对高炉炼铁系统几个节能技术的认识PPT课件
合集下载
高炉炼铁基本原理及工艺(PPT36页)

7
3.高炉用燃料焦碳:
①主要作用: 作为高炉热量主要来源的60~80%,其它的由热风提供 提供还原剂C、CO 料柱骨架,保证透气性、透液性
②质量要求: 含炭量:C↑灰份↓→→渣量↓、强度↑、反应性↓ →→焦比↓ 含S量:生铁中[S]80%±来源于焦碳 强 度:M40、M10
③粒度组成: 焦丁的利用及混装过渡区的问题
6
(3)熔剂的质量要求
①碱性氧化物含量(CaO+MgO≥52%) 概念:石灰石有效熔剂性
CaO(有效)=CaO(石灰石)-R×SiO2(石灰石)
②S、P↓ S(0.01~0.08%),P(0.001~0.03%)
③减少CaCO3入炉: 原因:a. 高温分解吸热,是高炉炉温下降 b. CO2+C=2CO,消耗焦炭 c. CO2会冲淡CO浓度 造成焦比K增加。
(三)烧结过程的特点
1.燃料燃烧需空气过剩,过剩系数α=1.4~1.5(燃料分布较 稀疏)
2.一般情况下烧结保持弱氧化气氛(金属化烧结除外) 3.烧结过程存在自动蓄热作用(可以考虑采用上高下低的分
层配炭) 4.存在传热速度与燃烧速度的同步问题 5.存在如何减少“过湿”现象的问题 6.存在有害杂质S的去除问题(S由易去除S化物转化为硫酸
低水原则) 8.双层烧结:二次点火,设备复杂 9.料面插孔烧结:提高透气性
15
四、高炉冶炼基本原理
(一)高炉还原过程 (二)造渣与脱S (三)风口前C的燃烧 (四)炉料与煤气运动 (五)高炉能量利用
16
高炉的五大系统
17
高炉炉型
18
(一)高炉还原过程
1.高炉炉内状况
19
(1)块状带:矿焦保持装料时的分层状态,与布料形式及粒 度有关,占BF总体积60%±(200~1100℃)
3.高炉用燃料焦碳:
①主要作用: 作为高炉热量主要来源的60~80%,其它的由热风提供 提供还原剂C、CO 料柱骨架,保证透气性、透液性
②质量要求: 含炭量:C↑灰份↓→→渣量↓、强度↑、反应性↓ →→焦比↓ 含S量:生铁中[S]80%±来源于焦碳 强 度:M40、M10
③粒度组成: 焦丁的利用及混装过渡区的问题
6
(3)熔剂的质量要求
①碱性氧化物含量(CaO+MgO≥52%) 概念:石灰石有效熔剂性
CaO(有效)=CaO(石灰石)-R×SiO2(石灰石)
②S、P↓ S(0.01~0.08%),P(0.001~0.03%)
③减少CaCO3入炉: 原因:a. 高温分解吸热,是高炉炉温下降 b. CO2+C=2CO,消耗焦炭 c. CO2会冲淡CO浓度 造成焦比K增加。
(三)烧结过程的特点
1.燃料燃烧需空气过剩,过剩系数α=1.4~1.5(燃料分布较 稀疏)
2.一般情况下烧结保持弱氧化气氛(金属化烧结除外) 3.烧结过程存在自动蓄热作用(可以考虑采用上高下低的分
层配炭) 4.存在传热速度与燃烧速度的同步问题 5.存在如何减少“过湿”现象的问题 6.存在有害杂质S的去除问题(S由易去除S化物转化为硫酸
低水原则) 8.双层烧结:二次点火,设备复杂 9.料面插孔烧结:提高透气性
15
四、高炉冶炼基本原理
(一)高炉还原过程 (二)造渣与脱S (三)风口前C的燃烧 (四)炉料与煤气运动 (五)高炉能量利用
16
高炉的五大系统
17
高炉炉型
18
(一)高炉还原过程
