反应离子刻蚀技术的原理
反应离子刻蚀原理

反应离子刻蚀原理一、引言反应离子刻蚀(RIE)是一种常用的微纳加工技术,它利用离子束和化学反应来实现对材料表面的刻蚀。
本文将介绍RIE的原理和主要特点,以及在微纳加工领域的应用。
二、RIE原理RIE是一种高度选择性的刻蚀技术,其原理是在低压等离子体中产生高能离子,通过控制离子束的能量和角度,使其与待刻蚀材料表面发生化学反应,从而实现刻蚀。
RIE的刻蚀过程主要包括三个步骤:离子撞击、反应和物质扩散。
1. 离子撞击在RIE中,通过加热和电离等手段,将气体转化为等离子体。
这些离子被加速器加速后,以高能量撞击待刻蚀材料表面。
离子撞击可以打开表面的化学键,形成反应活性位点,为后续的反应提供条件。
2. 反应离子撞击后,待刻蚀材料表面的化学键被断裂,产生活性基团。
同时,等离子体中的反应气体会与活性基团发生化学反应,生成易挥发的产物。
这些产物通过扩散过程从材料表面迅速脱离,从而实现刻蚀。
3. 物质扩散在刻蚀过程中,由于离子束的撞击和化学反应,材料表面的产物会被迅速去除。
这时,材料内部的新鲜表面暴露出来,继续参与反应。
通过物质的扩散,刻蚀过程在材料内部进行,从而实现对整个材料的刻蚀。
三、RIE特点RIE具有以下几个主要特点:1. 高选择性RIE技术可以实现高度选择性的刻蚀,即只在待刻蚀材料上进行刻蚀,不对其他材料产生影响。
这是因为RIE的刻蚀过程是通过离子撞击和化学反应实现的,而不是通过物理磨损或机械切割。
2. 高精度RIE技术可以实现亚微米级别的刻蚀精度,因为离子束的能量和角度可以被精确控制。
这使得RIE在微纳加工中得到广泛的应用,如制备微电子器件、光子器件和传感器等。
3. 高速刻蚀由于RIE技术结合了离子撞击和化学反应,可以实现快速而均匀的刻蚀。
与传统的物理刻蚀技术相比,RIE可以大大缩短刻蚀时间,提高生产效率。
四、RIE应用RIE技术在微纳加工领域有广泛的应用。
以下是几个常见的应用领域:1. 微电子器件制造RIE技术可以用于制备微电子器件,如晶体管、电容器和电阻器等。
纳米刻蚀工艺中的反应离子刻蚀技术

纳米刻蚀工艺是纳米制造中的一项关键技术,它涉及对材料进行微米级的剥离或去除。
其中,反应离子刻蚀(Reactive Ion Etching,RIE)是一种重要的纳米刻蚀技术,具有广泛的应用。
反应离子刻蚀技术是一种利用等离子体对材料进行刻蚀的工艺。
在RIE工艺中,气体被电离并形成等离子体,该等离子体包含带电粒子和中性粒子。
带电粒子在电场的作用下,可以吸附到工件表面并发生电荷交换,从而改变工件表面的化学环境。
这种改变有利于反应离子与材料发生化学反应,进而实现对材料的刻蚀。
反应离子刻蚀技术的优点主要包括高精度、高效率、深蚀深和大面积刻蚀等。
高精度和高效率使得RIE工艺在纳米制造中具有广泛的应用,可以快速地加工出复杂的纳米结构。
同时,由于反应离子与材料之间的化学反应,RIE可以实现深蚀深和大面积刻蚀,这对于大规模制造纳米器件具有重要的意义。
反应离子刻蚀技术的工作原理主要是通过电场产生等离子体,等离子体中的离子在电场的作用下吸附到工件表面并发生电荷交换,从而改变工件表面的化学环境。
这种改变有利于反应离子与材料发生化学反应,进而实现对材料的刻蚀。
同时,反应离子刻蚀技术还可以根据不同的材料和需求选择不同的气体进行刻蚀,这使得RIE工艺具有很高的灵活性和适应性。
总的来说,反应离子刻蚀技术是一种重要的纳米刻蚀技术,具有广泛的应用前景。
它通过高精度、高效率、深蚀深和大面积刻蚀等特点,为纳米制造提供了有力的支持。
随着纳米技术的不断发展,反应离子刻蚀技术将会在更多的领域得到应用,为人类社会的进步做出更大的贡献。
