试模问题点原因分析
模具试模十大问题

模具试模十大问题试模中常见问题1:主浇道粘模解决方法与顺序:1.拋光主浇道→2.喷嘴与模具中心重合→3.降低模具温度→4.缩短注射时间→5.增加冷却时间→6.检查喷嘴加热圈→7.拋光模具表面→8.检查材料是否污染试模中常见问题2:塑件脱模困难解决方法与顺序:1.降低注射压力→2.缩短注射时间→3.增加冷却时间→4.降低模具温度→5.拋光模具表面→6.增大脱模斜度→7.减小镶块处间隙试模中常见问题3:尺寸稳定性差解决方法与顺序:1.改变料筒温度→2.增加注射时间→3.增大注射压力→4.改变螺杆背压→5.升高模具温度→6.降低模具温度→7.调节供料量→8.减小回料比例试模中常见问题4:表面波纹解决方法与顺序:1.调节供料量→2.升高模具温度→3.增加注射时间→4.增大注射压力→5.提高物料温度→6.增大注射速度→7.增加浇道与浇口的尺寸试模中常见问题5:塑件翘曲和变形解决方法与顺序:1.降低模具→2.降低物料温度→3.增加冷却时间→4.降低注射速度→5.降低注射压力→6.增加螺杆背压→7.缩短注射时间试模中常见问题6:塑件脱皮分层解决方法与顺序:1.检查塑料种类和级别→2.检查材料是否污染→3.升高模具温度→4.物料干燥处理→5.提高物料温度→6.降低注射速度→7.缩短浇口长度→8.减小注射压力→9.改变浇口位置→10.采用大孔喷嘴试模中常见问题7:银丝斑纹浇道粘模解决方法与顺序:1.降低物料温度→2.物料干燥处理→3.增大注射压力→4.增大浇口尺寸→5.检查塑料的种类和级别→6.检查塑料是否污染试模中常见问题8:表面光泽差解决方法与顺序:1.物料干燥处理→2.检查材料是否污染→3.提高物料温度→4.增大注射压力→5.升高模具温度→6.拋光模具表面→7.增大浇道与浇口的尺寸试模中常见问题9:凹痕解决方法与顺序:1.调节供料量→2.增大注射压力→3.增加注射时间→4.降低物料速度→5.降低模具温度→6.增加排气孔→7.增大浇道与浇口尺寸→8.缩短浇道长度→9.改变浇口位置→10.降低注射压力→11.增大螺杆背压试模中常见问题10:气泡解决方法与顺序:1.物料干燥处理→2.降低物料温度→3.增大注射压力→4.增加注射时间→5.升高模具温度→6.降低注射速度→7.增大螺杆背压。
模具试模十大问题及解决办法

模具试模十大问题及解决办法模具试横十大问题及解决办法一、试模中常见问题:主浇道粘摸解夫问题的方法与顾序:1抛光主浇道- +2喷嘴与模具中心三合-3降低横其温度4缩短注射时间→5增加冷却时间→6检查喷嘞喊圈+7抛光模具表面→8+检材料是否污染。
二试模中常见问题:塑件脱模因难解夫问题的方法与顾序:1降低注射压力- +2缩短注射时间一→3增加冷却时间+4降低横具温度5抛光模具表面-6增大脱模鈄度-7减小镶块处间隙三试模中常见问题:尺寸稳定性差解夫问题的方法与顺序:1改变料管温度+2增加注射时间+3增大注射压力- +4改变螺杆背压5开高摸具温度-6降低模具温度-7调节供料t -8减小回料比例四试模中常见问题:表面波纹解夫问题的方法与顾序:1调节供料t 2升高摸具温度- +3增加注射时间- -4增大注射压力- +5提: 