第3章 表面精度
机械制造技术基础(第2版)第三章课后习题答案

《机械制造技术基础》部分习题参考解答第三章机械制造中的加工方法及装备3-1 表面发生线的形成方法有哪几种?答:(p69-70)表面发生线的形成方法有轨迹法、成形法、相切法、展成法。
具体参见第二版教材p69图3-2。
3-2 试以外圆磨床为例分析机床的哪些运动是主运动,哪些运动是进给运动?答:如图3-20(p87),外圆磨削砂轮旋转n c是主运动,工件旋转n w、砂轮的横向移动f r、工作台往复运动f a均为进给运动。
3-3机床有哪些基本组成部分?试分析其主要功用。
答:(p70-71)基本组成部分动力源、运动执行机构、传动机构、控制系统和伺服系统、支承系统。
动力源为机床运动提供动力;运动执行机构产生主运动和进给运动;传动机构建立从动力源到执行机构之间的联系;控制和伺服系统发出指令控制机床运动;支承系统为上述部分提供安装的基础和支承结构。
3-4什么是外联系传动链?什么是内联系传动链?各有何特点?答:外联系传动链:机床动力源和运动执行机构之间的传动联系。
如铣床、钻床传动链;内联系传动链:执行件和执行件之间的传动联系。
如车螺纹、滚齿的传动链。
外联系传动链两端没有严格的传动关系,而内联系传动链两端有严格的传动关系或相对运动要求。
3-5 试分析提高车削生产率的途径和方法。
答:(p76)提高切削速度;采用强力切削,提高f、a p;采用多刀加工的方法。
3-6 车刀有哪几种?试简述各种车刀的结构特征及加工范围。
答:(p77)外圆车刀(左、右偏刀、弯头车刀、直头车刀等),内、外螺纹车刀,切断刀或切槽刀,内孔车刀(通孔、盲孔车刀、)端面车刀、成形车刀等。
顾名思义,外圆车刀主要是切削外圆表面;螺纹车刀用于切削各种螺纹;切断或切槽车刀用于切断或切槽;内孔车刀用于车削内孔;端面车刀切断面;成形车刀用于加工成形表面。
3-7试述CA6140型卧式车床主传动链的传动路线。
答:(p82)CA6140型卧式车床主传动链的传动路线:3-8 CA6140型卧式车床中主轴在主轴箱中是如何支承的?三爪自定心卡盘是怎样装到车床主轴上去的?答:(p83-84)3-9CA6140型卧式车床是怎样通过双向多片摩擦离合器实现主轴正传、反转和制动的?答:如教材图3-17和3-18所示,操纵手柄向上,通过连杆、扇形齿块和齿条带动滑套8向右滑移,拨动摆杆10使拉杆向左,压紧左边正向旋转摩擦片,主轴实现正转;若操纵手柄向下,通过连杆、扇形齿块和齿条带动滑套8向左滑移,拨动摆杆10使拉杆向右,压紧右边反向旋转摩擦片,主轴反转。
第3章 几何精度规范

R5/2:1.00 2.50 6.30 16.0 40.0 100 R10/3:1.00 2.00 4.00 8.00 16.0 32.0
取值方法:计算值:取五位有效数字,供精确计算用 常用值:取三位有效数字,经常用的优先数
1.3 几何精度规范
3.优先数系的特点 ● 疏密均匀,分档合理, ● 简单易记,便于使用, ● 国际通用。
国家标准规定的优先数系具有广泛的适用性,常 见的量值,如长度、直径、转速及功率等分级,基本 上都是按一定的优先数系进行的。本课程所涉及的有 关标准里,诸如尺寸分段、公差分级及表面粗糙度的 参数系列等,基本上采用优先数系。
1.3 几何精度规范
2.标准化的基本含义
标准化是在经济、技术、科学及管理等社 会实践中,对重复性事物和概念通过制定、发 布和实施标准,达到统一,以获得最佳秩序和 效益。(这是国家标准《标准化基本术语》对标准化 所做的解释。它的最终目的是提高社会经济效益。)
标准化的主要任务是 制定标准、组织实 施标准和对标准的实施进行监督。
地方标准或企业标准:由省、自治区或企业 主管部门批准发布的标准。代号为DB、QB 。
