循环流化床燃煤锅炉石灰湿法烟气脱硫工艺的应用
烟气脱硫技术简介

国内烟气脱硫技术我国目前的经济条件和技术条件还不允许象发术达国家那样投入大量的人力和财力,并且在对二氧化硫的治理方面起步很晚,至今还处于摸索阶段,国内一些电厂的烟气脱硫装置大部分欧洲、美国、日本引进的技术,或者是试验性的,且设备处理的烟气量很小,还不成熟。
不过由于近几年国家环保要求的严格,脱硫工程是所有新建电厂必须的建设的。
因此我国开始逐步以国外的技术为基础研制适合自己国家的脱硫技术。
以下是国内在用的脱硫技术中较为成熟的一些,由于资料有限只能列举其中的一些供读者阅读。
石灰石——石膏法烟气脱硫工艺石灰石——石膏法脱硫工艺是世界上应用最广泛的一种脱硫技术,日本、德国、美国的火力发电厂采用的烟气脱硫装置约90%采用此工艺。
它的工作原理是:将石灰石粉加水制成浆液作为吸收剂泵入吸收塔与烟气充分接触混合,烟气中的二氧化硫与浆液中的碳酸钙以及从塔下部鼓入的空气进行氧化反应生成硫酸钙,硫酸钙达到一定饱和度后,结晶形成二水石膏。
经吸收塔排出的石膏浆液经浓缩、脱水,使其含水量小于10%,然后用输送机送至石膏贮仓堆放,脱硫后的烟气经过除雾器除去雾滴,再经过换热器加热升温后,由烟囱排入大气。
由于吸收塔内吸收剂浆液通过循环泵反复循环与烟气接触,吸收剂利用率很高,钙硫比较低,脱硫效率可大于95% 。
注意:锅炉出来的烟气经过除尘之后温度还是很高,而进入脱硫系统,温度是不能太高,温度过高,则吸收塔内的石膏结晶受到很大影响,而且设备的腐蚀和磨蚀会非常严重。
一般在原烟气和净烟气之间加设GGH(气气换热器),一方面对原烟气进行降温,以利于后面处理。
一方面对净烟气进行升温,有利于排烟的抬升,减少烟囱雨的形成,也在直观上减少烟囱排烟的量。
而且如果净烟气不升温的话,SO3会形成酸露,对烟囱的腐蚀非常严重。
脱硫过程的温度一般控制在40-60之间,不是需要太高的温度进行的。
旋转喷雾干燥烟气脱硫工艺喷雾干燥法脱硫工艺以石灰为脱硫吸收剂,石灰经消化并加水制成消石灰乳,消石灰乳由泵打入位于吸收塔内的雾化装置,在吸收塔内,被雾化成细小液滴的吸收剂与烟气混合接触,与烟气中的SO2发生化学反应生成CaSO3,烟气中的SO2被脱除。
目前广泛使用的5种脱硫工艺技术方案简介

目前广泛使用的5种脱硫工艺技术方案简介目录目前广泛使用的5种脱硫工艺技术方案简介 (1)1、湿法烟气脱硫工艺 (1)2、半干法烟气脱硫工艺 (3)3、烟气循环流化床脱硫工艺 (4)4、干法脱硫工艺 (5)5、NID半干法烟气脱硫 (6)目前世界上燃煤电厂烟气脱硫工艺方法很多,这些方法的应用主要取决于锅炉容量和调峰要求、燃烧设备的类型、燃料的种类和含硫量的多少、脱硫率、脱硫剂的供应条件及电厂的地理条件、副产品的利用等因素。
近年来,我国电力工业部门在烟气脱硫技术引进工作方面加大了力度,对目前世界上电厂锅炉较广泛采用的脱硫工艺都有成功运行工程,主要有湿法烟气脱硫、干法烟气脱硫和半干法烟气脱硫。
现将目前应用较为广泛的几种脱硫工艺原理、特点及其应用状况简要说明如下:1、湿法烟气脱硫工艺湿法烟气脱硫包括石灰石/石灰-石膏法烟气脱硫、海水烟气脱硫和用钠基、镁基、氨作吸收剂,一般用于小型电厂和工业锅炉。
氨洗涤法可达很高的脱硫效率,副产物硫酸铵和硝酸铵是可出售的化肥。
以海水为吸收剂的工艺具有结构简单、不用投加化学品、投资小和运行费用低等特点。
而以石灰石/石灰-石膏法湿法烟气脱硫应用最广。
《石灰石/石灰-石膏法烟气脱硫工程设计规范》中关于湿法烟气脱硫工艺的选择原则为:燃用含硫量Sar≥2%煤的机组或大容量机组(200MW及以上)的电厂锅炉建设烟气脱硫装置时,宜优先采用石灰石-石膏湿法脱硫工艺,脱硫率应保证在96%以上。
