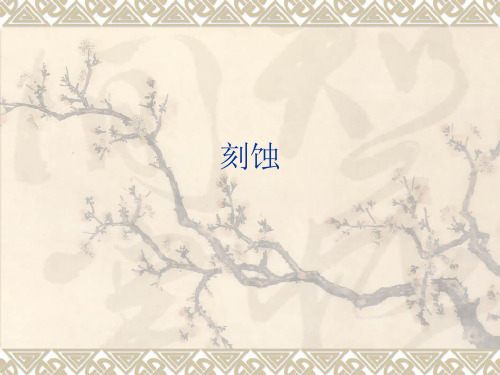
铜 CuCl2挥发性较弱,一般不用化学方式进行
主要是采用物理高能粒子的轰击方式,将其
去除
钨的回蚀: 采用氟化物等离子体(例如:CF4、NF3、SF6
等),进行反应离子刻蚀,将覆盖于介电层 表面的钨去掉,只留下介电层导电孔内的钨, 此过程又称为钨的回蚀。
终点检测
由于干法刻蚀选择比较差些,过度刻蚀会造
ion etching):通过活性离子对衬底的物理轰击 和化学反应双重作用刻蚀,
离子轰击加上自由基反应 具有溅射刻蚀和等离子刻蚀两者的优点
各向异性
选择性较好
目前,RIE已成为超大规模集成电路VLSI工
艺中应用最广泛的主流刻蚀技术
三种常见干法刻蚀方法的比较
等离子体刻蚀 刻蚀速率 选择性 刻蚀分布 终点控制 从高到低 很好 各向同性 时间或观察 溅射刻蚀 较低 较差 反应离子刻蚀 较高,可控 适中,可控
(1)等离子体引起损伤 原因:等离子体内具有一定能量的离子、电子 和处于激发状态的分子,对晶片表面的轰击会 产生机械损伤等。 形式:俘获界面电荷,材料缺陷迁移到主体材 料中等。
影响:
改变敏感器件的性质,如肖特基二极管的整流能
力降低; 在氧化层接触孔的刻蚀过程中,高分子聚合物的 淀积,会引起高的接触电阻; 在刻蚀过程中形成的挥发性物质会引起产品电学 性能的改变,影响稳定性等。
②
③ ④
特点 可实现各向异性的刻蚀,图形保真性高,有 很好的线宽尺寸控制,分辨率可在1µm以下 的精细图形加工的主要刻蚀方法; 刻蚀速率有较好控制,刻蚀均匀性好:片内, 片间以及批次间都可以保持较好的均匀性; 刻蚀选择性比湿法刻蚀差,要注意刻蚀终点 的监测。 设备复杂,成本高。
干法刻蚀的方法
刻蚀相关知识点总结

刻蚀相关知识点总结刻蚀技术主要分为湿法刻蚀和干法刻蚀两种。
湿法刻蚀是在溶液中通过化学反应去除材料表面的工艺,而干法刻蚀是在气相中通过物理或化学反应去除材料表面的工艺。
下面将详细介绍刻蚀的相关知识点。
一、刻蚀的基本原理1. 湿法刻蚀原理湿法刻蚀是利用化学溶液对材料表面进行腐蚀或溶解的工艺。
湿法刻蚀的原理是在溶液中加入具有特定功能的化学试剂,使其与被刻蚀物质发生化学反应,从而去除材料表面的部分物质。
湿法刻蚀通常可以实现较高的刻蚀速率和较好的表面质量,但需要考虑溶液中的成分和温度对环境的影响。
2. 干法刻蚀原理干法刻蚀是利用气相中的等离子体或化学反应对材料表面进行腐蚀或清除的工艺。
干法刻蚀的原理是在高能离子束或化学气体的作用下,使被刻蚀物质表面发生物理或化学反应,从而去除材料表面的部分物质。
干法刻蚀通常可以实现更高的加工精度和更好的表面质量,但需要考虑设备的复杂性和成本的影响。
二、刻蚀的工艺参数1. 刻蚀速率刻蚀速率是刻蚀过程中单位时间内去除的材料厚度,通常以单位时间内去除的厚度为单位。
刻蚀速率的选择需要综合考虑刻蚀材料的性质、刻蚀条件、刻蚀设备和加工要求等因素。
2. 刻蚀选择性刻蚀选择性是指在多种材料叠加或混合结构中选择性地去除某一种材料的能力。
刻蚀选择性的选择需要考虑被刻蚀材料和其它材料之间的化学反应性和物理性质的差异,以实现精确的刻蚀。
3. 刻蚀均匀性刻蚀均匀性是指在整个刻蚀过程中去除材料的厚度分布情况。
刻蚀均匀性的选择需要考虑刻蚀设备和刻蚀条件对被刻蚀物质的影响,以实现均匀的刻蚀。
4. 刻蚀深度控制刻蚀深度控制是指在整个刻蚀过程中去除材料的深度分布情况。
刻蚀深度控制的选择需要综合考虑刻蚀设备和刻蚀条件对被刻蚀物质的影响,以实现精确的刻蚀深度。
5. 刻蚀环境控制刻蚀环境控制是指在整个刻蚀过程中对刻蚀环境(如溶液中的成分、气相中的气体、温度和压力等)的控制。
刻蚀环境控制的选择需要考虑被刻蚀材料的特性和加工的要求,以实现良好的刻蚀效果。
刻蚀方法分类

刻蚀方法分类
刻蚀方法可以分为物理刻蚀和化学刻蚀两大类。
1. 物理刻蚀:物理刻蚀是利用物理方法(如离子束、激光、电火花等)进行材料刻蚀的工艺。
其原理主要是通过物理作用将材料表面一层逐渐去除,以达到刻蚀的目的。
物理刻蚀具有精度高、对材料损伤小等优点,但刻蚀速率较慢,不适合大规模生产。
