D热弯磁控真空溅射镀膜玻璃
VD磁控溅射镀膜生产工艺流程

VD磁控溅射镀膜生产工艺流程1.原材料准备:首先需要准备镀膜的原材料,一般包括金属靶材和镀膜基板。
根据具体的镀膜要求,可以选择不同的金属靶材,如铝、铜、银等。
镀膜基板也有不同的选择,常用的有玻璃、硅片、陶瓷等。
2.靶材装载:将选定的金属靶材安装到磁控溅射设备的靶材架上,并进行固定。
在安装过程中要注意保证靶材表面的平整度和与架子之间的良好接触,以确保均匀、稳定的靶材磨损和喷射。
3.真空抽气:在进行溅射之前,需要将磁控溅射设备的腔体抽至真空状态,通常要求达到10^-4Pa以下的高真空。
这是为了防止氧气、水分等杂质对镀膜质量的影响,保证镀膜过程的稳定性和可靠性。
4.靶材预处理:在抽气结束后,需要对靶材进行预处理。
通常情况下,靶材表面会有氧化、污染等问题,需要通过火烧、腐蚀等方法将其清洗和处理干净,以保证镀膜的质量。
5.溅射镀膜:在抽气和靶材预处理完毕后,进入溅射镀膜的实际操作环节。
首先打开镀膜基板的夹持装置,将其固定到旋转的夹持盘上。
然后通过控制磁场和电子束在真空环境中,让金属靶材表面的金属原子释放并与基板反应,形成一层金属薄膜。
通过调整溅射时间、功率、距离等参数,可以控制薄膜的厚度、均匀性和组成等性质。
6.膜层性能测试与调整:镀膜完成后,需要对膜层进行测试和表征。
常见的测试方法包括厚度测量、成分分析、表面形貌观察等。
通过这些测试结果,可以评估镀膜的质量,并根据需要调整和优化镀膜工艺参数。
7.膜层保护和后处理:在测试完成后,对镀膜进行保护和后处理。
常见的保护方法包括沉积保护膜、涂层保护剂等,以减少镀膜受环境和使用条件影响的机会。
同时,根据具体需要可以对膜层进行退火、热处理等操作,以提高膜层的力学、光学等性能。
8.检查和包装:最后,对镀膜进行检查和包装。
主要包括对膜层的外观和性能进行检查,如膜层的透光性、透射电镜性能等。
同时,根据客户需求进行产品的包装,以确保产品在运输和使用过程中的完整性和稳定性。
总之,VD磁控溅射镀膜工艺流程涉及到原材料准备、靶材装载、真空抽气、靶材预处理、溅射镀膜、膜层性能测试与调整、膜层保护和后处理,以及检查和包装等环节。
磁控真空溅射镀膜
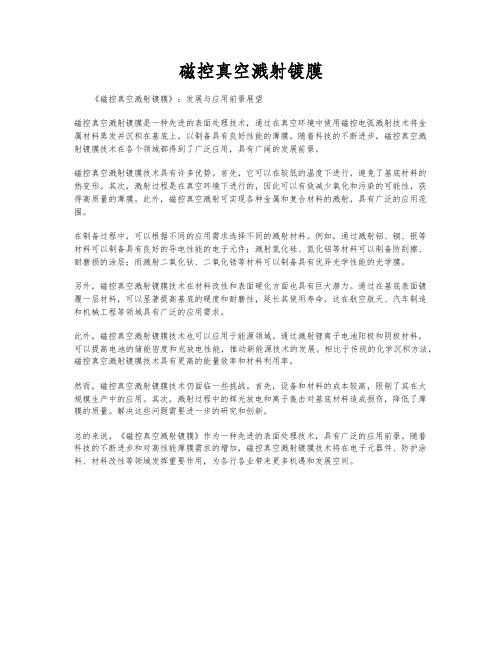
磁控真空溅射镀膜《磁控真空溅射镀膜》:发展与应用前景展望磁控真空溅射镀膜是一种先进的表面处理技术,通过在真空环境中使用磁控电弧溅射技术将金属材料蒸发并沉积在基底上,以制备具有良好性能的薄膜。
随着科技的不断进步,磁控真空溅射镀膜技术在各个领域都得到了广泛应用,具有广阔的发展前景。
磁控真空溅射镀膜技术具有许多优势。
首先,它可以在较低的温度下进行,避免了基底材料的热变形。
其次,溅射过程是在真空环境下进行的,因此可以有效减少氧化和污染的可能性,获得高质量的薄膜。
此外,磁控真空溅射可实现各种金属和复合材料的溅射,具有广泛的应用范围。
