仪表自动化系统应急预案
仪表应急预案
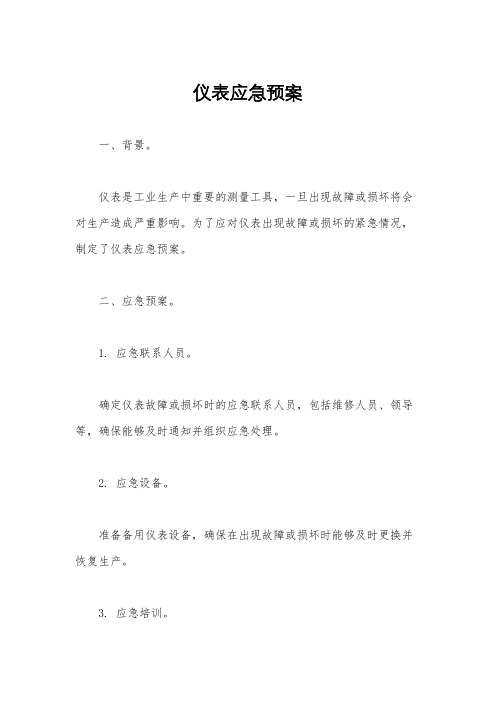
仪表应急预案一、背景。
仪表是工业生产中重要的测量工具,一旦出现故障或损坏将会对生产造成严重影响。
为了应对仪表出现故障或损坏的紧急情况,制定了仪表应急预案。
二、应急预案。
1. 应急联系人员。
确定仪表故障或损坏时的应急联系人员,包括维修人员、领导等,确保能够及时通知并组织应急处理。
2. 应急设备。
准备备用仪表设备,确保在出现故障或损坏时能够及时更换并恢复生产。
3. 应急培训。
对相关人员进行仪表应急处理的培训,包括如何快速识别故障、如何更换设备等,提高应对突发情况的能力。
4. 应急演练。
定期组织仪表应急演练,模拟不同情况下的应急处理过程,确保相关人员熟练掌握应急处理流程。
5. 应急备件。
储备常见故障的备件,确保在出现故障时能够快速更换,减少生产中断时间。
6. 应急通知。
建立应急通知机制,确保在出现故障或损坏时能够及时通知相关人员并启动应急预案。
7. 应急评估。
对每次仪表故障或损坏进行评估,总结经验教训,不断完善应急预案。
三、应急预案执行。
当出现仪表故障或损坏时,立即启动应急预案,按照预案流程进行应急处理,确保生产能够尽快恢复正常。
四、应急预案检查。
定期对仪表应急预案进行检查和评估,及时发现问题并进行改进,确保应急预案的有效性和可靠性。
五、总结。
仪表是生产中不可或缺的工具,出现故障或损坏将会对生产造成严重影响。
因此,制定和执行仪表应急预案是非常重要的,能够有效降低因故障或损坏导致的生产中断时间,保障生产的正常进行。
仪表应急预案
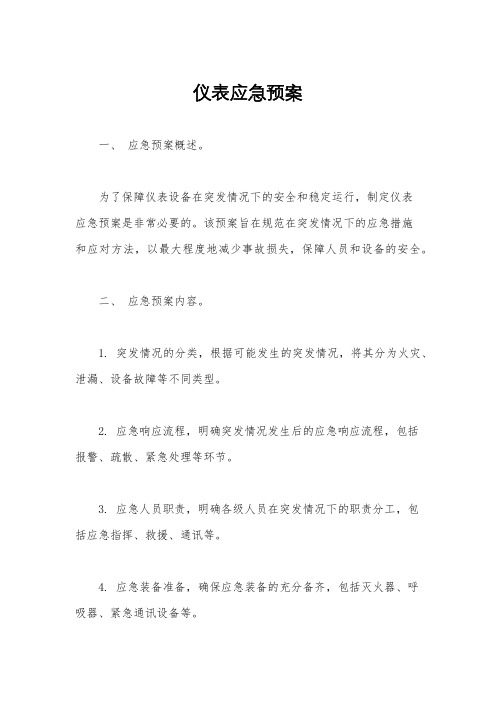
仪表应急预案
一、应急预案概述。
为了保障仪表设备在突发情况下的安全和稳定运行,制定仪表
应急预案是非常必要的。
该预案旨在规范在突发情况下的应急措施
和应对方法,以最大程度地减少事故损失,保障人员和设备的安全。
二、应急预案内容。
1. 突发情况的分类,根据可能发生的突发情况,将其分为火灾、泄漏、设备故障等不同类型。
2. 应急响应流程,明确突发情况发生后的应急响应流程,包括
报警、疏散、紧急处理等环节。
3. 应急人员职责,明确各级人员在突发情况下的职责分工,包
括应急指挥、救援、通讯等。
4. 应急装备准备,确保应急装备的充分备齐,包括灭火器、呼
吸器、紧急通讯设备等。
5. 应急演练计划,定期组织应急演练,提高人员的应急处理能力和协作效率。
三、应急预案执行。
1. 突发情况发生后,立即启动应急预案,按照预案规定的流程进行应急响应。
2. 各级人员严格按照职责分工,配合进行应急处理。
3. 在事故得到控制后,及时总结经验,完善应急预案。
四、应急预案的修订和完善。
1. 定期对应急预案进行评估,根据实际情况进行修订和完善。
2. 加强应急知识培训,提高员工的应急处理能力和意识。
通过制定和执行仪表应急预案,可以有效应对突发情况,最大程度地减少事故损失,保障人员和设备的安全。
自动化控制系统事故专项应急预案
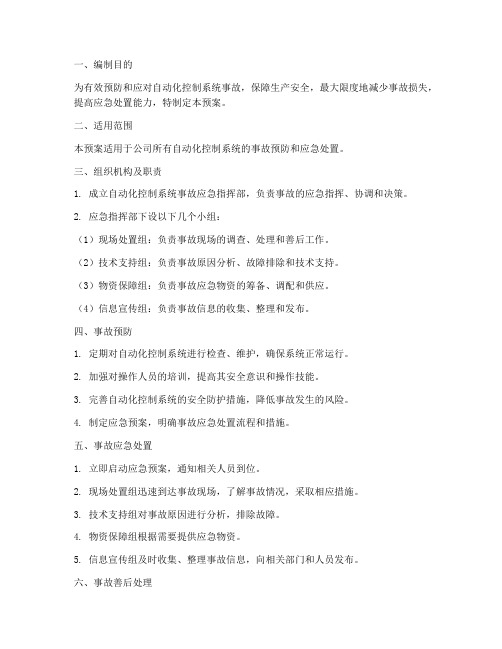
