原煤工艺系统简介
煤粉制备系统工艺流程简介

水泥厂煤粉制备系统工艺流程简介原煤由汽车运至原煤堆场,预均化堆场最大储量3700t,有效储量3300t,储存期7.12天,经板式喂料机由皮带输送至原煤预均化堆场预均化及储存,堆料能力150t/h,取料能力80t/h,原煤均化后由皮带送至煤磨原煤仓。
煤磨制备采用一台3.8(7.75+3.5)m风扫式煤磨系统,设计原煤水分≤8.5%,原煤进料粒度≤25mm,产品细度R80≤6%时,生产能力41t/h。
原煤经原煤仓、定量给料机喂入煤磨系统,在磨内进行烘干与粉磨,煤粉由出磨气体带入煤磨动态选粉机,分离出的粗粉返回磨头再次粉磨,细粉随气体进入高浓度煤磨专用袋式除尘器,收集下的煤粉送入带有荷重传感器的煤粉仓。
煤粉制备系统利用窑尾废气作为烘干热源。
煤粉仓下设有分解炉及窑头喂煤计量系统,计量后的煤粉气力输送至窑尾分解炉燃烧器和窑头多通道煤粉燃烧器。
第二章煤粉制备系统启停操作及注意事项第一节煤粉制备系统设备启停操作2.1.1 煤磨系统开停机顺序2.1.1.1 煤磨系统开机顺序(1)煤磨辅助系统组(2)煤粉输送设备组(3)收尘、排风机组(4)启动煤磨主电机(5)启动煤磨喂料组(定量给料机)2.1.1.2 煤磨系统停机顺序与开机顺序相反。
2.1.2 煤磨系统的联锁(1)减速机稀油站,进出口大瓦稀油站跳→煤磨跳→定量给煤机跳。
(2)煤磨排风机跳→煤磨选粉机跳→煤磨跳→定量给煤机跳。
2.1.3 运行前的准备工作(1)现场对系统设备进行巡检,确认设备是否具备开机条件。
(2)进行联锁检查,确认现场所有设备均打到“中控”位置,并处于备妥状态。
(3)开机前通知巡检员、窑操。
(4)检查原煤仓、煤粉仓料位,原煤仓料位不足则启动原煤预均化输送组。
(5)通知质管部做好取样准备。
(6)通知巡检员确认灭火系统可随时投入运行。
(7)检查各档板、闸阀位置是否正确,动作是否灵活。
2.1.4 正常操作过程2.1.4.1 窑尾废气作为烘干热源(1)联系窑操及巡检员,检查煤粉制备系统具备启动条件,确认袋收尘温度,各挡板关闭,检查关闭冷风阀及热风阀;(2)启动煤磨辅助设备组,确认各润滑系统正常。
洗煤厂工艺流程

洗煤厂工艺流程简介洗煤厂是指对原煤进行物理或化学方法处理,以去除杂质、提高煤质利用率和热值的工厂。
本文将介绍洗煤厂的工艺流程,包括原煤的处理、洗煤过程、尾矿处理等。
原煤处理原煤是指直接从矿井或采煤场获取的煤炭,通常含有大量的杂质,如岩石、泥土、铁、硫等。
在洗煤厂中,首先需要对原煤进行预处理,以提高洗煤效果。
原煤处理的步骤如下:1.破碎:原煤经过破碎设备进行颚式破碎或冲击破碎,将较大的原煤块破碎成适当的颗粒大小。
2.筛分:破碎后的原煤经过筛分设备,分离出不同粒径的原煤,为洗煤工艺提供适合的原料。
3.除尘:在筛分过程中,通过除尘设备去除原煤中的粉尘等颗粒杂质。
洗煤过程洗煤是指利用物理或化学方法从原煤中去除杂质的过程。
具体的洗煤过程根据洗煤厂的设备和工艺流程的不同而有所差异,下面是一个典型的洗煤过程示例:1.粗煤洗选:筛分出的适当粒径的原煤通过给料设备进入粗煤洗选系统。
这一步是通过重介质分选的方法,利用不同密度的杂质与煤炭的比重差异,将大部分密度高的杂质从原煤中分离出来。
2.中煤洗选:粗煤洗选后的煤炭通过给料设备进入中煤洗选系统。
这一步是通过浮选法或重介质分选法,去除煤炭中的轻质杂质,如泥土、岩石碎屑等。
3.精煤洗选:中煤洗选后的煤炭通过给料设备进入精煤洗选系统。
