《烧结球团》课件
烧结球团工艺介绍PPT课件

层进入混合料,而保证台车上烧结混合料 球团生产要求含铁原料粒度细,一般-325目粒级大于70%以上(或者-200目粒级大于90%以上),水份一般小于10%。
配料采用先进的重量法,就是圆盘给料机加电子皮带称进行配料。
中的燃料从上而下一直延续下去,才能像 焙烧过程通常可分为干燥、预热、焙烧、均热、冷却(球团带冷机尾部图)5个阶段,最后经由齿辊破碎机破碎可能粘结的大块后排出
学反应,最终成为烧结矿。烧结过程是在 厂的瓦斯灰、瓦斯泥。
经过破碎后的小块烧结矿一般进入到下道工序—冷却,也有的厂在破碎后经过垫矿筛将小于5mm粉末筛出来反回重新混合、烧结,而
烧结机台车上进行的,但和烧结机密切配 大于5mm的烧结矿才进冷却机。
烧结过程所用的设备叫烧结机,主要是带式烧结机,还有一种步进式平面烧结机。
。
上面说的最终生成烧结矿。烧结过程所用 配料因其原料种类少,一般2—3种,故工艺简单,一般采用圆盘给料机和皮带秤按预定配比控制。
烧结生产的第一道工序是配料,即根据烧结矿质量标准,把各种原燃料按照相应比例搭配在一起。
从各地源源不断运来的原燃料卸载在这里,经短暂整理后又要连续运送至烧结、球团、炼铁各生产厂。
由于生成烧结矿时是高温反应,造成烧 结矿成整块台车状,这就需要用单辊破碎 机将其破碎成小块烧结矿。
经过破碎后的小块烧结矿一般进入到下道 工序—冷却,也有的厂在破碎后经过垫矿 筛将小于5mm粉末筛出来反回重新混合、 烧结,而大于5mm的烧结矿才进冷却机。
冷却工序的作用就是将处于高温下的烧结 矿冷却到150oC以下,冷却设备常用的是带 式冷却机(和烧结机结构型式差不多)和 环式冷却机,也有采用机上冷却方法,如 前面所提的步进式平面烧结机。
中南大学《烧结球团学》之《球团理论与工艺3》41页PPT

43、重复别人所说的话,只需要教育; 而要挑战别人所说的话,则需要头脑。—— 玛丽·佩蒂博恩·普尔
44、卓越的人一大优点是:在不利与艰 难的遭遇里百折不饶。——贝多芬
45、自己的饭量自己知道。——苏联
Hale Waihona Puke 中南大学《烧结球团学》之《球团理 论与工艺3》
21、静念园林好,人间良可辞。 22、步步寻往迹,有处特依依。 23、望云惭高鸟,临木愧游鱼。 24、结庐在人境,而无车马喧;问君 何能尔 ?心远 地自偏 。 25、人生归有道,衣食固其端。
41、学问是异常珍贵的东西,从任何源泉吸 收都不可耻。——阿卜·日·法拉兹
烧结球团PPT课件
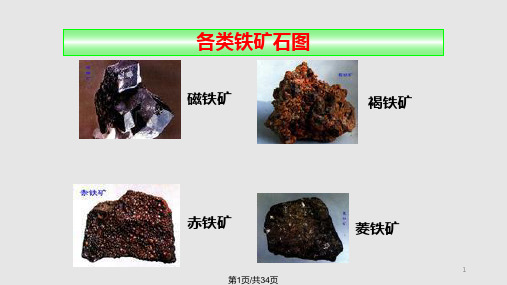
烧结点火示意图
13
第13页/共34页
1.烧结矿层:随烧结过程进行不断加厚,抽入空气过冷 使烧结矿骤冷将影响烧结矿强度。
2.燃烧层:主要反应为:C的燃烧、MCO3分解、FeS2 氧化、形成液相、铁氧化物分解还原氧化。(由于液 相的产生使该层透气性变差)
3.预热层:主要反应为:氧化还原、结晶水分解、部 分MCO3分解
