供应商DFC培训
施耐德供应商管理流程
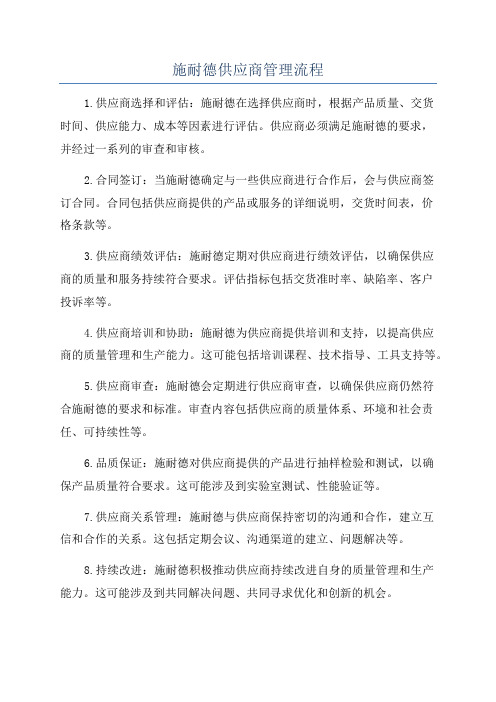
施耐德供应商管理流程1.供应商选择和评估:施耐德在选择供应商时,根据产品质量、交货时间、供应能力、成本等因素进行评估。
供应商必须满足施耐德的要求,并经过一系列的审查和审核。
2.合同签订:当施耐德确定与一些供应商进行合作后,会与供应商签订合同。
合同包括供应商提供的产品或服务的详细说明,交货时间表,价格条款等。
3.供应商绩效评估:施耐德定期对供应商进行绩效评估,以确保供应商的质量和服务持续符合要求。
评估指标包括交货准时率、缺陷率、客户投诉率等。
4.供应商培训和协助:施耐德为供应商提供培训和支持,以提高供应商的质量管理和生产能力。
这可能包括培训课程、技术指导、工具支持等。
5.供应商审查:施耐德会定期进行供应商审查,以确保供应商仍然符合施耐德的要求和标准。
审查内容包括供应商的质量体系、环境和社会责任、可持续性等。
6.品质保证:施耐德对供应商提供的产品进行抽样检验和测试,以确保产品质量符合要求。
这可能涉及到实验室测试、性能验证等。
7.供应商关系管理:施耐德与供应商保持密切的沟通和合作,建立互信和合作的关系。
这包括定期会议、沟通渠道的建立、问题解决等。
8.持续改进:施耐德积极推动供应商持续改进自身的质量管理和生产能力。
这可能涉及到共同解决问题、共同寻求优化和创新的机会。
9.风险管理:施耐德识别和管理与供应商相关的各种风险,包括供应风险、质量风险、环境和社会责任风险等。
这可能涉及到风险评估、风险控制和应急准备措施。
10.供应商退出管理:如果供应商无法满足施耐德的要求或出现重大问题,施耐德会采取相应的措施,包括暂停或终止与供应商的合作关系。
总结起来,施耐德的供应商管理流程包括供应商选择和评估、合同签订、供应商绩效评估、供应商培训和协助、供应商审查、品质保证、供应商关系管理、持续改进、风险管理和供应商退出管理等步骤。
这些步骤有助于确保施耐德与供应商之间的合作稳定,并保证产品和服务的质量和可靠性。
福特公司DV--PV培训教材
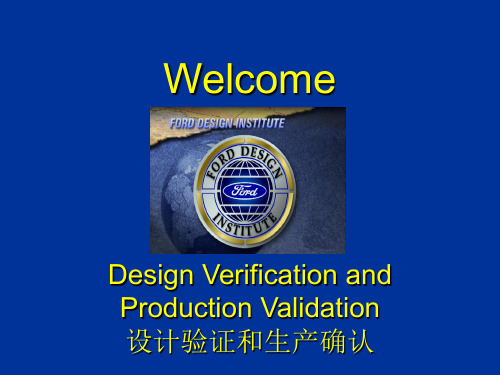
Parameter Design 参数设计
Course Structure 课程结构
• • • • • • • • • • • • • • • • Introduction to DV & PV 对设计验证及生产确认的介绍 Tools for DV & PV 设计验证及生产确认的工具 Vehicle Level DV 整车级别的设计验证 System/Sub-System Level DV 系统/子系统级别的设计验证 Component Level DV 零部件级别的设计验证 System/Sub-System Level PV 系统/子系统级别的生产确认 Component Level PV 零部件级别的生产确认 Summary 总结
I T E R A T I V E P L A N N I N G
Vehicle System
Top Down 由上到下
Sub-System Component
Verification Bottom-up 验证自下至上
• Verification testing is implemented as a bottom-up sequential process. • 验证试验是按照自下至上的顺序过程执行的 • Verification may include a combination of Analytical and physical tests. • 验证可能包括分析试验和物理试验的组合。
Vehicle testing complete: Final Eng Sign Off 整车试验完成:最 终工程签发
DVP Created
生成整车,系统& 子系统的DVP
100个工厂常用英文缩写
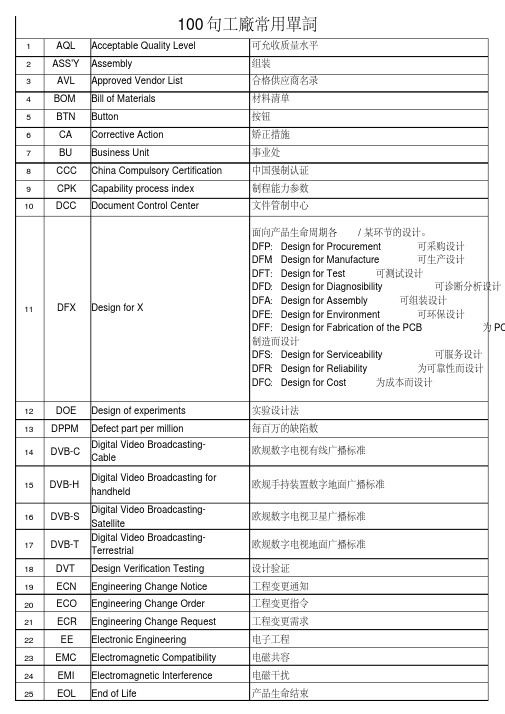
