塑料注射成型模具介绍
注塑模具知识概述(1)

三板模中的浇注系统:
优点﹕开模时自动断料﹐残余痕迹小 缺点﹕加工困难﹐压力损失较大,塑胶浪费大
三板模的三次分型:
第一次分型
第二次分型 第三次分型
开模状态的三板模:
第二次分型 第一次分型
一次分型
第三次分型
选择三板模的时机: A.制品必须在顶部开浇口,不能在边缘或侧面开浇口. B.为了实现充填平衡. D.自动切除浇口. 采用三板模形式的模具: 1.中心进胶的多型腔模具; 2.中心进胶的点形浇口单型腔模具; 3.表面进胶多处点形浇口模具; 4.边缘进胶的不平衡多型腔模; 5.多处边缘进胶的单型腔模具。
双射成型机的特点:
1.动模侧中心供水能随动Байду номын сангаас板旋转180度 2.一般模具水路开在机台内侧 3.两套独立作用的顶出系统
1.采用两组水平射出装置,平行配置. 2.A.B射出装置可独立或同时动作.
有兩套獨立作用的頂出系統﹐ 第一射不頂出,第二射頂出產品
双射成型视频
视频1(双击图片播放)
视频2 (双击图片播放)
三板模的优点: A﹑浇口的位置可依成品形状找到最优处 B﹑浇口可以使用针点进浇来自动切断 C﹑三板模点浇口比的边缘浇口小,这样浇口痕迹容易隐藏,同时限流作用会增大塑料的流速, 提高料温便于填充。 三板模的缺点 A﹑流道面积大﹐制品废料多 B﹑模具分模行程大﹐而且不稳定﹐需用较大的成型机 C﹑成型过程中压力损失大 D﹑模具构造复杂﹐价格高﹐容易出故障。
双射模具与普通两板模之间的区别: (1)双射模是由两套模具配合生产 (2)双射模与普通两板模所用机台不同 (3)冷却水路接法不同﹐双射模必须接内侧 (4)两套模具有分别独立的浇注系统 (5)两套模具有相同的顶出系统 (6)两套模具公模侧是相同结构
注塑模具三板模介绍

注塑模具三板模介绍注塑模具是一种用于注塑成型的工艺工具,广泛应用于塑料制品的生产中。
注塑模具三板模是其中一种常见的模具结构,由模座、模板及模腔组成。
下面将对注塑模具三板模进行详细介绍。
1.模座:模座是注塑模具的支撑结构,通常由铸铁或钢材制成。
模座上设有导柱孔和导套孔,用于安装模板和导柱导套。
2.模板:模板是模具的关键部分,承载着注塑过程中的压力和温度。
模板通常由优质的合金钢制成,具有良好的机械性能和耐热性。
模板上设置有注塑孔和冷却孔,注塑孔用于将熔融塑料注入模腔,冷却孔用于散热和控制注塑过程中的温度。
3.模腔:模腔是模具中用于成型塑料产品的空腔部分,在注塑过程中起到定型、冷却和排气的作用。
模腔的形状和尺寸决定了最终产品的外观和尺寸精度。
模腔通常由模板上的凹模和凸模组合而成,凹模和凸模之间的间隙称为缝隙,能够容纳塑料在注射过程中的膨胀。
模腔的表面通常进行表面处理,以提高产品的表面质量。
1.结构简单,易于制造和维修。
由于模座、模板和模腔之间没有复杂的配合关系,因此容易加工和装卸,维修和更换零部件也较为方便。
2.成本相对较低。
与其他结构的模具相比,三板模的制造成本相对较低,适用于注塑生产中的大批量制造。
3.适用范围广。
注塑模具三板模适用于各种塑料制品的生产,尤其是中小型注塑设备,具有较好的通用性。
4.注塑过程中的施工压力均衡。
注塑模具三板模结构相对稳定,能够均衡地承受注塑过程中的压力,减小了模具的变形和磨损,延长了模具的使用寿命。
总之,注塑模具三板模是一种常见且具有广泛应用的注塑模具结构。
它的结构简单、成本较低、适用范围广,并能保证注塑过程中的施工压力均衡,因此在塑料制品生产中得到了广泛的应用。
不过需要注意的是,在使用过程中要定期进行维护和保养,以确保模具的正常运行和延长使用寿命。
注塑模具基础知识
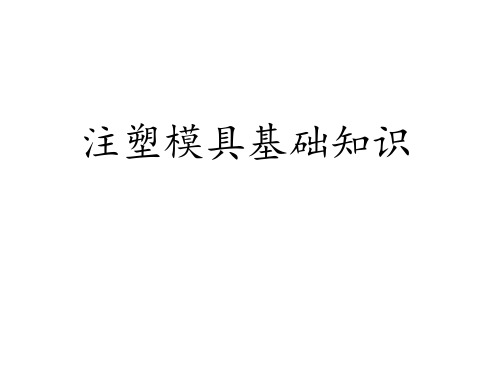
➢培训内容
一、注塑模具介绍 二、常见术语解释 三、注塑模具类型 四、注塑模具设计过程 五、注塑模具加工工艺 六、注塑模具修改方式 七、注塑模具常用钢材 八、常见注塑缺陷分析及案例
➢模具定义
模具
➢模具定义
通过一定的工艺,将特殊工业材料实现具有一 定外观,形状,尺寸,功能等要求的零件的模型 载体(工具).
