Process simulation and optimization of laser tube bending
AlSi9Mg变速箱下壳低压铸造工艺模拟及优化
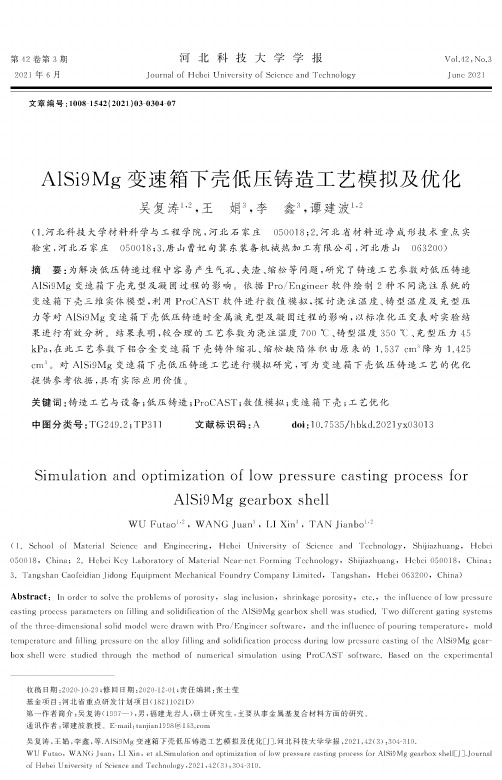
WU Futao1,, WANG Juan3 , LI Xin3 , TAN Jianbo1,
(1. School of Material Science and Engineering, Hcbci University of Science and Technology, Shijiazhuang, Hcbci 050018, China; 2. Hebei Key Laboratory of Material Near-net Forming Technology, Shijiazhuang, Hebei 050018, China; 3. Tangshan Caofeidian J idong Equipment Mechanical Foundry Company Limited, Tangshan, Hebei 063200, China.)
收稿日期:2020-10-29;修回日期:2020-12-01;责任编辑:张士莹 基金项目:河北省重点研发计划项目(18211021D) 第一作者简介:吴复涛(1997—)男,畐建龙岩人,硕士研究生,主要从事金属基复合材料方面的研究. 通讯作者:谭建波教授.E-mail: tanjanl9 98@ 吴复涛,王娟,李鑫,等.AlSi9Mg变速箱下壳低压铸造工艺模拟及优化[J].河北科技大学学报,021,2(3)304-310. WU Futao, WANG Juan, LI Xin, et al.Simulation and optimization of low pressure casting process for A1S19Mg gearbox shell[J].Journal of Hebei University of Science and Technology.2021.42(3) : 304-310.
仿真算法知识点总结

仿真算法知识点总结一、简介仿真算法是一种通过生成模型和运行模拟来研究系统或过程的方法。
它是一种用计算机模拟真实世界事件的技术,可以用来解决各种问题,包括工程、商业和科学领域的问题。
仿真算法可以帮助研究人员更好地理解系统的行为,并预测系统未来的发展趋势。
本文将对仿真算法的基本原理、常用技术和应用领域进行总结,以期帮助读者更好地了解和应用仿真算法。
二、基本原理1. 离散事件仿真(DES)离散事件仿真是一种基于离散时间系统的仿真技术。
在离散事件仿真中,系统中的事件和状态都是离散的,而时间是连续变化的。
离散事件仿真通常用于建模和分析复杂系统,例如生产线、通信网络和交通系统等。
离散事件仿真模型可以用于分析系统的性能、验证系统的设计和决策支持等方面。
2. 连续仿真(CS)连续仿真是一种基于连续时间系统的仿真技术。
在连续仿真中,系统中的状态和事件都是连续的,而时间也是连续的。
连续仿真通常用于建模和分析动态系统,例如电力系统、控制系统和生态系统等。
连续仿真模型可以用于分析系统的稳定性、动态特性和系统参数的设计等方面。
3. 混合仿真(HS)混合仿真是一种同时兼具离散事件仿真和连续仿真特点的仿真技术。
混合仿真可以用于建模和分析同时包含离散和连续过程的系统,例如混合生产系统、供应链系统和环境系统等。
混合仿真模型可以用于分析系统的整体性能、协调离散和连续过程以及系统的优化设计等方面。
4. 随机仿真随机仿真是一种基于概率分布的仿真技术。
在随机仿真中,系统的状态和事件都是随机的,而时间也是随机的。
随机仿真通常用于建模和分析具有随机性质的系统,例如金融系统、天气系统和生物系统等。
随机仿真模型可以用于分析系统的风险、概率特性和对策选择等方面。
5. Agent-Based ModelingAgent-based modeling (ABM) is a simulation technique that focuses on simulating the actions and interactions of autonomous agents within a system. This approach is often used for modeling complex and decentralized systems, such as social networks, biologicalecosystems, and market economies. In ABM, individual agents are modeled with their own sets of rules, behaviors, and decision-making processes, and their interactions with other agents and the environment are simulated over time. ABM can be used to study the emergent behavior and dynamics of complex systems, and to explore the effects of different agent behaviors and interactions on system-level outcomes.三、常用技术1. Monte Carlo方法蒙特卡洛方法是一种基于随机模拟的数值计算技术。
汽车总装车间生产物流流程建模与仿真优化

Chang’an University, Xi’an, China
摘要
科学合理的生产物流系统可将生产调整至最优状态,消灭浪费,使流动更加流畅, 实现资源合理配置,进而提高企业生产运作效率并快速响应市场,这直接关系到汽车制 造企业的经济效益与市场份额。而生产物流系统又是一个复杂动态的系统,如何选取适 当的研究方法,来准确地模拟反映现实生产物流系统显得尤为重要。
1.2 文献综述 ....................................................................................................................................... 2 1.2.1 生产物流流程优化理论研究综述 .................................................................... 2 1.2.2 生产物流流程优化方法研究综述 .................................................................... 3
aspen流程模拟外文文献

aspen流程模拟外文文献Aspen is a powerful flow simulation software widely used in various industries for process optimization and design. Aspen流程模拟软件是一种强大的流程模拟软件,在各个行业被广泛用于流程优化和设计。
With its user-friendly interface and advanced simulation capabilities, Aspen has become a go-to tool for engineers and researchers looking to analyze and improve their processes. Aspen凭借其用户友好的界面和先进的模拟能力,已经成为工程师和研究人员分析和改进其流程的常用工具。
Whether it's in the chemical, pharmaceutical, or food industries, Aspen can provide valuable insights and data to help increase efficiency and reduce costs. 无论是在化工、制药还是食品行业,Aspen都可以提供宝贵的见解和数据,帮助提高效率和降低成本。
One of the key features of Aspen is its ability to model complex processes and systems with accuracy and precision. Aspen的一个关键特点是能够精确地对复杂流程和系统进行建模。
By inputting various parameters and conditions, users can simulate different scenariosand predict outcomes before implementing any changes in the real world. 通过输入各种参数和条件,用户可以模拟不同的场景,并在实际世界中实施任何变化之前预测结果。