在制备过程中,可以根据不同的应用需求选择不同的溅射材料。
例如,通过溅射铝、铜、银等材料可以制备具有良好的导电性能的电子元件;溅射氮化硅、氮化铝等材料可以制备防刮擦、耐磨损的涂层;而溅射二氧化钛、二氧化锆等材料可以制备具有优异光学性能的光学膜。
另外,磁控真空溅射镀膜技术在材料改性和表面硬化方面也具有巨大潜力。
通过在基底表面镀覆一层材料,可以显著提高基底的硬度和耐磨性,延长其使用寿命。
这在航空航天、汽车制造和机械工程等领域具有广泛的应用需求。
此外,磁控真空溅射镀膜技术也可以应用于能源领域。
通过溅射锂离子电池阳极和阴极材料,可以提高电池的储能密度和充放电性能,推动新能源技术的发展。
相比于传统的化学沉积方法,磁控真空溅射镀膜技术具有更高的能量效率和材料利用率。
然而,磁控真空溅射镀膜技术仍面临一些挑战。
首先,设备和材料的成本较高,限制了其在大规模生产中的应用。
其次,溅射过程中的辉光放电和离子轰击对基底材料造成损伤,降低了薄膜的质量。
解决这些问题需要进一步的研究和创新。
总的来说,《磁控真空溅射镀膜》作为一种先进的表面处理技术,具有广泛的应用前景。
随着科技的不断进步和对高性能薄膜需求的增加,磁控真空溅射镀膜技术将在电子元器件、防护涂料、材料改性等领域发挥重要作用,为各行各业带来更多机遇和发展空间。
磁控溅射法原理
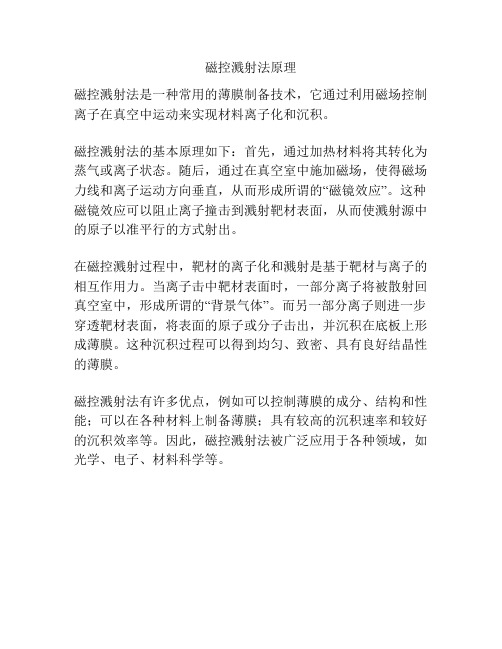
磁控溅射法原理
磁控溅射法是一种常用的薄膜制备技术,它通过利用磁场控制离子在真空中运动来实现材料离子化和沉积。
磁控溅射法的基本原理如下:首先,通过加热材料将其转化为蒸气或离子状态。
随后,通过在真空室中施加磁场,使得磁场力线和离子运动方向垂直,从而形成所谓的“磁镜效应”。
这种磁镜效应可以阻止离子撞击到溅射靶材表面,从而使溅射源中的原子以准平行的方式射出。
在磁控溅射过程中,靶材的离子化和溅射是基于靶材与离子的相互作用力。
当离子击中靶材表面时,一部分离子将被散射回真空室中,形成所谓的“背景气体”。
而另一部分离子则进一步穿透靶材表面,将表面的原子或分子击出,并沉积在底板上形成薄膜。
这种沉积过程可以得到均匀、致密、具有良好结晶性的薄膜。
磁控溅射法有许多优点,例如可以控制薄膜的成分、结构和性能;可以在各种材料上制备薄膜;具有较高的沉积速率和较好的沉积效率等。
因此,磁控溅射法被广泛应用于各种领域,如光学、电子、材料科学等。
光伏真空磁控溅射镀膜原理
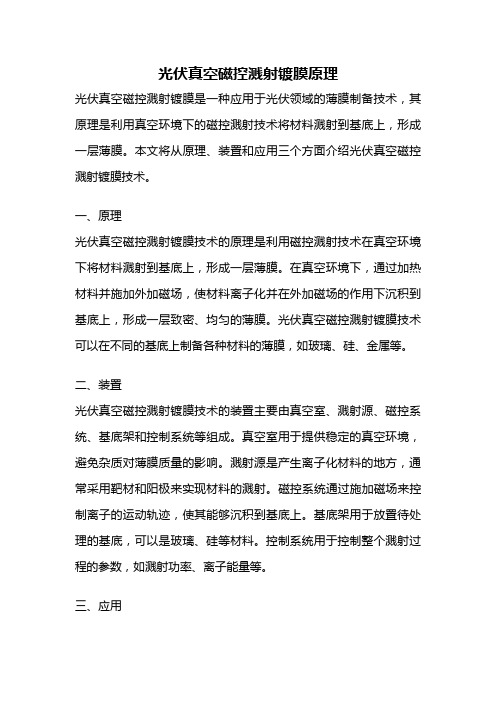
光伏真空磁控溅射镀膜原理光伏真空磁控溅射镀膜是一种应用于光伏领域的薄膜制备技术,其原理是利用真空环境下的磁控溅射技术将材料溅射到基底上,形成一层薄膜。
本文将从原理、装置和应用三个方面介绍光伏真空磁控溅射镀膜技术。
一、原理光伏真空磁控溅射镀膜技术的原理是利用磁控溅射技术在真空环境下将材料溅射到基底上,形成一层薄膜。