整体减铁料:将模仁,入子,斜销,滑块,顶针等全 部加工去除一部分铁料。
更换零件:原来就是入子的地方,更换新的入子
➢注塑模具修改方式
主要的修模方式的应用范围: 修补焊:补焊机头能够伸进去,或者焊条能够伸进去, 不会碰到模具其他地方的地方,修补焊面积不能太大, 经常受力的地方建议不用修补焊。 线割入子:产品表面允许有分型线,模具上没有水路、 气路的地方 局部放电减铁料:几乎可以在任何情况下使用。 整体减铁料:在产品整体尺寸超差,模具表面花纹有 更改时需要整体减铁料,同时模板上需要留有减铁料 的间隙,否则模板也同样需要减铁料。
➢模具分类
1. 按成型材料来分类:金属和非金属类 金属材料模分为:
铸造模,压铸模,冲压模(折弯,冲孔,落料,拉伸, 整形,翻边等),锻造模(热锻,冷镦,滚轧,拉丝, 挤压等),粉末冶金模(等静压成型粉末冶金 、金属喷 射成型粉末冶金 、粉末锻造粉末冶金 、压力烧结粉末 冶金 )等
非金属材料模分为:塑料模具,无机非金属模具
➢开辟器
➢其它辅助系统
➢先复位机构
先复位机构:当模具 滑块下排布顶针、斜 销等机构时,为防止 合模过程中滑块和顶 针、斜销相撞,需要 先复位机构,既确保 合模的时候顶针、斜 销先回到合模位置, 然后滑块再回到合模
位置。
➢其它辅助系统
➢精定位
浅谈塑料注射成型模具的设计
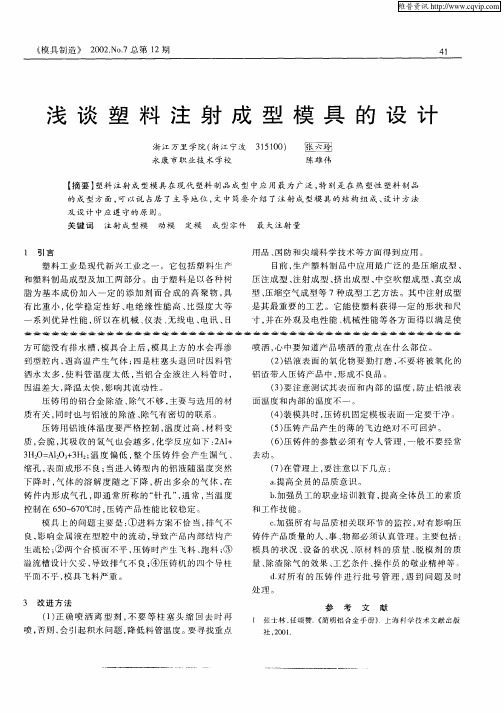
《 具 制造 》 2 0 .o7总第 1 模 0 2N . 2期
4 1
浅 谈 塑 料 注 射 成 型 模 具 的 设 计
浙 江 万里 学院 ( 江宁 波 3 5 0 ) 浙 1 10 永康 市职 业技 术 学校 陈雄 伟
【 要】 摘 塑料 注 射成 型模 具在 现 代 塑料 制 品 成 型 中应 用最 为 广 泛 , 别是 在 热 塑 性 塑料 制 品 特
一
压 注成 型 、 射成 型 、 出成 型 、 注 挤 中空 吹塑 成 型 、 空 成 真
型、 压缩 空气 成 型等 7种 成 型工艺 方 法 。其 中注 射成 型
是 其 最 重要 的工 艺 。它 能使 塑 料 获 得 一 定 的 形状 和 尺 寸, 并在 外 观及 电性 能 、 械性 能 等 各 方 面 得 以满 足 使 机
( ) 管理 上 , 7在 要注 意 以下 几 点 :
a提高 全员 的 品质 意 识 。 .
