CSB经典案例分析-ASCO乙炔生产装置单向阀失效导致的可燃气体爆炸事故
化工火灾爆炸事故案例分析总结
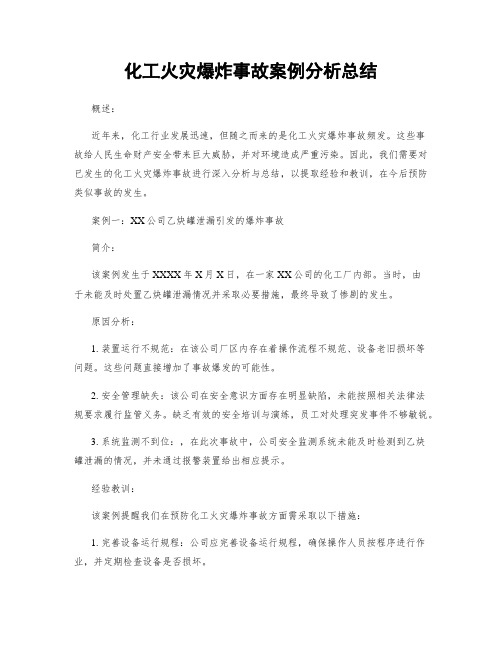
化工火灾爆炸事故案例分析总结概述:近年来,化工行业发展迅速,但随之而来的是化工火灾爆炸事故频发。
这些事故给人民生命财产安全带来巨大威胁,并对环境造成严重污染。
因此,我们需要对已发生的化工火灾爆炸事故进行深入分析与总结,以提取经验和教训,在今后预防类似事故的发生。
案例一:XX公司乙炔罐泄漏引发的爆炸事故简介:该案例发生于XXXX年X月X日,在一家XX公司的化工厂内部。
当时,由于未能及时处置乙炔罐泄漏情况并采取必要措施,最终导致了惨剧的发生。
原因分析:1. 装置运行不规范:在该公司厂区内存在着操作流程不规范、设备老旧损坏等问题。
这些问题直接增加了事故爆发的可能性。
2. 安全管理缺失:该公司在安全意识方面存在明显缺陷,未能按照相关法律法规要求履行监管义务。
缺乏有效的安全培训与演练,员工对处理突发事件不够敏锐。
3. 系统监测不到位:,在此次事故中,公司安全监测系统未能及时检测到乙炔罐泄漏的情况,并未通过报警装置给出相应提示。
经验教训:该案例提醒我们在预防化工火灾爆炸事故方面需采取以下措施:1. 完善设备运行规程:公司应完善设备运行规程,确保操作人员按程序进行作业,并定期检查设备是否损坏。
2. 加强安全意识培养:加强宣传教育,提高员工对于化工火灾爆炸事故风险的认识和防范意识。
同时组织定期培训和演练,以增强员工应对紧急情况的能力。
3. 安装先进监测系统:引进和使用先进的化学品泄漏监测系统,及时准确地获取关键指标数据,并做好预警准备。
案例二:XX市XX工厂氰化物泄露引发大规模火灾简介:该案例发生于XXXX年X月X日,位于XX市的一家化工工厂中,该工厂主要生产化学品。
当时,由于氰化物泄露溢出并遇到火源,火灾迅速蔓延且扩大,导致了严重的环境污染和人员伤亡。
原因分析:1. 安全设施缺失:该公司安全设备不齐全、维护保养不到位。
在事故发生前没有作出及时反应和应对。
2. 废水处理系统失效:该工厂废水处理设备存在严重故障,并未及时检修维护。
乙炔生产爆炸案例

乙炔生产过程中危害因素分析及安全控制江苏某医药原料有限公司是一家以生产医药中间体为主的企业,主产品1 ,4 - 丁炔二醇生产能力达3000 t/ a。
目前该公司有两台乙炔发生器,乙炔生产系统具有易燃、易爆等诸多危险、有害特性,如何实现乙炔系统的安全稳定运行,一直是该企业安全管理工作的重中之重。
1 乙炔生产事故案例分析案例1:发生器加料口燃烧某厂发生器在加料时,由于第1 贮斗排氮不彻底,电石块太大,在加料吊斗内“搭桥”。
操作人员采用吊斗撞击加料口,致使吊钩脱落。
于是现场挂吊钩,同时启动电动葫芦开关,结果引起燃烧,操作人员脸部和手部烧伤。
原因分析:乙炔气遇到电动葫芦开关火花引起燃烧。
案例2:乙炔发生器爆炸安徽某厂乙炔工段1# 发生器活门被电石桶盖卡住,操作人员进入贮斗内处理时突然发生爆炸,死亡3 人。
"原因分析:人进入发生器内处理被卡住的活门时,致使大量空气进入贮斗内,用工具敲击电石时产生火花,乙炔气与之接触后发生爆炸。
案例3:乙炔发生器发生爆喷燃烧广西某厂乙炔工段当班操作人员发现乙炔气柜高度降至180 m3 以下,按正常生产要求,此时发生器需要添加电石,于是操作人员到三楼添加电石,1 # 发生器贮斗的电石放完后,又去放2 # 发生器贮斗的电石,当放出约一半电石物料时,在下料斗的下料口与电磁振动加料器上部下料口连接橡胶圈的密封部位,突然发生爆喷燃烧。