物料温度+6增大注射速度+7增加落道与浇口的尺寸五、试模中常见问题:塑件翘曲和变形解夫问题的方法与顾序:1降低模具- +2降低物料温度+3增加呤却时间- +4降低注射速度- +5降低注射压力- +6增加螺杆背压→7缩短注射时间六试模中常见问题:塑件脱皮分层解夫问题的方法与顾序:1检查工塑料种类和级别+2检查材料是否污染一+3升:横具温度-+4物料干燥处理-→5提:物料温度→6降低注射速度→7缩短尧口长度+8减小注射压力+9改变浇口位一10采用大孔喷嘴七试模中常见问题:银丝班纹道粘模解夫问题的方法与顾序:1降低物料温度- +2物料干燥处理一+3增大注射压力-+4增大流口尺寸- +5检查塑料的种类和级别- +6检正塑料是否污染八试模中常见问题:表面光泽差解夫问题的方法与顺序:1物料干燥处理- +2检材料是否污染+3提物料温度+4增大注射压力- +5升高摸具温度+6抛光模具表面一+7增大道与浇口的尺寸九试模中常见问题:凹痕解夫问题的方法与顾序:1调节供料量t 2增大注射压力- +3增加注射时间-4降低物料速度+5降低横其温度+6增加啡气孔- -7增大溶道与浇口尺寸→8缩短深道长度→9改变浇口位重-10降低注射压力+11增大螺杆背压+.试模中常见问题:气泡解夫问题的方法与顾序:1物料干燥处理- +2降低物料温度+3增大注射压力+4增加注射时间- +5升模具温度-6降低注射速废-7增大螺杆背压。
注塑模具试模时几种经常出现问题及解决方法
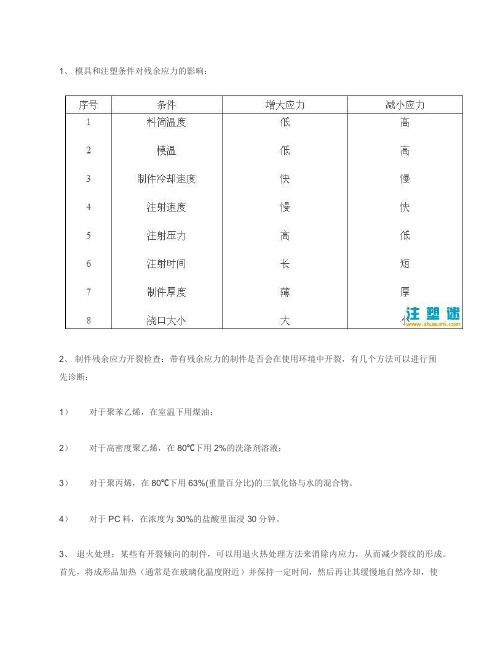
1、模具和注塑条件对残余应力的影响:
2、制件残余应力开裂检查:带有残余应力的制件是否会在使用环境中开裂,有几个方法可以进行预
先诊断:
1)对于聚苯乙烯,在室温下用煤油;
2)对于高密度聚乙烯,在80℃下用2%的洗涤剂溶液;
3)对于聚丙烯,在80℃下用63%(重量百分比)的三氧化铬与水的混合物。
4)对于PC料,在浓度为30%的盐酸里面浸30分钟。
3、退火处理:某些有开裂倾向的制件,可以用退火热处理方法来消除内应力,从而减少裂纹的形成。
首先,将成形品加热(通常是在玻璃化温度附近)并保持一定时间,然后再让其缓慢地自然冷却,使
发生裂纹处的大分子能自由活动、回复原来状态。
这种退火热处理法一般在成形后立即进行。
4、调湿处理:对于尼龙塑件,为了改善内应力分布状况及塑料内的晶体结构,提高制件韧性,保持尺寸相对稳定,可以进行调湿处理,其效果比退火处理更佳。
方法是将制件浸入沸水或醋酸钾水溶液(比例为 1.25:100,沸点121℃)中,浸泡时间视制件最大壁厚而定,从2小时至16小时不等。
10个试模问题解决方法

10个试模问题解决方法试模常见问题1:注浇道粘模解决问题的方法和顺序:1抛光主浇道→2喷嘴与模具中心重合→3降低模具温度→4缩短注射时间→5增加冷却时间→6检查喷嘴加热圈→7抛光模具表面→8检查材料是否污染试模常见问题2:塑料件脱模困难解决问题的方法和顺序:1降低注射压力→2缩短注射时间→3增加冷却时间→4降低模具温度→5抛光模具表面→6增大脱模斜度→7减小镶块处间隙试模常见问题3:尺寸稳定性差解决问题的方法和顺序:1改变料筒温度→2增加注射时间→3增大注射压力→4改变螺杆背压→5升高模具温度→6降低模具温度→7调节供料量→8减少回料比例试模常见问题4:表面波纹解决问题的方法和顺序:1调节供料量→2升高模具温度→3增加注射时间→4增大注射压力→5提高物料温度→6增大注射速度→7增加浇道与浇口的尺寸 