离子刻蚀原理-概述说明以及解释
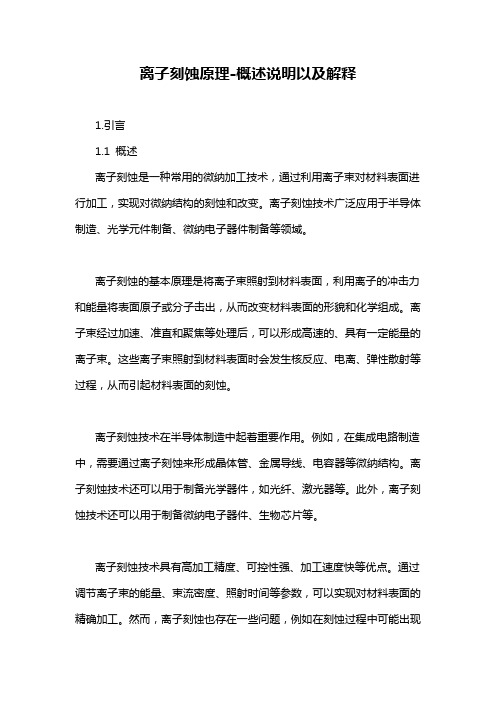
离子刻蚀原理-概述说明以及解释1.引言1.1 概述离子刻蚀是一种常用的微纳加工技术,通过利用离子束对材料表面进行加工,实现对微纳结构的刻蚀和改变。
离子刻蚀技术广泛应用于半导体制造、光学元件制备、微纳电子器件制备等领域。
离子刻蚀的基本原理是将离子束照射到材料表面,利用离子的冲击力和能量将表面原子或分子击出,从而改变材料表面的形貌和化学组成。
离子束经过加速、准直和聚焦等处理后,可以形成高速的、具有一定能量的离子束。
这些离子束照射到材料表面时会发生核反应、电离、弹性散射等过程,从而引起材料表面的刻蚀。
离子刻蚀技术在半导体制造中起着重要作用。
例如,在集成电路制造中,需要通过离子刻蚀来形成晶体管、金属导线、电容器等微纳结构。
离子刻蚀技术还可以用于制备光学器件,如光纤、激光器等。
此外,离子刻蚀技术还可以用于制备微纳电子器件、生物芯片等。
离子刻蚀技术具有高加工精度、可控性强、加工速度快等优点。
通过调节离子束的能量、束流密度、照射时间等参数,可以实现对材料表面的精确加工。
然而,离子刻蚀也存在一些问题,例如在刻蚀过程中可能出现侧向腐蚀、粗糙度增加等现象,需要进一步的研究和改进。
综上所述,离子刻蚀是一种重要的微纳加工技术,具有广泛的应用领域和潜力。
随着科技的不断进步和发展,离子刻蚀技术将继续得到改进和完善,为微纳加工领域的发展提供更多可能性。
1.2 文章结构文章结构部分的内容如下:文章结构部分主要介绍了本篇长文的组织结构和各个章节的内容概述。
本文主要分为以下几个章节:1. 引言:通过本章节,我们将会对离子刻蚀的基本概念作出简要阐述,并介绍本篇长文的整体结构和目的。
2. 正文:本章节将详细介绍离子刻蚀的基本原理,包括离子刻蚀的定义、刻蚀机制、刻蚀设备等内容。
同时,我们还将探讨离子刻蚀在不同领域中的应用,如半导体加工、纳米技术等。
3. 结论:在本章节中,我们将对离子刻蚀的基本原理进行总结,概括归纳其优势和局限性,并对离子刻蚀的未来发展进行展望,提出一些可能的研究方向和应用前景。
rie刻蚀的工作原理
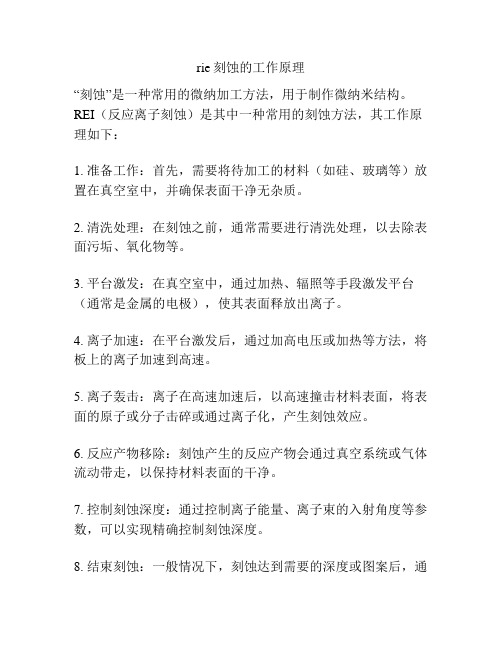
rie刻蚀的工作原理
“刻蚀”是一种常用的微纳加工方法,用于制作微纳米结构。
REI(反应离子刻蚀)是其中一种常用的刻蚀方法,其工作原理如下:
1. 准备工作:首先,需要将待加工的材料(如硅、玻璃等)放置在真空室中,并确保表面干净无杂质。
2. 清洗处理:在刻蚀之前,通常需要进行清洗处理,以去除表面污垢、氧化物等。
3. 平台激发:在真空室中,通过加热、辐照等手段激发平台(通常是金属的电极),使其表面释放出离子。
4. 离子加速:在平台激发后,通过加高电压或加热等方法,将板上的离子加速到高速。
5. 离子轰击:离子在高速加速后,以高速撞击材料表面,将表面的原子或分子击碎或通过离子化,产生刻蚀效应。
6. 反应产物移除:刻蚀产生的反应产物会通过真空系统或气体流动带走,以保持材料表面的干净。
7. 控制刻蚀深度:通过控制离子能量、离子束的入射角度等参数,可以实现精确控制刻蚀深度。
8. 结束刻蚀:一般情况下,刻蚀达到需要的深度或图案后,通
过关闭加速电压、停止离子源等方式结束刻蚀过程。
总之,REI刻蚀的工作原理主要是通过离子撞击材料表面,引发化学反应或物理剥离,以实现微纳米结构的制备。
这种刻蚀方式具有高加工精度、尺寸可控性好等特点,被广泛应用于微纳加工领域。
离子束刻蚀和反应离子刻蚀

