准时制(JIT)生产案例
国内企业推行JIT成功案例

国内企业推行JIT的案例作者:李庆远浏览次数: 1286 发布时间:2006-9-18 17:04:55【本讲重点】嘉陵公司JIT推行案例东莞某外资企业JIT推行案例广东某涂料企业JIT不完全推行案例推行案例1:嘉陵股份有限公司的JIT推行中国嘉陵股份有限公司所生产的“嘉陵”摩托车是全国第一品牌,现有8种排量(35-150ml)100多个车型,累计产销量逾1000多万辆,占全国摩托车总量的1/5以上,现已形成年产2 00万辆的生产能力。
这家公司具有强大、完善的开发、生产、营销体系,出口50多个国家和地区。
在过去,嘉陵公司也经历了大批量生产摩托、市场供不应求的阶段,随着市场竞争越来越激烈,摩托车的品种和式样越来越多,嘉陵摩托也积压了很多的库存。
为此,嘉陵公司通过实行JI T,获得了良好的效果。
嘉陵公司推行JIT的主要做法嘉陵股份有限公司在推行JIT生产管理的过程中,根据JIT 生产管理的思维和原理,经过多年的探索和试点,总结出了一系列推行JIT生产的有力措施。
国内企业可以借鉴嘉陵公司的宝贵经验,结合本企业生产情况以及市场变化等因素制定相应的推行举措。
1.多品种作业由于市场竞争的压力,嘉陵公司被迫实施“多品种、小批量、转产快”的生产方式。
这样就可以满足市场多品种、小批量的需求。
在摩托车生产线上可以间隔生产多种不同品种的产品,而且不同型号产品生产的换线速度很快。
这样就提高了企业对市场的适应能力,能够尽快地满足用户的需求。
2.加强人本管理JIT生产方式是需要人来推广的。
为此,嘉陵公司加强了实施“一人多岗、一专多能、一线多品”和“多功能小组”的人本管理。
人是企业最宝贵、最有价值、最富有创造性的资源,是企业生存与发展的无价之宝和资本。
只有高度重视人的管理,才能提高员工的技能水平,充分发挥员工所具有的功能和潜力。
3.强化物流管理嘉陵公司还强化了队伍物流的管理,实施了“一个产品流”、“一个盛具流”、“二分三定”配送流,“二定一线”(即定置、定具、划线)等物流管理方式。
企业生产组JIT准时制生产案例学习
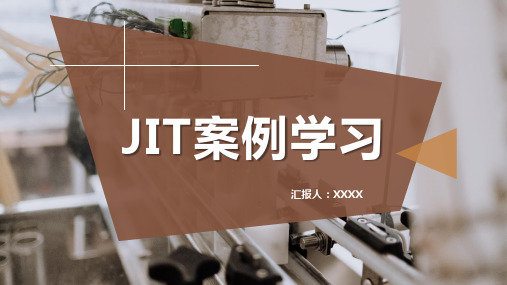
JIT的基础之一是均衡化生产,即平均制造 产品,使物流在各作业之间、生产线之间、 工序之间、工厂之间平衡、均衡地流动。为 达到均衡化,在JIT中采用月计划、日计划, 并根据需求变化及时对计划进行调整。
准时制运作的基本理念是需定供,即供给方根 据需要方的要求(或称看板),按照需要方的 品种、规格、质量、数量、时间、地点等要求, 将物资配送到指定的地点。不能早、不能晚、 不能多、不能少,并且确保所送物资没有任何 残次品。由此可知,准时制对库存的认识与传 统的库存控制方法截然不同,其认为库存是毫 无用处的,是对资源的浪费。
丰田公司的准时制采取的是多品种少批量、 短周期的生产方式,实现了消除库存,优化 生产物流,减少浪费目的。JIT生产方式的基 本思想是“只在需要的时候,按需要的量, 生产所需的产品”,也就是追求一种无库存, 或库存达到最小的生产系统。JIT的基本思想 是生产的计划和控制及库存的管理。所以, JIT生产模式又被称为“精益生产”。
精益生产方式JIT的基本目标工业企业是以盈利为目的的社会经济组 织。因此,最大限度地获取利润就成为企业的基本目标。JIT采用灵 活的生产组织形式,根据市场需求的变化,及时、快速地调整生产, 依靠严密细致的管理,通过"彻底排除浪费",防止过量生产来实现 企业的利润目标。为实现这一基本目的,精益生产方式JIT必须能很 好地实现以下三个子目标:零库存、高柔性(多品种)、无缺陷。
JIT案例学习
汇报人:XXXX
主要特征
准时制技术的一个重要特点就是严格的计划, 为了适时地满足企业对人员的需要,同时又 要消除人员的闲置,即不能靠大量"库存"来 满足变动的需求,必须做好准时制人员的规 划。一般应根据行业的商业周期或季节性规 律,科学预计企业业务的发展变化对人员需 求的影响,尤其是对临时需要人员的影响。
16-丰田案例:丰田是如何实现准时化生产的?

