循环流化床烟气脱硫工艺
循环流化床烟气脱硫工艺

03
CATALOGUE
循环流化床烟气脱硫工艺的应用
在不同类型电厂的应用
大型煤电基地
循环流化床烟气脱硫工艺适用于大型煤电基地,能够满足 高硫煤的脱硫需求,降低烟气中SO2的排放量。
02
副产物的处理与回收是工艺中 不可或缺的一环,通常采用脱 水、干燥、煅烧等工序将其转 化为有价值的产物。
03Leabharlann 部分副产物可作为建筑材料、 化工原料等再利用,从而实现 资源循环利用。
控制系统
控制系统是循环流化床烟气脱硫工艺的 神经中枢,负责监测、控制整个工艺流 程。
控制系统通常包括传感器、执行器、控制器 等组成部分,能够实现自动化控制和优化操 作。
智能化控制技术
利用先进的传感器、控制 系统和人工智能技术,实 现工艺过程的智能监控和 优化控制。
未来市场前景与竞争格局
市场需求增长
随着环保要求的提高和燃煤发电的增加,循环流化床烟气脱硫工 艺的市场需求将持续增长。
技术竞争加剧
随着技术的进步,竞争将更加激烈,企业需要不断提升技术水平和 创新能力。
跨国合作与技术引进
通过跨国合作和技术引进,推动循环流化床烟气脱硫工艺的国际交 流与合作。
对环境的影响与可持续发展
减少污染物排放
01
循环流化床烟气脱硫工艺能够有效降低SO2等污染物的排放,
减轻对环境的压力。
资源回收与利用
02
通过脱硫副产物的资源化利用,实现资源的有效回收和循环利
用。
节能减排与低碳发展
03
循环流化床烟气脱硫工艺的发展有助于推动节能减排和低碳经
循环流化床干法脱硫培训
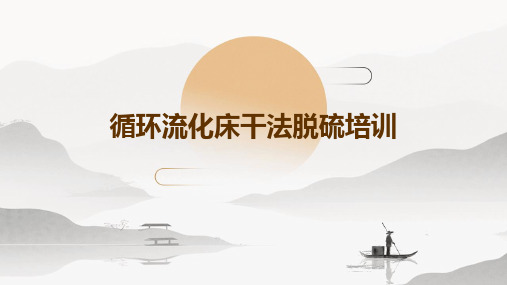
技术优势与局限性
优势
循环流化床干法脱硫技术具有高脱硫效率、低能耗、操作简单、投资成本低、 无二次污染等优点。此外,该技术适用于各种规模的燃煤电厂和工业锅炉的烟 气脱硫。
局限性
循环流化床干法脱硫技术的局限性在于对烟气流量和温度的适应性相对较小, 且对脱硫剂的粒度和活性有一定要求。同时,该技术的脱硫剂消耗量较大,需 要定期更换或补充。
选择活性高、反应性能好 的吸收剂,如石灰石、白 云石等。
吸收剂破碎与筛分
将大块吸收剂破碎成合适 的小颗粒,并通过筛分去 除杂质。
吸收剂输送
通过输送设备将破碎筛分 后的吸收剂输送到反应塔 内。
反应塔内脱硫反应
吸收剂与烟气混合
在反应塔内,吸收剂与烟 气充分混合,促进脱硫反 应的进行。
脱硫反应控制
通过控制反应温度、压力、 停留时间等参数,优化脱 硫效果。
吸收剂的粒度和化学性质对脱硫效果 有重要影响,因此需对吸收剂进行预 处理,以满足系统要求。
反应塔系统
反应塔是循环流化床干法脱硫 技术的核心设备,烟气中的二 氧化硫在反应塔内与吸收剂发 生化学反应,生成硫酸钙等物
质。
反应塔通常采用钢制结构,内 部装有布风板、防腐蚀衬里等 设施,以承受高温、高压和腐
蚀性介质的作用。
03
分离出的固体物料经过返料装置返回反应塔循环使用,气体则通过输 送管道排出或进一步处理。
04
为了提高分离效率和减少磨损,分离器系统通常配备有气流控制装置 和防磨措施。
排放系统
排放系统是循环流化床干法脱硫技术的必要组成部分, 主要负责将经过处理的烟气安全地排放到大气中。