离子束刻蚀和反应离子刻蚀离子束刻蚀(Ion Beam Etching, IBE)和反应离子刻蚀(Reactive Ion Etching, RIE)是常见的微纳加工和纳米制造技术,用于制作微结构、纳米结构和纳米材料。
本文将介绍离子束刻蚀和反应离子刻蚀的原理、过程、应用和优缺点。
离子束刻蚀是利用离子束的动能将物质从固体表面去除的一种刻蚀方式。
离子束源产生的高速离子束照射到待加工的材料表面,离子与原子或分子碰撞后传递能量,使表面原子具有足够的动能来克服结合能,从而将表面原子剥离。
离开表面的原子或分子通过真空环境扩散或被其他粒子吸附后被排除。
离子束刻蚀是一种无遮罩刻蚀方法,适用于对整个样品进行刻蚀或加工。
离子束刻蚀可控制刻蚀速度、刻蚀深度和表面质量,广泛应用于半导体器件制造、光学元件加工、微纳加工等领域。
反应离子刻蚀是在离子束刻蚀的基础上引入反应气体,使表面物质发生化学反应并形成可挥发的产物的一种刻蚀方式。
反应离子刻蚀一般使用高能粒子束和反应气体,高能粒子束提供克服表面能的能量,而反应气体提供物质溶解刻蚀的辅助。
反应离子刻蚀通过控制离子束能量、反应气体浓度和碰撞概率来调节刻蚀速率和刻蚀速度的非均匀性。
反应离子刻蚀的刻蚀选择性很高,可以实现对特定材料的选择性刻蚀。
相对于离子束刻蚀,反应离子刻蚀能够更精确地控制刻蚀深度和刻蚀形貌。
离子束刻蚀和反应离子刻蚀都可以使用不同种类的离子,包括惰性气体离子(如氦、氩)、反应离子(如氧、氮、氯气)以及金属离子。
离子能量、束流密度和束斑尺寸等参数都是刻蚀效果和加工精度的重要影响因素。
特别是在纳米尺度加工中,离子束直径和束聚焦是制造纳米结构和纳米材料的关键。
离子束刻蚀和反应离子刻蚀的刻蚀速率可以根据加工要求进行调节,通常在纳米加工中需要高精度和微纳米级的控制。
离子束刻蚀和反应离子刻蚀在微纳加工和纳米制造中有广泛的应用。
离子束刻蚀可用于制作平坦度高、表面质量好的光学元件、半导体器件和微纳结构,如光波导器件、集成电路和微机电系统。
反应离子刻蚀

反应离子刻蚀简介反应离子刻蚀(RIE)是一种通过气体放电产生的离子束来刻蚀材料表面的技术。
它是一种非常重要的微纳加工工艺,被广泛应用于半导体、光学和纳米科技领域。
本文将介绍反应离子刻蚀的原理、设备和应用。
原理反应离子刻蚀原理基于离子束与材料表面的相互作用。
在RIE设备中,通过一个高频电源产生一个电场,使得工作间隙中的气体(通常为氧气或氟气)在电场下发生电离。
产生的离子在电场的作用下加速并对材料表面进行刻蚀。
反应离子刻蚀的过程可以分为三个主要阶段:电离阶段、加速阶段和反应阶段。
1.电离阶段:利用高频放电使得气体中的原子或分子电离,产生大量正离子和电子。
2.加速阶段:通过电场作用,正离子在电场中加速并进入工作间隙,形成高速离子束。
3.反应阶段:离子束与材料表面发生碰撞,产生物理或化学反应,刻蚀材料表面。
设备反应离子刻蚀需要使用专门的设备,称为反应离子刻蚀机。
RIE机由多个关键组件组成:1.真空腔:用于形成高真空环境,防止气体分子的散射和干扰。
2.高频电源:提供高频放电电场,并驱动气体电离。
3.外加电源:用于控制电场及正离子束的加速程度和方向。
4.气体供给系统:提供刻蚀所需的气体,并控制气体的流量和压力。
5.气体排放系统:将刻蚀产生的废气排放到安全区域。
应用反应离子刻蚀在微纳加工领域具有广泛的应用,主要包括以下几个方面:1.半导体器件制造:RIE技术被广泛用于制造芯片中的光罩和微细结构,如晶体管、电容和互联线路等。
2.光学器件制造:RIE可以用于制造光学器件,如光纤、光波导和微透镜等。
3.微纳加工:RIE可以用于制造微纳米结构和微模具,如微通道、微阵列和微流体器件等。
