Nonlinear dynamics of elastic rods using the Cosserat theory Modelling and simulation
非牛顿流体电学:综述外文文献翻译、外文翻译、中英文翻译
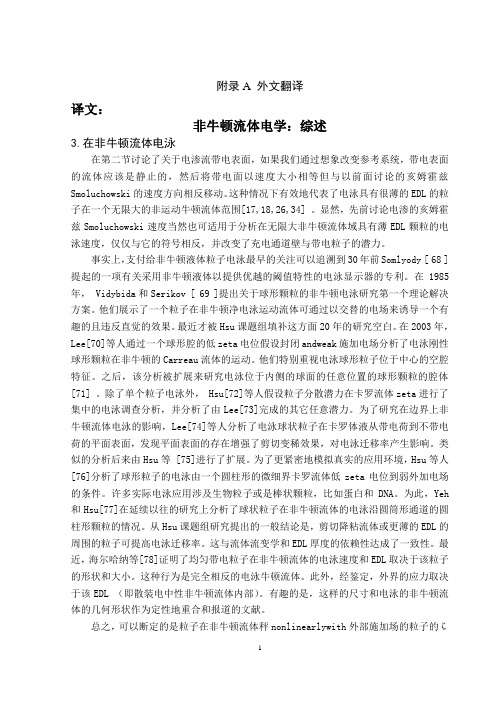
附录A 外文翻译译文:非牛顿流体电学:综述3.在非牛顿流体电泳在第二节讨论了关于电渗流带电表面,如果我们通过想象改变参考系统,带电表面的流体应该是静止的,然后将带电面以速度大小相等但与以前面讨论的亥姆霍兹Smoluchowski的速度方向相反移动。
这种情况下有效地代表了电泳具有很薄的EDL的粒子在一个无限大的非运动牛顿流体范围[17,18,26,34] 。
显然,先前讨论电渗的亥姆霍兹Smoluchowski速度当然也可适用于分析在无限大非牛顿流体域具有薄EDL颗粒的电泳速度,仅仅与它的符号相反,并改变了充电通道壁与带电粒子的潜力。
事实上,支付给非牛顿液体粒子电泳最早的关注可以追溯到30年前Somlyody [ 68 ]提起的一项有关采用非牛顿液体以提供优越的阈值特性的电泳显示器的专利。
在1985年, Vidybida和Serikov [ 69 ]提出关于球形颗粒的非牛顿电泳研究第一个理论解决方案。
他们展示了一个粒子在非牛顿净电泳运动流体可通过以交替的电场来诱导一个有趣的且违反直觉的效果。
最近才被Hsu课题组填补这方面20年的研究空白。
在2003年,Lee[70]等人通过一个球形腔的低zeta电位假设封闭andweak施加电场分析了电泳刚性球形颗粒在非牛顿的Carreau流体的运动。
他们特别重视电泳球形粒子位于中心的空腔特征。
之后,该分析被扩展来研究电泳位于内侧的球面的任意位置的球形颗粒的腔体[71] 。
除了单个粒子电泳外, Hsu[72]等人假设粒子分散潜力在卡罗流体zeta进行了集中的电泳调查分析,并分析了由Lee[73]完成的其它任意潜力。
为了研究在边界上非牛顿流体电泳的影响,Lee[74]等人分析了电泳球状粒子在卡罗体液从带电荷到不带电荷的平面表面,发现平面表面的存在增强了剪切变稀效果,对电泳迁移率产生影响。
类似的分析后来由Hsu等 [75]进行了扩展。
为了更紧密地模拟真实的应用环境,Hsu等人[76]分析了球形粒子的电泳由一个圆柱形的微细界卡罗流体低zeta电位到弱外加电场的条件。
含裂纹故障的转子轴承系统非线性动力学
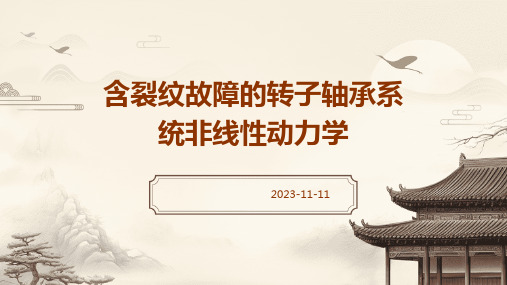
转子轴承系统动力学模型通常包括转子、轴承和支撑等部件,需要考虑各种动态效 应,如陀螺力、流体动力、摩擦力等。
含裂纹故障的转子轴承系统动力学模型需要额外考虑裂纹故障对系统动力学特性的 影响。
含裂纹故障的转子轴承系统建模
含裂纹故障的转子轴承系统建模 需要采用非线性动力学理论和方 法,建立能够准确描述系统动力
结论与展望
研究结论
转子轴承系统在运行过程中受到多种因素的影 响,如材料性能、制造工艺、运行环境等,导 致其动力学行为异常复杂。
在含裂纹故障的转子轴承系统中,裂纹的出现 会导致系统产生非线性振荡,且这种振荡具有 显著的复杂性。
通过实验和数值模拟,发现裂纹故障对转子轴 承系统的动力学行为具有显著影响,这为预测 和防止转子轴承系统的故障提供了新的视角。
1. 目前的研究主要集中在定常状态下 的动力学行为分析,而对瞬态过程的 研究较少。
3. 在研究方法上,多采用数值模拟和 实验研究,缺乏理论分析。
研究内容与方法
研究内容
1. 含裂纹故障的转子轴承系统非线性动力学模型的建立: 考虑裂纹故障的影响,建立非线性动力学模型,分析系统 的动态特性。 2. 裂纹故障的演化过程与系统响应的关系研究:通过数值 模拟和实验研究,揭示裂纹故障的演化过程与系统响应的 关系,分析裂纹故障对系统稳定性的影响。
学特性的模型。
常用的建模方法包括有限元法、 传递矩阵法和复模态法等。
含裂纹故障的转子轴承系统建模 需要考虑裂纹故障的位置、大小 和方向等因素,以及这些因素对
系统动力学特性的影响。
系统动力学特性分析
系统动力学特性分析是含裂纹故障的转 子轴承系统非线性动力学研究的重要环
涉及非体积功的热力学基本方程
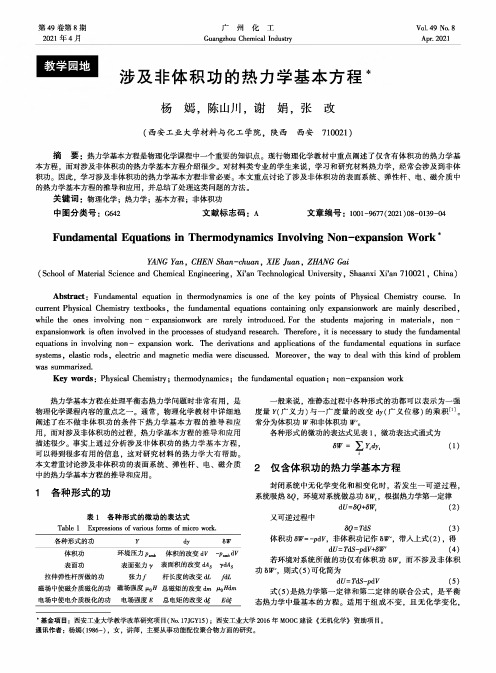
第49卷第8期2021年4月广州化工Guangzhou Chemical IndustryVol.49No.8Apr.2021涉及非体积功的热力学基本方程杨嫣,陈山川,谢娟,张改(西安工业大学材料与化工学院,陕西西安710021)摘要:热力学基本方程是物理化学课程中一个重要的知识点。
现行物理化学教材中重点阐述了仅含有体积功的热力学基本方程,而对涉及非体积功的热力学基本方程介绍很少。
对材料类专业的学生来说,学习和研究材料热力学,经常会涉及到非体积功。
因此,学习涉及非体积功的热力学基本方程非常必要。
本文重点讨论了涉及非体积功的表面系统、弹性杆、电、磁介质中的热力学基本方程的推导和应用,并总结了处理这类问题的方法。
关键词:物理化学;热力学;基本方程;非体积功中图分类号:G642文献标志码:A文章编号:1001-9677(2021)08-0139-04 Fundamental Equations in Thermodynamics Involving Non-expansion Work*YANG Yan,CHEN Shan-chuan,XIE Juan,ZHANG Gai(School of Material Science and Chemical Engineering,Xi9an Technological University,Shaanxi Xi'an710021,China) Abstract:Fundamental equation in thermodynamics is one of the key points of Physical Chemistry course・In current Physical Chemistry textbooks,the fundamental equations containing only expansionwork are mainly described, while the ones involving non-expansionwork are rarely introduced.For the students majoring in materials,non-expansionwork is often involved in the processes of studyand research.Therefore,it is necessary to study the fundamental equations in involving non-expansion work.The derivations and applications of the fundamental equations in surface systems,elastic rods,electric and magnetic media were discussed.Moreover,the way to deal with this kind of problem was summarized.Key words:Physical Chemistry;thermodynamics;the fundamental equation;non-expansion work热力学基本方程在处理平衡态热力学问题时非常有用,是物理化学课程内容的重点之一。
复合绝缘非线性电场的有限元迭代计算_张施令
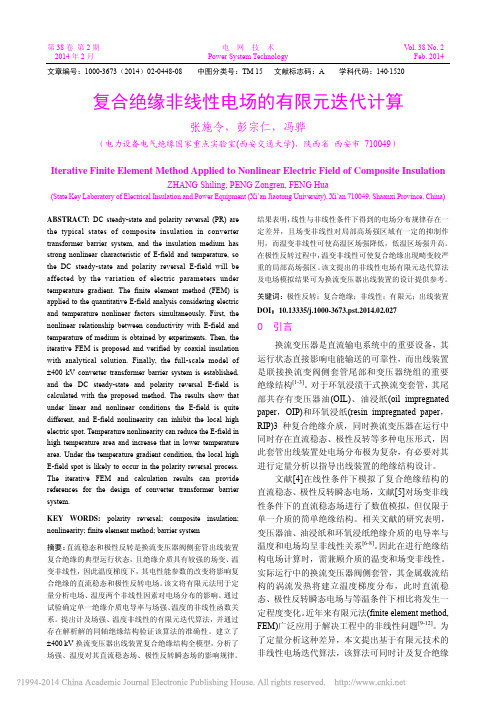
k 1 k Pk [ ( E k 1 , T k 1 ) k ]
(10)
阻尼系数 Pk 的值需用试探法选定, 一般在 0~1
(5)
之间取值。图 1 是对振荡的几何解释:曲线 1 和曲 线 2 是式(9)限定的场强、温度与电导率取值关系, 分别为某一工作场强较高、较低的有限元单元。曲 线 3 表征介质电导率的场变、 温变叠加非线性特性。 两种曲线的交点是该有限元单元的收敛解,图中以
max{|
k 1 k |k 1 N } 或 k 1
( E k 1 , T k 1 ) k ( E k , T k ) |k 1 N } (6) (E k ,T k ) 式中:N 为有限元单元总数; k , E k 和 T k 分别为
张施令,彭宗仁,冯骅
(电力设备电气绝缘国家重点实验室(西安交通大学),陕西省 西安市 710049)
Iterative Finite Element Method Applied to Nonlinear Electric Field of Composite Insulation
ZHANG Shiling, PENG Zongren, FENG Hua
电位是不可信的。文中采用逐次迭代的方法来解 决该问题:先对每一个有限元单元给定初始值, 由此得到场域中各点电位和场强 E,由电导率与 场强、温度的非线性关系 f ( E , T ) 获取新的值。 如此反复迭代计算,直到相邻两次求解的或值之 差小于某一给定精度为止, 其判断条件如式(6)所示:
f1 x2 f2 x2 fn x2
... ... ...
