反应离子刻蚀实验
反应离子刻蚀原理

反应离子刻蚀原理一、引言反应离子刻蚀(RIE)是一种常用的微纳加工技术,它利用离子束和化学反应来实现对材料表面的刻蚀。
本文将介绍RIE的原理和主要特点,以及在微纳加工领域的应用。
二、RIE原理RIE是一种高度选择性的刻蚀技术,其原理是在低压等离子体中产生高能离子,通过控制离子束的能量和角度,使其与待刻蚀材料表面发生化学反应,从而实现刻蚀。
RIE的刻蚀过程主要包括三个步骤:离子撞击、反应和物质扩散。
1. 离子撞击在RIE中,通过加热和电离等手段,将气体转化为等离子体。
这些离子被加速器加速后,以高能量撞击待刻蚀材料表面。
离子撞击可以打开表面的化学键,形成反应活性位点,为后续的反应提供条件。
2. 反应离子撞击后,待刻蚀材料表面的化学键被断裂,产生活性基团。
同时,等离子体中的反应气体会与活性基团发生化学反应,生成易挥发的产物。
这些产物通过扩散过程从材料表面迅速脱离,从而实现刻蚀。
3. 物质扩散在刻蚀过程中,由于离子束的撞击和化学反应,材料表面的产物会被迅速去除。
这时,材料内部的新鲜表面暴露出来,继续参与反应。
通过物质的扩散,刻蚀过程在材料内部进行,从而实现对整个材料的刻蚀。
三、RIE特点RIE具有以下几个主要特点:1. 高选择性RIE技术可以实现高度选择性的刻蚀,即只在待刻蚀材料上进行刻蚀,不对其他材料产生影响。
这是因为RIE的刻蚀过程是通过离子撞击和化学反应实现的,而不是通过物理磨损或机械切割。
2. 高精度RIE技术可以实现亚微米级别的刻蚀精度,因为离子束的能量和角度可以被精确控制。
这使得RIE在微纳加工中得到广泛的应用,如制备微电子器件、光子器件和传感器等。
3. 高速刻蚀由于RIE技术结合了离子撞击和化学反应,可以实现快速而均匀的刻蚀。
与传统的物理刻蚀技术相比,RIE可以大大缩短刻蚀时间,提高生产效率。
四、RIE应用RIE技术在微纳加工领域有广泛的应用。
以下是几个常见的应用领域:1. 微电子器件制造RIE技术可以用于制备微电子器件,如晶体管、电容器和电阻器等。
纳米刻蚀工艺中的反应离子刻蚀技术

纳米刻蚀工艺是纳米制造中的一项关键技术,它涉及对材料进行微米级的剥离或去除。
其中,反应离子刻蚀(Reactive Ion Etching,RIE)是一种重要的纳米刻蚀技术,具有广泛的应用。
反应离子刻蚀技术是一种利用等离子体对材料进行刻蚀的工艺。
在RIE工艺中,气体被电离并形成等离子体,该等离子体包含带电粒子和中性粒子。
带电粒子在电场的作用下,可以吸附到工件表面并发生电荷交换,从而改变工件表面的化学环境。
这种改变有利于反应离子与材料发生化学反应,进而实现对材料的刻蚀。
反应离子刻蚀技术的优点主要包括高精度、高效率、深蚀深和大面积刻蚀等。
高精度和高效率使得RIE工艺在纳米制造中具有广泛的应用,可以快速地加工出复杂的纳米结构。
同时,由于反应离子与材料之间的化学反应,RIE可以实现深蚀深和大面积刻蚀,这对于大规模制造纳米器件具有重要的意义。
反应离子刻蚀技术的工作原理主要是通过电场产生等离子体,等离子体中的离子在电场的作用下吸附到工件表面并发生电荷交换,从而改变工件表面的化学环境。
这种改变有利于反应离子与材料发生化学反应,进而实现对材料的刻蚀。
同时,反应离子刻蚀技术还可以根据不同的材料和需求选择不同的气体进行刻蚀,这使得RIE工艺具有很高的灵活性和适应性。
总的来说,反应离子刻蚀技术是一种重要的纳米刻蚀技术,具有广泛的应用前景。
