操作性前提方案计划表
HACCP计划示例(含操作性前提方案)

控制的危害
操作要求
监控
纠偏行动
记录
内容
方法
频率
责任人
OPRP-02
(预煮后)冷却
生物:致病菌生长
1、保持冷却过程器具、人员的清洁卫生;
2、冷却温度,时间符合工艺文件和作业文件要求。
冷却过程清洁卫生;
冷却温度、时间
检查
每批
操作人
现场品控员
发现不符合操作要求的立即纠正。
生产记录和检查记录
纠正预防措施处理单
配料:柠檬酸
加工方式
清洗、整理、切片、定量装罐(袋)、封口、杀菌
包装
密封铁罐;9升罐2听/箱、18升1听/箱
密封耐高温蒸煮袋(每箱袋数根据客户定单确定)
食用方法
烹调后食用
贮存条件
低温、干燥、避光贮存;
保质期
常温下,一年
销售方式
出口、批发和零售
适宜的消费者
一般公众
标签要求
国内销售符合GB7718,出口销售符合进口国食品标签要求
物理危害:无
3、 HACCP计划表
3.1 HACCP计划表(清水食用菌)
企业名称:某某(某某)食品有限公司
企业地址:
预期用途和消费者:大众
产品:清水食用菌、蔬菜
销售和储存方法:常温保藏;货架销售
食用方法:烹调后食用
编制/日期:
审核/日期:
(1)
(2)
(3)
(4)
(5)
(6)
(7)
(8)
(9)
(10)
压力:0.5pp- 2ppm。
杀菌温度、时间。
钟表计时,
观察温度计。
每锅
杀菌工;
PRP、OPRP和HACCP计划三者
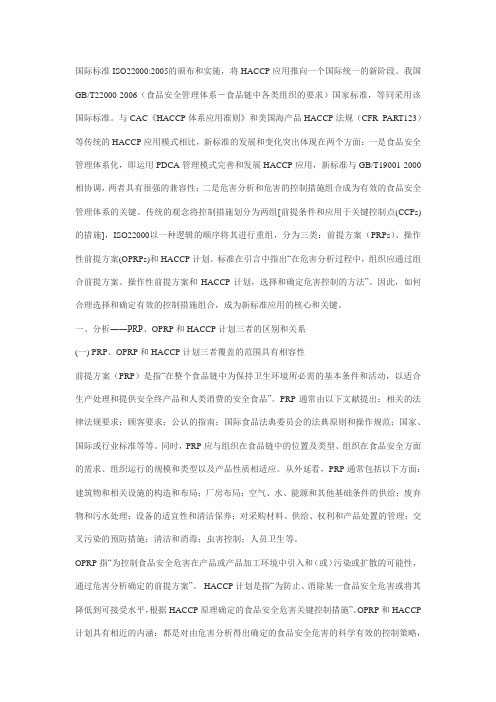
国际标准ISO22000:2005的颁布和实施,将HACCP应用推向一个国际统一的新阶段。
我国GB/T22000-2006(食品安全管理体系-食品链中各类组织的要求)国家标准,等同采用该国际标准。
与CAC《HACCP体系应用准则》和美国海产品HACCP法规(CFR PART123)等传统的HACCP应用模式相比,新标准的发展和变化突出体现在两个方面:一是食品安全管理体系化,即运用PDCA管理模式完善和发展HACCP应用,新标准与GB/T19001-2000相协调,两者具有很强的兼容性;二是危害分析和危害的控制措施组合成为有效的食品安全管理体系的关键。
传统的观念将控制措施划分为两组[前提条件和应用于关键控制点(CCPs)的措施],ISO22000以一种逻辑的顺序将其进行重组,分为三类:前提方案(PRPs)、操作性前提方案(OPRPs)和HACCP计划。
标准在引言中指出“在危害分析过程中,组织应通过组合前提方案、操作性前提方案和HACCP计划,选择和确定危害控制的方法”。
因此,如何合理选择和确定有效的控制措施组合,成为新标准应用的核心和关键。
