基于PLC可控硅的温度闭环控制系统设计
基于PLC温度控制系统设计

编号: 毕业论文(设计)题目基于PLC温度控制系统的设计指导教师学生姓名学号专业自动化教学单位机电工程学院毕业论文(设计)开题报告书德州学院毕业论文(设计)中期检查表院(系):机电工程学院专业:自动化 2014 年 4月 7日目录1引言 (2)1.1课题背景以及研究的目的、意义 (2)1.2温控系统的现状 (2)1.3项目研究内容 (3)2系统硬件设计 (4)2.1 PLC选择 (4)2.2 硬件电路设计 (7)3 系统软件设计 (13)3.1 编程与通信软件的使用 (14)3.2 程序设计 (14)3.3 系统程序流程图 (15)3.4 控制系统控制程序的开发 (16)4系统的仿真和运行测试 (25)4.1 组态王的运行 (25)4.2 实时曲线的观察 (26)4.3 分析历史趋势曲线 (27)4.4 编辑数据的报表 (27)4.5系统稳定性测试及最终评估 (27)参考文献 (29)谢辞 (30)附录一三菱FX系列PLC指令一览表 (30)附录二系统程序(梯形图) (32)基于PLC温度控制系统的设计(德州学院机电工程学院,山东德州253023)摘要:本文主要介绍了基于日本三菱公司FX2N系列的可编程控制器从而进行硬件设计和软件设计,进而完成了一个完整的关于炉温控制系统的设计方案。
该设计编程时调用了PID控制模块,使得程序更为简洁,运行速度更为理想。
在软件上,则是通过利用比较新型的三菱专用软件三菱(PLC)GX Developer 8.86Q,实现控制系统的实时监控、数据的实时采样与处理。
实验证明,此系统具有快、准、稳等优点,在工业温度控制领域能够广泛应用。
关键词:温度控制;可编程控制器;三菱FX2N;PID控制模块1引言1.1课题背景以及研究的目的、意义进入21世纪后,我国社会的各项发展突飞猛进,世界的技术更是日新月异,竞争也愈演愈烈,传统的人工的操作已不能满足于目前的制造业前景,也无法保证高质量的要求,更不能提升高新技术企业的形象。
基于PLC的水温控制系统设计

自动化技术0 前言温度是一种最基本的环境参数,它不仅与我们的日常生活息息相关,同时在工业生产、农业生产过程中,许许多多农产品的生长环境、工业产品的加工工艺流程都需要实时进行温度检测,才能生产出合格的产品。
为保证产品的质量,要求我们对温度进行精确控制。
例如:在某水箱水温控制系统中,控制要求如下:水箱水温由加热器控制,其功率为2kW;水温要求控制在50℃~60℃之间,当温度低于50℃时,启动加热器;当水温高于60℃时,关闭加热器,实现温度的自动调节与控制。
1 控制系统设计方案温度测量可采取不同的方式,如生活中的温度计,利用水银热胀冷缩原理,可反映出实时的天气温度。
在工业控制中,不仅要求进行温度的检测,而且要求能对产品的生产环境温度进行控制,使温度保持在要求的范围内,实现自动调节。
基于此,笔者在水箱水温控制系统设计中,采用基于可编程逻辑控制器(PLC)的温度测量与控制模块,可达到精确控制、灵活调节的效果。
2 控制系统硬件设计该系统硬件主要由西门子S7-200 SMART SR40PLC、模拟量扩展模块EM AT04、K型热电偶传感器、加热电阻丝、交流接触器KM和电源开关等组成。
在系统设计中需要解决两个问题:一是如何实现温度的测量?二是如何使水箱水温保持在50o C-60 o C之间?■2�1 温度测量电路首先温度测量采用应用广泛的K型热电偶传感器,它是一种自发电式传感器,工作时不需要外加电源。
K型热电偶测量温度范围在0℃~1200℃之间,具有良好的线性热电特性曲线;同时因为K型热电偶传感器具有造价低、测量精确度较高、测量温度范围广等特点。
这里选择型号为MT 的K型热电偶,其测量温度范围为0℃~600℃,满足本项目的水温测量要求。
在温度测量时,考虑到温度是一个随时间连续变化的模拟信号,经温度传感器转换的电信号也是一个模拟量,它不能作为输入信号直接与PLC相连,需要经过模-数转换,才能接入PLC的输入端。
(整理)基于PLC的温度控制闭环系统.