在真空环境下,通过加热材料并施加外加磁场,使材料离子化并在外加磁场的作用下沉积到基底上,形成一层致密、均匀的薄膜。
光伏真空磁控溅射镀膜技术可以在不同的基底上制备各种材料的薄膜,如玻璃、硅、金属等。
二、装置光伏真空磁控溅射镀膜技术的装置主要由真空室、溅射源、磁控系统、基底架和控制系统等组成。
真空室用于提供稳定的真空环境,避免杂质对薄膜质量的影响。
溅射源是产生离子化材料的地方,通常采用靶材和阳极来实现材料的溅射。
磁控系统通过施加磁场来控制离子的运动轨迹,使其能够沉积到基底上。
基底架用于放置待处理的基底,可以是玻璃、硅等材料。
控制系统用于控制整个溅射过程的参数,如溅射功率、离子能量等。
三、应用光伏真空磁控溅射镀膜技术在光伏领域有广泛的应用。
首先,它可以用于制备太阳能电池的薄膜层。
太阳能电池的薄膜层是光电转换的关键部分,通过光伏真空磁控溅射镀膜技术可以制备高效的薄膜层,提高太阳能电池的转换效率。
其次,光伏真空磁控溅射镀膜技术还可以用于制备光伏材料的防反射膜。
光伏材料的防反射膜可以提高光的吸收效率,从而提高光伏设备的能量转换效率。
此外,光伏真空磁控溅射镀膜技术还可以用于制备光伏材料的光学薄膜。
光学薄膜可以改变光的传播特性,实现光的分光、反射、透射等功能,用于光伏设备的光学器件。
总结起来,光伏真空磁控溅射镀膜技术是一种应用于光伏领域的薄膜制备技术,通过在真空环境下利用磁控溅射技术将材料溅射到基底上,形成一层致密、均匀的薄膜。
该技术具有制备高效太阳能电池薄膜层、防反射膜和光学薄膜的优点,在光伏领域有着广泛的应用前景。
真空磁控溅射镀膜原理与技术

真空磁控溅射镀膜原理与技术真空磁控溅射镀膜是一种常用的薄膜制备技术,通过在真空环境中使用磁控溅射装置,将固体靶材溅射成气相离子,然后沉积在基材上,形成一层均匀、致密的薄膜。
这种技术广泛应用于光学薄膜、电子器件、节能涂层等领域。
真空磁控溅射镀膜的原理是利用磁场和靶材上集中的高能离子束,将靶材表面的原子或分子溅射出来,然后沉积在基材上形成薄膜。
具体来说,真空磁控溅射装置包括真空室、靶材、基材和磁控装置。
在真空室中,通过抽气将压力降至10^-3到10^-6帕的真空状态。
当真空室内的气体被抽尽后,向离子源上的靶材施加直流或者交流电,产生高能离子束,击打在靶材上。
同时,在靶材表面施加交变磁场。
这样,气体原子和分子会受到束流的冲击,将离子溅射出来,并通过基材的倾角冲积在基材表面形成薄膜。
磁控装置主要通过磁场对离子进行引导,使得离子束在靶材和基材之间来回移动,进一步增强溅射效果。
真空磁控溅射镀膜技术有以下几个特点:首先,可以在较低的温度下进行薄膜沉积,适用于大多数材料。
其次,由于采用磁场控制,可以获得均匀、致密的薄膜。
再次,能够利用常规的靶材材料,如金属、合金、化合物材料等。
最后,真空磁控溅射镀膜还可通过调整离子束能量和沉积速度来控制薄膜的性质,如厚度、硬度、附着力等。
除了基本的真空磁控溅射镀膜技术,还有一些衍生的技术,如磁控溅射复合镀膜、磁控溅射多层膜、磁控溅射纳米结构膜等。