1.高炉炉内状况
19
(1)块状带:矿焦保持装料时的分层状态,与布料形式及粒 度有关,占BF总体积60%±(200~1100℃)
高炉炼铁安全ppt课件

四、炼铁常见事故分析及预防
2、物体打击 大锤、榔头使用不当;高处物件坠落;清理渣铁壕、板结 物料时发生崩块击中人员,尤其是眼睛;使用卡机卸风口、中 套时突然断裂,游锤飞出击打伤人。 此类事故的预防目前主要以软措施为主,如做好工器具的检查 确认、制定科学的安全防范措施和作业标准、尽量减少作业时 间与频次等。有条件的,可以自动化的机械设备(如使用挖掘 机进行渣铁壕解体,使用专用装置更换风口等)代替人工操作 或将人员的操作控制设置在远端进行计算机控制,从空间上实 现人机分离,但需要先进的技术与生产力做后盾。
并 罐 式 无 钟 炉 顶
串 罐 式 无 钟 炉 顶
一、炼铁厂除高炉本体外的几个系统
• 3.送风系统 主要包括高炉鼓风机和热风炉(含助燃风机、 冷风管道、热风管道、煤气管道、助燃空气管 道、烟气管道和烟囱等)。
• 4.煤气除尘系统 一般包括煤气上升管、煤气下降管、重力除 尘器(或旋风除尘器)、洗涤塔、文氏管、脱 水器等。高压操作的高炉还有高压阀组。
二、炼铁生产的主要危险因素
• 炼铁生产工艺设备复杂、作业种类多、 作业环境差,劳动强度大。 • 炼铁生产过程中存在的主要危险因素有: • 高温辐射、铁水和熔渣喷溅与爆炸、高 炉煤气中毒、高炉煤气燃烧爆炸、煤粉 爆炸、烟尘、噪声、机具及车辆伤害、 高处作业危险等。
三、炼铁生产的主要事故类别和 原因
熔剂、燃料等 球磨机高炉来自炼工艺流程图焦碳
混合机
石灰石 选 球 盘 除 尘 器
洗 涤 塔
天然矿
竖
文 氏 管
脱 水 器
炉
带 冷
除 尘 器
料
仓
烟
助 燃 风
高 炉
囱 热 风
热 风 炉
球磨机 鼓 风 机 集 煤 罐 贮 煤 罐 喷 吹 罐
炼铁生产过程中的能源利用与节能措施

采用节能环保设备,如 采用节能型加热炉、节 能型鼓风机等
加强能源管理,建立能 源管理体系,提高能源 利用效率
推广应用可再生能源, 如太阳能、风能等,降 低对传统能源的依赖
宝钢集团:采用高效节能技术,如高炉炉顶煤气回收、转炉余热回收等,降 低能源消耗。
首钢集团:通过优化生产工艺,减少能源浪费,如采用连续铸造、热装热送 等工艺,提高能源利用效率。
低碳环保技术的发展趋势: 高效、节能、环保
低碳环保技术在炼铁生产 过程中的应用:优化工艺 流程,提高能源利用效率
低碳环保技术在炼铁生产 过程中的推广:政府政策
支持,企业积极响应
循环经济的概念:减少资源浪费, 提高资源利用效率
炼铁生产过程中的节能技术发展趋 势:提高能源利用效率,减少能源 消耗
添加标题
余热回收效果:可以提高能源利用率,降低生产成本,减少环境污染
余热回收应用:广泛应用于钢铁、化工、水泥等行业
废气来源:高炉、转炉、 焦炉等生产设备
回收方法:采用吸附法、 催化燃烧法、生物过滤
法等
废气成分:主要包 括CO、CO2、 NOx、SO2等有 害气体
回收效果:减少废气 排放,降低环境污染,
提高能源利用率
能源利用效率的重要性:提高能源利用效率是降低生产成本、减少环境污染 的关键因素
炼铁生产过程中的能源利用:主要包括煤炭、焦炭、天然气等能源的利用
提高能源利用效率的措施:采用先进的生产工艺和技术,优化能源管理,提 高能源利用效率