为了防止烟气中的硫酸雾和灰尘等物质对环境造成影响, 排放系统需配备除尘器和脱硫剂喷嘴等设备。
内循环流化床烟气脱硫技术研究

内循环流化床烟气脱硫技术研究一、研究背景随着我国经济的快速发展,工业生产和能源消耗也在不断增加,这导致了空气质量逐渐恶化,尤其是大气中的二氧化硫(SO浓度逐年攀升。
为了改善空气质量,减少污染物排放,我国政府对环境保护和节能减排提出了更高的要求。
因此研究和开发新的烟气脱硫技术显得尤为重要。
内循环流化床烟气脱硫技术是一种新型的环保技术,它可以将烟气中的二氧化硫有效地去除,从而达到降低污染物排放的目的。
这种技术具有操作简便、效率高、能耗低等优点,因此备受关注。
然而目前内循环流化床烟气脱硫技术在实际应用中还存在一些问题,如脱硫效率不高、设备成本较高等,这些问题亟待解决。
1. 国内外内循环流化床烟气脱硫技术的发展现状及存在的问题;内循环流化床烟气脱硫技术作为一种环保的脱硫方式,近年来在国内外得到了广泛的关注和研究。
然而尽管这项技术有很多优点,但在实际应用中仍然存在一些问题和挑战。
首先让我们来看看国内外内循环流化床烟气脱硫技术的发展现状。
在国内这项技术已经取得了一定的进展,但与国外相比还有很大的差距。
目前国内的一些大型钢铁企业已经开始采用内循环流化床烟气脱硫技术,但由于技术和资金等方面的限制,这些项目的运行效果并不理想。
而在国外内循环流化床烟气脱硫技术已经非常成熟,广泛应用于各种工业领域。
那么为什么内循环流化床烟气脱硫技术在国内还存在这么多问题呢?一方面这可能与国内的技术水平和管理水平有关,与国外相比,国内的环保意识和技术水平还有待提高。
另一方面这也可能与国内的投资环境有关,由于环保政策的限制和市场竞争的压力,很多企业可能会选择更为简单和低成本的脱硫方式。
虽然内循环流化床烟气脱硫技术在国内外都得到了广泛的关注和研究,但在实际应用中仍然存在一些问题和挑战。
我们需要进一步加强技术研发和人才培养,同时改善投资环境和管理水平,才能更好地推动内循环流化床烟气脱硫技术在我国的发展。
2. 国家环保政策和法律法规的要求话说这环保事儿,可真是让人头疼。
目前广泛使用的5种脱硫工艺技术方案简介

目前广泛使用的5种脱硫工艺技术方案简介目录目前广泛使用的5种脱硫工艺技术方案简介 (1)1、湿法烟气脱硫工艺 (1)2、半干法烟气脱硫工艺 (3)3、烟气循环流化床脱硫工艺 (4)4、干法脱硫工艺 (5)5、NID半干法烟气脱硫 (6)目前世界上燃煤电厂烟气脱硫工艺方法很多,这些方法的应用主要取决于锅炉容量和调峰要求、燃烧设备的类型、燃料的种类和含硫量的多少、脱硫率、脱硫剂的供应条件及电厂的地理条件、副产品的利用等因素。
近年来,我国电力工业部门在烟气脱硫技术引进工作方面加大了力度,对目前世界上电厂锅炉较广泛采用的脱硫工艺都有成功运行工程,主要有湿法烟气脱硫、干法烟气脱硫和半干法烟气脱硫。
现将目前应用较为广泛的几种脱硫工艺原理、特点及其应用状况简要说明如下:1、湿法烟气脱硫工艺湿法烟气脱硫包括石灰石/石灰-石膏法烟气脱硫、海水烟气脱硫和用钠基、镁基、氨作吸收剂,一般用于小型电厂和工业锅炉。
氨洗涤法可达很高的脱硫效率,副产物硫酸铵和硝酸铵是可出售的化肥。
以海水为吸收剂的工艺具有结构简单、不用投加化学品、投资小和运行费用低等特点。