这些技术在一些特定应用中具有更好的性能,并能满足特定的需求。
总之,真空磁控溅射镀膜技术是一种重要的薄膜制备技术,具有广泛的应用前景。
通过控制离子束能量、磁场强度和沉积条件等参数,可以制备出具有多种特性的薄膜,满足不同领域的需求。
但是,该技术也存在一些问题,如工艺复杂、设备要求高等,需要进一步研究和改进。
《磁控溅射镀膜技术》课件

要点二
溅射参数与工艺条件
溅射参数和工艺条件对磁控溅射镀膜的沉积速率、膜层质 量、附着力等有着重要影响。主要的溅射参数包括工作气 压、磁场强度、功率密度等,工艺条件包括基材温度、气 体流量和组成等。通过对这些参数的优化和控制,可以获 得具有优异性能的膜层。
磁控溅射镀膜设备
03
与系统
磁控溅射镀膜设备的组成
多元靶材磁控溅射
技术
研究多种材料同时溅射的工艺技 术,实现多元材料的复合镀膜, 拓展镀膜材料的应用范围。
磁控溅射与其他技术的结合应用
磁控溅射与脉冲激光沉积技术结合
01
通过结合两种技术,实现快速、大面积的镀膜,提高生产效率
。
磁控溅射与化学气相沉积技术结合
02
利用化学气相沉积技术在磁控溅射的基础上进一步优化镀膜性
磁控溅射机制
在磁场的作用下,电子的运动轨迹发生偏转,增加与气体分子的碰撞概率,产 生更多的离子和活性粒子,从而提高了溅射效率和沉积速率。
磁控溅射镀膜的工艺流程
要点一
工艺流程概述
磁控溅射镀膜的工艺流程包括前处理、溅射镀膜和后处理 三个阶段。前处理主要是对基材进行清洗和预处理,确保 基材表面的清洁度和粗糙度符合要求;溅射镀膜是整个工 艺的核心部分,通过控制溅射参数和工艺条件,实现膜层 的均匀、致密和附着力强的沉积;后处理主要包括对膜层 的退火、冷却和清洗等处理,以优化膜层性能。
纳米薄膜的制备与应用
总结词
纳米薄膜因其独特的物理和化学性质在许多 领域具有巨大的应用潜力。
详细描述
磁控溅射技术可以用于制备纳米级别的薄膜 ,如纳米复合材料、纳米陶瓷、纳米金属等 ,这些薄膜在催化剂、传感器、电池等领域 有广泛应用。
其他领域的应用研究
磁控溅射镀膜的简介及其实际操作
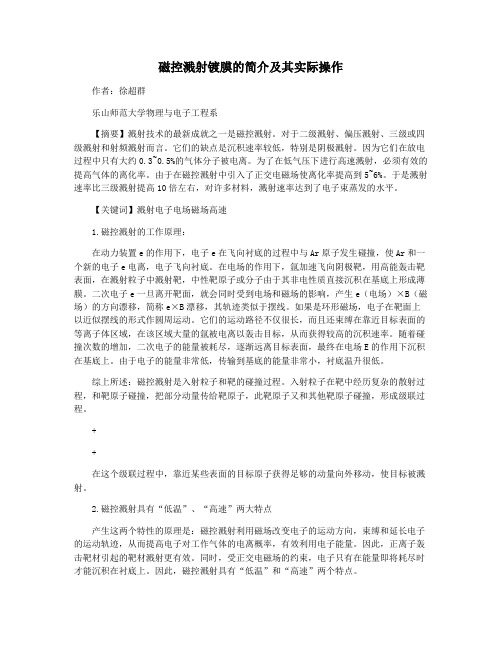
磁控溅射镀膜的简介及其实际操作作者:徐超群乐山师范大学物理与电子工程系【摘要】溅射技术的最新成就之一是磁控溅射。
对于二级溅射、偏压溅射、三级或四级溅射和射频溅射而言。
它们的缺点是沉积速率较低,特别是阴极溅射。
因为它们在放电过程中只有大约0.3~0.5%的气体分子被电离。
为了在低气压下进行高速溅射,必须有效的提高气体的离化率。
由于在磁控溅射中引入了正交电磁场使离化率提高到5~6%。
于是溅射速率比三级溅射提高10倍左右,对许多材料,溅射速率达到了电子束蒸发的水平。
【关键词】溅射电子电场磁场高速1.磁控溅射的工作原理:在动力装置e的作用下,电子e在飞向衬底的过程中与Ar原子发生碰撞,使Ar和一个新的电子e电离,电子飞向衬底。