f1 xn f2 xn fn xn
n 阶方阵,函数 f 为有限元单元局部 区域内电导率与温度、场强的非线性关系,即 f (E ,T ) (9) 牛顿拉夫逊迭代法解非线性方程能加快迭代 收敛过程,原因在于引入“阻尼系数”Pk 可有效减 小每次迭代的增量从而防止振荡和促进收敛,每个 迭代步对单元局部电导率的修正公式为
文献翻译-非线性动力学的实验和转子轴承系统支持的行为的数值研究

附录A英文原文Experimental and Numerica Studies on Nonlinear Dynam Behavior of Rotor System Supported by Ball BearingsBall bearings are important mechanical components in high-speed turbomachinery that is liable for severe vibration and noise due to the inherent nonlinearity of ball ing experiments and the numerical approach, the nonlinear dynamic behavior of a flexible rotor supported by ball bearings is investigated in this paper. An experimental ball bearing-rotor test rig is presented in order to investigate the nonlinear dynamic performance of the rotor systems, as the speed is beyond the first synchroresonance frequency. The finite element method and two-degree-of-freedom dynamic model of a ball bearing are employed for modeling the flexible rotor s ystem. The discrete model of a shaft is built with the aid of the finite element technique, and the ball bearing model includes the nonlinear effects of the Hertzian contact force, bearing internal clearance, and so on.The nonlinear unbalance response is observed by experimental and numerical analysis.All of the predicted results are in good agreement with experimental data, thus validating the proposed model. Numerical and experimental results show that the resonance frequency is provoked when the speed is about twice the synchroresonance frequency, while the subharmonic resonance occurs due to the nonlinearity of ball bearings and causes severe vibration and strong noise. The results show that the effect of a ball bearing on the dynamic behavior is noticeable in optimum design and failure diagnosis of high-speed turbomachinery. [DOI: 10.1115/1.4000586]Keywords: ball bearing, rotor, experiment, nonlinear vibrationA.1 IntroductionBall bearings are one of the essential and important components in sophisticated turbomachinery such as rocket turbopumps, aircraft jet engines, and so on. Because of the requirement of acquiring higher performance in the design and operation of ballbearings-rotor systems, accurate predictions of vibration characteristics of the systems, especially in the high rotational speed condition, have become increasingly important.Inherent nonlinearity of ball bearings is due to Hertzian contact forces and the internal clearance between the ball and the ring.Many researchers have devoted themselves to investigating the dynamiccharacteristics associated with ball bearings. Gustafsson et al. [1] studied the vibrations due to the varying compliance of ball bearings. Saito [2] investigated the effect of radial clearance in an unbalanced Jeffcott rotor supported by ball bearings using the numerical harmonic balance technique. Aktürk et al. [2] used a three-degree-of-freedom system to explore the radial and axial vibrations of a rigid shaft supported by a pair of angular contact ball bearings. Liew et al. [4] summarized four different dynamic models of ball bearings, viz., two or five degrees of freedom, with or without ball centrifugal force, which could be applied to determine the vibration response of ball bearing-rotor systems. Bai and Xu [5] presented a general dynamic model to predict dynamic properties of rotor systems supported by ball bearings. De Mul et al. [6] presented a five-degree-of-freedom (5DOF) model for the calculation of the equilibrium and associated load distribution in ball bearings. Mevel and Guyader [7] described different routes to chaos by varying a control parameter. Jang and Jeong [8] proposed an excitation model of ball bearing waviness to investigate the bearing vibration. Then, considering the centrifugal force and gyroscopic moment of ball, they developed an analytical method to calculate the characteristics of the ball bearing under the effect of waviness in Ref. [9]. Tiwari et al. [10,11] employed a two-degree-of-freedom model to analyze the nonlinear behaviors and stability associated with the internal clearance of a ball bearing.Harsha [12-14], taking into account different sources of nonlin-earity, investigated the nonlinear dynamic behavior of ball bearing-rotor systems. Gupta et al. [15] studied the nonlinear dynamic response of an unbalanced horizontal flexible rotor supported by a ball bearing. With the aid of the Floquet theory, Bai et al. [16] investigated the effects of axial preload on nonlinear dynamic characteristics of a flexible rotor supported by angular contact ball bearings. Using the harmonic balance method, Sinou [17]performed a numerical analysis to investigate the nonlinear unbalance response of a flexible rotor supported by ball bearings.In the abovementioned studies, main attention has been paid to the ball bearing modeling and the dynamic properties analysis according to simple bearing-rotor models. With theoretical analysis and experiment, Yamamoto et al. [18] studied a nonlinear forced oscillation at a major critical speed in a rotating shaft,which was supported by ball bearings with angular clearances.Ishida and Yamamoto [19] studied the forced oscillations of a rotating shaft with nonlinear spring characteristics and internal damping. They found that a self-excited oscillation appears in the wide range above the major critical speed. A dynamic model was derived, and experiments are carried out with a laboratory test rig for studying the misaligned effect of misaligned rotor-ball bearing systems in Ref. [20]. Tiwari et al. [21] presented an experimental analysis to study the effect of radial internal clearance of a ball bearing on the bearingstiffness of a rigid horizontal rotor. These experimental results validated theoretical results reported in their literatures [10,11]. Recently, Ishida et al. [22] investigated theoretically and experimentally the nonlinear forced vibrations and parametrically excited vibrations of an asymmetrical shaft supported by ball bearings. Mevel and Guyader [23] used an experimental test bench to confirm the predicted routes to chaos in their previous paper [7]. It is noticeable of lack of experiments on nonlinear dynamic behavior of flexible rotor systems supported by ball bearings. In Ref. [24], the finite element method was used to model a LH2 turbopump rotor system supported by ball bearings. Numerical results show that the subharmonic resonance, as well as synchroresonance, occurs in the start-up process. It is found that the subharmonic resonance is an important dynamic behavior and should be considered in engineering ball bearing-rotor system design. But, the experimental and numerical studies of the subharmonic resonance in ball bearing-rotor systems are very rare.With respect to the above, the present study is intended to cast light on the subharmonic resonance characteristics in ball bearing-rotor systems using experiments and numerical approach. An experiment on an offset-disk rotor supported by ball bearings is carried out, and the finite element method and two-degree-of-freedom model of a ball bearing are employed for modeling this rotor system. The predicted results are compared with the test data, and an investigation is conducted in the nonlinear dynamic behavior of the ball bearings-rotor system.2 Experimental InvestigationAn experimental rig is employed for studying the nonlinear dynamic behavior of ball bearing-rotor systems, as shown in Fig.1. The horizontal shaft is supported by two ball bearings at both ends, and the diskis mounted unsymmetrically. The shaft is coupled to a motor with a flexible coupling. The motor speed is controlled with a feedback controller, which gets the signals from an eddy current probe. Four eddy current probes, whose resolution is 0.5 m, are mounted close to the disk and bearing at the right end in the horizontal and vertical directions, respectively. The displacement signals, obtained with the help of probes, are input into an oscilloscope to describe the motion orbit, and a data acquisition and processing system were used to analyze the effects of ball bearings on the nonlinear dynamic behavior. The data acquisition and processing system utilizes a full period sampling as the data acquisition method. Its sampling rate is 500 kHz maximum, and sample size is 12 bits. The system provides eight channels for vibratory response acquisition and 1 channel for rotational speed acquisition. All channels are simultaneous.The limitation with the presented experimental setup is that the maximum attainable speed is 12,000 rpm. The first critical speed of the rotor system falls in the speed span, as the shaft is flexible and its fist synchroresonance frequency is near 66 Hz (3960rpm).Thus, the dynamic behavior can be studied as the speed is beyond twice the synchroresonance frequency.3 Rotor Dynamic ModelThe bearing-rotor system combines an offset-disk and two ball bearings, which support the rotor at both ends. The sketch map of the system is described in Fig. 2, where the frame oxyz is the inertial frame. The corresponding experiment assembly is shown in Fig. 3.3.1 Equations of Motion . Define ux and uy as the transverse deflections along the ox and oy directions, and x θ and y θ as the corresponding bending angles in the oxz and oyz planes, respectively. When x u 1, y u 1,x 1θ , and y 1θ denote the displacements of the ball bearing center location at the left end, the complex variables 1u and 1θ can be assumed asDenote the displacements of the disk center by 2u and 2θ, and the displacements of the ball bearing center location at the right end by 3u and 3θ. Using the finite element method, the equations of motion for the rotor system can be written as [25,26]where []M , []C , []K , and []G are the mass, damping, stiffness, and gyroscopic matrix of the rotor system, respectively, ω is the rotational speed, and {}u is the displacement vector{}g F and {}u F are the vectors of gravity load and unbalance forces.