湿法烟气脱硫工艺采用碱性浆液或溶液作吸收剂,其中石灰石/石灰-石膏湿法脱硫是目前世界上技术最成熟、应用最广,运行最可靠的脱硫工艺方法,石灰石经破碎磨细成粉状与水混合搅拌制成吸收剂浆液;也可以将石灰石直接湿磨成石灰石浆液。
石灰石或石灰浆液在吸收塔内,与烟气接触混合,烟气中的SO2与浆液中的碳酸钙以及鼓入的氧化空气进行化学反应,最终反应产物为石膏,经脱水装置脱水后可抛弃,也可以石膏形式回收。
由于吸收剂浆液的循环利用,脱硫吸收剂的利用率很高。
循环流化床锅炉烟气脱硫技术
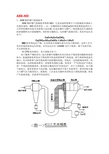
ABB-NID1、ABB锅炉烟气脱硫技术ABB锅炉烟气脱硫技术简称NID,它是由旋转喷雾半干法脱硫技术基础上发展而来的。
NID的原理是:以一定细度的石灰粉(CaO)经消化增湿处理后与大倍率的循环灰混合直接喷入反应器,在反应器中与烟气二氧化硫反应生成固态的亚硫酸钙及少量硫酸钙,再经除尘器除尘,达到烟气脱硫目的。
其化学反应式如下:CaO+H2O=Ca(OH)2Ca(OH)2+SO2=CaSO3·1/2H2O+1/2H2ONID技术将反应产物,石灰和水在容器中混合在加入吸收塔。
这种工艺只有很有限的商业运行经验,并且仅运行在100MW及以下机组,属于发展中的,不完善的技术。
和CFB技术相比,其主要缺点如下:由于黏性产物的存在,混合容器中频繁的有灰沉积由于吸收塔内颗粒的表面积小,造成脱硫效率低由于吸收塔中较高的固体和气体流速,使气体固体流速差减小,而且固体和气体在吸收塔中的滞留时间短,导致在一定的脱硫效率时,钙硫比较高,总的脱硫效果差。
需要配布袋除尘器,使其有一个”后续反应”才能达到一个稍高的脱硫效率,配电除尘器则没有”后续反应”。
对于大型机组,由于烟气量较大,通常需要多个反应器,反应器的增多不便于负荷调节,调节时除尘器入口烟气压力偏差较大。
脱硫剂、工艺水以及循环灰同时进入增湿消化器,容易产生粘接现象,负荷调节比较滞后。
Wulff-RCFBWulFF的CFB技术来源于80年代后期转到Wulff 去的鲁奇公司的雇员。
而LEE 近年来开发的新技术,Wulff公司没有,因此其技术有许多弱点:电除尘器的水平进口,直接积灰和气流与灰的分布不均。
没有要求再循环系统,对锅炉负荷的变化差,并直接导致在满负荷时烟气压头损失大。
消石灰和再循环产物的加入点靠近喷水点,使脱硫产物的黏性增加。
喷嘴上部引入再循环灰将对流化动态有负面影响,导致流化床中灰分布不均,在低负荷时,流化速度降低,循环灰容易从流化床掉入进口烟道中,严重时,大量的循环灰可将喷嘴堵塞。
循环流化床在脱硫技术中的应用
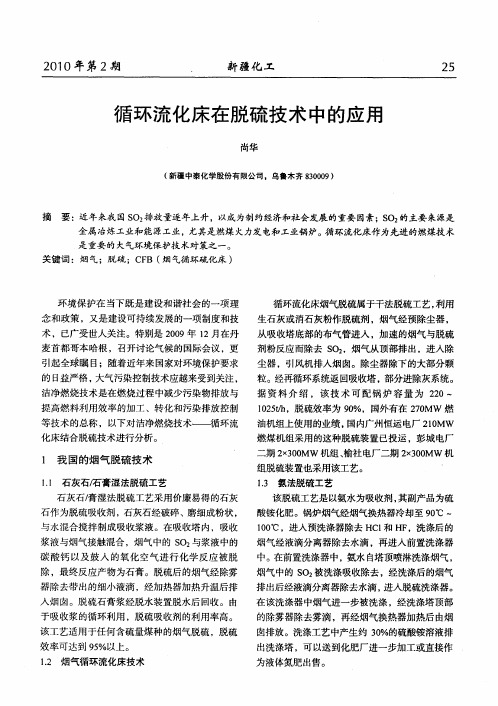
本工艺流程 由排烟预除尘、 烟气冷却 、 氨的充 人、电子束照射和副产品捕集等工序所组成 。锅 炉烟气经过除尘器粗滤处理之后进人冷却塔 ,冷
脱硫成本中等 ;
却塔 内喷射冷却水将烟气冷却 到适合于脱硫 、脱
硝处理的温度( 7 ℃) 约 O 。在反应器进 口处将一定 的氨气 、压缩空气和软水混合 喷人,冷却后的烟
1 烟气 循环 流化 床技 术 . 2
为液体氮肥出售。
2 6
1 喷雾干 燥法脱 硫工艺 . 4
新疆化工
21 0 0年第 2 期
() 3 丹麦 F . i 公司开发的气体悬浮吸收 .S t L mh
喷雾干燥法脱硫工艺以石灰为脱硫吸收剂, 石
灰 经消化 加 水制 成消 石灰乳 ,消石灰 乳在 吸收塔 内被 雾化成 细小 液滴 ,与烟 气 中的 S 2 0 发生化学 反应 生成 C S 3 C S , a O 和 aO4达到脱 除烟气 中的 S 2 O
(S ) G A 烟气脱硫技术。
21 工艺特 点 .
C B 工 艺具 有 以下 主 要 特点 :脱 硫 率 高 F ( a = .~1 时 , 8% ,与湿法相接近 , C/ 1 S 2 . 5 >5 ) 容易 选择最佳的 C B 操作气速 ,使得气固两相流在 F