一、分析――PRP、OPRP和HACCP计划三者的区别和关系(一) PRP、OPRP和HACCP计划三者覆盖的范围具有相容性前提方案(PRP)是指“在整个食品链中为保持卫生环境所必需的基本条件和活动,以适合生产处理和提供安全终产品和人类消费的安全食品”。
PRP通常由以下文献提出:相关的法律法规要求;顾客要求;公认的指南;国际食品法典委员会的法典原则和操作规范;国家、国际或行业标准等等。
同时,PRP应与组织在食品链中的位置及类型、组织在食品安全方面的需求、组织运行的规模和类型以及产品性质相适应。
从外延看,PRP通常包括以下方面:建筑物和相关设施的构造和布局;厂房布局;空气、水、能源和其他基础条件的供给;废弃物和污水处理;设备的适宜性和清洁保养;对采购材料、供给、权利和产品处置的管理;交叉污染的预防措施;清洁和消毒;虫害控制;人员卫生等。
(项目管理)饲料生产公司食品安全管理HACCP计划管理手册(完整版)
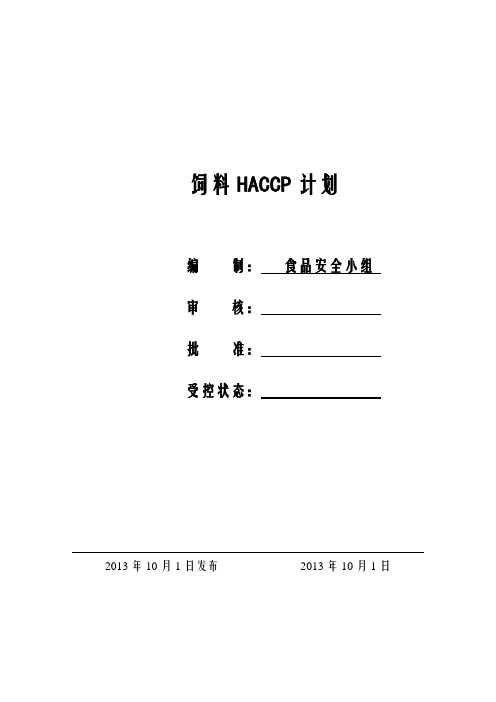
饲料HACCP计划编制:食品安全小组审核:批准:受控状态:2013年10月1日发布2013年10月1日0.1颁布令为保证本公司饲料产品的安全卫生质量,贯彻公司的质量方针,实现公司的质量目标,保证生产过程中任何可能出现的食品安全危害和有食品安全危害的点能够得到有效的控制,使本公司的食品安全危害能被控制、消除或降低到消费者可接受水平,以防止危害公众健康的问题发生,特编制本《HACCP计划》。
本《HACCP计划》是根据HACCP原理制定的, 是公司确保在食品安全管理体系中对食品安全危害进行控制的重要技术文件,本计划自2013年10月1日颁布实施,望公司全体员工认真贯彻执行。
总经理:2013年10月01日0.2《HACCP计划》管理说明《HACCP计划》是公司食品安全管理体系中对显著危害进行控制的重要技术文件。
为保证《HACCP计划》的适宜性、充分性、有效性和机密性,需加强对《HACCP计划》的管理。
《HACCP计划》的管理包括发放、宣贯、保管、更改等内容。
《HACCP计划》由食品安全小组组长负责组织有关人员起草,各职能部门会签,经管理者代表审核,总经理批准颁发。
《HACCP计划》为“受控”文件,其识别方法是在封面的受控状态栏中加盖或注明“受控”字样。
受控《HACCP计划》发放公司最高管理层人员、各职能部门、各车间负责人、质量管理员,更改受控制。
《HACCP计划》经总经理批准后,向认证机构和外公司提供。
《HACCP计划》管理的所有相关事宜均由办公室统一负责,未经总经理批准,任何人不得将《HACCP计划》提供给公司以外人员,持有者调离工作岗位时,应将《HACCP计划》归还办公室办理核收登记。