试模常见问题5:塑料件翘曲与变形解决问题的方法和顺序:1降低模具→2降低物料温度→3增加冷却时间→4降低注射速度→降低注射压力→6增加螺杆背压→7缩短注射时间试模常见问题6:塑料件脱皮分层解决问题的方法和顺序:1检查塑料件种类和级别→2检查材料是否污染→3升高模具温度→4物料干燥处理→5提高物料温度→6降低注射速度→7缩短浇口长度→8减小注射压力→9改变浇口位置→10采用大孔喷嘴试模常见问题7:银丝斑纹浇道粘模解决问题的方法和顺序:1降低物料温度→2物料干燥处理→3增大注射压力→4增大浇口尺寸→5检查塑料件的种类和级别→6检查塑料是否污染试模常见问题8:表面光泽差解决问题的方法和顺序:1物料干燥处理→2检查材料是否污染→3提高物料温度→4增大注射压力→5升高模具温度→6抛光模具表面→7增大浇道与浇口的尺寸试模常见问题9:凹痕解决问题的方法和顺序:1调节供料量→2增大注射压力→3增大注射时间→4降低物料速度→5降低模具温度→6增加排气孔→7增大浇道与浇口尺寸→8缩短浇道长度→9改变浇口位置→10降低注射压力→11增大螺杆背压试模常见问题10:气泡解决问题的方法和顺序:1物料干燥处理→2降低物料温度→3增大注射压力→4增加注射时间→5升高模具温度→6降低注射速度→7增大螺杆背压。
冲压模具结构与试模问题点

功能 成形模穴 成型冲头 顶出钣件 夹持及顶料 引导滑动用 素材定位 检测素材投放 连接顶杆 定位模具 锁付模具
No. 11 12 13 14 15 16 17 18
名称 成形到底挡块 安全挡板 防尘盖板 安全螺栓 平衡块 逃气孔 吊耳/起吊棒 电气盒
功能 控制成形到底 阻挡异物进入 阻止灰尘进入 避免B/H被拉起 控制钣厚间隙,提 升稳定性 排出模穴空气 模具吊运用 为模具与机台控制 提供连接 储存模具信息载体 防止清洗水堆积
电气盒:用于 连接电气源
模具结构简介
OP20上模
导套:与导柱配 合导向(精导向)
紧固螺栓:固 定压料板,防 松动掉落
上修边刀 (斜楔修边机构)
耐磨板 上模座 氮气缸:为 修边冲孔提 供力 冲孔结构 废料刀
模具结构简介
凹模套
下模 上模
冲孔过程及排废示意图
冲头吃入量:4mm (合理范围3~5mm)
模具结构简介
4、拉毛
模具硬度不够——对模具进行表面处理(渗氮、硬铬电镀) 模具型面有砂眼——仔细检查铸件,处理砂眼 型面不顺过渡不圆滑——抛光模具表面,提高光洁度 B/H与上模,上模与下模之间的间隙过紧——以下模做基准,研磨上模 模具或素材脏——素材擦拭,模具清洗擦拭干净。
5、线位移(板料与模具接触后,在应力集中摩擦造成的表面划痕)
模具结构简介
翻边整形模
10 9 1 2 11 3 4 5 12 6
7
8
N O
1
2 3 4 5
名称
上模座
压料板(PAD) 耐磨板 上折边刀 导根
机能
承载上模零件
压料 引导滑动用 成形折边 上下模具引导
NO
7
8 9 10 11
试模中工艺常见十一问题

试模工艺常见问题一翘曲:解决方案1、框壳产品的翘曲是常见的2、解决方法分为前中后三个时期3、前期设计时可以预放翘曲余量4、中期工艺调整时减少内应力和加长定型时间4、中期工艺调整时减少内应力和加长定型时间5、后期可以在产品出模后完全冷却前用治具再定型二龟裂:为什么会裂呢1 残余应力引起的龟裂:即充填过剩、脱模推出和金属镶嵌件造成的。
作为在充填过剩的情况下产生的龟裂2 外部应力引起的龟裂:这里的外部应力,主要是因设计不合理而造成应力集中,特别是在尖角处更需注意。