的 目的。脱硫反应产物及未被利用的吸收剂 以干 燥的颗粒物形式随烟气带出吸收塔 , 进人除尘器 被收集下来 。除尘后的烟气经烟囱排放 。
的 1益严格 , 3 大气污染控制技术应越来受到关注 , 洁净燃烧技术是在燃烧过程中减少污染物排放与 提高燃料利用效率的加工、转化和污染排放控制 等技术的总称 ,以下对洁净燃烧技术——循 环流 化床结合脱硫技术进行分析。
据 资料 介 绍 ,该 技 术 可 配锅 炉 容 量 为 20 2
燃煤电厂各种干法半干法湿法脱硫技术及优缺点汇总

燃煤电厂各种干法、半干法、湿法脱硫技术及优缺点汇总目前,湿法烟气脱硫技术最为成熟,已得到大规模工业化应用,但由于投资成本高还需对工艺和设备开展优化;干法烟气脱硫技术不存在腐蚀和结露等问题,但脱硫率远低于湿法脱硫技术,一般单想电厂都不会选用,须进一步开发基于新脱硫原理的干法脱硫工艺;半干法脱硫技术脱硫率高,但不适合大容量燃烧设备。
不同的工况选择最符合的脱硫方法才会得到最大的经济效益,接下来根据电厂脱硫技术的选择原则来分析各种工艺的优缺点、适用条件。
电厂脱硫技术的选择原则:1、脱硫技术相对成熟,脱硫效率高,能到达环保控制要求,已经得到推广与应用。
2、脱硫成本比较经济合理,包括前期投资和后期运营。
3、脱硫所产生的副产品是否好处理,最好不造成二次污染,或者具有可回收利用价值。
4、对发电燃煤煤质不受影响,及对硫含量适用范围广。
5、脱硫剂的能够长期的供给,且价格要低廉一、干法脱硫干法脱硫工艺工艺用于电厂烟气脱硫始于20世纪80年代初。
传统的干法脱硫工艺主要有干法喷钙脱硫工艺、荷电干法吸收剂喷射脱硫法、电子束照射法、吸附法等。
传统的干法脱硫技术有工艺简单投资少,设备简占地面积小且不存在腐蚀和结露,副产品是固态无二次污染等优点,在缺水地区优势明显。
但是脱硫效率很低,一般脱硫效率只能到达70%左右,难以满足排放要求。
干法喷钙脱硫工艺工艺介绍磨细的石灰石粉通过气力方式喷人锅炉炉膛中温度为900〜1250。
C的区域在炉内发生的化学反应包括石灰石的分解和煨烧,S02和SO3与生成的Cao之间的反应。
颗粒状的反应产物与飞灰的混合物被烟气流带人活化塔中;剩余的CaO与水反应,在活化塔内生成Ca(OH)2,而Ca(OH)2很快与S02反应生成CaSo3,其中部分CaSO3被氧化成CaSo4;脱硫产物呈干粉状,大部分与飞灰一起被电除尘器收集下来,其余的从活化塔底部分离出来从电除尘器和活化塔底部收集到的部分飞灰通过再循环返回活化塔中。
电厂脱硫工艺

电厂脱硫工艺电厂脱硫工艺多为烟气脱硫(FlueGasDesulfurization,简称FGD)是目前燃煤电厂控制SO2气体排放最有效和应用最广的技术。
电厂烟气脱硫工艺电厂烟气脱硫工艺按脱硫剂及脱硫反应产物的状态可分为湿法、干法及半干法三大类。
1、湿法脱硫工艺世界各国的湿法烟气脱硫工艺流程、形式和机理大同小异,主要是以碱性溶液为脱硫剂吸收烟气中的SO2。
湿法脱硫工艺主要有:石灰石/石灰-石膏法、海水法、双碱法、亚钠循环法、氧化镁法等。
2、干法脱硫工艺工艺用于电厂烟气脱硫始于20世纪80年代初。
干法脱硫工艺主要有:荷电干法吸收剂喷射脱硫法、电子束照射法、吸附法等。
3、半干法脱硫工艺工艺融合了湿法、干法脱硫工艺的优点,具有广阔的应用前景。
半干法脱硫工艺主要有:喷雾干燥法、循环流化床法、增湿灰循环法、烟道喷射法等。
目前烟气脱硫技术以湿法脱硫工艺占主导,同时干法、半干法脱硫工艺也在发展中。
四大电厂烟气脱硫工艺石灰石/石灰-石膏法是技术最成熟、应用最多、运行状况最稳定的方法,其脱硫效率在95%以上。
石灰石/石灰-石膏湿法是300MW及以上机组中最广泛采用的脱硫方式。
世界各国(如德国、日本等)在大型火电厂中,90%以上采用湿式石灰石/石灰-石膏法烟气脱硫工艺。
