橡胶垫的生产工艺
橡胶成型工艺及模具设计

挤出机由螺杆、机身、机头(包括口型和芯型)、 机架和传动装置等部件组成。
一、螺杆
螺杆种类: 按螺纹分:单头、双头、 三头 按螺距分:等距收敛式和 复合螺纹等 按螺杆外形分:圆柱形、
圆锥形
二、机身(机筒)
机筒为中空圆筒,为了及时散发
和提供热量,机筒备有夹套,可通入
冷却水和蒸汽。
三、机头与口型
1.机头 ①直向形机头 如圆筒形、喇叭形 ②T形、Y形
5. 必须进行硫化才能使用,热塑性弹性体除外。
6. 必须加入配合剂。
其它如比重小、硬度低、柔软性好、气密性好等 特点,都属于橡胶的宝贵性能。
橡胶基本加工工艺
无论什么橡胶制品,都要经过混炼和硫化这两个 过程。橡胶基本加工工艺主要包括塑炼、混炼、 压延、压出、成型和硫化等。另外,对于一些特 殊产品还包括注压、浇注和黏合。
聚合单体:氯丁二烯 ★一般工作温度:-35~120℃
★特性:耐候性、耐臭氧性、阻燃、耐热性及耐化学 药品性均好 ★用途:轮胎内衬层、低压电线电缆、输送带、减震 橡胶、窗户密封条、胶粘剂、胶布、涂料 ★参考价格:3.0~3.5万元/吨
硅胶 (Q )
聚合单体:主链由硅原子和氧原子交替组成 ★一般工作温度:-93~250℃ ★性能:使用温度范围最广,毒性最低、具生理惰性、 透气性好、电绝缘性好,物理机械性能较差 ★用途:胶管、胶带、胶辊、电绝缘制品、人造皮肤、 器官等. ★参考价格:7.0~8.0万元/吨
三元乙丙胶 ( EPDM )
聚合单体: 乙烯\丙烯\第三单体 ★一般工作温度:-50~150℃ ★性能:耐老化耐臭氧性、耐极性液体、耐水及 过热水、水蒸气好、耐电性能好 ★用途:电线电缆绝缘层、汽车玻璃除水条、窗户密 封条、 蒸汽胶管、输送带等 ★参考价格:2.8~3.3万元/吨
橡胶制品生产工艺流程

橡胶制品生产工艺流程一、橡胶制品基本工艺流程伴随现代工业尤其是化学工业的迅猛发展,橡胶制品种类繁多,但其生产工艺过程,却基本相同。
以一般固体橡胶 ( 生胶 ) 为原料的制品,它的生产工艺过程主要包括:原材料准备→塑炼→混炼→成型→硫化→休整→检验二、橡胶制品原材料准备橡胶制品的主要材料有生胶、配合剂、纤维材料和金属材料。
其中生胶为基本材料 ; 配合剂是为了改善橡胶制品的某些性能而加入的辅助材料 ; 纤维材料 ( 棉、麻、毛及各种人造纤维、合成纤维 ) 和金属材料 ( 钢丝、铜丝 ) 是作为橡胶制品的骨架材料,以增强机械强度、限制制品变型。
在原材料准备过程中,配料必须按照配方称量准确。
为了使生胶和配合剂能相互均匀混合,需要对某些材料进行加工:生胶要切胶、破胶成小块 ;块状配合剂如石蜡、硬脂酸、松香等要粉碎 ;粉状配合剂若含有机械杂质或粗粒时需要筛选除去 ;液态配合剂 ( 松焦油、古马隆 ) 需要加热、熔化、蒸发水分、过滤杂质;配合剂要进行干燥,不然容易结块、混炼时旧不能分散均匀,硫化时产生气泡,从而影响产品质量;三、橡胶制品的塑炼生胶富有弹性,缺乏加工时的必需性能 ( 可塑性 ) ,因此不便于加工。
