第七章合成气的生产过程
合成气的制备方法
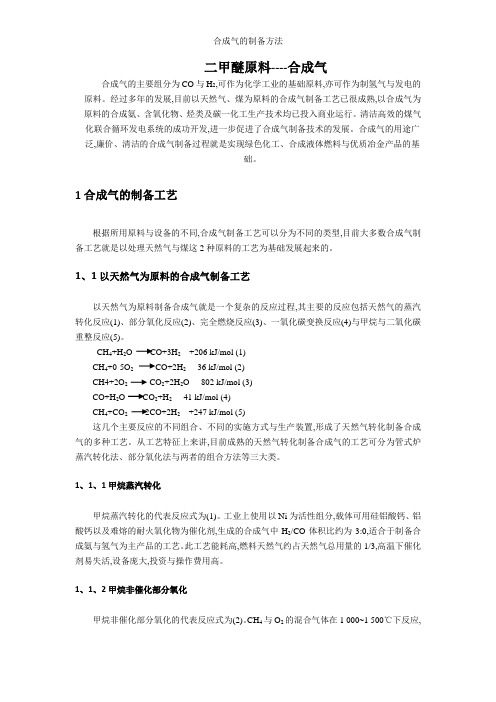
二甲醚原料----合成气合成气的主要组分为CO与H2,可作为化学工业的基础原料,亦可作为制氢气与发电的原料。
经过多年的发展,目前以天然气、煤为原料的合成气制备工艺已很成熟,以合成气为原料的合成氨、含氧化物、烃类及碳一化工生产技术均已投入商业运行。
清洁高效的煤气化联合循环发电系统的成功开发,进一步促进了合成气制备技术的发展。
合成气的用途广泛,廉价、清洁的合成气制备过程就是实现绿色化工、合成液体燃料与优质冶金产品的基础。
1合成气的制备工艺根据所用原料与设备的不同,合成气制备工艺可以分为不同的类型,目前大多数合成气制备工艺就是以处理天然气与煤这2种原料的工艺为基础发展起来的。
1、1以天然气为原料的合成气制备工艺以天然气为原料制备合成气就是一个复杂的反应过程,其主要的反应包括天然气的蒸汽转化反应(1)、部分氧化反应(2)、完全燃烧反应(3)、一氧化碳变换反应(4)与甲烷与二氧化碳重整反应(5)。
CH4+H2O CO+3H2+206 kJ/mol (1)CH4+0·5O2CO+2H2-36 kJ/mol (2)CH4+2O2CO2+2H2O -802 kJ/mol (3)CO+H2O CO2+H2-41 kJ/mol (4)CH4+CO22CO+2H2+247 kJ/mol (5)这几个主要反应的不同组合、不同的实施方式与生产装置,形成了天然气转化制备合成气的多种工艺。
从工艺特征上来讲,目前成熟的天然气转化制备合成气的工艺可分为管式炉蒸汽转化法、部分氧化法与两者的组合方法等三大类。
1、1、1甲烷蒸汽转化甲烷蒸汽转化的代表反应式为(1)。
工业上使用以Ni为活性组分,载体可用硅铝酸钙、铝酸钙以及难熔的耐火氧化物为催化剂,生成的合成气中H2/CO体积比约为3:0,适合于制备合成氨与氢气为主产品的工艺。
此工艺能耗高,燃料天然气约占天然气总用量的1/3,高温下催化剂易失活,设备庞大,投资与操作费用高。
1、1、2甲烷非催化部分氧化甲烷非催化部分氧化的代表反应式为(2)。
F-T合成
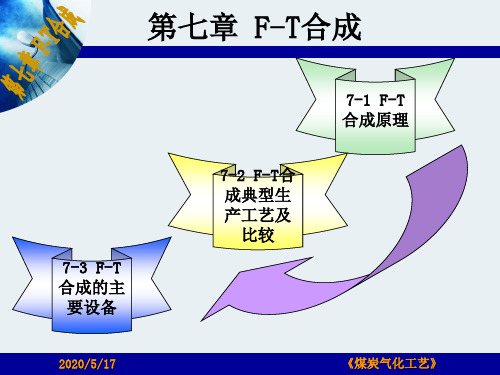
1、MFT合成工艺流程
该流程为两段固定床反应器合成工艺。第一段进行F-T合成, 生成C1~C40烃类,在第二段反应器对C1~C40进行改质。
换热 水冷 循环气
合成气 预热 脱硫、 脱氧
气液分 离器 一 预热 段 反 应 器 二 段 反 应 器
换热
氨冷
气液分 离器
产品后加工过程不 同
2013-6-28
《煤炭气化工艺》
四、F-T合成工艺上的问题及改进措施
F-T合成反应为强放热反应,要解决排除大量反应热的问题.为了达到产品 的最佳选择性和催化剂使用寿命长的要求,反应需在等温条件下进行。
①尽快去掉反应热,以保持合适的反应温度,防止催化剂烧结、失去
活性和大量的甲烷生成。 ②降低反应器中的温度梯度,防止催化剂上积炭,使催化剂活性下降
蒸馏
异构化
聚合
液化气 醇 酮 汽油 柴油 中蜡 硬蜡
2013-6-28
《煤炭气化工艺》
(1)Arge固定床合成流程
吸收塔
回 收 C3 和 C4
换热器 合 成 气 净化 合成 气 预热 新鲜合 成气 蜡分离器