目前,石灰石/石灰法是世界上应用最多的一种FGD工艺,对高硫煤,脱硫率可在90%以上,对低硫煤,脱硫率可在95%以上。
喷雾干燥法烟气脱硫最先由美国JOY公司和丹麦NiroAtomier公司共同开发的脱硫工艺,20世纪70年代中期得到发展,第1台电站喷雾干燥脱硫装置于1980年在美国北方电网河滨电站投入运行,并在电力工业迅速推广应用。
该工艺目前已基本成熟,在欧洲应用较多,法国、奥地利、丹麦、瑞典、芬兰等国家均建有这种设备。
器,用以脱除烟气中的SO2。
炉内喷钙脱硫技术早在20世纪50年代中期就已开始研究,但由于脱硫效率不高(只有15%~40%),钙利用率低(15%)而被搁置。
循环流化床燃煤锅炉石灰湿法烟气脱硫工艺的应用

I o t ie h ieo ecr u a in p n y t esz u r n a a i n h e e t n sz e ie t i o d mi e h p a o ze a d e o o cv a i t r t b an d t e sz ft ic lto o d b h ie c re t p ct a d t es l ci ier sd n me t e s r e s r y n z l . n c n mi ib l y wee h c y o t t t i
m an b d Ac o d n o t ec re ai n p ic pe i h d c rid o o p t t n a o t h e u D u a in s se n a eem ie h an dm e so fte i o y c r ig t h o r lt rn i l, t a a re n c m u a i b u e d s 1 h nz t y tm a d h d d tr n d t em i i n i n o o o t O h d s lh n ai nt w e, h a e a dt e s ep p l ea d s n h n i h dc lu a e h i u t e it n ea d h sc osn t earb o e n ecr u ai gp m p e uD u z l o r t eh z n h i i ei n o o T e t a ac lt dt ec r ir r ss c n a h e h i lw r d t ic lt u o z n c y a a h n
App i a i n o c lc to fTe hno o y o r ul t d Fl i z d Be o l g n Ci c a e u di e d f r
火电脱硫工艺

火电脱硫工艺一、燃烧前脱硫燃烧前脱硫通常采用物理或化学方法去除原煤中的硫分,以降低燃煤烟气中二氧化硫的排放。
常用的燃烧前脱硫技术包括:1. 洗煤技术:通过物理方法去除原煤中的部分硫分和杂质,常用的洗煤方法有重介质洗煤、浮选洗煤等。
2. 煤的脱硫技术:采用化学方法将原煤中的硫分转化为可分离的形态,常用的脱硫技术有氧化还原脱硫、化学链脱硫等。
二、燃烧中脱硫燃烧中脱硫即在燃烧过程中向炉内添加脱硫剂,以降低二氧化硫的排放。
常用的燃烧中脱硫技术包括:1. 循环流化床燃烧技术:通过向炉内添加石灰石等脱硫剂,利用循环流化床的特殊燃烧方式,使燃料和脱硫剂在炉内充分混合燃烧,提高脱硫效率。
2. 炉内喷钙技术:通过向炉内喷洒石灰石等钙基脱硫剂,利用高温燃烧产生的硫酸钙等物质,将二氧化硫转化为硫酸钙等物质,从而达到脱硫目的。
三、燃烧后脱硫燃烧后脱硫即对燃煤烟气进行脱硫处理,以进一步降低二氧化硫的排放。
常用的燃烧后脱硫技术包括:1. 湿法脱硫技术:利用碱性溶液(如石灰石、氧化镁等)吸收烟气中的二氧化硫,生成硫酸盐或亚硫酸盐,再将吸收液进行氧化、结晶、脱水等处理,最终得到硫磺或硫酸等产品。