注意下级标准不能与上级标准相违背
1.3 几何精度规范
国际标准:在国际上,为了促进世界各
国在技术上的统一,成立了国际标准化组织 (简称ISO)和国际电工委员会(简称IEC) 由这两个组织负责制定和颁发国际标准。我 国于1978年恢复参加ISO组织后。陆续修订了 自己的标准。修订的原则是,在立足我国生 产实际的基础上向ISO靠拢,以利于加强我国 在国际上的技术交流和产品互换。
1.3 几何精度规范
第3章_典型部件设计(主轴、支承件、导轨)

3.1.4.1 主轴部件主支承常用滚动轴承 (1) 角接触球轴承(向心推力球轴承)
角接触球轴承极限转速较高;可以同时承受 径向和一个轴向的载荷,a越大,可承受的进给力 越大。主轴用的a一般取15o或25o。
传动件放在主轴的后悬伸端,较多用于带传 动,可便于传动带的更换,如磨床。
3.1.3.3 主轴传动件位置的合理布置 (2) 驱动主轴的传动轴位置的合理布置 ★在布置传动轴的位置时,应尽量使传动力
Q与切削力P两者引起的主轴轴端位移和轴承受力 的影响能互相抵消一部分。
3.1.3.4 主轴主要结构参数的确定 主轴的主要结构参数有:
3.1.4.1 主轴部件主支承常用滚动轴承 (1) 角接触球轴承 球轴承为点接触,刚度不高,为提高刚度,
同一支承处可多联组配。 组配方式有三种: 背靠背组合;面对面组合;同向组合。
3.1.4.1 主轴部件主支承常用滚动轴承 (2) 双列短圆柱滚子轴承 特点:内圈有1:12的锥孔,轴向移动内圈可
径向圆跳动
端面圆跳动
3.1.4 主轴滚动轴承
主轴轴承的类型、配置方式、精度、安装、 调整、润滑和冷却等都直接影响主轴部件的工作 性能。
常用主轴轴承有滚动轴承、液体动压轴承, 液体静压轴承、空气静压轴承等。
轴承的轴向承载能力和刚度,由强到弱依次 为:推力球轴承、推力角轴承、圆锥滚子轴承、 角接触球轴承;
以调整轴承的径向间隙和预紧; 轴承的滚子能承受较大的
径向载荷和转速; 轴承由两列滚子交叉排列,
数量较多,因此刚度很高; 不能承受轴向载荷。
3.1.4.1 主轴部件主支承常用滚动轴承 (3) 圆锥滚子轴承 特点:刚度和承载能力大,既可承受径向力,
机械精度设计与检测课后习题答案

即5e0 55 0 0 0..0 05 6。 0 1
即5E 0850 。 (4 ) ¢50E8的极限偏差: ES=+89μm,EI=+50 μm。
0.089 精选2021版课件0.0154 0
8 .已 3- - 0 知 0 0 . 和 0 . N 3 0 2 t 6 0 8 0 0 0 . . 0 0 7 7。 5 4
试不用查表法计算¢30H7/n6与¢30T7/h6的配合公差,并 画 出尺寸公差带图。
答案:
对¢30H7/ n6 Tf=0.034
(1)配合公差: ② 对¢30T7/ h6 Tf=0.034
(2)尺寸公差带图:
+28
+21
n6
H7
+15
h6
-0.033
-0.013
¢30mm ¢30mm
图 作业题8 ① ¢30H7/ n6
答 案 : IT7=25μm,IT8=39 μ m(D=38.73mm,i=1.56 μm);
IT7.5=31μm,IT8.5=49 μm, IT7.25=23μm,
IT8.25=44μm。
精选2021版课件
12
5. 已知两根轴,其中d1=¢5,其公称值Td1=5μm; d2=¢180,其公称 值Td2=25μm。试比较以上两根轴加工的难易程度。
+0.005
Td
TD
¢45
(8) 过渡配合。
-0.025
-0.034
图 作业题精2尺选寸20公21差版课带件图
11
3. 若已知某孔轴配合的公称尺寸为¢30mm,最大间隙Xmax =