冷却器
碱
净化
固定床 反应器
分离器
冷 凝 油
水溶 性含 氧化 物
碱液
蜡
2013-6-28 《煤炭气化工艺》
循环气
油水分 离器
蒸 馏 塔
汽油
粗汽油 脱 蜡 换热 加 热 炉
残油
2013-6-28
《煤炭气化工艺》
2.MFT工艺流程的特点
①煤基合成气为原料,由于煤的气化方法不同,合成气中的V(H2)/V(CO)比 例在0.5~1.5之间变化。 ②工艺流程比较简单,投资费用低。MFT台成产品单一,主要为汽油产品,基 本不含重质烃类与含氧化合物,简化了产品的后加工流程。此外MFT合成的操 作温度和压力都较低,且等压操作,减少了过程的能耗,使投资费用大大降 低。 ③产品中主要为汽油,且质量较好。MFT合成产物中.汽油馏分较高-质量较 好,辛烷值可达80以上。
合成气的生产过程

水碳比 H2O/CH4摩尔比
水碳比
甲烷平衡含量(%)
2
18.0
4
7.9
6
1.0
P=3.5MPa、T=800℃
水碳比越高,甲烷平衡含量越低 高水碳比有利于抑制析碳副反应
压力 反应体积增大,低压有利平衡
催化剂
镍活性成分+助催化剂+载体+碱性物质
成分
助催化剂:提高活性、改善性能:金属氧化物 载体:提高表面积,防止烧结:Al2O3 或MgAl2O4尖晶石 碱性物质:中和酸性
C1化工指以合成气和甲烷为原料合成碳数为2或2个 以上化合物的化学工艺。
合成气的应用
合成氨 合成甲醇
合成醋酸
CH3OCH3 新燃料
烯烃的甲酰基化
合成天然气、汽油和柴油
新用途
煤变油
先转化为乙烯,再转化为其他 先转化为甲醇,再转化为汽油、乙烯等 直接转化为其他
目录
概述 由煤制合成气 由天然气制合成气 由渣油制合成气 一氧化碳的变换过程 脱硫与脱碳
合成气的生产过程
2020/8/13
目录
概述 由煤制合成气 由天然气制合成气 由渣油制合成气 一氧化碳的变换过程 脱硫与脱碳
合成气
合成气(syngas):CO与H2的混合气 H2: CO=1:2~3:1
合成气的制造:许多含碳资源如煤、天然气、石油馏 分、农林废料、城市垃圾等均可用来制造合成气
利用合成气可以转化为液体和气体燃料、大宗化学品 和高附加值的精细有机合成产度:1200℃ 压力:3MPa 煤的转化率:88~95% 特点:制得的水煤气中CH4和 CO2含量较高,而CO 含量较 低,适于制备城市煤气
流化床连续式气化
以高活性煤如褐煤或某些烟煤 为原料,生成气的组成为: H2 35~46%、CO 30~40%、 CO2 13~25%、CH4 1~2%, 目前多用于制氢、氨原料气和燃料煤气
合成气的制备方法
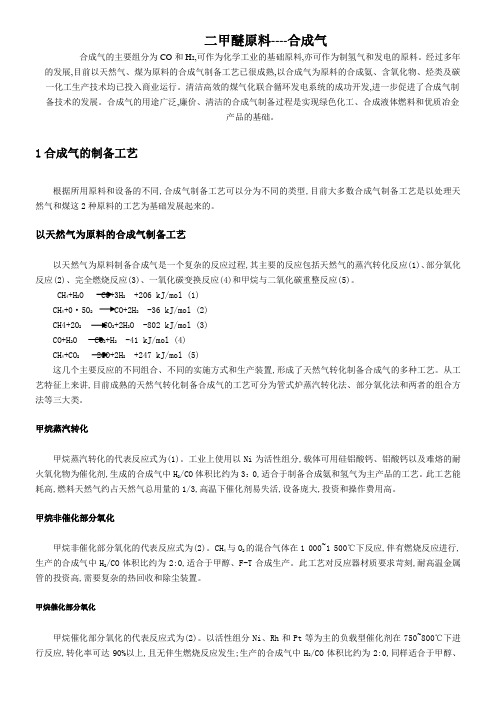
二甲醚原料----合成气合成气的主要组分为CO和H2,可作为化学工业的基础原料,亦可作为制氢气和发电的原料。
经过多年的发展,目前以天然气、煤为原料的合成气制备工艺已很成熟,以合成气为原料的合成氨、含氧化物、烃类及碳一化工生产技术均已投入商业运行。
清洁高效的煤气化联合循环发电系统的成功开发,进一步促进了合成气制备技术的发展。
合成气的用途广泛,廉价、清洁的合成气制备过程是实现绿色化工、合成液体燃料和优质冶金产品的基础。