下降时 , 气体 的溶 解 度 随 之 下 降 , 出多 余 的 气 体 , 析 在 铸 件 内形 成 气 孔 , 即通 常所 称 的 “ 孔 ” 通 常 , 针 , 当温 度
控 制在 6 0 6 0C , 5 ~ 7  ̄ 时 压铸 产 品性 能 比较 稳定 。 模 具 上 的 问题 主 要是 : 进 料 方 案不 恰 当 , 气 不 ① 排
业 业 坐 业 业 业 业 坐 业 业 业 业 业 鼗 业 业
系列 优 异性 能 , 以在 机 械 、 表 、 线 电 、 讯 、 所 仪 无 电 日
业 业 业 业 业 业 业 业 业 业 业 业 业
业
方 可 能没 有排 水 槽 , 具 合 上后 , 具 上 方 的水会 再 渗 模 模 到型 腔 内 , 遇高 温 产 生气 体 ; 四是 柱塞 头 退 回时 因料 管 洒 水 太 多 , 料 管 温度 太低 , 使 当铝 合 金 液 注 入 料 管 时 , 因温差 大 , 温 太快 , 响其 流 动性 。 降 影
注射模工作原理
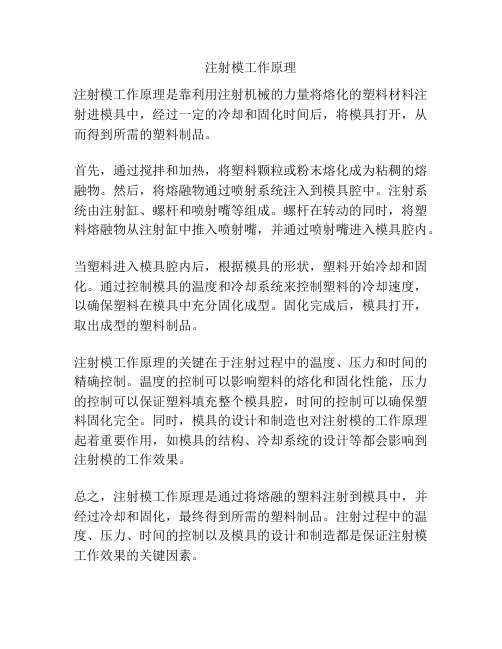
注射模工作原理
注射模工作原理是靠利用注射机械的力量将熔化的塑料材料注射进模具中,经过一定的冷却和固化时间后,将模具打开,从而得到所需的塑料制品。
首先,通过搅拌和加热,将塑料颗粒或粉末熔化成为粘稠的熔融物。
然后,将熔融物通过喷射系统注入到模具腔中。
注射系统由注射缸、螺杆和喷射嘴等组成。
螺杆在转动的同时,将塑料熔融物从注射缸中推入喷射嘴,并通过喷射嘴进入模具腔内。
当塑料进入模具腔内后,根据模具的形状,塑料开始冷却和固化。
通过控制模具的温度和冷却系统来控制塑料的冷却速度,以确保塑料在模具中充分固化成型。
固化完成后,模具打开,取出成型的塑料制品。
注射模工作原理的关键在于注射过程中的温度、压力和时间的精确控制。
温度的控制可以影响塑料的熔化和固化性能,压力的控制可以保证塑料填充整个模具腔,时间的控制可以确保塑料固化完全。
同时,模具的设计和制造也对注射模的工作原理起着重要作用,如模具的结构、冷却系统的设计等都会影响到注射模的工作效果。
总之,注射模工作原理是通过将熔融的塑料注射到模具中,并经过冷却和固化,最终得到所需的塑料制品。
注射过程中的温度、压力、时间的控制以及模具的设计和制造都是保证注射模工作效果的关键因素。
注塑模具的结构和组成
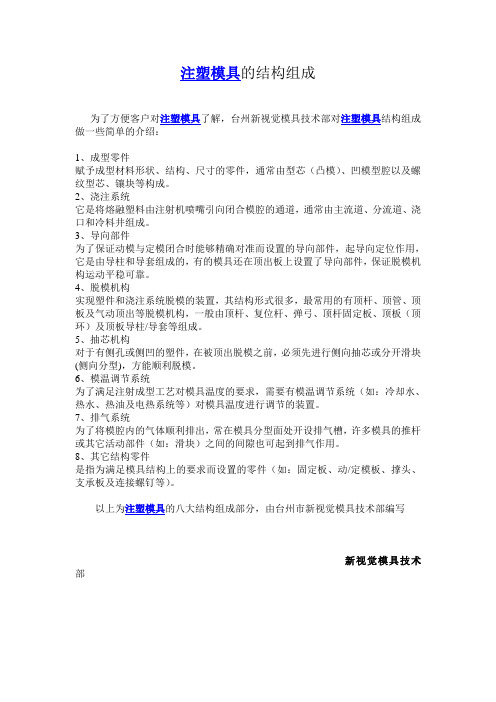
注塑模具的结构组成
为了方便客户对注塑模具了解,台州新视觉模具技术部对注塑模具结构组成做一些简单的介绍:
1、成型零件
赋予成型材料形状、结构、尺寸的零件,通常由型芯(凸模)、凹模型腔以及螺纹型芯、镶块等构成。
2、浇注系统
它是将熔融塑料由注射机喷嘴引向闭合模腔的通道,通常由主流道、分流道、浇口和冷料井组成。
3、导向部件