乙烯装置低温分离流程模拟与优化

大连理工大学专业学位硕士学位论文摘要乙烯装置是三烯的来源,是将炼厂资源转化为化工原料的关键,是现阶段国家炼化一体化进程中的龙头装置。
未来十年,我国乙烯产能将以500-600万吨/年的增速增长,故针对乙烯流程,尤其是工业装置流程的节能降耗研究十分重要。
根据裂解气组成不同,乙烯装置可选择的分离序列及换热网络组织形式千变万化。
至今,有许多针对低温分离过程中冷量与轴功进行分析的方法论问世,并不断更新进步,可对低温分离流程的分离过程及换热网络进行分析与优化,但它们更多应用在算例比对或工业装置流程片段上,较少用于工业装置全低温流程的节能降耗分析。
本文基于Aspen Plus平台对某厂乙烯装置的低温分离流程进行建模,并与该流程设计值进行比较,得到可以反映该装置真实分离效果及能耗的模型。
通过模拟计算得到的制冷机组制取冷量所需轴功消耗,与设计值比较误差低于5%,证明全流程建模过程中各冷量用户的模拟准确,模型可用于对该装置的节能降耗潜力进行分析。
通过搭建的低温分离流程模型所得的流股信息,基于Aspen Energy Analyzer平台对该装置低温分离流程全流程进行分析,结果表明该装置部分冷量与用户的匹配跨越了品位,出现高能低用的现象;总组合曲线中的“冷袋”存在降低㶲损的潜力,如优化冷量回收方式强化流程的分离过程;冷箱中的部分匹配存在冷热流股传热温差过大,㶲损较大的现象。
综上,该装置低温分离流程的换热网络存在较大节能挖潜的空间。
根据上述分析,对该装置低温分离流程进行分离过程及换热网络的优化。
针对低压脱丙烷塔进行塔总组合曲线分析,得出增设中间再沸器的优化方案,从而降低低温分离流程0.45MPaG蒸汽消耗13.6%;通过于脱甲烷单元应用低能耗乙烯分离技术,强化脱甲烷单元的分离过程,将装置乙烯产品收率由99.3%提高至99.6%;对脱乙烷-乙烯精馏单元流程进行优选及参数调优,低脱乙烷塔冷凝器负荷16.1%,并降低乙烯精馏塔塔顶气相至乙烯制冷机的气相流量8.3%。
CADCAM英文版期末复习资料

一. What is CAD, CAPP, CAM and CIMS, and briefly describe the relationship between them.1.CAD: computer-aided design ,it mainly refers to the use of the computer to complete the entire process of product design generally including CAD design and analysis of two aspects.2, CAPP: Computer Aided Process Planning, it refers to the use of computer technology to complete process planning of part machining.3.CAM: computer-aided manufacturing, it refers to the use of computers and numerical control equipment (such as CNC machine tools, machining centers, etc.) to manufacture parts.4.CAD / CAM: computer-aided design and computer-aided manufacturing referred to using the computer as the primary means to generate and use a variety of digital information and graphical information for the design and manufacture of the product.5.The relationship between CAD, CAPP, CAM: Generally speaking, CAD / CAM CAD / CAPP / CAM of. Referred to that contained in the CAD / CAM systems have CAPP. CAD system to produce parts (including geometricinformation and process manufacturing information, such as tolerance requirements, surface roughness, etc.). CAPP system to accept information from CAD, and the use of reasonable design, process design knowledge processing, optimized processing parameters and processing equipment. CAM CAD / CAPP / CAM system to accept the part information from the CAD and CAPP process planning and process parameters, after the processing of the CAM system to generate NC code, incoming numerical control equipment control equipment automatically processed6.CAD / CAM technology trends: integrated, intelligent, standardization, network-based, three-dimensional二:CADCAM1: Fill in the blanks (the big issue 20 small problem, every empty 1.5 points, a total of 30 points)(1) FMS is the abbreviation of Flexible Manufacturing System.(2) APT is an automatic programming tool (Automatically Programmed Tool) .(3) CAM is the abbreviation of computer aidedmanufacturing.(4) IMS is an abbreviation of the Intelligent Manufacturing Systems (Intelligent Manufacturing System.(5) RPM Rapid Prototyping / parts manufacturing (Rapid Prototyping / Parts Manufacturing abbreviation. (6) AM agile manufacturing Agile Manufacturing of abbreviations.(7) CAD functions can be grouped into geometric model, the four categories of engineering analysis, dynamic simulation and automatic drawing.(8) the engineering database for input and output, and management is required in the design process of the data used and generated by the pattern, documents, etc..(9) usually refers only to the narrow CAM NC program preparation, including the regulation of the tool path, the cutter location file generated simulation of the tool path and NC code generation.(10) The development of application software based on the the User programming language (UPL) supporting and CAD / CAM software system integrally has a good user interface, such enhancements may extend the functionof the CAD / CAM software system.