1合成气的制备工艺根据所用原料和设备的不同,合成气制备工艺可以分为不同的类型,目前大多数合成气制备工艺是以处理天然气和煤这2种原料的工艺为基础发展起来的。
以天然气为原料的合成气制备工艺以天然气为原料制备合成气是一个复杂的反应过程,其主要的反应包括天然气的蒸汽转化反应(1)、部分氧化反应(2)、完全燃烧反应(3)、一氧化碳变换反应(4)和甲烷与二氧化碳重整反应(5)。
CH4+H2O CO+3H2 +206 kJ/mol (1)CH4+0·5O2 CO+2H2 -36 kJ/mol (2)CH4+2O2 CO2+2H2O -802 kJ/mol (3)CO+H2O CO2+H2 -41 kJ/mol (4)CH4+CO2 2CO+2H2 +247 kJ/mol (5)这几个主要反应的不同组合、不同的实施方式和生产装置,形成了天然气转化制备合成气的多种工艺。
从工艺特征上来讲,目前成熟的天然气转化制备合成气的工艺可分为管式炉蒸汽转化法、部分氧化法和两者的组合方法等三大类。
甲烷蒸汽转化甲烷蒸汽转化的代表反应式为(1)。
工业上使用以Ni为活性组分,载体可用硅铝酸钙、铝酸钙以及难熔的耐火氧化物为催化剂,生成的合成气中H2/CO体积比约为3:0,适合于制备合成氨和氢气为主产品的工艺。
此工艺能耗高,燃料天然气约占天然气总用量的1/3,高温下催化剂易失活,设备庞大,投资和操作费用高。
甲烷非催化部分氧化甲烷非催化部分氧化的代表反应式为(2)。
合成气的制备方法
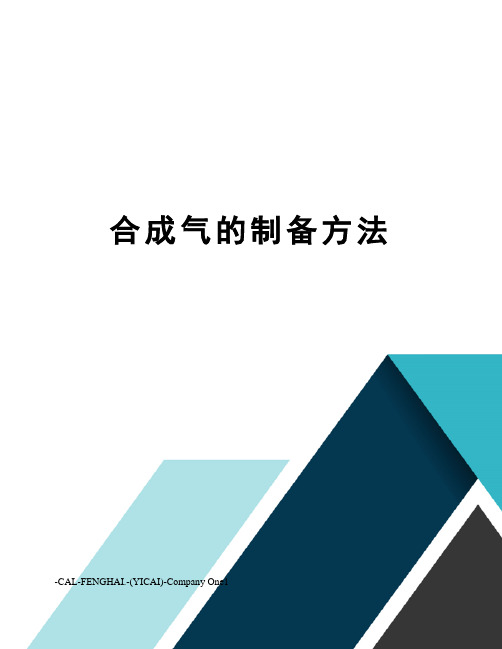
合成气的制备方法-CAL-FENGHAI.-(YICAI)-Company One1二甲醚原料----合成气合成气的主要组分为CO和H2,可作为化学工业的基础原料,亦可作为制氢气和发电的原料。
经过多年的发展,目前以天然气、煤为原料的合成气制备工艺已很成熟,以合成气为原料的合成氨、含氧化物、烃类及碳一化工生产技术均已投入商业运行。
清洁高效的煤气化联合循环发电系统的成功开发,进一步促进了合成气制备技术的发展。
合成气的用途广泛,廉价、清洁的合成气制备过程是实现绿色化工、合成液体燃料和优质冶金产品的基础。
1合成气的制备工艺根据所用原料和设备的不同,合成气制备工艺可以分为不同的类型,目前大多数合成气制备工艺是以处理天然气和煤这2种原料的工艺为基础发展起来的。
以天然气为原料的合成气制备工艺以天然气为原料制备合成气是一个复杂的反应过程,其主要的反应包括天然气的蒸汽转化反应(1)、部分氧化反应(2)、完全燃烧反应(3)、一氧化碳变换反应(4)和甲烷与二氧化碳重整反应(5)。
CH4+H2O CO+3H2 +206 kJ/mol (1)CH4+0·5O2 CO+2H2 -36 kJ/mol (2)CH4+2O2 CO2+2H2O -802 kJ/mol (3)CO+H2O CO2+H2 -41 kJ/mol (4)CH4+CO2 2CO+2H2 +247 kJ/mol (5)这几个主要反应的不同组合、不同的实施方式和生产装置,形成了天然气转化制备合成气的多种工艺。
从工艺特征上来讲,目前成熟的天然气转化制备合成气的工艺可分为管式炉蒸汽转化法、部分氧化法和两者的组合方法等三大类。
甲烷蒸汽转化甲烷蒸汽转化的代表反应式为(1)。