{}bF is the vector of nonlinear forces associated with ball bearings.3.2 Ball Bearing Forces. A ball bearing is depicted in a frame of axes oxyz in Fig.4. The contact deformation for the j-th rolling element j δis given aswhere i c and o c are the internal radial clearance between the inner,outer race, and rolling elements, respectively, in the direction of contact, and ubx and uby are the relative displacements of the inner and outer race along the x and y directions, respectively. As shown in Fig. 4, the angular location of the j-th rolling element j ϕ can be obtained fromWhere N , c ω, t , and 0ϕ are the number of rolling elements, cage angular velocity, time, and initial angular location, respectively. The cage angular velocity can be expressed as [27]where b D and p D are the ball diameter and bearing pitch diam- eter,respectively. α is the contact angle, which is concerned with the clearance and can be obtained as follows:Referring to Fig. 4, i r and o r are the inner and outer groove radius,respectively.If the contact deformation j δ is positive, the contact force could be calculated using the Hertzian contact theory; otherwise, no load is transmitted. The contact force j Q between the j-th ball and race can be expressed as follows:where b k is the contact stiffness that can be given bywhere bi k and bo k are the load-deflection constants between the inner and outer ball race, respectively[28]. Summing the contact forces for each rolling element, the total bearing reaction fb in a complex form is4 Experimental and Numerical AnalysisAs shown in Fig. 2, the experimental assembly and the finite element model used in the dynamic analysis represent the ball bearing-rotor system with the following geometrical properties:length between the disk center and left end bearing center mm L 1201=; length between the disk center and right end bearing center mm L 1202=; and the shaft diameter mm D 10=. In addition, the elastic shaft material is steel of density 37950m kg =ρ,Young’s modulus GPa E 211=, and Poisson’s ratio 3.0=v . The ball bearings at both ends are the same model, 7200AC, and its parameters are listed in Table 1.The unbalance load is acted wit h the aid of the mass fixed on the disk. By virtue of this act, the mass eccentricity of the disk can be definitely ascertained. As the mass eccentricity of the disk is 0.032 mm, the vibratory response at different rotational speed is determined via a numerical integration and Newton –Raphson iterations of the nonlinear differential equation (2). Note that the clearances used to simulate the bearings are measured ones. The horizontal and vertical displacements signals near the disk are acquired at different times, along with the increased rotational speed. Thus, the amplitudes of vibration at different speeds are determined according to the test data, and overall amplitudes are illustrated in Fig. 5, as the rotor system is run from 2000=ω rpm to 10,000 rpm. The prediction results compared with experimental data are shown in Fig. 5. It can be found that all of the predicted results are in good agreement with experimental data, thus validating the proposed model. The first predicted resonance peak—the so called forward critical speed in linear theory,located at3960=ω rpm, matches the experimental date near 3960=ω rpm quite well. Moreover, the other amplitude peak appearing in the rotational speedrange7700=ω rpm to 8100 rpm can be found in both experimental and numerical analysis results.The corresponding frequency value of this peak is just the frequency doubling of the system critical speed.The Floquet theory can be used for analyzing the stability and topological properties of the periodic solution of the ball bearingrotor system. If the gained Floquet multipliers are less than unity,the periodic solution of the system is stable. If at least one Floquet multiplier exists with the absolute value higher than unity, the periodic solution is unstable and the topological properties of response alter into nonperiodic motion [29]. The leading Floquet multipliers and its absolute value at 7600=ω rpm, 8029 rpm, and 8200 rpm are shown in Table 2. It is found that the leading Floquet multiplier of the system remains in the unit circle, which indicates a synchronous response, as the rotational speed is less than 7700 rpm. Stability analysis shows that the imaginary part of the two leading Floquet multipliers move in opposite directions along the real axis near 7700=ω rpm. When the speed exceeded 7700=ω rpm, the leading Floquet multiplier crosses the unit circle through -1, as shown in Table 2. The periodic solution loses stability and undergoes a period-doubling bifurcation to a period-2 response, which indicates that a subharmonicresonance occurs. The subharmonic resonance keeps on from 7700=ω rpm to 8100 rpm. At 8100=ω rpm, the leading Floquet multiplier moves inside the unit circle through -1. Imply that the subharmonic resonance vanishes and the synchronous response returns. The synchronous response then continues to exist forspeeds above 8100=ω rpm.The waterfall map of frequency spectrums comparisons for prediction and experiment results are illustrated in Fig. 6. It can be found that agreement between the prediction and the experimental data is remarkable. The frequency component 66.9 Hz, near the forward resonance frequency, emerges and its amplitude rises significant when the rotational speed is near 8029 rpm. It is shown that the resonance frequency is provoked when the speed is about twice the critical speed of the ball bearing-rotor system, and the subharmonic resonance occurs. The experimental and numerical analysis indicate that the representative nonlinear behavior and the subharmonic resonance arise from the nonlinearity of ball bearings, Hertzian contact forces, and internal clearance.The orbit and frequency spectrum at 8029=ω rpm are plotted in Fig. 7. Not only the prediction orbit but also the experiment results imply that the response is a period-2 motion, which is illustrated in Fig. 7(a). The predicted frequency components, consisting of 8.133=ω Hz (8029 rpm) and 9.662=ω Hz (4014rpm), coincide with experimental data. It indicates that the periodic response loses stability through a period-doubling bifurcation to a period-2 response. Thus, the subharmonic resonance occurs due to the effects of ball bearings. It can cause severe vibration and strong noise. Moreover, the subharmonic resonance could couple with other destabilizing effects on engineering rotor systems such as Alford forces, internal damping, and so on, and induce the rotor to lose stability and damage.5 ConclusionsAn experimental rig is employed to investigate the nonlinear dynamic behavior of ball bearing-rotor systems. The corresponding dynamic model is established wi th the finite element method and 2DOF dynamic model of a ball bearing, which includes the nonlinear effects of the Hertzian contact force and bearing internal clearance. All of the predicted results are in good agreement with experimental data, thus validating the proposed model. Numerical and experimental results show that the resonance frequency is provoked, and the subharmonic resonance occurs due to the nonlinearity of ball bearings when the speed is about twice the synchroresonance frequency. The subharmonic resonance cannot only cause severe vibration and strong noise, but also induce the rotor to lose stability and damage, once coupled with other destabilizing effects on high-speed turbomachinery such as Alford forces, internal damping, and so on. It is found that the effect of the Hertzian contact forces could also induce a subharmonic resonance, even if the internal clearance was not present. But, the response amplitude and subharmonic component of the rotor system without internal clearance are less than that with both Hertzian contact forces and internal clearance. Otherwise, the clearance may be unavoidable under high-speed operations, where the bearings are axially preloaded since the effect of unbalanced load is significant at high speed. Thus, the nonlinearity of ball bearings,Hertzian contact forces, and internal clearance should be taken into account in ball bearing-rotor system design and failure diagnosis.AcknowledgmentThe authors would like to acknowledgment the support of the National Natural Science Foundation of China (Grant No.10902080) and Natural Science Foundation of Shaanxi Province(Grant Nos. SJ08A19 and 2009JQ1008).References[1] Gutafsson, O., and Tallian, T., 1963, “Resear ch Report on Study of the Vibration Characteristics of Bearings,” SKF Ind. Inc. Technical Report No.AL631023.