1 绪论1.1 课题背景随着现代工业的逐步发展,在工业生产中,温度、压力、流量和液位是四种最常见的过程变量。
其中,温度是一个非常重要的过程变量。
例如:在冶金工业、化工工业、电力工业、机械加工和食品加工等许多领域,都需要对各种加热炉、热处理炉、反应炉和锅炉的温度进行控制[1]。
这方面的应用大多是基于单片机进行PID控制,然而单片机控制的DDC系统软硬件设计较为复杂,特别是涉及到逻辑控制方面更不是其长处,然而PLC在这方面却是公认的最佳选择。
随着PLC功能的扩充在许多PLC控制器中都扩充了PID控制功能,因此在逻辑控制与PID控制混合的应用场所中采用PLC控制是较为合理的,通过采用PLC来对它们进行控制不仅具有控制方便、简单和灵活性大的优点,而且可以大幅度提高被测温度的技术指标,从而能够大大提高产品的质量和数量。
因此,PLC对温度的控制问题是一个工业生产中经常会遇到的控制问题。
这也正是本课题所重点研究的内容。
1.2 研究的主要内容本课题的研究内容主要有:1)温度的检测;2)采用PLC进行恒温控制;3)PID算法在PLC中如何实现;4)PID参数对系统控制性能的影响;5)温控系统人机界面的实现。
2 基于PLC的炉温控制系统的硬件设计2.1系统控制要求本PLC温度控制系统的具体指标要求是:对加热器加热温度调整范围为0℃—150℃,温度控制精度小于3℃,系统的超调量须小于15%。
软件设计须能进行人机对话,考虑到本系统控制对象为电炉,是一个大延迟环节,且温度调节范围较宽,所以本系统对过渡过程时间不予要求。
2.2系统设计思路根据系统具体指标要求,可以对每一个具体部分进行分析设计。
整个控制系统分为硬件电路设计和软件程序设计两部分。
系统硬件框图结构如图所示:图2.1系统硬件框图被控对象为炉内温度,温度传感器检测炉内的温度信号,经温度变送器将温度值转换成0~10V的电压信号送入PLC模块。
PLC把这个测量信号与设定值比较得到偏差,经PID运算后,发出控制信号,经调压装置输出交流电压用来控制电加热器的端电压,从而实现炉温的连续控制。
基于PLC的温度控制系统的设计
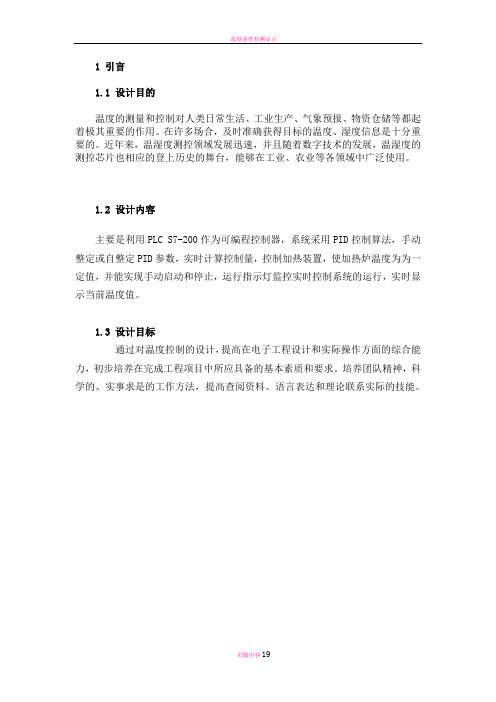
1 引言1.1 设计目的温度的测量和控制对人类日常生活、工业生产、气象预报、物资仓储等都起着极其重要的作用。
在许多场合,及时准确获得目标的温度、湿度信息是十分重要的。
近年来,温湿度测控领域发展迅速,并且随着数字技术的发展,温湿度的测控芯片也相应的登上历史的舞台,能够在工业、农业等各领域中广泛使用。
1.2 设计内容主要是利用PLC S7-200作为可编程控制器,系统采用PID控制算法,手动整定或自整定PID参数,实时计算控制量,控制加热装置,使加热炉温度为为一定值,并能实现手动启动和停止,运行指示灯监控实时控制系统的运行,实时显示当前温度值。
1.3 设计目标通过对温度控制的设计,提高在电子工程设计和实际操作方面的综合能力,初步培养在完成工程项目中所应具备的基本素质和要求。
培养团队精神,科学的、实事求是的工作方法,提高查阅资料、语言表达和理论联系实际的技能。
2 系统总体方案设计2.1 系统硬件配置及组成原理2.1.1 PLC型号的选择本温度控制系统采用德国西门子S7-200 PLC。
S7-200 是一种小型的可编程序控制器,适用于各行各业,各种场合中的检测、监测及控制的自动化。
S7-200系列的强大功能使其无论在独立运行中,或相连成网络皆能实现复杂控制功能。
因此S7-200系列具有极高的性能/价格比。
2.1.2 PLC CPU的选择S7-200 系列的PLC有CPU221、CPU222、CPU224、CPU226等类型。
S7-200PLC 硬件系统的组成采用整体式加积木式,即主机中包括定数量的I/O端口,同时还可以扩展各种功能模块。
S7-200PLC由基本单元(S7-200 CPU模块)、扩展单元、个人计算机(PC)或编程器,STEP 7-Micro/WIN编程软件及通信电缆等组成。
表2.1 S7-200系列PLC中CPU22X的基本单元本设计采用的是CUP226。
它具有24输入/16输出共40个数字量I/O点。
PLC的温度控制系统的设计与实现—关于S7300模拟量处理及闭环控制

电压,电 流 (对称的 )
电压,电 流 (不对称 的)
超限
-27648到+27648 可转换为对称的电压或电流的额定范围 : • ± 10V • ± 20mA
0 到+27648 可转换为不对称的电压或电流的额定范围 : • 0 到 10V • 1 到 5V • 0 到 20mA • 4 到 20mA
可以在更短的时间间隔内刷新。
PLC的温度控制系统的设计与实现— 关于S7300模拟量处理及闭环控制
PLC的温度控制系统的设计与实现— 关于S7300模拟量处理及闭环控制
• 输出类型 点击该选项以显示和选择可能的输出类型(例如,电流)。确 认在未连接的输出通道上没有电压,你应该不激活它们(输出类型不激活) 并使它们开路。这也降低循检时间。
• 结果存储器 模数转换的结果存储在结果存储器中,并一直保持到被一个新 的转换值所覆盖。可用“L PIW…”指令来访问模数转换的结果。
• 模拟输出 传递指令“T PQW...” 用来向模拟输出模板中写模拟量的数值 (由用户程序计算所得),该数值由模板中的DAC(数模转换器)变换为标 准的模拟信号
PLC的温度控制系统的设计与实现— 关于S7300模拟量处理及闭环控制