这一步是通过浮选法、重介质分选法、干燥选煤法等方法,进一步提高煤炭品质,去除煤炭中的硫、铁等有害元素。
4.脱水:精煤洗选后的煤炭通过脱水设备进行脱水处理,去除多余的水分。
尾矿处理洗煤过程产生的尾矿是指洗煤过程中分离出的含有较多杂质的煤矸石。
为了减少对环境的污染,洗煤厂还需要对尾矿进行处理。
尾矿处理的方法主要有以下几种:1.浸出法:将尾矿浸出,去除其中的可溶性盐类,减少对水质的污染。
2.卤化渣处理:利用卤化渣处理设备对尾矿中的重金属离子进行沉淀,减少对环境的危害。
3.填埋法:将尾矿进行填埋,采取合理的封闭和防渗措施,防止对地下水和土壤的污染。
结论洗煤厂的工艺流程主要包括原煤处理、洗煤过程和尾矿处理。
动筛车间工艺系统优化简介

动筛车间工艺系统简介山东泰安煤矿机械有限公司夏祯华2012-2-15动筛车间工艺系统简介根据矿方产品需求,我们选用液压动筛跳汰机进行排矸,设计了动筛车间,制定了详细的工艺流程,本动筛车间主要由动筛排矸系统、粗煤泥回收系统、煤泥浓缩压滤系统、产品储运系统三部分组成。
分述如下:一、动筛排矸系统:1、简述:井下原煤进入动筛车间后首先进入分级筛进行筛分,分级筛选用分段分级筛,前段筛板孔为50mm, 后段筛板孔为300mm。
<50mm的原煤由分级筛下后部溜槽直接到末煤运输皮带,通往洗煤厂或储煤仓。
50mm—300mm的原煤由分级筛下前部溜槽进入动筛入料皮带转进动筛跳汰机。
>300mm的原煤由筛面上进入破碎机,破碎到200mm粒度以下,通过分级筛前部溜槽进入动筛跳汰机。
通过动筛跳汰机地运转产出块煤、矸石两种产品,经运输皮带进入块煤、矸石仓。
为了更好的提高动筛车间的使用效率,考虑到如若原煤分级筛等设备出现短暂检修等情况会影响矿方生产,我们预留了事故通道。
该事故通道在皮带下溜槽中加设一翻板,平常生产时通过皮带下后部溜槽进入动筛进行分选,原煤分级筛或动筛等设备检修时打开溜槽翻板,原煤由皮带下前部溜槽直接进入分级筛前部溜槽到破碎机进行破碎至<50mm,然后进入末煤皮带。
2、动筛排矸系统分为以下几条通道:1)、末煤运输通道:原煤皮带201→皮带下后部溜槽→原煤分段分级筛202→分级筛下后部溜槽→末煤皮带210→洗煤厂或储存仓2)、块煤运输通道:①、原煤皮带201→皮带下后部溜槽→原煤分段分级筛202→分级筛下前部溜槽→动筛入料皮带204→动筛跳汰机205→块煤皮带211→块煤仓②、原煤皮带201→皮带下后部溜槽→原煤分段分级筛202→分级筛筛前溜槽→破碎机203→分级筛下前部溜槽→动筛跳汰机205→块煤皮带211→块煤仓3)、矸石运输通道:动筛跳汰机205→动筛排矸溜槽→矸石皮带213→矸石仓4)事故运输通道:①当振动筛出现故障:原煤皮带201→皮带下前部溜槽→原煤分段分级筛202→分级筛下前部溜槽(打开翻版)→破碎机218→末煤皮带210→洗煤厂或储存仓②当动筛出现故障,振动筛能正常运转时:原煤皮带201→皮带下后部溜槽→原煤分段分级筛202→分级筛下前部溜槽(打开翻版)→破碎机218→末煤皮带210→洗煤厂或储存仓二、粗煤泥回收系统:1、简述:动筛跳汰机分选过程中产生的煤泥由斗式提升机206提出,经斗式提升机排料溜槽进入高频筛208脱水,脱水后的产品,通过高频筛筛前溜槽进入末煤转载带式输送机,与末煤掺混一同输送至洗煤厂或储煤仓。
洗煤厂工艺及设备

洗煤厂工艺及设备洗煤的流程煤炭加工、矸石处理、材料和设备输送等构成了矿井地面系统。
其中地面煤炭加工系统由受煤、筛分、破碎、选煤、储存、装车等主要环节构成。