一、编制目的为有效预防和应对自动化控制系统事故,保障生产安全,最大限度地减少事故损失,提高应急处置能力,特制定本预案。
二、适用范围本预案适用于公司所有自动化控制系统的事故预防和应急处置。
三、组织机构及职责1. 成立自动化控制系统事故应急指挥部,负责事故的应急指挥、协调和决策。
2. 应急指挥部下设以下几个小组:(1)现场处置组:负责事故现场的调查、处理和善后工作。
(2)技术支持组:负责事故原因分析、故障排除和技术支持。
(3)物资保障组:负责事故应急物资的筹备、调配和供应。
(4)信息宣传组:负责事故信息的收集、整理和发布。
四、事故预防1. 定期对自动化控制系统进行检查、维护,确保系统正常运行。
2. 加强对操作人员的培训,提高其安全意识和操作技能。
3. 完善自动化控制系统的安全防护措施,降低事故发生的风险。
4. 制定应急预案,明确事故应急处置流程和措施。
五、事故应急处置1. 立即启动应急预案,通知相关人员到位。
2. 现场处置组迅速到达事故现场,了解事故情况,采取相应措施。
3. 技术支持组对事故原因进行分析,排除故障。
4. 物资保障组根据需要提供应急物资。
5. 信息宣传组及时收集、整理事故信息,向相关部门和人员发布。
六、事故善后处理1. 对事故原因进行彻底调查,分析事故原因,提出整改措施。
2. 对事故责任人进行责任追究,严肃处理。
3. 对事故影响范围进行评估,采取有效措施,减少事故损失。
4. 总结事故教训,完善应急预案,提高应急处置能力。
七、附则1. 本预案自发布之日起实施。
2. 本预案由自动化控制系统事故应急指挥部负责解释。
3. 本预案如有未尽事宜,可根据实际情况进行修订。
仪表应急预案
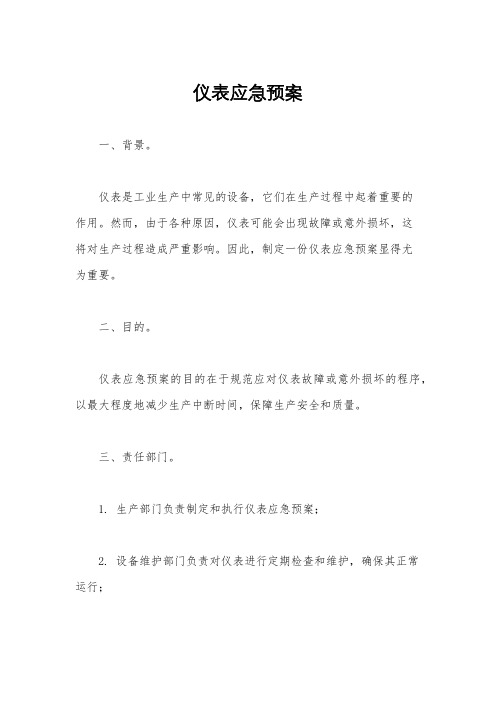
仪表应急预案
一、背景。
仪表是工业生产中常见的设备,它们在生产过程中起着重要的
作用。
然而,由于各种原因,仪表可能会出现故障或意外损坏,这
将对生产过程造成严重影响。
因此,制定一份仪表应急预案显得尤
为重要。
二、目的。
仪表应急预案的目的在于规范应对仪表故障或意外损坏的程序,以最大程度地减少生产中断时间,保障生产安全和质量。
三、责任部门。
1. 生产部门负责制定和执行仪表应急预案;
2. 设备维护部门负责对仪表进行定期检查和维护,确保其正常
运行;
3. 应急小组负责应对仪表故障或意外损坏,并及时进行修复或
更换。
四、预案内容。
1. 仪表故障或意外损坏的报警程序,当发现仪表出现故障或意
外损坏时,应立即向生产部门和设备维护部门报警,并启动应急预案。
2. 应急小组的组建和任务分工,生产部门应根据实际情况组建
应急小组,明确每个成员的任务分工,确保应急处理的高效进行。
3. 仪表维修或更换的程序,应急小组应根据故障情况,及时进
行维修或更换工作,确保仪表的正常运行。
4. 应急预案的演练和改进,定期组织应急预案的演练,发现问
题及时进行改进,提高应急处理的效率和水平。
五、应急预案的执行。
当发生仪表故障或意外损坏时,应急小组应立即启动应急预案,按照预案内容进行处理,确保生产过程的正常进行。
六、总结。