《HACCP计划》持有者应妥善保管,不得损坏、丢失和随意涂改。
《HACCP计划》使用期内如有修改建议,各部门负责人应汇总意见,及时反馈到办公室,办公室定期对《HACCP计划》的适宜性、充分性、有效性组织评审。
《HACCP计划》需要更改、修订时,由HACCP小组组长组织HACCP 小组成员对需更改或修订的内容按《验证控制程序》重新进行验证和确认,并按《文件控制程序》的有关要求组织修改。
oprp计划表
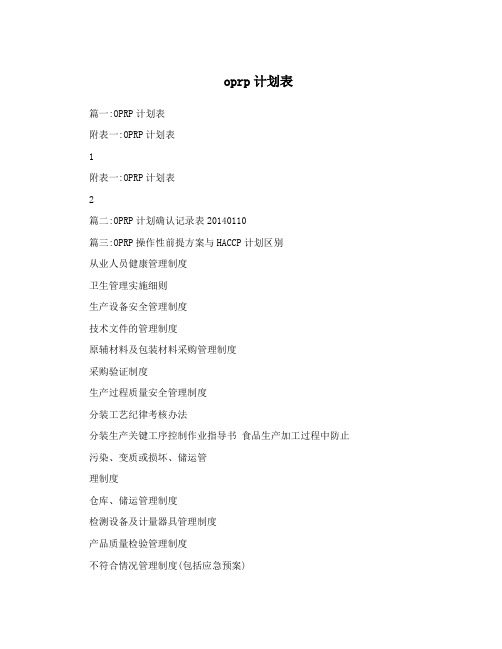
oprp计划表篇一:OPRP计划表附表一:OPRP计划表1附表一:OPRP计划表2篇二:OPRP计划确认记录表20140110篇三:OPRP操作性前提方案与HACCP计划区别从业人员健康管理制度卫生管理实施细则生产设备安全管理制度技术文件的管理制度原辅材料及包装材料采购管理制度采购验证制度生产过程质量安全管理制度分装工艺纪律考核办法分装生产关键工序控制作业指导书食品生产加工过程中防止污染、变质或损坏、储运管理制度仓库、储运管理制度检测设备及计量器具管理制度产品质量检验管理制度不符合情况管理制度(包括应急预案)产品召回管理制度回收食品管理制度产品销售管理制度产品的标识和可追溯性控制制度化验室仪器药品管理制度消费者投诉受理制度食品安全风险监测与评估信息制度食品安全事故处置方案让我们看看标准中关于OPRP操作性前提方案与HACCP计划区别:(请大家仔细阅读7.4.4第3-5段的描述)。
实际是在产品加工工序中经过危害分析后(请大家仔细阅读7.4.4第3-5段的描述),所制定的控制措施不需要作为HACCP计划控制的其他危害控制措施均为OPRP。
7.4.4控制措施的选择和评估 ---首先基于7.4.3 危害分析对每个加工步骤出现的显著危害确定相应的控制措施。
例如:以月饼为例包装车间内的三个工序中的危害:1. 金属碎屑检测---金属危害的控制2. 包材消毒(是工序的一部分)---微生物危害的控制3.包装气密性检测---微生物的控制经过危害分析并制定了相应的控制措施,按照标准中7.4.4介绍的a-g的评估之后以上三个控制点就可以分为1金属碎屑探测应为HACCP计划来管控。
2包材消毒,3包装气密性检测可以划分到OPRP来管控。
所以通过以上分析我想大家还是对标准中7.4.4条款的理解不够。
说明白点就是在危害分析后制定了针对每个工序制定了一系列的控制措施,按照7.4.4的控制措施分家了。
再例如说:水,如果水在产品的加工中非加工工序的一部分,并不能引入显著危害:蜜饯分装,水是用来清洗工器具的,那么就是一个PRP而已。
PRP、OPRP和HACCP计划三者
