VT探伤作业指导书
探伤手工检查作业指导书
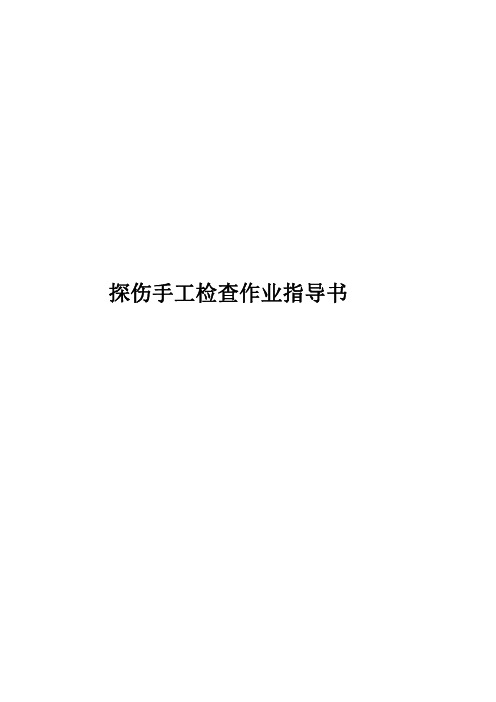
探伤手工检查作业指导书
目次
一、检查工具 (1)
二、钢轨手工检查的程序 (1)
1
仪器无法检查或探伤薄弱处所,正常探伤灵敏度条件下,回波显示和报警不正常,或正常回波不显示处所,此时应考虑手工检查。
一、检查工具
手工锤、反光镜、放大镜、钢丝钩、电筒、活动扳手、钢丝刷等。
二、钢轨手工检查的程序
检查应按照“一看、二敲、三照、四卸”的程序进行。
1、看(目视检查)
全面观察钢轨表面状态,注意发现伤损钢轨所具有的特征,根据这些特征,综合判断钢轨有无伤损。
2
2、敲(小锤检查)
用小锤敲击看所发现的可疑处所或不良接头、道岔部位。
小锤的重量应根据轨型而定,P43以下钢轨用0.5kg 小锤,P50用0.7kg ,P60及其以上用1.0kg 小锤。
3、照(用镜子和电筒检查)
⑴照轨头侧面、下颚及轨腰,从镜子中观看裂纹、绣线或其他伤损特征。
⑵将小镜子伸入轨底,
从轨缝处向上反光或从上面发射光线射入
3
轨缝内(阴天、隧道内可用手电),查看轨端裂纹。
⑶卸下一个螺栓,用双面小镜或袖珍手电插入螺栓孔内,察看螺栓孔裂纹。
4、卸(拆卸螺栓或夹板)
用看、敲、照等方法检查后,发现有疑问而不能确定时,应卸下螺栓或夹板进行检查。
卸夹板时,应按更换夹板作业设好防护,钢轨探伤时需要拆检,应通知巡养工区进行。
作业指导书-目视检验 VT
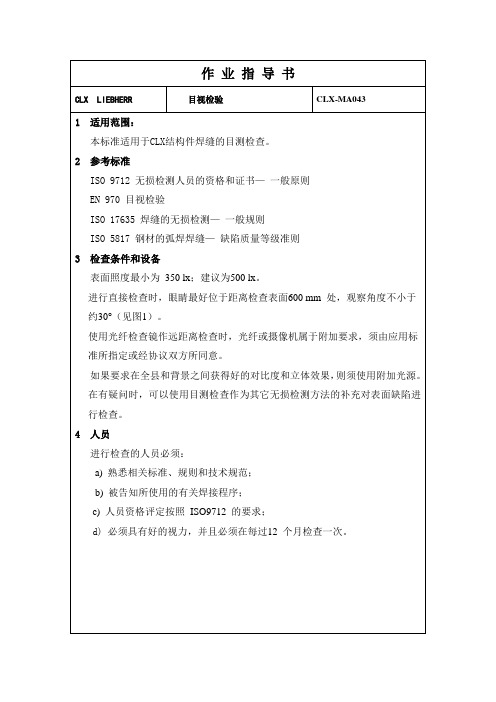
版次日期描述编写审核批准
5 目测检验—总则
检查范围必须由应用标准事先规定,或经协议双方同意。
检查员必须接近焊缝作必要的检查,并取得生产文件。
在可能实际接近的情况下,在同一焊接条件下检查焊缝,有时有必要在表面处理后再作检查。
6 目测检验焊缝的准备
在焊接之前需要进行目测检验时,必须检查:
a) 是否满足在焊接程序技术规范,即按照EN 288-2 标准中指定要求所准
备的焊缝形状和大小;
b) 熔融面和相邻面是否清洁;
c) 待焊接的零件是否按照图纸或说明已经相互固定。
7 焊接时的目视检验
需要的话,在焊接过程中可以进行以下检查:
a) 焊接金属的每道或每层在被另一焊道覆盖之前是否清洁,特别要注意焊
接金属和熔融面之间的连接。
b) 不能有可见缺陷如裂缝或凹坑,如发现这些缺陷,必须汇报以便在进一
步焊接之前采取救治行动。
c) 焊道之间以及焊缝和母材之间的过度在焊接下一焊道之前须有满意的
熔融状态;
d) 坡口的深度和形状必须符合焊接工艺规程(WPS)要求,以保证能按照规
定完全清除焊接金属。
8 完成焊缝的目视检验
8.1 总则。
钢轨探伤作业指导书
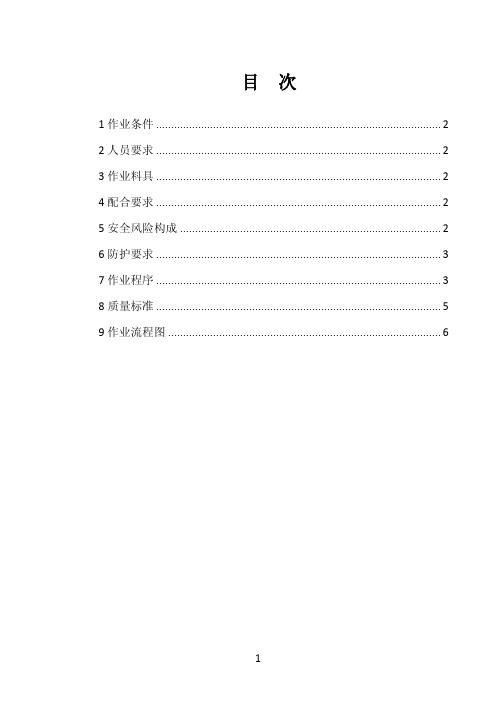