丰田案例:丰田是如何实现准时化生产的?丰田喜一郎应父亲丰田佐吉的要求,学习如何制造汽车;学成之后向他父亲提出他的造车计划,并于1937年成立丰田汽车;当时由于缺乏资金,无法像美国汽车厂一样,先造出一堆汽车然后才慢慢地去销售,所以喜一郎就在计划书中提出一个他造汽车的特殊观点:只有在需要的时候,才生产刚好满足客户需要数量的产品(类似现在接单生产的概念),并称之为Just In Time (JIT,准时生产,又称为:刚好准时,以匹配后来JIT向其他非生产领域的延伸应用的需要)。
此时的准时化(JIT)只不过是一种类似现在的〝接单生产〞的概念,由于在当时丰田的条件下,实施起来有很多的困难,所以只是停留在〝概念〞阶段而已,对丰田汽车厂而言尚未有太多的实际影响。
1945年丰田汽车于战后复工,大野耐一主管生产,并且很快就发现当时的生产计划不合理,遂将当时的月计划改成日计划,其大意是:当时丰田一个月约需生产500部卡车,前一月月底就将月计划下达给车间,车间按计划将每个零件或部件都生产足500个之后,再向下道工序转移。
这种〝批量等待〞(等待成为一批,例如:500个)的生产方式造成前后工序的等待与忙闲不均,于是大野下令将月计划(每月500台)改成日计划(平均每日20台),并要求做完20个就向下转移。
改善结果发现流动速度加快了、周期时间缩短了、库存积压时间缩短、流动资金的需求也缓解了。
大野因此提出了第一个在TPS里占重要地位的概念:降低生产和移动批量,可以加快流动速度、缩短周期、降低库存积压、减少对资金的需求。
当然,这种日平均量的概念也成为后来的〝平准化生产〞的滥觞。
1948年丰田因生产过剩、产品(卡车)滞销,资金链断裂,被迫将生产和销售分拆经营(产销分离)。
这个事件让大野先生体会到〝局部优化〞(只考虑生产的效率提升,未考虑到销售能力与资转能力)的后遗症、与〝站在全局的角度来实施改善活动〞的重要性,坚定了大野后来的〝全局思维〞的理念。
生产运营just in time案例

准时生产(Just in time,JIT)是指生产的产品能够精准地满足客户在时间、质量和数量上的需求,无论客户是产品的最终用户还是处于生产线上的其他流程。
JIT 的主要要素包括不断改进、消除浪费、良好的工作场所整理、缩短生产准备时间以及企业中所有员工的参与。
JIT 的优点包括:库存量低、降低了花费在存货上的运营资本、降低了存货变质、陈旧或过时的可能性、避免因需求突然变动而导致大量产成品无法出售的情况出现、降低了检查和返工产品的时间。
JIT 的缺点包括:仅为不合格产品的返工预留了最少量的库存,因而一旦生产环节出错则弥补空间较小、生产对供应商依赖性较强,并且如果供应商没有按时配货,则整个生产计划会被延误、由于企业按照实际订单生产所有产品,因此并无备用的产成品来满足预期之外的订单适用。
JIT 适用于制造型企业旨在降低库存,以及服务型企业旨在消除客户排队这一浪费现象。
在实际生产运营中,企业可以根据自身情况采用适合的 JIT 策略,以提高效率、降低成本、满足客户需求。
jit经典案例
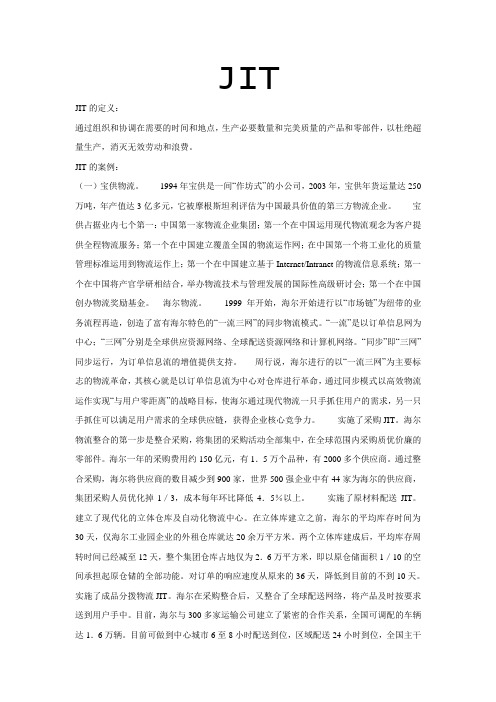
JITJIT的定义:通过组织和协调在需要的时间和地点,生产必要数量和完美质量的产品和零部件,以杜绝超量生产,消灭无效劳动和浪费。
JIT的案例:(一)宝供物流。
1994年宝供是一间“作坊式”的小公司,2003年,宝供年货运量达250万吨,年产值达3亿多元,它被摩根斯坦利评估为中国最具价值的第三方物流企业。