TFe波动≤±0.5%,SiO2 ≤±0.03%混匀的重要 性(条件:平铺直取——原料场应足够大); ⑻矿石代用品:
高炉炉尘、转炉炉尘、轧钢皮、硫酸渣等。 8 第8页/共34页
烧结的车间的全貌
9
第911
第11页/共34页
(二)烧结料层结构
12
第12页/共34页
稳:化学成分稳定(TFe、R) 熟:增加熟料率↑1%,η↑0.3%,焦比↓1.2kg/tFe
3
第3页/共34页
三、铁矿烧结及球团的基本原理、工艺
(一)烧结料组成:
(1)含铁料:精矿份200目以下(考虑成球性)、富矿 粉(5~8mm,烧结中的骨架)、其他(炉尘、轧钢皮 等)
(2)熔剂:以CaO为主, CaO ↑1%,烧结产量↑ 3%
4.存在传热速度与燃烧速度的同步问题
5.存在如何减少“过湿”现象的问题
6.存在有害杂质S的去除问题(S由易去除S化物转
化为硫酸盐的问题)
7.存在选用何种液相体第1系5页作/共3为4页固结成型机理问题
15
(四)强化烧结的措施
1.改善透气性:适宜的水分、延长混料时间、小球烧 结、预热混合料
2.提高抽风负压:但需考虑电耗成本增加问题
⑵脉石成分:SiO2、Al2O3↓越好(须重视Al2O3 ), MgO ↑越好
《烧结球团》课件解析
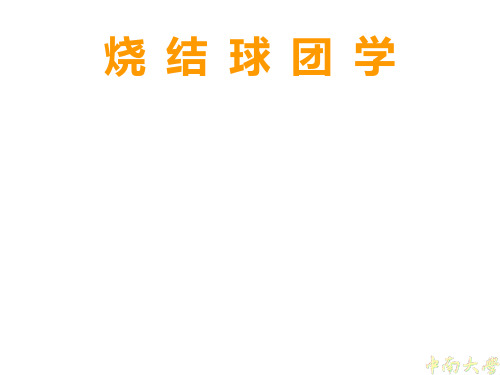
1.3.3 固体燃料的用量
燃料用量影响烧结的温度和烧结气氛。 燃料用量高时: 1)烧结温度高,有利烧结液相的发展,烧结矿强度高; 2)还原性气氛强,不利于铁酸钙体系的发展,烧结矿FeO含 量高,强度低,还原性差。
1.3.1 固体燃料的粒度
固体燃料的粒度,与混合料中各组分的特性有关。 当烧结8~0毫米粉矿时,燃料粒度稍大时对烧结过程 影响不大,而当减少燃料粒度时,烧结质量则明显地 下降。
烧结粒度为-8mm的铁矿粉时,粒度为1~2mm的焦粉 最适宜,这样的粒度有能力在周围建立18~20mm烧 结矿块。
铁精矿由于粒度细,当燃料粒度减少时对烧结过程影响不大, 而当其粒度稍有增大时,却使成品烧结矿的产率和强度显著 下降
碳粒燃烧速度
D D (CO C )
2
ቤተ መጻሕፍቲ ባይዱ
s O2
R R (C )
2
s n O2
s O2
D (CO C ) R C
s O2
D C CO D R
s O2
2
碳粒燃烧的总速度
D R CO CO D R
D R 2
2
D —界面层内传质系数(内扩散系数)
无烟煤的着火温度为750-770 ℃,挥发物的分解挥发 温度为380-400℃
挥发物不可能燃烧而进入废气,与废气-起进入抽风除尘 系统,而在管道壁、排灰阀、除尘器,以及抽风机的内壁 和转子的叶片上沉积下来,危及和妨害整个抽风系统的正 常工作。
烧结与团球操作烧结新技术课件

项目总结
本项目主要讲解了目前世界上几种已应用于工业或部分应用于工业的烧 结新工艺,并分别叙述了它们各自的工艺特点和其应用的关键条件,重点要 理解小球、球团烧结、低温烧结和低SiO2高还原性烧结矿的烧结工艺特点和 应对措施。要求熟练掌握烧结工艺流程,并要对传统烧结理论有所认识。
THANKS!