钢轨探伤作业指导书目次1作业条件 (2)2人员要求 (2)3作业料具 (2)4配合要求 (2)5安全风险构成 (2)6防护要求 (3)7作业程序 (3)8质量标准 (5)9作业流程图 (6)1作业条件1.1.1 V≤120km/h线路应在天窗点内作业,根据实际情况而定1.1.2 120km/h>V≤200km/h必须点内作业1.2作业时间根据具体情况确定2人员要求2.1 岗位要求2.1.1施工负责人应由工班长或胜任人员担任。
2.1.2 探伤人员必须经过培训并考试合格2.2人员配置防护人员2人,作业人员不少于4人。
3作业料具钢轨探伤仪1台、活口扳手1把、手工检查锤1把、钢卷尺1个、钢直尺1把、反光镜、照明器具。
4配合要求车务段5安全风险构成5.1违章施工作业风险5.1.1在探伤过程中发现问题不及时回放,造成钢轨折断风险5.1.2 重新上道无回退造成钢轨折断风险5.2从业人员伤害风险5.2.1进入桥梁或长大隧道,探伤前应和巡守人员、驻站联络员联系,掌握列车运行情况。
大桥上探伤时,应沿步行板走行,避免踩空。
5.2.2雨后、凝冻、结冰等天气应做好防滑措施,高道床地段提前下道避车,防止摔伤。
5.2.3施工地段探伤,要注意施工车辆的来往和线路上散放的机具、配件,防止绊脚和碰坏仪器。
6防护要求6.1线路区间作业设置驻站联络员1人、工地防护1人。
6.2道岔区段作业正线道岔作业:设置驻站防护1人、工地防护1人。
站线道岔作业:设置驻站防护1人、工地防护1人。
6.3站内作业正线作业:设置驻站防护1人、工地防护1人。
站线作业:设置驻站防护1人、工地防护1人。
7作业程序7.1探伤前7.1.1 作业负责人应督促检查仪器状态,机具备品和台帐记录簿。
对照作业卡片布置当天作业安排、作业要求,提出安全预警、薄弱地段预报。
并将有关安排和要求填入《探伤工作日志》。
7.1.2 检查仪器各部是否正常,调节仪器灵敏度。
灵敏度调节后须报请施工负责人确认。
无损检测VT PT作业指导书SOP

6.记录和反馈
例图
例图
(2)测量 尺寸; 例图
眼睛应位于距离 600 mm处,观 察角度不小于约30°
主要测量点:焊缝宽度、 余高,缺陷的长处
编制修订履历
主要内容描述 新文件编制
审核/日期:
批准/日期:
5、焊后检 验 (1)清理焊 缝检验区;
检查内容:层间清理氧化皮、 夹渣、气孔等影响焊缝质量
的异物或缺陷
例图
例图
(2)检验; 例图
3、焊前 检验 (1)检查 焊接件坡 例图
(3)检查 焊件定位
例图
(2)检查ห้องสมุดไป่ตู้坡口区域
例图
检查点: 坡口角度
和钝边
检查点:焊 接区
检查点:坡口间 隙和径向错边量
例图
清理掉影响判定的氧化 皮、飞溅等,以免误判
客户名称
适用范围 一作业 流程
1.确认产品和工 艺要求