是矿井地面生产的主体。
受煤受煤是在井口附近设有一定容量的煤仓,接受井下提升到地面的煤炭,保证井口上下均衡连续生产。
筛分用带孔的筛面把颗粒大小不同的混合物料分成各种粒极的作业叫筛分。
晒分所用的机器叫筛分机或者筛子。
在选煤厂中,筛分作业广泛地用于原煤准备和处理上。
按照筛分方式不同,分为干法筛分和湿法筛分。
破碎把大块物料粉碎成小颗粒的过程叫做破碎。
用于破碎的机器叫做破碎机。
在选煤厂中破碎作业主要有以下要求:1)适应入选颗粒的要求;精选机械所能处理的煤炭颗粒有一定的范围度,超过这个范围的大块要经过破碎才能洗选;2)有些煤快是煤与矸石夹杂而生的夹矸煤,为了从中选出精煤,需要破碎成更小的颗粒,使煤和矸煤分离;3)满足用户的颗粒要求,把选后的产品或煤快粉碎到一定的粒度。
物料粉碎主要用机械方法,有压碎、劈碎、折断、击碎、磨碎等几种主要方式。
选煤利用与其它物质的不同物理、物理-化学性质,在选煤厂内用机械方法去处混在原煤中的杂质,把它分成不同质量、规格的产品,以适应不同有户的需求。
按照选煤厂的位置与煤矿的关选煤厂可以分为:矿井选煤厂、群矿选煤厂、中心选煤厂和用户选煤厂;我国现有的洗煤厂大多是矿井洗煤厂。
现代化的洗煤厂是一个由许多作业组成的连续机械加工过程。
存储储煤仓:为调节产、运、销之间产生的不平衡,保证矿井和运输部门正常和均衡生产而设定的有一定容量的煤仓,接受生产成品煤炭,保证能顺利出厂,进入最后的装车阶段。
装车包括装车(船)、吊车和计量。
选煤是利用煤炭与其他矿物质的不同物理、物理一化学性质,在选煤厂内用机械方法除去原煤中的杂质,把它分成不同质量、规格的产品,以适应不同用户的要求。
原煤在生成过程中混入了各种矿物杂质,在开采和运输过程中不可避免地又混入顶板和底板的岩石及其他杂质(木材、金属及水泥构件等),随着采煤机械化程度的提高和地质条件的变化,原煤质量将越来越差,表现在混入原煤的矸石增加、灰分提高、末煤及粉煤含量增长、水分提高。
工艺原理与流程概述
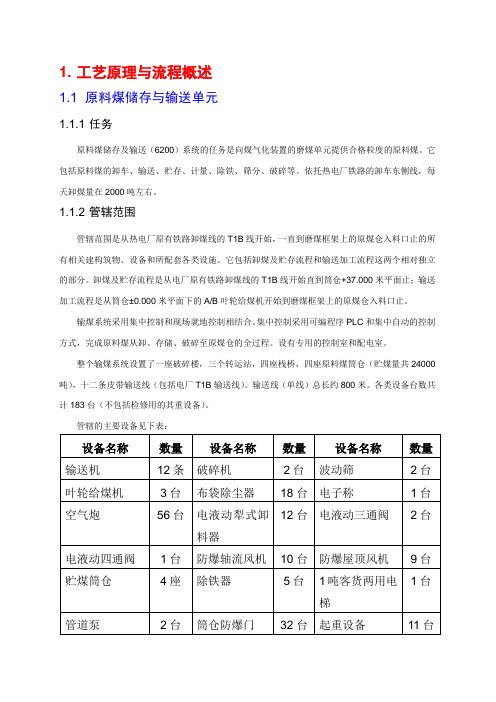
1. 工艺原理与流程概述1.1 原料煤储存与输送单元1.1.1 任务原料煤储存及输送(6200)系统的任务是向煤气化装置的磨煤单元提供合格粒度的原料煤。
它包括原料煤的卸车、输送、贮存、计量、除铁、筛分、破碎等。
依托热电厂铁路的卸车东侧线,每天卸煤量在2000吨左右。
1.1.2 管辖范围管辖范围是从热电厂原有铁路卸煤线的T1B线开始,一直到磨煤框架上的原煤仓入料口止的所有相关建构筑物、设备和所配套各类设施。
它包括卸煤及贮存流程和输送加工流程这两个相对独立的部分。
卸煤及贮存流程是从电厂原有铁路卸煤线的T1B线开始直到筒仓+37.000米平面止;输送加工流程是从筒仓±0.000米平面下的A/B叶轮给煤机开始到磨煤框架上的原煤仓入料口止。
输煤系统采用集中控制和现场就地控制相结合。
集中控制采用可编程序PLC和集中自动的控制方式,完成原料煤从卸、存储、破碎至原煤仓的全过程。
设有专用的控制室和配电室。
整个输煤系统设置了一座破碎楼,三个转运站,四座栈桥,四座原料煤筒仓(贮煤量共24000吨),十二条皮带输送线(包括电厂T1B输送线)。
输送线(单线)总长约800米。
各类设备台数共计183台(不包括检修用的其重设备)。
管辖的主要设备见下表:以及所属的工艺管道、电器设备、仪表仪器等。
