复合材料层板固化全过程残余应变应力的数值模拟
复合材料成型数值模拟及其应用

复合材料成型数值模拟及其应用复合材料在现代工业中应用广泛,具有轻质、高强度、高刚度和优异的耐久性等特点。
然而,复合材料的成型过程可谓是一门艺术和技术的结合,需要大量的工程经验,试错和大量的实验验证。
随着计算机技术的不断进步,数值模拟成为一种有效的预测和分析复合材料成型过程的方法。
本文将从数值模拟的角度出发,探讨复合材料在制造过程中的应用。
一、复合材料成型的基本过程复合材料的成型过程一般分为模具设计、预浸料制备、预浸料浸渍、层叠和压缩这几个步骤。
1. 模具设计模具是决定复合材料成型特性的关键因素之一。
合理的模具设计可以提高复合材料的成型质量和生产效率。
目前,常用的模具包括手工模具、金属模具和树脂模具等。
2. 预浸料制备复合材料一般采用热固性环氧树脂作为基体材料,预浸料是将纤维预先浸润在树脂中的半成品材料。
预浸料的制备是浸渍复合材料的基础,质量的高低直接影响到成品的质量。
3. 预浸料浸渍浸渍是将预浸料浸润在纤维上的过程,纤维的含量、树脂的流动性和浸渍过程的参数都是影响浸渍质量的重要因素。
4. 层叠和压缩将浸渍好的纤维层叠起来并进行压缩,以使树脂浸润在纤维之间,形成复合材料。
二、复合材料成型数值模拟的概述数值模拟是一种通过计算机模拟实际过程的方法,可以在虚拟环境中预测实际过程的结果。
数值模拟可以显著缩短调试时间和成本,减少实验次数和避免安全事故的发生。
复合材料成型数值模拟的基础是复合材料的力学行为和传热学理论。
主要包括有限元分析、流体力学分析、热传分析和材料模拟等方法。
可采用数值模拟技术模拟复合材料的成型过程及其过程参数和材料物性对成型过程的影响。
数值模拟可以分为几个步骤:模型的建立、边界条件的确定、求解方案的选择、数值计算和结果的分析等。
模型的建立是数值模拟的基础,复合材料成型过程的模型建立对数值模拟的精度有很大的影响。
应该综合考虑成型过程的物理和化学特性,设计实用、精确、高效、可靠的数值模拟模型。
涂层残余应力预测分析模型
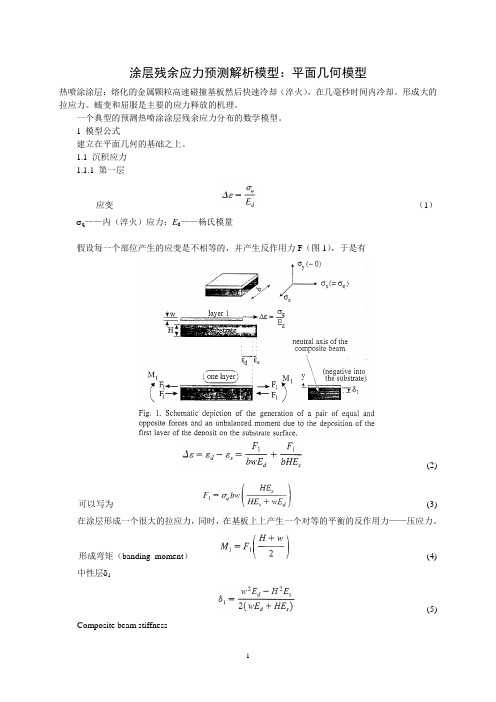
涂层残余应力预测解析模型:平面几何模型热喷涂涂层:熔化的金属颗粒高速碰撞基板然后快速冷却(淬火),在几毫秒时间内冷却。
形成大的拉应力。
蠕变和屈服是主要的应力释放的机理。
一个典型的预测热喷涂涂层残余应力分布的数学模型。
1 模型公式建立在平面几何的基础之上。
1.1 沉积应力1.1.1 第一层应变(1)σq——内(淬火)应力;E d——杨氏模量假设每一个部位产生的应变是不相等的,并产生反作用力F(图1),于是有(2)可以写为(3) 在涂层形成一个很大的拉应力,同时,在基板上上产生一个对等的平衡的反作用力——压应力。
形成弯矩(banding moment)(4) 中性层δ1(5)Composite beam stiffness(6)平衡弯矩M1,产生曲率变化,κ1-κ0(7)通常,κ0可以处理为零。
如果涂层在凹面,则曲率是可以明确的。
图1的情况。
假设双向应力相等(σx =σz),厚度方向应力可以忽略(σy =0)。
由泊松效应(Poisson effect),σz将在x方向导致一个应变。
X方向的net应变可以写为(8) 于是,x方向的应力应变关系可以表示为:(9) Effective young’s modulus value.由于仅考虑弹性状态,因此,基板内沿着厚度方向的应力变化应该是线性的,只需要计算基板的底部和顶部的应力即可。
从材料力学可以计算:(10)(11) 于是,可以得出涂层第一层中部的应力:(12) 1.1.2 第二层考虑在基板(镀层)上冲击形成第二层,如图2所示。
不等应变的大小与前面相同。
平衡应变改为:(13) 该式中,F2是作用在前面的镀层与基板构成的复合板上的,其中性层δ1如图1所示。