IN输入端的模拟值可直接从模板上读取或从一个 INT格式的数据接口上读取。
LO_LIM (下界) 和HI_LIM (上界) 输入参数用于定义规范化的物理量范围。本例 中,转换为0 到50 0升范 围。
规范化后 的值( 实际物 理量) 以实数 格式存 储在 O U T输 出端 (LO_LIM <= OUT <= HI_LIM) 。
• 诊断中断 当故障出现时,模板触发CPU的诊断中断 。有关信息被记录在CPU的诊断缓 冲区中并立即处理诊断中断组织块 OB82。在该块编程故障出现时需要的反应。模拟量 模板可以识别哪些故障由模板类型决定。
基于PLC的温度控制系统的设计
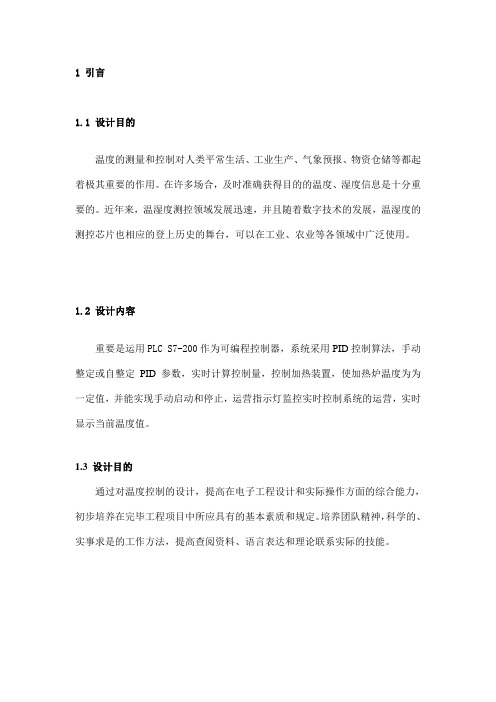
1 引言1.1 设计目的温度的测量和控制对人类平常生活、工业生产、气象预报、物资仓储等都起着极其重要的作用。
在许多场合,及时准确获得目的的温度、湿度信息是十分重要的。
近年来,温湿度测控领域发展迅速,并且随着数字技术的发展,温湿度的测控芯片也相应的登上历史的舞台,可以在工业、农业等各领域中广泛使用。
1.2 设计内容重要是运用PLC S7-200作为可编程控制器,系统采用PID控制算法,手动整定或自整定PID参数,实时计算控制量,控制加热装置,使加热炉温度为为一定值,并能实现手动启动和停止,运营指示灯监控实时控制系统的运营,实时显示当前温度值。
1.3 设计目的通过对温度控制的设计,提高在电子工程设计和实际操作方面的综合能力,初步培养在完毕工程项目中所应具有的基本素质和规定。
培养团队精神,科学的、实事求是的工作方法,提高查阅资料、语言表达和理论联系实际的技能。
2 系统总体方案设计2.1 系统硬件配置及组成原理2.1.1 PLC型号的选择本温度控制系统采用德国西门子S7-200 PLC。
S7-200 是一种小型的可编程序控制器,合用于各行各业,各种场合中的检测、监测及控制的自动化。
S7-200系列的强大功能使其无论在独立运营中,或相连成网络皆能实现复杂控制功能。
因此S7-200系列具有极高的性能/价格比。
2.1.2 PLC CPU的选择S7-200 系列的PLC有CPU221、CPU222、CPU224、CPU226等类型。
S7-200PLC 硬件系统的组成采用整体式加积木式,即主机中涉及定数量的I/O端口,同时还可以扩展各种功能模块。
S7-200PLC由基本单元(S7-200 CPU模块)、扩展单元、个人计算机(PC)或编程器,STEP 7-Micro/WIN编程软件及通信电缆等组成。
表2.1 S7-200系列PLC中CPU22X的基本单元本设计采用的是CUP226。
它具有24输入/16输出共40个数字量I/O点。
《基于PLC的环形炉温度控制系统设计与应用》范文

《基于PLC的环形炉温度控制系统设计与应用》篇一一、引言随着工业自动化技术的不断发展,温度控制系统的设计与应用在工业生产中显得尤为重要。
环形炉作为许多工业生产过程中的关键设备,其温度控制系统的稳定性和精确性直接影响到产品的质量和生产效率。
因此,基于PLC的环形炉温度控制系统应运而生,本文将介绍其设计思路和应用效果。
二、系统设计1. 系统构成基于PLC的环形炉温度控制系统主要由PLC控制器、温度传感器、执行机构、人机界面等部分组成。
其中,PLC控制器作为系统的核心,负责接收温度传感器的信号,根据设定的控制算法输出控制信号,驱动执行机构进行温度调节。
2. PLC控制器设计PLC控制器是整个系统的“大脑”,其设计应考虑到系统的实时性、稳定性和可扩展性。
首先,应选择合适的PLC型号,根据环形炉的规模和工艺要求,确定I/O点的数量和类型。
其次,编写控制程序,实现温度的实时监测、报警、自动调节等功能。
此外,还应考虑到系统的故障诊断和保护功能,确保系统的稳定运行。
3. 温度传感器和执行机构的选择温度传感器是测量环形炉温度的关键部件,应选择具有高精度、高稳定性的传感器。
执行机构则是根据PLC控制器的指令进行温度调节的部件,常见的有电动调节阀、电动执行器等。
在选择时,应考虑到其响应速度、调节精度和可靠性等因素。
4. 人机界面设计人机界面是操作人员与系统进行交互的界面,应设计得简洁、直观、易操作。
通过人机界面,操作人员可以实时监测环形炉的温度、设定温度目标值、查看报警信息等。
此外,还应具备历史数据查询、报表生成等功能,方便操作人员进行生产管理和数据分析。
三、系统应用基于PLC的环形炉温度控制系统在实际应用中取得了显著的效果。
首先,该系统具有较高的控制精度和稳定性,能够实时监测环形炉的温度,并根据设定的控制算法自动调节执行机构,使温度保持在设定范围内。
其次,该系统具有丰富的功能,如温度报警、历史数据查询、报表生成等,方便操作人员进行生产管理和数据分析。
《2024年基于PLC的环形炉温度控制系统设计与应用》范文

《基于PLC的环形炉温度控制系统设计与应用》篇一一、引言随着工业自动化技术的不断发展,温度控制系统的设计与应用在工业生产中显得尤为重要。
环形炉作为许多工业生产过程中的关键设备,其温度控制系统的稳定性和精确性直接影响到产品的质量和生产效率。
本文将介绍一种基于PLC的环形炉温度控制系统,探讨其设计原理、系统架构和应用实例,以期为相关领域的研究和应用提供参考。
二、系统设计1. 设计原理基于PLC的环形炉温度控制系统采用先进的控制算法和传感器技术,实现对环形炉内温度的实时监测和精确控制。
系统通过PLC控制器采集温度传感器的数据,根据预设的控制策略调整加热元件的功率,从而实现对环形炉内温度的精确控制。