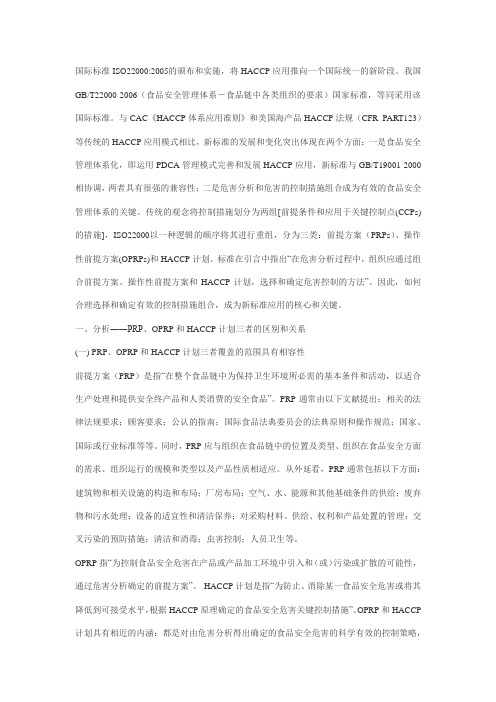
国际标准ISO22000:2005的颁布和实施,将HACCP应用推向一个国际统一的新阶段。
我国GB/T22000-2006(食品安全管理体系-食品链中各类组织的要求)国家标准,等同采用该国际标准。
与CAC《HACCP体系应用准则》和美国海产品HACCP法规(CFR PART123)等传统的HACCP应用模式相比,新标准的发展和变化突出体现在两个方面:一是食品安全管理体系化,即运用PDCA管理模式完善和发展HACCP应用,新标准与GB/T19001-2000相协调,两者具有很强的兼容性;二是危害分析和危害的控制措施组合成为有效的食品安全管理体系的关键。
传统的观念将控制措施划分为两组[前提条件和应用于关键控制点(CCPs)的措施],ISO22000以一种逻辑的顺序将其进行重组,分为三类:前提方案(PRPs)、操作性前提方案(OPRPs)和HACCP计划。
标准在引言中指出“在危害分析过程中,组织应通过组合前提方案、操作性前提方案和HACCP计划,选择和确定危害控制的方法”。
因此,如何合理选择和确定有效的控制措施组合,成为新标准应用的核心和关键。
一、分析――PRP、OPRP和HACCP计划三者的区别和关系(一) PRP、OPRP和HACCP计划三者覆盖的范围具有相容性前提方案(PRP)是指“在整个食品链中为保持卫生环境所必需的基本条件和活动,以适合生产处理和提供安全终产品和人类消费的安全食品”。
PRP通常由以下文献提出:相关的法律法规要求;顾客要求;公认的指南;国际食品法典委员会的法典原则和操作规范;国家、国际或行业标准等等。
同时,PRP应与组织在食品链中的位置及类型、组织在食品安全方面的需求、组织运行的规模和类型以及产品性质相适应。
从外延看,PRP通常包括以下方面:建筑物和相关设施的构造和布局;厂房布局;空气、水、能源和其他基础条件的供给;废弃物和污水处理;设备的适宜性和清洁保养;对采购材料、供给、权利和产品处置的管理;交叉污染的预防措施;清洁和消毒;虫害控制;人员卫生等。
操作性前提方案
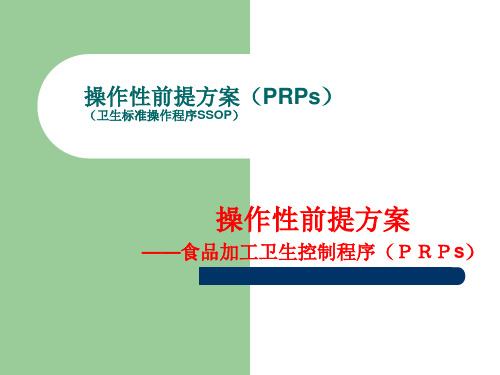
怎样洗手
摘掉首饰; 用温水(43℃)把手弄湿; 用肥皂水(洗洁精)彻底刷洗(30秒以上); 用清水清洗; 用含有效氯浓度50ppm的消毒水消毒30秒; 用清水冲洗 用处理过的纸巾擦干(或自动干手机烘干); 避免再次污染
食品接触表面
接触食品的表面 在正常加工过程中会将水滴溅在食品或食品接 触表面(包括工器具、刀具、桌面、案板、传 送带、制冰机、储水池、手套、围裙等)。
监测目标、监测什么?
