GE Fanuc 0-15-16-18-21 All Version Backup Manual
FANUC 16i 18i 21i维修教程介绍.

BEIJING-FANUC北京发那科机电有限公司培训讲义FANUC 16i/18i/21i/0i-Model B 系统维修BEIJING-FANUCFANUC 16i/18i/21i- MODEL B系统连接 系统连接 FANUC 16i/18i/21i- MODEL B系统连接 系统连接与 LCD 显示单元集成一体 的超小超薄型 CNC- 内嵌以太网 (FS16i/18i)Internet CNC PC- FANUC 串行伺服总线 FSSB伺服电机 光缆 用于双安全检测的FSSB I/O 用于双安全检测的- FANUC I/O Link ( 2 通道 )总的 I/O点 : 输入 2048 / 输出 2048 点手持机床操作面板接口单元机床操作面板在强电柜内安装的I/O 模块 在强电柜内安装的 I/O LINK β 放大器手持机床操作面板BEIJING-FANUCFANUC 0i - MODEL B系统连接 系统连接结构控制单元 (单槽 单槽) 单槽 内置 I/O点 点 96 输入 64 输出 PC αi 主轴电机 以太网 10 base T/100 base TX Internet伺服放大器/主轴放大器 αi 伺服放大器 主轴放大器FANUC 串行伺服总线 (FSSB)光缆 7.2” 单色LCD 单色 9” 单色 CRT 8.4” 彩色 LCD 10.4” 彩色 LCD 具有 PC功能的显示单元 功能的显示单元FANUC I/O Link同样可以连接 βi 系列的放大器αis 伺服电机总的I/O点数 总的 点数 : 输入 1024 / 输出 1024 (包括内置 I/O) 包括内置机床操作面板分线盘I 分线盘 /O 模块I/O Link β 伺服放大器β 伺服电机BEIJING-FANUCFANUC 0i Mate -- MODEL B系统连接 系统连接 FANUC 0i Mate MODEL B系统连接 系统连接结构控制单元(单槽) 控制单元(单槽) βi 伺服主轴放大器βi 主轴电机FSSB 光缆 7.2 " LCD / 9 " CRT(单色 单色) 单色βi伺服放大器βiS 伺服电机FANUC I/O Link 点数: 最大 I/O 点数 输入 240 / 输出 160 I/O Link β伺服放大器 操作面板 (操作面板 安装 模块 模块) 操作面板 安装I/O模块 I/O 点数 输入 96 /输出 64 点数: 输出 βis 伺服电机 (1 轴) s 分线盘I/O 模块 分线盘BEIJING-FANUC FANUC LTDFANUC 16i/18i/21i- MODEL B系统规格 系统规格项目控制轴数 同时控制轴数 主轴数量 加工程序存储容量 PMC I/O 点数 内嵌以太网 双安全检测 AI 纳米高精度轮廓控制 AI 纳米轮廓控制 5 轴加工功能 刀具管理功能 Trouble Shooting Guidance ● ○ ○ ○ ○ ○ ● 16 i 8 6 4 5,120m m ( 2MB ) 18 i 6 → 8 4 3 21 i 4→ 5 → 4 22,560m m 1,280m m ( 1MB ) ( 0.5MB ) 0.033μs/步 ,64,000 步 μ 步 ● ○ ○ ○ ― ○ ● ○ ○ ― ○ ― ○ ●2048/2048 (I/O Link 2 通道 通道)BEIJING-FANUCFANUC 0i // 0i Mate -- MODEL B系统规格 系统规格 FANUC 0i 0i Mate MODEL B系统规格 系统规格● 标准 ○ 选择 × 无此功能0i -MODEL BA包 B包 4 2 i s,βi s α αi , βi αi , βi 7.2”LCD / 9”CRT (单色) 8.4” / 10.4”LCD (彩色) 具有 PC功能的显示单元0i Mate-MODEL B3(T;+Cs) 1 βi s βi βi 7.2”LCD / 9”CRT (单色)最大控制轴数 可连接的主轴电机的最大数量 可连接的伺服电机型号 可连接的主轴电机型号 可连接的放大器显示单元插补 存储容量/ 存储容量/ 程序数量 PMC 最大输入/ 最大输入/ 输出点数 伺服HRV控制 AI 先行控制 AI 轮廓控制 刚性攻丝 通用回退 外部触摸屏接口 