(11) The application software can be automatic programming software, including identifying and processing of the source language software written by the CNC language (such as the APT language software) and a variety of CAD / CAM software.(12) to optimize the design including the optimization of the overall program the part structure optimization and optimization of process parameters.(13) CAD / CAM is a human-computer interaction process, from the shape of the products, ideas and programs, structural analysis process simulation system at any time to ensure the user to view, modify, intermediate results, real-time editing process.(14) modeling technique is the core of the CAM system, for the design and manufacture of the product to provide all the basic data and the original information, is the basis of the subsequent processing.(15) CAD / CAM system according to the three-dimensional model to calculate the geometric characteristics and physical characteristics of the corresponding objects.(16) CAD / CAM system with good information transmission management functions and information exchange process, to support the design and manufacture of the whole process of information transmission and exchange, and the transmission and sharing of information between multiple designers and design teams.(17) CIMS subsystem including management information systems, manufacturing automation systems and CAD / CAPP / CAM integrated system.(18) networking equipment necessary equipment, CAD / CAM systems set up its network equipment is composed of a computer network hubs, network cards, the transmission medium.(19) System software is responsible for managing hardware resources and software resources, for all users, it is a public computer software, including operating systems, compilers, graphics jack and jack standard.(20) Boolean operations, including pay and poor kinds of operations.2: Explain the following terms (the big issue of 6, atotal of 18 points)(1) parametric modeling: parametric modeling is to first establish the constraint relationship between the graphics and size parameters, and then use constraints to define and modify the geometry model. Size constraints and topological constraints reflect the factors to be considered in the design. Because the parameters of a set of parameters to maintain a certain relationship with these constraints, the initial design of the entity is natural to meet these constraints, enter the new parameter values will also keep these constraints and get a new geometric model.(2) plane contour sweeping method: planar contour sweeping method is closely combined with a two-dimensional system, commonly used in a way prismatic or rotary generated. Planar contour scanning method is translated in space by any plane contour a distance or around a fixed axis of rotation of will scan an entity. The plane contour scanning of the prerequisites is to have a closed planar contour (ie the plane contour scanning voxel). Closed planar contour is moved along one coordinate direction orrotation around a given axis.(3) Forming manufacturing technology: molding manufacturing technology is casting, plastic processing, connection, a collection of techniques of powder metallurgy unit. Prototyping and manufacturing technologies are manufacturing the workpiece blank, close to the shape of the part to be made directly workpiece precision molding technology. Plastic molding and grinding combined will replace most of the small parts machining.(4) Boolean operators: Boolean operators is the basis of geometric modeling technology, it is a set operation from Boolean algebra. Boolean operations voxel can be combined into complex shapes, the two objects combined to construct a new object. Boolean operations can facilitate the construction of complex geometric entities. Therefore, in the geometric modeling Boolean operation is very important. Boolean operators include cross (intersection), and (Union) (Difference) three operations.