节能措施的效果:降低能源消耗,减少环境污染,提高经济效益
高炉炉顶煤气 回收技术:回 收高炉炉顶煤 气,减少能源
鞍钢集团:推广节能减排技术,如采用干熄焦、高炉煤气发电等,降低能源 消耗,减少环境污染。
高炉炼铁概述PPT课件

过程
①还原过程 实现矿石中金属元素(主要是Fe)和氧 元素的化学分离; ② 造渣过程 实现已还原的金属与脉石的熔融态机械 分离; ③ 传热及渣铁反应过程 实现成分及温度均合格的液态铁水。
23
1. 1高炉原料
高炉原料
—高炉炼铁—
铁矿石
熔剂
其它含铁代用品
天然块矿 人造富矿
烧结矿 球团矿
碱性熔剂―石灰, 石灰石,白云石 酸性熔剂― 硅石 特殊熔剂― 萤石
4
1.1钢铁工业概况
—高炉炼铁—
1.1.1国民经济中钢铁工业的地位
评价一个国家的工业发达程度
工业化水平
工业生产所占比重
工业机械化、 自动化程度
工业化水平的标志
劳动生产率↑ 需要大量机械设备
国民生活水准
交
市
民
生
通
政
用
活
工
设
住
用
具
施
宅
品
需要大量基础材料
钢铁产品
5
➢价格低廉有较高的强度和韧性 ➢易于加工制造 ➢所需原料资源丰富 ➢ 冶炼工艺成熟、效率高
13 、修风率
定义:高炉修风时间占规定作业时间的百分数。
14、炉龄
定义:从高炉点火开炉到停炉大修,或高炉相邻两次
的大修之间的冶炼时间。
34
第一章 思考题
—高炉炼铁—
1、试述3种钢铁生产工艺的特点。 2、简述高炉冶炼过程的特点及三大主要过程。 3、画出高炉本体图,并在其图上标明四大系统。 4、归纳高炉炼铁对铁矿石的质量要求。 5、试述焦炭在高炉炼铁中的三大作用及其质量要求。 6、试述高炉喷吹用煤粉的质量要求。 7、熟练掌握高炉冶炼主要技术经济指标的表达方式。
①还原过程 实现矿石中金属元素(主要是Fe)和氧 元素的化学分离; ② 造渣过程 实现已还原的金属与脉石的熔融态机械 分离; ③ 传热及渣铁反应过程 实现成分及温度均合格的液态铁水。
23
1. 1高炉原料
高炉原料
—高炉炼铁—
铁矿石
熔剂
其它含铁代用品
天然块矿 人造富矿
烧结矿 球团矿
碱性熔剂―石灰, 石灰石,白云石 酸性熔剂― 硅石 特殊熔剂― 萤石
4
1.1钢铁工业概况
—高炉炼铁—
1.1.1国民经济中钢铁工业的地位
评价一个国家的工业发达程度
工业化水平
工业生产所占比重
工业机械化、 自动化程度
工业化水平的标志
劳动生产率↑ 需要大量机械设备
国民生活水准
交
市
民
生
通
政
用
活
工
设
住
用
具
施
宅
品
需要大量基础材料
钢铁产品
5
➢价格低廉有较高的强度和韧性 ➢易于加工制造 ➢所需原料资源丰富 ➢ 冶炼工艺成熟、效率高
13 、修风率
定义:高炉修风时间占规定作业时间的百分数。
14、炉龄
定义:从高炉点火开炉到停炉大修,或高炉相邻两次
的大修之间的冶炼时间。
34
第一章 思考题
—高炉炼铁—
1、试述3种钢铁生产工艺的特点。 2、简述高炉冶炼过程的特点及三大主要过程。 3、画出高炉本体图,并在其图上标明四大系统。 4、归纳高炉炼铁对铁矿石的质量要求。 5、试述焦炭在高炉炼铁中的三大作用及其质量要求。 6、试述高炉喷吹用煤粉的质量要求。 7、熟练掌握高炉冶炼主要技术经济指标的表达方式。
《高炉炼铁简述》PPT课件

构建高效率、低消耗、低成本、低排放生产体系