监测应确保食品接触表面包括:手套和外衣设 计合理、结构和维护便于卫生处理,恰当地、按 时进行清洗和消毒。
接触食品的表面什么的状况; 食品接触表面的清洁和消毒; 使用的消毒剂的类型和浓度; 可能接触食品的手套和外衣是清洁并且状态良好。
设计和安装食品接触的设备
留有检修通道 提供清洁和检查的通道 适用于工厂的环境
食品接触表面的清洁和消毒
五个步骤
消除 预冲洗 使用清洗剂 后冲洗 使用消毒剂
器具的清洗和消毒
固定的场所和区域 最好使用热水 要用流动水 注意排水问题 注意清洗剂、消毒剂残留
交叉污染 是通过生的食物、食物处理或 食物环境把生物或化学污染转移到 食品的过程。当致病菌或病毒被转 移到即食食品上的,通常意味着产 生食源性疾病的交叉污染就发生了。
交叉污染的防止
员工防止污染的操作 生的和即食食品的隔离 工厂设计时防止交叉污染的产生
为防止交叉污染应进行的每日卫生操作 生、熟食品在加工过程适当的隔离 储藏中的产品的适当的隔离或保护 食品处理或加工区域和设备适当地清洁 和消毒 员工的个人卫生(衣着、手清洁操作) 加工人员的食品处理操作和工器具 员工在加工场所或区域的来往或移动
HACCP计划确认记录表
√
6.防止污染物污染
设备设施清洗消毒、维护程序中是否明确防止污染方法
是否明确冷凝水的控制方法
是否明确刀具等金属危害的控制方法
是否明确包装材料中可能污染物的控制方法
√
7.人员健康与卫生
否有健康检查制度并明确检查周期及特殊需要的情况
是否明确何种情况应调离生产岗位
是否明确洗手、工作服穿戴的卫生规范
√
4.手的清洁和厕所、更衣室的维护与保持
是否明确洗手程序和消毒、干手方法
是否明确什么情况下需要洗手
是否明确洗手用品及设施检查维护的频率
√
5.防止交叉污染
是否明确防止设计缺陷造成交叉污染的控制程序
人员操作规范、车间卫生规范等相关文件中是否明确人流、物流、水流、气流的要求,及生熟品分离操作要求、不同用途工具表识方法、运输工具交叉使用卫生控制
1.3流程图是否与实际相符
√
1.4实际操作是否与工艺描述相符
√
1.5加工设备有否改变?对食品安全有无影响
√
1.6工作人员有否变化?对食品安全有无影响
√
1.7产量是否改变?对食品安全有无影响
√
2评价产品安全历史√Βιβλιοθήκη 2.1是否存在过多的CCP偏离
√
2.2同类产品是否不止一次采取产品召回行动
√
2.3是否存在涉及产品安全的消费投诉
√
3评价HACCP计划的实施情况
√
3.1检查关键控制点是否按HACCP计划
√
3.2检查加工过程中是否按确定的关键限值操作?CCP的关键限值是否恰当
√
3.3检查记录是否准确按要求的时间来完成
√
3.4监控是否按HACCP计划规定的地点予以完成
PRP、OPRP和HACCP三者间的关系和区别
PRP、OPRP和HACCP三者间的关系和区别? ? 在ISO22000中不再提GMP、SSOP,而提出了“前提方案”(prerequisite program,简写为PRP。
其定义为:(食品安全)在整个食品链中为保持卫生环境所必须的基本条件和活动,以适合生产、处理和提供安全终产品和人类消费的安全食品)的概念,以替代传统的GMP 、SSOP概念。
GAP、GVP、GMP、GHP、GPP、GDP、GTP等都属于“前提方案”的范畴。
OPRPSSOP? ? 在方案(1.PRP应与组OPRP能性,通过危害分析确定的前提方案”。