1.1.3 主要工艺流程和设备原理1.1.3.1 卸煤及贮存流程原料煤(淮北刘二矿煤)由火车运至热电厂铁路卸车东侧线,由位于其上的2台螺旋卸煤机同时卸车,卸入东侧缝式卸煤槽里。
缝式卸煤槽内的原料煤经T1B叶轮给煤机刮入T1B带式输送机上,经T1B带式除铁器一级除铁后(上述设备为热电厂原有的),通过1#转运楼转运至1#带式输送机(VA-6201),1#带式输送机上的原料煤经1#电子皮带称(VW-6201)计量后,通过2#转运楼电液动四通换向阀的切换转运到2#A/B带式输送机(VA-6202A/B)上或直接落入1#煤筒仓,最后2#A/B 带式输送机上的原料煤通过1#~6#A/B电液动犁式卸料器(VM-6202~6207A/B)的分流,进入1#~4#贮煤筒仓贮存。
选煤厂工艺流程
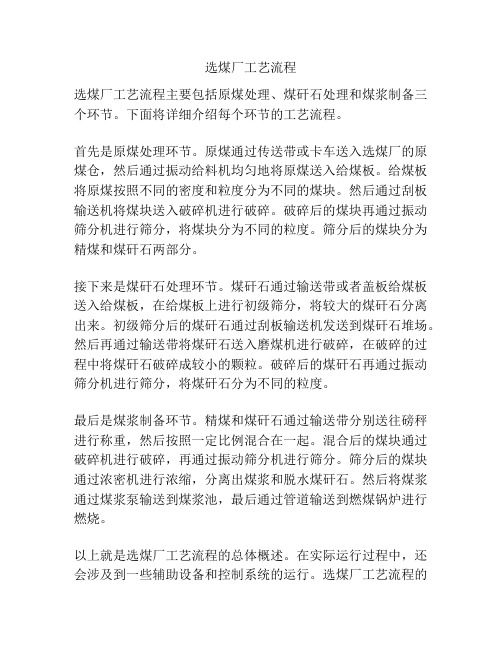
选煤厂工艺流程选煤厂工艺流程主要包括原煤处理、煤矸石处理和煤浆制备三个环节。
下面将详细介绍每个环节的工艺流程。
首先是原煤处理环节。
原煤通过传送带或卡车送入选煤厂的原煤仓,然后通过振动给料机均匀地将原煤送入给煤板。
给煤板将原煤按照不同的密度和粒度分为不同的煤块。
然后通过刮板输送机将煤块送入破碎机进行破碎。
破碎后的煤块再通过振动筛分机进行筛分,将煤块分为不同的粒度。
筛分后的煤块分为精煤和煤矸石两部分。
接下来是煤矸石处理环节。
煤矸石通过输送带或者盖板给煤板送入给煤板,在给煤板上进行初级筛分,将较大的煤矸石分离出来。
初级筛分后的煤矸石通过刮板输送机发送到煤矸石堆场。
然后再通过输送带将煤矸石送入磨煤机进行破碎,在破碎的过程中将煤矸石破碎成较小的颗粒。
破碎后的煤矸石再通过振动筛分机进行筛分,将煤矸石分为不同的粒度。
最后是煤浆制备环节。
精煤和煤矸石通过输送带分别送往磅秤进行称重,然后按照一定比例混合在一起。
混合后的煤块通过破碎机进行破碎,再通过振动筛分机进行筛分。
筛分后的煤块通过浓密机进行浓缩,分离出煤浆和脱水煤矸石。
然后将煤浆通过煤浆泵输送到煤浆池,最后通过管道输送到燃煤锅炉进行燃烧。
以上就是选煤厂工艺流程的总体概述。
在实际运行过程中,还会涉及到一些辅助设备和控制系统的运行。
选煤厂工艺流程的目的是通过对原煤的处理,提高煤的质量,使其适合使用作为燃料。
需要注意的是,选煤厂工艺流程在不同的选煤厂可能会有所差异,具体的流程和设备配置会根据实际情况进行调整。
此处提供的工艺流程仅作为参考,具体的工艺流程应根据选煤厂的实际情况进行设计和调整。
火力发电厂的生产工艺流程分析介绍
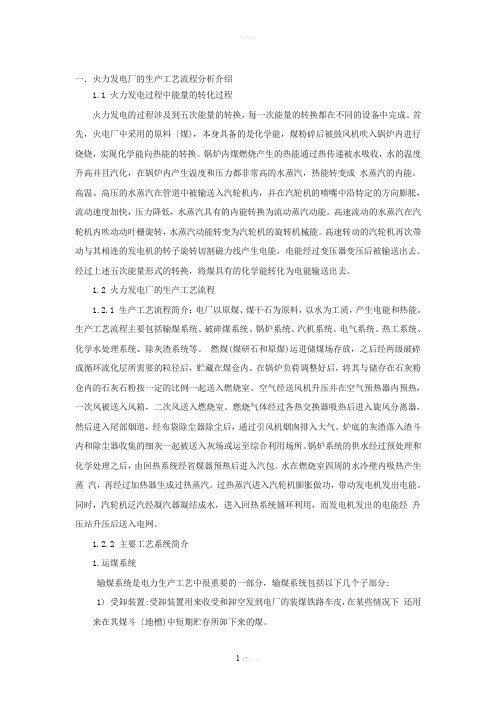
一.火力发电厂的生产工艺流程分析介绍1.1 火力发电过程中能量的转化过程火力发电的过程涉及到五次能量的转换,每一次能量的转换都在不同的设备中完成。
首先,火电厂中采用的原料〔煤),本身具备的是化学能,煤粉碎后被鼓风机吹入锅炉内进行烧烧,实现化学能向热能的转换。
锅炉内煤燃烧产生的热能通过热传递被水吸收,水的温度升高并且汽化,在锅炉内产生温度和压力都非常高的水蒸汽,热能转变成水蒸汽的内能。
高温、高压的水蒸汽在管道中被输送入汽轮机内,并在汽轮机的喷嘴中沿特定的方向膨胀,流动速度加快,压力降低,水蒸汽具有的内能转换为流动蒸汽动能。
高速流动的水蒸汽在汽轮机内吹动动叶栅旋转,水蒸汽动能转变为汽轮机的旋转机械能。
高速转动的汽轮机再次带动与其相连的发电机的转子旋转切割磁力线产生电能,电能经过变压器变压后被输送出去。
经过上述五次能量形式的转换,将煤具有的化学能转化为电能输送出去。