工业上使用以Ni为活性组分,载体可用硅铝酸钙、铝酸钙以及难熔的耐火氧化物为催化剂,生成的合成气中H2/CO体积比约为3:0,适合于制备合成氨和氢气为主产品的工艺。
此工艺能耗高,燃料天然气约占天然气总用量的1/3,高温下催化剂易失活,设备庞大,投资和操作费用高。
合成气的制备方法

二甲醚原料----合成气合成气的主要组分为CO和H2,可作为化学工业的基础原料,亦可作为制氢气和发电的原料。
经过多年的发展,目前以天然气、煤为原料的合成气制备工艺已很成熟,以合成气为原料的合成氨、含氧化物、烃类及碳一化工生产技术均已投入商业运行。
清洁高效的煤气化联合循环发电系统的成功开发,进一步促进了合成气制备技术的发展。
合成气的用途广泛,廉价、清洁的合成气制备过程是实现绿色化工、合成液体燃料和优质冶金产品的基础。
1合成气的制备工艺根据所用原料和设备的不同,合成气制备工艺可以分为不同的类型,目前大多数合成气制备工艺是以处理天然气和煤这2种原料的工艺为基础发展起来的。
1.1以天然气为原料的合成气制备工艺以天然气为原料制备合成气是一个复杂的反应过程,其主要的反应包括天然气的蒸汽转化反应(1)、部分氧化反应(2)、完全燃烧反应(3)、一氧化碳变换反应(4)和甲烷与二氧化碳重整反应(5)。
CH4+H2O CO+3H2+206 kJ/mol (1)CH4+0·5O2CO+2H2-36 kJ/mol (2)CH4+2O2CO2+2H2O -802 kJ/mol (3)CO+H2O CO2+H2-41 kJ/mol (4)CH4+CO22CO+2H2+247 kJ/mol (5)这几个主要反应的不同组合、不同的实施方式和生产装置,形成了天然气转化制备合成气的多种工艺。
从工艺特征上来讲,目前成熟的天然气转化制备合成气的工艺可分为管式炉蒸汽转化法、部分氧化法和两者的组合方法等三大类。
1.1.1甲烷蒸汽转化甲烷蒸汽转化的代表反应式为(1)。
工业上使用以Ni为活性组分,载体可用硅铝酸钙、铝酸钙以及难熔的耐火氧化物为催化剂,生成的合成气中H2/CO体积比约为3:0,适合于制备合成氨和氢气为主产品的工艺。
此工艺能耗高,燃料天然气约占天然气总用量的1/3,高温下催化剂易失活,设备庞大,投资和操作费用高。
1.1.2甲烷非催化部分氧化甲烷非催化部分氧化的代表反应式为(2)。
合成气的生产过程
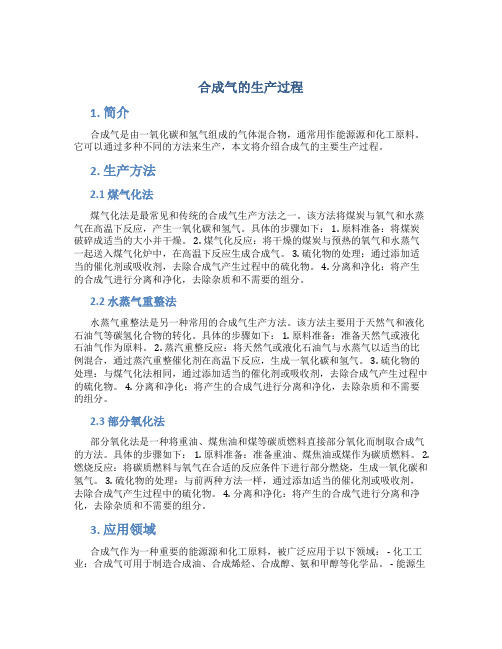
合成气的生产过程1. 简介合成气是由一氧化碳和氢气组成的气体混合物,通常用作能源源和化工原料。
它可以通过多种不同的方法来生产,本文将介绍合成气的主要生产过程。
2. 生产方法2.1 煤气化法煤气化法是最常见和传统的合成气生产方法之一。
该方法将煤炭与氧气和水蒸气在高温下反应,产生一氧化碳和氢气。
具体的步骤如下: 1. 原料准备:将煤炭破碎成适当的大小并干燥。
2. 煤气化反应:将干燥的煤炭与预热的氧气和水蒸气一起送入煤气化炉中,在高温下反应生成合成气。
3. 硫化物的处理:通过添加适当的催化剂或吸收剂,去除合成气产生过程中的硫化物。
4. 分离和净化:将产生的合成气进行分离和净化,去除杂质和不需要的组分。
2.2 水蒸气重整法水蒸气重整法是另一种常用的合成气生产方法。
该方法主要用于天然气和液化石油气等碳氢化合物的转化。
具体的步骤如下: 1. 原料准备:准备天然气或液化石油气作为原料。