站在电磁振动器旁的操作人员全身被喷射出来的热电石渣浆烧伤,送医院抢救无效死亡。
原因分析:操作人员在放发生器贮斗的电石时,没注意到乙炔气柜液位的变化,致使加入粉料过多,产气量瞬间过大,压力超高,气压把中间连接的胶圈冲破,大量电石渣和乙炔气喷出,并着火。
案例4 :乙炔发生器加料口爆炸湖南某厂乙炔站1 # 发生器加料口爆炸起火,随后2 # 发生器加料口和贮斗胶圈的密封处也发生爆炸起火,电石飞溅到一楼排渣池,产生乙炔气导致起火,为此发生器一、三、四楼都起火。
美国乙炔服务公司乙炔泄漏爆炸事故

下 溶 解在 丙 酮中 , 使 其保 持 稳定 , 防止 它 发 生分
解 。 副产 品 石灰 稀 浆连 续 地从 发 生 器中 排 放 到建
筑 物 外边 的 一个 凹 坑中 。 石灰 稀 浆 由泵 从 凹 坑中
抽 到 沉淀 分 离罐 中 。
1.2 生 产 装置 布 置
ASCO 生 产 装 置 位 于 连 接 新 泽 西 和 纽 约 斯 塔
编辑 王广亮
美国乙炔服务公司 乙炔泄漏爆炸事故
高 吉峰 ( 中国石油安 全技术研究所, 辽宁大连 116031)
摘 要 介 绍 了 发生 事 故 公司 的 背 景 和 工 艺 设备 概 况, 描述 了 乙炔 泄 漏积 聚 爆炸 事 故 的经 过 , 详细 地 分析 了 事故 原 因, 提 出了 应 该 吸取 的 教 训 以及 相 关的 改 进建 议 。
石 灰 部 分 沉降 下 来 , 水继 续 流 进 2# 沉 淀 分 离 罐 。
在 后 续的 罐 中进 一 步分 离 石灰 和 水 , 当 水 到 达 5#
和 6# 罐 时 , 水 中 含有 微 量的 石 灰。 沉淀 下 来的 石 灰浆 由 泵从 罐 底 抽出 , 并 且 随
时 由 承包 商 将其 运 走。积 累 在 5# 和 6# 罐内 的 水根
b) 对 员工 进 行操 作 规程 培 训, 使 其具 备 正 确 遵守 操 作规 程 的能 力 。
c) 将 连 接到 可 燃气 体 收集 设 备 的 排液 口 和 排 气口 重 新配 置 在一 个 安全 的 、位 置更 佳 的地 点 。
d) 确 保可 能 存有 乙 炔的 建 筑和 封 闭空 间 满 足 美国 消 防协 会 的要 求 。
1.3 沉 淀 分离 罐
ASCO 使 用连在一 起的 6 个上部 敞口的 沉淀 分
石化行业典型事故案例分析报告

石化行业典型事故案例分析报告石化行业是一个高危行业,由于其生产环节中存在着易燃、易爆、有毒和高温的物质,所以常常发生各种事故。
本文将以一起典型的石化行业事故为例进行分析。
1. 事故概述2018年5月,某石油化工公司的生产车间发生了一起重大事故。
事故发生在该公司的乙炔生产车间,造成了4人死亡、10人受伤。
事故原因是由于车间管理不善和操作不规范导致的。
2. 事故经过事故当天,车间内正在进行乙炔氧化反应的生产工作。
由于当时车间管理不善,一位工人在进行反应装置的检修时没有按照规定进行操作。
他在检修完毕后没有关闭相关设备,而是直接离开岗位。
由于疏忽大意,设备并未被关闭,乙炔氧化反应仍在继续进行。
之后,由于车间操作人员对设备的监控不到位,无法及时发现问题。
乙炔氧化反应持续进行,导致温度和压力升高,最终达到了危险的程度。