4.纳米科技研究:RIE可以用于制备纳米材料和纳米结构,如纳米颗粒、纳米线和纳米孔洞等。
优势与挑战反应离子刻蚀具有以下优势:1.高加工速度:RIE可以在较短的时间内实现高精度的刻蚀,提高生产效率。
2.高精度:RIE可以实现亚微米级别的刻蚀精度,满足微纳加工的要求。
drie干法蚀刻原理
drie干法蚀刻原理DRIE(双极型反应离子刻蚀,Deep Reactive Ion Etching)干法蚀刻是一种高精度的微纳米加工技术,广泛应用于半导体、微电子器件、MEMS、光电子、生命科学等领域。
其优点在于可控制深度、垂直性和纵横比高。
下面简单介绍一下DRIE干法蚀刻的原理:1. 反应离子蚀刻(RIE)过程DRIE干法蚀刻依靠的是反应离子蚀刻(RIE)过程,其主要特点是等离子体与刻蚀表面间存在的反应物质的反应,最终产生气相或溶液中的物质,同时释放出反应所需要的新的原子或离子。
通过反应离子蚀刻过程,可以高效地完成微细结构的制备。
2. 阴极自我吸引(CIA)效应在DRIE干法蚀刻中,阴极自我吸引效应(CIA,Cathode Self-Biasing)是非常重要的。
当反应离子轰击刻蚀的地方产生电荷,从而形成电场。
电子在电场的吸引下会聚集到阴极上,使其形成一个更负的电位(负自我吸引)。
这意味着氢氟酸(HF)分子在撞击阴极表面后能够更容易地分解并产生反应,从而促进刻蚀过程。
3. 冲击产生等离子体DRIE干法蚀刻采用了高能量电离辉光放电(HEDP)的方式产生等离子体。
这种放电方式可以使气体在较低的压力下进行电离,从而产生高浓度的反应物,以保持较高的刻蚀速率和质量。
4. 双极金属反应DRIE干法蚀刻使用阴极和阳极的双金属反应体系,这种体系可以形成一种稳定的化学反应,可以产生氟化物(F^-)和钨酸根(WO4^-2 )等反应物,以加速刻蚀过程。
在DRIE干法蚀刻过程中,通过调节工艺参数如气体流速,功率密度等,可以控制反应离子轰击材料表面的能量和反应速率,有效地实现高精度加工的控制。
总之,DRIE干法蚀刻的原理是基于反应离子蚀刻、阴极自我吸引效应、等离子体和双极金属反应体系。
可以实现高精度和高质量的微纳米结构制备,是微纳加工领域中的一项重要技术。
反应性离子刻蚀技术的研究与应用
反应性离子刻蚀技术的研究与应用章节一:引言反应性离子刻蚀技术(RIE)是一项重要的微纳加工技术,被广泛应用于集成电路、光电、微系统等领域。
该技术的实现取决于离子束在物质表面所产生的化学反应,这些反应在等离子体和物质之间传递电荷。
与传统的干法刻蚀技术相比,RIE具有高成像分辨率、刻蚀速度快等优点,在集成电路制造、光学元件、微电子机械系统、纳米技术等领域,具有广泛的应用前景。
本文将从RIE技术的原理、设备结构、刻蚀参数、优缺点等方面进行详细阐述。
章节二:RIE技术的原理反应性离子刻蚀技术(RIE)是一种利用化学反应进行刻蚀的离子束刻蚀技术。
其基本原理是利用离子束与待刻蚀材料表面所发生的等离子体化学反应,使得材料表面形成易挥发性的化合物并被排出。
RIE主要涉及等离子体物理和表面化学两个机制。
等离子体化学反应是通过金属电极、电磁场、气体放电等进一步生成等离子体,使反应物与物质表面发生化学反应。
表面化学反应是利用表面材料原子(或分子)的空缺位置与等离子体中的离子和分子相互反应,并使表面材料发生化学变化,以产生易挥发产品的表面化学反应。
章节三:RIE技术的设备结构RIE的设备结构主要由等离子体处理室、真空装置、电源、气体输送系统等四部分组成。
其中,等离子体处理室是RIE的核心部分,包括气体分析系统、真空泵、样品保护措施、接地系统、隔热系统等。