宏执行器 MANUAL GUIDE 0i 磨削功能 I/O link β放大器连接 放大器连 以太网功能 新 简体中文显示 机床报警诊断 新 (故障诊断)直线、圆弧、螺旋线、圆柱、 直线、圆弧、螺旋线、圆柱、极坐标 640m/400 320m/400 SB7 SA1 1024/1024 点 (内置 I/O 96/64 点) HRV3 HRV1 ● × ○ ● ● ○(SNP 协议) ○(4MB / 2MB / 512KB) ○ ○ ○ ○ ● ○直线、圆弧、螺旋线、圆柱、 直线、圆弧、螺旋线、圆柱、 极坐标 640m/400 SA1 240/160 点 HRV1 ● × ● ● ○(SNP 协议) ○(512KB) ○ × ○ ( 1 轴) × ● ○BEIJING-FANUC新FANUC 0i -- P MODEL B系统 系统 FANUC 0i P MODEL B系统 系统FANUC 0i - P MODEL B 系统是用于冲床具有高可靠性和高精度的 CNC ,其最大控制轴 数为4轴 数为 轴。
FANUC 15i16i18i21i网络接口及PC功能简介
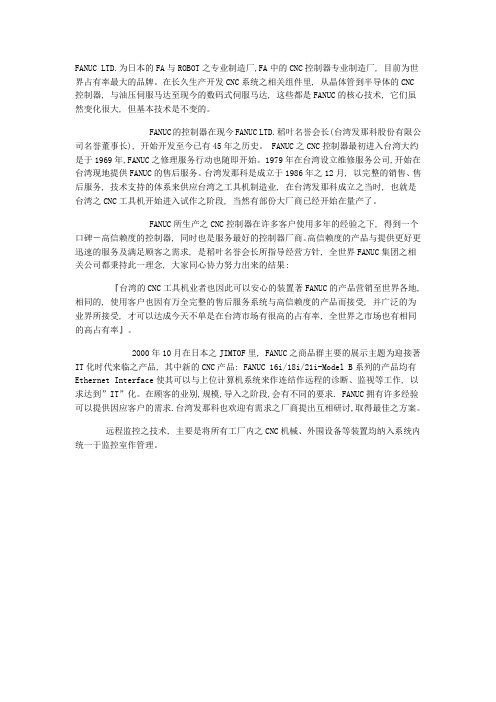
FANUC LTD.为日本的FA与ROBOT之专业制造厂,FA中的CNC控制器专业制造厂, 目前为世界占有率最大的品牌。
在长久生产开发CNC系统之相关组件里, 从晶体管到半导体的CNC控制器, 与油压伺服马达至现今的数码式伺服马达, 这些都是FANUC的核心技术, 它们虽然变化很大, 但基本技术是不变的。
FANUC的控制器在现今FANUC LTD.稻叶名誉会长(台湾发那科股份有限公司名誉董事长), 开始开发至今已有45年之历史。
FANUC之CNC控制器最初进入台湾大约是于1969年,FANUC之修理服务行动也随即开始。
1979年在台湾设立维修服务公司,开始在台湾现地提供FANUC的售后服务。
台湾发那科是成立于1986年之12月, 以完整的销售、售后服务, 技术支持的体系来供应台湾之工具机制造业, 在台湾发那科成立之当时, 也就是台湾之CNC工具机开始进入试作之阶段, 当然有部份大厂商已经开始在量产了。
FANUC所生产之CNC控制器在许多客户使用多年的经验之下, 得到一个口碑-高信赖度的控制器, 同时也是服务最好的控制器厂商。
高信赖度的产品与提供更好更迅速的服务及满足顾客之需求, 是稻叶名誉会长所指导经营方针, 全世界FANUC集团之相关公司都秉持此一理念, 大家同心协力努力出来的结果:『台湾的CNC工具机业者也因此可以安心的装置著FANUC的产品营销至世界各地, 相同的, 使用客户也因有万全完整的售后服务系统与高信赖度的产品而接受, 并广泛的为业界所接受, 才可以达成今天不单是在台湾市场有很高的占有率, 全世界之市场也有相同的高占有率』。
2000年10月在日本之JIMTOF里, FANUC之商品群主要的展示主题为迎接著IT化时代来临之产品, 其中新的CNC产品: FANUC 16i/18i/21i-Model B系列的产品均有Ethernet Interface使其可以与上位计算机系统来作连结作远程的诊断、监视等工作, 以求达到”IT”化。
FANUC机器人控制柜CRMA-15.16接线图(2)

FANUC机器⼈控制柜CRMA-15.16接线图(2)B-82725EN-2/05 CONNECTIONS4. PERIPHERAL DEVICE ANDEND EFFECTOR INTERFACES 4.3INTERFACE FOR PERIPHERAL DEVICES4.3.1Connection between the Main board (CRMA15, CRMA16) andPeripheral Devices-2NDEND EFFECTOR INTERFACESControl unit (peripheral device control interface A1)Connector pin No.CRMA15 (49、50)Peripheral deviceDI101 DI102 Receiver circuit3.3kRV CRMA15 (01) CRMA15 (02) DI103DI104 RV DI105 RV DI106 RV DI107 RV DI108 RV SDICOM1 RV DI109 RV DI110 RV DI111 RV DI112 RV