1.2 火力发电厂的生产工艺流程1.2.1 生产工艺流程简介:电厂以原煤、煤干石为原料,以水为工质,产生电能和热能。
生产工艺流程主要包括输煤系统、破碎煤系统、锅炉系统、汽机系统、电气系统、热工系统、化学水处理系统、除灰渣系统等。
燃煤(煤研石和原煤)运进储煤场存放,之后经两级破碎成循环流化层所需要的粒径后,贮藏在煤仓内。
在锅炉负荷调整好后,将其与储存在石灰粉仓内的石灰石粉按一定的比例一起送入燃烧室。
空气经送风机升压并在空气预热器内预热,一次风被送入风箱,二次风送入燃烧室。
燃烧气体经过各热交换器吸热后进入旋风分离器,然后进入尾部烟道,经布袋除尘器除尘后,通过引风机烟囱排入大气。
炉底的灰渣落入渣斗内和除尘器收集的细灰一起被送入灰场或运至综合利用场所。
锅炉系统的供水经过预处理和化学处理之后,由回热系统经省煤器预热后进入汽包。
水在燃烧室四周的水冷壁内吸热产生蒸汽,再经过加热器生成过热蒸汽。
过热蒸汽进入汽轮机膨胀做功,带动发电机发出电能。
同时,汽轮机泛汽经凝汽器凝结成水,进入回热系统循环利用,而发电机发出的电能经升压站升压后送入电网。
棋盘井洗煤厂工艺简介(改造后)

棋盘井选煤厂生产系统及工艺介绍生产系统介绍棋盘井选煤厂是一座设计年入选原煤4.0Mt/a的矿区型焦煤选煤厂。
全厂生产系统可分为:原煤入仓系统、原煤分选系统及成品煤运输系统三部分。
分选系统采用无压给料三产品重介旋流器主选+煤泥重介+直接浮选的联合工艺流程。
成品煤运输系统可实现汽车短倒运输和铁路系统运输。
生产工艺的介绍:矿井来煤和外调原煤分别经运输皮带和配煤刮板,分配至四个原煤仓。
入仓原煤经仓下24台给煤机将原煤按要求比例给入准备车间。
原煤在准备车间经分级、捡矸、除杂、破碎后输至主厂房。
进入厂房的原煤由刮板机平均分配给两台无压给料三产品重介旋流器进行重介分选,选后的精煤、中煤、矸石分别经弧形筛、脱介筛脱介脱水后,矸石脱介筛筛上物运至矸石仓;精煤、中煤脱介筛筛上物分别进入精煤、中煤卧式离心机进一步脱水,最终卸入各自的产品皮带。
重介分选工艺中,六台精煤脱介筛合格介质段增设喷水,合介段筛下物经分流部分物料进入煤泥重介分选系统,分选后的溢流进入精煤稀介桶,底流进入中矸稀介桶。
介质回收系统中,精煤稀介和中矸稀介单独回收。
精煤稀介经六台精煤磁选机回收介质,磁旋尾矿通过六台击打弧形筛实现截粗后,筛上粗粒精煤经煤泥离心脱水机脱水后进入精煤皮带;筛下物给入一段浮选入料桶,再经泵给入一段浮选机;一段浮选尾煤进入二段浮选缓冲桶,再经泵打入二段浮选机进行分选。
二段浮精和一段浮选精煤混合,经三台精煤加压过滤机脱水后,卸入精煤产品皮带。
二段浮选的尾煤连同中矸稀介磁选尾矿进入一段斜管浓缩池。
一段斜管浓缩浓底流经卧式沉降离心脱水机脱水后卸入中煤皮带,溢流进入二段耙式浓缩沉降池。
二段浓缩底流由快开式板框压滤机脱水后,形成最终成品——煤泥,二段浓缩溢流连同加压过滤机滤液、板框压滤滤液汇至浓缩池。
由三台多级离心空压机提供的压缩空气,经风包连接至精煤加压过滤机和快开式压滤机。
循环水池的水经循环水泵打入精煤、中煤、矸石脱介筛,用作筛上喷水及各处生产补水、清扫卫生使用。
- 1、下载文档前请自行甄别文档内容的完整性,平台不提供额外的编辑、内容补充、找答案等附加服务。
- 2、"仅部分预览"的文档,不可在线预览部分如存在完整性等问题,可反馈申请退款(可完整预览的文档不适用该条件!)。
- 3、如文档侵犯您的权益,请联系客服反馈,我们会尽快为您处理(人工客服工作时间:9:00-18:30)。