气体输送系统主要是将待处理实验样品送入等离子体处理室中,保证反应气体的稳定输送。
电源系统是RIE技术必不可少的一个部分,主要包括射频电源、直流电源、微波辅助电源等。
章节四:RIE技术的刻蚀参数成功的RIE制程需要通过多种参数的综合调整和优化来实现。
RIE技术的刻蚀参数包括六个方面:气体类型、压力、放电功率、放电频率、反应室温度、等离子体电荷密度。
其中,气体和压力是决定RIE反应物质刻蚀状态的重要因素,不同的气体和压力对反应物的刻蚀速度、反应物质的稳定性和丝杆的寿命有着重要的影响。
北京三和联反应离子刻蚀
北京三和联反应离子刻蚀
反应离子刻蚀(RIE)是一种用于微细加工的蚀刻技术,它利用了化学
反应等离子体去除沉积在晶圆上的材料。
等离子体是在低压(真空)
下通过电磁场产生的,高能离子攻击晶圆表面并与其发生反应。
该刻蚀技术具有干法蚀刻的特性,与湿法蚀刻不同。
在反应离子刻蚀中,来自等离子体的高能离子与晶圆表面发生化学反应,形成容易刻
蚀的损伤层和促进化学反应。
同时,离子还可以清除表面生成物以露
出清洁的刻蚀表面。
由于反应离子的大部分垂直输送,反应离子刻蚀
可以产生非常各向异性的蚀刻剖面,这与其它的湿法化学蚀刻的各向
同性剖面形成对比。
然而,该刻蚀技术不能获得较高的选择比,对表面的损伤大,有污染,难以形成更精细的图形。
此外,该技术还存在一些局限性,例如对表
面的损伤大和有污染等。
总之,反应离子刻蚀是一种重要的微细加工技术,它可以用于制造各
种微电子器件和纳米结构。
然而,该技术还需要不断改进和完善,以
实现更高的精度和更广泛的应用。
反应离子刻蚀技术的原理
摘要:详细阐述离子刻蚀技术的原理,反应腔功能与结构设计,着重介绍适应集成电路特征尺寸微细化发展所采用的新技术。
关键词:刻蚀,等离子体,射频Author: 刘晓明from Applied Material (China) --SolidState Technology( China) 前言目前,整个集成电路制造技术向着高集成度、小特征尺寸(CD)的方向发展。
硅片直径从最初的4英寸发展到已批量生产的12英寸生产线。
同时,衡量半导体制造技术的关键参数-特征尺寸亦朝着微细化方向发展,从最初的5祄发展到当前的110nm、90nm、65nm。
而刻蚀是决定特征尺寸的核心工艺技术之一。
刻蚀技术分为湿法刻蚀和干法刻蚀。
湿法刻蚀采用化学腐蚀进行,是传统的刻蚀工艺。
它具有各项同性的缺点,即在刻蚀过程不但有所需要的纵向刻蚀,还有不需要的横向刻蚀,因而精度差,线宽一般在3祄以上。
干法刻蚀是因应大规模集成电路电路生产的需要而被开发出的精细加工技术,它具有各项异性的特点,在最大限度上保证了纵向刻蚀,还控制了横向刻蚀。
目前流行的典型设备为反应离子刻蚀(RIE-Reactive Ion Etch)系统。
它已被广泛应用于微处理器(CPU)、存储(DRAM)和各种逻辑电路的制造中。
其分类按照刻蚀的材料分为介电材料刻蚀(Dielectric Etch)、多晶硅刻蚀(Poly-silicon Etch)和金属刻蚀(Metal Etch)。
反应离子刻蚀技术的原理刻蚀精度主要是用保真度(Profile)、选择比(Selectivity)、均匀性(Uniformity)等参数来衡量。
所谓保真度度,就是要求把光刻胶的图形转移到其下的薄膜上,即希望只刻蚀所要刻蚀的薄膜,而对其上的掩膜和其下的衬底没有刻蚀。
事实上,以上三个部分都会被刻蚀,只是刻蚀速率不同。
选择比(Selectivity)就是用来衡量这一指标的参数。
S=V/U(V为对薄膜的刻蚀速率,U为对掩膜或衬底的刻蚀速率),S越大则选择比越好。