它通过高精度、高效率、深蚀深和大面积刻蚀等特点,为纳米制造提供了有力的支持。
随着纳米技术的不断发展,反应离子刻蚀技术将会在更多的领域得到应用,为人类社会的进步做出更大的贡献。
反应离子刻蚀实验

反应离子刻蚀硅阵列实验一、实验目的:1、掌握反应离子刻蚀的基本原理。
2、掌握利用单晶硅刻蚀硅阵列的实验流程。
3、了解刻蚀后的硅阵列的表征方法。
二、实验原理刻蚀技术分为湿法刻蚀和干法刻蚀。
湿法刻蚀是传统的刻蚀工艺,把硅片浸泡在一定的化学试剂或试剂溶液中,使没有被抗蚀剂掩蔽的那一部分薄膜表面与试剂发生化学反应而被除去,其优点是操作简便、对设备要求低、易于实现大批量生产,并且刻蚀的选择性也好。
但是,它具有各项同性的缺点,即在刻蚀过程不但有所需要的纵向刻蚀,还有不需要的横向刻蚀,因而精度差,线宽一般在3μm以上。
干法刻蚀是应大规模集成电路生产的需要而被开发出的精细加工技术,它具有各项异性的特点,在最大限度上保证了纵向刻蚀,还控制了横向刻蚀。
反应离子刻蚀(Reactive Ion Etching,RIE)是干法刻蚀的一种,是以物理溅射为主并兼有化学反应的过程,通过物理溅射实现纵向刻蚀,同时应用化学反应来达到所要求的选择比,其基本工作原理是刻蚀气体(主要是F基和Cl基的气体)在高频电场(频率通常为13.56MHz)作用下产生辉光放电,使气体分子或原子发生电离,形成“等离子体”(Plasma)。
在等离子体中,包含有正离子(Ion+)、负离子(Ion-)、游离基(Radical)和自由电子(e)。
游离基在化学上是很活波的,它与被刻蚀的材料发生化学反应,生成能够由气流带走的挥发性化合物,从而实现化学刻蚀。
而质量较大的正离子,被阴极附近带负电的鞘层电压有效的加速,垂直轰击放置于阴极表面的硅片,以较大的动量进行物理刻蚀,这种离子轰击可大大加快表面的化学反应及反应生成物的脱附,从而导致很高的刻蚀速率。
三、实验装置ME-3A型多功能磁增强反应离子刻蚀机四、实验内容和步骤1. 硅片的清洗:采用RCA标准清洗法进行硅片的清洗,具体步骤:(1)SPM清洗:去除硅片表面的有机污物和部分金属,(2)DHF清洗:去除硅片表面的自然氧化膜,(3)APM清洗(SC-1):去除硅片表面的颗粒和金属,(4)HPM清洗:去除硅表面的钠、铁、镁和锌等金属污染物。
反应性离子束刻蚀工艺在半导体制备中的应用研究
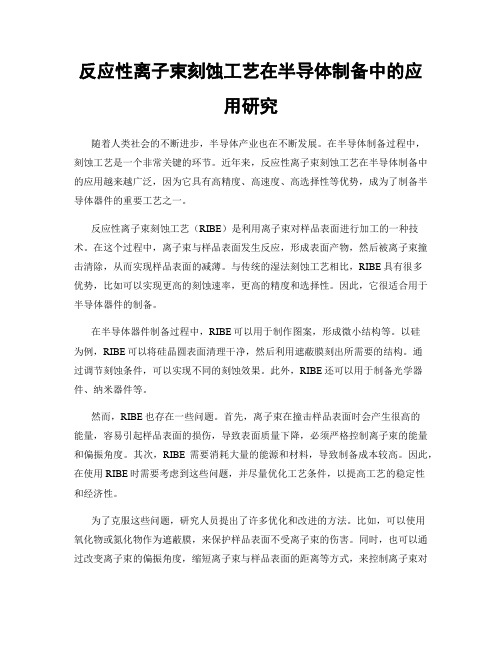
反应性离子束刻蚀工艺在半导体制备中的应用研究随着人类社会的不断进步,半导体产业也在不断发展。
在半导体制备过程中,刻蚀工艺是一个非常关键的环节。
近年来,反应性离子束刻蚀工艺在半导体制备中的应用越来越广泛,因为它具有高精度、高速度、高选择性等优势,成为了制备半导体器件的重要工艺之一。
反应性离子束刻蚀工艺(RIBE)是利用离子束对样品表面进行加工的一种技术。
在这个过程中,离子束与样品表面发生反应,形成表面产物,然后被离子束撞击清除,从而实现样品表面的减薄。
与传统的湿法刻蚀工艺相比,RIBE具有很多优势,比如可以实现更高的刻蚀速率,更高的精度和选择性。
因此,它很适合用于半导体器件的制备。
在半导体器件制备过程中,RIBE可以用于制作图案,形成微小结构等。
以硅为例,RIBE可以将硅晶圆表面清理干净,然后利用遮蔽膜刻出所需要的结构。
通过调节刻蚀条件,可以实现不同的刻蚀效果。
此外,RIBE还可以用于制备光学器件、纳米器件等。
然而,RIBE也存在一些问题。