HACCP计划是指“为防止、消除某一食品安全危害或将其降低到可接受水平,根据HACCP原理确定的食品安全危害关键控制措施”。
从上面分析,PRP具有较为明确的内涵和外延,但其不是针对特定危害的控制措施;OPRP和HACCP计划没有明确的外延,其包括的范畴由危害分析确定的具体的食品安全危害决定。
OPRP和HACCP计划具有相近的内涵:都是对由危害分析得出确定的食品安全危害的科学有效的控制策略。
ISO22000标准中对于关键的食品安全危害的控制措施通常由HACCP计划管理;同时,HACCP计划的管理策略更为严格。
从上面看,三者覆盖的范围具有相容性。
2.PRP是建立OPRP和HACCP计划的基础? ? 标准之“7 安全产品的策划和实现”给出了PRP 、OPRP 、HACCP 计划策划和建立的计方法、监视频率、记录要求等。
? ? 验证是在控制措施实施后实施的,以证实控制措施得以有效实施,达到了控制效果。
标准对三者都有验证要求,7.8条款要求验证活动应确定“前提方案得以实施”、“HACCP 计划中的要素和操作性前提方案得以实施且有效”、“危害水平在确定的可接受水平之内”。
? ? PRP 、OPRP 、HACCP 计划三者比较如下:? ?“不符合”是指不满足PRP、OPRP和HACCP计划的要求。
前提方案PRP和操作性前提方案OPRP介绍
前提方案PRP和操作性前提方案OPRP介绍前提方案(Preliminary Research Plan, PRP)是指在正式研究开始之前所制定的一个计划,旨在明确研究的目标、方法、工作内容以及预期结果等。
它是研究过程中的第一步,提供了实施研究的基本框架。
PRP通常包括以下几个方面的内容:1. 研究目标:明确研究的目的和意义,概括研究所要解决的问题以及所期望的结果。
2. 研究背景:介绍该研究领域的相关背景知识,包括已有的研究成果和存在的问题,以及国内外研究的现状和发展动态。
3. 研究内容和方法:详细阐述研究的内容、范围和方法,包括数据采集和分析的具体步骤,实验设计和调查问卷等工具的使用。
4. 预期结果和意义:说明研究的预期结果和对学术、实践或政策的影响,指出研究可能带来的创新点和进一步研究的方向。
操作性前提方案(Operational Preliminary Plan, OPRP)是在PRP的基础上展开的,更加注重具体实施步骤和时间安排。
OPRP主要包括以下几个方面的内容:1. 研究计划和时间安排:明确研究的具体计划和各项工作任务的时间节点,制定合理的时间表,确保研究进度的可行性。
2. 数据采集和处理方法:具体规划数据采集的方法和来源,并提出数据处理和分析的具体方法和软件工具,保证研究数据的准确性和可靠性。
3. 研究的资源和条件:明确研究所需的人力、物力、财力等资源的配置,并提出合理的利用和保障措施,确保研究的顺利进行。
4. 风险管理和应急措施:提前考虑可能遇到的问题和困难,并制定相应的风险管理和应急措施,以应对不可预见的情况。
通过PRP和OPRP的制定,研究者能够在正式研究开始之前明确研究目标、方法和工作计划,降低研究过程中的风险和不确定性,提高研究的有效性和可操作性。
同时,PRP和OPRP也可以作为研究的框架和指导,使研究者更加有序地进行研究工作,保证研究的顺利进行。
ISO22000-2005 标准的理解
关于ISO22000:2005标准的认识摘要:ISO22000:2005标准要求的操作性前提方案与SSOP是有区别的,前者是通过危害分析确定的必需的前提方案,而后者是法规,特别是出口食品企业注册卫生规范的要求。