在温度和压力超过设定值后,反应装置发生了爆炸,导致车间内多个设备损坏,造成人员伤亡。
3. 事故原因分析a. 车间管理不善:公司在管理方面存在严重问题,对车间人员的培训和安全意识教育不到位,对设备和操作的监控不到位。
b. 操作不规范:由于工人在检修后没有按照规定关闭设备,导致乙炔氧化反应持续进行,最终引发事故。
c. 设备监控不到位:车间操作人员对设备的监控不到位,无法及时发现温度和压力升高的异常情况。
4. 事故教训和改进措施a. 加强车间管理:公司应加强对车间人员的培训和安全意识教育,提高员工的安全意识和操作规范性。
b. 建立严格的操作程序:确保每一项操作都按照规定进行,特别是在检修完成后,必须验证设备是否正常关闭。
c. 完善设备监控系统:引入先进的监控系统,对设备的温度、压力、液位等参数进行实时监测,及时发现异常情况并采取相应的措施。
d. 加强安全检查:公司应定期对设备进行安全检查和维护,确保设备的正常运行。
5. 结论本次事故的发生给石化行业敲响了警钟,也给我们带来了深刻的教训。
只有加强车间管理、规范操作、完善设备监控,才能最大程度地减少事故的发生,保障生产安全。
乙炔事故典型案例
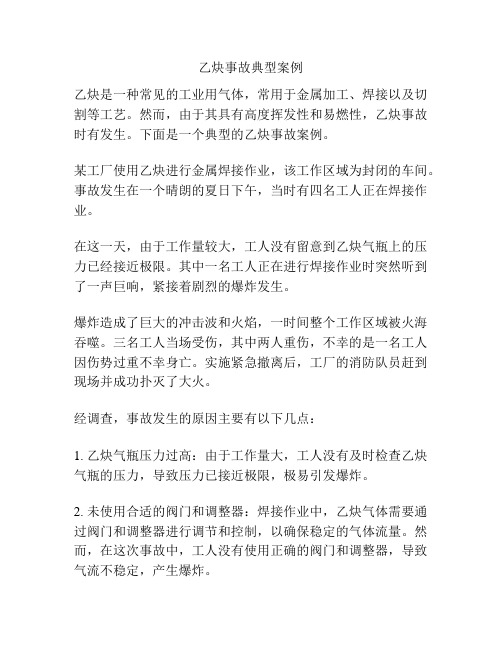
乙炔事故典型案例乙炔是一种常见的工业用气体,常用于金属加工、焊接以及切割等工艺。
然而,由于其具有高度挥发性和易燃性,乙炔事故时有发生。
下面是一个典型的乙炔事故案例。
某工厂使用乙炔进行金属焊接作业,该工作区域为封闭的车间。
事故发生在一个晴朗的夏日下午,当时有四名工人正在焊接作业。
在这一天,由于工作量较大,工人没有留意到乙炔气瓶上的压力已经接近极限。
其中一名工人正在进行焊接作业时突然听到了一声巨响,紧接着剧烈的爆炸发生。
爆炸造成了巨大的冲击波和火焰,一时间整个工作区域被火海吞噬。
三名工人当场受伤,其中两人重伤,不幸的是一名工人因伤势过重不幸身亡。
实施紧急撤离后,工厂的消防队员赶到现场并成功扑灭了大火。
经调查,事故发生的原因主要有以下几点:1. 乙炔气瓶压力过高:由于工作量大,工人没有及时检查乙炔气瓶的压力,导致压力已接近极限,极易引发爆炸。
2. 未使用合适的阀门和调整器:焊接作业中,乙炔气体需要通过阀门和调整器进行调节和控制,以确保稳定的气体流量。
然而,在这次事故中,工人没有使用正确的阀门和调整器,导致气流不稳定,产生爆炸。
3. 不当的存储和保管:乙炔气瓶存放时需要注意防止摩擦、颠簸和高温等因素,以免引发泄漏和爆炸。
然而,由于工人的疏忽,乙炔气瓶没有得到适当的保管,增加了事故发生的风险。
这起乙炔事故给工人的生命和财产安全造成了巨大损失,也给人们敲响了警钟。
在日常工作中,正确使用、存储和保管乙炔气体至关重要。
工人需要严格按照操作规程进行操作,并定期检查和维护相关设备。
此外,提高工人的安全意识和培训,加强设备的维修和检查,都是预防乙炔事故的重要措施。
总之,通过这起典型的乙炔事故案例,我们应该认识到安全意识的重要性,并在工作中严格遵循安全操作规程,保障自己和他人的生命安全。
乙炔作为一种常见的工业用气体,广泛应用于金属加工、焊接和切割等工艺。
然而,由于乙炔具有高度挥发性和易燃性,乙炔事故时有发生,给工人的生命和财产安全带来严重威胁。
案例氧气乙炔爆炸事故分析
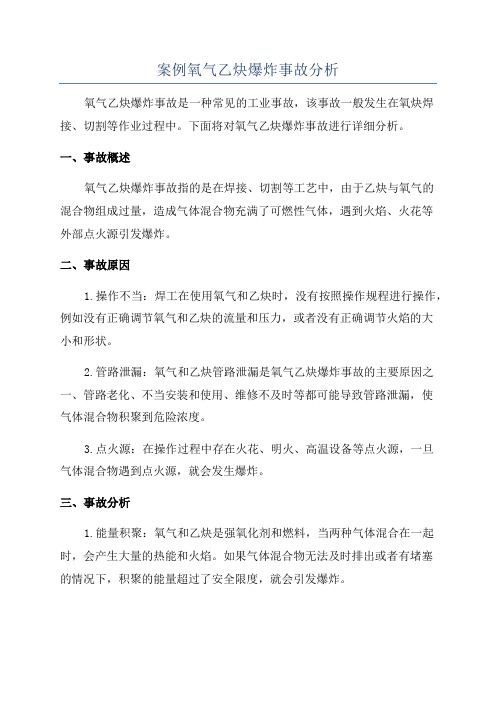