(5) contour milling: the tool contour inspection hierarchical processing of the workpiece, theperipheral contour finishing choose a method.The milling part contour to be considered to maximize the use of the climb milling processing methods, this can increase the surface roughness of parts and machining accuracy and reduce the Machine "flutter". To select reasonable into the retraction position, try to avoid along the part contour method to pause midway to cut and feed; into the retraction position is to be elected in a less important position; when the workpiece border open, in order to ensure processing surface quality, should be outside the boundaries of the workpiece into and retract.(6) virtual manufacturing: the virtual manufacturing is to achieve the essence of the actual manufacturing process on the computer, that computer simulation and virtual reality technology, group work together on the computer, product design, process planning, manufacturing, performance analysis, quality inspection and enterprise levels, process management and control products such as the nature of the manufacturing process in order to enhance the manufacturing process at all levels of decision-makingand control.(7)modification technology: modification technology, including the technology of heat treatment and surface engineering. The major trends is achieved through a variety of new precision heat treatment and composite processing the accurate performance parts, precision of shapes and sizes and a variety of special performance requirements of the surface (coating), while significantly reducing energy consumption and completely eliminate the pollution of the environment.(8) placed characteristics: Place features include hole features, round features, chamfer feature array characteristics. Placing characterized in that the parametric feature to change the location of the feature size and shape parameters, characteristic shape can be changed. Placed generally characterized by late in Part modeling was gradually added, because these features are designed to supplement and refine Part, such as the premature join, will shape the inconvenience.(9) feature-based modeling: feature-based modeling is usually characterized by the shape model the accuracyfeature model, material characteristics model, the shape of the feature model is the core and foundation of feature-based modeling. Is characterized by an integrated concept, as a carrier of information in the product development process, in addition to containing the part geometry and topology information, but also includes some non-geometric information required in the design and manufacturing process. Feature-based modeling is a built in solid modeling based on the use of the characteristics of the concept-oriented modeling method of the entire product design and manufacturing process design, it not only contains information related to the production, but also to describe the relationship between these information .(10) tool set sub-sequence method: Tool centralized sub-sequence method is used by the the tool division process, the site can be completed with the same knife finish machining parts, and then the second, third knife they can accomplish other parts. This can reduce the number of tool changes, compressed air-way time, reduce unnecessary positioning error.(11) geometric modeling: geometric modeling bygeometric elements such as point, line, surface, body, after geometric transformations such as translation, rotation and cross, and poor Boolean operations, resulting in a solid model. Geometric modeling technology as the basis of the CAD / CAM technology, wide range of applications in the field of mechanical engineering.