2. 蒸汽重整反应:将天然气或液化石油气与水蒸气以适当的比例混合,通过蒸汽重整催化剂在高温下反应,生成一氧化碳和氢气。
3. 硫化物的处理:与煤气化法相同,通过添加适当的催化剂或吸收剂,去除合成气产生过程中的硫化物。
4. 分离和净化:将产生的合成气进行分离和净化,去除杂质和不需要的组分。
2.3 部分氧化法部分氧化法是一种将重油、煤焦油和煤等碳质燃料直接部分氧化而制取合成气的方法。
具体的步骤如下: 1. 原料准备:准备重油、煤焦油或煤作为碳质燃料。
2. 燃烧反应:将碳质燃料与氧气在合适的反应条件下进行部分燃烧,生成一氧化碳和氢气。
3. 硫化物的处理:与前两种方法一样,通过添加适当的催化剂或吸收剂,去除合成气产生过程中的硫化物。
4. 分离和净化:将产生的合成气进行分离和净化,去除杂质和不需要的组分。
3. 应用领域合成气作为一种重要的能源源和化工原料,被广泛应用于以下领域: - 化工工业:合成气可用于制造合成油、合成烯烃、合成醇、氨和甲醇等化学品。
合成气的制备方法

合成气的制备方法(总3页)--本页仅作为文档封面,使用时请直接删除即可----内页可以根据需求调整合适字体及大小--二甲醚原料----合成气合成气的主要组分为CO和H2,可作为化学工业的基础原料,亦可作为制氢气和发电的原料。
经过多年的发展,目前以天然气、煤为原料的合成气制备工艺已很成熟,以合成气为原料的合成氨、含氧化物、烃类及碳一化工生产技术均已投入商业运行。
清洁高效的煤气化联合循环发电系统的成功开发,进一步促进了合成气制备技术的发展。
合成气的用途广泛,廉价、清洁的合成气制备过程是实现绿色化工、合成液体燃料和优质冶金产品的基础。
1合成气的制备工艺根据所用原料和设备的不同,合成气制备工艺可以分为不同的类型,目前大多数合成气制备工艺是以处理天然气和煤这2种原料的工艺为基础发展起来的。
以天然气为原料的合成气制备工艺以天然气为原料制备合成气是一个复杂的反应过程,其主要的反应包括天然气的蒸汽转化反应(1)、部分氧化反应(2)、完全燃烧反应(3)、一氧化碳变换反应(4)和甲烷与二氧化碳重整反应(5)。
CH4+H2O CO+3H2 +206 kJ/mol (1)CH4+0·5O2 CO+2H2 -36 kJ/mol (2)CH4+2O2 CO2+2H2O -802 kJ/mol (3)CO+H2O CO2+H2 -41 kJ/mol (4)CH4+CO2 2CO+2H2 +247 kJ/mol (5)这几个主要反应的不同组合、不同的实施方式和生产装置,形成了天然气转化制备合成气的多种工艺。
从工艺特征上来讲,目前成熟的天然气转化制备合成气的工艺可分为管式炉蒸汽转化法、部分氧化法和两者的组合方法等三大类。
甲烷蒸汽转化甲烷蒸汽转化的代表反应式为(1)。
工业上使用以Ni为活性组分,载体可用硅铝酸钙、铝酸钙以及难熔的耐火氧化物为催化剂,生成的合成气中H2/CO体积比约为3:0,适合于制备合成氨和氢气为主产品的工艺。
- 1、下载文档前请自行甄别文档内容的完整性,平台不提供额外的编辑、内容补充、找答案等附加服务。
- 2、"仅部分预览"的文档,不可在线预览部分如存在完整性等问题,可反馈申请退款(可完整预览的文档不适用该条件!)。