案例氧气乙炔爆炸事故分析氧气乙炔爆炸事故是一种常见的工业事故,该事故一般发生在氧炔焊接、切割等作业过程中。
下面将对氧气乙炔爆炸事故进行详细分析。
一、事故概述氧气乙炔爆炸事故指的是在焊接、切割等工艺中,由于乙炔与氧气的混合物组成过量,造成气体混合物充满了可燃性气体,遇到火焰、火花等外部点火源引发爆炸。
二、事故原因1.操作不当:焊工在使用氧气和乙炔时,没有按照操作规程进行操作,例如没有正确调节氧气和乙炔的流量和压力,或者没有正确调节火焰的大小和形状。
2.管路泄漏:氧气和乙炔管路泄漏是氧气乙炔爆炸事故的主要原因之一、管路老化、不当安装和使用、维修不及时等都可能导致管路泄漏,使气体混合物积聚到危险浓度。
3.点火源:在操作过程中存在火花、明火、高温设备等点火源,一旦气体混合物遇到点火源,就会发生爆炸。
三、事故分析1.能量积聚:氧气和乙炔是强氧化剂和燃料,当两种气体混合在一起时,会产生大量的热能和火焰。
如果气体混合物无法及时排出或者有堵塞的情况下,积聚的能量超过了安全限度,就会引发爆炸。
2.火焰传播:火焰传播是氧气乙炔爆炸事故中的关键环节,一旦火焰传播到燃烧区域,就会导致气体混合物燃烧,产生大量热量和压力,从而引发爆炸。
3.爆炸后果:氧气乙炔爆炸的后果严重,会造成人员伤亡和物质损失,同时还可能引发连锁反应,导致更大范围的爆炸事故。
四、事故防范措施1.加强操作培训和教育:对从事氧气乙炔操作的人员进行相关培训和教育,提高其安全意识和操作技能,减少人为操作错误引发事故的可能性。
2.检修管路和设备:定期对氧气和乙炔管路进行检修和维护,确保管路的完好无损,避免泄漏和积聚。
3.采取防火措施:在使用氧气和乙炔进行焊接、切割等操作时,应采取有效的防火措施,例如禁止吸烟、禁止火种等。
4.使用防爆设备:在作业现场使用防爆设备,例如防爆灯、防爆电器等,减少外部点火源对气体混合物的引发可能性。
5.建立安全管理制度:企业应建立完善的安全管理制度,明确安全责任和安全操作规程,加强对操作流程和设备使用的监管和管理,减少事故发生的概率。
乙炔事故案例分析[1]
![乙炔事故案例分析[1]](https://img.taocdn.com/s3/m/0790d72acc22bcd127ff0c1a.png)
乙炔站事故案例案例一吉林吉化电石厂乙炔泄漏导致空间爆炸,死亡2人一.事故经过和危害1988年6有29日,吉林省吉化电石厂氯乙烯车间违章检修致乙炔气泄露,发生空间爆炸,死亡2人。
6有29日。
吉化电石厂氯乙烯车间将1#乙炔泵出.入口短节拆下,因原出口阀门内漏,更换新阀后,出.入口管线分别堵加了盲板,做好了检修前的准备工作。
机械工开始检修1#乙炔泵。
7月5 日该车间检修蒸镏系统尾凝器,因乙炔系统没有安排检修项目,故只对后部蒸馏系统进行了清洗置换,而前部乙炔及转化系统采用了隔断措施停车。
机械工继续对1#乙炔泵检修。
14时6分,忽听到“轰”的一声,乙炔泵房发生爆炸。
1名工人被崩到泵房窗外18.5m远的地方,全身无一布丝,仅剩一条皮带,当即死亡;另1名工人被倒塌的墙壁压在电机室内1#电机旁,待抢救出,心脏已停止跳动。
二.事故原因分析1.在拆短节上螺丝时,1 名工人拆下盲板上的4 个螺丝,使管内乙炔气外逸。
由于出现金属碰撞火花,使达到爆炸极限的乙炔气体发生空间爆炸。
2.在没有与化工工段取得联系前,对违章拆卸盲板螺丝未能察觉和只制止。