(12) characterized in tree: a feature-based modeling process, the characteristics of 11 successively added to the model, the follow-up characteristic feature attached to the front, the front characteristics of the changes will affect the follow-up characteristics of the changes. In order to properly record the course of feature-based modeling, the use of the feature tree "concept, feature-based modeling process as a tree growing process, starting from the root (basic features), and gradually grow tree twigs (additional features). Part structure of different levels of complexity, the complexity of the feature tree type. Brief answer (the big 4, a total of 25 points)(1) CAD / CAM system (6)1. A variety of CAD / CAM systems basic human-computerinteraction (also known as man-machine dialogue) (1) 2. The operator according to the specific requirements of the instruction issued to the computer (1),3. Computer will be the result of the operation in the form of graphics or data displayed on the computer display (1)4. Operator via the input device to issue a new command to the computer (1).5. Computer according to the new instructions to complete the new instruction (1).6. The job information in the CAD / CAM generated continuously modify, exchange, access process. (2) (2) which aspects should pay attention to when the workpiece is being clampedShould maximize the use of modular fixture, but when the workpiece bulk, high precision, you can design special fixtures. (1)2 part positioning, clamping parts should be without prejudice to the measurement of the various parts of the processing, the replacement of the tool as well as important parts of the tool and the workpiece, tool and fixture collision phenomenon, in particular, should beavoided. (2)3 clamping force should seek close to the main points of support within the triangle formed by the points of support; should seek close to the cutting area, and rigid; Try not above the aperture processing, to reduce the warp. (2)4 parts clamping, positioning to consider the consistency of repeated installations, in order to reduce the time on the knife to improve the consistency of the same batch parts processing; generally the same batch of parts with the same positioning reference and the same clamping means. (2)(3) how to determine the point on the knife and tool change point (6)1. Knife point CNC machining starting point of the tool relative to the workpiece movement, the position of the tool in the workpiece coordinate system. (1)2. Determine the knife point of principle is: to facilitate the mathematical processing and simplify programming; easy alignment on the machine; to facilitate inspection process; processing errors caused by small. (2)3. Knife point can be set on the part fixture or machine, but must be part of the positioning reference coordinate dimensions, so as to determine the relationship between the machine coordinate system and workpiece coordinate system. (1)4. When you require a higher accuracy of the knife, the knife point should be selected on the part of the design basis or process basis. For parts positioning hole, the election center of the hole as the knife point. (1)5. Should be on the knife, the knife point coincide with the knife sites. Knife sites for end mills, end mill as the center of the underside of the head, the ball head center ball end mill for turning, boring tool is the tool tip for the drill bit to drill tip. (1)6. The tool change point should be determined according to the process content. In order to prevent the tool bumps workpiece is when the tool change, tool change point should be located in the outside of the part or fixture. (1)(4) the difference of the feature tree and the course number and contact (7)1. "Feature tree" and subsequent features characteristic attached to the front, the front characteristics of the changes will affect the follow-up characteristic