仪表是生产过程中不可或缺的设备,制定一份完喲的仪表应急预案对于保障生产安全和质量至关重要。
通过定期演练和改进,提高应急处理的效率,确保生产过程的顺利进行。
自动化设备应急预案与故障措施
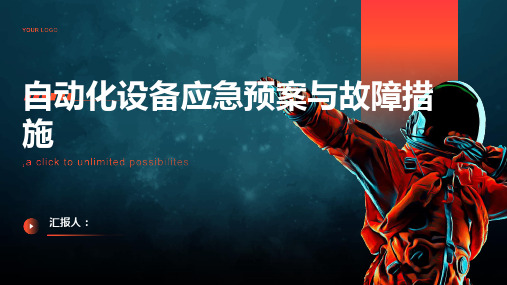
汇报人:
自动化设备应急预案 自动化设备故障措施
自动化设备应急预案
预案制定目的
保障自动化设备运行安全 减少设备故障对生产的影响 提高设备维护效率 确保生产过程顺利进行
预案适用范围
适用于自动化设 备在生产过程中 出现的突发故障
适用于设备故障 导致的生产中断、 人员伤亡等紧急 情况
添加标题
添加标题
添加标题
添加标题
评估方法:对比故障发生前后的设 备性能参数,分析故障原因和处理 效果
持续改进:根据评估结果,优化应 急预案和故障措施,提高设备可靠 性
THANK YOU
汇报人:
适用于自动化设 备的安全运行和 生产安全的管理
适用于企业对于 自动化设备应急 预案的制定和实 施
应急组织架构
应急指挥部:负责全面领导和协调应急工作 应急救援组:负责现场应急处置和救援工作 应急保障组:负责提供应急救援所需的物资、装备和资金等保障 应急宣传组:负责对应急处置和救援工作进行宣传和舆论引导
仪表检测法:使用各种 仪表对自动化设备的各 项参数进行测量,如温 度、压力、流量等,以 判断是否存在故障。
经验法:根据操作人员 长期积累的经验,通过 触摸、听声音等方式判 断自动化设备是否存在 故障。
故障自诊断法:利用自 动化设备自带的故障诊 断系统,对设备进行实 时监测和故障诊断。
故障应对策略
定期检查:对自动化设备进行定期检查,及时发现潜在故障 应急预案:制定应急预案,确保在故障发生时能够迅速响应 故障诊断:使用专业工具对故障进行诊断,确定故障原因 修复与更换:对故障设备进行修复或更换,确保生产线的正常运行
故障恢复流程
故障发现与诊断:及时发现并确定 故障原因
仪表应急预案
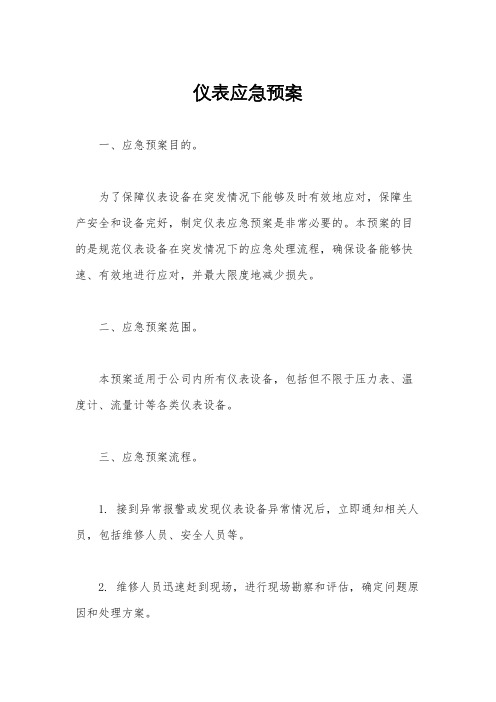
仪表应急预案一、应急预案目的。
为了保障仪表设备在突发情况下能够及时有效地应对,保障生产安全和设备完好,制定仪表应急预案是非常必要的。
本预案的目的是规范仪表设备在突发情况下的应急处理流程,确保设备能够快速、有效地进行应对,并最大限度地减少损失。
二、应急预案范围。
本预案适用于公司内所有仪表设备,包括但不限于压力表、温度计、流量计等各类仪表设备。
三、应急预案流程。
1. 接到异常报警或发现仪表设备异常情况后,立即通知相关人员,包括维修人员、安全人员等。
2. 维修人员迅速赶到现场,进行现场勘察和评估,确定问题原因和处理方案。
3. 根据维修人员的评估,决定是否需要紧急停机处理,如果需要停机,应按照公司规定程序进行停机操作。
4. 维修人员根据现场情况,进行设备维修或更换,确保设备能够尽快恢复正常运行。
5. 维修完成后,进行设备测试和运行监控,确保设备正常运行。
6. 维修人员对此次事件进行总结和记录,包括问题原因、处理过程和解决方案,以便日后的参考和改进。
四、应急预案执行。
1. 公司应当对本预案进行定期演练和培训,确保相关人员熟悉应急处理流程和操作规程。