一、小球、球团烧结工艺
相关知识
相关知识
一、小球、球团烧结工艺 将烧结原料和溶剂的粒度<3mm粒级控制在60%~70%,并在配料室内加雾化水进行润湿。
按球团造球无水长大,无水密实理论,根据混合机内不同区域对加水强度的要求,在一次 混合机内进行三段加水,在二次混合机内进行一段加水,当一混加水不足时进行补充,小 球烧结工艺流程见图10-1。
知识拓展
EOS(Emission Optimized Sintering)工艺是德国的蒂森、日本新日铁及荷兰 的霍戈文等烧结厂都有使用的降低NOx和SO2排放的烧结工艺。EOS烧结工艺和传统烧 结工艺的比较见图10 2。EOS系统利用部分废气循环,可减少烟囱排除的粉尘、NOx 和SO2,同时降低工序能耗,并可不同程度地改善烧结矿质量、产量。
优点:不仅能生产具有较高机械强度和良好冶金性能的优质烧结原性烧结矿的烧结生产新工艺 定义:低SiO2烧结矿一般是指烧结矿中SiO2含量低于5.0%的烧结矿。 优点:使入炉品位提高,渣量减少;改善烧结矿冶金性能,尤其是其软熔温度升高、
烧结球团
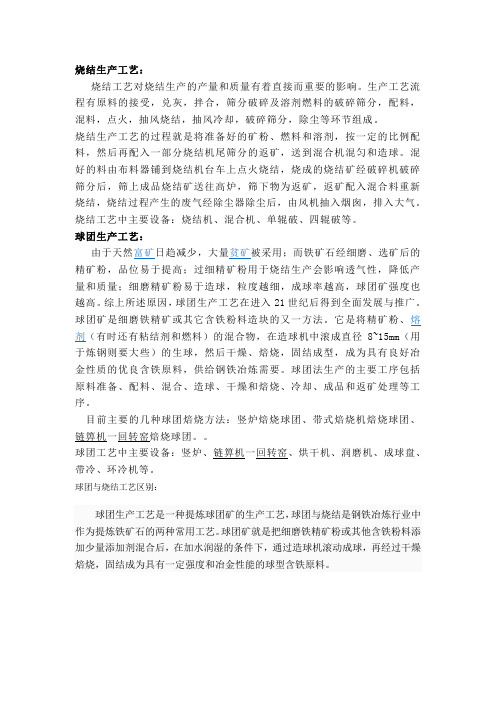
烧结生产工艺:烧结工艺对烧结生产的产量和质量有着直接而重要的影响。
生产工艺流程有原料的接受,兑灰,拌合,筛分破碎及溶剂燃料的破碎筛分,配料,混料,点火,抽风烧结,抽风冷却,破碎筛分,除尘等环节组成。
烧结生产工艺的过程就是将准备好的矿粉、燃料和溶剂,按一定的比例配料,然后再配入一部分烧结机尾筛分的返矿,送到混合机混匀和造球。
混好的料由布料器铺到烧结机台车上点火烧结,烧成的烧结矿经破碎机破碎筛分后,筛上成品烧结矿送往高炉,筛下物为返矿,返矿配入混合料重新烧结,烧结过程产生的废气经除尘器除尘后,由风机抽入烟囱,排入大气。
烧结工艺中主要设备:烧结机、混合机、单辊破、四辊破等。
球团生产工艺:由于天然富矿日趋减少,大量贫矿被采用;而铁矿石经细磨、选矿后的精矿粉,品位易于提高;过细精矿粉用于烧结生产会影响透气性,降低产量和质量;细磨精矿粉易于造球,粒度越细,成球率越高,球团矿强度也越高。
综上所述原因,球团生产工艺在进入21世纪后得到全面发展与推广。
球团矿是细磨铁精矿或其它含铁粉料造块的又一方法。
它是将精矿粉、熔剂(有时还有粘结剂和燃料)的混合物,在造球机中滚成直径8~15mm(用于炼钢则要大些)的生球,然后干燥、焙烧,固结成型,成为具有良好冶金性质的优良含铁原料,供给钢铁冶炼需要。
球团法生产的主要工序包括原料准备、配料、混合、造球、干燥和焙烧、冷却、成品和返矿处理等工序。
目前主要的几种球团焙烧方法:竖炉焙烧球团、带式焙烧机焙烧球团、链箅机一回转窑焙烧球团。
球团工艺中主要设备:竖炉、链箅机一回转窑、烘干机、润磨机、成球盘、带冷、环冷机等。
球团与烧结工艺区别:球团生产工艺是一种提炼球团矿的生产工艺,球团与烧结是钢铁冶炼行业中作为提炼铁矿石的两种常用工艺。
球团矿就是把细磨铁精矿粉或其他含铁粉料添加少量添加剂混合后,在加水润湿的条件下,通过造球机滚动成球,再经过干燥焙烧,固结成为具有一定强度和冶金性能的球型含铁原料。
烧结矿球团矿海绵铁30页PPT
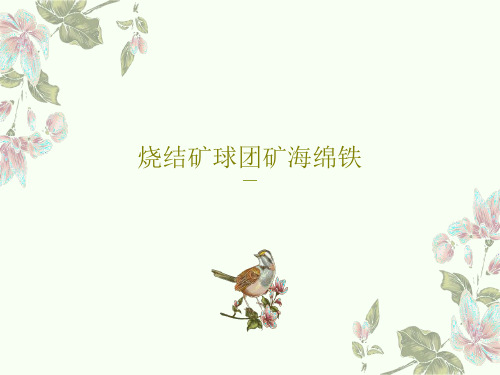
41、学问是异常珍贵的东西,从任何源泉吸 收都不可耻。——阿卜·日·法拉兹