产品名称 2.检测前准备
检测方法
目视检测VT
碳钢、不锈钢和铝合金焊缝的外观检验
文件编号
3.焊前检测
4.焊中检验
5.焊后检验
二、作 业步骤 1、确认 产品和
根据《客车真空集便装置污物箱技术规格书》,产品污物箱的焊缝外观符合ISO 5817-B,需进行100%VT, 检测内容和要求: (1)对各 个(2焊)对接各件 个焊接件
(3)对各个焊接件焊后焊缝尺寸和外观质量进行检测:①焊缝及热影响区表面不得有气孔、夹渣、裂纹、弧坑 、未填满、焊瘤等缺陷,②焊缝余高≤1+0.15b(mm),③焊接咬边≤0.1t,且最大不能超过0.35mm;
2、检测 前准备 (1)工具 、(2用)检具查准 条(3件)检准测 人员应经
VT探伤作业指导书
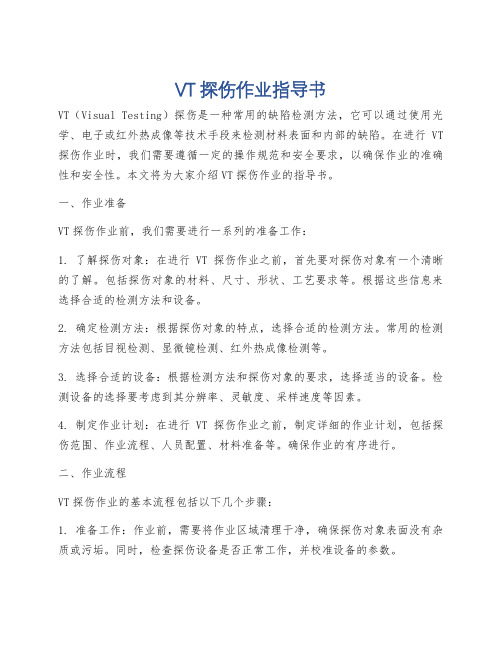
VT探伤作业指导书VT(Visual Testing)探伤是一种常用的缺陷检测方法,它可以通过使用光学、电子或红外热成像等技术手段来检测材料表面和内部的缺陷。
在进行VT 探伤作业时,我们需要遵循一定的操作规范和安全要求,以确保作业的准确性和安全性。
本文将为大家介绍VT探伤作业的指导书。
一、作业准备VT探伤作业前,我们需要进行一系列的准备工作:1. 了解探伤对象:在进行VT探伤作业之前,首先要对探伤对象有一个清晰的了解。
包括探伤对象的材料、尺寸、形状、工艺要求等。
根据这些信息来选择合适的检测方法和设备。
2. 确定检测方法:根据探伤对象的特点,选择合适的检测方法。
常用的检测方法包括目视检测、显微镜检测、红外热成像检测等。
3. 选择合适的设备:根据检测方法和探伤对象的要求,选择适当的设备。
检测设备的选择要考虑到其分辨率、灵敏度、采样速度等因素。
4. 制定作业计划:在进行VT探伤作业之前,制定详细的作业计划,包括探伤范围、作业流程、人员配置、材料准备等。
确保作业的有序进行。
二、作业流程VT探伤作业的基本流程包括以下几个步骤:1. 准备工作:作业前,需要将作业区域清理干净,确保探伤对象表面没有杂质或污垢。
同时,检查探伤设备是否正常工作,并校准设备的参数。
2. 开始探伤作业:按照作业计划和探伤范围,开始进行探伤作业。
根据探伤对象的特点和所选的检测方法,进行探测。
3. 判断缺陷:通过观察探伤结果,判断是否存在缺陷。
缺陷一般分为表面缺陷和内部缺陷两种。
根据缺陷的类型、形状、尺寸等特征,进行判断和记录。
4. 处理缺陷:根据缺陷的性质和要求,对缺陷进行相应的处理。
处理方式可以包括修复、更换、报废等。
5. 作业记录:对探伤作业的过程和结果进行详细的记录,包括探测时间、地点、使用的设备和方法、探测结果等。
三、注意事项在进行VT探伤作业时,需要注意以下几点:1. 安全性:保证作业过程的安全。