而以石灰石/石灰-石膏法湿法烟气脱硫应用最广。
《石灰石/石灰-石膏法烟气脱硫工程设计规范》中关于湿法烟气脱硫工艺的选择原则为:燃用含硫量Sar≥2%煤的机组或大容量机组(200MW及以上)的电厂锅炉建设烟气脱硫装置时,宜优先采用石灰石-石膏湿法脱硫工艺,脱硫率应保证在96%以上。
湿法烟气脱硫工艺采用碱性浆液或溶液作吸收剂,其中石灰石/石灰-石膏湿法脱硫是目前世界上技术最成熟、应用最广,运行最可靠的脱硫工艺方法,石灰石经破碎磨细成粉状与水混合搅拌制成吸收剂浆液;也可以将石灰石直接湿磨成石灰石浆液。
石灰石或石灰浆液在吸收塔内,与烟气接触混合,烟气中的SO2与浆液中的碳酸钙以及鼓入的氧化空气进行化学反应,最终反应产物为石膏,经脱水装置脱水后可抛弃,也可以石膏形式回收。
由于吸收剂浆液的循环利用,脱硫吸收剂的利用率很高。
循环流化床锅炉烟气脱硫技术
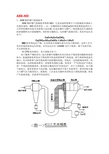
ABB-NID1、ABB锅炉烟气脱硫技术ABB锅炉烟气脱硫技术简称NID,它是由旋转喷雾半干法脱硫技术基础上发展而来的。
NID的原理是:以一定细度的石灰粉(CaO)经消化增湿处理后与大倍率的循环灰混合直接喷入反应器,在反应器中与烟气二氧化硫反应生成固态的亚硫酸钙及少量硫酸钙,再经除尘器除尘,达到烟气脱硫目的。
其化学反应式如下:CaO+H2O=Ca(OH)2Ca(OH)2+SO2=CaSO3·1/2H2O+1/2H2ONID技术将反应产物,石灰和水在容器中混合在加入吸收塔。
这种工艺只有很有限的商业运行经验,并且仅运行在100MW及以下机组,属于发展中的,不完善的技术。
和CFB技术相比,其主要缺点如下:由于黏性产物的存在,混合容器中频繁的有灰沉积由于吸收塔内颗粒的表面积小,造成脱硫效率低由于吸收塔中较高的固体和气体流速,使气体固体流速差减小,而且固体和气体在吸收塔中的滞留时间短,导致在一定的脱硫效率时,钙硫比较高,总的脱硫效果差。
需要配布袋除尘器,使其有一个”后续反应”才能达到一个稍高的脱硫效率,配电除尘器则没有”后续反应”。
对于大型机组,由于烟气量较大,通常需要多个反应器,反应器的增多不便于负荷调节,调节时除尘器入口烟气压力偏差较大。
脱硫剂、工艺水以及循环灰同时进入增湿消化器,容易产生粘接现象,负荷调节比较滞后。
Wulff-RCFBWulFF的CFB技术来源于80年代后期转到Wulff 去的鲁奇公司的雇员。
而LEE 近年来开发的新技术,Wulff公司没有,因此其技术有许多弱点:电除尘器的水平进口,直接积灰和气流与灰的分布不均。
没有要求再循环系统,对锅炉负荷的变化差,并直接导致在满负荷时烟气压头损失大。
消石灰和再循环产物的加入点靠近喷水点,使脱硫产物的黏性增加。
喷嘴上部引入再循环灰将对流化动态有负面影响,导致流化床中灰分布不均,在低负荷时,流化速度降低,循环灰容易从流化床掉入进口烟道中,严重时,大量的循环灰可将喷嘴堵塞。
循环流化床烟气脱硫工艺设计 资料

1、前言循环流化床燃烧是指炉膛内高速气流与所携带的稠密悬浮颗粒充分接触,同时大量高温颗粒从烟气中分离后重新送回炉膛的燃烧过程。
循环流化床锅炉的脱硫是一种炉内燃烧脱硫工艺,以石灰石为脱硫吸收剂,与石油焦中的硫份反应生成硫酸钙,达到脱硫的目的。