2. 在实际应急事件中,相关人员应当按照预案流程进行操作,并及时报告处理情况。
3. 应急预案执行过程中,应当及时记录相关信息和数据,以便后续的分析和改进。
五、应急预案评估。
1. 公司应当定期对应急预案进行评估和改进,包括预案流程的完善和相关人员的培训。
2. 在实际应急事件中,应当及时总结经验教训,对预案进行修订和完善。
3. 公司应当建立健全的应急预案管理制度,确保预案的有效性和可持续性。
以上为仪表应急预案,希望公司的仪表设备能够在突发情况下保持高效、安全地运行。
自动化系统故障应急预案
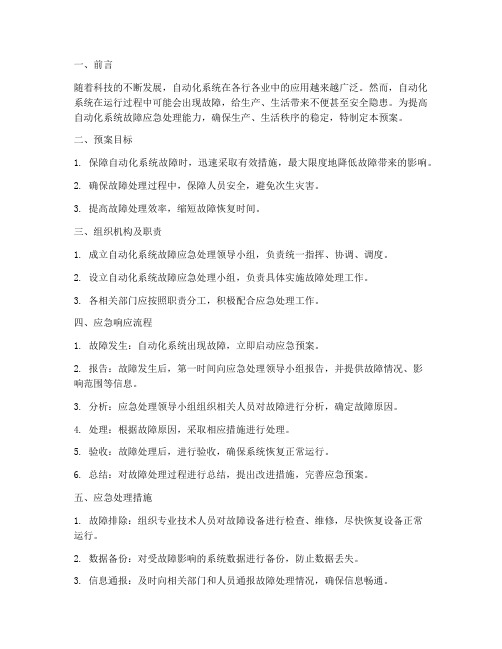
一、前言随着科技的不断发展,自动化系统在各行各业中的应用越来越广泛。
然而,自动化系统在运行过程中可能会出现故障,给生产、生活带来不便甚至安全隐患。
为提高自动化系统故障应急处理能力,确保生产、生活秩序的稳定,特制定本预案。
二、预案目标1. 保障自动化系统故障时,迅速采取有效措施,最大限度地降低故障带来的影响。
2. 确保故障处理过程中,保障人员安全,避免次生灾害。
3. 提高故障处理效率,缩短故障恢复时间。
三、组织机构及职责1. 成立自动化系统故障应急处理领导小组,负责统一指挥、协调、调度。
2. 设立自动化系统故障应急处理小组,负责具体实施故障处理工作。
3. 各相关部门应按照职责分工,积极配合应急处理工作。
四、应急响应流程1. 故障发生:自动化系统出现故障,立即启动应急预案。
2. 报告:故障发生后,第一时间向应急处理领导小组报告,并提供故障情况、影响范围等信息。
3. 分析:应急处理领导小组组织相关人员对故障进行分析,确定故障原因。
4. 处理:根据故障原因,采取相应措施进行处理。
5. 验收:故障处理后,进行验收,确保系统恢复正常运行。
6. 总结:对故障处理过程进行总结,提出改进措施,完善应急预案。
五、应急处理措施1. 故障排除:组织专业技术人员对故障设备进行检查、维修,尽快恢复设备正常运行。
2. 数据备份:对受故障影响的系统数据进行备份,防止数据丢失。
3. 信息通报:及时向相关部门和人员通报故障处理情况,确保信息畅通。
4. 人员疏散:如故障可能引发安全隐患,应立即组织人员疏散,确保人员安全。
5. 次生灾害防范:加强对故障区域及周边环境的监测,防止次生灾害发生。
六、后期处理1. 故障原因分析:对故障原因进行深入分析,查找管理、技术等方面的不足。
2. 改进措施:针对故障原因,提出改进措施,完善自动化系统。
3. 预案修订:根据实际情况,对应急预案进行修订,提高应对能力。
4. 培训演练:定期组织应急处理培训演练,提高应急处置能力。
自动化系统事故应急预案
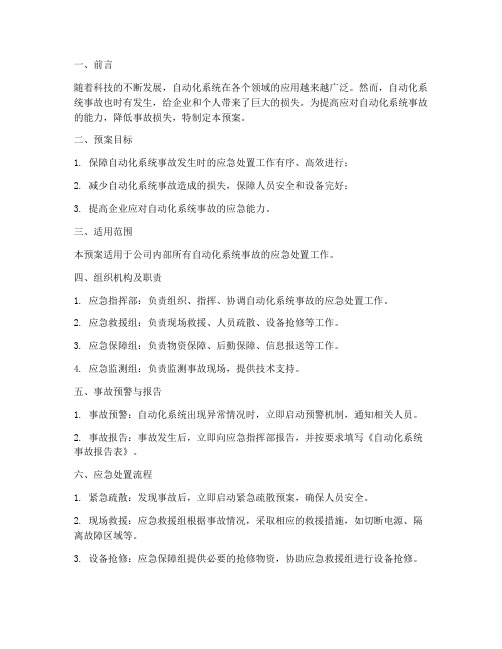
一、前言随着科技的不断发展,自动化系统在各个领域的应用越来越广泛。
然而,自动化系统事故也时有发生,给企业和个人带来了巨大的损失。
为提高应对自动化系统事故的能力,降低事故损失,特制定本预案。