[2] Saito, S., 1985, “Calculation of Non-Linear Unbalance Response of Horizontal Jeffcott Rotors Supported by Ball Bearings With Radial Clearances,” ASME J.Vib., Acou st., Stress, Reliab. Des., 107(4), pp. 416–420.[3] Aktürk, N., Uneeb, M., and Gohar, R., 1997, “The Effects of Number of Balls and Preload on Vibrations Associated With Ball Bearings,” ASME J. Tribol.,119, pp. 747–753.[4] Liew, A., Feng, N., and Hahn, E., 2002, “Transient Rotordynamic Modeling of Rolling Element Bearing Systems,” ASME J. Eng. Gas Turbines Power,124(4), pp. 984–991.[5] Bai, C. Q., and Xu, Q. Y., 2006, “Dynamic Model of Ball Bearing With Internal Clearance and Waviness,” J. Sound Vib., 294(1-2), pp. 23–48.[6] De Mul, J. M., Vree, J. M., and Maas, D. A., 1989, “Equilibrium and Associated Load Distribution in Ball and Roller Bearings Loaded in Five Degrees of Freedom While Neglecting Friction—Part I: General Theory and Application to Ball Be arings,” ASME J. Tribol., 111, pp. 142–148.[7] Mevel, B., and Guyader, J. L., 1993, “Routes to Chaos in Ball Bearings,” J.Sound Vib., 162, pp. 471–487.[8] Jang, G. H., and Jeong, S. W., 2002, “Nonlinear Excitation Model of Ball Bearing Waviness in a Rigid Rotor Supported by Two or More Ball Bearings Considering Five Degrees of Freedom,” ASME J. Tribol., 124, pp. 82–90.[9] Jang, G. H., and Jeong, S. W., 2003, “Analysis of a Ball Bearing With Waviness Considering the Centrifugal Force and Gyroscopic Moment of the Ball,”ASME J. Tribol., 125, pp. 487–498.[10] Tiwari, M., Gupta, K., and Prakash, O., 2000, “Effect of Radial Internal Clearance of a Ball Bearing on the Dynamics of a Balanced Horizontal Rotor,” J.Sound Vib., 238(5), pp. 723–756.[11] Tiwari, M., Gupta, K., and Prakash, O., 2000, “Dynamic Response of an Unbalanced Rotor Supported on Ball Bearings,” J. Sound Vib., 238(5), pp.757–779.[12] Harsha, S. P., 2005, “Non-Linear Dynamic Response of a Balanced Rotor Supported on Rolling Element Bearings,” Me ch. Syst. Signal Process., 19(3),pp. 551–578.[13] Harsha, S. P., 2006, “Rolling Bearing Vibrations—The Effects of Surface Waviness and Radial Internal Clearance,” Int. J. Computational Methods in Eng Sci. and Mech., 7(2), pp. 91–111.[14] Harsha, S. P., 2006, “Nonlinear Dynamic Analysis of a High-Speed Rotor Supported by Rolling Element Bearings,” J. Sound Vib., 290(1–2), pp. 65–100.[15] Gupta, T. C., Gupta, K., and Sehqal, D. K., 2008, “Nonlinear Vibration Analysis of an Unbalanced Flexible Rotor Supported by Ball Bearings With Radial Internal Clearance,” Proceedings of the ASME Turbo Expo, Vol. 5, pp. 1289–1298.[16] Bai, C. Q., Zhang, H. Y., and Xu, Q. Y., 2008, “Effects of Axial Preload of Ball Bearing on theNonlinear Dynamic Characteristics of a Rotor-Bearing System,” Nonlinear Dyn., 53(3), pp. 173–190. [17] Sinou, J. J., 2009, “Non-Linear Dynamics and Contacts of an Unbalanced Flexible Rotor Supported on Ball Bearings,” Mech. Mach. Theory, 44(9), pp.1713–1732.[18] Yamamoto, T., Ishida, Y., and Ikeda, T., 1984, “Vibrations of a Rotating Shaft With Rotating Nonlinear Restoring Forces at the Major Critical Speed,” Bull.JSME, 27(230), pp. 1728–1736.[19] Ishida, Y., and Yamamoto, T., 1993, “Forced Oscillations of a Rotating Shaft With Nonlinear Spring Characteristics and Internal Damping (1/2 Order Subharmonic Oscillations and Entrainment),” Nonlinear Dyn., 4(5), pp. 413–431.[20] Lee, Y. S., and Lee, C. W., 1999, “Modeling and Vibration Analysis of Misaligned Rotor-Ball Bearing Systems,” J. Sound Vib., 224(1), pp. 17–32.[21] Tiwari, M., Gupta, K., and Prakash, O., 2002, “Experimental Study of a Rotor Supported by Deep Groove Ball Bearing,” Int. J. Rotating Mach., 8(4), pp.243–258.[22] Ishida, Y., Liu, J., Inoue, T., and Suzuki, A., 2008, “Vibrations of an Asymmetrical Shaft With Gravity and Nonlinear Spring Characteristics (IsolatedResonances and Internal Resonances),” ASME J. Vib. Acoust., 130(4),p.041004.[23] Mevel, B., and Guyader, J. L., 2008, “Experiments on Routes to Chaos in Ball Bearings,” J. S ound Vib., 318, pp. 549–564.[24] Bai, C. Q., Xu, Q. Y., and Zhang, X. L., 2006, “Dynamic Properties Analysis of Ball Bearings—Liquid Hydrogen Turbopump Used in Rocket Engine,”ACTA Aeronaut. Astronaut. Sinica, 27(2), pp. 258–261. [25] Nelson, H., 1980, “A Finite Rotating Shaft Element Using Timoshenko Beam Theory,” ASME J. Mech. Des., 102(4), pp. 793–803.[26] Zhang, W., 1999, Basis of Rotordynamic Theory, Science Press, Beijing,China, Chap. 3.[27] Harris, T. A., 1984, Rolling Bearing Analysis, 2nd ed., Wiley, New York.[28] Aktürk, N., 1993, “Dynamics of a Rigid Shaft Supported by Angular Contact Ball Bearings,” Ph.D. thesis, Imperial College of Science, Technology and Medicine, London, UK.[29] Zhou, J. Q., and Zhu, Y. Y., 1998, Nonlinear Vibrations, Xi’an Jioatong University Press, Xi’an, China.附录B英文翻译非线性动力学的实验和转子轴承系统支持的行为的数值研究深沟球轴承在高速流体机械部件承担严重的振动和噪声的固有的非线性是很重要的。
Jeffcot转子_滑动轴承系统不平衡响应的非线性仿真

振 动 与 冲 击第18卷第1期JOU RNAL O F V I BRA T I ON AND SHOCK V o l.18N o.11999 Jeffcot转子2滑动轴承系统不平衡响应的非线性仿真Ξ王德强 张直明(山东省内燃机研究所) (上海大学轴承研究室)摘 要 本文用动力仿真法考察了Jeffco t转子2椭圆轴承系统的不平衡响应。
计入了轴承油膜力的非线性。
仿真计算前,先以非定常雷诺方程和雷诺破膜条件为依据,生成了轴瓦非定常油膜力数据库。
用龙格2库塔法对运动方程作步进积分,同时反复对轴瓦力数据库进行插值以获得轴承力的瞬时值。
考察了支撑于一对椭圆轴承上的Jeffco t转子的不平衡响应。
所得的动力学行为以及转子和轴颈的涡动轨迹,均与线性动力学(以轴承的线性化动特性系数为依据)所得的结果相比较。
两者虽在很小的不平衡量下吻合良好,但凡当不平衡量不是很小时就有显著差别。
可见有必要计入油膜力的非线性,特别是当需要计算大不平衡量下的不平衡响应时。
关键词:非线性仿真,不平衡响应,转子动力学中图分类号:TH11330 前 言在工程实践中,常常用线性动力理论来计算转子2滑动轴承系统的不平衡响应,即:计算时以线性化的轴承动力特性(轴承的八个刚度和阻尼)来表达轴承油膜的动态力[1]。
但油膜力实际上是非线性的动力元素,因此这样的线性化不可避免地要导致不平衡响应计算中的误差。
本文目的在于用非线性和线性动力学两种计算来考察不平衡响应,并作比较,以明确其异同。
符 号c m in 轴承最小半径间隙(m) x j、y j 以c m in为参考的轴颈中心坐标无量纲值d轴承直径(m)x r、y r以c m in为参考的转子中心坐标无量纲值e u转子质量中心的偏心距(m)Λ润滑油的动力粘度(Pa.s)E u质量中心的相对偏心(e u c m in)F轴承的静载荷(N)f轴在自重下的静挠度(m)Ξ转子角速度Γ轴的相对挠度(f c m in)Ξk转子固有频率l轴承长度(m)8相对速度(Ξ Ξk)SO k以转子固有频率为参考的轴承7m in轴承的最小间隙化Somm erfeld数7m in=c m in rSO k=FΩ3m in d lΛΞk1 线性分析本文以Jeffco t转子2轴承系统(图1)为考察对象。
非牛顿流体电动力学外文文献翻译、中英文翻译、外文翻译
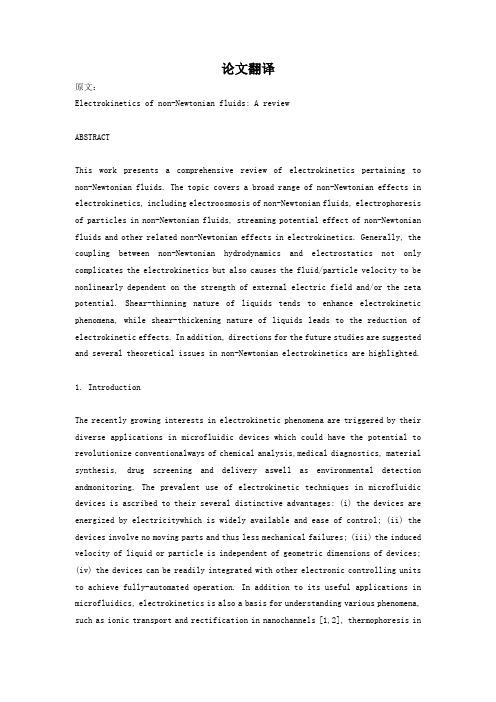
论文翻译原文:Electrokinetics of non-Newtonian fluids: A reviewABSTRACTThis work presents a comprehensive review of electrokinetics pertaining to non-Newtonian fluids. The topic covers a broad range of non-Newtonian effects in electrokinetics, including electroosmosis of non-Newtonian fluids, electrophoresis of particles in non-Newtonian fluids, streaming potential effect of non-Newtonian fluids and other related non-Newtonian effects in electrokinetics. Generally, the coupling between non-Newtonian hydrodynamics and electrostatics not only complicates the electrokinetics but also causes the fluid/particle velocity to be nonlinearly dependent on the strength of external electric field and/or the zeta potential. Shear-thinning nature of liquids tends to enhance electrokinetic phenomena, while shear-thickening nature of liquids leads to the reduction of electrokinetic effects. In addition, directions for the future studies are suggested and several theoretical issues in non-Newtonian electrokinetics are highlighted.1. IntroductionThe recently growing interests in electrokinetic phenomena are triggered by their diverse applications in microfluidic devices which could have the potential to revolutionize conventionalways of chemical analysis,medical diagnostics, material synthesis, drug screening and delivery aswell as environmental detection andmonitoring. The prevalent use of electrokinetic techniques in microfluidic devices is ascribed to their several distinctive advantages: (i) the devices are energized by electricitywhich is widely available and ease of control; (ii) the devices involve no moving parts and thus less mechanical failures; (iii) the induced velocity of liquid or particle is independent of geometric dimensions of devices; (iv) the devices can be readily integrated with other electronic controlling units to achieve fully-automated operation. In addition to its useful applications in microfluidics, electrokinetics is also a basis for understanding various phenomena, such as ionic transport and rectification in nanochannels [1,2], thermophoresis inaqueous solutions [3,4], electrowetting of electrolyte solutions [5,6] and so on. When a solid surface is brought into contact with an electrolyte solution, the solid surface obtains electrostatic charges. The presence of such surface charges causes redistribution of ions and then forms a charged diffuse layer in the electrolyte solution near the solid surface to naturalize the electric charges on solid surface. Such electrically nonneutral diffuse layer is usually dubbed electric double layer (EDL) which is responsible for two categories of electrokinetic phenomena, (i) electrically-driven electrokinetic phenomena and (ii) nonelectrically-driven electrokinetic phenomena. The basic physics behind the first category is as follows: when an external electric field is applied tangentially along the charged surface, the charged diffuse layer experiences an electrostatic body force which produces relativemotion between the charged surface and the liquid electrolyte solution. The liquid motion relative to the stationary charged surfaces is known as electroosmosis (Fig. 1a), and the motion of charged particles relative to the stationary liquid is known as electrophoresis (Fig. 1b). The classic electroosmosis occurs around solids with fixed surface charges (or, equivalently, zeta potential ζ) for given physiochemical properties of surface and solution, and then the effective liquid slip at