发现有乙炔味时,虽找化工工段进行了处理,但在乙炔气继续外逸的情况下,均未采取有效措施,使乙炔气长时间外逸,达到爆炸极限。
3.泵出口阀使用前,没有进行强度试验和气密性试验,阀门的内在质量缺陷未以能及时发现。
事故后发现阀门关闭不严,有6mm月牙缝。
经解体检查阀体上的闸板导轨不起作用,阀杆与闸板脱落,位置发生变化,产生内漏。
4.在易燃易爆岗位检修未按规定使用防爆工具。
5.检修任务书填写的安全措施不全,在对蒸馏系统检修停车中,前部只采取了隔离措施,易燃易爆岗位未切断气源。
车间领导未向职工交待清楚,管理混乱。
三.同类事故防止措施强化全员安全意识,提高群体安全技术素质,牢固树立“安全第一”的思想。
1.狠抓基础工作,对各项规章制度落实情况经常进行检查。
宣贯安全管理标准,完善工作标准,加强安全管理。
化工安全生产案例
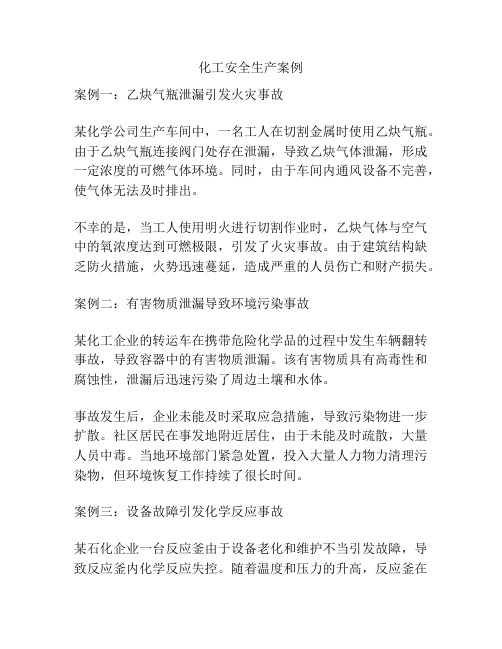
化工安全生产案例案例一:乙炔气瓶泄漏引发火灾事故某化学公司生产车间中,一名工人在切割金属时使用乙炔气瓶。
由于乙炔气瓶连接阀门处存在泄漏,导致乙炔气体泄漏,形成一定浓度的可燃气体环境。
同时,由于车间内通风设备不完善,使气体无法及时排出。
不幸的是,当工人使用明火进行切割作业时,乙炔气体与空气中的氧浓度达到可燃极限,引发了火灾事故。
由于建筑结构缺乏防火措施,火势迅速蔓延,造成严重的人员伤亡和财产损失。
案例二:有害物质泄漏导致环境污染事故某化工企业的转运车在携带危险化学品的过程中发生车辆翻转事故,导致容器中的有害物质泄漏。
该有害物质具有高毒性和腐蚀性,泄漏后迅速污染了周边土壤和水体。
事故发生后,企业未能及时采取应急措施,导致污染物进一步扩散。
社区居民在事发地附近居住,由于未能及时疏散,大量人员中毒。
当地环境部门紧急处置,投入大量人力物力清理污染物,但环境恢复工作持续了很长时间。
案例三:设备故障引发化学反应事故某石化企业一台反应釜由于设备老化和维护不当引发故障,导致反应釜内化学反应失控。
随着温度和压力的升高,反应釜在未能承受的情况下发生爆炸,造成周边设备受损。
事故发生后,企业应急响应不迅速,未能做好人员疏散和火灾扑救工作。
事故造成多名工人死亡和受伤,同时对周边环境也造成了一定的污染。
案例四:危险品储存不当引发漏气事故某化学仓库在储存危险品时未按照规定的方法和条件进行,导致某种化学品产生漏气现象。
由于仓库通风设备不足,危险气体积聚在室内,超过了可燃极限,引发了爆炸事故。
事故发生后,周边居民感受到了爆炸的冲击波和烟尘,造成恐慌情绪。
部分工人身受重伤,仓库设备也严重损坏。
事故后,企业接受了相关部门的调查,并采取了更加严格的安全措施来避免类似事故再次发生。
- 1、下载文档前请自行甄别文档内容的完整性,平台不提供额外的编辑、内容补充、找答案等附加服务。
- 2、"仅部分预览"的文档,不可在线预览部分如存在完整性等问题,可反馈申请退款(可完整预览的文档不适用该条件!)。
- 3、如文档侵犯您的权益,请联系客服反馈,我们会尽快为您处理(人工客服工作时间:9:00-18:30)。
CSB经典案例分析—ASCO乙炔生产装置单向阀失效导致的可燃气体爆炸事故唐彬天津市居安企业管理咨询有限公司中国石油和化学工业协会培训中心摘要本文结合美国化学品安全与危害调查委员会(CSB)对2005年ASCO乙炔服务公司乙炔气生产装置因单向阀失效导致乙炔气逆流并泄漏爆炸事故的调查,详细介绍该起事故的发生背景、过程与后果,并从技术和管理角度综合分析、总结导致事故的各方面原因,分享CSB调查组根据事故调查结果总结的经验教训和建议措施。