这一层与基板具有相同的应变,E2e是等效杨氏模量:(14) 代入上式,可以得到F2的表达式:(15)F2分摊在镀层第一层和基板中。
作用在基板上的力为:(16)同样,作用第一层镀层上的力为:(17)显然地,F2s和F2w都是压应力。
基于COMSOL的树脂基复合材料固化成型过程多场耦合仿真
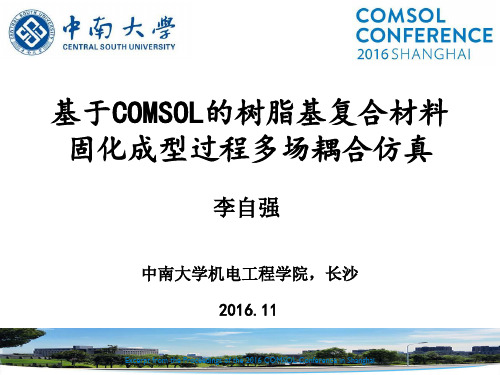
20mm孔
30 27
20
厚度超差\mm
0.4
0.2
厚度超差基线0[mm]
0.0
-0.2
Φ12mm孔
Φ20mm孔
-0.4
1
2
3
4
5
位置
厚度偏差
当硅橡胶芯模预制调型孔孔径为12mm时,辅助成型的帽型加筋结构制件 成形精度较好。
四、基于COMSOL的复合材料帽型件的建模仿真
仿真结果分析-预制调型孔最佳尺寸范围的确定
无孔
Φ6mm孔
内、外模具辅助成型复合材料帽形制件示意图
Φ12mm孔
Φ20mm孔
不同结构硅橡胶芯模
本文通过在硅橡胶芯模内部预制调型孔,实现硅橡胶芯模在固化过程中的压力可
控,但是预制调型孔孔径的大小与帽型制件成型质量紧密相关,需要建立基于压力 场均匀调控的调型孔孔径模型,最终实现对帽型制件的维形保压效果。
2000
3000
4000
5000
6000
7000
8000
时 间 \s
Φ12.5mm孔
Φ11.5mm孔
Φ12.5mm孔
当硅橡胶芯模预制调型孔孔径为11.5~12.5mm时,辅助成型的帽型加筋结构制件固化 压力较均匀,并且能够较好维持初始设计尺寸。可确定对于该类复合材料帽型加筋结 构成型所需硅橡胶芯模调型孔孔径的最佳尺寸范围为d=11.5mm~12.5mm。
m (1Vf
) ( m 12 f )(km (k f Gm )km
k f )Gm (1Vf )Vf (k f km )GmVf
23
2 E1k T
E1E2 2E1kT
4122kT
T300AG80复合材料U形结构件成型残余应力的有限元模拟

2021 年 2 月第 45 卷第 2 期 \ 〇丨.45 No. 2 Feb. 2021MATERIALS FO R MECHANICAL ENGINEERING1X )I : 10.11973/jx g ccl202102015T 300/AG 80复合材料U 形结构件成型残余应力的有限元模拟杨康闫照为\梁宇u 2,王吉1>2, 丁文喜1(1.沈阳航空航天大学辽宁省通用航空重点实验室.沈阳110136;2.辽宁通用航空研究院设计部,沈阳110136)摘要:利用ABAQUS 有限元软件建立T 300碳纤维增强AG 80环氧树脂(T 300/AG 80)复合材料U 形薄壁结构件模型•研究了热压固化成型过程中的应力和回弹变形量(同步模拟脱模)变化 以及脱模后的残余应力分布,通过小孔试验法对残余应力模拟结果进行了验证。
结果表明:成型过 程中,U 形结构件侧壁和底面的应力和回弹变形量均随时间延长而增加;随着距底面距离或距对 称中心距离的增大,应力和回弹变形量增大;脱模后,U 形结构件对称中心处的残余应力最小,残 余应力随着距底面距离或距对称中心距离的增大而增大;脱模前后释放的残余应力越大,回弹变形 量越大;小孔法测得的残余应力与模拟结果的相对误差小于10% ,说明模拟结果较准确。
关键词:树脂基复合材料;固化成型;残余应力;ABAQUS 软件;小孔法中图分类号:V 214.8文献标志码:A文章编号:1000-3738(2021)02-0085-05Finite Element Simulation of Molding Residual Stress of T300/AG80(1. Liaoning K e y Laboratory of General Aviation, S h e n y a n g Aerospace University, S h e n y