宝供占据业内七个第一:中国第一家物流企业集团;第一个在中国运用现代物流观念为客户提供全程物流服务;第一个在中国建立覆盖全国的物流运作网;在中国第一个将工业化的质量管理标准运用到物流运作上;第一个在中国建立基于Internet/Intranet的物流信息系统;第一个在中国将产官学研相结合,举办物流技术与管理发展的国际性高级研讨会;第一个在中国创办物流奖励基金。
海尔物流。
1999年开始,海尔开始进行以“市场链”为纽带的业务流程再造,创造了富有海尔特色的“一流三网”的同步物流模式。
“一流”是以订单信息网为中心;“三网”分别是全球供应资源网络、全球配送资源网络和计算机网络。
“同步”即“三网”同步运行,为订单信息流的增值提供支持。
周行说,海尔进行的以“一流三网”为主要标志的物流革命,其核心就是以订单信息流为中心对仓库进行革命,通过同步模式以高效物流运作实现“与用户零距离”的战略目标,使海尔通过现代物流一只手抓住用户的需求,另一只手抓住可以满足用户需求的全球供应链,获得企业核心竞争力。
实施了采购JIT。
海尔物流整合的第一步是整合采购,将集团的采购活动全部集中,在全球范围内采购质优价廉的零部件。
海尔一年的采购费用约150亿元,有1.5万个品种,有2000多个供应商。
通过整合采购,海尔将供应商的数目减少到900家,世界500强企业中有44家为海尔的供应商,集团采购人员优化掉1/3,成本每年环比降低4.5%以上。
实施了原材料配送JIT。
建立了现代化的立体仓库及自动化物流中心。
在立体库建立之前,海尔的平均库存时间为30天,仅海尔工业园企业的外租仓库就达20余万平方米。
JIT及其案例分析

(1)通过联机进行实时数据处理。
(2)货物装卸作业量减少到最小。
(3)电子设备淘汰了物流过程中的纸张文件作业,可节省费 用、减少失误。
(4)计算机系统进行全面库存控制。
(5)货物流转数据准确。
(6)极大地提高信息交换速度。
(7)保证生产安全。
Autocon公司在配送方面取得了很大成功,促进了 Autocon公司及通用公司业务的不断拓展。
JIT的基本原理: 根据需方的指令,将需方所需的品种按桌订的数量在所需的
时间送到指定的地点。不少送,也不多送;不迟送,也不早 送。送的货品个个都保证质量。
也就是在适当的时间,把适当的物品以适当的数量,送到适 当的地点。
它体现了以下要点: 1.品种合适,拒绝不合适的品种规格; 2.数量合适,不少,也不多; 3.时间合适,不迟,也不早; 4.地点合适; 5.质量合适,百分之百合格。 它体现了以下优越性: 1.可以实现线边零库存; 2.可以实现最大的节约; 3.最大限度地消除废品损失
JIT强调全面质量管理,认为仅靠检验只能发现缺陷,而不能 防止和消除缺陷,即使事后补救业已造成浪费。因此,必须建 立质量保证体系,从根源上保证产品质量。同时,坚持预防性 设备维护制度,一旦出现设备故障,就全线停车,群策群力查 明事故根源,一次性彻底解决问题。
JIT追求最优的质量成本比。JIT致力于开发旨在实现零缺陷的 制造流程,表面上看起来,这似乎是个不切现实的目标。但是, 从长远的角度看,由于消除了一些冗余的功能,就可使企业大 大降低成本费用,实现最优的质量成本比。
JIT采购的主要特点: 1.单源供应。。 2.小批量采购。 3.合理选择供应商。 4.从根源上保障采购质量。 5.可靠的送货和特定的包装要求。 6.有效的信息交换。
JIT案例(推进拉动式生产可以参考)

出 货 场 ( 完 成
交集 换货