较低的炉床温度(850°C〜900°C),燃料适应性强,特别适合较高含硫燃料,脱硫率可达80%〜95%,使清洁燃烧成为可能。
2、循环流化床内燃烧过程石油焦颗粒在循环流化床的燃烧是流化床锅炉内所发生的最基本而又最为重要的过程。
当焦粒进入循环流化床后,一般会发生如下过程:①颗粒在高温床料内加热并干燥;②热解及挥发份燃烧;③颗粒膨胀及一级破碎;④焦粒燃烧伴随二级破碎和磨损。
符合一定粒径要求的焦粒在循环流化床锅炉内受流体动力作用,被存留在炉膛内重复循环的850C〜900C的高温床料强烈掺混和加热,然后发生燃烧。
受一次风的流化作用,炉内床料随之流化,并充斥于整个炉膛空间。
床料密度沿床高呈梯度分布,上部为稀相区,下部为密相区,中间为过渡区。
上部稀相区内的颗粒在炉膛出口,被烟气携带进入旋风分离器,较大颗粒的物料被分离下来,经回料腿及J阀重新回入炉膛继续循环燃烧,此谓外循环;细颗粒的物料随烟气离开旋风分离器,经尾部烟道换热吸受热量后,进入电除尘器除尘,然后排入烟囱,尘灰称为飞灰。
炉膛内中心区物料受一次风的流化携带,气固两相向上流动;密相区内的物料颗粒在气流作用下,沿炉膛四壁呈环形分布,并沿壁面向下流动,上升区与下降区之间存在着强烈的固体粒子横向迁移和波动卷吸,形成了循环率很高的内循环。
物料内、外循环系统增加了燃料颗粒在炉膛内的停留时间,使燃料可以反复燃烧,直至燃尽。
循环流化床锅炉内的物料参与了外循环和内循环两种循环运动,整个燃烧过程和脱硫过程就是在这两种形式的循环运动的动态过程中逐步完成的。
3、循环流化床内脱硫机理循环流化床锅炉脱硫是一种炉内燃烧脱硫工艺,以石灰石为脱硫吸收剂,石油焦和石灰石自锅炉燃烧室下部送入,一次风从布风板下部送入,二次风从燃烧室中部送入。
烟气循环流化床(CFBFGD)干法脱硫工艺介绍.
2.5
%
CaCO3 etc
2.3
%
Ca(OH)2
0.4
%
CaCl2·2H2O
0.3
%
CaF2
0.1
%
飞灰和中性成分
85.9
%
自由水分
0.5
%
成分为估计值,并随飞灰,SO3和CaO中的中性成分的量的变化 而变化。
谢谢观赏!
撰写:郑彬,万驰
6.09
Vol%
备注 标准、湿 标准、干
4.3 烟气中有害成分量 (相对于含氧6%,标准,干基)
SO2 SO3 HCl HF 灰分
原烟气 净化烟气 单位 效率 (-%)
2251
225
90
0
mg/m3
99
50
2.5
mg/m3
95
20
1
mg/m3
95
30000
200
mg/m3
99.9
4.4消耗量
参数
三 循环流化床脱硫技术特点及其运用范围
1) 塔内没有任何运动部件,磨损小,设备使用寿 命长维护量小。
2) 脱硫效率高、运行费用低。 3) 加入吸收塔的消石灰和水是相对独立的,没有
喷浆系统及浆液喷嘴,便于控制消石灰用量及喷 水量,容易控制操作温度。 4) 负荷适应性好。由于采用了清洁烟气再循环技 术,以及脱硫灰渣循环等措施,可以满足不同的 锅炉负荷要求。锅炉负荷在10%~110%范围内变 化,脱硫系统可正常运行。
在文丘里出口扩管段设一套喷水装置,喷入的雾化 水一是增湿颗粒表面,二是使烟温降至高于烟气露点 20℃左右,创造了良好的脱硫反应温度,吸收剂在此 与SO2充分反应.