DI113 RV DI114 RV DI115 RV DI116 RV DI117 RV DI118 RV DI119 RV DI120 RV SDICOM2RVCRMA15 (03) CRMA15 (04) CRMA15 (05) CRMA15 (06) CRMA15 (07) CRMA15 (08) CRMA15 (19) CRMA15 (09) CRMA15 (10) CRMA15 (11) CRMA15 (12) CRMA15 (13) CRMA15 (14) CRMA15 (15) CRMA15 (16) CRMA15 (22) CRMA15 (23) CRMA15 (24) CRMA15 (25) CRMA15 (20)CRMA15 (17、18)0VNOTEIn this diagram, common voltage of input devices is +24V.RVRV4. PERIPHERAL DEVICE ANDEND EFFECTOR INTERFACES CONNECTIONS B-82725EN-2/05Control unit (peripheral device control interface A1)DOSRC1Connector pin No.CRMA15 (31,32)Driver circuitDVDO101CRMA15 (33)Peripheral device+24V 0V+24V regulatedpower supplyLOADRELAYDO102 DO103 DO104 DO105 DO106 DO107 DO108DVDVDVDVDVDVCRMA15 (34)CRMA15 (35)CRMA15 (36)CRMA15 (37)CRMA15 (38)CRMA15 (39)CRMA15 (40)CRMA15 (17、18)LOADLOADLOADLOADLOADLOADLOAD 0VA maximum output current per DO point is 0.2 A.B-82725EN-2/05CONNECTIONS 4. PERIPHERAL DEVICE AND END EFFECTOR INTERFACES Control unit (peripheral device control interface A2)+24F Connector pin No.CRMA16 (49、50)Peripheral deviceXHOLD RESET Receiver circuit3.3kRVCRMA16 (01)CRMA16 (02)CRMA16 (03)CRMA16 (04)CRMA16 (05)CRMA16 (06)CRMA16 (07)CRMA16 (08)CRMA16 (19)CRMA16 (17、18).RVRVRVSTARTRVENBLPNS1PNS2PNS3PNS4SDICOM3RVRVRVRV0 VNOTEIn this diagram, common voltage of input devices is +24V4. PERIPHERAL DEVICE ANDEND EFFECTOR INTERFACES CONNECTIONS B-82725EN-2/05 Control unit (peripheral device control interface A2)Connector pin No.Pe ripheral device+24V 0VDriver circuitDO109DVCRMA16 (31、32)CRMA16 (41)+24V regulatedpower supplyLOADRELAYDO110DO111DO112DO113DO114DO115DO116DO117DO118DO119DO120 CMDENBL FAULT BATALMBUSY DVDVDVDVDVDVDVDVDVDVDVDVDVDVDVCRMA16 (42) CRMA16 (43) CRMA16 (44) CRMA16 (45) CRMA16 (46) CRMA16 (47)CRMA16 (48)CRMA16 (26)CRMA16 (27)CRMA16 (28)CRMA16 (21)CRMA16 (33)CRMA16 (34)CRMA16 (35)CRMA16 (36)LOADLOADLOADLOADLOADLOADLOADLOADLOADLOADLOADLOADLOADLOADLOADCRMA16 (17、18)0VA maximum output current per DO point is 0.2 A.DOSRC2B-82725EN-2/05 CONNECTIONS4. PERIPHERAL DEVICE ANDEND EFFECTOR INTERFACES The following shows the connector interface of the optional peripheral device cables on the peripheraldevice side.CONNECTIONS B-82725EN-2/054. PERIPHERAL DEVICE ANDEND EFFECTOR INTERFACES 4.3.2 Connection between the Process I/O Board MA and Peripheral DevicesNOTE1 The peripheral device connection cable is optional.2 The DOSRC3 pin of CRMA52A and CRMA52B supply power to the drivers (connect all pins).B-82725EN-2/05CONNECTIONS 4. PERIPHERAL DEVICE AND END EFFECTOR INTERFACES Control unit +24F Connector pin No.Peripheral device (Peripheral device controlinterface:B1)DI121RVDI122RVDI123RVDI124RVDI125RVDI126RVDI127RVDI128RVDI129RVDI130RVCOM1RV+24E B Common-level change-over setting pin (ICOM1) A CRMA52A (49、50)CRMA52A (01)CRMA52A (02)CRMA52A (03)CRMA52A (04)CRMA52A (05)CRMA52A (06)CRMA52A (07)CRMA52A (08)CRMA52A (09)CRMA52A (10) CRMA52A (17、18)0V0V(This common voltage is for 24V.)DOSRC3Driver circuitDVDO121Connector pin No.CRMA52A (31、32)CRMA52A (33)EXT24V+24V0V+24V regulatedpower supplyLOADRELAYDO122 DO123 DO124 DO125 DO126 DO127 DO128DV DVDVDVDVDVDVCRMA52A (34)CRMA52A (35)CRMA52A (36)CRMA52A (37)CRMA52A (38)CRMA52A (39)CRMA52A (40)CRMA52A (29、30)0VLOADLOADLOADLOADLOADLOADLOADEXT0VNOTEIn this diagram, common voltage of input device is 24V.4. PERIPHERAL DEVICE ANDEND EFFECTOR INTERFACES CONNECTIONS B-82725EN-2/05 Control unit +24F Connector pin No.Peripheral device (Peripheral device control interface:B2)DI131RVDI132RVDI133RVDI134RVDI135RVDI136RVDI137RVDI138RVDI139RVDI140RVCOM1RV+24E B ACRMA52B (49、50)CRMA52B (01)CRMA52B (02)CRMA52B (03)CRMA52B (04)CRMA52B (05)CRMA52B (06)CRMA52B (07)CRMA52B (08)CRMA52B (09)CRMA52B (10) CRMA52B (17、18)0VCommon-level change-over setting pin (ICOM2)(This common voltage isfor 