首先,离子束在撞击样品表面时会产生很高的能量,容易引起样品表面的损伤,导致表面质量下降,必须严格控制离子束的能量和偏振角度。
其次,RIBE需要消耗大量的能源和材料,导致制备成本较高。
因此,在使用RIBE时需要考虑到这些问题,并尽量优化工艺条件,以提高工艺的稳定性和经济性。
为了克服这些问题,研究人员提出了许多优化和改进的方法。
比如,可以使用氧化物或氮化物作为遮蔽膜,来保护样品表面不受离子束的伤害。
同时,也可以通过改变离子束的偏振角度,缩短离子束与样品表面的距离等方式,来控制离子束对样品表面的影响。
此外,还可以结合其他工艺方法,比如湿法刻蚀、等离子体刻蚀等,来实现更高的刻蚀精度和选择性。
总的来说,反应性离子束刻蚀工艺是半导体制备中非常重要的一环,具有很大的发展前景。
未来,随着新材料和新器件的出现,RIBE将面临更多的挑战和机遇。
研究人员需要不断探索新的技术和方法,来实现更高的刻蚀精度和效率,为半导体产业的发展做出更大的贡献。
离子束刻蚀和反应离子刻蚀

离子束刻蚀和反应离子刻蚀离子束刻蚀(Ion Beam Etching, IBE)和反应离子刻蚀(Reactive Ion Etching, RIE)是常见的微纳加工和纳米制造技术,用于制作微结构、纳米结构和纳米材料。
本文将介绍离子束刻蚀和反应离子刻蚀的原理、过程、应用和优缺点。
离子束刻蚀是利用离子束的动能将物质从固体表面去除的一种刻蚀方式。
离子束源产生的高速离子束照射到待加工的材料表面,离子与原子或分子碰撞后传递能量,使表面原子具有足够的动能来克服结合能,从而将表面原子剥离。
离开表面的原子或分子通过真空环境扩散或被其他粒子吸附后被排除。
离子束刻蚀是一种无遮罩刻蚀方法,适用于对整个样品进行刻蚀或加工。
离子束刻蚀可控制刻蚀速度、刻蚀深度和表面质量,广泛应用于半导体器件制造、光学元件加工、微纳加工等领域。
反应离子刻蚀是在离子束刻蚀的基础上引入反应气体,使表面物质发生化学反应并形成可挥发的产物的一种刻蚀方式。
反应离子刻蚀一般使用高能粒子束和反应气体,高能粒子束提供克服表面能的能量,而反应气体提供物质溶解刻蚀的辅助。
反应离子刻蚀通过控制离子束能量、反应气体浓度和碰撞概率来调节刻蚀速率和刻蚀速度的非均匀性。
反应离子刻蚀的刻蚀选择性很高,可以实现对特定材料的选择性刻蚀。
相对于离子束刻蚀,反应离子刻蚀能够更精确地控制刻蚀深度和刻蚀形貌。
离子束刻蚀和反应离子刻蚀都可以使用不同种类的离子,包括惰性气体离子(如氦、氩)、反应离子(如氧、氮、氯气)以及金属离子。
离子能量、束流密度和束斑尺寸等参数都是刻蚀效果和加工精度的重要影响因素。
特别是在纳米尺度加工中,离子束直径和束聚焦是制造纳米结构和纳米材料的关键。
离子束刻蚀和反应离子刻蚀的刻蚀速率可以根据加工要求进行调节,通常在纳米加工中需要高精度和微纳米级的控制。
离子束刻蚀和反应离子刻蚀在微纳加工和纳米制造中有广泛的应用。
离子束刻蚀可用于制作平坦度高、表面质量好的光学元件、半导体器件和微纳结构,如光波导器件、集成电路和微机电系统。
反应离子刻蚀的机理及其实验研究方法

反应离子刻蚀是一种用于微细加工的技术,它通过溅射带电离子来刻蚀材料表面,从而形成精细的微结构。
反应离子刻蚀的机理是:当带电离子溅射到材料表面时,会产生大量的热能和碰撞力,使材料表面的原子或者分子被碰撞力或者热能打碎,形成离子和自由电子。
这些离子和自由电子再受到电场的作用,被带走,从而形成刻蚀。
实验研究方法:
1.实验装置:反应离子刻蚀的实验装置通常由真空容器、离子源、真空泵、电子枪、控制
系统等部件组成。