在电场的作用下,氩加速飞向阴极靶,用高能轰击靶表面,在溅射粒子中溅射靶,中性靶原子或分子由于其非电性质直接沉积在基底上形成薄膜。
二次电子e一旦离开靶面,就会同时受到电场和磁场的影响,产生e(电场)×B(磁场)的方向漂移,简称e×B漂移,其轨迹类似于摆线。
如果是环形磁场,电子在靶面上以近似摆线的形式作圆周运动。
它们的运动路径不仅很长,而且还束缚在靠近目标表面的等离子体区域,在该区域大量的氩被电离以轰击目标,从而获得较高的沉积速率。
随着碰撞次数的增加,二次电子的能量被耗尽,逐渐远离目标表面,最终在电场E的作用下沉积在基底上。
由于电子的能量非常低,传输到基底的能量非常小,衬底温升很低。
综上所述:磁控溅射是入射粒子和靶的碰撞过程。
入射粒子在靶中经历复杂的散射过程,和靶原子碰撞,把部分动量传给靶原子,此靶原子又和其他靶原子碰撞,形成级联过程。
++在这个级联过程中,靠近某些表面的目标原子获得足够的动量向外移动,使目标被溅射。
2.磁控溅射具有“低温”、“高速”两大特点产生这两个特性的原理是:磁控溅射利用磁场改变电子的运动方向,束缚和延长电子的运动轨迹,从而提高电子对工作气体的电离概率,有效利用电子能量。
真空磁控溅射镀膜原理与技术

真空磁控溅射镀膜原理与技术
真空磁控溅射镀膜技术是一种高效、环保、高质量的表面处理技术,广泛应用于电子、光学、航空航天、汽车、建筑等领域。
其原理是利用高能离子轰击靶材表面,使靶材原子脱离并沉积在基材表面形成薄膜。
真空磁控溅射镀膜技术的核心是磁控溅射装置。
该装置由真空室、靶材、基材、磁控电源、离子源等组成。
在真空室中,通过抽气将压力降至10^-4Pa以下,然后加入惰性气体(如氩气),使气体分子与靶材表面原子碰撞,产生高能离子。
磁控电源产生磁场,将离子束聚焦在靶材表面,使靶材原子脱离并沉积在基材表面形成薄膜。
真空磁控溅射镀膜技术具有以下优点:
1. 镀膜质量高:由于真空环境下,薄膜表面无气体和杂质污染,因此薄膜质量高,具有良好的光学、电学、机械性能。
2. 镀膜厚度均匀:磁控电源产生的磁场可以使离子束均匀聚焦在靶材表面,使得薄膜厚度均匀。
3. 镀膜速度快:由于离子束能量高,靶材原子脱离速度快,因此镀膜速度快。
4. 环保节能:真空磁控溅射镀膜技术无需使用有机溶剂和化学药品,不会产生废气、废水和废渣,符合环保要求。
真空磁控溅射镀膜技术的应用非常广泛。
在电子领域,可以用于制造集成电路、显示器、太阳能电池等;在光学领域,可以用于制造反射镜、滤光片、透镜等;在航空航天领域,可以用于制造航空发动机叶片、航天器表面涂层等;在汽车领域,可以用于制造汽车玻璃、车身涂层等;在建筑领域,可以用于制造建筑玻璃、金属门窗等。
真空磁控溅射镀膜技术是一种高效、环保、高质量的表面处理技术,具有广泛的应用前景。
- 1、下载文档前请自行甄别文档内容的完整性,平台不提供额外的编辑、内容补充、找答案等附加服务。