24V.)DOSRC30VConnector pin No.EXT24V+24V0VDriver circuitDO129DVCRMA52B (31、32)CRMA52B (33)+24V regulatedpower supplyLOADRELAYDO130 DO131 DO132 DO133 DO134 DO135 DO136DV DVDVDVCRMA52B (34)CRMA52B (35)CRMA52B (36)CRMA52B (37)CRMA52B (38)CRMA52B (39)CRMA52B (40)CRMA52B (29、30)0VLOADLOADLOADLOADLOADLOADLOADEXT0VNOTEIn this diagram, common voltage of input device is 24V.CONNECTIONS 4. PERIPHERAL DEVICE AND END EFFECTOR INTERFACESThe following shows the connector interface of the optional peripheral device cables on the peripheral device side. ControllerCRMA 52A 010203040506070809101415161718DI 121 DI 122 DI 123 DI 124 DI 125 DI 126 DI 127 DI 128 DI 129 DI 130 0V0V19202122232425262728293031320VDOSRC3 Peripheral device A133 DO 12134 DO 12235 DO 12336 DO 12437 DO 12538 DO 12639 DO 12740 DO 128414243444546474849 24F50 24FCRMA 52B 01020304050607080910111213161718DI 131DI 132DI 133DI 134DI 135DI 136DI 137DI 1380V0V19202122232425262728293031320V0VDOSRC3 DOSRC3 Peripheral device A2 33 DO 12936 DO 132 37383940414243444546474849 24F50 24FDI 139DI 140 DO 134 DO 133 DO 135 DO 136。
FANUC 16(18)系统的一些维修技巧1

(十二) 显示程序名和种类 PRM3107#4(SOR) PRM3107#0(NAM)
(十三)MDI 的种类(小型和标准型) PRM3100#3(FKY)
(十四)9"CRT 的颜色显示信息 PRM3100#7
(十五)位置反馈系统的选择 PRM1815#1(OPTx) PRM2023 (速度反馈脉冲数) PRM2024 (位置反馈脉冲数)
PRM2084 (柔性齿轮比 N) PRM2085 (柔性齿轮比 M)
daifengchen
3、 也可以把 PRM 1023 设为-128; PRM1815#5(APC)=0。
4、 如果要使系统处于 INTERLOCK 状况。
PRM1005#7(RMB)
PRM0012#7(RMV)
PRM1005#6(MCC)
daifengchen
(三) 硬件 OT 是否使用。 PRM3004#4(OTH)
PRM2205#2 (PDMY) (Separate type PC)
PRM1800#1 (CVR)
MLK 信号接通
2、如果把 α 双轴伺服放大器当 α 单轴伺服放大器使用时
α双轴伺服 放大器 Type A 接口
Type B 接口
FSSB 接口
短接管脚
插头
短接 8 和 10 管 JVx 脚 短接 8 和 10 管 JSx 脚 短接 11 和 12 JFx 管脚
(八) 即使是在 MPG 方式下,也能进行 STEP FEED 操作。 7100#0(JH)
(九) 手动脉冲发生器是与系统直接相连还是通过 I/O LINK 相连。 PRM7100#0(IOL)
(十) INTERRM3003#0(ITL) *IT 信号 PRM3003#1(RILK) *RILK 信号 PRM3003#2(ITx) *IT1~*IT8 PRM3003#3 (DIT) +MIT1~-MIT4
GE系统简介(sis)