2.刻蚀条件:刻蚀的条件包括真空度、溅射离子的能量、刻蚀时间、刻蚀距离等。
3.微细加工方法:可以通过调节刻蚀条件,实现对不同材料的微细加工,例如精密削减、
型腔加工、表面处理等。
4.数据分析:通过扫描电子显微镜(SEM)或者其他分析仪器对刻蚀后的表面进行观察和
测量,可以了解刻蚀的效果和质量。
可以使用光学显微镜、X射线衍射仪、扫描探针显微镜等仪器对刻蚀后的表面进行分析。
5.应用:反应离子刻蚀技术可以用于各种材料的微细加工,包括金属、硅、玻璃、陶瓷、
聚合物等。
反应离子刻蚀技术在微纳米加工、微细机械加工、生物医学技术、半导体工业等领域具有广泛的应用。
注意:反应离子刻蚀是一种危险的技术,需要在适当的实验室条件下进行,并使用相应的安全防护措施。
反应离子刻蚀
反应离子刻蚀简介反应离子刻蚀(RIE)是一种通过气体放电产生的离子束来刻蚀材料表面的技术。
它是一种非常重要的微纳加工工艺,被广泛应用于半导体、光学和纳米科技领域。
本文将介绍反应离子刻蚀的原理、设备和应用。
原理反应离子刻蚀原理基于离子束与材料表面的相互作用。
在RIE设备中,通过一个高频电源产生一个电场,使得工作间隙中的气体(通常为氧气或氟气)在电场下发生电离。
产生的离子在电场的作用下加速并对材料表面进行刻蚀。
反应离子刻蚀的过程可以分为三个主要阶段:电离阶段、加速阶段和反应阶段。
1.电离阶段:利用高频放电使得气体中的原子或分子电离,产生大量正离子和电子。
2.加速阶段:通过电场作用,正离子在电场中加速并进入工作间隙,形成高速离子束。
3.反应阶段:离子束与材料表面发生碰撞,产生物理或化学反应,刻蚀材料表面。
设备反应离子刻蚀需要使用专门的设备,称为反应离子刻蚀机。
RIE机由多个关键组件组成:1.真空腔:用于形成高真空环境,防止气体分子的散射和干扰。
2.高频电源:提供高频放电电场,并驱动气体电离。
3.外加电源:用于控制电场及正离子束的加速程度和方向。
4.气体供给系统:提供刻蚀所需的气体,并控制气体的流量和压力。
5.气体排放系统:将刻蚀产生的废气排放到安全区域。
应用反应离子刻蚀在微纳加工领域具有广泛的应用,主要包括以下几个方面:1.半导体器件制造:RIE技术被广泛用于制造芯片中的光罩和微细结构,如晶体管、电容和互联线路等。
2.光学器件制造:RIE可以用于制造光学器件,如光纤、光波导和微透镜等。
3.微纳加工:RIE可以用于制造微纳米结构和微模具,如微通道、微阵列和微流体器件等。
4.纳米科技研究:RIE可以用于制备纳米材料和纳米结构,如纳米颗粒、纳米线和纳米孔洞等。
优势与挑战反应离子刻蚀具有以下优势:1.高加工速度:RIE可以在较短的时间内实现高精度的刻蚀,提高生产效率。
2.高精度:RIE可以实现亚微米级别的刻蚀精度,满足微纳加工的要求。
反应离子刻蚀原理的应用
反应离子刻蚀原理的应用1. 引言反应离子刻蚀(Reactive Ion Etching, RIE)是一种常用的半导体制造工艺,可以用于微纳加工、半导体器件制造以及纳米材料研究等领域。
本文将介绍反应离子刻蚀的原理及其在实际应用中的重要性。
2. 反应离子刻蚀的原理反应离子刻蚀是一种通过气体离子与样品表面原子发生化学反应,使表面原子发生剥离的过程。
它主要分为两步:离子轰击和表面反应。
2.1 离子轰击离子轰击是指将高能离子加速并聚焦到样品表面,使其与表面原子发生碰撞。
这些离子具有足够的能量,能够克服表面原子之间的键能,并将其剥离。
离子轰击的能量和角度可以通过调整加速器电压和样品的摆放角度来控制。