LOREM IPSUM 节能减排 DOLOR LOREM IPSUM 高效低耗 DOLOR
LOREM 循环经 IPSUM 济 DOLOR
清洁环保
低碳冶炼
安全长寿
5/11/2019
宝钢4号高炉
结束语
高炉炼铁的未来
大型化是高炉发展的一个主要方向。目前,大型高炉基本分布在欧亚地区,其 中日本最多,北美地区相对较少。全球2000立方米以上的中大型高炉共有107 座。与小高炉相比,大型高炉的劳动生产率成倍的增长。据统计,我国炼铁高 炉总数已达3228座,其中容积小于100立方米的高炉占总数的93%,劳动生产率 低,污染环境严重。随着我国加入WTO,市场竞争更趋激烈,高炉大型化大概 也是必然的趋势。
热制度:根据冶炼条件和所炼生铁品种的需要,在争取最低焦比的前 提下,选择并控制均匀而热量充沛的炉温(通常包括生铁含硅量和渣 铁温度两方面含义)。
3.高炉的基本操作制度
冷却制度:冷却器结构一般是将钢管铸入生铁铸体中,或直接用铜或 生铁铸成腔室型的构件,冷却器内的钢管或腔室通过冷却介质水时,将 与其接触的炉衬砌体内的热量带出,达到冷却降温的作用。冷却器固定 在炉壳内,直接冷却炉衬的外表,使炉衬内表面温度降低,并形成渣皮, 用于保护炉衬或代替炉衬工作,使高炉长寿。
高炉内部工作空间的形状称为高 炉内型从自上而下分为炉喉、炉 身、炉腰、炉腹、炉缸五个部分 。该容积总和为它的有效容积, 反应高炉多具备的生产能力。
6
2.高炉本体及主要构成
高炉内型
h6
高炉有效容积:
炉 喉
Vu Vi
1
5
d1
高炉炼铁设计原理课件
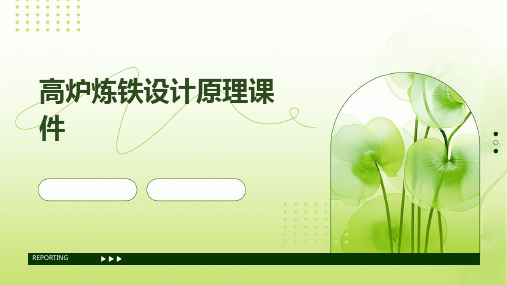
。型与结构设计
总结词
炉型与结构设计是高炉炼铁设计的核心,它决定了高炉的产能、能耗和环保性 能。
详细描述
炉型的选择要根据原料条件、产品需求和工艺要求等因素来确定,同时要考虑 高炉的结构稳定性、安全性和经济性。结构设计要合理安排炉膛、炉底、炉缸 和炉衬等部分,以确保高炉运行的稳定性和耐久性。
PART 04
高炉操作与控制
REPORTING
装料与送风操作
装料操作
根据高炉炼铁工艺要求,将原料 按照一定比例和顺序装入高炉炉 膛内,以保证高炉炼铁过程的顺 利进行。
送风操作
通过鼓风机将空气送入高炉炉膛 内,与焦炭和矿石发生反应,产 生高温和还原气体,为高炉炼铁 提供必要的热量和还原剂。
炉温与压力控制
排渣与排气的处理是高炉炼铁环保要求的重点,它涉及到对废气、废水和废渣的处理和利用。
详细描述
高炉排渣是炼铁过程中的必然产物,其处理要尽量减少对环境的污染。排气中含有大量的有害气体, 其处理要采用有效的净化措施,以符合环保标准。同时,对于废气、废水和废渣等资源,应积极探索 再利用的可能性,以实现资源的循环利用。
趋势
未来高炉炼铁的节能减排趋势将更加注重低 碳、环保、循环发展,通过技术创新和产业 升级实现高炉炼铁的可持续发展。
PART 06
高炉炼铁案例分析
REPORTING
国内某大型钢铁企业的高炉炼铁工艺流程
01
02
03
04
05
原料准备
配料与上料
燃烧与传热
生铁形成与出铁 环境保护与节能 减排
国内某大型钢铁企业使用 铁矿石、焦炭和熔剂等原 料,通过破碎、筛分和混 合等工艺,为高炉炼铁提 供合格的原料。
炉温控制
总结词
炉型与结构设计是高炉炼铁设计的核心,它决定了高炉的产能、能耗和环保性 能。