the solid surface under the situation of thin EDLs is quantified by the well-known Helmholtz–Smoluchowski velocity, i.e., us = −εζE0/μ (ε is the electric permittivity of the electrolyte solution, ζis the zeta potential of the solid surface, E0 is the external electric field strength and μ is the dynamic viscosity of electrolyte solution). When a charged particle with a thin EDL is freely suspended in a stationary liquid electrolyte solution, electroosmotic slip motion of solution molecules on the particle surface induces the electrophoretic motion of particle with a velocity given by the Smoluchowski equation, U =εζE0/μ(Note that here ζ denotes the zeta potential of particle). One typical behavior of the second category is the generation of streaming potential effect in pressure-driven flows (Fig. 1c). There are surplus counterions in EDLs adjacent to the channel walls, and the pressuredriven flow convects these counterions downstream to gives rise to a streaming current. Simultaneously, the depletion (accumulation) of counterions in the upstream (downstream) sets up a streaming potential which drives a conduction current in opposite direction to the streaming current. At the steady state, the conduction current exactly counter-balances the streaming current, and the streaming potential built up across the channel under the limit of thin EDLs is givenby Es = Pεζ/(σ0μ) (P is externally applied pressure gradient and σ0 represents the bulk conductivity of electrolyte solution). More fundamental and comprehensive descriptions of electrokinetic phenomena are given in textbooks and reviews [7–13].Previous description of electrokinetics usually assumes Newtonian fluids with constant liquid viscosity, and most studies of electrokinetics in literature adopt such assumption. But in reality, microfluidic devices are more frequently involved in analyzing and/or processing biofluids (such as solutions of blood, saliva, protein and DNA), polymeric solutions and colloidal suspensions. These fluids cannot be treated as Newtonian fluids. Therefore, the characterization of hydrodynamics of such non-Newtonian fluids relies on the general Cauchy momentum equation in conjunction with proper constitutive equations which generally define the viscosity of liquid to vary with the rate of hydrodynamic shear, rather than the Navier–Stokes equation which is only applicable to Newtonian fluids. Since electrokinetics results from the coupling of hydrodynamics and electrostatics, it is straightforward to believe that non-Newtonian hydrodynamics would modify the conventional Newtonian electrokinetics. In this review, non-Newtonian effects on electrokinetics are comprehensively summarized and discussed. This review is organized as follows: Section 2 provides a review on the most widelystudied electroosmosis of non-Newtonian fluids. Section 3 presents a review for the electrophoresis of particles in non-Newtonian fluids, and Section 4 discusses the streaming potential effects of non-Newtonian fluids. Other non-Newtonian effects of particular interest on electrokinetics are given in Section 5. Lastly, Section 6 concludes the review and identifies the directions for the future studies.2. Electroosmosis of non-Newtonian fluidsThe pioneering contribution to this field is probably attributed to Bello et al.[14] who experimentally measured an electroosmotic flow of a polymer (methyl cellulose) solution in a capillary. Their investigation showed that the electroosmotic velocity of such polymer solution is much higher than that predicted with the classic Helmholtz–Smoluchowski velocity. It was then proposed that the shear-thinning induced by polymermolecules lowers the effective fluid viscosity inside the EDL. About a decade later, more interests were paid to such phenomenonboth experimentally and theoretically. Chang and Tsao [15] conducted an experiment similar to that of Bello et al. [14] to investigate an electroosmotic flowof the polyethylene glycol solution and observed that the drag aswell as the effective viscositywas greatly reduced due to the sheared polymericmolecules inside the EDL. On theoretical aspects, recent efforts have resulted in a great deal of information on electroosmotic flows of non-Newtonian fluids. Specifically, non-Newtonian effects are characterized by proper constitutive models which relate the dynamic viscosity and the rate of shear. There has been a large class of constitutive models available in the literature for analyzing the non-Newtonian behavior of fluids, such as power-law model, Carreau model, Bingham model, Oldroyd-B model, Moldflow second-order model and so on. Power-law fluid model is certainly the most popular because it is simple and able to fit awide range of non-Newtonian fluids. One important parameter in the power law fluid model is the fluid behavior index (n) which delineates the dependence of the dynamic viscosity on the rate of shear. If n is smaller (greater) than one, the fluids demonstrate the shear-thinning (shear-thickening) effect that the viscosity of fluid decreases with the increase (decrease) of the rate of shear. If n is equal to one, the fluids then exactly behave as Newtonian fluids. Das and Chakraborty [16] obtained the first approximate solution for electroosmotic velocity distributions of power-law fluids in a parallel-plate microchannels. However, their analysis did not clearly address the effect of non-Newtonian effects on electroosmotic flows. Zhao et al. [17,18] carried out theoretical analyses of electroosmosis of power-law fluids in a slit parallel-plate microchannel and fully discussed the non-Newtonian effects on electroosmotic flow. Their analyses revealed that the fluid rheology substantially modifies the electroosmotic velocity profiles and electroosmotic pumping performance. Particularly, they derived a generalized Helmholtz–Smoluchowski velocity for power-lower fluids in a similar fashion to the classic Newtonian Smoluchowski velocity and further elaborated the influencing factors of such velocity. Similar analyses were later extended to a cylindrical microcapillary by Zhao and Yang [19,20]. Recently, an experimental investigation was performed by Olivares et al. [21] who measured the electroosmotic flow rate of a non-Newtonian polymeric (Carboxymethyl cellulose) solution, and their experimental measurements agree well with the theoretical results predicted from the generalized Helmholtz–Smoluchowski velocity of power-law fluids. Paul [22] conceptuallydevised a series of fluidic devicesemploying electroosmosis of shear-thinning fluids. These devices included pumps, flow controllers, diaphragmvalves and displacement systemswhichwere all claimed to outperform their counterparts employing Newtonian fluids. Berli and Olivares [23] addressed the electrokinetic flow of non- Newtonian fluids in microchannels with the depletion layers near channel walls. Their analysis essentially considered a combined effect of electroosmosis and pressure-driven flow, and is greatly simplified due to the presence of depletion layers. Berli [24] evaluated the thermodynamic efficiency for electroosmotic pumping of power-law fluids in cylindrical and slit microchannels. It was revealed that both the output pressure and pumping efficiency for shear-thinning fluids could be several times higher than those for Newtonian fluids under the same experimental conditions. Utilizing the Lattice–Boltzmann method, Tang et al. [25] numerically investigated the electroosmotic flow of power-law fluids in microchannels. An electroosmotic body force was incorporated in the Bhatnagar–Gross–Krook collision approximation which simulates the Cauchy momentum equation. These studies of electroosmotic flow of non-Newtonian fluids however all assumed small surface zeta potentials which are much less than the so-call thermal voltage, i.e., kBT/(ze), where kB is the Boltzmann constant, T is the absolute temperature, e is the elementary charge, z denotes the valence of electrolyte ion. This assumption could be easily violated when large surface zeta potentials are present. Therefore, investigations of electroosmotic flow of power-law fluids over solid surfaces with arbitrary surface zeta potentials were reported in [26,27].However, the constitutive model for non-Newtonian fluids in abovementioned investigations is just an extreme case of the more general non-Newtonian Carreau fluid model. In comparison with the Newtonian fluid model, Carreau constitutive model includes five additional parameters and can describe the rheology of a wide range of non-Newtonian fluids. Under the limit of zero shear rates, the commonly used power-lawmodelwould predict an infinitely large viscosity for shear-thinning fluids, while the Carreau model does not have such defect but has smoothly transits to a constant viscosity. The Carreau fluid model can well characterize the rheology of various polymeric solutions, such as glycerol solutions of 0.3% hydroxyethyl-cellulose Natrosol HHX and 1% methylcellulose Tylose [28], and pure poly(ethylene oxide) [29]. These polymers arewidely used for improving selectivity and resolution in the capillary electrophoresis for separation of protein [30] andDNA [31]. Zimmerman et al. [32,33] performed finite element numerical simulations of the electroosmotic flow of a