3.3 工艺系统说明3.3.1 一号转载点根据招标文件提供的资料,井下毛煤存在特大块(400mm*300mm*300mm),这些大块物料撕胶带、砸设备、砸仓底、堵溜槽,给选煤厂的正常生产带来极大的危害。
因此,在原煤仓之前首先篦除特大块物料并将井下原煤破碎至 200mm 以下,为后续作业正常生产创造条件。
一号转载点采用钢筋混凝土框架结构形式,内设 1 台 10t 电动葫芦,用于日常检修维护。
车间内其它部位考虑了起吊和检修空间、起吊运输梁或吊环等起吊设施。
转载点内布置有楼梯间、提升孔。
矿井原煤进入一号转载点 2 台固定筛(筛孔 600mm),筛上+600mm 特大块直接落到室外的矸石池外排,筛下 600-0mm 进入 2 台双齿辊破碎机破碎至 200mm 以下后经皮带转载进入原煤仓储存。
室内各层设有冲洗水和地漏,到一层通过地沟汇集至集水坑,坑内布置一台斗提机,坑内煤泥经斗提机脱水提升后落入底层原煤皮带上,煤泥水由扫地泵回收转排至主厂房矸石脱介筛。
3.3.2 原煤仓原煤采用 2 个φ30m 钢筋混凝土圆筒仓储存,单仓储量为 2.8 万t。
原煤仓设有 1 台载货电梯,大的设备部件通过原煤仓顶部设置的电动葫芦由提升孔提升。
人员上下通行及设备部件运输提升十分方便安全。
原煤仓布置时,充分考虑了人行通道、设备提升及检修空间。
仓上、仓下均设有排污泵。
原煤仓上通过 2 台刮板配仓,每个仓下设 16 台甲带式给煤机,仓内原煤通过给煤机给到仓下 2 条转载皮带上,皮带机头溜槽分岔,仓下原煤可以经 2 号转载点的任一条皮带转载进入主厂房洗选。
室内冲洗水通过地沟汇集至 2 个集水坑,每个坑内布置 1 台斗提机,坑内煤泥经斗提机脱水提升后落入仓下原煤转载皮带上,煤泥水由扫地泵转排至 2号转载点集水坑,再由泵打至主厂房脱介筛。
在东侧的原煤仓下向东布置一条转载皮带供仓内原煤临时地销。
在原煤仓的东侧预留后期一个原煤仓(φ30m)的位置。
一期原煤仓上配仓刮板机的驱动装置按照后期配三个原煤仓的情况一次考虑到位。
3.3.3 主厂房主厂房采用钢筋混凝土框架结构,楼面为钢筋混凝土楼面,厂房内按双系统布置,原煤分级系统、块煤脱泥系统、块煤分选系统、末煤脱水系统、粗煤泥回收系统、固液分离系统、压滤系统进行大厅式分区布置,系统按照。
车间内分区设置有 1 台 20/5t 电动双梁起重机(大钩用于设备的整机起吊、更换检修、安装,小钩用于日常检修维护)、1 台 10t 电动单梁起重机、3 台 10t 电动葫芦、2 台 5t 电动葫芦。
厂房内主要区域均在 7台起重设备的操控之下,设备安装、检修、提升极为方便。
所有设备的主要部位均考虑了起吊和检修空间、起吊运输梁或吊环等起吊设施,并配有足够吨位的手动葫芦和手动单轨小车。
主厂房内考虑足够的人行空间,每层之间至少留有 3 个主要人行通道。
所有人行爬梯角度小于 45°,宽度不小于 1m。
合理设置设备的检修操作平台和安全护栏,车间内人员通行畅通、安全。
主厂房北侧布置 1 台载货电梯,厂房北侧底层布置卫生间,厂房内(各层总和)布置 600m2的工具间和 600m2材料房,在厂房脱介筛层布置 20m2的控制室。
主厂房洗选工艺为:块煤重介浅槽分选+末煤脱水回收+粗煤泥脱水回收+细煤泥固液分离+压滤联合回收。
块煤分选系统、末煤脱水回收系统、粗煤泥脱水回收系统、压滤系统均按双系统平行布置,根据生产需要可以灵活组合开启需要的生产系统。