3 外部环境引起的龟裂:化学药品、吸潮引起的水降解,以及再生料的过多使用都会使物性劣化,产生龟裂解决方法1:(1)由于直浇口压力损失最小,所以,如果龟裂最主要产生在直浇口附近,则可考虑改用多点分布点浇口、侧浇口及柄形浇口方式。
(2)在保证树脂不分解、不劣化的前提下,适当提高树脂温度可以降低熔融粘度,提高流动性,同时也可以降低注射压力,以减小应力。
(3)一般情况下,模温较低时容易产生应力,应适当提高温度。
但当注射速度较高时,即使模温低一些,也可减低应力的产生。
(4)注射和保压时间过长也会产生应力,将其适当缩短或进行Th次保压切换效果较好。
(5)非结晶性树脂,如AS树脂、ABS树脂、PMMA树脂等较结晶性树脂如聚乙烯、聚甲醛等容易产生残余应力,应予以注意。
脱模推出时,由于脱模斜度小、模具型胶及凸模粗糙,使推出力过大,产生应力,有时甚至在推出杆周围产生白化或破裂现象。
只要仔细观察龟裂产生的位置,即可确定原因。
检查模具流道是否太小,入水位是否太薄,尽量保压压力不要太高三顶白的原因(1)射胶压力过大,产品打的太实,其次顶针压力,产品的冷却时间不足;产品脱模不顺。
(2)后模有倒扣(抛光不足、锣痕、顶针不够,顶针过长……)解决模具稍作修改四粘模原因(1)模具粗糙度太大,模温过高。
脱模斜度太小,材料干燥不彻底,注射压力太大模具的抛光不到位。
解决方案;(1)模具的抛光到位,产品的脱模角度加大,降低模温。
注塑件试模常见问题与解决方法

注塑件试模常见问题与解决方法http:2009年02月14日13:52生意社02月14日讯收縮痕一、注塑件缺陷的特征通常与表面痕有关,而且是塑料从模具表面收缩脱离形成的。
二、可能出现问题的原因(1).熔融温度不是太高就是太低。
(2).模腔内塑料不足。
(3).冷却阶段时接触塑料的面过热。
(4).流道不合理、浇口截面过小。
(5).模温是否与塑料特性相适应。
(6).产品结构不合理(加强进古过高,过厚,明显厚薄不一).(7).冷却效果不好,产品脱模后继续收缩。
三、补救方法(1).调整射料缸温度。
(2).调整螺杆速度以获得正确的螺杆表面速度。
(3).增加注塑量。
(4).保证使用正确的垫料;增加螺杆向前时间;增加注塑压力;增加注塑速度。
(5).检查止流阀是否安装正确,因为非正常运行会引致压力流失。
(6).降低模具表面温度。
(7).矫正流道避免压力损失过大;根据实际需要,适当扩大截面尺寸。
(8).根据所用塑料的特性及产品结构适当控制模温。
(9).在允许的情况下改善产品结构。
(10).设法让产品有足够的冷却。
包封一、注塑件缺陷的特征可以容易地在透明注塑件的“空气阱”内见到但也可出现在不透明的塑料中,这与厚度有关,而且常因塑料收缩离开注塑件中心而引起。
二、可能出现问题的原因(1).模具未充分填充。
(2).止流阀的不正常运行。
(3).塑料未彻底干燥。
(4).预塑或注射速度过快。
(5).某些特殊材料应用特殊的设备生产。
三、补救方法(1).增加射料量。
(2).增加注塑压力。
(3).增加螺杆向前时间。
(4).降低熔融温度。
(5).降低或增加注塑速度。
(例如对非结晶体类的塑料要增加45%速度)。
(6).检查止逆阀是否裂开或无法运作。
(7).应根据塑料的特性改善干燥条件,让塑料彻底干燥。
(8).适当降低螺杆转速和增大背压,或降低注射速度。