- 3、如文档侵犯您的权益,请联系客服反馈,我们会尽快为您处理(人工客服工作时间:9:00-18:30)。
(2) 转化催化剂的使用和失活 转化催化剂在使用前是氧化态,装入反应器后应先进行 严格的还原操作,使氧化镍还原成金属镍才有活性。还原 气可以是氢气、甲烷或一氧化碳。转化催化剂在使用中出 现活性下降现象的原因主要有老化、中毒、积碳等。 催化剂在长期使用过程中,由于经受高温和气流作用, 镍晶粒逐渐长大、聚集甚至烧结,致使表面积降低,或某 些促进剂流失,导致活性下降,此现象称为老化。 许多 物质,例如硫、砷、氯、溴、铅、钒、铜等的化合物,都 是转化催化剂的毒物。最重要、最常见的毒物是硫化物, 上述反应是可逆的,称为暂时性中毒,可以再生。砷中毒 和卤素中毒是不可逆的,会使镍催化剂烧结而造成永久性 失活。
Hale Waihona Puke (2) 水碳比的影响 水碳比对于甲烷转化影响重大,高的水 碳比有利于甲烷的蒸汽重整反应,同时,高水碳比也有利 于抑制析碳副反应。 (3) 压力的影响 甲烷蒸气转化反应是体积增大的反应, 低压有利平衡,低压也可抑制一氧化碳的两个析碳反应, 但是低压对甲烷裂解析碳反应平衡有利,适当加压可抑制 甲烷裂解。压力对一氧化碳变换反应平衡无影响。 总之,从反应平衡考虑,甲烷水蒸气转化过程应该用适当 的高温、稍低的压力和高水碳比。
较早的气流床法是K-T法,由德国Koppers公司的 Totzek工程师开发成功,是一种在常压、高温下以水蒸气 和氧气与粉煤反应的气化法。气化设备为K-T炉。第二代 气流床是德士古法,由美国Texaco公司于20世纪80年代 初开发成功。
7.3由天然气制造合成气
7.3.1天然气制合成气的工艺技术及其进展
析炭危害: (1)炭黑覆盖在催化剂表面,堵塞微孔,降低催化剂活 性,使甲烷转化率下降而使出口气中残余甲烷增多。 (2)影响传热,使局部反应区产生过热而缩短反应管 使用寿命。 (3)使催化剂破碎而增大床层阻力,影响生产能力。 生产中,催化剂活性显著下降可由三个现象来判断:其一 是反应器出口气中甲烷含量升高;其二是出口处平衡温距 增大。平衡温距为出口实际温度与出口气体实际组成对应 的平衡温度之差。催化剂活性下降时,出口甲烷含量升高, 一氧化碳和氢含量降低,此组成对应的平衡常数减小,故 平衡温度降低,平衡温距增大。催化剂活性越低,平衡温 距则越大;其三是出现“红管”现象。因为反应是吸热的, 活性降低则吸热减少,而管外供热未变,多余热量将管壁 烧得通红。
(2)温度 从热力学角度看,高温下甲烷平衡浓度低,从
动力学看,高温使反应速率加快,所以出口残余甲烷含量 低。因加压对平衡的不利影响,更要提高温度来弥补。但 高温下,反应管的材质经受不了,需要将转化过程分为两 段进行。第一段转化800℃左右,出口残余甲烷10%(干 基)左右。第二段转化反应器温度1000℃,出口甲烷降至 0.3%。
化学工艺学电子教案——第七章
合成气的生产过程
7 合成气的生产过程
7.1 概述 7.2 由煤制合成气 7.3 由天然气制造合成气 7.4 由渣油制合成气 7.5 一氧化碳变换过程 7.6 气体中硫化物和二氧化碳的脱除
7.1 概述
合成气是指一氧化碳和氢气的混和气,英文缩写 是Syngas。其H2/ CO(摩尔比)由1/2到3/1。 合成气在化学工业中有着重要作用。