- 2、"仅部分预览"的文档,不可在线预览部分如存在完整性等问题,可反馈申请退款(可完整预览的文档不适用该条件!)。
- 3、如文档侵犯您的权益,请联系客服反馈,我们会尽快为您处理(人工客服工作时间:9:00-18:30)。
热弯磁控真空溅射镀膜玻璃随着我国建筑业的蓬勃发展,建筑物外墙墙体也日新月异,由砖墙发展到轻体的幕墙,又由有框铝合金玻璃幕墙,隐框玻璃幕墙,发展到铝板幕墙、陶瓷板、石材、单元式幕墙,国外已发展到铝合金隔热保温多功能玻璃幕墙。
不论什么形式幕墙和各种类型的窗都离不开玻璃,由于镀膜玻璃具备有优良的性能和诱人的镜面效果,特别引起设计师及用户极大的青睐。
用于外墙透光部份的镀膜玻璃,目前以磁控真空溅射法生产的镀膜玻璃为最佳,用在建筑墙体上,镀膜玻璃给人们有一种高雅富贵的感觉。
真空溅射镀膜玻璃,不仅外观美观,同时又是一种新型的节能的建筑材料,因此使用镀膜玻璃被视为控制建筑物热量流失及降低成本的关键要素,能节约大量能源消耗,对于高楼大厦使用空调机能节约大量的耗电量,节能率30-50%左右。
镀膜牢固度及各种物理性能均较其它方法生产的镀膜玻璃为佳,尤其是用在隐框玻璃幕墙上,结构胶直接粘在玻璃的镀膜上,因此镀膜的牢固度更显得重要。
幕墙的设计师们除了横平竖直的幕墙效果外,绝大部份幕墙设计向多曲面,多层次复杂的立体效果方向发展,从幕墙的造形和颜色(包括玻璃颜色)要与建筑物用途相匹配。
如文化儿童娱乐建筑用鲜艳的颜色,政府机关(法院)只能用严肃的深颜色,因此对镀膜玻璃不仅在颜色上有要求,更重要的是对镀膜玻璃各种半径弯曲的弧面要求。
要得到镀膜玻璃的各种弯曲弧度,需在高温高压下热弯成形,这对镀膜玻璃要求很高。
有不少建筑物为了简化玻璃弧面,采用多片平直玻璃折线安装使之最大限度的近似弧面,这种玻璃折线做法永远只能是按近弧面形状,外观形状无法和热弯成形镀膜玻璃准确的弧形相比美。
因此镀膜玻璃的弯弧问题如何解决,尤其是离线镀膜玻璃弯弧问题,往往成为幕墙界难以解决的问题。
一、弯弧镀膜玻璃目前主要有下列几种处理方案:
1.采用与常规平面磁控溅射同样类型的镀膜玻璃
这种方案应该是最为理想的选择方案。
这样可以在颜色和透过率反射率等方面随心所欲的作任何平、弯组合选择。
目前平面使用的镀膜玻璃通常是选用在镀膜中综合性能最为优秀、工艺最先进、色彩与透光率十分丰富的磁控溅射镀膜玻璃。
其中采用引进设备和技术生产的产品在国内市场已占主导地位。
但是由于国内外通常使用的阳光反射膜磁控溅射镀膜玻璃,-般不可经受玻璃烘弯的温度及工艺气氛条件,因此只能采用其它一些补救方案。
要想取得与平面磁控膜玻璃同色彩及透光率的弯弧玻璃,唯有在玻璃弯制后,用同样的磁控溅射工艺镀制。
但是由于目前适用于平面条件的磁控溅射工艺技术设备包括进口设备,无法适用于各种玻璃弯弧状态下镀制使用。
而适用于弯弧条件下的磁控溅射镀膜设备,国内没有,国外也十分稀少,加上这些数量极少的设备,因工艺技术、设备技术、成本、价格等诸多因素的限制,也只能单块、单炉的制作,使其成本十分昂贵。