- 1、下载文档前请自行甄别文档内容的完整性,平台不提供额外的编辑、内容补充、找答案等附加服务。
- 2、"仅部分预览"的文档,不可在线预览部分如存在完整性等问题,可反馈申请退款(可完整预览的文档不适用该条件!)。
- 3、如文档侵犯您的权益,请联系客服反馈,我们会尽快为您处理(人工客服工作时间:9:00-18:30)。
反应离子刻蚀技术的原理-标准化文件发布号:(9456-EUATWK-MWUB-WUNN-INNUL-DDQTY-KII摘要:详细阐述离子刻蚀技术的原理,反应腔功能与结构设计,着重介绍适应集成电路特征尺寸微细化发展所采用的新技术。
关键词:刻蚀,等离子体,射频 Author: 刘晓明 from Applied Material (China) --SolidState Technology( China) 前言目前,整个集成电路制造技术向着高集成度、小特征尺寸(CD)的方向发展。
硅片直径从最初的4英寸发展到已批量生产的12英寸生产线。
同时,衡量半导体制造技术的关键参数-特征尺寸亦朝着微细化方向发展,从最初的5祄发展到当前的110nm、90nm、65nm。
而刻蚀是决定特征尺寸的核心工艺技术之一。
刻蚀技术分为湿法刻蚀和干法刻蚀。
湿法刻蚀采用化学腐蚀进行,是传统的刻蚀工艺。
它具有各项同性的缺点,即在刻蚀过程不但有所需要的纵向刻蚀,还有不需要的横向刻蚀,因而精度差,线宽一般在3祄以上。
干法刻蚀是因应大规模集成电路电路生产的需要而被开发出的精细加工技术,它具有各项异性的特点,在最大限度上保证了纵向刻蚀,还控制了横向刻蚀。
目前流行的典型设备为反应离子刻蚀(RIE-Reactive Ion Etch)系统。
它已被广泛应用于微处理器(CPU)、存储(DRAM)和各种逻辑电路的制造中。
其分类按照刻蚀的材料分为介电材料刻蚀(Dielectric Etch)、多晶硅刻蚀(Poly-silicon Etch)和金属刻蚀(Metal Etch)。
反应离子刻蚀技术的原理刻蚀精度主要是用保真度(Profile)、选择比(Selectivity)、均匀性(Uniformity)等参数来衡量。
所谓保真度度,就是要求把光刻胶的图形转移到其下的薄膜上,即希望只刻蚀所要刻蚀的薄膜,而对其上的掩膜和其下的衬底没有刻蚀。
事实上,以上三个部分都会被刻蚀,只是刻蚀速率不同。
选择比(Selectivity)就是用来衡量这一指标的参数。
S=V/U(V为对薄膜的刻蚀速率,U为对掩膜或衬底的刻蚀速率),S越大则选择比越好。
由于跨越整个硅片的薄膜厚度和刻蚀速率不尽相同,从而也导致图形转移的不均匀,尤其是中心(Center)和边缘(Edge)相差较大。
因而均匀性(Etch Rate Uniformity)成为衡量这一指标的重要参数。
除以上参数外,刻蚀速率(Etch Rate)也是一个重要指标,它用来衡量硅片的产出速度,刻蚀速率越快,则产出率越高。
反应离子刻蚀是以物理溅射为主并兼有化学反应的过程。
通过物理溅射实现纵向刻蚀,同时应用化学反应来达到所要求的选择比,从而很好地控制了保真度。
刻蚀气体(主要是F基和CL基的气体)在高频电场(频率通常为13.56MHz)作用下产生辉光放电,使气体分子或原子发生电离,形成“等离子体”(Plasma)。
在等离子体中,包含有正离子(Ion+)、负离子(Ion-)、游离基(Radical)和自由电子(e)。
游离基在化学上是很活波的,它与被刻蚀的材料发生化学反应,生成能够由气流带走的挥发性化合物,从而实现化学刻蚀。
另一方面,如图1所示,反应离子刻蚀腔体采用了阴极(Cathode)面积小,阳极面积大的不对称设计。