关键词:乙炔、单向阀失效、爆炸、美国化学品安全与危害调查委员会(CSB)1. 事故简介2005年1月25日,位于美国新泽西州Perth Amboy的乙炔服务公司(Acetylene ServicesCompany, ASCO)是一家从事乙炔气生产和包装的公司,因乙炔发生器循环水管线上的单向阀失效内漏,导致乙炔气通过循环水管线逆流并泄漏进入封闭空间聚集,遇点火源后引发剧烈爆炸(如图1所示),事故造成3人死亡,1人重伤,附近生产厂房严重受损。
图1:爆炸事故现场照片2. 事故背景2.1 公司背景ASCO是一个家族式自营企业,于1982年开始在纽约和费城市区生产和包装乙炔气服务。
事故发生时,ASCO拥有14名员工。
ASCO主要在Perth Amboy厂区生产乙炔气,2004年7月,ASCO开始直接从一家石化企业购买乙炔气,以补充自己的生产能力。
2.2 装置布置ASCO生产装置位于一处工业区,乙炔气生产工艺设备、气瓶充装操作区、办公室和休息室均位于46号厂房内,如图2所示。
在46号厂房外部紧挨着设有6个沉降罐,中间是一个木制结构的厂棚。
厂棚里面设有水泵和相关附属管线。
接货码头用于卸载购买的乙炔气,另外还有一个丙酮储罐。
图2:平面布置示意图2.3 乙炔乙炔(俗称风煤或电石气)是一种无色、高反应活性和极度易燃的气体。
纯乙炔是无臭的,但工业用乙炔由于含有硫化氢、磷化氢等杂质,而有一股大蒜的气味,密度比空气稍轻。
乙炔气的可燃范围很宽,约2.5%~82%。
当乙炔气的压力被压缩至大于0.1MPa(表压)时,乙炔气可能发生剧烈的分解。
当乙炔气被液化时,也非常不稳定,也可能发生剧烈分解。
因为乙炔气的上述特点,乙炔通常被储存在专用乙炔气瓶内,气瓶内部装有浸入液态丙酮的多孔填料(高比表面积),目的是保持乙炔气稳定,防止分解。
使用时,溶解在丙酮内的乙炔变为气体分离出来,而丙酮仍留在瓶内,以便再次充入乙炔使用。
2.4 乙炔气生产工艺ASCO通过将电石(碳化钙,化学式为CaC2)和水(化学式为H2O)混合生产乙炔气(化学式为C2H2),同时生成副产物石灰(化学式为Ca(OH)2),反应过程为放热反应。
反应过程如下:CaC2+H2O→C2H2+ Ca(OH)2+热量混合过程在一个卧式储罐内进行,称作发生器,如图3所示。
发生器内装有一定量的水,根据发生器的压力,控制电石以一定的速率进入发生器中。
该过程为半自动化式控制,如果给发生器供料的电石料斗保持满料状态,反应过程就可以连续进行。
图3:乙炔发生器(圆圈处为循环水管线上的单向阀)生成的乙炔气经压缩机转输至附属设备除去杂质,净化后的乙炔气被送至充装操作间,充装至气瓶中。
副产品石灰浆从发生器连续排放到位于厂房外部的一个储槽中,然后经泵加压输送至沉降罐里。
2.5 沉降罐ASCO使用6个敞口的串联的沉降罐临时储存副产品石灰浆,也用于准备和储存发生器循环使用的水。
这6个钢制的常压储罐,高度约6米,直径约3米,分为两排南北方向布置。
石灰浆从储槽被泵入到1#沉降罐里,石灰颗粒逐渐沉降,上部的水则溢流至2#沉降罐里,石灰颗粒经进一步沉降分离,水继续进入到下游沉降罐。
当水进入到5#和6#沉降罐时,水中的石灰含量已很少,如图4所示。