42、只有在人群中间,才能认识自 己。——德国
43、重复别人所说的话,只需要教育; 而要挑战别人所说的话,则需要头脑。—— 玛丽·佩蒂博恩·普尔
44、卓越的人一大优点是:在不利与艰 难的遭遇里百折不饶。——贝多芬
烧结矿球团矿海绵铁
16、自己选择的路、跪着也要把它走 完。 17、一般情况下)不想三年以后的事, 只想现 在的事 。现在 有成就 ,以后 才能更 辉煌。
18、敢于向黑暗宣战的人,心里必须 充满光 明。 19、学习的关键--重复。
20、懦弱的人只会裹足不前,莽撞的 人只能 引为烧 身,只 有真正 勇敢的 人才能 所向披 靡。
- 1、下载文档前请自行甄别文档内容的完整性,平台不提供额外的编辑、内容补充、找答案等附加服务。
- 2、"仅部分预览"的文档,不可在线预览部分如存在完整性等问题,可反馈申请退款(可完整预览的文档不适用该条件!)。
- 3、如文档侵犯您的权益,请联系客服反馈,我们会尽快为您处理(人工客服工作时间:9:00-18:30)。
特
点
烧结料层中燃料燃烧除空气供给氧外,混合料中某些氧化物 所含的氧,也往往是燃料活泼的氧化剂。
燃烧产物除中除O2外,还包括CO、CO2的O2。 理想状态:CO2+0.5CO+O2接近21%; 赤铁矿:22-23%,软锰矿:23.5%;磁铁矿:18.5-20%。
气相组成
0
2
4
6
8
10
12
图 在烧结试验过程测得废气成分的变化
最适宜的燃料用量应保证所获得的烧结矿具有足够的强度和 良好的还原性。(由试验确定)
1)磁铁矿烧结过程中,由于Fe3O4氧化放热,燃料用量小些;
2)赤铁矿缺乏磁铁矿氧化的热收入,故燃料用量要高些; 3)菱铁矿和褐铁矿则因为碳酸盐和氢氧化物的分解需要消 耗热量,-般则要求更高的燃料用量。 目前一般烧结的燃料用量为5~6%
无烟煤
随着煤炭化的程度不同,煤中的挥发物含量的差别是很大的。 炭化程度越高,它的挥发分含量也就越少。 无烟煤是各种煤中炭化最好的烧结燃料。
要求无烟煤的发热量大于6000千卡/公斤,挥发分小于10%, 灰分小于15%,硫小于2.5%,进厂的粒度小于40毫米。
无烟煤
无烟煤孔隙率小,反应性较差,导致垂直烧结速度 下降和烧结矿质量恶化。
碳粒燃烧速度
D D (C O C
2
s O2
)
R R (C
D (C O C
2
s O2
)
n
s O2
) RC C O2
s O2
C
s O2
D D R
碳粒燃烧的总速度
D
R
D R D R
C O2 C O2
D
—界面层内传质系数(内扩散系数)
温度,K
在烧结料层中可能进行的反应
• 高温 CO稳定,低温 CO2稳定; • 氧过剩生成 CO2 碳过剩生成 CO; 燃料所处状态: 燃料群→燃烧前沿有C →生成CO 单颗粒→燃烧前沿有O2→生成CO2 对于烧结料层,碳完全燃烧的可能性大,但在高温 燃烧带,或者当燃料太多时,也可能生成CO。
烧结料层中,总体是氧化气氛,局部存在还原气氛。
1.3.1 固体燃料的粒度
固体燃料的粒度,与混合料中各组分的特性有关。 当烧结8~0毫米粉矿时,燃料粒度稍大时对烧结过程 影响不大,而当减少燃料粒度时,烧结质量则明显地 下降。
烧结粒度为-8mm的铁矿粉时,粒度为1~2mm的焦粉 最适宜,这样的粒度有能力在周围建立18~20mm烧 结矿块。