在射频电源所产生的电场的作用下带负电的自由电子因质量小、运动速度快,很快到达阴极;而正离子则由于质量大,速度慢不能在相同的时间内到达阴极, 从而使阴极附近形成了带负电的鞘层电压。
同时由于反应腔的工作气压在10-3~10-2Torr, 这样正离子在阴极附近得到非常有效的加速,垂直轰击放置于阴极表面的硅片,这种离子轰击可大大加快表面的化学反应及反应生成物的脱附,从而导致很高的刻蚀速率。
正是由于离子轰击的存在才使得各向异性刻蚀得以实现。
[attach]201183[/attach] 图1. DPSII 刻蚀腔结构图初期的射频系统普遍为电容式耦合单射频系统设计(Bias RF)。
但随着工艺要求的不断提高,双射频设计(Bias RF 和Source RF)开始被广泛应用。
特别是到65nm以后,这已经成为必然选择。
该设计方式能把离子的轰击速度和浓度分开控制,从而更好地控制刻蚀速率、选择比、均匀性和特征尺寸(CD)。
传统的单射频系统为了提高刻蚀速率,通常会增加RF功率以提高电场强度,从而增加离子浓度(Ion Density)、加快刻蚀。
但离子的能量(Ion Energy)也会相应增加,损伤硅片表面。
为了解决这一问题,半导体设备厂商普遍采用了双射频系统设计,也就是在原有基础上,增加一个置于腔体顶部的射频感应电场来增加离子的浓度。
其工作原理如下,如图2所示,一个射频电源(Source RF)加在一个电感线圈上,产生交变磁场从而产生感应电场。
该电场加速产生更多的离子,而又不直接轰击硅片。
[attach]201184[/attach] 图2. 电感耦合原理图此外,在反应腔四周安装电磁场也是被广泛应用的以增加离子浓度的重要手段。
电子在磁场和电场的共同作用下将作圆柱状回旋运动而不是电场下的直线运动。
磁场的存在将直接导致反应气体电离截面的增加。
磁场的引进会增强离子密度,并使得等离子刻蚀技术可以在更低气压下得以运用(<10 mT)。
由于离子密度的增加,撞击表面的离子能量也可以在不降低刻蚀速率的情况下被降低,从而提高刻蚀选择比。
反应腔功能与结构一个典型的刻蚀腔体(Plasma Etch Chamber)主要由以下几个部分组成: 1. 反应腔由铝合金反应腔体、换洗套件(Swap Kit)和工艺套件(Process Kit)组成。
它们与阴极(Cathode)和腔体上盖一起构成产生等离子体的反应室。
在设备的定期保养和清洗过程中,只需更换换洗套件、工艺套件和腔体上盖,从而延长了腔体的使用寿命、缩短了保养时间、提高了生产效率。
2.真空及压力控制系统刻蚀反应腔工作在真空状态下,工作压力一般在10-3~10-2Torr之间。
整个系统主要由干泵(Dry Pump)、分子泵(Turbo Pump)、调压阀(Throttle Valve)、门阀(Gate Valve)、隔离阀(Isolation Valve)、真空计和各种真空检测开关组成。
干泵真空度通常能达到100mT,分子泵则能达到0.1mT,分子泵的选型根据刻蚀压力和刻蚀腔容积的不同而不同。
随着硅片由200mm发展到300mm,极限真空的要求越来越高,分子泵的抽速越来越大。
从300-2200L/s发展到1600-2500L/s。
为了进一步提高刻蚀的均匀性,某些产品还采用了双分子泵设计,如应用材料公司的300mm EMAX。
压力的测量是由真空计来实现的,要求具有精度高、稳定性好的优点。
薄膜式电容真空计(Manometer)则因具备上述特点,而被业界广泛应用。
其量程范围有100mT,1T和10T三种。
金属和多晶硅刻蚀多选用100mT 真空计,而介电材料刻蚀选用1T真空计。
压力控制由电动调压阀(Throttle Valve)来完成。