与 看 板
品
店
5、总装厂(客户)每次到零)件厂集货时将下两次集货的看板和清单交零部件
厂,零件厂分奇偶交叉集货(已集好货在装车,正在集货),集货时通过将客
户看板和社内完成品看板交换,每次集完货将交换出来的社内完成品看板返回
到平准化看板箱中,完成A循环。
精选版ppt
6
完成品店
精选版ppt
7
9、社内与供应商之间流转(如下图)
看板作业流程
精选版ppt
8
看板能调整工序间平衡流程上促使线小时产能满足节拍最大化生产平准化促进柔性化生领取周期意义14081日或1班表示领取频领取回数或次数表示周转次数提前次数看板发行的提前次数概念1总车厂每月定期向零部件厂发出未来三个月内示计划一般第一个月平准到每日基本不变后两个月只是需求总数
概念 JIT生产方式是以降低成本为基本目的,在生产系统的各个环节 全面展开的一种使生产有效进行的新型生产方式。JIT又采用了 看板管理工具,看板犹如巧妙连接各道工序的神经而发挥着重 要作用
2、零件厂以总装厂的集货周期制定自己的完成品交(集)货周期和时间表, 以内示计划和集货周期为依据确定平准化看板(完成品看板)的发行量。 以内部各工序的生产能力确定工序内各工程看板的发行量,将计划管理 完全变成了对看板的管理。
3、零件厂与自己的供应商之间同样按上述方式。
精选版ppt
5
4、三大循环:A、总车厂(客户)与零件厂出货场之间 的物流和看板流; B、出货场与各工序之间的集货和看板流 转与交换; C、零件厂与自己供应商之间的交货和看板 流转。
集货
7、社内按与客户对应的时间周期从平准化看板箱中取周期时段的完成品看板, 由“水蜘蛛”到各工序岗位集货,同时进行完成品与工序内生产指示看板进行 交换,将交换出来的指示看板投入工序内指示看板箱,工序员工就可以生产 了,在这里“水蜘蛛”的路线时间一定,工序内只能依看板生产。完成B循环。
及时制造JIT准时化生产方式实施案例
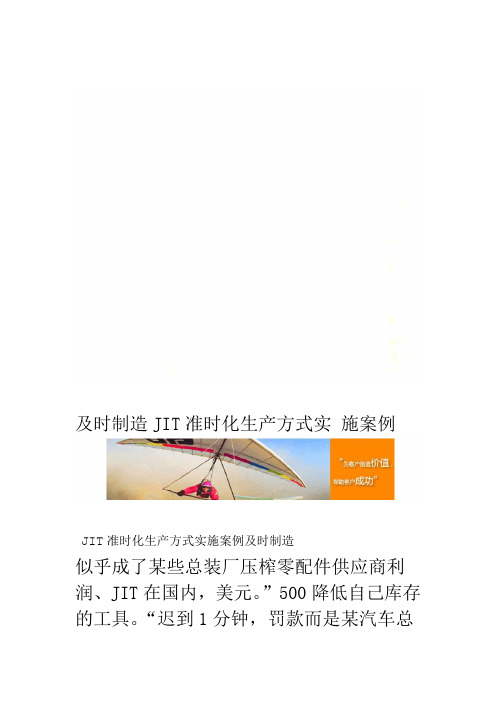
及时制造JIT准时化生产方式实施案例JIT准时化生产方式实施案例及时制造似乎成了某些总装厂压榨零配件供应商利润、JIT在国内,美元。
”500降低自己库存的工具。
“迟到1分钟,罚款而是某汽车总装这可不是用来约束员工上班的考勤制度,制造企业对其现在,厂用来约束其零配件供应商供货的。
零配件供应商几乎都有类似的要求,为的是实现准时制 Just In Time)供货和制造。
JIT(,的基本思路就是用最准时、最经济的生产资料采购、JIT的由头,配送,以满足制造需求。
“有些总装厂借着JIT”私下里一些零把库存压力毫不留情地转嫁到我们头上。
配件厂商很气愤地表示道。
JIT身上,是因为在引入零配件商之所以将怨气撒在JIT模式前,总装厂与零配件企业之间采用的是入库结算方模式后,总装厂又引进了“上线”和式;而在引入JIT“下线”两种新的结算法——零配件上生产线时或在生对总装厂显然,产线上被装配为合格成品入库时才结算。
来说,这三种结算方式能使它们的库存资金递减,“下按理线”结算甚至可以让它们的原材料库存真正变为零。
但据相当零配件的价格应该不一样,说不同的结算方式,一部分国内零配件厂商透露,即使面对下线结算方式,他们也难有讨价还价的能力,因为“这是一个整车为王的时代”。
一些总装厂在自己内部生产尚缺乏计划和控制时,却偏偏要求与供应商实行下线结算,零配件厂送来的产品在总装厂甚至能被搁置数周。
“反正也不是它们的库存,它们一点也不心疼。
”一些零配件厂商很无奈地说。