a n g 110136, C h i n a ;2. Design Department, Liaoning General Aviation A c a d e m y , S h e n y a n g 110136, China)Abstract : A U -s h a p e d thin-walled structure part m o d e l of T 300 carbon fiber reinforced A G 80 e p o x y resin(T 300/A G 80) composite w a s established b y A B A Q U S finite element software. T h e stress a nd spring b ack a m o u n t (synchronous demolding by simulation) changes during hot-press curing molding and the residual stress distribution after demolding w e r e studied. T h e simulation of residual stress w a s verified by the small-hole test method. T h e results s h o w that during the molding process, the stress and springback a m o u n t of the side wall a nd b o t t o m surface of the U -s h a p e d structure part increased with time. T h e stress an d springback a m o u n t increased with the distance f r o m the b o t t o m surface or the distance f r o m the center of sy m m e t r y. After demolding, the residual stress at the center of s y m m e t r y of the U -s h a p e d structure part w a s the smallest, a nd the residual stress increased with the distance f r o m the b o t t o m surface or the distance f r o m the center of s y m m e t r y. T h e greater the residual stress released before and after demolding, the greater the springback amount. T h e relative error b e tween the residual stress m e a s u r e d b y the small-hole m e t h o d and the simulation w a s less than 10%,indicating the simulation w a s accurate.Key words : plasticvS com posite ; curing m olding ; residual stress ; A B A Q U S softw are ; small-hole methodComposite U-shaped Structure PartYANG Kang 1 2, YAN Zhaowei 1, LIANG Yu ' 2, WANG Ji 1 2, DING Wenxi〇引言收稿日期:2020-02-20;修订日期:2021-01-12作者简介:杨康(1988 —),男.湖北黄冈人,工程师.硕士 通信作者:梁宇丁.程师纤维增强树脂基复合材料具有优异的综合性 能,广泛应用于大型民用飞机结构。