3. 射频(RF)系统射频系统由射频发生器(RF Generator)和匹配器(RF Match)组成,发生器产生的射频信号首先输出到匹配器,然后输出到反映腔阴极。
该系统通常有两种组合方式:常用的为固定频率射频发生器和可调匹配器;另一种则为变频式射频发生器和不可调匹配器。
当反应腔内的等离子体形成后,整个腔体为可变电容性负载。
对于第一种组合方式,射频发生器的输出频率和功率固定,匹配器则自动调节其内部的可变电感(L)实现共振;同时调节可变电容器来实现阻抗匹配(50Ω)以减小反射频率,从而使发生器的功率最大限度地输出到阴极。
对于第二种组合方式,匹配器由固定的电容和电感组成,射频发生器通过调节频率实现共振,同时增大实际输出功率来保证输出到阴极的功率达到设定值。
4. 静电吸盘和硅片温度控制系统在200mm和300mm集成电路制造设备中,各供应商普遍采用了静电吸盘(Electrostatic Chuck)技术,而抛弃了传统的机械固定模式。
它提高了刻蚀均匀性、减少了尘埃微粒(Particle)。
同时,热交换器和硅片背面氦气(He)冷却技术进行温度控制的运用确保了整个硅片在刻蚀过程中的温度均匀,从而减少了对刻蚀速率均匀性的影响。
静电吸盘按照原理分为库仑力静电场吸附和Johnsen-Rahbeck效应两种,主要是利用吸盘上所加高电压(HV)与硅片上因等离子效应而产生的负电压(DC Bias)之间的电压差将硅片吸附到吸盘上。
它们采用了不同的介电材料,前一种采用高分子聚合物(Polymer),后一种则采用氮化铝(AlN)。
它们与高电压(HV Module)发生器相配合,产生可通过软件设定的电压值。
总的来说,高分子聚合物静电吸盘所需电压较高,漏电流也大,使用寿命较短。
而陶瓷静电吸盘(ALN Ceramic ESC)价格相对昂贵,但使用寿命长,能提供更稳定的吸附力(Chucking Force)和背氦控制。
5.气体流量控制系统刻蚀气体的流量由质量流量控制器(MFC)来控制,其流量范围一般为50-1000sccm,控制精度可达+/-1%,流量稳定时间<1s 。
该控制器按照内部结构可分为模拟电路型,数字电路型及目前最先进的压力变化补偿型(PTI-Pressure Transient Insensitive Technology)。
该控制器能够自动补偿气源压力的波动,保证输出流量稳定。
6.刻蚀终点检测系统该系统被广泛应用于先进刻蚀设备中,以保证刻蚀深度。
其工作原理为通过检测特定波长的光,来确定刻蚀是否结束。
通常有两种方式:一是检测参与反应的化学气体浓度突然升高,或者检测反应生成物的浓度骤然下降。
该设备按照检测波长的范围可分为单波长(High Optical Throughput)和分光镜(Monochromator)两种。
前者只能通过特定波长的光,后者可通过电机控制分光镜的角度将所需波长的光分离出来。
7.传送系统传送系统由机械手(Robot)、硅片中心检测器和气缸等主要部件组成。
机械手负责硅片的传入和传出。
在传送过程中,中心检测器会自动检测硅片中心在机械手上的位置,进而补偿机械手伸展和旋转的步数以保证硅片被放置在静电吸盘的中心。
硅片在反应腔中通常有硅片刻蚀时的位置硅片被传送时的位置,它们是通过气缸带动波纹管上下运动来实现的。
8.系统软件及控制随着软件技术的发展,用在刻蚀设备上的专业控制软件也从传统的DOS 或类DOS 操作界面过渡到了Windows操作系统。
同时,还引入了分布式控制系统的概念。
每个反应腔都具备了独立的控制软件和硬件,即使在主机台停机的情况下仍可继续完成整个刻蚀过程以提高设备的可靠性。