为了提高其可塑性,所以要对生胶进行塑炼 ; 这样,在混炼时配合剂就容易均匀分散在生胶中 ; 同时,在压延、成型过程中也有助于提高胶料的渗透性 ( 渗入纤维织品内 ) 和成型流动性。
将生胶的长链分子降解,形成可塑性的过程叫做塑炼。
生胶塑炼的方法有机械塑炼和热塑炼两种。
机械塑炼是在不太高的温度下,通过塑炼机的机械挤压和摩擦力的作用,使长链橡胶分子降解变短,由高弹性状态转变为可塑状态。
热塑炼是向生胶中通入灼热的压缩空气,在热和氧的作用下,使长链分子降解变短,从而获得可塑性。
四、橡胶制品的混炼为了适应各种不同的使用条件、获得各种不同的性能,也为了提高橡胶制品的性能和降低成本,必须在生胶中加入不同的配合剂。
混炼就是将塑炼后的生胶与配合剂混合、放在炼胶机中,通过机械拌合作用,使配合剂完全、均匀地分散在生胶中的一种过程。
橡胶垫的生产工艺
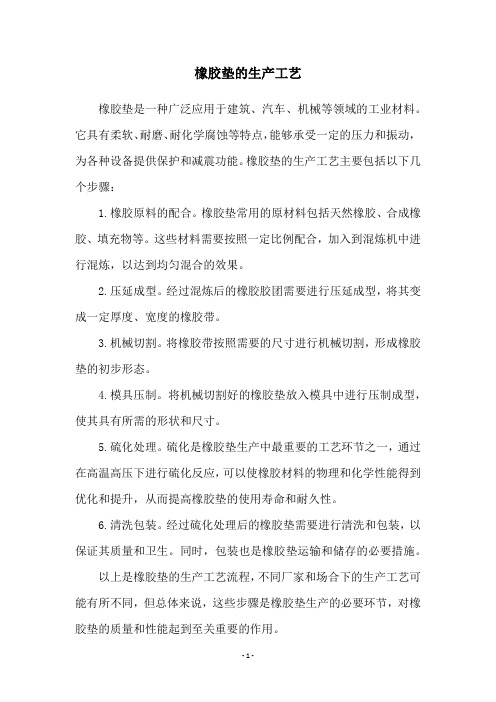
橡胶垫的生产工艺
橡胶垫是一种广泛应用于建筑、汽车、机械等领域的工业材料。
它具有柔软、耐磨、耐化学腐蚀等特点,能够承受一定的压力和振动,为各种设备提供保护和减震功能。
橡胶垫的生产工艺主要包括以下几个步骤:
1.橡胶原料的配合。
橡胶垫常用的原材料包括天然橡胶、合成橡胶、填充物等。
这些材料需要按照一定比例配合,加入到混炼机中进行混炼,以达到均匀混合的效果。
2.压延成型。
经过混炼后的橡胶胶团需要进行压延成型,将其变成一定厚度、宽度的橡胶带。
3.机械切割。
将橡胶带按照需要的尺寸进行机械切割,形成橡胶垫的初步形态。
4.模具压制。
将机械切割好的橡胶垫放入模具中进行压制成型,使其具有所需的形状和尺寸。
5.硫化处理。
硫化是橡胶垫生产中最重要的工艺环节之一,通过在高温高压下进行硫化反应,可以使橡胶材料的物理和化学性能得到优化和提升,从而提高橡胶垫的使用寿命和耐久性。
6.清洗包装。
经过硫化处理后的橡胶垫需要进行清洗和包装,以保证其质量和卫生。
同时,包装也是橡胶垫运输和储存的必要措施。
以上是橡胶垫的生产工艺流程,不同厂家和场合下的生产工艺可能有所不同,但总体来说,这些步骤是橡胶垫生产的必要环节,对橡胶垫的质量和性能起到至关重要的作用。
硅胶垫片的制备方法

硅胶垫片的制备方法全文共四篇示例,供读者参考第一篇示例:硅胶垫片是一种常用的密封材料,广泛应用于工业领域中的防漏、减震和隔热等方面。
制备硅胶垫片的方法有很多种,其中较为常见的就是涂布、浸渍和压制法。
下面将详细介绍这几种方法的制备步骤及其特点。
一、涂布法制备硅胶垫片涂布法是一种比较简单、易操作的硅胶垫片制备方法。
首先需要准备好硅胶材料,按照一定的比例混合均匀。
然后通过刮板或者刷子等工具将混合好的硅胶涂布到底材表面,在室温下自然干燥或者通过加热加速固化。
最后将硅胶与底材剪裁成所需尺寸即可。
涂布法制备硅胶垫片的优点是操作简单、成本低,可生产较大尺寸和复杂形状的垫片。
但由于涂布的均匀性和厚度难以控制,所以对硅胶垫片的性能要求较低时比较适用。
浸渍法是将底材浸泡在硅胶溶液中,使其表面吸附一层硅胶薄膜,再通过干燥和固化形成硅胶垫片的制备方法。