基于abaqus的复合材料固化变形及参与应力仿真简介
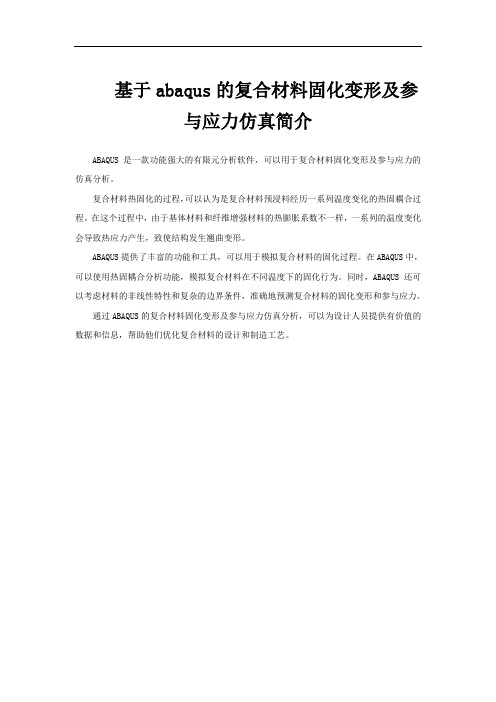
基于abaqus的复合材料固化变形及参
与应力仿真简介
ABAQUS是一款功能强大的有限元分析软件,可以用于复合材料固化变形及参与应力的仿真分析。
复合材料热固化的过程,可以认为是复合材料预浸料经历一系列温度变化的热固耦合过程。
在这个过程中,由于基体材料和纤维增强材料的热膨胀系数不一样,一系列的温度变化会导致热应力产生,致使结构发生翘曲变形。
ABAQUS提供了丰富的功能和工具,可以用于模拟复合材料的固化过程。
在ABAQUS中,可以使用热固耦合分析功能,模拟复合材料在不同温度下的固化行为。
同时,ABAQUS还可以考虑材料的非线性特性和复杂的边界条件,准确地预测复合材料的固化变形和参与应力。
通过ABAQUS的复合材料固化变形及参与应力仿真分析,可以为设计人员提供有价值的数据和信息,帮助他们优化复合材料的设计和制造工艺。
缠绕复合材料结构固化残余应力的数值计算

缠绕复合材料结构固化残余应力的数值计算李雷;刘庆;沈创石【摘要】利用傅里叶热传导方程、基体的固化动力学方程以及复合材料在固化过程中的力学性能本构模型,建立缠绕复合材料结构的固化工艺以及残余应力应变分析模型,分析计算研究复合材料固化过程中产生的残余应力.计算结果显示:缠绕复合材料最外层的残余应力均为正应力,最内层的残余应力均为负应力;缠绕复合材料的内径、层数、纤维体积分数、基体化学收缩比以及固化工艺温度对残余应力的影响较大.%The curing process and residual stress model for filament wound composite structure were established by using the Fourier heat conduction equation, the curing kinetics equation of the matrix and the mechanical consti-tutive model of the composite material during the curing process to study the residual stress produced during the cu-ring process.The calculate results show that the residual stress of the outermost layer of the wound composite mate-rial is positive stress, and the residual stress in the innermost layer is negative stress.The influence of the inner di-ameter, number of layers, volume fraction of the fiber, shrinkage ratio of the matrix and the curing temperature on residual stress are larger.【期刊名称】《科学技术与工程》【年(卷),期】2018(018)015【总页数】7页(P237-243)【关键词】缠绕复合材料;残余应力;固化【作者】李雷;刘庆;沈创石【作者单位】中国飞行试验研究院飞机所,西安710089;中国飞行试验研究院飞机所,西安710089;西北工业大学工程力学系,西安710072【正文语种】中文【中图分类】TB332缠绕复合材料因其具有强度大、刚度高、抗疲劳性能和耐腐蚀性能好以及结构的可设计性好等诸多优点而被广泛应用于航空、航天等多个行业。