1AQL Acceptable Quality Level可允收质量水平2ASS'Y Assembly组装3AVL Approved Vendor List合格供应商名录4BOM Bill of Materials材料清单5BTN Button按钮6CA Corrective Action矫正措施7BU Business Unit事业处8CCC China Compulsory Certification中国强制认证9CPK Capability process index制程能力参数10DCC Document Control Center文件管制中心11DFX Design for X 面向产品生命周期各/某环节的设计。
DFP:Design for Procurement 可采购设计DFM:Design for Manufacture 可生产设计DFT:Design for Test 可测试设计DFD:Design for Diagnosibility 可诊断分析设计DFA:Design for Assembly 可组装设计DFE:Design for Environment 可环保设计DFF:Design for Fabrication of the PCB 为PC 制造而设计DFS:Design for Serviceability 可服务设计DFR:Design for Reliability 为可靠性而设计DFC:Design for Cost 为成本而设计12DOE Design of experiments实验设计法13DPPM Defect part per million每百万的缺陷数14DVB-C Digital Video Broadcasting-Cable欧规数字电视有线广播标准15DVB-H Digital Video Broadcasting forhandheld欧规手持装置数字地面广播标准16DVB-S Digital Video Broadcasting-Satellite欧规数字电视卫星广播标准17DVB-T Digital Video Broadcasting-Terrestrial欧规数字电视地面广播标准18DVT Design Verification Testing设计验证19ECN Engineering Change Notice工程变更通知20ECO Engineering Change Order工程变更指令21ECR Engineering Change Request工程变更需求22EE Electronic Engineering电子工程23EMC Electromagnetic Compatibility电磁共容24EMI Electromagnetic Interference电磁干扰25EOL End of Life产品生命结束100句工廠常用單詞26ERP Enterprise Resources planing企业资源规划系统27ESD Electro-Static Discharge静电释放(放电)28EU Europe欧洲29FA Failure Analysis失效分析30FAI First Article Inspection首件样品检查31FMEA Failure model effectivenessanalysis失效模式分析32FPC Flexible Printed Circuit可绕性印刷电路板33FQC Finish Quality Control成品质量管理34FR Failure Rate不良率35F/T Function Test功能测试36FYI For Your Information提供您参阅(对平级和下级用)37FYR For Your Reference提供您参考(对平级和上级用)38GND Ground地面39ID Industry Design工业设计40IPQC In-process Quality Control制程质量控制41IQC Incoming Quality Control进料质量控制42ISDB-T