首先需要将硅胶溶液配置好,根据需要的硅胶厚度和性能要求选择合适的浓度。
然后将底材浸泡在硅胶溶液中,使其吸收足够的硅胶液。
最后通过干燥和固化完成硅胶垫片的制备。
浸渍法制备硅胶垫片的优点是硅胶涂布均匀、硅胶与底材结合牢固,适用于要求较高的硅胶垫片制备。
但缺点是生产周期较长、不适用于生产大批量硅胶垫片。
压制法是将硅胶材料与底材在一定的温度和压力下通过压制成型的硅胶垫片制备方法。
首先需要将硅胶材料与底材通过涂布或者浸涂的方式固定在一起。
然后将固定好的硅胶材料放入热压机中,在一定的压力和温度下进行压制成型。
最后将压制好的硅胶垫片冷却后进行剪裁加工即可。
压制法制备硅胶垫片的优点是制备速度快、产品质量稳定,适用于大批量生产硅胶垫片。
但需要专门的设备和操作技术,成本较高。
涂布法适用于简单的硅胶垫片制备,浸渍法适用于对硅胶均匀性要求较高的情况,压制法适用于大批量生产硅胶垫片的情况。
根据具体的要求和条件选择合适的制备方法,可以提高硅胶垫片的性能和使用效果。
希望本文对硅胶垫片的制备方法有所帮助。
8mm防滑绝缘垫技术数据
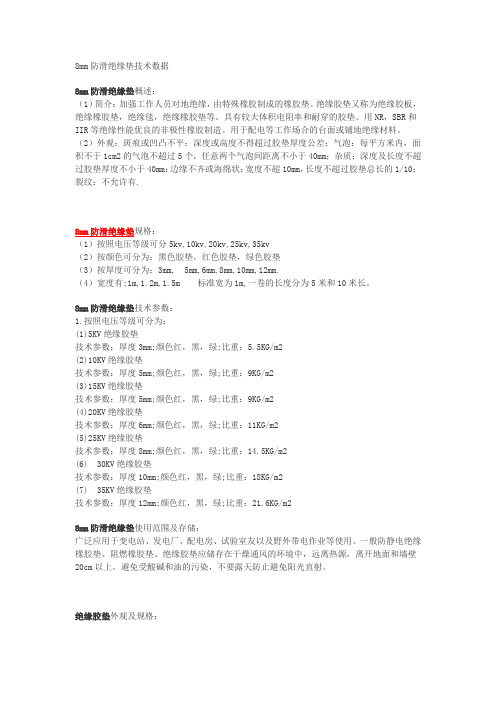
8mm防滑绝缘垫技术数据8mm防滑绝缘垫概述:(1)简介:加强工作人员对地绝缘,由特殊橡胶制成的橡胶垫。
绝缘胶垫又称为绝缘胶板,绝缘橡胶垫,绝缘毯,绝缘橡胶垫等。
具有较大体积电阻率和耐穿的胶垫。
用NR,SBR和IIR等绝缘性能优良的非极性橡胶制造。
用于配电等工作场合的台面或铺地绝缘材料。
(2)外观:斑痕或凹凸不平:深度或高度不得超过胶垫厚度公差;气泡:每平方米内,面积不于1cm2的气泡不超过5个,任意两个气泡间距离不小于40mm;杂质:深度及长度不超过胶垫厚度不小于40mm;边缘不齐或海绵状:宽度不超10mm,长度不超过胶垫总长的1/10;裂纹:不允许有.8mm防滑绝缘垫规格:(1)按照电压等级可分5kv,10kv,20kv,25kv,35kv(2)按颜色可分为:黑色胶垫,红色胶垫,绿色胶垫(3)按厚度可分为:3mm, 5mm,6mm,8mm,10mm,12mm.(4)宽度有;1m,1.2m,1.5m 标准宽为1m,一卷的长度分为5米和10米长。
8mm防滑绝缘垫技术参数:1.按照电压等级可分为:(1)5KV绝缘胶垫技术参数:厚度3mm;颜色红,黑,绿;比重:5.5KG/m2(2)10KV绝缘胶垫技术参数:厚度5mm;颜色红,黑,绿;比重:9KG/m2(3)15KV绝缘胶垫技术参数:厚度5mm;颜色红,黑,绿;比重:9KG/m2(4)20KV绝缘胶垫技术参数:厚度6mm;颜色红,黑,绿;比重:11KG/m2(5)25KV绝缘胶垫技术参数:厚度8mm;颜色红,黑,绿;比重:14.5KG/m2(6) 30KV绝缘胶垫技术参数:厚度10mm;颜色红,黑,绿;比重:18KG/m2(7) 35KV绝缘胶垫技术参数:厚度12mm;颜色红,黑,绿;比重:21.6KG/m28mm防滑绝缘垫使用范围及存储:广泛应用于变电站、发电厂、配电房、试验室友以及野外带电作业等使用。