总装厂却因为没有库存压力显得颇为轻松,一位总装厂的物流经理说:“现在,我们没有原材料库存的压力了。
”在国内的供应链上,JIT 似乎成了某些总装厂压榨供应商的工具。
被扭曲的JIT“这是危险之举,不仅害人,更重要的是最终会害自己。
”一位曾在福特公司从事过多年管理工作的专家痛心地说。
他认为,“国内某些企业在学习先进经验时,只学了形式,而没抓住本质,甚至走到了反面。
”这位专家的“害己”之说,并非危言耸听。
- 1、下载文档前请自行甄别文档内容的完整性,平台不提供额外的编辑、内容补充、找答案等附加服务。
- 2、"仅部分预览"的文档,不可在线预览部分如存在完整性等问题,可反馈申请退款(可完整预览的文档不适用该条件!)。
- 3、如文档侵犯您的权益,请联系客服反馈,我们会尽快为您处理(人工客服工作时间:9:00-18:30)。
积。 2、确定标准在制品数量,制作工序间滑道,改 变转运方式,取消转运车。 3、制定工序能力表,通过对工序能力的分析与 论证,制定标准作业组合表及改善后标准作业
案例三:X齿轮车间整流
(四)改善效果 1、设备U形布局,工序内物流U形走向,节省作 业面积90平方米。
58%
50%
44%
40% 38% 35% 38%
30%
41% 改善前 平均
20%
10%
0%
1
2
3
4
5 平均
案例三:X齿轮车间整流
(二)改善 目标根据目前生产及设备的实际状况,对设备布局
进行调整,对工序内容进行优化组合,做到少 人化,一人多机。在生产线内减少在制品数量, 确定标准手持量及合理的序间在库,实现“一 个流”和“先入先出”的生产方式,提高产品 品质,提高劳动生产率,降低产品成本。
如采用JIT 生产,工序间在制品数减为1,则最早在第 20 个就会发现质量问题。
案例一:发动机箱体
仍以上例为例,若平均 工序加工时间为3 分钟, 则首件成品完成的时间 依次为17103 分钟,573 分钟,和60 分钟。工序 间物料所占用的空间和 生产资金也和300,10, 1 成比例。因此准时制 生产方式,无论时间, 空间,资金都得到极大 的节省,不仅能及时满 足市场对多品种和数量 的需要,同时又可以及
在制品多,烘干炉的储备是车门72辆份、 前盖和后盖各36辆份。
占用工位器具多,四门两盖占用的工位
器具共64个。
占后地盖面器积大,共前占盖器用面积 126米2车具。门及器储
生具产及操储作人员多具达及储16人。
备72辆
车 门过备量3份6生辆产导致大备量3份6辆的资金被积压。份
吊 具在制品过多,造成质量衰减。
案例二:XX轿车焊装车间
四门两盖工段各项指标改善前后对比
90 80 70 60 50 40 30 20 10 0
储备 (辆份) 改善前 72 改善后 12
工位器 具
64 26
人员
16 9
吊具 更换吊 (个) 具(个)
81
54
27
0
改善前 改善后
案例三:X齿轮车间整流
(一)改善的 问题点
案例三:X齿轮车间整流
90%
80%
70%
60%
33%
50%
改善后
40%
80%
74%
30% 60%
64%
改善前
20%
41%
10%
0%
1
2
3
4
平
案例四:嘉陵股份有限公司
❖ 公司概况 ▪ “嘉陵”摩托车是全国第一品牌 ▪ 100多个车型,年产200万辆 ▪ 摩托车的品种和式样越来越多,嘉陵摩 托也积压了很多的库存
❖ 推行JIT的主要做法 ▪ 多品种作业 ▪ 加强人本、物流管理 ▪ 追求尽善尽美:“六零”管理