Integrated Services DigitalBroadcasting-Terrestrial日规数字电视地面广播标准43ISO International StandardOrganization国际标准化组织44KPI Key Performance Indicator关键绩效指标45KR Korea韩国46MAJ Major主要的47MBO Management by Objective目标管理48MCN Manufacturing Change Notice制造变更通知49MCR Manufacturing ChangeRequest 制程变更需求50ME Mechanical Engineering机构工程51MES Manufacturing ExecutionSystem制造执行系统52MFG Manufacturing制造53MIN Minor轻微的54MIS Management InformationSystem管理信息系统55MO Manufacturing Order工单56MP Mass Production量产57MRB Material Review Board材料审核会议58MRP Material Requirement Plan物料需求计划59NA Not Available无效/不适用60NG No Good不良61NPI New Product Introduction新机种导入62ODM Original Design Manufacturer代设计制造者63OEM Original EquipmentManufacture委托代工64OP Operator作业员65OQA Outgoing Quality Assurance出货品质确认66OQC Outgoing Quality Control成品出货质量管理67ORT On-going Reliability Test持续性可靠度测试68OS Operation System操作系统69PCB Printed CircuitBoard印刷电路板70PCBA Printed CircuitBoard assembly电路板组装71PDCA Plan-Do-Check-Action PDCA管理循环72PE Process Engineering制程工程师73PKG Packing包装74PM Project Management项目管理75PN(P/N)Part Number料号76PO Purchase order订购单77PP Production Plan生产计划78PPM Percent Per Million百万分之一79P/R Pilot Run试产80PV Proces Verification制程验证81QA Quality Assurance质量保证82QC Quality Control质量控制83QE Quality Engineering质量工程84QM Quality Management质量管理85QS Quality System质量系统86RD Research&Development研发87RMA Return Materials Approval退货验收88SFC Shop Floor Control现场控制89SFIS Shop Floor Integrated System 现场信息整合系统90SIP Standard Inspection Procedure标准检验程序91SMD Surface Mount Device表面粘着组件92SMT Surface Mount Technology表面粘着技术93SN Serial Number序号94SOP Standard Operation Procedure标准作业指导95SPC Statistical Process Control统计制程管制96SPK Speaker喇叭/扬声器97SQE Supplier Quality Engineer供应商质量管理98TBD To Be Determined待决定99TE Test Engineering测试工程100WIP Working In Process在制半成品。