+23μm,最大过盈Ymax = - 10 μm,孔的尺寸公差TD=20 μm,
第3章-表面粗糙度
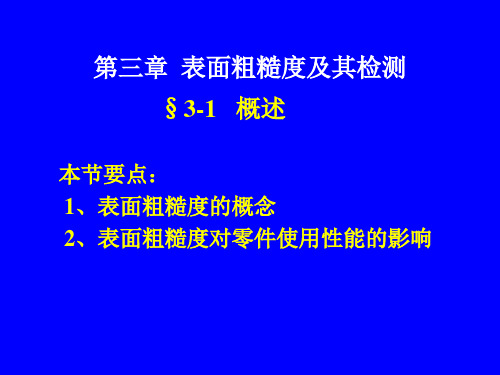
2、表面粗糙度形成的原因 1)加工过程中的刀痕 2)切屑分离时的塑性变形
3)刀具与已加工表面间的摩擦
4)工艺系统的高频振动
二、表面粗糙度对零件使用性能的影响 1)耐磨性 零件表面越粗糙,摩擦系数就越大,二相互运动的零 件表面磨损就越快,即零件的耐磨性差。 2)稳定性 影响到配合性质的稳定性,如对间歇配合,微观不平 度的峰尖在工作中首先被磨损而使间歇增大;对过盈配合, 微观不平度的峰尖在装配时被挤平,实际有效过盈减少, 降低了联结强度。 3)疲劳强度 零件表面越粗糙,微观不平度的凹谷就越深,应力集 中就越严重,在交变应力作用下,零件损坏的可能性就越 大,疲劳强度显著降低。 4)抗腐蚀性 粗糙的表面易使物质附着于微观不平度的凹谷,并渗 入金属内层,造成零件表面锈蚀。
§3-2 表面粗糙度的评定
本节要点: 1、基本术语和定义 2、表面粗糙度评定参数 3、表面粗糙度评定参数及数值的选用
§5-2 表面粗糙度的评定
一、基本术语和定义 1、 实际轮廓:平面与实际表面相交 所得的轮廓线 2 、取样长度L 取样长度是指取具有 表面粗糙度特征的一段基 准线长度,在取样长度范 围内,一般应包含至少5 个轮廓峰和轮廓谷。但取 样长度过长,表面粗糙度 的测量值又会把表面波度 的成分包括进去,所以要 适当。
三、表面粗糙度评定参数及数值的选用 1、评定参数的选择 对大多数表面而言, Ra、 Rz是国标规定必须标注的参数,Ra 较客观地反映表面微观几何形状的特征,国标推荐优先选用,其他 参数如RSm 、Rmr(c)只有在Ra、Rz不能满足零件表面功能要求时才 选用。 (1) 优先选用Ra;(不宜用于太粗或太光的表面) (2) 超精加工表面用Rz; Ra 、Rz联用,常用于控制表面微观裂纹。 2、参数值的选用 表面粗糙度参数值选用的原则是:满足功能要求而顾及经济合 理性,即在满足功能要求的前提下,参数的允许值应尽可能大。参 数已经标准化,设计时应按GB/T 1031—1995规定的参数值系列选取
第3章 精密成形技术

• 家电和玩具等行业,并且能生产出形状复杂、 薄壁精美的金属器件。 • 我国压铸生产开始于20世纪50年代,发展于60 年代到70年代,90年代后有了长足进展。我国 多小型压铸,压铸合金以锌合金为主,多为家 电、玩具等非受力件,在汽车、摩托车等机械 设备零件的压铸所占比重较小,在压铸件的质 量方面于国外相比仍有较大差距。
第3章 精密成形技术
• 第一节 精密洁净铸造技术
• 铸造是一种液态金属成形方法。长期以来, 应用最广泛的是普通砂型铸造。随着科学技 术的不断发展和生产水平的不断提高以及人 类社会生活、生产的需要,在继承古代铸造 技术和应用近代科学技术成就的基础上,开 创了许多新的铸造方法和工艺。使现代铸造 技术朝着“精密、洁净、高效”方向发展。
• 2、压铸原理与压铸工艺
• 压铸在压铸机上进行,压铸机一般由压型也
称为压铸模、压室、射压系统等组成,压铸
时把液态金属装入压室,射压系统推动压射
头把液态金属高速压入压型,保持压力,结
晶凝固后,压射头回退,由顶出机构顶出铸
件。
• 压力铸造的基本工艺流程如下图所示:
• 3、压铸设备
• 压铸机是压铸生产的主要设备,主要由合型 机构和压射机构两部分组成。 • 根据压室的不同,压铸机分为热压室和冷压 室两类。 • 热压室压铸机的压室与金属液的保温装臵连