凡是超出 增加产品 价值所必 需的绝对 最少的物 料、机器 和人力资 源的部分, 都是浪费。
• 一个流生产,即各 工序只有一个工件 在流动,使工序从 毛坯到成品的加工 过程始终处于不停 滞、不堆积、不超 越的流动状态,是 一种工序间在制品 向零挑战的生产管 理方式,通过追求 “一个流”,使各 种问题、浪费和矛 盾明显化,迫使人 们主动解决现场存
工艺和产品设计
•采用标准件
•降低复杂性
案例一:发动机箱体
某摩托车厂生产摩托车发动机箱体,工艺安排有20 道 工序,其中最后一道为气密性试验(水压试验)。按原 生产工艺规定,工序之间要备有300 个在制品的库存, 如按此工艺组织生产,则最早能发现第一个试验漏水的 产品是在300×19+1=5701 个以后的产品。 如果变换一种生产方式,把工序间在制品的数量减少到 10,则在191 个产品后就可发现漏水现象
1、设备未按工艺流程布局,工序内物流象迷宫一样,作 业面积450平方米。 2、工序间在制品数量多,搬运频繁,易产生漏检现象, 出现不良品难追溯。
案例三:X齿轮车间整流
3、操作者工作负荷不满、操作过程中有一些不必 要的动作、等待时间长,作业效率低,生产过程中 存在问题不易暴露。(11人)
70%60%Fra bibliotek工件质量烘不干好控制,质量问题源的追溯 受到阻碍。炉
前后盖现场摆放器具过多造成秩序混乱,工位 吊具各器具不足。
案例二:XX轿车焊装车间
• 冲压品种的生产按小时的生产数量进行。 • 烘干炉只设12辆份的专用吊具和1份备用吊具; • 前后盖在制品储备减少到6辆份; • 减少占地面积,优化作业人员7人。
案例三:X齿轮车间整流
2、在制品由改善前的220件下降到14件,下降了 206件,实现“一个流”和“先入先出”的生产方 式,提高产品品质。
案例三:X齿轮车间整流
3、人员由改善前11人变为8人(双班生产),减少 3人,平均负荷率由改善前的41%提高到74%,提高 了33%,实现少人化,一人多机。提高劳动生产率, 降低产品成本。
案例分析
JIT实施过程全貌
易 缺足
难
JIT具体实施过程
进行准备工作
•高层的支持 •人员培训
实行全面质量管理
•尽力实现“零缺陷” •进而实现“零库存”
不断改善
•理想化目标 •永不停止
实施过程
对现行系统进行分析
•找出缺陷与不足 •明确改进目标
使供应商成为JIT系统的一部分
•保证及时性 •保证可靠性
高库存将掩盖管理过程中的许多缺
案例二:XX轿车焊装车间
推行“拉动式”生产,降低标准在制品储备
XX轿车焊 装车间通 过学习准 时化生产 管理,推 行“拉动 式”生产, 将四门两 盖工段的 大批量生 产改善为 小批量生
产。
案例二:XX轿车焊装车间
采用单品种、大批量的压合和烘干方式。 每个品种烘干完成后,再更换吊具烘干 下一品种。
专用位
备用位
烘干 炉
案例二:XX轿车焊装车间
改善达到的效果
1、只按节拍生产下道工序需要的产品,体现 准时化生产。 2、不会出现零件滞留,保证零件先进先出。 3、小批量生产,很容易保证质量。 4、在制品少,使问题源的追溯性成为可能。 5、减少工位器具,使工作现场整洁有序。 6、能及时暴露出设备停台、生产不均衡等问 题。
案例四:嘉陵股份有限公司
➢降低成品与生产资金占用 •库存比前两年分别降低
✓205.1% ✓120% •生产资金占用分别降低 ✓56.49% ✓44.08%
成效
➢向按需生产模式转换 •适应市场需求 •按照订单生产
➢产品质量有所提高 •成车交验合格率提高10%以上 •良好的声誉和经济效益