Carreau fluid in a microchannel T-junction. The analyses suggested that the flow field remarkably depends on the non-Newtonian characteristics of fluids, and therefore could guide the design of electroosmotic flow rheometers. Zhao and Yang [34] presented a general framework to address electroosmotic/electrophoretic mobility regarding non-Newtonian Carreau fluids. They concluded that electroosmotic/electrophoretic mobility can be significantly enhanced with shearthinning fluids and large surface zeta potentials.Due to the nonlinear dependence of the dynamic viscosity on the rate of shear, equations governing electroosmotic flows of non-Newtonian fluids also become highly nonlinear and then most of theoretical analyses rely on either approximate solutions or numerical simulations. Exact solutions are valuable because they not only can provide physical insight into the studied phenomena, but also can serves as benchmarks for experimental, numerical and asymptotic analyses. An exact solution for electroosmotic flow of non-Newtonian fluids was presented by Zhao and Yang[18]who considered electroosmosis of a power-law fluid in a slit parallel-plate microchannel as illustrated in Fig. 2. The channel is filledwith a non-Newtonian power-lawelectrolyte solution having a flowbehavior index n, anda flowconsistency indexm. The microchannel walls are uniformly charged with a zeta potential ζ. The application of an external electric field E0 drives the liquid into motion because of electroosmotic effect, and the velocity profile was derived for the situation of low zeta potentials as [18]()()()()1,,cosh s n G n H G n y u y u H κκκ-= (1)where the Debye parameter κ is defined as κ = 1/λ D = [2e2z 2n ∞/(εkBT)]1/2 (wherein e is the charge of an electron, z is the ionic valence, n ∞ is the bulk number concentration of ions, ε is the electric permittivity of the solution, kB is the Boltzmann constant, and T is the absolute temperature). The function G(υ,ϖ) in Eq. (1) is defined as()()()()1222121113,cosh ,;;cosh 222G F υυυυϖϖϖυυ---⎡⎤=⎢⎥⎣⎦(2) where 2F1[α1,α2;β1;z] denotes the Gauss' hypergeometric function [35]. us in Eq.(1) denotes the so-called Helmholtz –Smoluchowski velocity for power-law fluids and can be written as110n nn s E u n m εζκ-⎛⎫=- ⎪⎝⎭ (3) which was firstly derived by Zhao et al. [17] using an approximate method. The thickness of EDL on the channel wall is usually measured by the reciprocal of the Debye parameter (κ−1), so the nondimensional electrokinetic parameter κH = H/κ−1 characterizes the relative importance of the half channel height to the EDL thickness. Then for large values of electrokinetic parameter κH (thin EDL or large channel), the Helmholtz –Smoluchowski velocity given by Eq. (3) signifies the constant bulk velocity in microchannel flows due to electroosmosis. In electrokinetically-driven microfluidics dealing with non-Newtonian fluids, the Helmholtz –Smoluchowski velocity in Eq. (3) is of both practical and fundamental importance due to two reasons: First, the volumetric flow rate can be simply calculated by multiplying the area of channel cross-section and the Helmholtz –Smoluchowski velocity. Second, numerical computations of electroosmotic flow fields in complex microfluidic structures can be immensely simplified by prescribing the Helmholtz –Smoluchowski velocity as the slip velocity on solid walls. One can find more detailed derivation and discussion of this generalized Smoluchowski velocity in Refs. [17,18,21]. Very recently, Zhao and Yang [20] reported an interesting but counterintuitive effect that the Helmholtz –Smoluchowski velocity of non-Newtonian fluids becomes dependent on the dimension and geometry of channels owing to the complex coupling between the non-Newtonian hydrodynamics and the electrostatics.Inmicrofluidic pumping applications, the flow rate or average velocity is usually an indicator of pump performance.With the above derived electroosmotic velocity in Eq. (1), the electroosmotic average velocity along the cross-section of channel can be sought as()01Hu u y dy H =⎰ (4) where 3F2[α1,α2,α3;β1,β2;z] represents one of the generalized hypergeometric functions [35]. It needs to be pointed out that all the hypergeometric functions presented in this review can be efficiently computed in commercially-available software, such as MATLab and Mathematica.翻译:非牛顿流体电动力学:回顾摘要:本文对关于非牛顿流体电动力学进行了全面的回顾,涵盖大量非牛顿流体电动力学效应,包括非牛顿流体的电渗、非牛顿流体的电泳、流动的非牛顿流体的潜在影响以及其他电动力学中的非牛顿流体影响。
碳纳米管/尼龙6复合材料的非等温结晶动力学研究

可 以很好地描述碳纳米管/ 尼龙 6复合材料 的非等温结 晶过 程。随着降温速率 的升高 ,结 晶温度 降低 ,结 晶温 度范 围
变 大 ,结 晶 所 需 要 的 时 间 缩 短 。
关键词 :碳纳米管 ;尼龙 6 ;非等温结 晶动力学
中 图分 类 号 :T 33 6 Q 2 . 文 献 标 识 码 :A 文章 编 号 :10 5 7 (0 2 2— 0 1 0 0 5— 7 0 2 1 )0 0 7 — 4
Ab ta t f ra i rame to l - l d c r o a o tb s ( sr c :A e cd te t n n mut wal ab n n n - e MW N s ,te c aa tr ain 0 t i e u T ) h h rcei t f z 0
Ki tc f No io he m a y t lia i n f r M W CNT/PA6 Na o o po ie ne i so n-s t r lCr sa lz to o n cm st s
W ANG S a -u. Z h oy HAO Hu n mi S in a — n. HI a J ( oeeo tr l c ne& C e cl nier g i j n esyo eh o g ,Taj 02 2 hn ) Cl பைடு நூலகம் f ei i c l Ma a S e hmi g ei ,Ta i U i r t f c nl y i i 3 0 2 ,C ia aE n n nn v i T o nn
( MWN s :L M T 12 T ) - WN -0 0,直 径 范 围 1 ~2 m, 0 0n
第4 0卷第 2期
21 0 2年 2月
- 1、下载文档前请自行甄别文档内容的完整性,平台不提供额外的编辑、内容补充、找答案等附加服务。
- 2、"仅部分预览"的文档,不可在线预览部分如存在完整性等问题,可反馈申请退款(可完整预览的文档不适用该条件!)。
- 3、如文档侵犯您的权益,请联系客服反馈,我们会尽快为您处理(人工客服工作时间:9:00-18:30)。
Nonlinear dynamics of elastic rods using the Cosserattheory:Modelling and simulationD.Q.Caoa,*,1,Robin W.TuckerbaSchool of Astronautics,Harbin Institute of Technology,P.O.Box 137,Harbin 150001,ChinabDepartment of Physics,Lancaster University,Lancaster LA14YB,UKReceived 20March 2006;received in revised form 9July 2007Available online 6September 2007AbstractThe method of Cosserat dynamics is employed to explore the nonplanar nonlinear dynamics of elastic rods.The rod,which is assumed to undergo flexure about two principal axes,extension,shear and torsion,are described by a general geometrically exact theory.Based on the Cosserat theory,a set of governing partial differential equations of motion with arbitrary boundary conditions is formulated in terms of the displacements and angular variables,thus the dynamical anal-ysis of elastic rods can be carried out rather simply.The case of doubly symmetric cross-section of the rod is considered and the Kirchoffconstitutive relations are adopted to provide an adequate description of elastic properties in terms of a few elastic moduli.A cantilever is given as a simple example to demonstrate the use of the formulation developed.The nonlinear dynamic model with the corresponding boundary and initial conditions are numerically solved using the Fem-lab/Matlab software packages.The corresponding nonlinear dynamical responses of the cantilever under external har-monic excitations are presented through numerical simulations.Ó2007Elsevier Ltd.All rights reserved.Keywords:Cosserat model;Nonlinear dynamics;Slender rod;Modelling and simulation;Femlab;Matlab1.IntroductionNonlinear dynamic analysis of slender elastic structures under external forces and torques and parametric excitations remains an active area of study.Such a study can find application in accelerating missiles and space crafts,components of high-speed machinery,manipulator arm,microelectronic mechanical structures (MEMS),components of bridges (such as towers and cables)and other structural elements.Considerable attention has been devoted to the study of nonlinear dynamics of rods or beams subject to both external and parametric excitations (see,for example,Nayfeh and D.T.Mook,1979;Saito and Koizumi,1982;Kar and Dwivedy,1999and the references cited therein).While attention so far has mainly been devoted to the0020-7683/$-see front matter Ó2007Elsevier Ltd.All rights reserved.doi:10.1016/j.ijsolstr.2007.08.016*Corresponding author.Tel.:+86(0)45186414479;fax:+86(0)45186402822.E-mail addresses:dqcao@ (D.Q.Cao),r.tucker@ (R.W.Tucker).1On leave from the Department of Physics,Lancaster University,Lancaster LA14YB,UK.Available online at International Journal of Solids and Structures 45(2008)460–477/locate/ijsolstrD.Q.Cao,R.W.Tucker/International Journal of Solids and Structures45(2008)460–477461 study of planar,nonlinear dynamic analysis of beams,research has been done concerning nonplanar,nonlin-ear motions of beams.Bolotin(1964)addressed such motions in beams,but restricted himself to consideration of nonlinear inertia terms and stability of the planar response.Crespo da Silva and Glynn(1978a)formulated the equations of motion describing the nonplanar,nonlinear dynamics of an inextensional beam.The nonpla-nar,nonlinear forced oscillations of a cantilever are then analyzed in Crespo da Silva and Glynn(1978b)using the perturbation method.Cartmell(1990)and Forehand and Cartmell(2001)derived the nonlinear equation of motion for the in-plane and out-of-plane forced vibration of cantilever beams with a lumped mass.The studies mentioned above are restricted to systems with no extension of the beam’s neutral axis and no warping or shear deformation.Crespo da Silva(1988a,b)investigated the problem of nonlinear dynamics of the nonplanarflexural-torsional-extensional beams,but the effects of rotary inertia and shear deformation were neglected.Thus,cross-sectional dimensions of the beam were assumed