一般防静电绝缘橡胶垫、阻燃橡胶垫、绝缘胶垫应储存在干燥通风的环境中,远离热源,离开地面和墙壁20cm以上。
开口垫圈生产工艺

开口垫圈生产工艺开口垫圈是一种在各种工业领域广泛应用的密封材料,其主要功能是填充和密封机械设备中的间隙,以防止液体、气体和固体颗粒的泄漏。
开口垫圈的生产工艺主要包括原材料准备、材料成型、加工加热、涂覆表面和品质检验等多个环节。
首先,原材料准备是生产过程中的第一步。
开口垫圈的主要原材料是高温耐压的橡胶,如氟橡胶、硅橡胶等。
在此环节中,需要根据产品的规格和要求准备足够的原材料,并将其进行分析和测试,确保原材料的质量符合标准。
接下来,是材料成型的过程。
这一步主要是通过橡胶模具将原材料进行成型,以形成开口垫圈的基本形状。
成型过程中需要注意模具的选择和橡胶与模具之间的适配性,以确保成型的垫圈具有较高的精度和光滑的表面。
然后,进行加工加热的环节。
这一步骤主要是将成型的垫圈放入高温箱中进行热处理,以改善其物理性能和耐高温能力。
在加热过程中需要控制温度和时间,以保证垫圈在加热过程中能够均匀地升温,并使垫圈的内部结构发生相应的变化。
再者,是涂覆表面的工序。
在此步骤中,通过涂覆涂料和粉末等材料,对垫圈的表面进行处理,以提高其使用寿命和耐磨性。
涂覆材料主要要根据产品的技术要求进行选择,并需要注意涂覆的均匀性和精确性。
最后,进行品质检验。
这一步骤是生产过程中十分重要的一环,通过对成品垫圈进行抽样检验和全检验,检测其尺寸、密封性能和外观质量等指标,以确保产品的合格性。
同时,在品质检验中还需要记录、收集和分析数据,以不断改进生产工艺和提高产品质量。
综上所述,开口垫圈的生产工艺包括原材料准备、材料成型、加工加热、涂覆表面和品质检验等多个环节。
每个环节都需要严格控制和操作,以确保最终产品的质量和性能。
这些工艺步骤的完善和优化,对于提高开口垫圈的生产效率和质量水平具有重要意义。
绝缘垫生产工艺
绝缘垫生产工艺绝缘垫是一种常用于电力设备、电气工程等领域的绝缘材料。
它由绝缘材料制成,用于在电工作业时隔离工人与工作环境之间的绝缘层。
绝缘垫的生产工艺相对简单,通常包括原材料准备、复合成型、加工成型和质量检测等步骤。
首先,绝缘垫的原材料主要包括橡胶和塑料等绝缘材料。
这些材料具有良好的绝缘性能和机械性能,能够有效保护使用者免受电击的伤害。
在生产之前,需要对原材料进行检验,确保其质量合格,符合相关标准和要求。
接下来是复合成型的步骤。
将经过橡胶或塑料粉碎研磨处理的原材料,经过一定比例的配料后,放入混炼机进行混合和捏合,使其形成均匀的糊状物。
然后将糊状物过滤和塑化,去除杂质和气泡,并使其具有一定的流动性。
然后将塑化后的糊状物通过挤出机进行挤压成型,形成厚度均匀的板材或片材。
加工成型是绝缘垫生产的关键步骤。
首先,将挤压成型的板材或片材放入冷却机中进行冷却,使其固化成型,并保持一定的强度和弹性。
冷却后,通过裁切机将板材或片材切割成指定尺寸和形状的绝缘垫。