铁精矿由于粒度细,当燃料粒度减少时对烧结过程影响不大, 而当其粒度稍有增大时,却使成品烧结矿的产率和强度显著 下降
本章内容
1.1 燃料燃烧基本原理 1.2 燃烧带的特性分析 1.3 固体燃料特性及用量对烧结过程的影响 1.4 烧结料层中的温度分布及蓄热 1.5 烧结过程传热规律及应用
1.1烧结料层燃料燃烧基本原理
烧结过程中,混合料中固体燃料燃烧所提供的热量占烧结 总需热量的90%左右,因此,主要介绍固体燃料燃烧规律。
1.1.1 固体燃料燃烧热力学
固体炭在温度达700℃以上即着火燃烧,发生如下反应: 碳的不完全燃烧反应: 2C+O2=2CO △G0=-223426—175.31T J 碳的完全燃烧反应: C+O2=CO2 △G0 =-394133-0.84T J CO的燃烧反应: 2CO+O2=2CO 2 △G0 =-564840+173.64T J 布都尔反应(歧化反应、碳素沉积反应): CO 2+C=2CO △G0 =170707-174.47T J
R —化学反应速率常数
C O2 1 k 1 kD 1 k
R
kDkR kD kR
或者
1 k
1 kD
1 kR
称为反应的总阻力 称为扩散阻力 称为化学反应阻力
扩散阻力 化学反应阻力
反应的总阻力
氧气浓度 气流速度 燃料粒度 燃烧温度
在低温下,化学反应速度很慢,过程的总速度取决于化学反 应速度,称为“动力学燃烧区”。燃烧速度主要受温度的影 响,次之为氧气的浓度。
在烧结精矿时(-lmm,其中-0.074mm占30%),焦粉粒度 0.5~3mm最好;
1.3.2 固体燃料的种类
碎焦粉粉末和无烟煤
焦碳是炼焦煤在隔绝空气高温加热后的固体产物
碎焦粉末是高炉用的焦碳的筛下物,粒度一般小于25毫米
焦 粉
衡量焦碳的质量—化学成分、物理机械性能、物理化学性质。 化学成分-工业分析(固定炭、灰分、挥发分和含硫量) 物理机械性能-机械强度 (如耐磨性和抗冲击强度、抗压强度)及筛分粒度组成 物理化学性质-燃烧性和反应性。 燃烧反应速度越快,燃烧反应性越高, 反应性好的焦碳燃烧性也好。
烧结料层中的热交换十分有利,固体碳颗粒燃烧迅速,在 一个厚度不大(一般为30~40mm)的高温区内进行。燃烧在 “扩散燃烧区”进行。 计算氧平衡时,考虑碳酸盐的分解、铁氧化物的氧化或还 原,废气中(CO2+1/2CO+O2)与空气和单一碳的燃烧反 应的平衡组成不同。
特
点
燃烧带的特征是一种“嵌晶”结构——碳粒燃烧是在周围 没有含碳的惰性物料包围下进行的。 在靠近燃料颗粒附近,高温度和还原性气氛占优势,氧气 不足。特别是在烧结块形成时,燃料被熔融物包裹时氧更 显得不足。 空气抽过邻近不含碳的区域,温度低得多,明显的氧化气氛
-1 0 0 0 0 0
-2 0 0 0 0 0
O 2C
-3 0 0 0 0 0
+
O
2
=
2C
O
2
G , J
C + O 2=
-4 0 0 0 0 0
CO
2
0
978k
-5 0 0 0 0 0
CO
2
+
2 C + O 2=
-6 0 0 0 0 0
2C O
C=
2C
O
-7 0 0 0 0 0 0 500 1000 1500 2000 2500
3)不能使用高发挥份的烟煤。 焦粉和无烟煤中的挥发分含量,不应超过5%。 燃料的灰分尽可能低些。燃料中灰分含量增多必然引起烧结 料含铁量降低和酸性氧化物增多(灰分中SiO2的数量高达 50%以上)因而必然相应需要增加熔剂的消耗量 。