to be small enough in comparison to the beam length.However,the shear deformation may be of considerable importance and can not be neg-ligible for studying the vibration of high frequencies when a comparative short rod is investigated.In such a case,the effect of shear deformation should be taken into account for.For the planar problem,although such effects can be included by using the Timoshenko beam theory,most of the studies are limited to the determi-nation of natural frequencies and eigenfunctions(Huang,1961;Bishop and Price,1977;Grant,1978;Bruch and Mitchell,1987).For the three-dimensional problem,we refer to Simo and Vu-Quoc(1988,1991)for a geometrically exact rod model incorporating shear and torsion-warping deformation.Further studies on the dynamic formulation of sandwich beams have been presented in Vu-Quoc and Deng(1995)and Vu-Quoc and Ebcioglu(1995)based on the geometrically-exact description of the kinematics of deformation.Moreover, Esmailzadeh and Jalili(1998)investigated the parametric response of cantilever Timoshenko beams with lumped mass,but restricted themselves to consideration of nonlinear inertia terms.Based on the geometri-cally-exact model of sliding beams,parametric resonance has been presented in Vu-Quoc and Li(1995),where the beams can undergo large deformation with shear deformation accounted for.In the case involving the full dynamic response,the strong nonlinearity and fully coupling introduce a chal-lenge for solving the partial differential equations of motion of rods.We refer to Rubin(2001)for a formu-lation of a numerical solution procedure for three-dimensional dynamic analysis of rods by modelling the rod as a set of connected Cosserat points,also Rubin and Tufekci(2005)and Rubin(2000)for three-dimensional dynamics of a circular arch and shells using the theory of a Cosserat point,respectively.A Galerkin projection has been applied to discretize the governing partial differential equations of sliding beams in Vu-Quoc and Li (1995)and sandwich beams in Vu-Quoc and Deng(1997).Recently,a new modelling strategy has been pro-posed in Cao et al.(2006)to discretize the rod and to derive the ordinary differential equations of motion with third order nonlinear generic nodal displacements.This modelling strategy has been successfully used to inves-tigate the nonlinear dynamics of typical MEMS device that comprises a resonator mass supported by four flexible beams(Cao et al.,2005).In this paper we explore the nonplanar,nonlinear dynamics of an extensional shearable rod by using the simple Cosserat model.The method of Cosserat dynamics for elastic structures is employed since it can accommodate to a good approximation the nonlinear behavior of complex elastic structures composed of materials with different constitutive properties,variable geometry and damping characteristics(Antman, 1991;Antman et al.,1998;Tucker and Wang,1999;Cull et al.,2000;Gratus and Tucker,2003).With arbitrary boundary conditions,the Cosserat theory is used to formulate a set of governing partial differential equations of motion in terms of the displacements and angular variables,describing the nonplanar,nonlinear dynamics of an extensional rod.Bending about two principal axes,extension,shear and torsion are considered,and care is taken into account for all the nonlinear terms in the resulting equations.As an example,a simple cantilever is given to demonstrate the use of the formulation developed.The nonlinear dynamic model with the corre-sponding boundary and initial conditions are numerically solved using the commercially available software packages Femlab and Matlab.Corresponding nonlinear dynamical responses of the cantilever under external harmonic excitations are presented and discussed through numerical simulations.The following conventions and nomenclature will be used through out this paper.Vectors,which are ele-ments of Euclidean3-space R3,are denoted by lowercase,bold-face symbols,e.g.,u,v;vector-valued functions are denoted by lowercase,italic,bold-face symbols,e.g.,u,v;tensors are denoted by upper-case,bold-face symbols,e.g.,I,J;matrices are denoted by upper-case,italic,bold-face symbols,e.g.,M,K.The symbolso t and o s denote differentiation with respect to time t and arc-length parameter s ,respectively.The symbols ð:Þand (0)denote differentiation with respect to dimensionless time parameter s and dimensionless length param-eter r ,respectively.2.Background on the simple Cosserat modelIn this section the basic concepts of the Cosserat theory for an elastic rod of unstressed length ‘are sum-marized.The three vectors {e 1,e 2,e 3}are assumed to form a fixed right-handed orthogonal basis.Elements of the rod are labelled in terms of the Lagrangian coordinate 06s 6‘at time t .The motion of an elastic segment may be described in terms of the motion in space of a vector r that locates the line of centroids (shown dash-dotted)of the cross-sections as shown in Fig.1.Specifying a unit vector d 3(which may be identified with the normal to the cross-section)at each point along this line enables the state of shear to be related to the angle between this vector and the tangent o s r to the centroid space-curve.Specifying a second vector d 2orthogonal to the first vector (thereby placing it in the plane of the cross-section)can be used to encode the state of bend-ing and twist along the element.In such a way,the current orientation of each cross-section at s 2[0,‘]is defined by specifying the orientation of a moving basis d 1,d 2,d 3=d 1·d 2,see Simo and Vu-Quoc (1988)and Vu-Quoc and Deng (1995)for details.Elastic deformations about the line of centroids are then coded into the rates of change of r and the triad d 1,d 2,d 3of the cross-section at s .Thus a time dependent field of two mutually orthogonal unit vectors along the segment provides three continuous dynamical degrees of freedom that,together with the three continuous degrees of freedom describing the centroid space-curve relative to some arbitrary origin in space (with fixed inertial frame e 1,e 2,e 3),define a simple Cosserat rod model.Sup-plemented with appropriate constitutive relations and boundary conditions such a model can fully accommo-date the modes of vibration that are traditionally associated with the motion of slender rods in the engineering literature:namely axial motion along its length,torsional or rotational motion and transverse or lateral motion.The tangent to the space-curve,v =v (s ,t ),is given byv ðs ;t Þ¼o s r ðs ;t Þ;ð1Þthe rotation of the directions along the space curve and the local angular velocity vector of the director triad are measured by u =u (s ,t ),w =w (s ,t )according too s d i ðs ;t Þ¼u ðs ;t ÞÂd i ðs ;t Þ;o t d i ðs ;t Þ¼w ðs ;t ÞÂd i ðs ;t Þ;ð2Þrespectively.It follows from the first equation of (2)that462 D.Q.Cao,R.W.Tucker /International Journal of Solids and Structures 45(2008)460–477X 3i ¼1ðd i Âo s d i Þ¼X 3i ¼1ðd i Âðu Âd i ÞÞ¼X 3i ¼1ðu ðd i Ád i ÞÀd i ðd i Áu ÞÞ¼2u :ð3ÞSimilarly,we haveX 3i ¼1ðd i Âo t d i Þ¼X 3i ¼1ðd i Âðw Âd i ÞÞ¼X 3i ¼1ðw ðd i Ád i ÞÀd i ðd i Áw ÞÞ¼2w :ð4ÞSince the basis {d 1,d 2,d 3}is natural for the intrinsic description of deformation,we decompose relevant vectorvalued functions with respect to it:v ðs ;t Þ¼P 3i ¼1v i ðs ;t Þd i ðs ;t Þ;u ðs ;t Þ¼P3i ¼1u i ðs ;t Þd i ðs ;t Þ;w ðs ;t Þ¼P 3i ¼1w i ðs ;t Þd i ðs ;t Þ:8>>>>>>>><>>>>>>>>:ð5ÞThe contact forces n (s ,t )and contact torques m (s ,t )are related to the extension and shear strains v (s ,t ),and flexure and torsion strains u (s ,t )by constitutive relations,respectively.The angular momentum h (s ,t )is related to the rotary inertia and the director angular velocity w (s ,t ).The dynamical evolution of the rod with density,q (s ),and cross-section area,A (s )is governed by the New-ton’s dynamical laws:q ðs ÞA ðs Þo tt r ¼o s n ðs ;t Þþf ðs ;t Þ;o t h ðs ;t Þ¼o s m ðs ;t Þþv ðs ;t ÞÂn ðs ;t Þþl ðs ;t Þ;ð6Þwhere f (s ,t )and l (s ,t )denote external force and torque densities,respectively,the contact force vector,contact torque vector,and the angular momentum vector can be written asn ðs ;t Þ¼P 3i ¼1n i ðs ;t Þd i ðs ;t Þ;m ðs ;t Þ¼P 3i ¼1m i ðs ;t Þd i ðs ;t Þ;8>>><>>>:ð7Þandh ðs ;t Þ¼X 3i ¼1h i ðs ;t Þd i ðs ;t Þ;ð8Þrespectively.For more details about Eqs.