DFMA培训材料

面向装配的 设计检查表
塑胶件设计 检查表
0 0 0 1 0 0 1 0 0 0 0 2 0 0 0 3 0 0 0 0 3 0 0 0 3 0
0
钣金件设计 检查表
压铸件设计 检查表
机械加工件 设计检查表
51
DFMA 和 丰田精益产品开发体系
52
丰田的精益研发和DFX的关系
1. 丰田精益产品研发体系:同步开发
为辅助工具提供空间
为重要零部件提供装配止位
宽松的零件公差 要求
1.合理设计零件间隙 2.为关键尺寸缩短尺寸链 3.使用定位特征
避免零件欠约束 1.避免零件欠约束
和过约束
2.避免零件过约束
1.零件仅具有唯一正确的装配位置
设计防错
2.零件的防错特征越明显越好 3.相似零件合并,如不能则夸大零件
的不相似性
DFMA 面向制造和装配的设计
1
什么是: Design Design for Customer
(DFC)
设计 为客户设计
2
苹果的设计 其他设计
3
当你只是其他设计时: DFX
4
DFM DFMA
DFA
面向制造和装配的设计 Design for
Manufacture
Design for Assembly
5. 塑胶件上增加特征代替线束或线夹
b)
26
DFA 面向装配的设计:减少零件的数量
6. 将铰链和卡扣合并在盒体装配的设计:减少零件的数量
7. 去除标签
b)
28
DFA 面向装配的设计:减少紧固件
1. 使用同一种类型的紧固件
b)
29
DFA 面向装配的设计:减少紧固件
DFC(design for cost)面向成本优化的设计
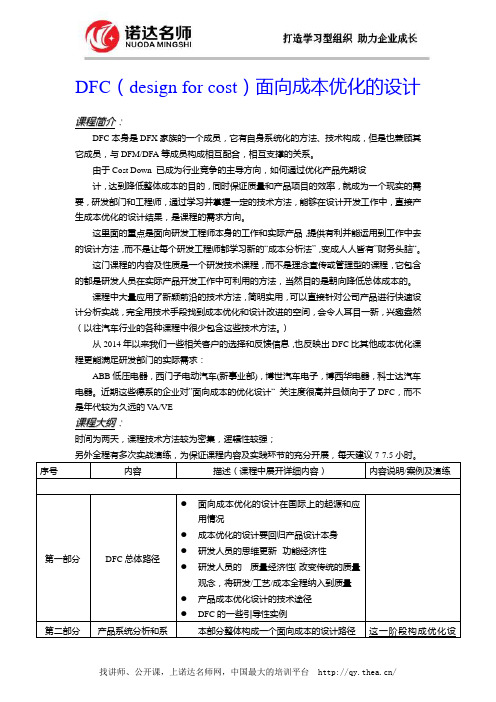
DFC(design for cost)面向成本优化的设计课程简介:DFC本身是DFX家族的一个成员,它有自身系统化的方法、技术构成,但是也兼顾其它成员,与DFM/DFA等成员构成相互配合,相互支撑的关系。
由于Cost Down 已成为行业竞争的主导方向,如何通过优化产品先期设计,达到降低整体成本的目的,同时保证质量和产品项目的效率,就成为一个现实的需要,研发部门和工程师,通过学习并掌握一定的技术方法,能够在设计开发工作中,直接产生成本优化的设计结果,是课程的需求方向。
这里面的重点是面向研发工程师本身的工作和实际产品,提供有利并能运用到工作中去的设计方法,而不是让每个研发工程师都学习新的“成本分析法”,变成人人皆有”财务头脑“。
这门课程的内容及性质是一个研发技术课程,而不是理念宣传或管理型的课程,它包含的都是研发人员在实际产品开发工作中可利用的方法,当然目的是朝向降低总体成本的。
课程中大量应用了新颖前沿的技术方法,简明实用,可以直接针对公司产品进行快速设计分析实战,完全用技术手段找到成本优化和设计改进的空间,会令人耳目一新,兴趣盎然(以往汽车行业的各种课程中很少包含这些技术方法。
)从2014年以来我们一些相关客户的选择和反馈信息,也反映出DFC比其他成本优化课程更能满足研发部门的实际需求:ABB低压电器,西门子电动汽车(新事业部),博世汽车电子,博西华电器,科士达汽车电器。
近期这些德系的企业对”面向成本的优化设计“ 关注度很高并且倾向于了DFC,而不是年代较为久远的V A/VE课程大纲:时间为两天,课程技术方法较为密集,逻辑性较强;另外全程有多次实战演练,为保证课程内容及实践环节的充分开展,每天建议7-7.5小时。