1.3.3 固体燃料的用量
燃料用量影响烧结的温度和烧结气氛。 燃料用量高时: 1)烧结温度高,有利烧结液相的发展,烧结矿强度高; 2)还原性气氛强,不利于铁酸钙体系的发展,烧结矿FeO含 量高,强度低,还原性差。
燃料分散于烧结料中,碳含量少、粒度细而且分散,按重 量计燃料只占总料重的3%~5%,按体积计不到总料体积 的10%;烧结过程中的燃烧是介于单颗粒与燃料群的典型 的固定床燃烧。 空气过剩系数较高(常为1.4~1.5),故废气中均含一定数量 的氧。烧结过程整体是氧过剩,局部碳过剩。
1.2.2 燃烧带特性与燃烧废气组成
烧结矿带(成矿带): 熔融物(液相)冷凝 矿物析晶 空气得到预热
预热干燥带: 水分蒸发, 结晶水及石灰石分解 矿石氧化还原 固相反应 热交换迅速 废气温度 从1500 ℃下降到60~70 ℃
水分冷凝带(过湿带): 上层高温废气带入较多的水气 进入下层冷料时水分析出 影响烧结透气性 破坏已造好的混合料小球
1.2 烧结料层中燃烧带的特性分析
1.2.1 烧结过程中燃烧带的特性分析
研究烧结过程中碳粒燃烧速度的目的之一是要研 究燃烧带的厚度和燃烧带的移动速度。
假定烧结料是由惰性物料与燃料组成,并不发生 任何化学反应,同时燃料的燃烧反应以扩散为主。 此外,在推算中考虑到燃料颗粒相对表面积的作 用及影响燃烧速度的化学反应速度的因素。
在高温下,化学反应速度很快,氧的扩散速度相对很慢,过 程的总速度取决于氧的扩散速度,称为“扩散燃烧区”。 燃烧速度主要受气流速度,燃料的粒度等因素。
氧气浓度 气流速度 燃料粒度 燃烧温度
在“动力学燃烧区”与“扩散燃烧区”存在一个过渡燃烧 区。 不同反应由动力学区进入扩散区的温度不同: C和O2的反应于800℃左右开始转入;
原始烧结料带 物料的物理、化学性质基本不变
①冷却再氧化过程 ②熔体结晶 ③固相反应,氧化还原,原氧化物、 碳酸盐、硫化物的分解 ④燃料燃烧,液相熔体生成,高温分解 ⑤挥发,分解,氧化还原,水分蒸发 ⑥水汽冷凝
烧结过程
(1)混合料接受高温饱和废气中的水分,料层水分提
高而逐渐成为过湿层;
(2)当废气水分由饱和过渡到不饱和时,烧结混合料 开始干燥;
C和CO2的反应则在1200℃时才转入。
烧结过程影响燃烧速度的因素
在点火后不到1min,料层温度升高到1200-1350℃
烧结过程燃烧反应基本上是在扩散区内进行。 一切能够增加扩散速度的因素,都能提高燃烧反应
速度,强化烧结过程:
减小燃料粒度
增加气流速度(改善料层透气性、增大风机风量等)
气流中的氧含量
1.3 固体燃料特性及用量对烧结过程的影响
1.3.1 固体燃料的粒度
燃料的粒度过大时,会带来一系列的不良影响 a.燃烧带变宽,从而使烧结料层透气性变坏。
b.燃料在料层中分布不均匀,在大颗粒燃料的周围熔化得厉害, 离燃料颗粒较远的地方的物料则不能很好地烧结。 c.粗粒燃料周围,还原性气氛较强,而没有燃料地方空气 得不到利用 d.在向烧结机布料时,易产生燃料偏析现象,大颗粒燃料集中 在料层的下部,再加上烧结料层下部的蓄热作用,使烧结料层 的温度差异更大,以至造成上层烧结矿的强度差,下层过熔 FeO含量偏高。
1.1.2 固体燃料燃烧动力学
在烧结过程中,固体燃料呈分散状分布在料层中, 燃烧规律介于单体焦粒燃烧与焦粒层燃烧之间, 固体碳的燃烧属非均相反应。