二、预案目标1. 保障自动化系统事故发生时的应急处置工作有序、高效进行;2. 减少自动化系统事故造成的损失,保障人员安全和设备完好;3. 提高企业应对自动化系统事故的应急能力。
三、适用范围本预案适用于公司内部所有自动化系统事故的应急处置工作。
四、组织机构及职责1. 应急指挥部:负责组织、指挥、协调自动化系统事故的应急处置工作。
2. 应急救援组:负责现场救援、人员疏散、设备抢修等工作。
3. 应急保障组:负责物资保障、后勤保障、信息报送等工作。
4. 应急监测组:负责监测事故现场,提供技术支持。
五、事故预警与报告1. 事故预警:自动化系统出现异常情况时,立即启动预警机制,通知相关人员。
2. 事故报告:事故发生后,立即向应急指挥部报告,并按要求填写《自动化系统事故报告表》。
六、应急处置流程1. 紧急疏散:发现事故后,立即启动紧急疏散预案,确保人员安全。
2. 现场救援:应急救援组根据事故情况,采取相应的救援措施,如切断电源、隔离故障区域等。
3. 设备抢修:应急保障组提供必要的抢修物资,协助应急救援组进行设备抢修。
4. 信息报送:应急监测组对事故现场进行监测,收集相关数据,并及时上报应急指挥部。
5. 事故调查:事故处理后,应急指挥部组织相关部门对事故原因进行调查,提出改进措施。
七、应急物资与装备1. 应急物资:应急指挥部根据事故类型,提前储备必要的应急物资,如应急照明、应急通讯设备、防护用品等。
2. 应急装备:应急指挥部根据事故类型,配备相应的应急装备,如灭火器、抢修工具等。
八、应急演练1. 定期组织应急演练,提高应急处置能力。
2. 演练内容应包括事故预警、事故报告、现场救援、设备抢修、信息报送等环节。
3. 演练结束后,对演练情况进行总结,提出改进措施。
- 1、下载文档前请自行甄别文档内容的完整性,平台不提供额外的编辑、内容补充、找答案等附加服务。
- 2、"仅部分预览"的文档,不可在线预览部分如存在完整性等问题,可反馈申请退款(可完整预览的文档不适用该条件!)。
- 3、如文档侵犯您的权益,请联系客服反馈,我们会尽快为您处理(人工客服工作时间:9:00-18:30)。
精心整理一、DCS控制系统应急预案1、仪表操作人员接到通知后应在十分钟内到达事件发生现场。
2、检查计算机系统电源电压是否正常引入计算机。
3、检查控制器、电源箱及外围设备是否正常接入,有无松动和漏电情况。
4、检查UPS是否正常投入,是否旁路运行。
5、检查控制器I/O卡件运行信号灯是否正常闪烁。
6、检查系统通讯传输及数据采集是否正常。
7、检查DCS操作系统与数据库连接是否正常。
8、检查OPC是否正常运行。
9、检查DCS操作系统自诊断是否正常。
10、检查控制器功能模块是否正常。
11、检查事件记录及历史趋势曲线图是否正常记录及显示。
12、检查数据库临时性文件是否占用内存过大。
13、如上述情况存在不正常,与车间领导联系。
厂用电中断的现象及处理:1.厂用电中断现象:1.1DCS系统机柜只有一路电源运行。
1.2现场设备跳停,并且中控无法控制。
1.3UPS电源由市电转换为蓄电池供电模式。
1.4现场事故应急灯打开。