详细描述
炉型的选择要根据原料条件、产品需求和工艺要求等因素来确定,同时要考虑 高炉的结构稳定性、安全性和经济性。结构设计要合理安排炉膛、炉底、炉缸 和炉衬等部分,以确保高炉运行的稳定性和耐久性。
PART 04
高炉操作与控制
REPORTING
装料与送风操作
装料操作
根据高炉炼铁工艺要求,将原料 按照一定比例和顺序装入高炉炉 膛内,以保证高炉炼铁过程的顺 利进行。
送风操作
通过鼓风机将空气送入高炉炉膛 内,与焦炭和矿石发生反应,产 生高温和还原气体,为高炉炼铁 提供必要的热量和还原剂。
炉温与压力控制
排渣与排气的处理是高炉炼铁环保要求的重点,它涉及到对废气、废水和废渣的处理和利用。
详细描述
高炉排渣是炼铁过程中的必然产物,其处理要尽量减少对环境的污染。排气中含有大量的有害气体, 其处理要采用有效的净化措施,以符合环保标准。同时,对于废气、废水和废渣等资源,应积极探索 再利用的可能性,以实现资源的循环利用。
趋势
未来高炉炼铁的节能减排趋势将更加注重低 碳、环保、循环发展,通过技术创新和产业 升级实现高炉炼铁的可持续发展。
PART 06
高炉炼铁案例分析
REPORTING
国内某大型钢铁企业的高炉炼铁工艺流程
01
02
03
04
05
原料准备
配料与上料
燃烧与传热
生铁形成与出铁 环境保护与节能 减排
国内某大型钢铁企业使用 铁矿石、焦炭和熔剂等原 料,通过破碎、筛分和混 合等工艺,为高炉炼铁提 供合格的原料。
炉温控制
《系统节能》ch07炼铁系统的节能

02 炼铁工艺流程与能耗分析
CHAPTER
炼铁工艺流程简介
01
02
03
高炉炼铁工艺流程
包括原料准备、烧结、炼 焦、高炉炼铁等环节,最 终得到铁水。
直接还原工艺流程
采用非高炉炼铁法,通过 直接还原剂将铁矿石还原 成海绵铁。
熔融还原工艺流程
以煤或天然气为主要能源, 将铁矿石熔融还原成铁水。
炼铁系统各环节能耗分析
节能措施有助于降低炼铁生产成本, 提高企业的经济效益和市场竞争力。
减少环境污染
炼铁过程中会产生大量的废气、废水 和固体废弃物,节能措施有助于减少 污染物排放,减轻对环境的压力。
炼铁系统节能的途径
优化工艺流程
通过对炼铁工艺流程进 行优化,降低能耗和提
高生产效率。
设备升级改造
采用高效、低能耗的设 备和工艺,替换老旧、
开发新能源
开发利用新能源,减少对传统能源 的依赖。
03
02
提高能源利用效率
采用先进的能源利用技术和设备, 提高能源的利用效率。
加强节能管理
加强节能管理和监管,推动企业采 取节能措施。
04
03 炼铁系统节能技术与实践
CHAPTER
高效能设备与节能技术
高炉设备升级
采用高效能高炉设备,提 高炼铁效率,降低能耗。
富氧鼓风技术
通过提高鼓风中的氧含量, 增强燃烧效率,降低燃料 消耗。
喷煤技术
将煤粉直接喷入高炉中, 替代部分焦炭,降低炼铁 成本和能耗。
余热回收与利用技术
余热锅炉回收
利用高炉炉渣和烟气中的余热,通过余热锅炉转 化为蒸汽或电能。
热泵技术
利用热泵将低品位余热转化为高品位热能,用于 加热或供暖。
高炉炼铁基本原理及工艺 PPT
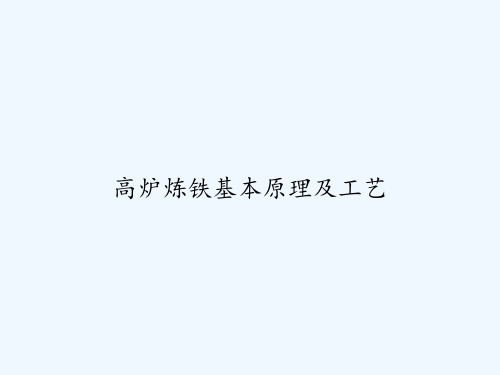
结晶水分解
除CaCO3外的其它MCO3分解 间接还原