目前在国外的弯弧磁控溅射玻璃几乎达到每平方米四百到五百美元的水平。
使绝大部份潜在用户望而却步,无力选用。
2.采用在线镀膜玻璃
这是目前国内解决弯弧镀膜玻璃较多采用的产品。
在线镀膜由于成膜原理大部分由CVD法化学气相沉积,或粉沫喷雾在热基片上反应成膜,往往存在这样一些情况。
1)存在光化学长期耐久稳定性问题。
在较长时间日光、紫外线照射和照射程度不同(建筑物遮档)会不同程度引起残余光化学反应,引起一定程度的变色及色彩差异。
2)膜厚度控制精度不可能很高。
在严格意义上而言,不能确保所出同种产品长时间间隔产品供货的一致性,不同批次的产品会有差异。
特别是对于一些热弯与平面连贯一体的工程,要求有一定程度配色,则色差问题会程度不同的出现困难。
3)同一批次产品也有一定程度的差异。
用磁控溅射膜工艺中色差测定的方法,即由电脑色度检测系统配合国际照明委员会CIE(1976)色度坐标的L*、a*、b*值的△E来判定。
磁控溅射工艺一般△E <2是不成问题的,而在线膜产品的△E<2则比较困难,即会程度不同的存在色差问题.
3.我国首创磁控溅射可热弯镀膜玻璃
磁控溅射可热弯膜工艺,实际上是采用常规的美国AIRCO公司磁控溅射设备技术所通常使用的物理方法,在玻璃面形成反射膜层,同时其膜层在大气热弯高温条件下能保持化学稳定性。
并且工艺参数电脑储存,可确保同一系列同色产品长期供货的色差一致性。
该工艺已由苏州华东镀膜玻璃有限公司研制成功,并已批量使用于工程项目,其膜层的化学物理性能的稳定性,颜色的一致性明显优于在线膜,弯制过程的操作简便性也优于在线膜。
此类镀膜的特点主要是:由一些热稳定性能较好的薄膜组成。
此类薄膜在500℃-600℃高温的大气环境下能够抗拒继续氧化或其它化学反应,使薄膜在烘弯或半钢化的温度和大气条件下不变性、不粉沫化剥落,再加上外加耐热耐化学腐蚀,机械性能优异的保护层,使磁控溅射可热弯膜具有耐热弯、经久不变色、机械化学稳定性好的优良的可热处理薄膜。
二、磁控溅射可热弯膜与在线膜热弯工艺性比较
1)由于镀制工艺方法的不同,磁控溅射物理成膜与在线化学成膜在理化、光化稳定性上有-定的差异。
在长时间光照、化学(大气、酸反应、潮湿)环境条件下在线膜会有程度不同的颜色细微变化。
特别在同一外墙立面上由于光照遮挡程度不一,较长时间以后会在对比条件下显现出人眼可感知的色彩差异。
2)由于成膜方法不同。
在线膜在国内弯制工艺和作业中有许多不足之处。
A.在弯制前,玻璃面上不能有任何残留污渍、手印等,否一旦弯制后其印迹等将咬死,难以再清洗恢复。
B.在弯制时考虑到加工效率,在出炉取出和重新放入过程中,由于炉具及环境炎热,万一操作人员汗水滴在膜面上,或由于裁切清洗后水滴未干即行投入弯制,则弯制取出时往往水滴处膜层已不复存在,形成漏光点而报废或严重影响质量。
而且在众多的使用加工者中对弯制后出现的局部淡化、薄化和铜钱斑(局部剥落)感到束手无策。
而磁控溅射可热弯膜几乎不存在这一弊病。