以上三式中各组分的分压均为体系在某指定状态时的实际 分压,而非平衡分压。可由温度、压力查出Kp,再根据指 定组成和总压计算Jp,最后由Jp/ Kp是否小于1来判断该 状态下有否析碳发生。 当Jp/ Kp<1时,⊿G<0,反应自发向右进行,会析碳; 当Jp/ Kp=1时,⊿G=0,反应达平衡,是热力学析碳的 边界; 当Jp/ Kp>1时,⊿G>0,反应不能自发进行,体系不析 碳。 甲烷水蒸气转化体系中,水蒸汽是一个重要组分,由各 析碳反应生成的碳与水蒸汽之间存在的平衡,通过热力学 计算,可求得开始析碳时所对应的H2O/CH4摩尔比,称 为热力学最小水碳比。不同温度、压力下有不同的热力学 最小水碳比。综上所述,影响甲烷水蒸气转化反应平衡的 主要因素有温度、水碳比和压力。
(3)水碳比 水碳比高,有利于防止积碳,残余甲烷含量 也低。实验指出,当原料气中无不饱和烃时,水碳比若小 于2,温度到400℃时就析碳,而当水碳比大于2时,温度 要高达1000℃才有碳析出;但若有较多不饱和烃存在时, 即使水碳比大于2,当温度≥400℃时就会析碳。为了防止 积碳,操作中一般控制水碳比在3.5左右。 (4)气流速度 反应炉管内气体流速高有利于传热,降低 炉管外壁温度,延长炉管寿命。当催化剂活性足够时,高 流速也能强化生产,提高生产能力。但流速不宜过高,否 则床层阻力过大,能耗增加。
7.3.4甲烷水蒸气转化反应动力学
由以上方程可知,对于一定的催化剂而言,影响反应速率 的主要因素有温度、压力和组成。 (1) 温度的影响 温度升高,反应速率常数k增大,反应速 率亦增大;在上式中还有一项Kp1也与温度有关,因甲烷 蒸汽转化是要吸热的,平衡常数随温度的升高而增大,结 果反应速率也是增大的。
在压力不太高时,Kp仅是温度的函数。表7-1列出了不同 温度时上述两个反应的平衡常数。
表7-1 甲烷水蒸气反应和一氧化碳变换反应的平衡常数
根据物料衡算可计算出反应后各组分的组成和分压,若反 应达平衡,该表中各项则代表各对应的平衡值,可将有关 组分的分压代入甲烷水蒸气转化制合成气反应的Kp1和 CO变换反应的Kp2的公式,整理后得到。 根据反应温度查出或求出Kp1和Kp2,再将总压和气体的 初始组成代入以上两式,解出nx和ny,那么 ,平衡组成 和平衡分压即可求出。平衡组成是反应达到的极限,实际 反应距平衡总是有一定距离的,通过对一定条件下实际组 成与平衡组成的比较,可以判断反应速率快慢或催化剂活 性的高低。在相同反应时间内,催化剂活性越高,实际组 成越接近平衡组成。 下面分析在什么情况下会有碳析出,如何避免或尽量减 少析碳的可能性。三个析碳反应也是可逆的,它们的平衡 常数式分别为:
7.1.1 合成气的生产方法
(1) 以煤为原料的生产方法:有间歇和连续两种操作方式。 煤制合成气中H2/ CO比值较低,适于合成有机化合物。 (2) 以天然气为原料的生产方法:主要有转化法和部分氧 化法。目前工业上多采用水蒸气转化法(steam reforming),该法制得的合成气中H2/ CO比值理论上是3, 有利于用来制造合成氨或氢气。 (3) 以重油或渣油为原料的生产方法:主要采用部分氧化 法(partial oxidation)。
7.1.2工业化的主要产品