然后,根据需要,在绝缘垫的边缘进行定制设计,例如添加扣环、加固边缘等。
最后是质量检测的环节。
对每批生产的绝缘垫进行抽样检查,主要检测其外观质量、尺寸精度、机械性能和绝缘性能等指标。
例如,外观质量检测包括检查绝缘垫表面是否有气泡、裂纹等缺陷。
尺寸精度检测主要检测绝缘垫的厚度、长度和宽度是否达到要求。
机械性能和绝缘性能检测主要检测绝缘垫的拉伸强度、冲击强度、电气绝缘性能等。
绝缘垫的生产工艺相对简单,但在生产过程中需要严格控制各个环节,以确保绝缘垫的质量和可靠性。
只有在质量检测合格的情况下,绝缘垫才能出厂并投入使用。
通过科学的生产工艺和质量控制措施,可以生产出高质量、可靠性好的绝缘垫,为电力设备的安全使用提供保障。
密封垫片生产工艺
密封垫片生产工艺
1. 密封垫片生产工艺概述
密封垫片是一种常见的工业元件,用于在机械设备的接合处防止
液体、气体、粉尘等物质的泄漏。
密封垫片的生产工艺主要包括材料
选型、模具制造、压制成型、加工与测试等环节。
2. 材料选型
密封垫片的材料种类繁多,包括合成橡胶、丁腈橡胶、氟橡胶、
硅橡胶、聚四氟乙烯、纤维素等。
材料的选择需要考虑到密封垫片的
使用环境、压力、温度等因素,并且需要符合相关标准和法规的要求。
3. 模具制造
为了让密封垫片能够具有一定的精度和一致性,必须要制造出适
合的模具。
模具制造的过程包括设计、加工、调试等环节,需要具有
精密的加工技术和优秀的工艺水平。
4. 压制成型
在模具的作用下,材料被压制成为密封垫片的形态。
这个过程需
要考虑到材料的流动性、模具的合理设计和合适的压力等因素,以确
保密封垫片的内部结构和外观形态都符合要求。
5. 加工与测试
密封垫片在成型后还需要进行后续的加工和测试,以确保其能够符合用户的使用要求。
加工包括打孔、裁剪、抛光等工序,测试包括密封性能、硬度、耐热性等方面的检测。
6. 小结
密封垫片的生产工艺需要具有一定的技术实力和质量管理能力,以确保产品的质量和稳定性。
制造商需要从材料、模具、压制、加工到测试等方面全面考虑,不断改进和优化生产过程,提高产品质量和市场竞争力。
橡胶加工工艺—橡胶注射工艺(高分子成型课件)
橡胶注射定义: 将胶料加热塑化成粘流态(熔融态),施以高压注射进入模具 热压硫化,然后开启模具取出成型制品的工艺过程。
三、橡胶的注射工艺
工艺特点
① 成型过程和硫化过程同时进行,工序简单,制品性能优异、质量稳 定; ② 胶料利用率高,可获得形状复杂的制品; ③ 自动化和半自动化程度高,劳动强度低,硫化速度快,生产效率高, 但需严格控制硫化工艺,否则胶料易过硫; ④属于周期性生产工艺,一次性投资大,模具结构复杂,加工成本高。 应用范围
6 成型周期—时间
高温快速硫化体系配方可大大缩短硫化时间。 厚制品硫化时由于制品内外层存在一定的温差,因此仍需适当延长硫化 时间保证制品质量。 一般情况下,充模时间与保压时间之和应小于焦烧时间,以防胶料在喷 嘴和模型流道处硫化,同时保证在硫化前完成压力均化过程,消除物料流 动中造成的内应力现象。
三、橡胶的注射工艺