新标准要求识别食品危害应覆盖食品的产品类别、过程类别以及可能涉及的生产设施产生的食品安全危害,识别的危害应完整,危害评价时应评价每种危害在在终产品中是否显著,并最终通过控制措施的组合对显著危害进行控制。
关键词:ISO22000:2005,控制措施的组合2005年9月1日,ISO颁布《食品安全管理体系——食品链中各类组织的要求》,即ISO22000:2005,我们国家在2006年7月1日将其等同转换了国家标准,即GB/T22000:2006。
随着标准的实施,对于标准中的要求的理解,审核员之间发出了不同的声音,本文就标准实施将近两年来个人的体会发表一点看法。
一、操作性前提方案、前提方案和SSOP前提方案是在企业中为保持卫生环境所必需的基本条件和活动,以适合生产、处置和提供安全终产品;前提方案等同于良好农业规范(GAP)、良好兽医规范(GVP)、良好操作规范(GMP)、良好卫生规范(GHP)、良好生产规范(GPP)、良好分销规范(GDP)、良好贸易规范(GTP)等。
我们应该注意,前提方案的内容是包括两部分的,一是卫生管理所需的基本条件,就是我们经常讲的基础设施,二是卫生管理中的活动,即为了使基础设施符合要求所需的卫生管理要求。
因此在判定企业前提方案是否符合ISO22000标准时,应该从以上两个方面进行评价。
前提方案是食品安全管理体系的基础,并且,对于企业而言,ISO22000标准7.2明确要求:“无论是普遍适用还是适用于特定产品或生产线,前提方案都应在整个生产系统中实施。
”对此,审核员应该关注,当企业的食品安全管理体系没有覆盖全部产品或生产线时,企业的危害分析应该关注没有在食品安全管理体系部分产品的经营管理活动对体系内产品可能造成的影响。
- 1、下载文档前请自行甄别文档内容的完整性,平台不提供额外的编辑、内容补充、找答案等附加服务。
- 2、"仅部分预览"的文档,不可在线预览部分如存在完整性等问题,可反馈申请退款(可完整预览的文档不适用该条件!)。
- 3、如文档侵犯您的权益,请联系客服反馈,我们会尽快为您处理(人工客服工作时间:9:00-18:30)。
第六届HACCP应用及认证研讨会论文
操作性前提方案在肉鸡屠宰企业中的应用
作者:张孙现
单位:福建东南标准认证中心
操作性前提方案在肉鸡屠宰企业中的应用
福建东南标准认证中心350002 张孙现
操作性前提方案(OPRP)指为控制食品安全危害在产品或加工环境中引入和(或)食品安全危害污染或扩散的可能性,通过危害分析确定的必不可少的前提方案。
操作性前提方案是在危害分析的基础上获得的,用于对识别的危害进行控制,而基础设施和维护方案则不基于危害分析。
为解决肉鸡屠宰过程中的危害,通过HACCP原理和操作性前提方案等控制
措施相结合的办法进行控制,即被确定为关键控制点的显著危害通过HACCP计划控制,而其它的显著危害,通过建立操作性前提方案进行控制。
HACCP对危害的控制固然重要,但没有操作性前提方案等控制措施的有效控制,同样无法显示HACCP的巨大威力。
一、肉鸡屠宰生产工艺流程:
毛鸡验收卸鸡挂鸡击晕放血沥血浸烫打毛摘小毛高压冲淋切爪转挂割颈皮勾腺胃砍鸡头开膛挑破肠鸡只掏膛腹腔检查冲洗高压冲淋卸鸡冷却转挂分割包装金属探测入库冷藏
二、操作性前提方案的建立
操作性前提方案计划表
中国国家认证认可监督管理委员会食品伙伴网