• 术进入工业生产。20世纪50年代大型压铸机 的诞生,压铸技术才真正拓宽了广泛地工业 应用领域。随着压铸机,压铸工艺、压铸模 及润滑剂等压铸技术的发展,压铸合金也从 最初的铅到锌、铝、铜、镁最后到铁合金的 发展过程,随着压铸合金熔点的不断提高, 压铸技术的应用会越来越广泛。目前压铸技 术已广泛用于汽车工业、仪表、电气通信、
凝固,保证获得更加致密的铸件。
摩擦学第三章表面接触

b
N
△Ari
3)实际接触面积(miàn jī)Ar(真实接触面积(miàn jī))
实际接触面积是指在固/固界面上,直接传递界面 力的各个局部实际接触的微观面积△Ari的总和。今假 定在界面上有n个微观的实际接触面,则其总的实际 接触面积为:
n
Ar
Ari(3-2)
i 1
第二页,共二十五页。
一两球体接触半径可由赫兹公式引入3334一般作用在接触面中心的最大接触应力是平均应力的15倍max0389pe当两个球均为钢球时代入353637二两圆柱体接触由赫兹公式如圆柱长度为lmax0418qe3839310311代入b式max3882a弹性压入面积压缩应力四圆球面与凹球面的接触hz在接触两球中令凹球半径为rmax388五结论与讨论1在弹性变形状态下最大接触应力与载荷成非线形2球与平面接触最大剪应力在表层下054当法向载荷与切向力同时作用最大剪应力位置向表面移动5由于表面粗糙度的影响每个微凸体进入接触时出现微观赫兹应力分布6大多数粗糙表面接触表面接触具有弹塑性特点7表面接触的形式取决于接触条件第三节粗糙表面的接触一单个球体与刚性平面的接触计算研究单个弹性球体与刚性平面的接触情况法向变形量故
(3-13)
a
a1
A' 实际是球体塑性变形时的接触圆面积 i
实际加载时弹性体侧向变形受到限制,实际面积比理论面积小
1 2
实际面积
法向变形量
Ai
1 2
A'i
R
13
16
9 E'2
R
pi2 3
(3-14)
(3-15)
已知
a2 R
a
3
3Pi 4
R E'
第3章-2零件尺寸的检验

三.验收极限方式和相应计量器具的选择示例
例3. 50h8 轴加工后尺寸遵循偏态分 布 (偏向最大实体尺寸一边),试确定其验收极 限,并选择相应的计量器具. 解:(1)确定验收极限 被测轴加工后遵循偏态分布,因此其验收极 限可以这样确定,其尺寸偏向50mm的一边采用内 缩方式,而最小实体尺寸一边采用不内缩方式.
返回首页
§2.光滑极限量规
检验孔的量规称为塞规,检验轴的量规 称为环规或卡环.量规按用途可分为: 1.工作量规:指在工件制造中,操作者使 用的量规. 2.验收量规:指在验收零件时,检验人员 或用户代表所使用的量规. 3.校对量规:指用以检验工作量规或验收 量规的量规.
返回首页
一、光滑极限量规的功用和分类
返回首页
二、计量器具的选择
根据测量误差的来源测量条
件引起的测量不确定度u2组成的。
u1是表征由计量器具内在误差所引起的
测得的实际尺寸对真实尺寸可能分散得一
个范围。一般来讲,u1影响较大,u2影响较
小.主要根据u1的大小来选定具体的计量
器具.
2 u u12 u2
返回首页
塞规简图
例2.计算Φ 40k6轴颈用工作卡规的三种校对量规工作部 分的极限尺寸. 解:Φ 40k6轴颈用工作卡规的校对量规的定形尺寸公 差TP=T/2=1.2um.按图7-6,TT和TS校对量规的定形尺寸皆为 40.018mm,ZT校对量规的定形尺寸为40.002mm;TT校对量规 的上偏差为-Z=-2.8um, 下偏差为-(Z+TP)=- 4.0um;TS校对量规的上偏差为0,下偏差为-Tp=-1.2um;ZT 校对量规的上偏差为+Tp=+1.2um,下偏差为0. 。 40 . 018 。 因此,TT校对量规按 mm,即按 40.0152 mm制造.TS校对量规按 40.018 mm制造. 0.0012 ZT校对量规按 40.0020 mm制造.校对量规定形尺 寸公差带示意图见下图.