适合于尺寸精度高、形状复杂、产量高的橡胶制品的生产,主要用于 密封圈、带金属骨架的模制品、减震垫及鞋类制品的生产。
三、橡胶的注射工艺
(一)注射过程及原理 1 注射成型过程
塑化
脱模
注射
热压 硫化
橡胶注射成型过程:塑化、注射、热压硫化,脱模。注射之前要求胶 料温度较低,防止发生焦烧,同时胶料应有较好的流动性,保证顺利注 模。注射保压后快速升温,且模具中内外层胶料温度均匀一致,提高 体系硫化效率。
三、橡胶的注射工艺
(二)注射工艺条件分析
5 喷嘴结构 喷嘴结构十分重要,喷嘴锥形部位斜度为30°-75°时,胶温上升最慢, 压力损失小。 减小喷嘴直径,注射时间延长,通过喷嘴摩擦生热高,易引起焦烧; 喷嘴直径增加,注射时间减小,焦烧危险性减小,但硫化时间增加。一 般情况下,喷嘴直径控制在2-6mm。
绝缘胶垫,绝缘橡胶垫,高压绝缘橡胶垫
-河北五星电力设备有限公司
A9崔跃骁
EVA胶垫
• •
• • • • • • • • • • • • • • •
一、EVA胶垫(绝缘胶板,绝缘橡胶垫,绝缘垫)应采用胶类绝缘材料制作。 二、绝缘垫分类:
1.按照电压等级可分为: (1)5KV绝缘垫 技术参数:厚度3mm;颜色 红,黑,绿 (2)10KV绝缘胶垫 技术参数:厚度5mm;颜色 红,黑,绿; (3)15KV绝缘垫 技术参数:厚度5mm;颜色 红,黑,绿; (4)20KV绝缘胶垫 技术参数:厚度6mm;颜色 红,黑,绿; (5)25KV绝缘垫 技术参数:厚度8mm;颜色 红,黑,绿; (6) 30KV绝缘垫 技术参数:厚度10mm;颜色红,黑,绿; (7) 35KV绝缘胶垫 技术参数:厚度12mm;颜色红,黑,绿;
12/21/2012
五星EVA胶垫
• 产品图片
12/21/2012
河北五星电力设备(石家庄)有限公司成功合作案例:
• • • • • • • • • • •
1、不全国电力系统的1758多家单位(变电所机房)进行合作,绝缘胶垫品质、 质量获得一致好评。 2、中国南水北调工程北京惠南庄泵站配电机房绝缘胶板工程的供货安装 3、石家庄五十四所军工仪器设备生产操作机房绝缘胶垫安装施工 4、石家庄国祥精密机械公司生产车间配电房、实验室绝缘胶板安装 5、中国水利水电七局绝缘胶板 6、柬埔寨大型民用船舶船上防滑绝缘胶板 7、廊坊供电公司 8、中国水利水电十三局 9.河北省委迎宾馆-----翠屏山迎宾馆的整个机房地面工程。 10.天津地铁一号线、二号线的机房地面工程。 11.邢台烟草公司物流中心地面工程。
12/21/2012
河北五星EVA胶垫
• 石家庄五星电力设备有限公司绝缘胶垫产品质量好,价格 低,受到广大新老客户的一致认可,五星电力设备公司在 北京水利水电七局的招标采贩项目中,五星中标绝缘胶垫, 全部绝缘胶垫采贩量,包括施工在内,全部由五星电力设 备公司中出,产品获得客户的认可。 • 河北五星电力向全国供应绝缘胶垫、绝缘胶板、标志桩、 挡鼠板、标志桩,为北京水利水电七局、山东中石油等多 家国营单位工应绝缘胶垫,产品质量获得客户的一致好评, 销量全国领先,欢迎广大客户来电!