2.确认厂用电中断应:2.1打开控制站柜门,观察卡件是否工作正常,有无故障显示(FAIL灯亮);2.2从每个操作站实时监控的故障诊断中观察是否存在故障;3.当电气通知投入保安电源后,3.1对DCS系统机柜及UPS电源进行全面检查(如有问题及时处理),进入实时监控画面,观察系统是否运行正常。
3.2对系统实时监控画面进行全面检查如无问题,通知有关人员系统恢复正常,可以正常操作。
4.当电气确认一小时内不能投入保安电源,应通知调度及生产车间进行准备。
当确认短时间内供电无法恢复,UPS电源无法坚持运行时,在保证现场设备安全的前提下,可以对DCS电源进行断电操作。
DCS系统断电操作:1.每个操作站依次退出实时监控及操作系统后,关闭操作站工控机及显示器电源;2.依次关闭卡件柜、安全栅柜、继电器柜、网络柜、电源柜的电源;3.关闭不间断电源(UPS)电源开关;4.关闭总电源开关。
5.当恢复正常送电时,应对DCS系统进行全面检查开始送电5.1合上总电源开关;5.2合上不间断电源(UPS)电源开关;5.3依次合上电源柜、卡件柜、安全栅柜、继电器柜、网络柜;5.4开启各操作站及显示器电源,之后按照正常操作步骤操作。
二、PLC系统事故专项应急预案1上位机通讯出现故障:2.冗余的控制器是否正常运行,如果主控制器故障,而从控制器未正常切换,则应立即汇报相关领导并通知调度做好紧急停车的准备,同时人为重启从控制器,启动失败等待停车命令。
3.确保控制器正常的情况下,迅速检查各冗余控制器与交换机之间、工程师站、操作员站与交换机之间的网络连接情况:是否有通讯接头破损、脱落和松动状况,如有损坏立即更换备用或现场制作,松动则立即插紧,然后再经工程师站检查网络,测通网络,恢复正常运行。
4.PLC系统卡件损坏:4.1非冗余AI\DI\DO卡件损坏,首先确认损坏卡件上的仪表点是否牵扯联锁停车,如果有则应立即汇报相关领导并通知调度做好紧急停车的准备,同时将备用的卡件插入到已损坏的卡件位置,与工艺密切联系,随时注意工艺运行情况。
待卡件更换完成后,检查该卡件及所有仪表通道工作是否正常。
4.2冗余AO卡件损坏,首先与工艺联系将损坏卡件上的控制点切换到就地手动控制,然后将备用的卡件插入到已损坏的卡件位置。
如果不成功,及时汇报相关领导并采取措施更换,等待调度命令。
4.3UPS出现故障时,在电池供电期间应立即通知相关领导和调度做好停车的准备,同时将系统下电。
4.4UPS出现故障且电池不能供电的情况下,立即通知调度做停车处理。
4.5如因外部干扰对PLC系统供电造成影响,致使系统不能正常运作的,应首先检查接地情况,若接地正常,不能立即排除干扰,则立即汇报相关领导,同时通知调度做停车处理。
三、仪表停气应急处理预案1、停气后,应立刻通知分管领导(夜间应通知值班领导),现场阀门气闭式将会打开,气开式将关闭。
2、处理方案及应急措施:2.1停气后,及时到现场观察阀门状态,根据生产需求,手动将阀门打到生产要求状态。
若阀芯卡死或脱落应找该分厂维修工配合维修。
2.2待来气后,将手动装置打到自动状态,仪表阀门将正常工作。
四、仪表自控柜着火应急处理预案1、自控柜着火,若不能及时扑灭,会产生触电事故,烧坏模块、CPU。