例如,使用安全防护设备,注意操作规范,避免因操作不当造成意外伤害。
探伤作业指导书

一、钢轨探伤
1. 目的与要求
目的:钢轨伤损检查。
要求:钢轨伤损的判伤作业人员需具备国家无损检测Ⅰ级及以上资格、焊缝伤损的判伤需具备国家无损检测Ⅱ级及以上资格。
2. 适用范围
2.1 本作业指导书适用于采用钢轨探伤仪对线路钢轨母材及焊缝进行探伤作业。
3. 引用标准
《铁路工务安全规则》、《铁路线路修理规则》、TB/T2340-2012《钢轨超声波探伤仪》、GB/T10061-1999 《A型脉冲反射式超声探伤仪通用技术条件》。
4. 工具材料
4.1 普通线路作业使用的钢轨探伤仪必须符合TB/T2340-2012标准要求。
4.2 防护用品:
4.2.1 上道作业人员必须按规定穿着防护服,夜间必须穿着带有反光标志的防护服。
4.2.2 驻站联络员及现场防护员应按规定携带防护用品和各种记录手册。
5. 作业程序。
射线探伤工艺作业指导书
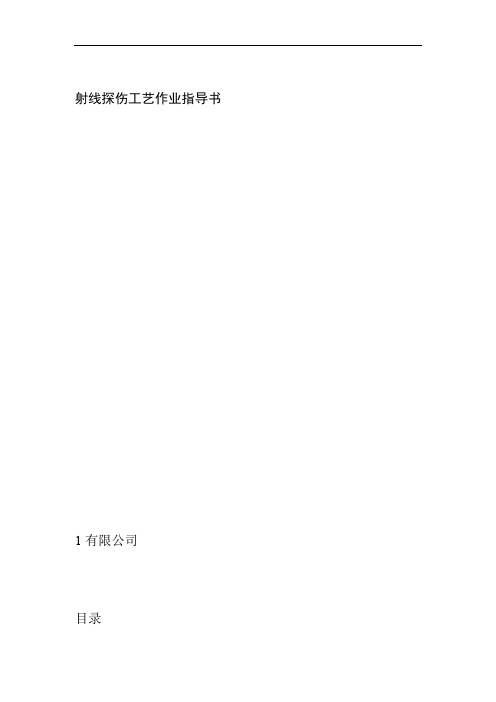
射线探伤工艺作业指导书1有限公司目录1、主题内容2、适用范围3、对探伤人员的要求4、对透照工件表面的要求5、探伤比例的要求及合格级别6、器材的选择7、透照工艺8、胶片的暗室处理9、底片质量10、底片的观察11、记录报告12、安全防护1、主题内容1.1保证工业锅炉对接焊缝射线探伤的准确性,保证锅炉能够正常的运行。
2、适用范围2.1适用于工业锅炉的过热器、省煤器、集箱、压力管道等安装中管-管、管-板对接焊缝射线透照检测。
焊接方式为氩弧焊打底、手工焊盖面。
3、对探伤人员的要求凡从事射线探伤工作人员,都必须经过技术培训,并按3.1.照劳动部文件“锅炉压力容器无损检测人员资格考核规则”进行考核鉴定。
3.2无损检测人员按技术等级分高、中、初级。
取得各技术等级人员,只能从事与该技术等级相应的无损检测工作,并负相应的技术责任。
3.3操作人员应具有RT—I 以上资格证书,评定及审核人员应具有RT—II级以上资格证书。
3.4从射线探伤人员应能辨别距离400mm远的一组高为0.5mm,间距为0.5mm的印刷字母。
4、对透照工件表面的要求4.1焊缝及热影响区的表面质量(包括余高高度)应经外观检查合格。
表面的不规则状态在底片上应不掩盖焊缝中的缺陷或与之相混淆,否则应做适当的修整。
4.2焊缝外观检验合格后,由检验员签发《无损探伤委托书》。
4.3焊缝透照质量达到NB/T47013—2015标准AB级。
5、探伤比例的要求及合格级别5.1探伤比例的要求及合格级别5.2焊缝合格级别达到NB/T47013—2015标准的II级。
6、器材的选择6.1焊缝透照选用理学----300或国产300周向射线探伤机,固定焊缝选用理学-----2505或丹东----2505定向射线探伤机。