changes. A complex parts by many characteristics, the characteristics of complex dependencies (2)2. Feature tree for parametric modeling system (2)3. History tree the variable modeling system using (2)4. Characteristics in addition to the "history tree" remain associated with the characteristics of the front, at the same time to establish contact with the system global coordinate system. The history tree also allows a number of parts merged together to construct a complex parts. The history tree clearly documented the design process, easy to modify, easy multiplayer co-design.(1)IV: Analysis answer the following questions (the big issue of small, a total of 27 points)(1) feature-based solid modeling method which is divided into several categories, its shape What are the steps (13)A modeling program planning: including thecharacteristics of the analysis part, the relationship between the analysis part features, the construction method of the analysis of the characteristics of the construction sequence and characteristics. (4)2 Create the basic characteristics of the basic features: the building blocks of a part. (3)3 to create additional features: add on additional features one by one according to the shape of program planning. (2)4 Edit to modify the characteristics of: any time in the process of feature-based modeling can be modified characteristics, including modifying the characteristics of the shape, size, location, or characterized by affiliation, or even delete constructed features. (3)5 generated drawings: 3D to 2D technologies interact to generate two-dimensional drawings. (2)(2) CNC machining process decision with which aspects and Description (14)1 Make sure the processing program. Determine the processing program should be considered a reasonable and economical use of CNC machine tools, and give fullplay to the functions of the CNC machine tools. (2) 2 fixture design and selection. Should pay particular attention to speedy completion of the positioning of the workpiece and clamping process, in order to reduce the auxiliary time. Using modular fixture, production preparation period is short, fixture parts can be used repeatedly, the effect of the economy. In addition, the fixture should be easy to install, easy to size relationship between the coordination of the workpiece and machine coordinate system.3 Select the feed path. Reasonable choice of the feed path for CNC machining is very important. Should consider the following aspects: as far as possible to shorten the feed path, to reduce idling knife trip, improve production efficiency; reasonable selection from the knife point, entry point and cut way to ensure a smooth cut, there is no impact; ensure the accuracy and surface of the machined parts roughness requirements; guarantee the security of the process, to avoid the interference of the surface of the tool and the non-processing; help simplify the numerical calculation, to reduce the number of block programmingworkload. (5)4 Select a reasonable tool. To select the tool should be based on the performance of the workpiece material, the processing capacity of the machine, the type of processing operations, cutting and other process-related factors, including the structure of the tool type, material grades and geometrical parameters. (3)5 to determine a reasonable cutting.。
仿真花不同类型的英文术语

仿真花不同类型的英文术语在仿真领域中,有许多不同类型的英文术语。