2. 系统架构系统架构主要包括PLC控制器、温度传感器、加热元件、执行机构和人机界面等部分。
其中,PLC控制器作为核心部件,负责采集温度传感器的数据、执行控制策略、输出控制信号等工作。
温度传感器用于实时监测环形炉内的温度,将温度信号转换为电信号传输给PLC控制器。
加热元件根据PLC控制器的指令调整功率,以实现对环形炉内温度的调节。
执行机构包括电机、阀门等,用于实现系统的自动化控制。
人机界面用于显示系统的工作状态、温度值、控制参数等,方便操作人员进行监控和调整。
三、控制策略系统的控制策略采用先进的PID控制算法,通过对温度传感器的实时数据进行采集和处理,计算出实际的温度值与设定值之间的偏差,然后根据偏差大小调整加热元件的功率,以实现对环形炉内温度的精确控制。
此外,系统还具有自动调节、手动调节和故障诊断等功能,以满足不同生产需求和应对突发情况的能力。
四、应用实例以某钢铁企业的环形炉为例,该企业采用基于PLC的环形炉温度控制系统对环形炉进行温度控制。
系统通过实时监测环形炉内的温度,根据预设的控制策略调整加热元件的功率,以实现对环形炉内温度的精确控制。
在应用过程中,系统表现出了良好的稳定性和精确性,有效提高了产品的质量和生产效率。
- 1、下载文档前请自行甄别文档内容的完整性,平台不提供额外的编辑、内容补充、找答案等附加服务。
- 2、"仅部分预览"的文档,不可在线预览部分如存在完整性等问题,可反馈申请退款(可完整预览的文档不适用该条件!)。
- 3、如文档侵犯您的权益,请联系客服反馈,我们会尽快为您处理(人工客服工作时间:9:00-18:30)。
摘要在许多现代工业生产中,温度控制都是要解决的问题之一,对于无需人力控制的领域,我们需要自动控制。
随着电子技术的发展, 可编程序控制器(PLC)已经由原来简单的逻辑量控制, 逐步具有了计算机控制系统的功能。
PLC具有通用性强、使用方便、适应面广、可靠性高、抗干扰能力强、编程简单等特点。
PLC 在工业自动化控制特别是顺序控制中的地位,在可预见的将来,是无法取代的。
本文提出了采用可编程控制器和可控硅组成一个比较简单、通用的温度控制系统。
PLC是温度控制的主控核心,采用PID算法,运用PLC梯形图编程语言进行编程,实现温度的自动控制。
可编程控制器的一个优势就是可以很方便的改写其中的程序以满足不同的控制系统,尤其在控制系统需要改进时优势更加明显。
文章分别就控制系统的基本工作原理,特殊模块的选型、PLC配置、等几方面进行阐述。
通过提高温度控制系统具有响应快、稳定性好、可靠性高、控制精度好等特点,对工业控制有现实意义。
关键词: 温度控制 PLC PID 可控硅闭环系统AbstractIn many modern industrial production, temperature control is one of problems to solve, without human control on the field, we need automatic control. With the development of electronic technology, programmable logic controller (PLC) have by original simple logical quantity control, gradually with a computer control system function. PLC has strong commonality, use convenient, wide adaptability, high reliability, strong anti-jamming capability, programming of simple features. PLC in industrial automation control especially the status of sequence control in the foreseeable future, is irreplaceable.This paper proposes using the programmable controller and SCR form a relatively simple, general temperature control system. PLC is the main controlling of temperature control, PID algorithm, core using PLC ladder-diagram programming programming language, realize temperature automatic control. One of the strengths of the programmable controller is very convenient rewrite the program to meet different control system, especially in the control system that needs to improve more obvious when advantage.Articles respectively basic working principle of the control