胶片选用爱克发型6.2.6.3增感屏选取用厚度为0.03mm的铅箔增感屏,暗盒选用360×80和240×80两种,选用铅质阿拉伯数字英文母。
探伤作业指导书

无损检测作业指导书(磁粉检测部分)1. 目的与范围1.1目的:使我公司涉及的产品无损检测过程得到有效控制。
1.2范围:对API 4F第4版覆盖的井架、底座、天车及API 7K第5版覆盖的绞车输入轴。
2. 引用文件API 4F第4版钻井和修井井架、底座规范API 7K第5版钻井和修井设备AWS D1.1-2008 美国钢结构焊接规范ASME BPVC V-2010 锅炉及压力容器国际性规范V无损检测ASTM E709-2001 磁粉检验的标准推荐操作方法ASNT SNT-TC-1A-2011 无损检测人员的鉴定与认证ASTM E543-09 无损检测机构资格认可的实施标准3. 人员资格直接为我公司进行磁粉检测工作的人员必须经国家技术监督部门授权的机构培训,并按ASNT-SNT-TC-1A(无损检测人员的鉴定与认证)进行鉴定,并取得国家相关部门颁发的磁粉检测Ⅱ级及以上资质证书,矫正视力不得低于1.0,并且一年检查一次,不得有色盲和色弱,持证上岗。
4. 检测设备4.1 CDX-1型荧光磁粉探伤机。
此设备应每年校准一次。
4.2 30/100试片。
用于检测磁粉检测设备、磁粉和磁悬液的综合性能,了解被检工件表面有效磁场强度和方向、有效检测区以及磁化方向是否正确。
4.3磁粉及磁悬液4.3.1选用荧光磁粉、无味煤油配制的浓度为0.5~3.0g/l(沉淀浓度0.1~0.4ml/100ml)的磁悬液。
每8小时或每班次应对湿粉浓度进行一次检查。
4.3.2湿磁粉的浓度应采用梨形离心管测定它的沉淀体积来决定。
在取样之前,通过循环系统旋转磁悬液至少30分钟,取100ml溶液,并允许它沉淀30分钟,在试管底部的沉淀表示溶液中磁粉深度。
荧光磁粉沉淀体积应是100ml,磁悬液中为0.1~0.4ml。
如果磁粉沉淀物显示处松散的聚集而不是一个固体层,则应重新取样,若仍是松散的聚集物,则磁粉可能被磁化,需要更换磁悬液。
4.4 相关设备的检验周期5. 检测工序及其要求5.1 检测工序:API 4F:在焊缝完成并冷却至环境温度后;API 7K:磁粉检测应当在最终热处理和最终机加工后进行检验。
- 1、下载文档前请自行甄别文档内容的完整性,平台不提供额外的编辑、内容补充、找答案等附加服务。
- 2、"仅部分预览"的文档,不可在线预览部分如存在完整性等问题,可反馈申请退款(可完整预览的文档不适用该条件!)。
- 3、如文档侵犯您的权益,请联系客服反馈,我们会尽快为您处理(人工客服工作时间:9:00-18:30)。
V T探伤作业指导书公司标准化编码 [QQX96QT-XQQB89Q8-NQQJ6Q8-MQM9N]
.