中国国家认证认可监督管理委员会食品伙伴网
中国国家认证认可监督管理委员会食品伙伴网
三、操作性前提方案实施效果验证
对肉鸡屠宰生产线的微生物状况做了调查,具体包括员工的手、刀具、案板、传送带、屠宰过程中主要工序胴体表面、包装前分割肉的菌落总数和大肠菌群两项微生物指标进行了测定。
通过实验验证操作性前提方案的实施效果以及进一步明确操作性前提方案的控制要点。
3.1生产线上主要工序的微生物状况
图-1屠宰过程中胴体表面微生物的变化
Fig3-1Microbial level on the surface of carcass during slaughtering
图3-1是屠宰加工过程中微生物的变化,在打毛和掏膛后胴体上的污染状况较为严重,导致这种变化可能的原因是经打毛工序,鸡胴体与打毛棒存在着交叉污染;掏膛将肉鸡内容物带出从而污染胴体,但两者的污染程度都可在后面的工序中减轻。
经高压冲淋后微生物水平有所降低,但仍然维持在一个比较高的水平,由于微生物与胴体表面相结合,淋水很难将其去除[46];接下来的冷却消毒工序将微生物进一步降低至理想水平。
冷却消毒工序对于肉鸡进入分割车间之前的微生物控制是至关重要的,后续没有对肉鸡胴体和鸡肉进行消毒的工序,因此冷却消毒工序应确定为关键控制点,这与之前的危害分析结果是一致的。
1 2 3 4 5 打毛后
道冲淋后
掏膛
后高压冲淋后
冷却消毒后
22
3.2生产线上刀具、案板和员工的手的微生物状况
图3-2屠宰分割线主要工具和工人手上的菌落总数
Fig 3-2 lg cfu/cm 2
of the Main Facilities and Workers' Hands on the Slaughtering
图3-3屠宰分割线主要工具和工人手上的大肠菌群污染状况
Fig 3-3 lg (MPN/100cm 2) of Coliform Group of the Main Facilities and Workers' Hands on the
Slaughtering
通过检测刀具、接触面和员工的手均存在不同程度的交叉污染,从而能够更加明确了操作性前提方案控制的重点。
经过操作性前提方案的控制,分割的刀具、案板、分割车间流水线的传送带和分割工人的手的微生物状况是符合要求的。
说
菌落总数(Lg cfu/ cm 2)
0.5 1 1.5 2 2.5 3 3.5 4 放血刀具
掏膛具
分割具
分割案板
传送带
放血员工的手掏膛员工的手
分割员工的
明采取的操作性前提方案的控制是有效的、合理的。
四、讨论
改革开放以来,我国的禽肉行业得到快速的发展,鸡肉的产量居世界前列。
由于我国屠宰行业起步晚,生产的肉制品合格率偏低,档次不高。
但随着人们生活水平的提高,对肉制品的质量要求越来越高。
如何提高肉制品的安全质量,成为广大肉类生产企业努力的方向。
根据美国国家科学院全国研究委员会(U.S .A NAS/NRC)制定的风险模式,肉鸡屠宰加工是细菌等微生物污染主要渠道之一,也是影响鸡肉制成品的关键。
本项目的研究将以HACCP为核心的ISO22000食品安全管理体系应用于肉鸡屠宰加工企业,在危害分析的基础上列出每个工艺环节的危害类型和程度,并将显著危害分别列入HACCP计划和操作性前提方案加以控制。
这样,即使某些生产人员的卫生观念淡薄,只要按要求操作,也可以到达监控的目的。
即使出现问题,仍有章可循,有因可究,做到心中有数,对待问题可对症下药,达到治标治本的目的.。