2.2 表面反应离子轰击之后,被剥离的表面原子会与气体中的反应物发生化学反应。
这些反应物通常是一种或多种气体,如氧气、氟气等。
表面的化学反应会产生新的化合物,这些化合物是可挥发的并可从表面去除的。
2.3 反应选择性反应离子刻蚀的一个重要特点是反应选择性。
不同材料对不同的气体反应物具有不同的反应速率。
通过选择合适的气体反应物,可以实现对特定材料的选择性刻蚀。
这对于复杂的器件制造过程以及纳米材料的研究非常重要。
3. 反应离子刻蚀的应用3.1 微纳加工反应离子刻蚀在微纳加工领域有着广泛的应用。
它可以用于制作微电子元件、微机械系统和微电子传感器等。
通过控制离子的能量和角度以及选择适当的气体反应物,可以实现高精度、高选择性的微纳加工。
3.2 半导体器件制造反应离子刻蚀在半导体器件制造过程中起到至关重要的作用。
它可以用于制作金属线路、介质层、光掩膜以及其他重要的器件结构。
反应离子刻蚀可以实现高分辨率、高可控性的图案转移,是制造高性能半导体器件的关键步骤。
3.3 纳米材料研究反应离子刻蚀也被广泛应用于纳米材料研究领域。
通过调整离子能量和角度以及气体反应物的选择,可以在纳米材料表面产生特定的形状和尺寸。
这些特定形状和尺寸的纳米材料在电子、光学、能量储存等领域具有重要的应用前景。
反应离子刻蚀的机理及其实验研究方法
反应离子刻蚀的机理及其实验研究方法目前,许多科学家都在研究一种物质——离子刻蚀剂。
这种物质可以将单分子层的大分子裂解成单个的低聚体,这些低聚体通过氢键的作用,重新形成更大的高聚体。
这就是科学家们称之为分子克隆的过程。
基本原理是在水溶液中或气相中通过电离辐射诱发的自由基化学反应过程。
1。
电离辐射诱发自由基的化学反应机制实验1:用甲基三甲氧基硅烷( TMMO)水溶液来模拟水溶液中的离子刻蚀剂。
在含有TMMO的水溶液中,即使在很窄的pH值范围内,也能看到有很强的离子活性的氢气自由基出现。
此时的自由基被称为“甲基三甲氧基硅烷的硅自由基”。
实验还证明了在碱性介质中,在不同温度下离子活性会发生变化,但在高温下甲基三甲氧基硅烷的硅自由基会与空气中的氧自由基( O, n)发生反应,消耗掉氧自由基,并生成稳定的硅酸盐自由基( Si, n)。
实验2:在不同酸度和不同离子浓度下离子活性也会发生变化。
结论:离子活性在某一特定范围内随着离子浓度的增加而增加,但超过一定值后,再继续增加离子浓度,离子活性不再随着离子浓度的增加而增加,并开始缓慢减小。
这表明在离子刻蚀剂中离子活性主要取决于离子浓度,而离子浓度又取决于离子活性。
2。
反应离子刻蚀的机理实验3:利用前面得到的模型,我们可以推导出离子刻蚀的机理。
从图1、 2中我们可以看出,硅离子是从含有反应离子的单分子层通过其它共价键或者氢键重新形成了二氧化硅的大分子层,此时的大分子层不仅具有硅原子之间的共价键和氢键,而且硅原子还形成了硅烷和硅烷的共价键。
当在水溶液中向二氧化硅大分子层中加入氢离子时,硅烷和硅烷之间形成氢键,从而抑制了氢离子的进一步渗入,结果,大分子层不能被分解成单个的硅原子。
当然,当电压升高时,二氧化硅大分子层就会被分解成硅原子和氢离子,于是氢离子的迁移速率就会降低,最终停止渗入。
2。
反应离子刻蚀的实验实验3:利用前面得到的模型,我们可以推导出离子刻蚀的实验。
根据实验1中所说的离子刻蚀机制,在前面的反应中我们假设负电位已经建立,并且要求负电位必须要建立起来,而且不会消失,只能改变,从而达到引发离子刻蚀的作用。
等离子体刻蚀反应离子刻蚀