树脂基复合材料残余应力与固化变形机理及控制研究进展
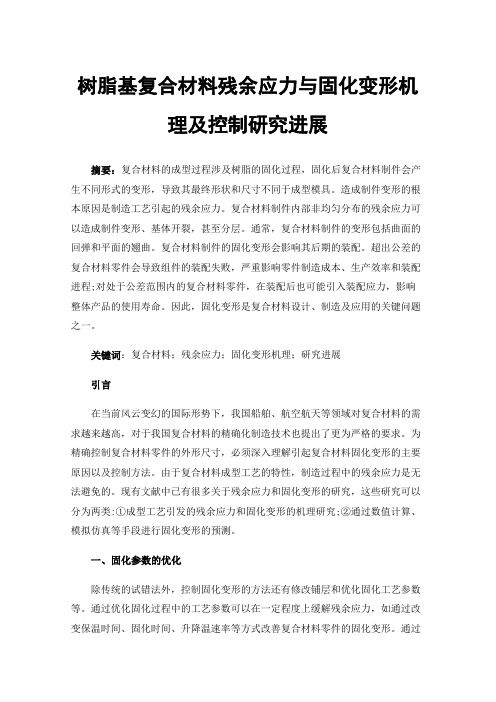
树脂基复合材料残余应力与固化变形机理及控制研究进展摘要:复合材料的成型过程涉及树脂的固化过程,固化后复合材料制件会产生不同形式的变形,导致其最终形状和尺寸不同于成型模具。
造成制件变形的根本原因是制造工艺引起的残余应力。
复合材料制件内部非均匀分布的残余应力可以造成制件变形、基体开裂,甚至分层。
通常,复合材料制件的变形包括曲面的回弹和平面的翘曲。
复合材料制件的固化变形会影响其后期的装配。
超出公差的复合材料零件会导致组件的装配失败,严重影响零件制造成本、生产效率和装配进程;对处于公差范围内的复合材料零件,在装配后也可能引入装配应力,影响整体产品的使用寿命。
因此,固化变形是复合材料设计、制造及应用的关键问题之一。
关键词:复合材料;残余应力;固化变形机理;研究进展引言在当前风云变幻的国际形势下,我国船舶、航空航天等领域对复合材料的需求越来越高,对于我国复合材料的精确化制造技术也提出了更为严格的要求。
为精确控制复合材料零件的外形尺寸,必须深入理解引起复合材料固化变形的主要原因以及控制方法。
由于复合材料成型工艺的特性,制造过程中的残余应力是无法避免的。
现有文献中已有很多关于残余应力和固化变形的研究,这些研究可以分为两类:①成型工艺引发的残余应力和固化变形的机理研究;②通过数值计算、模拟仿真等手段进行固化变形的预测。
一、固化参数的优化除传统的试错法外,控制固化变形的方法还有修改铺层和优化固化工艺参数等。
通过优化固化过程中的工艺参数可以在一定程度上缓解残余应力,如通过改变保温时间、固化时间、升降温速率等方式改善复合材料零件的固化变形。
通过改变石墨/双马树脂基复合材料的成型工艺条件来控制和减少固化工艺引起的残余应力,针对不对称铺层的层合板,分别研究了保压温度、保压时间、冷却速率、冷却压力和后固化对残余应力的影响。
实验结果表明,通过在较低温度下固化更长的时间或在三步固化循环中利用中间的低温保压,可以在保持或增强横向力学性能的同时,将残余应力降低25%~30%。
精密加工中复合材料残余应力分布实验分析

精密加工中复合材料残余应力分布实验分析一、复合材料在精密加工中的重要性随着现代工业的快速发展,对材料性能的要求越来越高,复合材料因其优异的机械性能、耐腐蚀性和轻质化特点,在航空航天、汽车制造、电子设备等领域得到了广泛应用。
在这些领域中,精密加工是实现高性能产品的关键步骤,而复合材料在精密加工过程中产生的残余应力分布,对其性能和使用寿命有着显著影响。
1.1 复合材料的特性复合材料是由两种或两种以上不同材料组合而成的新型材料,这些材料在性能上互补,使得复合材料具有比单一材料更优异的综合性能。
例如,碳纤维增强树脂基复合材料具有高强度、高刚度、低密度等特点,是精密加工中理想的材料选择。
1.2 精密加工对复合材料的要求精密加工要求材料具有高度的一致性和可预测性,复合材料在加工过程中的稳定性和可加工性是其在精密加工领域应用的关键。
此外,复合材料在加工过程中的热应力、机械应力等都会影响到最终产品的精度和性能。
1.3 残余应力对复合材料性能的影响残余应力是指在没有外部载荷作用下,材料内部存在的应力状态。
在精密加工过程中,由于材料的切削、磨削等加工方式,会在复合材料内部产生残余应力。
这些应力可能会导致材料变形、裂纹甚至断裂,影响产品的精度和可靠性。