常用的湿法脱硫技术有石灰石-石膏法、氧化镁法等。
2. 干法脱硫技术:利用干态的吸附剂(如活性炭、分子筛等)吸附烟气中的二氧化硫,达到脱硫目的。
常用的干法脱硫技术有活性炭吸附法、分子筛吸附法等。
3. 电子束照射法:利用高能电子束照射烟气,使二氧化硫和氮氧化物转化为硫酸和硝酸,再与氨反应生成硫酸铵和硝酸铵,从而达到脱硫脱硝的目的。
4. 脉冲电晕法:利用高压脉冲电源产生高能电子,激活烟气中的氧气和水分子,产生强氧化性自由基,将二氧化硫和氮氧化物转化为硫酸和硝酸,再与添加的氨反应生成硫酸铵和硝酸铵。
四、烟气处理对烟气进行除尘、脱硝、脱汞等处理,以降低烟气中有害物质的排放。
常用的烟气处理技术包括:1. 除尘技术:通过物理或化学方法去除烟气中的粉尘颗粒物,常用的除尘技术有机械除尘、静电除尘、袋式除尘等。
- 1、下载文档前请自行甄别文档内容的完整性,平台不提供额外的编辑、内容补充、找答案等附加服务。
- 2、"仅部分预览"的文档,不可在线预览部分如存在完整性等问题,可反馈申请退款(可完整预览的文档不适用该条件!)。
- 3、如文档侵犯您的权益,请联系客服反馈,我们会尽快为您处理(人工客服工作时间:9:00-18:30)。
广东化工2011年第1期· 200 · 第38卷总第213期循环流化床燃煤锅炉石灰湿法烟气脱硫工艺的应用付帅,董瑞斌,胡红艳(南昌大学环境与化学工程学院,江西南昌 330031)[摘 要]文章对二氧化硫污染现状及CFB-FGD系统的应用情况进行了综述,介绍其反应机理。
并根据某厂的要求,选择了以喷淋塔为主体的石灰湿法脱硫工艺,根据相关原理进行了脱硫系统工艺计算,确定了脱硫塔、烟气和浆液管道、循环池等的主要尺寸,进而选择了风机和循环泵,由所得浆液流量及选取的浆液停留时间计算得出循环池的尺寸,并分析其工艺的经济可行性。
为锅炉烟气脱硫提供了参考依据。
[关键词]烟气脱硫;喷淋塔;吸收塔[中图分类号]TH [文献标识码]A [文章编号]1007-1865(2011)01-0200-03Application of Technology on Circulated Fluidized Bed forFlue Gas Desulphurization Coal-fired BoilerFu Shuai, Dong Ruibin, Hu Hongyan(School of Environment & Chemical Engineering, Nanchang University, Nanchang 330031, China)Abstract: The design had carried on the summary to the sulfur dioxide pollution and the CFB-FGD system application situation, and introduced its reflect mechanism. And according to the request of the project description, it had chosen the wet lime flue gas desulphurization process which took the sprays tower as the main body. According to the correlation principle, it had carried on computation about the desulphurization system and had determined the main dimension of the desulphurization tower, the haze and