等离子体刻蚀反应离子刻蚀
等离子体刻蚀和反应离子刻蚀是现代微纳加工中广泛应用的两种微细加工技术。
它们可以通过高能粒子的轰击,在材料表面上形成微米级别的凹凸结构,以实现微米级甚至纳米级别的加工精度。
等离子体刻蚀是利用等离子体对材料表面进行加工的一种技术。
等离子体是指气体在高功率电场作用下电离后形成的带正负电荷的气体体系,其中包括电子、离子、自由基等。
在等离子体刻蚀中,首先需要将加工目标材料置于真空室中,然后通过高频电场或者直流电场加热气体,使其电离并形成等离子体。
等离子体与材料表面相互作用,通过离子轰击、化学反应等方式,逐渐将材料表面的原子或分子剥离,从而实现微米级别的加工。
反应离子刻蚀则是利用化学反应对材料表面进行加工的一种技术。
在反应离子刻蚀中,首先需要将加工目标材料置于真空室中,然后将反应气体(如氟化氢、氧化氢、氧气等)引入真空室中,并通过高频电场或者直流电场加热气体,使其电离并形成等离子体。
等离子体与反应气体发生化学反应,产生出一些可与加工目标材料反应的化合物,在离子轰击的同时,这些化合物也能够对材料表面进行化学反应,从而逐渐将材料表面的原子或分子剥离,实现微米级别的加工。
等离子体刻蚀和反应离子刻蚀在微纳加工中具有很大的应用前景。
它们可以实现高精度、高效率的微米级别加工,同时也是制备微纳
器件的重要工艺之一。
比如,在集成电路、光学器件、生物芯片等领域,等离子体刻蚀和反应离子刻蚀被广泛应用,为微纳加工提供了可靠的技术支持。
等离子体刻蚀和反应离子刻蚀是现代微纳加工中不可或缺的两种技术。
它们通过高能粒子的轰击和化学反应,实现了微米级别的加工精度,为微纳器件制备提供了有效的技术支持。
- 1、下载文档前请自行甄别文档内容的完整性,平台不提供额外的编辑、内容补充、找答案等附加服务。
- 2、"仅部分预览"的文档,不可在线预览部分如存在完整性等问题,可反馈申请退款(可完整预览的文档不适用该条件!)。
- 3、如文档侵犯您的权益,请联系客服反馈,我们会尽快为您处理(人工客服工作时间:9:00-18:30)。
反应离子刻蚀硅阵列实验
一、实验目的:
1、掌握反应离子刻蚀的基本原理。
2、掌握利用单晶硅刻蚀硅阵列的实验流程。
3、了解刻蚀后的硅阵列的表征方法。
二、实验原理
刻蚀技术分为湿法刻蚀和干法刻蚀。
湿法刻蚀是传统的刻蚀工艺,把硅片浸泡在一定的化学试剂或试剂溶液中,使没有被抗蚀剂掩蔽的那一部分薄膜表面与试剂发生化学反应而被除去,其优点是操作简便、对设备要求低、易于实现大批量生产,并且刻蚀的选择性也好。
但是,它具有各项同性的缺点,即在刻蚀过程不但有所需要的纵向刻蚀,还有不需要的横向刻蚀,因而精度差,线宽一般在3μm以上。
干法刻蚀是应大规模集成电路生产的需要而被开发出的精细加工技术,它具有各项异性的特点,在最大限度上保证了纵向刻蚀,还控制了横向刻蚀。
反应离子刻蚀(Reactive Ion Etching,RIE)是干法刻蚀的一种,是以物理溅射为主并兼有化学反应的过程,通过物理溅射实现纵向刻蚀,同时应用化学反应来达到所要求的选择比,其基本工作原理是刻蚀气体(主要是F基和Cl基的气体)在高频电场(频率通常为13.56MHz)作用下产生辉光放电,使气体分子或原子发生电离,形成“等离子体”(Plasma)。
在等离子体中,包含有正离子(Ion+)、负离子(Ion-)、游离基(Radical)和自由电子(e)。
游离基在化学上是很活波的,它与被刻蚀的材料发生化学反应,生成能够由气流带走的挥发性化合物,从而实现化学刻蚀。