1 已工业化的产品
(1) 合成氨 (2) 合成甲醇 (3) 合成醋酸 (4) 烯烃的氢甲酰化产品 (5) 合成天然气、汽油和柴油
2 合成气应用新途径
(1) 直接合成乙烯等低碳烯烃 (2) 合成气经甲醇再转化为烃类 (3) 甲醇同系化制乙烯 (4) 合成低碳醇 (5)合成乙二醇 (6)合成气与烯烃衍生物羰基化产物
现在暂且不考虑副反应来讨论主反应的化学平衡。三个主 反应中只有其中两个是独立的,通常认为第一个和第三个 是独立反应。反应达平衡时,产物含量达到最大值,而反 应物含量达最小值。列出这两个独立反应的化学平衡常数 式再加上物料衡算式,联立求解此方程,就可以计算出平 衡组成(一般用摩尔分数表示)
7.3.2甲烷水蒸汽转化反应和化学平衡
(1) 温度的影响 甲烷与水蒸气反应生成CO和H2是吸热的
可逆反应,高温对平衡有利,即H2及CO的平衡产率高, CH4平衡含量低。高温对一氧化碳变换反应的平衡不利, 可以少生成二氧化碳,而且高温也会抑制一氧化碳岐化和 还原析碳的副反应。但是,温度过高,会有利于甲烷裂解, 当高于700℃时,甲烷均相裂解速率很快,会大量析出碳, 并沉积在催化剂和器壁上。
7.2由煤制合成气
以煤或焦炭为原料,以氧气(空气、富氧或纯 氧)、水蒸气等为气化剂,在高温条件下通过 化学反应把煤或焦炭中的可燃部分转化为气体 的过程,其有效成分包括一氧化碳、氢气和甲 烷等。
7.2.1煤气化的基本反应
1 煤气化过程的主要反应
这些反应中,碳与水蒸气反应的意义最大,此反应为 强吸热过程。碳与二氧化碳的还原反应也是重要的气化反 应。气化生成的混合气称为水煤气。总过程为强吸热的。 提高反应温度对煤气化有利 ,但不利于甲烷的生成。 当温度高于900℃时,CH4和CO2的平衡浓度接近于零。 低压有利于CO和H2生成,反之,增大压力有利于CH4生 成。
7.3.3甲烷水蒸气转化催化剂
(1)转化催化剂的组成和外形 工业上一直采用镍催化剂,并添加一些助催化剂,如铝、 镁、钾、钙、钛、镧、鈰等金属氧化物。催化剂应该具有 较大的镍表面。提高镍表面的最有效的方法是采用大比表 面的载体,为了抑制烃类在催化剂表面酸性中心上裂解析 碳,往往在载体中添加碱性物质中和表面酸性。 目前,工业上采用的转化催化剂有两大类,一类是以高温 烧结的α-Al2O3或MgAl2O4尖晶石为载体,用浸渍法将含 有镍盐和促进剂的溶液负载到预先成型的载体上,再加热 分解和煅烧,称之为负载型催化剂,镍在整个催化剂颗粒 中的含量可以很低,一般为10%~15%(按NiO计);另 一类转化催化剂以硅铝酸钙水泥作为粘接剂,与用沉淀法 制得的活性组分细晶混合均匀,成型后用水蒸气养护,使 水泥固化而成,称之为粘结剂催化剂,镍的含量高些,一 般为20%~30%(按NiO计)。
(2) 压力的影响 总压增高,会使各组分的分压也增高,对 反应初期的速率提高很有利。此外加压尚可使反应体积减 小。 (3) 组分的影响 原料的组成由水碳比决定,H2O/CH4过 高时,虽然水蒸气分压高,但甲烷分压过低,反应速率不 一定高;反之,H2O/CH4过低时,反应速率也不会高。 所以水碳比要适当。在反应初期,反应物CH4和H2O的浓 度高,反应速率高。到反应后期,反应物浓度下降,产物 浓度增高,反应速率降低,需要提高温度来补偿。