为了保证动模与定模闭合时能够精确对准而设置的导向部件,起导向定位作用,它是由导柱和导套组成的,有的模具还在顶出板上设置了导向部件,保证脱模机构运动平稳可靠。
4、脱模机构
实现塑件和浇注系统脱模的装置,其结构形式很多,最常用的有顶杆、顶管、顶板及气动顶出等脱模机构,一般由顶杆、复位杆、弹弓、顶杆固定板、顶板(顶环)及顶板导柱/导套等组成。
5、抽芯机构
对于有侧孔或侧凹的塑件,在被顶出脱模之前,必须先进行侧向抽芯或分开滑块(侧向分型),方能顺利脱模。
6、模温调节系统
为了满足注射成型工艺对模具温度的要求,需要有模温调节系统(如:冷却水、热水、热油及电热系统等)对模具温度进行调节的装置。
7、排气系统
为了将模腔内的气体顺利排出,常在模具分型面处开设排气槽,许多模具的推杆或其它活动部件(如:滑块)之间的间隙也可起到排气作用。
8、其它结构零件
是指为满足模具结构上的要求而设置的零件(如:固定板、动/定模板、撑头、支承板及连接螺钉等)。
以上为注塑模具的八大结构组成部分,由台州市新视觉模具技术部编写
新视觉模具技术部。
注塑模具结构基本常识
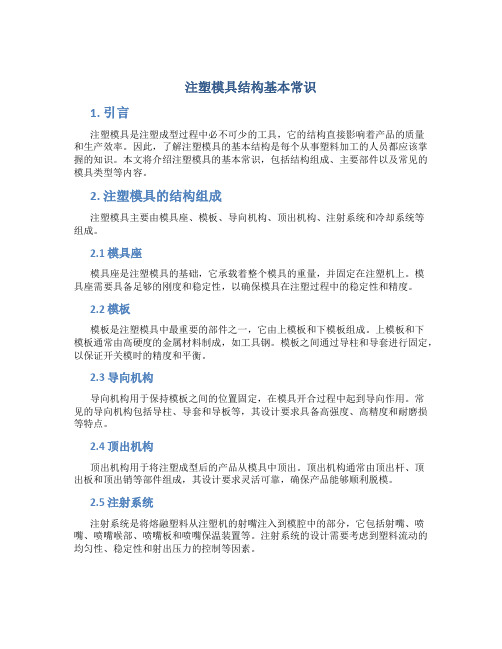
注塑模具结构基本常识1. 引言注塑模具是注塑成型过程中必不可少的工具,它的结构直接影响着产品的质量和生产效率。
因此,了解注塑模具的基本结构是每个从事塑料加工的人员都应该掌握的知识。
本文将介绍注塑模具的基本常识,包括结构组成、主要部件以及常见的模具类型等内容。
2. 注塑模具的结构组成注塑模具主要由模具座、模板、导向机构、顶出机构、注射系统和冷却系统等组成。
2.1 模具座模具座是注塑模具的基础,它承载着整个模具的重量,并固定在注塑机上。
模具座需要具备足够的刚度和稳定性,以确保模具在注塑过程中的稳定性和精度。
2.2 模板模板是注塑模具中最重要的部件之一,它由上模板和下模板组成。
上模板和下模板通常由高硬度的金属材料制成,如工具钢。
模板之间通过导柱和导套进行固定,以保证开关模时的精度和平衡。
2.3 导向机构导向机构用于保持模板之间的位置固定,在模具开合过程中起到导向作用。
常见的导向机构包括导柱、导套和导板等,其设计要求具备高强度、高精度和耐磨损等特点。
2.4 顶出机构顶出机构用于将注塑成型后的产品从模具中顶出。
顶出机构通常由顶出杆、顶出板和顶出销等部件组成,其设计要求灵活可靠,确保产品能够顺利脱模。
2.5 注射系统注射系统是将熔融塑料从注塑机的射嘴注入到模腔中的部分,它包括射嘴、喷嘴、喷嘴喉部、喷嘴板和喷嘴保温装置等。
注射系统的设计需要考虑到塑料流动的均匀性、稳定性和射出压力的控制等因素。
2.6 冷却系统冷却系统用于控制模具的温度,以保证注塑成型周期的稳定和产品的质量。
冷却系统通常由冷却水管、冷却水道和冷却水口等组件组成,其设计要求水路布置合理、冷却效果良好。