制品成型尺寸精度低注塑件缺陷的特征一﹐注塑过程中重量尺寸的变化超过了模具、注塑机、塑料组合的生产能力。
注塑模具试模出现的问题

1、塑件不足:主要由于供料不足,融料填充流动不良,充气过多及排气不良等原因导致填充型腔不满,塑件外形残缺不完整或多型腔时个别型腔填充不满2、尺寸不稳定:主要由于模具强度不良,精度不良,注射机工作不稳定及成形条件不稳定等原因,使塑件尺寸变化不稳定3、气泡:由于融料内充气过多或排气不良而导致塑件内残留气体,并呈体积较小或成串的空穴(注意应与真空泡区别)4、塌坑(凹痕)或真空泡:由于保压补料不良,塑件冷却不匀,壁厚不匀及塑料收缩大时5、飞边过大:由于合模不良,间隙过大,塑料流动性太好,加料过多使塑件沿边缘挤出多余薄片6、熔接不良:由于融料分流汇合时料温低,树脂与附合物不相溶等原因,使融料在汇合时,熔接不良,沿塑件表面或内部产生明显的细接缝线7、塑件表面波纹:由于融料沿模具表面不是整齐流动填充型腔而是成半固化波动状在型腔面流动或融料有滞流现象8、脱模不良:由于填充作用过强,模具脱模性能不良等原因,使塑件脱模困难或脱模后塑件变形、破裂,或塑件残留方向不符合设计要求。
9、云母片状分层脱皮:由于混入异料或模温低,融料沿模具表面流动时剪切作用过大,使料成薄层状剥落,物理性能下降10、浇口粘模:由于浇口套内有机械阻力,冷却不够或拉料杆失灵,使浇口粘在浇口套内11、透明度不良:由于融料与模具表面接触不良,塑件表面有细小凹穴造成光线乱放射或塑料分解,有异物杂质,或模具表面不光亮,使透明塑料透明度不良或不匀12、银丝斑纹:由于料内有水分或充气,及挥发物过多,融料受剪切作用过大,融料与模具表面密合不良,或急速冷却或混入异料或分解变质,而使塑件表面沿料流方向出现银白色光泽的针状条纹或云母片状斑纹13、翘曲,变形:由于成形时残余应力、剪切应力、冷却应力及收缩不均,造成的内应力;脱模不良,冷却不足,塑件强度不足、模具变形等原因,使塑件发生形状畸变,翘曲不平或型孔偏,壁厚不匀等现象14、裂纹:由于塑件内应力过大,脱模不良、冷却不匀,塑料性能不良或塑件设计不良及其它弊病(如变形)等原因,使塑件表面及进料口附近产生细裂纹,或开裂或在负荷和溶剂作用不发生开裂等现象15、黑点、黑条:由于塑料分解或料中可燃性挥发物,空气等在高温高压下分解燃烧,燃烧物随融料注入塑腔,在塑件表面呈现黑点,黑条纹,或沿塑件表面呈炭状烧伤现象16、色泽不匀或变色:由于颜料或填料分布不良,塑料或颜料变色在塑件表面的色泽不匀。
- 1、下载文档前请自行甄别文档内容的完整性,平台不提供额外的编辑、内容补充、找答案等附加服务。
- 2、"仅部分预览"的文档,不可在线预览部分如存在完整性等问题,可反馈申请退款(可完整预览的文档不适用该条件!)。
- 3、如文档侵犯您的权益,请联系客服反馈,我们会尽快为您处理(人工客服工作时间:9:00-18:30)。
飞边:
1:注塑压力太大,进胶口太小
2:模具配模不好
3:模具制造不良,有塌角。
4:抛光时,没有明显的界限
5:插穿面角度太小。
6:封胶位的长度太短。
7:局部的料位太薄。
8:注塑不平衡。
9:行位的锁紧块变形。
10:边在胶口附近很明显的话,说明注塑压力大,模板的强度不够,下面加撑头。
顶白:
1:顶针下的位置不对
2:脱模斜度太小
3:顶针太小
4:模具的表观太粗糙
5:在斜面上的顶针,没有做防滑槽。
6:顶出结构不同步。