而质量较大的正离子,被阴极附近带负电的鞘层电压有效的加速,垂直轰击放置于阴极表面的硅片,以较大的动量进行物理刻蚀,这种离子轰击可大大加快表面的化学反应及反应生成物的脱附,从而导致很高的刻蚀速率。
三、实验装置
ME-3A型多功能磁增强反应离子刻蚀机
四、实验内容和步骤
1. 硅片的清洗:采用RCA标准清洗法进行硅片的清洗,具体步骤:(1)SPM清洗:去除硅片表面的有机污物和部分金属,(2)DHF清洗:去除硅片表面的自然氧化膜,(3)APM清洗(SC-1):去除硅片表面的颗粒和金属,(4)HPM清洗:去除硅表面的钠、铁、镁和锌等金属污染物。
每一步骤完成后用去离子水将硅片冲洗干净后方可进行下一步骤。
在硅片较为清洁的情况下可采用以下简化步骤进行清洗:(1)在丙酮中超声5min,去除表面有机污物,(2)在无水乙醇中超声5min,去除硅片表面的颗粒物等无机污物。
之后用去离子水冲洗干净。
2. 掩膜的制备:通过电子束蒸发技术,在已清洁的硅片上蒸镀上10nm Au膜,之后在快速退火炉中600℃退火2min,使Au膜熔成小颗粒,作为刻蚀的掩膜。
(注:前两步骤为实验准备工作,可以由实验指导人员提前完成,并向学生演示。
)
3.硅片的刻蚀:
(1)装片:开冷却水,开总电源,预热射频电源灯丝后放气,打开反应室盖,将硅片放在圆盘形金属下电极上,盖严反应室上盖。
(2)抽真空:检查“分子泵”旋钮是否处于“开”状态,若是,启动机械泵,约30s后分子泵自动启动,待分子泵进入稳定工作状态后进行后续操作。
(3)选择刻蚀方式:选择MERIE刻蚀方式,定时90min。
(4)通气:将流量计开关置于“阀控”,打开CF4进气阀门,调节气体流量40SCCM,通过“抽速调节”旋钮调节气压,保持工作气压4Pa。
(5)启辉刻蚀:按“启动”,开板压Ua至ON,启辉工作,调节输出功率并调节匹配器,使反射功率指示Pr最小
(6)刻蚀结束,关闭系统:关闭气路,抽反应室内残余气体1~3min后,按“关泵”,机械泵停止工作后放气,取出样品。
五、实验结果分析及思考
1、试讨论刻蚀精度用哪些参数进行衡量?并对每个参数进行简单的讨论。
刻蚀Si的化学反应方程式。
2、试写出利用CF
4
3、试总结本实验过程中对Si阵列质量的影响因素。
附:
RIE操作步骤
一、 刻蚀前的准备
1、开冷却水,抽气管放到窗外;
2、开“总电源”:将总电源开关向上拨(A、B、C三指示灯亮表明正常);
3、预热射频电源灯丝:将“Uf”(橙黄色)开关置于“ON”,指示灯亮,一般须
预热5min才可加板压Ua;
4、开流量计电源:将流量显示面板的“电源”开关拨向上方,显示灯亮;
5、装片:按下“放气”(黑色)按钮,等待放气约1min,打开反应室盖,将待
刻蚀的样品放在圆盘形金属下电极上,盖严反应室上盖(注:一定要确认上盖已经平整地压在密封圈上后,才可进行后续操作!!!);
6、检查气路:检查“阀1—阀4”、“总阀”、两“清洗”阀是否关闭,若未关闭,
应将它顺时针旋转至拧不动为止。
(注:关阀的时候顺时针转到不能动为止,开阀的时候逆时针转动1~2圈即可);
7、检查“分子泵”旋钮是否处于“开”的位置:通常情况下,“分子泵”旋钮应
处于“开”的位置(启动机械泵之后约30s会自动启动分子泵;若开始“分子泵”旋钮不是处于“开”的位置,也可手动启动分子泵,不建议这样操作),如果不打算使用分子泵,则可将“分子泵”旋钮拨向“关”。
二、 刻蚀操作
6、抽真空:按“开泵”按钮,指示灯亮,启动机械泵(若“分子泵”旋钮处于