净化后的含尘烟气从吸收塔顶部侧向排出,然后进 入脱硫除尘器(可根据需要选用布袋除尘器或电除尘 器),再通过引风机排入烟囱。由于排烟温度高于露 点温度20℃左右,因此烟气不需要再加热,同时整个 系统无须任何的防腐。
循环流化床炉内脱硫影响因数及脱硫组合工艺
表明, 增加 炉 内压力 可 以提 高脱硫效 率 , 因是压 原 力 的提高 可 以提高脱 硫反 应 速度 。 当炉 内压 力从
常压增 至 0 5MP . a时 , 脱硫 效 率 明显 提 高 , 佳脱 最 硫 窗 口温度 也 提 升 了 , 这对 脱 硫 非 常 有 利 。国 内
De u f r z to c o s a d Co b n d s lu i a i n Fa t r n m i e Pr c s e f CFB i r o e s so Bo l e
u n mi
( hn ogBa c o e l t f h aA u iu n ut , io 5 0 , hn ) S a dn rn hP w rPa i lm n m Id s y Zb 5 5 C ia noC n r 2 1
是 当加 入过 多 的脱 硫 剂 时 , 硫 效 率 增 加 得很 缓 脱
炉 内压力是 影 响脱硫 的又一 因素 。运行 结果
慢 , 仅 浪 费 了脱硫 剂 , 加 运 行成 本 , 且 多余 不 增 而
的 C O又 是 生 成 N x的催 化 剂 , N x排 放 量 a O 使 O
增加。
C C + a +C 一 1 3k / l a O— C 0 O, 8 J mo
到 40℃ 时就开 始分解 , 0 但对 不 同煤种 略有 差异 。
一
般 认为 , 机 硫 首 先 分解 为 中问 产 物 ( 有 主要 是
.
H S , 后在 遇氧 和其他 氧 化性 自由基 时逐 步 被 )而 氧化 为 S , O。 无机物 硫 ( e 在 氧 化性 气 氛 下 , 直 接 氧 FS) 可
循环流化床烟气脱硫工艺
吊顶是现代家庭装修常见的装饰手法。 吊顶既具有美化空间的作用,也是区分室 内空间一种方法。很多情况下,室内空间不能 通过墙体、隔断来划分,那样就会让空间显得 很拥挤,很局促。设计上可以通过天花与地面 来对室内空间进行区分,而天花所占的比例又 很大。吊顶材料可以分为面板和架构龙骨。吊 顶面板分为普通石膏板和防水防潮类面板。龙 骨分为金属龙骨与木龙骨。
现代房产大多是清水房,因此家庭装修的 一个很大的项目就是包门窗套、安装室内门。 中国过去的房子,大多以实用为主,随着室内 装饰的兴起,人们越来越关注房屋空间的美化 和装饰。因此,在门框的基础上,发展成为门 套,即将安装门后剩余的墙壁给包起来,一则 美观漂亮,二则起到对墙壁的保护作用。
2.对已建电厂典型的CFD-FGD工艺布置方式:
1.对新建电厂典型的CFD-FGD工艺布置方 式:
锅炉空气预热器 一级除尘 循环流化床吸收 塔 脱硫除尘器 引风机 烟囱。
一级除尘的目的是:可回收部分经济效益 高的粉煤灰‘减少脱硫灰量。效率可达 70%~90%。
• 在CFD-FGD工艺布置中。通常有以下两 种情况:
• 场地较宽裕时:一级除尘器两个进出口, 吸收塔一个进出口,二级(脱硫除尘器) 两个进出口,或引风机布置在二级除尘 器与引风机之间。
典型工艺系统流程
一个典型的循环流化床烟气脱硫系统是由预除尘 器、吸收剂制备、脱硫塔、脱硫灰再循环、注 水系统、脱硫除尘器以及仪表控制系统等组成。
影响系统脱硫效率的主要因素
• 床料循环倍率 • 流化床床料浓度(一般在5~塔操作温度
CFD-FGD工艺布置
本章小结
循环流化床法烧结烟气脱硫系统.