序号内容描述(课程中展开详细内容)内容说明/案例及演练第一部分DFC总体路径●面向成本优化的设计在国际上的起源和应用情况●成本优化的设计要回归产品设计本身●研发人员的思维更新--功能经济性●研发人员的---质量经济性(改变传统的质量观念,将研发/工艺/成本全程纳入到质量●产品成本优化设计的技术途径●DFC的一些引导性实例第二部分产品系统分析和系本部分整体构成一个面向成本的设计路径这一阶段构成优化设(首要重点) 统开发(从功能系统到成本系统)●产品特征分析●功能单元分析●产品结构界面分析与媒体分析●功能界面法●特性分析(关键)--特性输出对潜在成本具有直接的影响●功能成本定义●技术经济性评价计最关键的前期阶段,可以以企业实际产品作为小组设计目标来开展实战作业,老师和学员共同参与第三部分(重点)采用V A/VE的功能成本决策工具●V A/VE内在的分析方法本质—以系统分析为基础●V A/VE倡导的设计优化途径●V A/VE中的专门功能成本分析方法●V A/VE功能整理与策划---FAST图●功能价值决策工具在这里V A/VE是作为一个分析工具模块加以运用的,采用V A/VE中的分析方法,第四部分(重点) 设计阶段的技术风险成本及设计预防措施●技术风险是如何界定的●技术风险的属性和规律●设计风险与产品功能的关系●设计风险与产品特性的关系●特性变异引发潜在功能变异类型与方向●功能变异带来的成本损失●设计风险对产品成本的影响关系这一部分的内容和一般的失效风险分析不同,是基于产品内在技术运行规律的风险分析,这也是设计评审和设计改进的一套方法第二天内容(两天的时间分割在此处可能有一些偏差,因为第四章节的内容开展会受前面部分学员掌握情况的影响第五部分(首要重点)潜在工艺成本分析与优化●结构化的潜在工程成本分析●设计方案的工艺可行性●什么是潜在工艺水平●潜在工艺水平对成本的依赖●设计阶段降低因潜在工艺水平要求高而带来的制造成本●潜在工艺成本与外协件的直接关联●外协件技术/成本策划与先期管控●实际对工艺的包容性本部分内容非常重要,它是为了搭建设计与工艺及制造之间的桥梁,目的是在设计阶段综合考虑整个产品诞生周期的成本,这是企业普遍关心的问题,即设计阶段如何通过优化来降低后续制造成本第六部分(重点)包容性设计方法●包容性设计的含义●包容性设计的目标●包容性设计技术原理(通过设计优化,降低对材料/工艺条件/制造环境的要求这部分实际上是基于前面章节的综合提升,小组要重新或继续通过样本开发任务来实践有关的技术方法来降低潜在制造成本●包容性设计的路径●用系统开发和特性开发方法建立研发项目第七部分面向成本的设计所需要的灵活工具●breakthrough—7工具●层次分析法●TRIZ工具的应用●水平对比法(可对应于选型设计和横向比较)●更多的一些创新工具这部分内容较为灵活,可根据实际产品进行分析,也可根据学员掌握的情况来插入新的模块化的工具方法第八部分内容说明:由于前面各章节都包含了比较密集的技术方法及设计实践,本课程七个主体章节内容已经很丰富因此第八部分是作为总结探讨,以消除研发部门日常工作中遇到的一些障碍,尤其是涉及到与工艺,质量,制造部门✧面向成本的设计与新产品开发项目的结合✧合理看待并处理在项目合作中工艺/制造/质量部门与研发部的合作障碍✧面向成本的设计中“成本”的界定✧站在研发角度正确认识技术成本,工艺成本,制造成本,采购成本和质量成本之间的关系,这也对跨部门合作关系起到融洽的作用。
供应商QRQC培训

供应商质量控制
质量保证体系
要求供应商建立完善的质量保证体系,确保产品符合质量要 求。
质量控制计划
与供应商共同制定质量控制计划,明确质量检验和控制环节 。
供应商绩效评估
绩效评估指标
制定绩效评估指标,如交货准时率、产品合格率、服务响应时间等。
绩效评估实施
定期对供应商进行绩效评估,及时发现和解决潜在问题,促进持续改进。
持续改进与预防措施
介绍持续改进的理念和方法,以及如 何通过数据分析发现潜在问题并采取 预防措施。
案例分析与实战演练
结合实际案例进行深入剖析,并组织 供应商进行实战演练,提高应对问题 和解决问题的能力。
质量管理体系
02
质量管理体系介绍
质量管理体系的概念
质量管理体系是一种系统化的方法, 用于确保产品或服务的质量符合规定 的要求,从而满足客户的需求。
01
02
03
04
制定培训计划
明确培训目标、时间、地点和 参与人员,准备相关培训资料
。
理论教学
讲解质量管理体系、质量控制 方法、检验标准等理论知识。
实际操作演示
现场演示检验设备的操作、检 测方法、数据处理等实际操作
技能。
互动交流
鼓励学员提问,进行讨论和交 流,加深理解和掌握。
案例分析