下面是一些常见的术语及其解释:1. Simulation (仿真): The imitation or representation of the operation or features of one system through the use of another system, typically a computer program. It is used to study, analyze, and predict the behavior of complexreal-world systems.2. Virtual Reality (虚拟现实): A computer-generated simulation of a three-dimensional environment that can be interacted with and experienced by a person. It typically involves the use of a head-mounted display and other sensory devices to create a sense of presence in thevirtual world.3. Augmented Reality (增强现实): An interactive experience that combines real-world elements with computer-generated sensory inputs, such as graphics, sound, or GPSdata. It enhances the user's perception of the real world by overlaying digital information onto the physical environment.4. Agent-based Modeling (基于代理的建模): A simulation technique that models the behavior of individual agents or entities and their interactions within a system. Agents can represent individuals, organizations, or other entities, and their behavior is governed by predefined rules or algorithms.5. Monte Carlo Simulation (蒙特卡洛仿真): A statistical technique that uses random sampling to model and analyze the behavior of complex systems. It is particularly useful for assessing the risk and uncertainty associated with decision-making processes.6. Discrete Event Simulation (离散事件仿真): A simulation technique that models the behavior of a system as a sequence of discrete events in time. It is commonly used to study systems with dynamic, time-dependent processes, such as manufacturing systems or transportationnetworks.7. Continuous Simulation (连续仿真): A simulation technique that models the behavior of a system as a continuous function of time. It is often used to study systems with continuous, time-dependent processes, such as fluid dynamics or electrical circuits.8. Sensitivity Analysis (敏感性分析): A technique used to assess the impact of changes in input parameters or assumptions on the output of a simulation model. It helps identify the most influential factors and understand the robustness of the model.9. Validation (验证): The process of comparing the behavior of a simulation model to the real-world system it represents. It involves verifying that the model accurately reproduces the observed behavior and meets the intended objectives.10. Optimization (优化): The process of finding the best possible solution to a problem within a given set ofconstraints. In simulation, optimization techniques are often used to identify the optimal configuration or parameter values that maximize or minimize a certain objective.这些术语涵盖了仿真领域的一些关键概念和技术。
成型仿真操作流程的归纳
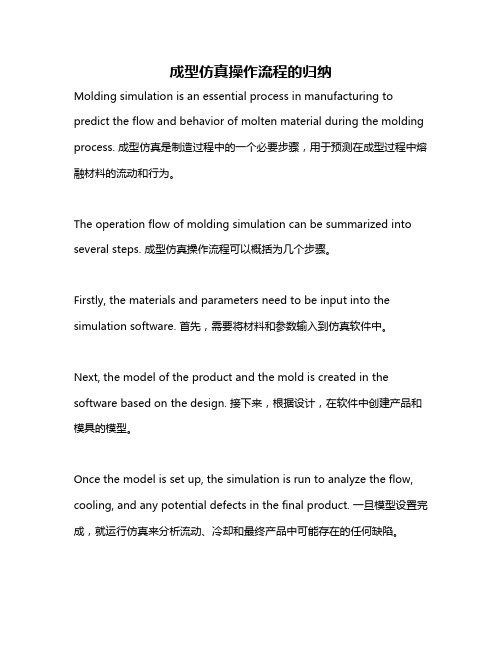
成型仿真操作流程的归纳Molding simulation is an essential process in manufacturing to predict the flow and behavior of molten material during the molding process. 成型仿真是制造过程中的一个必要步骤,用于预测在成型过程中熔融材料的流动和行为。
The operation flow of molding simulation can be summarized into several steps. 成型仿真操作流程可以概括为几个步骤。
Firstly, the materials and parameters need to be input into the simulation software. 首先,需要将材料和参数输入到仿真软件中。
Next, the model of the product and the mold is created in the software based on the design. 接下来,根据设计,在软件中创建产品和模具的模型。
Once the model is set up, the simulation is run to analyze the flow, cooling, and any potential defects in the final product. 一旦模型设置完成,就运行仿真来分析流动、冷却和最终产品中可能存在的任何缺陷。
After the simulation, the results are analyzed to make any necessary adjustments to the design or process. 仿真之后,需要分析结果,并对设计或工艺进行必要的调整。
Finally, the optimized design and process are implemented for actual production. 最后,优化后的设计和工艺被用于实际生产。
- 1、下载文档前请自行甄别文档内容的完整性,平台不提供额外的编辑、内容补充、找答案等附加服务。
- 2、"仅部分预览"的文档,不可在线预览部分如存在完整性等问题,可反馈申请退款(可完整预览的文档不适用该条件!)。
- 3、如文档侵犯您的权益,请联系客服反馈,我们会尽快为您处理(人工客服工作时间:9:00-18:30)。
There are many influencing factors on laser tube forming, such as forming process parameters, material’s properties, optic parameters, and geometrical parameters. Figure 1 gives factors of influence on laser tube bending. The melting point and yield strength are basic conditions to restrict to the forming process. For a given forming objective, material’s properties and geometrical parameters of the tube are already decided. The aim of the laser tube bending is to acquire the desired bending deformation by means of the reasonable match of the process parameters.