各个沉降罐底部聚集的石灰泥反复用泵抽出来,然后被承包商运走。
根据生产需要,5#和6#沉降罐里集聚的水可以通过泵输送回发生器循环使用。
图4:沉降罐流程简图2.6 木制厂棚(石灰棚)ASCO装置区域的6个沉降罐之间建有一个木制厂棚,长约8.5m,宽约4.6m,如图2所示,6个沉降罐的罐璧构成了厂棚的一部分围墙。
厂棚里面设有2个电动泵,一个用于从沉降罐抽出沉积的石灰泥,另一个用于将经沉降处理后的水循环至发生器。
厂棚使用一个安装在墙面上的丙烷加热器供暖,防止机泵和附属管线发生冻结。
厂棚没有机械通风设备。
2.7 丙烷加热器厂棚的一处墙面上安装了一个家用的直喷丙烷加热器,如图5所示。
加热器通过两个同轴管道的环形空间吸入厂棚外面的空气用于燃烧,高温烟气通过同轴管道的内管排出。
燃烧室和厂棚内部空间是完全密封的,厂棚内的空气不会和火焰或者燃烧产物接触。
图5:丙烷加热器示意图加热器通过自然对流提高室内温度,运行过程中燃烧室的外表面的温度约590℃。
加热器内还设置了一个自动切断阀,用于当长明灯熄灭时自动切断向燃烧室供给的丙烷燃料。
根据事故后的检查,发现这个自动切断阀实现了预定的功能。
3. 事故发生过程2005年1月25日早上,ASCO员工把购买的乙炔气充装到专用气瓶中。
上午约9:30,他们开始用电石生产乙炔气。
由于当时下了暴雪,ASCO工人正在沉降罐南面的区域(靠近装货码头)铲雪。
上午10:36,厂棚的正中心位置发生爆炸,紧靠厂棚南侧的2名工人当场死亡,更靠近装货码头的1名工人重伤,送到纽约救护中心后不久也被宣告死亡。
位于装货码头/石灰槽区域的1名工人因爆炸冲击波受到重伤。
根据法医检查,遇难者身体的内部器官、骨骼和肌肉均受到严重损伤,正是由于暴露在高速爆燃(压力波为亚声速)或者爆轰(一种急速爆炸现象,会产生超音速的压力冲击波)产生的高强度冲击波造成的。
另外,厂棚已被彻底破坏,厂棚墙壁被炸成碎片,散落到距离爆炸现场约137米的地方。
爆炸在46号厂房的砌筑墙上炸出两个大洞,乙炔气瓶被爆炸冲击到各个地方。
爆炸后没有发生后续火灾。
4. 事故分析4.1 燃料来源ASCO装置的生产过程涉及两种爆炸性物质,分别是乙炔气和丙烷气。
根据分析,一种可能的事故场景是,发生器中的乙炔气可能通过沉降罐水管线上的排水阀泄漏进入厂棚区域,这个排水阀门通常情况下是打开的,在冬季每天工作结束后也被打开,目的是为了防止排水管线被冻住。
还有一种可能的事故场景,丙烷气可能从位于厂棚北端的丙烷加热器或者丙烷燃料管线中泄漏出来进入厂棚区域。
根据事故现场的破坏机理和爆炸现象来看,这次爆炸是一种爆轰现象,或者至少是一种高速的爆燃现象。
BST(Baker-Strehlow-Tang)模型理论认为,蒸气云爆炸的强度取决于燃料的反应活性、空间阻塞度和爆炸区域的拥挤度。
反应活性和物料的火焰速度有关。
根据收集的现场证据和事故调查分析(如表1所示),都认为导致这次爆炸的物质是乙炔气。
表1:爆炸燃料的来源对比分析4.2 事故场景如图6所示,由于乙炔气发生器循环水管线上的单向阀发生内漏,导致发生器内生成的乙炔气穿过失效的单向阀,通过循环水管线上处于打开状态的排水阀泄漏进入厂棚内部区域,乙炔气在厂棚内部聚集,遇到点火源后发生爆炸。
图6:乙炔生产流程简图ASCO公司的常规做法是在晚上保持沉降水管线处于打开状态,通过设置在低点的阀门把水排到厂棚地面上,防止冬季时管线外部被冻坏。