选择典型案例
挑选具有代表性的供应 商质量问题案例。
训。
培训目标
培养供应商的质量意 识,提高质量管理水 平。
建立长期、稳定的合 作关系,共同提升产 品品质。
确保供应商能够按照 企业的质量要求进行 生产和质量控制。
培训内容
质量管理体系的建立与实施
介绍质量管理体系的基本概念、原理 和实施方法,包括ISO9001等标准。
供应链清单

下级供应商相关信息 供应商 序号 供应商名称 代码 供应商供货 供应商供货产品 产品重要度 下级供应商 名称 联系人 联系电话
说明:填写要求:供应商必须对下级供应商供货产品的重要度和风险度系统识别,对重要度和风险度高的下级供应商(包括D 、安保件、功能/性能件、表面处理外委工序等)必须按下表方式报DFCV供应商质量保证部备案。 供应商确认签字 编制: 审核: 批准: DFCV审核签字/日期
Hale Waihona Puke 下级供应商相关信息 供货产品 供货产品重 下级供应商 下级供应商变 要度 层级 更履历 备注
要度和风险度高的下级供应商(包括DFC明确要求及供应商自主识别的重要材料 部备案。
DFCV审核签字/日期
供应商管理心得体会
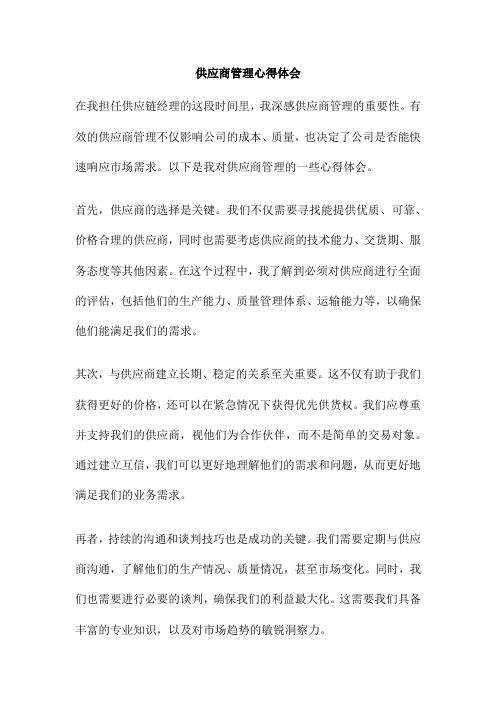
供应商管理心得体会在我担任供应链经理的这段时间里,我深感供应商管理的重要性。
有效的供应商管理不仅影响公司的成本、质量,也决定了公司是否能快速响应市场需求。
以下是我对供应商管理的一些心得体会。
首先,供应商的选择是关键。
我们不仅需要寻找能提供优质、可靠、价格合理的供应商,同时也需要考虑供应商的技术能力、交货期、服务态度等其他因素。
在这个过程中,我了解到必须对供应商进行全面的评估,包括他们的生产能力、质量管理体系、运输能力等,以确保他们能满足我们的需求。
其次,与供应商建立长期、稳定的关系至关重要。
这不仅有助于我们获得更好的价格,还可以在紧急情况下获得优先供货权。
我们应尊重并支持我们的供应商,视他们为合作伙伴,而不是简单的交易对象。
通过建立互信,我们可以更好地理解他们的需求和问题,从而更好地满足我们的业务需求。
再者,持续的沟通和谈判技巧也是成功的关键。
我们需要定期与供应商沟通,了解他们的生产情况、质量情况,甚至市场变化。
同时,我们也需要进行必要的谈判,确保我们的利益最大化。
这需要我们具备丰富的专业知识,以及对市场趋势的敏锐洞察力。
最后,我认为供应商管理需要引入更多的技术手段。
比如,使用数据分析工具可以帮助我们更好地理解供应商的生产效率、质量情况等;使用电子化平台可以简化采购流程,提高效率。
总的来说,供应商管理是一个复杂而重要的工作。
它需要我们具备专业知识、敏锐的市场洞察力,以及良好的人际关系处理能力。
我相信,只要我们用心去做,我们就一定能够做好这个工作。
随着全球化的深入发展,供应链的复杂性和多样性日益凸显。
在这个背景下,供应商质量管理的重要性愈发突出。
有效的供应商质量管理有助于提高供应链的稳定性、可靠性和效率,进而提升企业的整体竞争力。
本文将分析供应商质量管理现状,提出解决方案,并探讨实施措施及效果。
当前,许多企业在供应商质量管理方面存在一些问题。
供应商选择标准不清晰,导致潜在供应商的质量水平参差不齐。
- 1、下载文档前请自行甄别文档内容的完整性,平台不提供额外的编辑、内容补充、找答案等附加服务。
- 2、"仅部分预览"的文档,不可在线预览部分如存在完整性等问题,可反馈申请退款(可完整预览的文档不适用该条件!)。
- 3、如文档侵犯您的权益,请联系客服反馈,我们会尽快为您处理(人工客服工作时间:9:00-18:30)。
优化零件的尺寸、工艺参数,降低零件的制造加工成本
创新运用 替代
轻量化
优化参数 简化 提高效率
简化复杂零部件结构,改善零部件的制造和装配性能, 降低加工成本和装配成本
外部调整
起始点 •政府监管 •普及 •创 化 新
各层级具体调整
•技术 •复杂 •模块 •设 •DFC 规格 性 战略 计 •功 能成 本
总计
A.第一轮调整方案 : 1.政府监管 (如排 放标准)
B.