循环流化床法烧结烟气脱硫系统一、引言SO2主要来自能源的燃烧,燃料中的硫化铁和有机硫,在750℃温度下,90%受热分解氧化释放,同时将其中的硫分90%转化为SO2排入大气。
在我国,能源结构中煤占3/4。
我国煤产量的4/5用于直接燃烧。
根据环境年鉴资料,我国2000年SO2排放总量已达到1995万吨,为世界之冠。
SO2排放是构成我国酸雨污染的主要因素。
一般来说,在人为中排放的SO2总量中,火电厂约占一半,工业企业占1/3,其余属于交通运输工具移动源和广泛分散的商用民用炉灶。
未来10年将是我国经济持续高速发展时期,如不采取有效措施,SO2污染可能制约发展的速度。
SO2控制的办法很多,除了采用无污染或少污染的原燃料和清洁生产工艺外,还有高烟囱扩散稀释和烟气脱硫。
对于火电厂和烧结厂来说,在今后相当长的时期内,烟气脱硫仍然是首选的SO2减排技术。
目前,我国已在燃煤电厂实施烟气脱硫工程,以循环流化床为代表的半干法脱硫工艺和以石灰石/石膏法为代表的湿法脱硫工艺得到广泛应用。
国家环保局于2005年10月1日正式发布实施了《火电厂烟气脱硫工程技术规范—烟气循环流化床法》和《火电厂烟气脱硫工程技术规范—石灰石/石膏法》标准,该两种脱硫工艺技术得到国内业界一致认可。
二、烧结烟气脱硫技术和工艺推荐2.1 国内外烧结烟气脱硫现状2.1.1 国外烟气脱硫现状国外烧结烟气脱硫的总体状况和技术水平,以日本、美国和德国为代表。
由于日本环保法规严厉,烧结废气含硫较高的各类生产厂几乎都设有废气脱硫装置,因此其烧结烟气脱硫工艺的应用程度高于美国和德国。
日本烧结厂比较重视环境保护,自20世纪70年代以来,日本烧结厂对含硫高的废气采用了各种脱硫装置,有的还采用了废气脱氮装置,并采取了回收利用除尘系统收集的风尘以及噪音防治等措施。
日本烧结行业环保技术有很多在世界上属于一流,在废气脱硫方面,日本在20世纪70年代就已开发了各种烧结废气脱硫技术。
- 1、下载文档前请自行甄别文档内容的完整性,平台不提供额外的编辑、内容补充、找答案等附加服务。
- 2、"仅部分预览"的文档,不可在线预览部分如存在完整性等问题,可反馈申请退款(可完整预览的文档不适用该条件!)。
- 3、如文档侵犯您的权益,请联系客服反馈,我们会尽快为您处理(人工客服工作时间:9:00-18:30)。
Ca(OH )2 SO2 CaSO3 0.5H 2O 0.5H 2O Ca(OH )2 SO3 CaSO4 0.5H 2O 0.5H 2O CaSO3 0.5H 2O 0.5O2 CaSO4 0.5H 2O
典型工艺系统流程
一个典型的循环流化床烟气脱硫系统是由预除尘 器、吸收剂制备、脱硫塔、脱硫灰再循环、注 水系统、脱硫除尘器以及仪表控制系统等组成。
循环流化床烟气脱硫工艺的优缺点
• 优点:脱硫剂反应停留时间长,对锅炉负 荷变化的适应性强。 • 缺点:只在较小规模电厂锅炉上得到应用, 尚缺乏大型化的应用业绩。
循环流化床烟气脱硫技术
• 1 从锅炉空气预热器出来的温度为120~180℃左右的烟 气,从底部通过文丘里管进入循环流化床吸收塔内。在文 丘里管出口扩管段设一套喷水装置,创造了良好的脱硫反 应温度。循环流化床烟气脱硫技术的主要化学反应原理如 下: • 2 在自然界垂直的气固两相流体系中,在循环流化床 状态(气速4~6m/s)下可获得相当于单颗粒滑落速度数十至 上百倍的气固滑落速度。由于SO2与氢氧化钙的颗粒在循 环流化床中的反应过程,是一个外扩散控制的化学反应过 程,通过气固间大的滑落速度,强化了气固间的传质、传 热速率和气固混合,从而满足了二氧化硫与氢氧化钙高效 反应的条件要求。