二、复合材料残余应力分布的实验分析为了准确评估和控制复合材料在精密加工中的残余应力分布,需要进行系统的实验分析。
通过实验可以了解加工过程中应力的产生、分布和变化规律,为优化加工工艺和提高产品质量提供依据。
2.1 实验材料与方法实验通常采用典型的复合材料,如碳纤维增强树脂基复合材料,通过精密加工设备进行加工。
实验方法包括但不限于切削实验、磨削实验、热处理实验等,通过这些实验可以模拟实际加工过程中的应力状态。
2.2 残余应力的测量技术残余应力的测量是实验分析的关键环节,常用的测量技术包括X射线衍射法、超声法、层析法等。
这些技术可以无损地测量材料内部的应力分布,为分析应力产生的原因和规律提供数据支持。
- 1、下载文档前请自行甄别文档内容的完整性,平台不提供额外的编辑、内容补充、找答案等附加服务。
- 2、"仅部分预览"的文档,不可在线预览部分如存在完整性等问题,可反馈申请退款(可完整预览的文档不适用该条件!)。
- 3、如文档侵犯您的权益,请联系客服反馈,我们会尽快为您处理(人工客服工作时间:9:00-18:30)。
第28卷 第2期2008年4月航 空 材 料 学 报J OURNAL OF A ERONAUT ICAL MAT ER I A LSV o l 128,N o 12 A pr il 2008复合材料层板固化全过程残余应变/应力的数值模拟胡照会, 王荣国, 赫晓东, 杜善义(哈尔滨工业大学复合材料与结构研究所,哈尔滨150001)摘要:采用商业软件对带有铝板的复合材料层板固化全过程残余应变/应力进行数值模拟计算。
在固化过程的模拟中,应用有限元法计算复合材料层板热-化学模型,有限差分法计算固化动力学模型,通过设置较小的时间步实现求解两个模型强耦合的关系。
在残余应力数值模拟中,化学收缩引起的应变在每一计算步以初始应变施加在复合材料结构上。
基于以上技术,对带有铝合金的复合材料层板固化全过程残余应变/应力演化进行数值模拟,并分析纤维方向和垂直纤维方向复合材料的残余应变/应力演化历程。
通过与试验中层板曲率的比较,验证文中模型计算的准确性。
关键词:残余应变/应力;耦合;初始应变;约束中图分类号:V 21418 文献标识码:A 文章编号:1005-5053(2008)02-0055-05收稿日期:2007-05-18;修订日期:2007-08-15基金项目:国家863项目(2005AA 304010)作者简介:胡照会(1975)),男,博士研究生,研究方向:复合材料设计,计算,性能表征。
先进复合材料因高强度比,重量轻,可设计性使其在航天航空中广泛应用。
复合材料经常和金属材料一同使用,例如,复合材料导弹弹翼中需要加入钛合金骨架,蜂窝夹层结构中的复合材料蒙皮和铝蜂窝,金属内衬纤维缠绕复合材料压力容器等。
固化成型过程是复合材料高性能形成的一个关键阶段,残余应变/应力形成也是伴随固化过程进行。
其中残余应变直接关系结构的尺寸稳定性,并且总应变中机械应变通过本构关系与残余应力相联系。
残余应力的产生降低了结构强度,甚至是造成结构破坏。
如果能有效评估固化过程中残余应变/应力的形成,可以准确保证结构尺寸稳定性并预防和降低由于残余应力而造成的/前负载0,数值模拟为实现这一目标提供一种途径。
对于固化过程中残余应力的模拟,已开展了很多这方面的工作[1~3]。
多数固化过程中残余应力的数值评估,都是采用专有的残余应力程序[4~6],针对一些特殊的问题,没有广泛性。
商业软件具有强大的前后处理,但是,并未提供固化过程瞬态温度场及残余应力模拟的程序和单元,需要二次开发实现。
文中采用有限差分法计算复合材料的固化动力学方程,应用有限元法计算复合材料热-化学模型,通过设置小的时间步实现固化模拟中热-化学方程与固化动力学方程的强耦合过程。
借助热弹性理论,将固化计算得到温度场以体荷载方式施加计算热的残余应力,并将化学收缩引起的应变以初始应变在每一计算步施加,这样就可以利用现有的商业软件对残余应力进行数值模拟。