2、处理方法及应急措施:2.1火灾发生时,电气设备因绝缘损坏而碰壳短路,线路因断线而接地,使正常不带电的金属构架、地面等部位带电,导致触电事故,所以应先切断电源,并立刻通知相关领导。
2.2应按灭火剂的种类选择适当灭火剂。
二氧化碳、二氟一氯一溴甲烷(即1211),二氟二溴甲烷或干粉灭火剂都是不导电的,即可用于电器灭火。
不能用泡沫灭火器灭火、水灭火。
2.3注意事项:严禁从自控柜引接任何与仪表无关的电源线(如:电焊机,照明灯等)。
五、热电阻应急预案1、仪表操作人员接到通知后应在十分钟内到达事件发生现场。
2、在检查热电阻时必须提前通知生产车间,并确定没有和其他仪表设备连锁才能进行操作。
3、观察历史曲线记录,是否存在突变,为零或趋于最大。
4、现场检查线路是否存在短路或断路情况。
现象原因处理方法电阻值偏低内部局部短路更换热电阻绝缘降低清洗烘干电阻值偏高或无穷大接线端子接触不良拧紧接线端子热电阻内部断路或引线断开更换热电阻示值不稳定接线端子接触不良拧紧接线端子绝缘降低清洗烘干5、检查热电阻阻值与正常阻值对照,判断是否存在偏差。
6、如不存在上述情况,通知调度与工艺操作人员协商,检查工艺,寻找是否存在引起变化的原因,如工艺操作正常,更换热电阻或热电阻芯。
7、运行记录、故障处理记录、检修记录、校准记录、零部件更换记录应准确无误。
8、系统原理图和接线图应完整、准确。
六、质量流量计应急预案1、仪表操作人员接到通知后应在十分钟内到达事件发生现场。
2、观察历史曲线记录,是否存在突变,为零或趋于最大。
3、检查信号线路,输入电压是否正常,是否存在短路或断路情况。
4、检查管线是否有污垢,清洗管道。
5、确认现场是否有其它干扰源(剧烈的震动,信号干扰)。
6、如不存在上述情况,通知调度与工艺操作人员协商,检查工艺,寻找是否存在引起变化的原因,如工艺操作正常,更换为备用质量流量计管线或开旁路。
7、运行记录、故障处理记录、检修记录、校准记录、零部件更换记录应准确无误。
8、系统原理图和接线图应完整、准确。
9、当无法查明故障原因或故障无法排除时,及时与车间领导联系。
七、液位变送器应急预案1、仪表操作人员接到通知后应在十分钟内到达事件发生现场。
2、观察历史曲线记录,是否存在突变,为零或趋于最大。
3、检查信号线路,输入电压是否正常,是否存在短路或断路情况。
4、打开排污阀,进行排污。
5、检查引压管线是否有污垢,清洗管道。
6、输出信号线路电压、电流如果正常,进行手动调校,或者使用手操器进行调校。
7、如不存在上述情况,通知调度与工艺操作人员协商,检查工艺,寻找是否存在引起变化的原因,如工艺操作正常,更换变送器。
8、运行记录、故障处理记录、检修记录、校准记录、零部件更换记录应准确无误。
9、系统原理图和接线图应完整、准确。
10、当无法查明故障原因或故障无法排除时,及时与车间领导联系。
八、压力变送器应急预案1、仪表操作人员接到通知后应在十分钟内到达事件发生现场。
2、观察历史曲线记录,是否存在突变,为零或趋于最大,检查信号线路输入电压是否正常,是否存在短路或断路情况。
3、检查引压管线是否有污垢,清洗管道。
4、打开排污阀,进行排污。
5、输出信号线路电压、电流如果正常,进行手动调校,或者使用手操器进行调校。