这个处于打开状态的排水阀为发生器内乙炔气泄漏进入厂棚内部区域提供了一个潜在通道,而且厂棚封闭空间的设计也没有考虑可能出现乙炔气的工况,没有设置机械通风。
工艺危害分析(Process hazards analysis, PHA)是一个基于团队合作、头脑风暴的风险识别技术,也是OSHA过程安全管理法规(Process Safety Management Regulation, PSM)中的一个重要要素。
ASCO乙炔生产装置涉及的可燃液体或气体量超过了10000磅(包括乙炔和丙酮),属于OSHA过程安全管理法规(29 CFR 1910.119)管辖范围。
通过进行PHA可以帮助识别工艺流程和操作过程中存在的潜在风险、可能后果,以及相应的保护措施,通过采取系统的建议措施来消除或控制识别出来的潜在风险。
ASCO公司在1996年进行的PHA活动没有识别出厂棚内沉降水管线排水位置可能带来的潜在风险。
根据OSHA PSM的要求,ASCO公司在2001年应再次进行PHA,但是ASCO没有按照要求做这项工作,又一次错失了发现导致这次爆炸事故的原因的机会。
4.3 操作顺序爆炸发生后,发现乙炔气发生器的循环水管线上的排水阀是处于打开位置的,这说明事故发生时循环系统并不处于运行状态。
CSB调查组认为,在循环水系统启动之前,操作人员关闭了自来水供给阀,导致发生器系统没有带压水去防止乙炔气的逆流工况。
如果在关停自来水供给之前,关闭排水阀并投用循环水系统,就可能阻止乙炔气逆流泄漏进入厂棚内部。
ASCO制定了关于乙炔气发生器的操作手册,但是手册中没有涉及循环水系统的内容。
所以,对于如何正确操作循环水系统,操作人员没有相关的书面指导手册,也不清楚操作程序出现偏离时可能导致的后果。
发生器所在房间的墙上张贴了一些常规操作程序,但是没有涉及向发生器加水(循环水或者自来水)的正确操作步骤的有关内容。
员工培训记录不完整,而且每个员工的操作步骤也不一致。
4.4 单向阀逆流发生器循环水管线上安装的单向阀是由Rexarc公司设计和提供的,由于该单向阀内漏发生失效,导致发生器内的乙炔气发生逆流,并从打开的排水阀处泄漏进入厂棚区域。
根据爆炸后对单向阀的测试,发现可燃气逆流通过了该单向阀,而且OSHA进行X射线检测后发现单向阀内部的导向针被卡在了下部管线凸点处,如图7所示。
ASCO公司员工曾经发现过这个单向阀发生泄漏,当时是由这名员工对阀门进行了拆卸、清洁和重新组装。
图7:单向阀失效示意图●该单向阀依靠重力和背压实验密封,没有弹簧辅助进行阀塞的密封;●阀塞没有被有效地导向,出现了未对中的趋势;●单向阀内部表面容易出现固体聚集,例如结垢或者循环水中携带的石灰颗粒等。
当工艺管线上设置的单向阀对于防止出现逆流工况很关键时,涉及危险物料时不应该单独依靠单向阀保护逆流场景。
好的做法是提供一种更加可靠的隔离方案,例如,除了设置一个单向阀外,再设置两个截止阀和一个放空阀(排放至安全位置),从而确保不会发生爆炸性气体逆流的工况。
4.4 石灰棚设计石灰棚的设计和建造没有考虑可能出现乙炔气的工况,没有设置强制通风,安装的加热器的表面温度很高,足以点燃乙炔气。
这样的环境条件很容易在出现乙炔气泄漏的情况下导致可燃气云爆炸事故。
由于冬季气温很低,而且石灰棚没有保温,所以在爆炸事故发生时,加热器很可能正在运行或者处于频繁启停状态。
乙炔气的自燃温度约304℃,远远低于加热器燃烧室表面的温度(约593℃)。