3. 常见的注塑模具类型根据注塑产品的形状和结构特点,注塑模具可以分为单面模、多面模、复合模和家用电器模等类型。
3.1 单面模单面模是指模具只有一个模腔,适用于制造单一形状的产品。
它结构简单、生产周期短,常用于生产一些简单的注塑产品。
3.2 多面模多面模是指模具具有多个模腔,可以一次性生产多个产品。
塑料注射模具零部件名称及作用

塑料注射模具零部件名称及作用一、成型零件凹模(型腔):成形塑件的表面的凹状零件。
凹模板(型腔板):板状零件,其上有面形塑件表面的凹状轮廓。
置于定模部分称作定模型腔板。
置于动模部分称作动模型腔板。
型芯:成形塑件内表面的凸状零件。
侧型芯:成形塑件侧孔,侧凹或侧凸台的零件,可手动或随滑块在模内作抽拔和复位运动的型芯。
镶件:凹模或型芯有容易损坏或难以整体加工的部位时,与主体件分开制造,并嵌入主体的局部成形零件。
活动镶件:根据工艺和结构的要求,须随塑件一起出模,才能与塑件分离的成形零件。
拼块:用以拼合成凹模或型芯的若干个分别制造的成形零件,可以分别称凹模拼块,型芯拼块。
螺纹型芯:成形塑件内螺纹的成形零件,可以是活动的螺纹型芯(取出模外)或在模内作旋转动动的螺纹型芯。
螺纹型环:成形塑件外螺纹的成形零件,可以是活动的螺纹型环(整体的或拼合)或在模内作旋转运动的螺纹型环。
二、导向零件导柱:与安装在另一半的模具上的导套(或孔)相配合,用以保证动模具开合模运动导向精度的圆柱形零件。
有带头导柱和带肩导柱两种。
推板导柱:与推板导套(或孔)呈滑配合,用于脱模机构运动导向的圆柱形两种。
导套:与安装在另一半模具上的导柱相配合,用以保证动模与定模的相对位置,保证模具开合模运动导向精度的圆套形零件。
有直导套和带头导套两种。
推扳导套:固定于推板上,与推板导柱呈滑配合,用于脱模机构运动导向的圆套形零件。
三、推出零件推杆:直接推出塑件或浇注系统凝料的杆件,有圆柱头推杆、带肩推杆和扁头推杆等。
圆柱头推杆可用来推顶推顶板,亦称预杆。
推管:直接推出塑件的管状零件。
推件板:直接推出塑件的板状零件。
推件环:局部或整体推出塑件的环状或盘形零件。
推杆固定板:固定推出和复位零件以及推板导套的板状零件。
推杆:支承推出和复位零件,直接传递机床推出力的板件。
连接推杆:连接推件板与推板固定板,传递推力的杆件。
拉料杆:设置在主流道的正对面,头部形状特殊,能够拉出主流道凝料的杆件,头部形状有Z形,球头形,倒锥形,菌形及圆锥头形等。
- 1、下载文档前请自行甄别文档内容的完整性,平台不提供额外的编辑、内容补充、找答案等附加服务。
- 2、"仅部分预览"的文档,不可在线预览部分如存在完整性等问题,可反馈申请退款(可完整预览的文档不适用该条件!)。
- 3、如文档侵犯您的权益,请联系客服反馈,我们会尽快为您处理(人工客服工作时间:9:00-18:30)。
注射机的选择和校核