system, special module selection, PLC configuration, wait a few aspects. By raising the temperature control system has a fast response, good stability, high reliability, control precision is good wait for a characteristic, and the industrial control have realistic significance.Keywords :temperature-control PLC PID SCR closed-loop system目录摘要 (I)Abstract (II)1 绪论.............................................................................................................................. - 1 -1.1 课题背景及研究目的 ......................................................................................... - 1 -1.2 国内外的研究状况.............................................................................................. - 1 -1.3 课题研究内容....................................................................................................... - 2 -1.4 课题研究方法....................................................................................................... - 3 -2 PLC控制系统的硬件组成 .................................................................................... -3 -2.1 可编程控制器基础.............................................................................................. - 4 -2.1.1 可编程序控制器的概述................................................................................ - 4 -2.1.2 可编程控制器的组成和工作原理................................................................ - 4 -2.1.3 可编程控制器的分类及特点........................................................................ - 7 -3 PLC控制系统的硬件设计 .................................................................................... - 8 -3.1 PLC控制系统设计的基本原则和步骤........................................................... - 8 -3.1.1 PLC控制系统设计的基本原则..................................................................... - 8 -3.1.2 PLC控制系统设计的一般步骤..................................................................... - 8 -3.1.3 PLC程序设计的一般步骤............................................................................. - 9 -3.2 PLC的选型和硬件配置.................................................................................. - 10 -3.2.1 PLC型号的选择........................................................................................... - 10 -3.2.2 FX2N的功能简介.......................................................................................... - 11 -3.2.3 温度检测模块FX2N-4AD-TC........................................................................ - 11 -3.2.4 电加热控制器.............................................................................................. - 13 -3.3 系统整体设计方案和电器接线图................................................................. - 15 -3.4 PLC控制器的设计............................................................................................. - 16 -3.4.1 PID控制的原理和特点............................................................................... - 16 -3.4.2 PID控制的参数整定................................................................................... - 17 -4 PLC控制系统的软件设计 .................................................................................. - 20 -4.1 PLC程序设计的方法 ........................................................................................ - 20 -4.2 编程软件FXGP_WIN-C概述与简介 .............................................................. - 21 -4.3.1 PLC编程指令............................................................................................... - 21 -4.3.2 控制程序的编写.......................................................................................... - 23 -5 系统调试 ...................................................................................................................... - 27 -5.1 系统软件调试..................................................................................................... - 27 -5.2 系统硬件调试..................................................................................................... - 27 -5.3 温度系统特性..................................................................................................... - 27 -6 结论................................................................................................................................. - 30 - 附录1..................................................................................................................................... - 31 - 附录2..................................................................................................................................... - 32 - 致谢.................................................................................................................................... - 33 - 【参考文献】.................................................................................................................... - 34 -1 绪论1.1 课题背景及研究目的温度控制的应用领域是很广泛的,大到工业生产、航空航天,小到我们的日常生活。