谢谢
影响系统脱硫效率的主要因素 • • • • • 床料循环倍率 流化床床料浓度(一般在5~10 kg/m3) 烟气停留时间 Ca/S 脱硫塔操作温度
CFD-FGD工艺布置
1.对新建电厂典型的CFD-FGD工艺布置方式: 锅炉空气预热器 一级除尘 循环流化床吸收塔 脱硫除尘器 引风机 烟囱。 一级除尘的目的是:可回收部分经济效益高 的粉煤灰‘减少脱硫灰量。效率可达 70%~90%。
ห้องสมุดไป่ตู้
• 3 吸收塔的流化床中巨大表面积的、激烈湍动的 颗粒,为注水的快速汽化和快速可控的降温提供 了根本保证,从而创造了良好的化学反应温度条 件( 露点以上20~30°C),使二氧化硫与氢氧化钙 的反应转化为瞬间完成离子型反应。 • 4 通过颗粒的激烈湍动导致颗粒之间不断的碰 撞,使脱硫剂氢氧化钙颗粒的表面得到不断的更 新,以及脱硫灰的不断再循环使用,从而大大提 高了氢氧化钙的利用率。
• 在CFD-FGD工艺布置中。通常有以下两 种情况: • 场地较宽裕时:一级除尘器两个进出口, 吸收塔一个进出口,二级(脱硫除尘器) 两个进出口,或引风机布置在二级除尘 器与引风机之间。 • 场地较紧张时:吸收塔采用双进口‘或 引风机布置在除尘器的底部’或在二级 除尘器的出口烟道进行特殊布置设计。
技术特点
• • • • • • 1、脱硫效率高,达95%以上; 2、工艺简单,操作方便,系统可靠性高; 3、烟气无需再加热; 4、能同时脱除SO3,烟囱无需防腐; 5、脱硫副产物为干态,无废水产生; 6、占地面积小、投资省、维护费用低。
学习目的
• 1.了解硫循环及硫排放、燃烧前燃料脱硫、 硫化床燃烧脱硫 • 2.理解和掌握高浓度二氧化硫尾气脱硫、低 浓度二氧化硫烟气脱硫 • 3.掌握石灰/石灰石烟气脱硫的原理及影响 因素 • 4.理解同时脱硫脱氮工艺 • 5.了解烟气脱硫现状
循环流化床烟气脱硫工艺
• PPT制作:沈俊 赖政源 • 查找资料:周俊贤 郭志安 陈耀明 赖胜健 • 演讲:张晓峰
循环流化床烟气脱硫工艺流程图
循环流化床烟气脱硫工艺 循环流化床烟气脱硫工艺(CFB—FGD)是一 种半干法烟气脱硫技术。
脱硫原理: 循环流化床主要根据循环流化床的工作原 理,使吸收剂烟气在循环流化床内实现二 氧化硫与氢氧化钙反应的一种脱硫方法。 主要化学反应方程式如下:
在循环流化床内,SO2与Ca(OH)2的 反应生成副产物CaSO3· 1/2H2O,同时还 与SO3、HF和HCl反应生成相应的副产物 CaSO4· 1/2H2O、CaF2、CaCl2等。主要 化学反应方程式如下:
• • • • • • •
Ca(OH)2+ SO2=CaSO3· H2O +1/2 H2O 1/2 Ca(OH)2+ SO3=CaSO4· H2O +1/2 H2O 1/2 CaSO3· H2O+ 1/2O2=CaSO4· H2O 1/2 1/2 Ca(OH)2+ CO2=CaCO3 + H2O Ca(OH)2+ 2HCl=CaCl2· 2H2O 2Ca(OH)2+ 2HCl=CaCl2· Ca(OH)2· 2H2O Ca(OH)2+ 2HF=CaF2 + 2H2O