(6)–(8),we refer to the governing equations (i)–(iii)derived in termsof the noncommutative Lie group of proper orthogonal transformations in Simo and Vu-Quoc (1988),see also in Vu-Quoc and Deng (1995)and Vu-Quoc and Ebcioglu (1995).It will be assumed that the Young’s modulus E ,the shear modulus G ,and the material density q along the rod are functions of s only,and the mass center coincides with the area centroid of the cross-section at s .In this case,the simplest constitutive model for the linear elastic material is based on the Kirchhoffconstitutive relations with shear deformation,see the discus-sions in Simo and Vu-Quoc (1988,1991)for details of constitutive relations.Such a model provide an ade-quate description of elastic properties in terms of a few elastic moduli.The presence of arbitrary rotations relating the local director frame to the global inertial frame renders the equations of motion inherently non-linear.The contact forces,contact torques and the angular momentum are then given asn ¼K ðv Àd 3Þ;m ¼Ju ;h ¼Iw ;ð9Þwhere,for a symmetric cross-section of a rod,the tensors K ,J and I are described asD.Q.Cao,R.W.Tucker /International Journal of Solids and Structures 45(2008)460–477463K ðs ;t Þ¼P 3i ¼1K ii ðs ;t Þðd i ðs ;t Þ d i ðs ;t ÞÞ;J ðs ;t Þ¼P3i ¼1J ii ðs ;t Þðd i ðs ;t Þ d i ðs ;t ÞÞ;I ðs ;t Þ¼P 3i ¼1I ii ðs ;t Þðd i ðs ;t Þ d i ðs ;t ÞÞ:8>>>>>>>><>>>>>>>>:ð10ÞHere the symbol is used to denote the tensorial product u v of two vectors u and v that assigns to each vector w the vector (u v )w =(v Æw )u .The corresponding terms in (10)can be written asK 11¼K 22¼j ðs ÞG ðs ÞA ðs Þ;K 33¼E ðs ÞA ðs Þ;J 11¼R A ðs ÞE ðs Þg 2d A ;J 22¼R A ðs ÞE ðs Þn 2d A ;I 11¼R A ðs Þq ðs Þg 2d A ;I 22¼R A ðs Þq ðs Þn 2d A ;J 33¼R A ðs ÞG ðs Þn 2þg 2þn o W þg o W d A ;I 33¼R A ðs Þq ðs Þðn 2þg 2Þd A ;8>>>>>>>><>>>>>>>>:ð11Þwhere W is the warping function which is the same for all cross-sections according to the Saint-Venant Theory,and j (s )is a numerical factor depending on the shape of the cross-section at s .Making use of (5),(9)and (10),we have n ¼K 11v 1d 1þK 22v 2d 2þK 33ðv 3À1Þd 3;m ¼J 11u 1d 1þJ 22u 2d 2þJ 33u 3d 3;h ¼I 11w 1d 1þI 22w 2d 2þI 33w 3d 3:8><>:ð12ÞComparing with (7),we getn 1¼K 11v 1;m 1¼J 11u 1;h 1¼I 11w 1;n 2¼K 22v 2;m 2¼J 22u 2;h 2¼I 22w 2;n 3¼K 33ðv 3À1Þ;m 3¼J 33u 3;h 3¼I 33w 3:8><>:ð13Þ3.Specifications for the deformed configuration spaceConsider a uniform and initially straight rod of constant length ‘,supported in an arbitrary manner at each end as shown in Fig.2.It is assumed that the static equilibrium of the rod corresponds to the situation where the directions of d 3and e 3coincide,d 1and d 2are parallel to e 1and e 2,respectively.The components of the elastic displacement vector of the centroid at an arbitrary location s is assumed to be x (s ,t ),y (s ,t ),z (s ,t ),i.e.464 D.Q.Cao,R.W.Tucker /International Journal of Solids and Structures 45(2008)460–477rðs;tÞ¼xðs;tÞe1þyðs;tÞe2þðsþzðs;tÞÞe3:ð14ÞThe orientation of the directors d1,d2,d3at location s,relative to the inertial basis{e1,e2,e3},can be described by three successive rotations,called Euler angles.Alternatively,the moving frame can be described by the rotation group SO(3)as the formulations in Simo and Vu-Quoc(1988,1991),Vu-Quoc and Deng(1995) and Vu-Quoc and Ebcioglu(1995).The three successive rotations starts by rotating the basis{e1,e2,e3}an angle w(s,t)about the axis aligned with the director e2as shown in Fig.3a.Next,we rotate the basis f^e1;e2;^e3g an angle h(s,t)about the axis aligned with the new director^e1as shown in Fig.3b.Finally,we rotate the basis f^e1;^e2;d3g an angle/(s,t)about the axis aligned with the new director d3as shown in Fig.3c.The representative matrices for the three successive rotations can be written asD wðs;tÞ¼cos wðs;tÞ0Àsin wðs;tÞ010sin wðs;tÞ0cos wðs;tÞ264375;ð15ÞD hðs;tÞ¼1000cos hðs;tÞsin hðs;tÞ0Àsin hðs;tÞcos hðs;tÞ264375;ð16ÞandD/ðs;tÞ¼cos/ðs;tÞsin/ðs;tÞ0Àsin/ðs;tÞcos/ðs;tÞ0001264375;ð17Þrespectively.Denote d ij=d iÆe j.Then,using Eqs.(15)–(17),one can write the transformation matrix between the inertial basis{e1,e2,e3}and the basis{d1,d2,d3}as follows:Dðs;tÞ¼½d ijðs;tÞ ¼D/ðs;tÞD hðs;tÞD wðs;tÞ¼cos/cos wþsin/sin h sin w sin/cos hÀcos/sin wþsin/sin h cos wÀsin/cos wþcos/sin h sin w cos/cos h sin/sin wþcos/sin h cos wcos h sin wÀsin h cos h cos w264375:ð18ÞSince D is an orthogonal matrix,from the definition of d ij=d iÆe j,we haveD.Q.Cao,R.W.Tucker/International Journal of Solids and Structures45(2008)460–477465d i ¼X 3j ¼1d ije j ;e j ¼X 3k ¼1d kj d k :ð19ÞThuso s d i ¼o sX 3j ¼1d ije j!¼X 3j ¼1o s d ij e j ¼X 3j ¼1X 3k ¼1ðo s d ij Þd kj d k :ð20ÞSubstituting (20)into (3)yieldsu ¼12X 3i ¼1d i Âo s d i ¼12X3i ¼1d i ÂX 3j ¼1X 3k ¼1ðo s d ij Þd kj d k!¼12X 3j ¼1½ðo s d 1j Þd 2j Àðo s d 2j Þd 1j d 3þ12X 3j ¼1½ðo s d 2j Þd 3j Àðo s d 3j Þd 2j d 1þ12X 3j ¼1½ðo s d 3j Þd 1j Àðo s d 1j Þd 3j d 2:ð21ÞTaking notice ofX 3j ¼1d ij ðs ;t Þd kj ðs ;t Þ¼d ik ;ð22Þwhere d is the Kronecker d -function,we haveX 3j ¼1½ðo s d ij ðs ;t ÞÞd kj ðs ;t Þþd ij ðs ;t Þðo s d kj ðs ;t ÞÞ ¼0:ð23ÞHence,(21)can be written asu ¼X 3j ¼1½ðo s d 2j Þd 3j d 1þðo s d 3j Þd 1j d 2þðo s d 1j Þd 2j d 3 :ð24ÞTherefore,from (18)and (24)we can obtain u 1¼o s h cos /þo s w cos h sin /;u 2¼Ào s h sin /þo s w cos h cos /;u 3¼o s /Ào s w sin h :8><>:ð25ÞSimilarly,replacing the time derivative by the space derivative,we can easily obtainw 1¼o t h cos /þo t w cos h sin /;w 2¼Ào t h sin /þo t w cos h cos /;w 3¼o t /Ào t w sin h :8><>:ð26ÞIn order to express the extension and shear strains as functions of displacements x (s ,t ),y (s ,t ),z (s ,t )and angles h (s ,t ),w (s ,t ),/(s ,t ),we definer e 1ðs ;t Þ¼x ðs ;t Þ;r e 2ðs ;t Þ¼y ðs ;t Þ;r e 3ðs ;t Þ¼s þz ðs ;t Þ:ð27ÞThen,the strain vector v (s ,t )can be written asv ¼o s r ¼X 3i ¼1ðo s r ei Þe i ¼X3i ¼1ðo s r e i Þd ji d j :ð28ÞSubstituting (18)and (27)into (28)yields466D.Q.Cao,R.W.Tucker /International Journal of Solids and Structures 45(2008)460–477v 1¼o s x ðcos /cos w þsin /sin h sin w Þþo s y sin /cos h þð1þo s z ÞðÀcos /sin w þsin /sin h cos w Þ;v 2¼o s x ðÀsin /cos w þcos /sin h sin w Þþo s y cos /cos h þð1þo s z Þðsin /sin w þcos /sin h cos w Þ;v 3¼o s x cos h sin w Ào s y sin h þð1þo s z Þcos h cos w :8>>>>>><>>>>>>:ð29Þerning equations of motionTo obtain the partial differential equations of motion in terms of the displacements x (s ,t ),y (s ,t ),z (s ,t )and angles h (s ,t ),w (s ,t ),/(s ,t ),we decompose the contact force n (s ,t )with respect to the fixed basis {e 1,e 2,e 3}asn ðs ;t Þ¼X 3i ¼1n e i ðs ;t Þe i :ð30ÞThen,making use of (9)and (19),we haven ¼X 3i ¼1n i d i ¼X 3i ¼1X 3j ¼1n i d ij e j ¼X 3i ¼1n e j e j :ð31ÞIt follows from (13)thatn e 1¼P 3i ¼1d i 1n i ¼d 11K 11v 1þd 21K 22v 2þd 31K 33ðv 3À1Þ;n e2¼P 3i ¼1d i 2n i ¼d 12K 11v 1þd 22K 22v 2þd 32K 33ðv 3À1Þ;n e 3¼P 3i ¼1d i 3n i ¼d 13K 11v 1þd 23K 22v 2þd 33K 33ðv 3À1Þ:8>>>>>>>><>>>>>>>>:ð32ÞTo proceed,using the relations between the strain vector u (s ,t )and the differentiation of the directors d 1(s ,t ),d 2(s ,t )and d 3(s ,t )with respect to s ,and the relations between the angular velocity vector w (s ,t )and the dif-ferentiation of the directors d 1(s ,t ),d 2(s ,t )and d 3(s ,t )with respect to t ,we can easily obtain the following expressions:o s m ¼X 3i ¼1o s ðm i d i Þ¼X 3i ¼1ðo s m i d i þm i u Âd i Þ¼ðo s m 1Àm 2u 3þm 3u 2Þd 1þðo s m 2Àm 3u 1þm 1u 3Þd 2þðo s m 3Àm 1u 2þm 2u 1Þd 3;ð33Þo t h ¼X 3i ¼1o t ðh i d i Þ¼X 3i ¼1ðo t h i d i þh i w Âd i Þ¼ðo t h 1Àh 2w 3þh 3w 2Þd 1þðo t h 2Àh 3w 1þh 1w 3Þd 2þðo t h 3Àh 1w 2þh 2w 1Þd 3:ð34ÞIn addition,we recordv Ân ¼X 3i ¼1v i d i !ÂX3j ¼1n j d j !¼ðv 2n 3Àv 3n 2Þd 1þðv 3n 1Àv 1n 3Þd 2þðv 1n 2Àv 2n 1Þd 3:ð35ÞD.Q.Cao,R.W.Tucker /International Journal of Solids and Structures 45(2008)460–477467Now,let us assume that the external force and torque are distributed loadings with fixed direction and pre-scribed intensity.Consequently,the external force and torque densities can be written as:f ðs ;t Þ¼f x ðs ;t Þe 1þf y ðs ;t Þe 2þf z ðs ;t Þe 3;l ðs ;t Þ¼l x ðs ;t Þe 1þl y ðs ;t Þe 2þl z ðs ;t Þe 3:ð36ÞDecomposing the torque density with respect to the moving basis {d 1,d 2,d 3},we havel ðs ;t Þ¼X 3i ¼1l i ðs ;t Þd i ðs ;t Þ;ð37Þwhere,l i (s ,t )(i =1,2,3)can be expressed by using the transformation matrix (18)and the relation (19)asl 1¼l x ðcos /cos w þsin /sin h sin w Þþl y sin /cos h þl z ðÀcos /sin w þsin /sin h cos w Þ;l 2¼l x ðÀsin /cos w þcos /sin h sin w Þþl y cos /cos h þl z ðsin /sin w þcos /sin h cos w Þ;l 3¼l x cos h sin w Àl y sin h þl z cos h cos w :8>>>>>><>>>>>>:ð38ÞSubstituting the expressions (32)–(37)into the dynamic equation (6),we can obtainq A o tt x ¼o s ðd 11K 11v 1þd 21K 22v 2þd 31K 33ðv 3À1ÞÞþf x ;q A o tt y ¼o s ðd 12K 11v 1þd 22K 22v 2þd 32K 33ðv 3À1ÞÞþf y ;q A o tt z ¼o s ðd 13K 11v 1þd 23K 22v 2þd 33K 33ðv 3À1ÞÞþf z;o t h 1Àh 2w 3þh 3w 2¼o s m 1Àm 2u 3þm 3u 2þv 2n 3Àv 3n 2þl 1;o t h 2Àh 3w 1þh 1w 3¼o s m 2Àm 3u 1þm 1u 3þv 3n 1Àv 1n 3þl 2;o t h 3Àh 1w 2þh 2w 1¼o s m 3Àm 1u 2þm 2u 1þv 1n 2Àv 2n 1þl 3;8>>>>>>>><>>>>>>>>:ð39Þwhere d ij is defined by (18),n i ,m i and h i are given by (13),while u i ,w i ,v i and l i are given by (25),(26),(29)and (38),respectively.The boundary conditions at the ends of the rod should be determined in each particular case.For example,at a fixed end the deflections and the rotations are equal to zero.In this case the boundary conditions arex ¼y ¼z ¼0andh ¼w ¼/¼0:ð40ÞAt a free end the boundary conditions area m n þfb ðt Þ¼0anda m m þlb ðt Þ¼0;ð41Þwhere a m =+1at the right end of the rod,a m =À1at the left end,andf bðt Þ¼f b x ðt Þe 1þf b y ðt Þe 2þf b z ðt Þe 3;l b ðt Þ¼l b x ðt Þe 1þl b y ðt Þe 2þl bz ðt Þe 3(ð42Þare the external force and torque applied to the corresponding end of the rod.As the external distributed tor-que l (s ,t ),the torque vector l b (t )can be expressed in the moving frame {d 1,d 2,d 3}and the corresponding com-ponents l b i ðt Þði ¼1;2;3Þcan be determined through the relation (19)and the transformation matrix (18)asfollows:l b1¼l b x ðcos /cos w þsin /sin h sin w Þþl by sin /cos h þl b z ðÀcos /sin w þsin /sin h cos w Þ;l b 2¼l b x ðÀsin /cos w þcos /sin h sin w Þþl by cos /cos h þl b z ðsin /sin w þcos /sin h cos w Þ;l b 3¼l b xcos h sin w Àl b ysin h þl b zcos h cos w ;8>>>>>>><>>>>>>>:ð43Þ468 D.Q.Cao,R.W.Tucker /International Journal of Solids and Structures 45(2008)460–477。