碳素沉积反应(2CO=C+CO2) (2)软熔带:矿石层开始熔化与焦碳层交互排列,焦碳层也称“焦窗” 形状受煤气流分布与布料影响,可分为正V型,倒V型,W型
主要反应:Fe的直接还原 Fe的渗碳 CaCO3分解 吸收S(焦碳中的S向渣、金、气三相分布) 贝波反应:C+CO2=2CO
(3)滴落带:主要由焦碳床组成,熔融状态的渣铁穿越焦碳床 主要反应:Fe、Mn、Si、P、Cr的直接还原,Fe的渗C
(4)回旋区:C在鼓风作用下一面做回旋运动一面燃烧,是高炉热量发 源地(C的不完全燃烧),高炉唯一的氧化区域。 主要反应: C+O2=CO2 CO2+C=2CO
(5)炉缸区:渣铁分层存在,焦碳浸泡其中 主要反应: 渣铁间脱S,Si、Mn等元素氧化还原
(4)用直接还原度rd、间接还原度ri来衡量高炉C素利用好坏,评价 焦比。
3.非铁元素的还原
(1)Mn的还原:
①一般规律: MnO2→(550℃间还)→Mn2O3→(1100 ℃ 间还)→Mn3O4→
(1000 ℃间还) →MnO→(1200 ℃直接还原)→Mn
②Mn还原的特点:间接还原放热大,使炉顶温度↑ 直接还原吸热大,使焦比↑
2. (助)熔剂
(1)作用: 形成低熔点易流动的炉渣、脱S(碱性熔剂)
(2)种类:
3 焦碳
①主要作用:
作为高炉热量主要来源的60~80%,其它热风提供 提供还原剂C、CO 料柱骨架,保证透气性、透液性
②质量要求:
含炭量:C↑ 灰份:10%左右,灰分低可使渣量↓ 含S量:<0.6% 生铁中[S]80%±来源于焦碳 强 度:M40 (kangsuiqd)、M10 (lmqd) 粒度组成:均匀 60mm左右的>80%,大于80mm的<10%,大于 80mm的<10%
除CaCO3外的其它MCO3分解 间接还原
碳素沉积反应(2CO=C+CO2) (2)软熔带:矿石层开始熔化与焦碳层交互排列,焦碳层也称“焦窗” 形状受煤气流分布与布料影响,可分为正V型,倒V型,W型
主要反应:Fe的直接还原 Fe的渗碳 CaCO3分解 吸收S(焦碳中的S向渣、金、气三相分布) 贝波反应:C+CO2=2CO
(3)滴落带:主要由焦碳床组成,熔融状态的渣铁穿越焦碳床 主要反应:Fe、Mn、Si、P、Cr的直接还原,Fe的渗C
(4)回旋区:C在鼓风作用下一面做回旋运动一面燃烧,是高炉热量发 源地(C的不完全燃烧),高炉唯一的氧化区域。 主要反应: C+O2=CO2 CO2+C=2CO
(5)炉缸区:渣铁分层存在,焦碳浸泡其中 主要反应: 渣铁间脱S,Si、Mn等元素氧化还原
(4)用直接还原度rd、间接还原度ri来衡量高炉C素利用好坏,评价 焦比。
3.非铁元素的还原
(1)Mn的还原:
①一般规律: MnO2→(550℃间还)→Mn2O3→(1100 ℃ 间还)→Mn3O4→
(1000 ℃间还) →MnO→(1200 ℃直接还原)→Mn
②Mn还原的特点:间接还原放热大,使炉顶温度↑ 直接还原吸热大,使焦比↑
2. (助)熔剂
(1)作用: 形成低熔点易流动的炉渣、脱S(碱性熔剂)
(2)种类:
3 焦碳
①主要作用:
作为高炉热量主要来源的60~80%,其它热风提供 提供还原剂C、CO 料柱骨架,保证透气性、透液性
②质量要求:
含炭量:C↑ 灰份:10%左右,灰分低可使渣量↓ 含S量:<0.6% 生铁中[S]80%±来源于焦碳 强 度:M40 (kangsuiqd)、M10 (lmqd) 粒度组成:均匀 60mm左右的>80%,大于80mm的<10%,大于 80mm的<10%
- 1、下载文档前请自行甄别文档内容的完整性,平台不提供额外的编辑、内容补充、找答案等附加服务。
- 2、"仅部分预览"的文档,不可在线预览部分如存在完整性等问题,可反馈申请退款(可完整预览的文档不适用该条件!)。
- 3、如文档侵犯您的权益,请联系客服反馈,我们会尽快为您处理(人工客服工作时间:9:00-18:30)。
图3 德国蒂森公司的ri与C消耗的关系
8
9
中国与欧洲还原度与碳素消耗的差别
图2与图3无本质上的差别,只是横坐标的起点中国用rd=0, 欧洲用rd=1.0。欧洲的炼铁工作者在作图时考虑rH2的因素, 而我国喷吹的燃料中含H2低,因此作图时将riH2忽略不计。 从图2和图3上将ηCO和ηCO+H2达到50%为目标确定出最低碳素 消耗,折算成燃料比。在中国的当前冶炼条件下,这个目标 为480kg/t,而蒂森公司确定的目标是460kg/t。
B Cd
Fe
D
A
Ce
Cd Si,Mn,P,S
0.0
0.1
0.2
0.3
0.4
0.5
0.6
0.7
0.8
0.9
1.0
铁的直接还原度,rd
图1 生铁的直接还原度rd与碳素C消耗的关系
图1 表示最低的吨铁C素消耗在CR与C热的交点处,这是经典的图解。 它是以FeO在1000℃下被CO还原达到平衡状态 (FeO+nCO→Fe+(n-1)CO+CO2,n=3.45)为基础绘制的。
10
2.实现低燃料比,达到低碳炼铁的技术
2.1 精料是实年来,精料 工作取得很大进步,为高炉降低焦比,提高喷煤量,实现 低燃料比做出了贡献。但是近年来由于矿价高涨,为了降 低采购成本,出现了与精料原则相违背的现象,需要认真 思考。广义上讲,高炉精料包括焦炭、喷吹煤的优化,含 Fe炉料的优化和综合鼓风三个方面。
699.5 281
30 35 40
45 50
55 60
1000
800 668 600
400 269.7 200
0
0.0
0.2
0.4
0.6
0.8
1.0
r d
7
欧洲炼铁界在喷吹含H2燃料时用铁的间接还原度ri与碳素消耗的关系图 (图3)来判别。
C +C in kg/t HM Comb. SL
900 800 700 600 500 400 300 200 100
12
入炉品位降低,必然造成渣量的增加,给高炉炼铁带来不利的影响, 主要是冶炼过程中,软熔带中软熔层比例增加,而软熔层的透气性仅 为1/52,而滴落带中炉渣的滞留率增加,使上升煤气通过的焦炭的空 隙度降低,结果造成炉内△P的上升,其次是烧结矿的粒度细化,05mm的粒度增多,造成块状带的△P 也上升,因此我们在使用这类富 矿料生产烧结矿时,要在提高燃料还原性和强度,以及粒度的均匀性 上下功夫。
对高炉炼铁系统几个节能技术的认识
30号,100083 Tel:
E-mail: 江西 新余 2012.05.22
目录
1. 前言 2. 实现低燃料比,达到低碳炼铁的技术
2.1 精料是实现低燃料比
2.1.1 含Fe料(铁矿石)质量劣化情况下生产优质烧结矿的技术分析 2.1.2 烧结生产过程的节能 2.1.3 利用国产磁精矿粉生产优质球团矿
0 -100
0
Gas utilization %
CO2 H2O
100