3)由于在线膜工艺装备简单成本低,但同时受喷涂、气相沉积等工艺的限制,虽然国外技术先进的厂家在工艺技术方面作了许多努力,而且取得了许多成果,但由于成膜原理及控制精度的限制,长时间的工艺一致性还是存在不同程度的局限。
如果不是选用连贯同一时序生产,而是有一个时间段间隔的产品往往会出现色差值△E比较大的状况。
如果安装后在同一立面同一视区内可能会感觉出有色差。
而磁控溅射可热弯膜由于控制精度高,采用离线冷基片可确保不会出现可感知色差(△T>2)的情况。
三、弯弧镀膜玻璃产品品种单一问题
可热弯膜,包括在线膜和磁控真空溅射可热弯膜,由于膜的耐高温烘烤的要求,膜材料及膜结构的选择余地小,膜的品种单-。
使膜层与玻璃基片形成的透反射性能的调节余地不大。
根据幅射(包括光波)能量的守恒定律:
T透射+R反射+A吸收=1
整个膜与玻璃系统的性能与玻璃的吸收率A关系密切。
可热弯镀膜玻璃一般均采用有色的吸收玻璃作基片。
例如:绿色、兰色、海兰色、古铜色、灰色玻璃,均是在玻璃熔炼时,添加各种特定金属元素。
其光学特点是,由于金属原子在可见光谱区域(3800-7200A)的光谱吸收率不同而形成各种特定的颜色(透过)。
光波在带有一定光谱吸收率的玻璃中行进后膜层界面反射,再在吸收玻璃内反射行进,使最终吸收玻璃与膜组成系统反射色也形成相应的光谱反射和吸收综合而成的颜色。
而有色吸收玻璃的光谱吸收与该品种是一一对应的,绝大部分浮法玻璃厂家生产的有色吸收玻璃的品种(光谱吸收率A值)只限定在-种。
根据上述原理玻璃吸收A值不变,膜结构材料不变,导致玻璃与膜面的反射率也难有变化,从而使镀膜玻璃透过率和反射颜色也只能有少量几个品种,而不可能象常规磁控溅射平板镀膜玻璃那样反射颜色和透过率反射率可以有许多变化和品种供选择。
苏州华东镀膜玻璃公司在国际上首创磁控真空溅射镀膜玻璃热弯弧形成功,是对真空溅射镀膜玻璃深加工的一大突破,国际上尚无先例,这是对引进国外设备(美国AIRCO公司)消化吸收和突破,这是在利用国外设备加上自己的高新技术生产出外国人做不出的产品。
该公司有大量高层次科技人员,大量硕士、博士生,生产工人一般为大专生。
该公司目标向高科技发展,对技术、产品要求非常严谨。
每批镀膜玻璃热弯成形后,均送交国家指定的秦皇岛国家玻璃质量监督检验中心去检验。
热弯后的玻璃,可见光透射比、反射比、太阳光透射比、反射比、太阳光总透射比、色差、耐磨、耐酸等技术要求,理化性能均达到没热弯前真空溅射镀膜玻璃标准,该公司三年前热弯镀膜玻璃已用在杭州武林综合楼(海兰色),宁波石油大厦(绿色),宁波第二人人民医院(灰色),杭州电信大楼等工程共计约一万五千平米左右,但华东镀膜玻璃公司仍没有对外大量宣传,而仍在默默的进一步研究,如何增加可热弯的颜色和品种。
这种对技术精益求精,严谨的态度值得学习。
该公司正在向镀膜玻璃深加工方向进一步发展,希望同行业的朋友们向高新技术方向研究发展,没有新的发展没有新的突破,就意味着将要落后。