Compared to laser bending of sheet metals, the laser tube bending is more complex because much more process parameters are involved. Meanwhile, the laser tube bending has a high demand on forming machine and tools. Thus, the forming process is hard to be controlled. Few researches involved laser tube bending. Nao and Li [5] investigated the developments of stress and strain during laser tube bending by means of a thermal–mechanical finite element transient analysis. A new analytical model [6] describing the bending angle was established. The model gives an analytical expression for the bending angle as a function of the energy (laser power, absorption, and scanning speed), geometric (tube diameter and wall thickness), and material properties (coefficient of thermal expansion, density, heat capacity, Young’s modulus, and yield stress). Hsieh [7, 8] investigated the buckling mechanism of a thin metal tube with and without axial preloads during laser forming numerically and experimentally. Zhang [9] studied numerically different laser scanning schemes for tube bending without and with water cooling. Safdar [10] studied the effect of scanning direction on laser tube bending using finite element analysis.
Y. Guan (*) : S. Sun : G. Zhao
Key Laboratory for Liquid–Solid Structural Evolution and Processing of Materials Ministry of Education, Shandong University, Jinan, China e-mail: guan_yanjin@
G. Yuan Jining Vocational Technology College, Jining 272000, China
velocity are 426.12 W, 4.9 mm, 14.31 mm/s respectively, a fixed angle bending can be achieved.
Keywords Laser tube bending . FEM . Process simulation . Process optimization . Genetic algorithm
1 Introduction
Laser bending is a noncontact method of 2D bending, 3D shaping, and precision alignment of metallic and nonmetallic components using laser energy [1–4]. Based on laser bending, sheets and tubes can be formed conveniently depending upon the non-uniform thermal stresses induced by laser heating.
Байду номын сангаас
334
Int J Adv Manuf Technol (2013) 65:333–342
Guglielmotti [11] studied bending of slotted tubes as well as enlarging of one tube end by means of a high power diode laser and found that high power diode lasers are very efficient laser sources for tube forming due to their large laser spot.
Received: 6 November 2008 / Accepted: 13 April 2012 / Published online: 5 May 2012 # Springer-Verlag London Limited 2012
Abstract A 3D thermomechanical finite element analysis model for laser tube bending is developed based on the software MSC/Marc. The processes of single- and multiscan are analyzed numerically. The gradient and development of the temperature between the laser scanning side and the nonscanning side leads to the changing complexity of the stress and strain. Consequently, the length of the laser scanning side becomes shorter than that of nonscanning side after cooling. The length difference between both sides makes the tube produce the bending angle. The relationship between the number of scans and the bending angle is about in direct ratio. The bending angle induced by the first irradiated time is largest. Meanwhile, the finite element simulation is integrated with the genetic algorithm. Aiming at different process demands, corresponding objective functions are established. Laser power, beam diameter, scanning velocity, and scanning wrap angle are regarded as design variables. Process optimizations of maximum angle bending and fixed angle bending after single laser scan are realized. Groups of optimized process parameters can be obtained according to different optimization objectives. The bending angle can approach to the maximum when the laser power, spot diameter, scanning velocity, and scanning wrap angle are 381.24 W, 3.37 mm, 16.34 mm/s, and 123.1°, respectively. When the laser power, spot diameter and scanning