the size pipeline and so on. Then it had calculated the circuitry resistance and has chosen the air blower and the circulating pump. It obtained the size of the circulation pond by the size current capacity and the selection size resident time to demister the spray nozzle, and economic viability were also introduced in the paper. It can supply reference basis data for this kind of enterprise to treat sulfur dioxide in flue gas.Keywords: CFB-FGD;the sprays tower;the absorption tower我国是以燃煤为主的国家,我国的电力供给以火力发电为主,燃煤发电在电力供给中占80 %以上。
以煤为主的能源消耗结构导致了二氧化硫的大量排放。
煤炭燃烧产生的烟气中含有大量粉尘、有害气体(主要为SO X, NO X等)和温室气体CO2等污染物,造成了严重的环境问题。
目前全国62 %以上的城市SO2浓度超过国家《环境空气质量标准》二级标准,占全国面积40 %左右的地区受到大量排放引起的酸雨污染,造成了难以估量的经济和社会损失DI对SO2危害的认识导致许多国家相继制定SO2排放的控制标准。
目前,控制燃煤SO2污染技术可分为四类:煤燃烧前脱硫、燃烧中脱硫、燃烧后烟气脱硫以及煤转化过程中脱硫。
这四类脱硫技术中,燃烧后烟气脱硫被认为是控制SO2污染最行之有效的途径,也是目前世界上唯一大规模商业化应用的脱硫技术。
迄今,世界各国研究开发的烟气脱硫技术多达200余种,其中有的还处于实验室研究阶段,真正能应用于工业生产的不超过20种。
按脱硫过程是否加水和脱硫产物的干湿形态,烟气脱硫技术可分为湿法、半干法和干法三类工艺[1]。
目前石灰石/石灰湿法脱硫技术和循环流化床烟气脱硫技术(CFB-FGD )为世界主流脱硫技术。
石灰石/石灰湿法脱硫技术是目前世界上应用最广泛的烟气脱硫技术,超过80 %使用的是该技术。
该技术原理简单,脱硫效率和吸收剂利用率高,适应性强,其缺点是系统复杂庞大、投资高、操作维护工作量大和占地面积大。
CFB-FGD技术为20世纪80年代后期开发的一种新的脱硫技术。
该技术装置建设投资少、占地小、结构简单,易于操作,而且还能在很低的钙硫比(1.1~1.2)的情况下接近或达到湿法工艺的脱硫效率,即95 %以上[2]。
1 反应机理该法以石灰为脱硫吸收剂,通过向吸收塔内喷入含亚硫酸钙和硫酸钙的石灰浆液,使之与烟气充分接触并混合,从而对烟气进行洗涤,使得烟气中的SO2与浆液中的碱性物质以及鼓入的强制氧化空气发生化学反应,最后生成石膏,从而达到脱出SO2的目的。
其特点是脱硫效率高(大于95 %),吸收剂利用率高(大于90 %),设备运转率高,使用广泛。
其中主要化学反应为:⑴SO2进入液相并离解:SO2(g) SO2(aq) (1) SO2(aq)+H2O H+ + HSO3-(2)HSO3- H+ +SO32-(3)(2)石灰的溶解CaO(s)+H2O→Ca(OH)2(4) Ca(OH)2(s) →Ca(OH)2(aq) (5)(3)Ca(OH)2在水中的离解:Ca(OH)2 Ca2+ +2OH-(6) 溶液中H+和OH-,以及Ca2+和SO32-的化合:OH-+H+ = H2O (7) 2Ca2+ + 2 SO32-+ H2O 2CaSO3·1/2H2O (8) 在脱硫初始阶段首先生成CaSO3·1/2H2O,随着脱硫过程的进行,溶液中Ca(OH)2浓度逐渐减少,pH降低。