6、如不存在上述情况,通知调度与工艺操作人员协商,检查工艺,寻找是否存在引起变化的原因,如工艺操作正常,更换变送器。
7、运行记录、故障处理记录、检修记录、校准记录、零部件更换记录应准确无误。
8、系统原理图和接线图应完整、准确。
9、当无法查明故障原因或故障无法排除时,及时与车间领导联系。
九、转子流量计应急预案1、仪表操作人员接到通知后应在十分钟内到达事件发生现场。
2、观察历史曲线记录,是否存在突变,为零或趋于最大,检查信号线路是否存在短路或断路情况。
3、检查管线是否有污垢,卡住转子,清洗管道。
4、如不存在上述情况,通知调度与工艺操作人员协商,检查工艺,寻找是否存在引起变化的原因。
5、运行记录、故障处理记录、检修记录、校准记录、零部件更换记录应准确无误。
6、系统原理图和接线图应完整、准确。
7、当无法查明故障原因或故障无法排除时,及时与车间领导联系。
十、电磁流量计应急预案1、仪表操作人员接到通知后应在十分钟内到达事件发生现场。
2、观察历史曲线记录,是否存在突变,为零或趋于最大。
3、检查线路电压、电流是否正常,是否存在短路或断路情况。
4、检查管线是否有污垢,清洗管道。
5、如不存在上述情况,通知调度与工艺操作人员协商,检查工艺,寻找是否存在引起变化的原因,如工艺操作正常,更换为备用流量计管线或开旁路。
6、运行记录、故障处理记录、检修记录、校准记录、零部件更换记录应准确无误。
7、系统原理图和接线图应完整、准确。
8、当无法查明故障原因或故障无法排除时,及时与车间领导联系。
十一、温度开关、压力开关应急预案1、仪表操作人员接到通知后应在十分钟内到达事件发生现场。
2、在检查温度、压力开关时必须提前通知生产车间,并确定没有和其他仪表设备连锁才能进行操作。
3、观察历史曲线记录,是否存在突变,为零或趋于“1”。
4、检查信号线路是否存在短路或断路情况。
5、检查有无24VDC输入,如果没有电压,检查回路保险。
6、如不存在上述情况,通知调度与工艺操作人员协商,检查工艺,寻找是否存在温度开关、压力开关引起变化的原因,如工艺正常,应更换温度开关、压力开关。
7、运行记录、故障处理记录、检修记录、校准记录、零部件更换记录应准确无误。
8、系统原理图和接线图应完整、准确。
9、当无法查明故障原因或故障无法排除时,及时与车间领导联系。
十二、调节阀应急预案1、仪表操作人员接到通知后应在两分钟内到达事件发生现场。
2、观察历史曲线记录,阀位输出信号是否存在突变,为零或趋于最大。
3、检查线路电压、电流是否正常,是否存在短路或断路情况。
4、对调节阀通电供气后,在DCS中手动给出阀门的开度,与现场阀位相对应,两者应具有相同的开度指示,在DCS中将调节阀置于自动状态,更改设定值,阀位应随之开或关。
最后一步在现场对调节阀进行气关或气开,断电和送电试验,记录阀门在通断电和通断气的状态,以备故障时使用。
5、阀位输出信号线路电压、电流如果正常,进行手动调校,或者使用手操器进行自动调校。
6、如不存在上述情况,通知调度与工艺操作人员协商,开旁路阀,手动操作。
7、运行记录、故障处理记录、检修记录、校准记录、零部件更换记录应准确无误。
8、系统原理图和接线图应完整、准确。