- 1、下载文档前请自行甄别文档内容的完整性,平台不提供额外的编辑、内容补充、找答案等附加服务。
- 2、"仅部分预览"的文档,不可在线预览部分如存在完整性等问题,可反馈申请退款(可完整预览的文档不适用该条件!)。
- 3、如文档侵犯您的权益,请联系客服反馈,我们会尽快为您处理(人工客服工作时间:9:00-18:30)。
(1)一般标注
①可标注在轮廓线或延长线上、尺寸线或尺寸界线上
(在图形的右边和下边标注时,用带箭头的引线引出,且符号正放)
②可标注在几何公差框格上方,见图3-12(d)示。
图3-12 (d)
③必要时可用带箭头的或黑点的引线引出,见图3-12(e)示
图3-12 (e)
(2)简化标注
①当零件的大部分表面具有相同的表面粗糙度时,可 统一标注在标题栏附近。
如图3-13表示除 外,其余表面均为Ra3.2m
②若图样标注空间所限, 对具有相同表面粗糙度 要求的表面,见图3-14。
图3-14
(3)表面粗糙度附加参数或其他项目的标注 见图3-15、3-16示。
第4 节
内容包括:
表面粗糙度的选择
即 表面精度设计
评定参数 选择 评定参数值 三方面内容 加工方法
1.评定参数的选择
幅度参数为基本参数,当有其他表面功能要求时,再
选择附加参数。 国标推荐在常用数值范围 ( Ra 为 0.025m ~ 6.3m ) 内, 选择轮廓算术平均偏差Ra (用轮廓仪测量Ra方便 ) 。 当零件表面较小时,或特别粗糙或光滑时,选择 轮廓 最大高度RZ 。(Ra>6.30m或<0.025m)
第3章
表面精度
学 习 内 容
● ● ●
●
表面粗糙度基本术语 表面粗糙度的评定参数 表面粗糙度的标注 表面粗糙度的选择
表征零件表面在加工后形成的由微小间距的峰 谷组成的微观几何形状特征称为表面粗糙度, 即 表面精度。
图3-1 车削外圆柱面
图3-2 零件的表面几何形状误差
第1 节
1.表面轮廓
表面粗糙度基本术语
上下面积相等的直线。即
指在取样长度内,将实际轮廓划分为上下两部分,使
第2 节
表面粗糙度的评定参数
幅度参数 国标规定的评定参数有四类: 间距参数 混合参数 曲线和相关参数 在生产中应用最多的是幅度参数。 主要幅度参数有 轮廓算术平均偏差Ra 轮廓最大高度RZ
1.轮廓算术平均偏差Ra
指在取样长度内,被测实际轮廓上各点到轮廓中线的 距离Z(轮廓偏差)的绝对值的平均值,如图3-6所示。 数学表达式为: R = 1 lr | Z ( x) | dx a lr 0 或
指理想平面与实际平面垂直 相截所得的轮廓线,见图3-3示
2.基准长度 (1)取样长度lr
指评定表面粗糙度时所取的一段基准线长度。 一般不少于5个以上的轮廓峰和轮廓谷 。 见图3-5示
(2)评定长度ln
指评定表面轮廓必需的最小长度。 默认的评定长度为ln = 5lr,
见图3-4示
图3-5 轮廓算术平均中线
表面粗糙度的标注
1.表面粗糙度符号
符号及涵义见表3-4示。 幅度参数标注示例及含义见表16%规则(上限值、下限值) 在同一评定长度下的表面粗糙度参数的全部实测值中, 最多允许有16%超差。 (2)最大规则(最大值、最小值) 要求表面粗糙度参数的全部实测值不得超差。
3. 表面粗糙度的标注方法
图3-4 取样长度lr和评定长度ln
3.基准中线
是具有理想特征的评定表面粗糙度参数值大小的一条 基准线,有两种确定方法:
(1)轮廓最小二乘中线
Z(轮廓偏差)的平方和为最小。即
lr
见图3-6示
指在取样长度内,实际被测轮廓线上各点到该线的距离
0
Z dx min
见图3-5示
2
(2)轮廓算术平均中线
应用范围:为首选参数,在生产中广泛采用
图3-6 轮廓算术平均偏差Ra示意图
2.轮廓最大高度RZ
见图3-7示
指在取样长度内,轮廓的峰顶线和谷底线之间的最大距离。 数学表达式为: RZ =|Zpmax|+|Zvmax| 应用范围:小零件的表面,在交变载荷作用 场合
图3-6 轮廓算术平均偏差Ra示意图
第3 节
当表面上不允许出现较深加工痕迹以防止应力集中及 疲劳破坏(交变载荷作用)时,附加轮廓最大高度RZ。
2.评定参数值的选择
选择原则:是在满足功能要求的前提下,参数允许值 应尽量大,以减小加工难度,降低加工成本。 选择时应注意问题见P87。
3.加工方法的选择
表面粗糙度的表面特征及其对应的 经济加工方法 ,见 表3-7示。