3、锁模力的校核 注射或保压时,高压塑料熔体产生使模具分型面涨开的力,力的大小等于 塑件和浇注系统在分型面上的投影面积之和乘以型腔内的最大平均压力; 该涨模力应小于注射机的锁模力,从而保证分型面的锁紧,避免产生溢料。
F涨 pA F锁
式中 F涨 —— 熔体产生的使模具分型面涨开的力; F锁 —— 注射机的额定锁模力; p —— 熔融塑料在型腔内的最大平均压力,约为注射压力的1/3~2/3,
注射机的选择和校核
最大注射量的校核
v实 v实 max
式中 V实 ——实际充满模具所需塑料的量; V实max ——最大实际注射量,即注射机能往模具中注入的最大的塑料
的量,一般可取理论注射量的75%左右。
2、注射压力的校核
p额 p注
式中 P额 ——注射机的额定注射压力; P注 ——成型所需的注射压力。
浇注系统设计
一、概述
1、浇注系统的定义 从喷嘴到型腔间的塑料熔体流动通道 2、浇注系统的分类 普通浇注系统,无流道浇注系统(绝热/热) 3、普通浇注系统的组成 主流道,分流道,浇口,冷料井
二、浇注系统的设计原则
结合塑料的流变性能,浇注系统尽量让塑料熔体以尽可能低的粘度和速度 充满型腔
热量和压力在浇注系统中的损失尽量少 保压阶段浇注系统应能充分传递压力 控制浇注系统中浇口的凝固时间以控制补料时间 确保各型腔均衡进料 排气性好 浇注系统凝料尽量少,去除方便 充分考虑塑料件外观、大小、形状、技术要求和模具结构及注射机的性能
单分型面注射成型模具概述
注射模的组成
注射模均由动、定模两大部分组成。 根据模具上各部件所起的作用,可细分为以下几个部分 : (1) 成型零件 成型零件是构成模具型腔的零件。通常由型腔、凹模、镶件等组成; (2) 浇注系统 将熔融塑料由注射机喷嘴引向型腔的流道,一般由主流道、分流道、 浇口、冷料穴组成。 (3) 导向机构 常见由导柱和导套组成,用于引导动、定模正确闭合,保证动、定模 合模后的相对准确位置; (5) 脱模机构 将塑件和浇注系统凝料从模具中脱出的机构,由推杆、复位杆、推杆 固定板、推板、及推板导柱和导套等组成。 (6) 加热、冷却系统 为满足注射工艺对模具温度的要求、模具设有冷却或加热系统; 模具需冷却时,常在模内开设冷却水道;需加热时则在模内或其周围设置加热元件, 如电加热元件。 (7) 排气系统 充模过程中,为排出模腔内气体,常在分型面处开设排气槽;小型塑 件排气量不大,可直接利用分型面上的间隙排气;模具的推杆或其它活动零件之间 的间隙均可起排气作用。 (8) 其它结构零件 为满足模具结构上的要求而设置的;如固定板,动、定模座板, 支承板,连接螺钉等。
注射机的选择和校核
二、注射机基本参数的校核
1、最大注射量的校核 制品及浇注系统总质量的计算
m=nmz十mj 式中: n——型腔数
mz——一个塑件的质量 mj——浇注系统塑料质量 螺杆式注射机最大注射量 mmax=VρC 式中 : v——注射机规定注射体积,cm3 ρ——注射塑料在常温下的密度,g/cm3 C——料筒温度下塑料体积膨胀的校正系数 对结品性塑料:C=0.85 对非结晶性塑料:C=0.93