根据不同的原煤煤质和市场要求,主厂房工艺系统具有全面的灵活性,完全可以满足产品结构对生产方式及工艺灵活性的要求。
(1)原煤准备系统原煤仓下原煤进入主厂房东侧 28.80m 平面的 4 台双层弛张筛(3685 型,上层筛孔30mm,下层筛孔 8mm)分级,原煤被分成200-30mm 大块煤、30-8mm 中块煤和-8mm 末原煤,200-30mm 大块煤和 30-8mm 中块煤混合进入主厂房东侧 24.30m 平面的 4 台块煤脱泥筛(3048 直线筛),-8mm 末煤则经过主厂房东侧 20.80m 平面的 2 条收集皮带转载至主厂房南侧 3.60m 平面的末煤转载皮带落入末原煤出厂皮带或经过主厂房南侧 14.80m 平面的二期末煤入洗皮带进入二期主厂房洗选。
当原煤全部不分选直接作为产品:A、拆除弛张筛下层 8mm 筛板,只保留上层 30mm 筛板,筛上200-30mm 原煤经过主厂房中部 14.80m 平面的 2 台块原煤转载刮板转载进入 7.80m 平面的 2 台块煤分级筛(2448直线筛)进行 80mm 分级,分成 200-80mm 大块原煤、80-30mm 中块原煤,弛张筛筛下-30mm末煤经皮带转载落入末原煤皮带。
B、弛张筛上层筛板更换为 50mm 筛孔,拆除弛张筛下层 8mm 筛板,筛上 200-50mm 原煤经过 14.80m 平面的 2 台块原煤转载刮板转载进入 7.80m 平面的 2 台双齿辊破碎机破碎至-50mm,与弛张筛筛下-50mm 混合后作为产品。
(2)末煤脱水回收系统进入块煤洗选系统的 200-8mm 块煤经 4 台块煤脱泥筛 6mm 湿法脱泥,筛下水进入主厂房±0.00m 平面的煤泥水桶(φ5500mm),经泵打至二期主厂房末煤脱泥筛作为末煤脱泥润湿水;当末煤不入洗时则经过 14.80m 平面的 2 台振动弧形筛(B=2400mm)、2 台末煤脱水筛(2448 直线筛),2 台末煤离心机(φ1500mm 卧式)脱水后,经过7.80m 平面的转载刮板进入末煤转载皮带后掺入末原煤,筛下煤泥水及离心液进入块煤煤泥水桶(φ5500mm)。
(3)块煤重介分选系统脱泥筛上块煤进入主厂房 20.80m 平面的 2 台重介浅槽分选机(B=7.9m)分选,分选出块精煤和块矸石。
浅槽溢流经固定筛和14.80m 平面的 2 台块精煤脱介筛(4373 双层香蕉筛,30mm/1.5mm)脱介、脱水,上层筛上 200-30mm 块精煤可直接经过 7.80m 平面的 2台块煤分级筛进行 80mm 分级,分级筛上 00-80mm 洗大块落入厂房中部 7.80m 平面的大块煤出厂皮带,分级筛下 80-30mm 洗中块落入厂房中部±0.00m 平面的中块煤出厂皮带,200-30mm 块精煤也可通过 .80m 平面的 2 台双齿辊破碎机破碎到-50mm 作为末精煤产品;下层筛上 30-1.5mm 小块经过的 2 台末精煤离心机(φ1500mm 卧式)脱水后作为末精煤产品。
浅槽底流经过主厂房南侧和北侧 14.80m 平面的 2 台矸石脱介筛(3661 单层香蕉筛)脱介、脱水后作为矸石产品落入厂房中部 7.80m 平面的矸石出厂皮带。
(4)块煤介质回收系统块精煤固定筛下的合格介质,经分流后大部分和块精煤脱介筛、块矸石脱介筛筛下合格介质一起返回厂房东部±0.00m 平面的 2 个块煤合格介质桶(φ5500mm)循环使用。
分流出的少部分合格介质,与块精煤脱介筛和块矸石脱介筛下的稀介质一起,进入厂房东部 7.80m 平面的 6 台磁选机(Φ1219×2972mm)磁选回收磁铁矿粉,磁选精矿返回块煤合格介质桶,磁选尾矿进入块煤煤泥水桶。