采用以上技术,对带有铝板的复合材料层板的固化全过程残余应变/应力数值模拟,并分析复合材料层合板纤维方向和垂直纤维方向代表点的应变/应力的演化历程。
1 基本方程及数值解法固化过程中热残余应力的计算属于热机械耦合问题,本研究采用间接法考虑。
间接法的第一步是计算固化瞬态温度场,即通过有限元法并结合有限差分法考虑热-化学模型与固化动力学模型二者之间的强耦合关系。
第二步计算残余应力,即将每个时间步固化模拟得到的温度场分布以体荷载的方式进行施加,计算这个时间步应力/应变场问题。
111 固化模拟中的模型方程复合材料固化过程分析是一个传热和化学反应相耦合的非线性内热源问题,其中内热源来自树脂基体内部的聚合交联放热反应。
复合材料的热-化学模型,即Fourier 热传导方程为:Q c p 9T 9t =K x 92T 9x 2+K y 92T 9y2+q #(1)航 空 材 料 学 报第28卷式中,Q 为密度;c p 为比热;T 为温度;K 为热导率,下标表明方向;q #单位时间内由于固化反应所产生的热量。
固化过程中的内热源q #可以通过树脂体系的固化反应动力学模型求解,方程的表达式为: q =d A d t H ](2)d Ad t =A exp (-E A RT)f (A )(3)式中:H ]为单位质量固化反应放热量;E a 为激活能;A 为指前因子;R 为气体常数。
f (A )为机理函数。
其中公式(3)为树脂的固化动力学模型,并将此方程用作复合材料体系的固化动力学模型。
固化成型温度场数值模拟中的强耦合过程体现在固化动力学模型将为热-化学模型提供内热源,热-化学模型计算复合材料温度场反过来又将影响树脂的固化速度,影响内热源。
因此,固化动力学模型和热-化学模型是相互影响,所以二者的计算必须同时进行,这样才能够真正实现真实固化过程数值模拟。
文中强耦合实现过程:假设模型各点初始的固化度及温度,根据公式(3),(2)计算模型各点的内热源项,并代入方程(1),应用有限元法求解温度场,通过求解得到各点温度,利用公式(3)求解树脂的固化速度,将固化速率代入公式(2)求解内热源,得到内热源代入公式(1)计算温度场,如此反复,相互影响。
事实上,固化动力学方程和热-化学方程耦合过程是时变的,时间步设置小量是两个方程强耦合过程实现的关键。
公式(1)微分方程通过有限元求解,在商业有限元软件可以直接实现,所以这里主要是描述固化动力模型的计算实现。
树脂固化动力学模型通过向前有限差分法进行求解,如公式(4)所示: At+$t=A t+(d A d t)t+$t$t (4)对于固化度的求解,可假设在某一个小时间内温度为常量,用时间积分的方法计算固化度,假设A t为已知上一步计算值,(d A d tt +$t)可以事先由固化动力学模型确定,很容易得到A t +$t,这部分工作需要在商业软件上进行二次开发。
112 残余应力模拟方程文中的应力-应变之间认为保持弹性关系: R i =Q ij (E i -e j )(5)式中,E i 为总应变;e j 为非机械应变;Q ij 为材料参数。
通过公式(5)可知,机械应变直接影响着残余应力。
带有铝合金板复合材料层板机械应变来源于复合材料厚度方向上非机械应变的不匹配及与铝合金非机械应变的不匹配,其中非机械应变由化学收缩应变e chj 和热应变e thj 构成: e j =e thj +e chj(6)热应变即由温度产生的应变,这里不再累述。
化学收缩应变通过树脂固化度计算:e ch m =(1+B A )1/3-1(7)式中,B 由试验确定的树脂总体积的收缩,这里取-0105。