CO CO2 H2 H2O
Heat boundary
Actual fuel rate
Chemical boundary Minimum fuel rate
20
40
60
80
100
Indirecte reduction in %
2.2 降低燃料比的重要工艺技术
2.2.1 高风温技术 2.2.2 富氧技术 2.2.3 脱湿与调湿技术 2.2.4 喷吹燃料技术 2.2.5 提高操作水平,使煤气利用率达到ηCO=0.5的技术分析
2.3 延长高炉一代寿命
3. 结论
2
1. 前 言
高炉炼铁属于碳冶金学,它用焦炭(煤粉)的碳为发热剂和还原剂, 而冶炼的产品为铁碳合金,碳在风口前燃烧放热形成的CO又是还原剂 ,上升过程中还原氧化铁转变成CO2,形成含CO和CO2的高炉煤气。
高炉煤气作为低热值气体燃料在热风炉、加热炉及锅炉内燃烧,其中 的CO转化成为CO2。溶解在铁水中的C(含碳铁合金的组成部分)在 炼钢过程中又氧化成CO而成为转炉煤气的主要成分。转炉煤气作为热 值较高的气体燃料在用户处再氧化成CO2。这样高炉炼铁的燃料消耗 (燃料比)就决定了其能耗的高低和CO2排放量的多少。
2011年中国生铁产量达到6.297亿吨。它表明中国炼铁消耗的碳量和排 放的CO2居世界前列,因此,降低吨铁的燃料消耗,也即降低吨铁的 CO2排放,即低碳炼铁成为炼铁节能减排的首要任务。
3
冶炼1吨生铁需要消耗多少碳?
决定碳消耗有三个方面: ①生铁渗碳和生铁中少量元素耗碳; ②铁氧化物还原耗碳; ③为冶炼提供必需的热量,风口前燃烧的碳。
生铁渗碳和少量元素还原(包括脱硫)消耗碳在55-60kg/t,在当今 冶炼低硅生铁和生铁对锰没有特殊要求的情况下,生铁渗碳量在4650kg/t,而少量元素还原在6-12kg/t。
4
铁氧化物还原耗碳与热量耗碳通常是用rd(铁的直接还原度)与C消 耗的图解法(图1)来判别。
F
C
C
H
O
碳消耗量
Ci
E
Fe
5
但是实际生产中的与理论上的有差别,造成差别的原因在于冶炼条件和 高炉操作水平不同,使还原离平衡状态有一定差距,表现在炉顶煤气 CO利用率ηCO的高低。如果将这些因素考虑在内,则得到实际生产中的 碳素消耗与rd之间的关系图(图2)。
图2 实际生产高炉的rd与碳素C消耗的关系
6
中国
C
1400
1200
本节只讨论含Fe料的优化与实现精料方面的问题。
11
2.1.1含Fe料(铁矿石)质量劣化情况下生产优质烧 结矿的技术分析
我们在这里所说的铁矿石质量劣化是指富矿石的含Fe量下降,有害元 素含量在增加。
例如东半球的富矿,以澳矿为例,品位降低到58-62%,Al2O3含量上 升至1.5%以上,有的达到3.0%,P含量上升到0.07%以上。即使这样 ,富矿的储量不断减少,价格大幅度攀升。至于其他国家(马来西亚 、菲律宾、印尼、非洲国家)的矿石含铁量均较低,而有害元素(例 如K2O,Na2O,Zn,Cr,Mn,Ni,As等)含量比澳矿多。目前出现 的争购低品位(含Fe 50±2%)质量更差的矿石是不可取的。2005年 前,我国高炉入炉品位曾达到60%以上,由于矿石质量的劣化,这种 高炉品位以后不可能再出现。我们认为在目前的矿石质量条件下,应 该把住入炉品位为:大高炉在58%以上,中小高炉在57%以上,低于 55%的入炉品位对任何高炉都是不可取的。