第二轮调整方案:
2. 3. 4. 5. 6. 7. 8. 9.
普及化 创新和技术 简化技术规格 复杂性/内容管理 模块战略 DFC/按成本设 计 设计竞赛 优化系统功能
安全气囊、侧气帘、安全带、座椅骨架与CD101通用,共同降低成本230元; 例 EPS与E301通用,共同降低成本90元; 前后减震器、液压助力转向系统采用其他车型产品,大幅度减少了开发费和模具 费。
5
限价开发, 充分发挥 优秀供应 商的专业 知识和开 发 能力,早期 优化设计 , 达到成本可 控。
施乐公司,DFC技术已 与市场同步管理体 系整合,用以降低产品的生 命周期成本,最大 限度地满足客户的需求。 休斯飞机公司从1970~1978年里, 推行 DFC的效益是10亿美元。
CV6项目,从2006年 到2007年,单车降 低9000元。
5
降低技术成本的手段(麦肯锡)
1 2 3 4 5 6 7 8 9
参观
请供应商到公司DFC工作间学习,讲解如何开展DFC 工作。 (到目前为止,共计有10批82人次到公司 学习。)
培训
选择部分本地供应商,组织供应商集中学习DFC理论 。
推广
向供应商延伸,指导供应商开展DFC价值工程分析, 实现配套件成本的降低。
结束语
DFC的实施,需要各位供应商朋友的大力支持! DFC不仅能帮助主机厂降低整车成本,也能帮助各 位供应商朋友降低零部件生产成本!
二、案例
(一) 采用HPS液压助力转向系统替换原EPS电子助力转向系统(CV6)
再进一步分析 论证,认为HPS液压助力转向系 统的技术已经相当 成 熟,在性能上完全可以替换 EPS,对于CV6这样 的经济型轿车,完 全没有 必要采用很先进且昂贵的技 术,并且采用 HPS液压助力转向系 统的价格 仅为1178元/套。采用该方案后 ,成本可以降低:
不降低产品性能和 质量
DFC
产品研发人员建立 起成本的概念
... 延伸到供应商
... 提高技术人员的创 新思维能力
9
第二部分 DFC应用
DFC的基本思想和原则
与供应商 共同发展的原则
价值最大化原则
有限功能原理 用户第一的原则
DFC
跟踪新技术原则
信息全面原则 并行工程的工作方法 节省每一分钱的原则
坚持以“基于市场,基于标杆,基 于竞争对手”为导向,以“①、 关注用户感 知,追求性价比 ②、 细化开发目标突出亮点、卖点 ③ 、彻底解决TOP10问题 ,提升可靠性”为基础,形成C201目标成本管理 体系和机制。实现质量和成本的平衡, 打造经典产品的 目标。
……… 4
总成、零部件尽可能通用化,减少新开发,降低开发费和模具费。
制定合理工艺方案,改进生产工艺,充分考虑高效率加 工产品手段的运用,使产品功能和制造能力实现统一
第三部分 DFC应用案例
二、案例
(一)采 用HPS液压助力转向系 统替换原EPS电子 助力转向系统(CV6) 1、创新方案 采用HPS液压助力转向系 统替换原EPS电 子助力转向系统
2、创新类型 设计方案替换 3、分析论证
DFC(Design For Cost)
——“面向成本的设计”
采 购 部 生 产 寻 源 处
二○一一年四月
前
言
以最低成本,在最短时间内生产出高质量的产品已成为制造 企业竞争的焦点。研发过程决定了产品成本的 75%-80%,成本控制 的源头在设计前端。公司组织力量对CV6价值创新的具体做法进行 归纳总结,提炼出了一套价值创新理论和方法,在公司内部被命 名为“汽车产品面向成本的设计”(Design For Cost:DFC), 并形成一套标准化的价值创新资料 《长安汽车DFC简明设计手册》。
•包括供货商 研 讨会
6
DFC
Design For Cost 面向成本的设计
设计
成本 要素