2. 化学刻蚀:化学刻蚀是利用化学反应进行材料刻蚀的工艺。
其原理主要是通过选择适当的化学试剂与材料表面发生化学反应,生成可溶性物质或气体,然后将其去除,以达到刻蚀的目的。
化学刻蚀具有刻蚀速率快、适用范围广等优点,但容易对材料造成较大的损伤。
此外,按照刻蚀工艺的不同,刻蚀方法还可以分为干法刻蚀和湿法刻蚀两种。
干法刻蚀主要利用等离子体进行刻蚀,具有精度高、对材料损伤小等优点,但设备成本较高。
湿法刻蚀主要利用化学溶液进行刻蚀,具有刻蚀速率快、成本低等优点,但容易对材料造成较大的损伤。
在实际应用中,可以根据需要选择不同的刻蚀方法和工艺参数,以达到最佳的刻蚀效果。
刻蚀
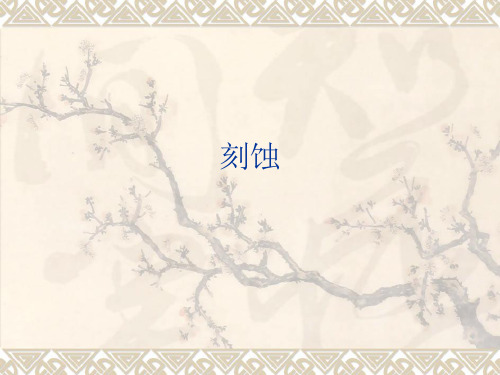
刻蚀:用物理或化学的方法有选择的从硅片 表面去除不需要的材料的过程
目的:腐蚀未被光刻胶覆盖的硅片表面,实 现图形的最终转移
刻蚀要求:
图形转移时的保真度 选择比 均匀性 刻蚀的清洁
刻蚀参数介绍 ① 刻蚀速率:是指单位时间内硅片表面被刻蚀
的材料去除量 ② 选择比:对不同的材料的刻蚀速率的比值
S=E1/E2
③ 均匀性:衡量刻蚀工艺在硅片内和硅片间的 可重复性
材料膜厚的均匀性
刻蚀本身的均匀性—刻蚀速率,刻蚀剖面,图 形尺寸和密度
负载效应:刻蚀面积和厚度的不同会导致刻蚀 速率的不同
湿法刻蚀
原理:湿法刻蚀又称湿法化学腐蚀,它是利 用化学试剂,与被刻蚀材料发生化学反应生 成可溶性物质或挥发性物质。
⑤ 光刻胶与晶片表面的粘附质量:粘附性不好, 容易出现刻蚀边缘图形不齐
湿法刻蚀存在的一些缺点: ① 需要使用大量有毒与腐蚀性的化学药品 ② 侧向腐蚀的存在导致线宽难以精确控制 ③ 腐蚀过程中的放热放气现象会影响对刻蚀工
艺的控制性
干法刻蚀
干法刻蚀
原理:利用高能粒子轰击或者等离子体,与 被刻蚀材料发生物理的、化学的或物理—化 学的作用,形成易挥发性物质,实现去除材 料的目的
⑤ 反应的产物必须为气体或者可溶于刻蚀剂的 物质,否则沉淀影响刻蚀的正常进行。
⑥ 批处理,容量大,但化学试剂用量大且有害, 处理麻烦,也不利于环境保护。
二氧化硅的湿法刻蚀
氢氟酸溶液(HF),极高的选择比
SiO2 + 4 HF → 2 H2O + SiF4 SiF4 + 2 HF → H2(SiF6) SiO2 + 6 HF → H2(SiF6)+ 2H2O
- 1、下载文档前请自行甄别文档内容的完整性,平台不提供额外的编辑、内容补充、找答案等附加服务。
- 2、"仅部分预览"的文档,不可在线预览部分如存在完整性等问题,可反馈申请退款(可完整预览的文档不适用该条件!)。
- 3、如文档侵犯您的权益,请联系客服反馈,我们会尽快为您处理(人工客服工作时间:9:00-18:30)。
刻蚀、清洗、镀膜段设备维护工艺关注点
1.刻蚀:
1)刻蚀机功率在500W附近是否稳定,4、6号机功率不稳定;
2)刻蚀机压强是否正常,5号机>110。
2.清洗:
1)甩干机油位是否正常,油温是否在正常范围内(120±10℃)。
2)甩干机启动和关闭时是否平稳;
3.镀膜
3.1板式镀膜:
1)碳板辅条的磨损情况,严重者需更换;
2)各腔内角阀滤网处碎硅片是否清理,角阀盖板需紧固,紧固螺钉不能凸出过多;
3)工艺腔内传动轮防护罩位置是否正常,传动轮上是否有氮化硅沉积;
4)工艺腔内沉积防护槽是否变形,严重者需更换;
5)两条线工艺腔的起始压强很难达到原来的设定值,起始真空度降低;
6)4号线更换石英管时,工艺腔盖板闭合情况不好,需反复开关(盖板变形); 7)工艺腔排风口的石英碎渣是否清理;
8)碳板变形,毛刺较多。
3.2 管式镀膜:
1)1-1硅烷流量故障;
2)1-3蝶阀/压强控制系统故障;
3)石墨舟有的只有一侧有编号,需补齐;
4)上料区传感器时有感应错误,传感器的位置和光强需调校;
5)各炉管内的碎片是否清理;
6)冷却站风机的两个出风口,风量相差很大,冷却效果不好;
7)上料区的吸笔有的采用铜管,强度低,容易变形,另外,铜的磨损可能对硅片造成污染。
8)手推车的位置需要校准。