❖注射制品占模型制品三分之一 ❖注射模约占塑料成型模具的二分之一
塑料注射成型模具概述
设计注射模应考虑的问题
(1)了解塑料熔体的流动行为,考虑塑料在流道和型腔各处的流动阻 力,流动速度,校核最大流动长度及流动面积比。根据塑料的充模 顺序,考虑塑料在模具内重新熔合和模腔内气体导出的问题。 (2) 考虑冷却过程中塑料的收缩及补给问题。 (3) 通过模具设计,控制塑料在模具内结晶、取向和改善制品的内应 力。 (4) 浇口的形式、位置和分型面的选择问题。 (5) 制品的顶出及侧向分型抽芯问题。 (6) 模具的冷却或加热问题。 (7) 模具与所用注射机的关系问题。 (8) 模具总体结构要合理,模具零件要便于制造、能采用标准件。
塑料注射成型
模块二 注射成型提高 项目一 塑料垫圈注射成型 任务二 塑料垫圈模具认知
注射机的选择和校核
一、注射机的基本参数
最大注射量; 最大注射压力; 最大锁模力; 最大成型面积 模具的最大厚度或最小厚度; 最大开模行程; 注射机模板上安装模具的螺纹孔的位置和尺 寸; 顶出机械的形式、位置及顶出行程。
6、顶出装置的校核
①顶出装置的形式 中心顶杆机械顶; 两侧顶杆机械顶; 中心顶杆液压顶加两侧双顶杆机械顶; 中心顶杆液压顶与其它开模辅助液压缸联合作用
②顶出装置的校核 ► 顶出方式 ► 顶出成型模具 塑料注射成型所用的模具
❖塑料注射成型模具的适用 热塑性塑料制品的注射成型 热固性塑料制品的注射成型
S —— 模具所需的开模距离。包括型芯高度、塑料高度、浇注系统 高度及一定的余量
B 开模行程和模具厚度有关 Sk-Hm≥S Sk:注射机动定模板间最大开距 Hm:模具厚度 S:取出塑件及浇注系统料所需距离
C 开模行程校核 1)与模厚无关:Smax≥S 2)与模厚有关:Smax≥S+Hm
注射机的选择和校核
通常可取20~ 40MPa; A —— 塑件和浇注系统在分型面上的投影面积之和
注射机的选择和校核
4、注射机安装模具部分的尺寸校核 ①喷嘴尺寸和主流道衬套间配合 ②定位圈和定位孔间的配合 模具上的定位圈与定位孔应是较松间隙配合 定位圈的高度应比定位孔的深度略小 ③模具在注射机上的固定 压板加螺钉 螺栓直接连接 ④模具的厚度和外形尺寸——模厚 模具的最大厚度与最小厚度 模具最大厚度Hmax与最小厚度Hmin是指动模板闭合后,达到规定合模力时,
动模板与固定模板间的最大(小)距离。 模具厚度应在允许最大及最小模厚之间。
注射机的选择和校核
5、开模行程校核 校核目的:为了取出塑件及浇注系统凝料 注意事项:开模行程是否与模厚有关 注:肘杆式合模和模厚无关;液压式合模和模厚有关 A 开模行程和模具厚度无关
式中 Smax —— 注射机sm的ax最大开s 模行程;