当溶液中的Ca(OH)2耗尽时,继续进入液相的SO2与 CaSO3·1/2H2O反应生成亚硫酸氢钙:2CaSO3·1/2H2O+2SO2+H2O 2Ca(HSO3)2(9) 脱硫液初始pH=9~11时,溶液中有CaS04·2H2O、Ca(HSO3)2、CaSO3·1/2H2O和CaCO3,4种生成物共存。
随着脱硫液初始pH的升高,Ca(HSO3)2浓度逐渐减少,当初始pH=11时,脱硫终点pH=6.3,此时无Ca(HSO3)2存在。
CaSO3·1/2H2O 和CaCO3浓度逐渐增大,表明随着脱硫液初始pH的升高,第(1-8)反应式的化学反应速率加快,同时,脱硫液吸收烟气中CO2的能力也增强,即Ca(OH)2的碳酸化速率增大:Ca(OH)2+CO2 =CaCO3+H2O (10) 本设计在循环池用风机鼓入空气,属强制氧化过程,使Ca(HSO3)2和CaSO3·1/2H2O的氧化速率较大,导致CaSO4·2H2O 生成并使浓度逐渐升高:CaSO3·1/2H2O+O2+3H2O 2CaSO4·2 H2O (11) 2Ca(HSO3)2+1/2O2+H2O CaSO4·2H2O+SO2 (12) 在循环池内脱硫液与空气接触,就有部分CaSO3·1/2H2O 或Ca(HSO3)2被氧化成CaSO4·2H2O,所以在脱硫液中CaSO4·2H2O的浓度是呈饱和状态的,CaSO4·2H2O的沉淀也主要发生在循环池脱硫后的烟气依次经过除雾器除去雾滴,加热器加热升温后,经烟囱排放,脱硫石膏可以综合利用。
目前,脱硫系统大多数采用了大处理量洗涤塔,节省投资和运行费用。
系统的运行可靠性已达99 %以上,通过添加有机酸可使脱硫效率提高到95 %以上[7]。
2 系统构成及工艺流程图烟气脱硫(FGD)装置采用高效的石灰石/石膏湿法工艺,整[收稿日期] 2010-11-23[作者简介] 付帅(1984-),男,江西樟树人,在读硕士研究生,主要研究方向为水资源学。
2011年第1期广东化工第38卷总第213期 · 201 ·套系统由以下子系统组成:(1)烟气系统;(2)脱硫剂制备系统;(3)SO2吸收系统;(4)脱硫液再生和脱硫渣处理系统;(5)石膏脱水系统;(6)供水和排放系统;(7)压缩空气系统;(8)废水处理系统;图1 循环流化床烟气脱硫工艺流程Fig.1 Circulating fluidized bed flue gas desulfurization process3 主要设计参数见表1。
表1 烟气参数[5]Tab.1 Flue gas parameters序号指标名称数值备注1 FGD进口烟气量(Nm/h,湿,5.89 % O2) 5060002 FGD进口SO2浓度(mg/Nm3,干,6.32 % O2) 39003 FGD出口SO2浓度(mg/Nm3,干,6.32 % O2) ≤4004 FGD出口含尘浓度(mg/Nm3,干,6.32 % O2) <1005 FGD进口烟气温度/℃ 1506 FGD出口烟气温度/℃<807 系统脱硫效率/% ≥958 系统可用率/% ≥ 989 FGD使用年限/a 3010 负荷变化范围/% 25~10012 石灰浆浓度/% 30浆液制备13 吸收塔浆池Cl浓度/ppm 2000运行值14 故障烟温/℃ 150旁路运行15 钙硫比Ca/S/mol ≤1.24 主要设备通过工艺参数的要求及场地选择的局限设计计算,需要以下主要设备:(1)除尘脱硫塔:l座,内径10.6 m,风速1.65 m/s左右,液气比3 L/m3,进气速度20 m/s,清洗量最大时自来水流量:15 m3/h。
(2)浆液循环池的尺寸:长×宽×高=7 m×7 m×5 m。