“开”位置,则机械泵启动30s后,分子泵会自动启动,默认为此种方式),约30s后,分子泵启动,指示灯亮,“分子泵电源”上的“频率显示”窗口显示分子泵电源提供的驱动频率,当“分子泵电源”窗口上绿灯亮,分子泵频率稳定在约为704Hz时,表明分子泵已完成加速过程进入稳定的工作状态(分子泵进入稳定工作状态才可进行后续操作);
6、选择刻蚀方式:拨动MERIE/RIE开关选择在刻蚀时是否加磁场(选择MERIE
为加磁场,选择RIE为不加磁场);
6、定时:确定是否采用“定时”模式,设定时间显示器(从左至右分别为X10
分、X1分、X10秒、X1秒);
6、通气:
(1)此时分子泵频率应稳定在约704Hz,打开总阀;
(2)选择所用气体,流量计开关置于“阀控”,打开所用气体的进气阀
门;(注:通气顺序为开总阀—开流量计—开气体进气阀,刻蚀结束后关气顺序为关气体进气阀—关流量计—关总阀)
(3)调节气体流量和反应室内气压,气体流量稳定后,通过反应室右后方“抽速调节”旋钮调节气压,刻线水平时抽速最大,垂直时抽速最小;(若工作气压为1~10Pa,应用机械泵+分子泵,若工作气压为10~100Pa,应关闭分子泵只用机械泵)
注:(1)建议使用某种气体刻蚀之前先抽空该气体气路(若连续使用该种气体刻蚀,则只需在第一次刻蚀前进行该操作),具体步骤为:打开总阀、流量计及该气体阀门之后,打开该气体气瓶上的减压阀(此时气瓶总阀不打开),等待片刻至该气体流量计显示为0,表明该气体气路已抽空,关闭减压阀,打开气瓶总阀,开减压阀,减压阀输出0.1~0.2MPa即可,不可超过0.3MPa,若刻蚀时间较短,可在打开减压阀之后关闭总阀,以节约气体。
(2)当分子泵处于工作状态时,不允许将流量计置于“清洗”档,否则会使分子泵过载。
5、启辉刻蚀:
(1)对不定时情况:开板压Ua至ON,即可启辉,对定时情况:按一下“启动”,然后开板压Ua至ON,启辉工作,同时定时器开始计时,到所设定的时间后,板压会自动关闭;
(2)启辉后调节匹配器的“C1调节”和“C2调节”,使反射功率指示Pr最小;(若气流、气压条件不变,匹配只需开始调节一次,以后只需微调,条件改变,则需重新调节匹配)
(3)调节输出功率,先调节“Ua粗调”,分几次逐渐增大到所需功率值,再调节“Ua细调”,进行功率微调,每一次改变输出功率,都需要调节匹配器的“C1调节”和“C2调节”,使反射功率Pr最小;
注:(1)实际操作时,可先按下“启动”,迅速调节好匹配和输出功率,在按下
“启动”,这样定时器会重新计时;
(2)启辉时,若反射功率很大,应先降低输出功率,待调好匹配(即反射功率最小)后在调高输出功率;匹配器调节技巧请参见RIE说明书。
6、关气,关泵、关水:
刻蚀结束后,先关板压“Ua”开关(对于定时刻蚀情况,板压会自动关闭,若不能自动关闭,按下红色的“Ua-OFF”键结束刻蚀),然后关气体进气阀,抽空气路即流量计显示为0,关流量计,关总阀,抽反应室内残余腐蚀气体1~3min,然后按照以下步骤关机:
(1)按“关泵”,分子泵先停止工作,约1min后机械泵自动停机;
(2)机械泵停止工作后,按“放气”按键,约35s后充气完毕,可打开反应室上盖,取出样品(打开上盖前请确认板压“Ua-ON”开关已关闭);
(3)关总电源;
(4)每天最后一次刻蚀结束后,应关闭气瓶减压阀和总阀并抽空管路里残余气体,关闭冷却水。
注:刻蚀机在不工作的时候,所有阀门及流量计应处于关闭状态;刻蚀结束后,对反应室抽真空;不用的气体及时关闭气瓶减压阀和总阀。