纤维在固化过程中不发生化学收缩,复合材料的化学收缩可以根据细观力学模型确定,其中顺纤维方向和垂直复合材料应变为: ech 1=e chm E m (1-v f )E f(8) e ch2=(1+u m )e chm (1-v f )-u c E ch1(9)式中,v f 为纤维体积分数;u m ,u c 分别为树脂和复合材料的泊松比;E m ,E f 分别为树脂和纤维的弹性模量。
计算全过程的残余应力/应变,首先将计算的化学应变在每一荷载步计算前以初始应变施加。
然后将固化分析得到的温度以体荷载方式施加就可以进行全过程的残余应力计算,最后给出残余应力/应变的分析。
可以看出,固化过程中温度场和树脂的收缩将直接影响复合材料应力/应变演化历程。
因此,影响固化过程中温度场分布的变量和树脂收缩的变量也间接对复合材料全过程中应力/应变有所贡献,其中包括影响温度场分布的树脂固化方程中各个参数及其反应热量和影响树脂化学收缩的固化度。
2 有限元模型本工作对带有铝板的复合材料层板进行计算,图1为结构示意图。
横坐标X 方向代表顺纤维方向,Y 方向为垂直纤维方向,Z 方向为厚度方向。
因为结构为正方形,对称结构,所以只选择了四分之一进行分析计算。
认为结构的X 方向上各个截面应图1 复合材料结构示意图F i g 11 Sche m a tic plan o f co m posite struct u re56第2期复合材料层板固化全过程残余应变/应力的数值模拟变/应力一致,同样认为Y 方向上各个截面的应力/应变也一致,将三维问题简化为二维平面分析,即选择了两个平面CC .A .A 和BB .C .C 进行分析,分别代表顺纤维一个平面,垂直纤维一个平面。
若复合材料层板计算结果输出的是温度场,应变场和应力场,则需要大量不同时刻的各个场分布图说明连续的演化过程。
鉴于篇幅,并未采用这种表述方式,而是在每个平面上中间处选择2个中心点说明两种材料应变/应力演化历程,即平面CC .A .A 选择A .,A 两个点,平面BB .C .C 选择B ,B .。
复合材料固化过程中瞬态温度场及全过程残余应力的计算都在ANSYS 软件平台上完成。
图2为带有铝合金板的复合材料有限元网格图,单元数目为70。
复合材料固化成型热分析选用单元P l a ne55。
在全过程残余应力的计算中,选用结构单元P l a ne42。
树脂体系的动力学模型通过动态DSC 获得,结果如下:d A d t=8086@exp(511261@1000/RT)(1-A )1104图2 层板有限元模型F ig 12 F i nite e le m en tm ode l for la m i nated p l a te3 残余应变/应力模拟及试验验证311 固化的数值模拟图3为结构示意图中A .点(复合材料内部)温度与固化度历程曲线。
由温度历程可以看出,温度场基本上与固化工艺(MRC )一致,也呈现两个温度平台。
在第一平台温度较MRC 工艺升温慢,复合材料导热系数较小,使其温度有些延迟。
在到达第一平台时,材料内部温度已经高于了平台温度80e。
图3 材料内部温度与固化度历程曲线F ig 13 Curves of te m perature and the deg ree o fcure hist o ry ins i de composite m ateria l从固化度历程可以看出,这时树脂已经开始固化,固化放热是其高于平台温度的原因。
在第二个平台升温时,树脂的固化速率升高加快,使固化放热愈加明显。
材料内部温度达到129e ,已经高于平台温度9e ,此阶段固化放热加剧温度场的变化。
此阶段计算温度场将作为体荷载施加进行残余应力计算,其中利用固化度考虑结构中的树脂化学收缩。
结构示意图中B .点也得到类似结论,这里不再讨论。
312 残余应变/应力31211 树脂物理性能变化固化全过程残余应力数值模拟中,考虑复合材料性能的变化,即认为纤维在固化过程中不发生变化,所有性能变化都是树脂的贡献。
固化过程中,树脂由液态变为橡胶态,最后形成玻璃态,固化完全。