主厂房底层布置 1 个合格介质转排桶(φ5500mm)和转排泵,当合格介质桶检修时,满足合格介质的临时存储。
每个合格介质桶对应 1 台合介泵、1 台转排泵。
每台浅槽分选机单独设置自动分流和密度调节装置,在块煤合格介质泵的入口管路安装有自动加水阀,可实现系统密度的自动调节和运行。
(5)块煤粗煤泥回收系统末煤脱水筛筛下水和末煤离心液(二期时进入一个块煤煤泥水桶,经泵打至二期主厂房末煤脱泥筛作润湿水)以及块煤磁选尾矿(二期时进入另一个煤泥水桶,与末煤脱水筛下水和离心液分开)进入厂房东侧±0.00m 平面的 2 个煤泥水桶,经泵打至主厂房西南侧 20.80m 平面的 4 台分级旋流器组(Ф500mm×4)分级,分级旋流器底流经过 14.80m平面的 4 台振动弧形筛(B=2100mm)脱水,筛上物料进入 7.80m 平面的 4 台煤泥离心机(φ1200mm 立式)脱水后落入末原煤皮带,分级旋流器溢流、弧形筛下水和离心液进入块煤浓缩机(φ45m)。
(6)块煤细煤泥回收系统块煤浓缩机底流,经泵打至主厂房东侧 20.80m 平面的 1 个固液分离机入料缓冲箱,再给入厂房东侧 14.80m 平面的 3 台固液分离机离心脱水,离心煤泥经过 7.80m 平面的 1台刮板转载至末煤转载皮带后落入末原煤皮带。
浓缩底流也可以打至主厂房西侧±0.00m平面的 2 个压滤机入料缓冲桶(φ5500mm),再经泵打入厂房西侧 14.80m 平面的 4 台快56开隔膜压滤机(F=800m2)脱水,滤饼经 7.80m 平面的 4 台煤泥刮板收集,再经 1 台煤泥转载刮板转载后进入 3.60m 平面的 1 台煤泥破碎机破碎后落入末原煤皮带。
固液分离机离心液和滤液返回浓缩机。
根据市场需要预留压滤煤泥经转载后掺入矸石的通道和接口,浓缩机溢流作为澄清水返回系统复用,实现洗水闭路循环。
3.3.4 浓缩车间浓缩车间选用 2 台Φ45m 的周边传动高效浓缩机(加盖),其中 1 台Φ45m 浓缩机为备用浓缩机。
在浓缩池中间布置有循环水池和泵房,来自主厂房洗选系统的煤泥水,经沉淀浓缩后底流打回主厂房进行固液分离脱水或压滤。
溢流作为循环水重复使用。
浓缩池底流管要与浓缩池套管连接,不能将底流管与浓缩池混凝土部分直接浇注。
在每根底流管上加一路稀释水管道(管径不小于DN50mm)和一路高压风管路(管径不小于 DN25mm),要求接口靠近浓缩池底部。
稀释冲洗水管应引自循环水管或澄清水管,并应设止回阀。
循环水泵 1 用 1 备,1 台循环水泵可满足 4 台脱介筛、4 台脱泥筛喷水量的需要。
每台浓缩机配 2 台底流泵,底流管设有高压风吹风管和高压水冲洗管。
泵房内布置 1 套聚丙烯酰胺絮凝剂制备添加设备,聚丙烯酰胺絮凝剂溶液箱 2 套,2套座于搅拌桶的下方,2 套放于旁边。
两溶液箱内的药剂通过泵相互转排。
1 套聚合氯化铝制备添加设备,并具有煤泥水沉降自动监测装置的功能,聚丙烯酰胺添加位置实现多点加药(至少 4 点):浓缩机稳料桶或入料管。
药剂的制备和添加全部进入集控程序,可以就地操作也可以集控操作。
3.3.5 地销煤仓地销煤仓为 7 个 7m×10m 的方仓,总储量 5000t。
大的设备部件通过仓顶设置的 1台 5t 电动葫芦提升。
地销煤仓布置时,充分考虑了人行通道、设备提升及检修空间。
仓上通过 1 台刮板输送机配仓,刮板通过电液动平板闸门卸料,将大块煤配入仓内。