广州忆民有限公司
目视检验作业指导书
编制:
审核:
批准:
2012-12-06发布 2012-12-28实施
目视检验作业指导书
1、范围
本文件规定了目视检验的方法及人员等技术管理要求。
本文件适用于碳钢、不锈钢及铝合金焊缝外观检查。
2、人员要求
从事目视检验人员必须取得VTⅡ级及Ⅱ级以上资格证书,有半年以上工作经验方可独立上岗操作。
检测人员必须熟悉和掌握相关的检验标准(如ISO5817、ISO10042)。
检测人员必须熟悉和掌握相应的焊接工艺。
检测人员必须满足ISO 9712的要求(如每12个月检查一次视力),且应当有足够的视力和颜色分辨力。
3、外观检测条件
被检工件表面的光照度应至少达到350Lx,推荐值为500Lx。
眼睛距离被检区域的距离应不超过600mm。
眼睛与被检工件的夹角应大于30°。
经商定可采用其它检测设备,如内窥镜。
图1 外观检测角度示意图
4、环境要求
作业场地应远离翻砂、电焊、潮湿,场所应整洁宽敞。
检验环境光照度应至少达到350Lx,推荐值为500Lx。
5、检测设备
检测尺如直尺、卡尺、塞尺、焊接检验尺。
放大镜的放大倍数为2~5倍,应尽量有刻度。
其它检测仪器如成型量具、镜子、照像机、内窥镜。
6、焊缝的外观检测
焊缝的外观检测的基本范围在所应用的标准中作出了规定:焊缝必须可见且便于检测,检测时间在表面处理之前。
焊缝的外观检测可分三个阶段:——焊前准备的外观检测
——焊接过程中的外观检测
——焊接后的外观检测
焊前准备的外观检测
坡口的形状、尺寸和均匀度必须符合相应标准的有关要求(与焊接工艺规程是否相符)。
坡口的尺寸不能过大。
焊接坡口及界面必须按要求进行清理。
按图纸要求进行装配和固定。
焊接过程中的外观检测
多层焊时,在其进行下道焊道的施焊前,都要进行层间清理(特别是在焊缝金属和母材的过渡区)。
如果一旦发现有裂纹、空穴或其它缺陷,应立即停止施焊,且采取措施加以消除。
注意焊道的结构,以达到足够的熔合比,避免出现未熔合。
坡口和表面的形状应保证焊接不至于出现不规则性。
焊接后的外观检测
焊缝的外观特征(形状和几何偏差)必须满足ISO5817的要求。
焊缝表面应尽可能地均匀,不要出现纵向和横向的缺口。
焊缝表面不应有夹渣和其它的覆盖性缺陷。
机械划痕和可见的表面空穴是不允许的。
如果要求对焊缝进行机械加工,应保证不出现缺口(比如打磨)且不使局部材料出现过热,特别是在向母材的过渡区内。
每次热处理后应重新进行外观检测。
7、返修焊缝的外观检测
清根或新坡口准备
背面清根的深度应足够,应清到焊缝金属。
不规则性应清除干净,然后再进行无损检测。
在修补前所开坡口的角度和宽度,应有利于焊接达到一定的熔化系数。
全部清除焊缝时不得有材料损失。
焊接过程中和焊后的外观检测要求与原始焊接要求一样。
8、测量工具的应用
坡口间隙和错边量的大小对焊接质量有很大影响,因此焊接件装配点固后,可采用焊缝检验尺等焊缝检测设备进行测量。
测量表面缺陷的尺寸和位置可用:游标卡尺、直尺、卷尺或放大镜(有时里面带有刻度)。
测量咬边深度时,使用焊缝检验尺的薄而尖的直边,以焊缝两侧的母材为基准面进行测量。
对接焊缝的余高可用成型量具或焊缝尺等焊缝测量工具来测量。
如果焊缝两侧
厚度不一样,可按下图来计算:22
1
H +
H
=
H。
角焊缝中存在着焊角高度与焊脚长度之间的比例如下图,对此也有不同的量具,如果角焊缝表面不规则,应多测几个位置,焊缝厚度选最低值。
9、
焊接缺陷的种类
焊接缺陷的种类很多,根据标准ISO6520把熔焊缺陷分为六类: 第一类缺陷: 裂纹 第二类缺陷: 孔穴
第三类缺陷: 固态夹渣物 第四类缺陷: 未熔合和未焊透 第五类缺陷: 外观缺陷 第六类缺陷: 其他缺陷。
具体缺陷编号及说明见标准ISO6520。
10、 观察及处理
对缺陷件,须对缺陷的部位、大小、性质在检测报告上做出详细描述,并在工件上做出标识。
11、 质量要求
焊缝的质量等级根据相关的标准(碳钢和不锈钢按照ISO5817、铝合金按照ISO10042)进行判定,并对照图纸要求看是否合格。
返修后部位及热影响区重新进行目视检验。
12、 记录
记录及保存见表1:
求填写及保管。