优化 设计
控制 产品 成本
面向成本的设计(DFC)是指在满足用户 需求的前提下,尽可能地降 低成本,并通过 分析和研究产品全生命周期 的多种成本因素 ,对原设计中影响产品成本 的过高费用部分 进行修改,最终达到降低成 本的目的。
目
第一部分
第二部分
录
DFC 简 介
DFC 应 用
第三部分
DFC 应 用 案 例
第一部分 DFC简 介
DFC 成功案例
通用汽车公司从1960年开始采用DFC并持 续到现在,每年为公司节省 上千万美元。
杜邦在300个 项目上应用DFC,用 以改进 和创新化工生具采用限价开发的方式,与优秀供应商一起在早期进行技术方案优化,在大幅
度提升零部件质量的前提下,使成本可控。
6
例
对已掌控的核心 技术,扶 持低成本 供应商风 险开发, 降 低成本。
全车座椅开发技术长安已掌控,通过对低成本供应商的管理与指导,选用低成本 供应商风险开发,降低成本。
………
DFC推广计划
希望DFC的应用,能让我们达成“降本 共赢”!
谢 谢 大 家!
DFC推进的五阶段法
1 2 3 4 5
业务培训
收集数据
产生方案
方案验证
实施与总 结
总顾问
总顾问 DFC团队
DFC团队
DFC团队
总顾问
DFC团队
结合创新技法 价值增值分析 性能和质量分 总监签字确认 用新方案替换
DFC理念和应 零部件分析
用技术
创新技法:检
零件相关数据
(二)C201成本控制总体思路---------坚持“顾客至上”的理念
关注用户感知 追求性价比
多次开展市场调研, 深入挖掘产品的亮点、 卖点。 动态监控竞争对手成 本变化
细化开发目标 突出卖点亮点
设计任务书 性能目标书 质量目标书 可靠性目标书 工艺目标书
彻底解决TOP10 问题提升可靠性
异响 雨刮系统 前后减振器 全车门锁 玻璃升降器 灯具起雾 ……
建立目标成本管 理体系和机制
全面导入DFC设计理念 将开发目标作为制定系统、 零部件成本的基础 将成本分解,分解到不能 再分解 强化与供应商谈价机制 强化设变管理
深入与竞品全方位对 标 成本向用户关注的部 位倾斜
DFC 特 性
适用性
预防性
系统性
可操作性
主要适用于新品 开发,特别适用 于自主品牌、自 主开发项目。
预防性控制:在 产品尚未交付生 产之前的成本控 制。
涉及到产品设计 、制造、采购、 销售、使用的方 方面面,具有多 因素性
有一套具有高度 可操作性的方法
协商降低成本
减少不必要的功能 和性能,避免冗余 功能
-1122元/套
4、案例启示
对于采用设计 方案替换降低成本 ,本案例非常典型 。设计方案替 换的前提是功能和性能的对 等性,另外,方案 替换还不能对用户 造成 不良影响。对于助力转向系 统这类消费者既不 关心的内在技术特 性, 且替换又不影响其原有使用 感受,同时可以带 来大量降低单车成 本的 方案,不仅可以在现有车型 改进时采用,同时 更应该在新车开发 中大 胆应用
收集和分析
逐条应用检核 表
提出多个替换
析
老方案
成本效益分析
增加到案例库
核表、5W2H、 头脑风暴法
方案
12
DFC团队
用户 财务 服务
设计
DFC团队
供应 商
供应商拥 有配 套件实际 生产 经验,可 以从 工艺角度 对实 际提出建 设性 建议。
销售 工艺
制造
DFC如何降低成本? 核心是采用各种技术减少一切冗余 !
只要功能相同 且性能没有改变, 在产品设计中应该 使用成本更低的方 案。 CV6原来采用 EPS电子助力转 向系统,最早由韩 国万都独家供货 ,价格约2300元/ 套,价格难于降低。后引进荆 州恒隆和重庆长融 公司进行风险开发 和国产化,采 用EPS电子助力转向系统 ,但成本可以降低 :
-500元/套