(特别是斜顶,直顶的地方,因加工和配模的问题,底部可能和顶针底板有间隙,从而引起顶出不同步)
7:2次顶出结构的拉白,是因为产品没有让位造成的,然后强制顶出。
8:注塑机的顶出力太大,顶出速度太高
9:因模具制造不良,有到扣,如:放电时积碳,过切等
注塑的压力太大:
1:产品设计本身的壁厚不均
2:加工时,有偏差
注塑时镶件有位移。
(踞开产品,产品的断面有就能清楚的看到)
3:双色模的左右2个产品的厚度不一样,此时应考虑,左右2个产品的模仁的高度是不是相等的,前后模闭和后型腔的高度是不是相等的。
(用保险丝压,可以来检测型腔的厚度)。
产品有花纹时料的流动会改变。
做模流分析时要考虑花纹的高度。
4:进胶口在产品的薄壁处。
模板打不开
1:阻力太大、
2:脱模力太小
3:模具升温不一致产生的膨胀系数不一样,而胀死。
4:模具结构不合理,引起的互缩。
注塑不平衡
1:模具的2个型腔的温度不一样,
2:胶口大小不一样
3:流道的长,短不一样
型腔的壁厚不一样
4:2个型腔加工的壁厚不一样
5:热流道的温度进胶不一样,改变热流道的温度。
6:产品在模具中的排位一个上,一个在下面,因重力的关系产生不平衡。
产品的壁厚不均、
产品设计不合理
模具的型芯在注塑时偏位
模具加工的精度,在高度方向不相等
困气:
1:模具上排气不良时,会引起产品的困气。
困气会引起产品起波纹,
困气还引起产品的表面的气雾
2:双色模的2个产品溶接不好
困气必须理解困气的位置是在产品的中间,还是在产品的边缘
开排气的位置要准确。
3:产品的困气,可以通过垫纸片,和薄的铁皮来检测。
粘前模的检验
产品粘在前模后,观察产品在前模是否有间隙来决定产品粘模的具体部位。
通过喷脱模剂来检查
7:注塑压力太高:
料筒的熔胶温度高,注塑的压力会减小
模具的实际温度高,注塑的压力会减小。
模具的冷却水的冷却的效率(如07-066的产品),产品的壁厚不均匀,注塑的压力会加大(07-052的灯体)
模具的排气不好
进胶口的大小
8:产品的开裂
1:开模时开裂,
A:开模时受力不平衡(开模时开裂的检测方法:在模具上用手摸,去感觉裂口的高低,来判断粘模的方位)
B:加工时前模的某一部分有倒扣
C:后模的镶件跟前模动一段距离后,把产品拉伤(07-058行位上的镶件)
2:顶出时开裂,顶出时受力不平衡,(主要要查产品的脱模斜度、产品的骨位和下顶针的位置。
双色模的开裂和预压有关,预压不够会冲裂,预压过多,会在第2次成型合模的过程中,压产品时受力不平衡而压坏。
3:花纹粒子的很容易开裂,和顶出不平衡有很大的关系,花纹粒子对影响产品的壁厚和流动顺序。
要注意花纹粒子的出模方向,不能随便更改产品的出模方向,在没有明确花纹的出模方向前。
利用脱模剂来检测
4:模具的温度分布不均匀,模温太低。
产品有内应力
5:冷却时间过长,产品就会具有内部钢件(模芯)的尺寸和钢件间(如2个销钉位置)的距离,产生内应了,使顶出变形。
针阀式胶口
1:有飞边(直面封胶,针对模具有磨损,一段时间后会有间隙,斜面封胶对针的长度要求比较高
2:模腔的光洁度要求镜面,针的圆锥面和顶面要求镜面。
、
热流道本身对料没有加热,
3:箱的温度显示温度不稳定时,要查看感温线的型号是不是匹配,K型还是J 型。
K型和J型的温度相差50°。
模具漏水
1:防水圈的预压不够、
2:防水圈压坏
3:模具镶件装配不正
4:防水圈周围的螺丝不够,位置太远
5:镶件变形。