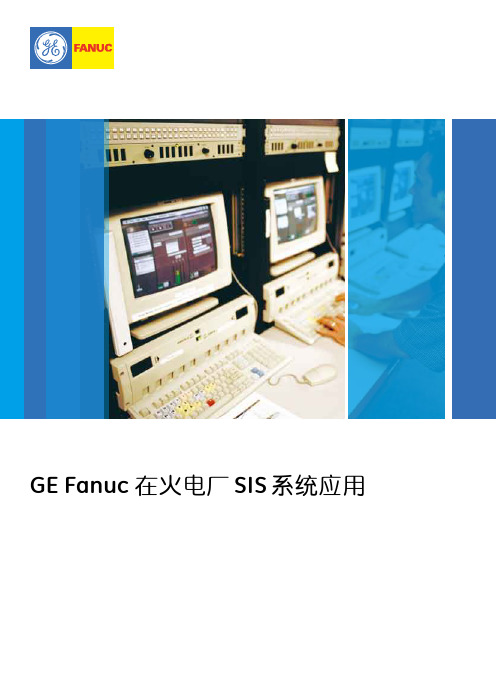
GE Fanuc 不仅仅是一个自动化产品的供应商,更是满足不 同客户需求的方案提供者。我们为客户提供良好的物流保 障和随时可及的售前、售后服务。更重要的是,我们的自 动化专家为您提供专业的项目咨询,从而确保您的自动化 系统是最优化的。
GE Fanuc 总部位于美国弗吉尼亚州夏洛茨韦尔,是 GE 工业系统集团的一部 分,它将 GE 家族广泛的全球性优势与满足本地的用户需求相结合,设计、开 发并维护用户在自动化方面的投资。
GE Fanuc 亚太公司业务遍及整个亚太地区,包括中国、韩国、日本、东南亚、 西亚和大洋洲。位于上海的亚太地区业务总部为这些地区提供市场、客户服 务、财务、订单处理和发货管理等服务。
GE Fanuc 公司介绍
GE Fanuc 公司介绍
GE Fanuc 公司由美国通用电气公司(GE)和日本 Fanuc 公司合资组建,提供自 动化硬件和软件解决方案,帮助用户降低成本、提高效率并增强其盈利能力。 凭藉适合于几乎每种工业门类的解决方案和服务,GE Fanuc 提供多样化的产品 和服务,范围包括控制器、嵌入式系统、高端软件、运动控制产品、操作员界 面产品、工业计算机和激光设备。
在 SIS 系统中为了提高可靠性,可以配置冗余历史数据库 服务器,将两台互为冗余的历史数据服务器通过双网冗 余星形拓扑结构以太网与电厂各生产系统进行通讯,读 取所有子系统的信息,形成 SIS 的历史数据数据库。
应用报表和数据分析部分是 SIS 系统应用集成功能计算分 析的核心,这部分功能同样要结合 MIS进行集成开发, 结 果 的 发 布 和 表 现 形 式 则 可 通 过 WEB服务器集中发布 完成。Proficy Real Time Information Portal 企业信息 门户技术(简称 RTIP),负责将 SIS 应用与 MIS 应用集成 为统一信息发布平台,所有生产实时信息可通过 RTIP 服 务器发布到厂级的管理信息网络上,供给厂长、总工及 生产科室等厂级用户浏览、分析。
fanuc 16i 18i 21i series 操作手册--附录c 启动系统说明书
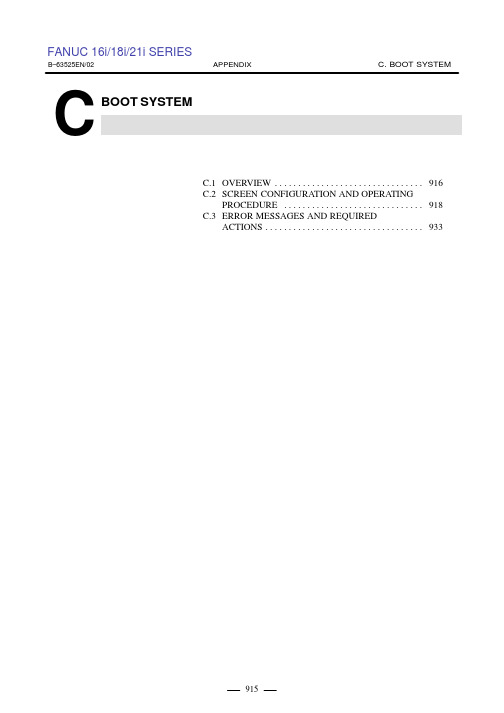
ACTIONS . . . . . . . . . . . . . . . . . . . . . . . . . . . . . . . . . . 933
918
FANUC 16i/18i/21i SERIES
C. BOOT SYSTEM
APPENDIX
B–63525EN/02
C.2.5 SRAM DATA BACKUP Screen
D Description
D Screen configuration
This screen is used to collectively save and restore parameters, programs, and other data, retained after the CNC power in SRAM is turned off, to and from a memory card.
(1) Registering a file in flash ROM
⋅ Reads a file from a memory card, in FAT format, into flash ROM. (2) Checking a file (series and edition) in flash ROM
When the boot system is first started, the MAIN MENU screen is displayed. This screen is described below :
FANUC-数控系统基本硬件及其连接PPT讲稿思维导图[PPT课件白板课件]
![FANUC-数控系统基本硬件及其连接PPT讲稿思维导图[PPT课件白板课件]](https://img.taocdn.com/s3/m/2e09451abe1e650e52ea9960.png)
目前国内市场常见的FANUC 数控系统:
FANUC 0C / 0D 系列
FANUC 0i – A / B / C / D系列
FANUC – 21 / 21i 系列 FANUC – 16 / 16i 系列 FANUC – 18 / 18i 系列 FANUC - 15 / 15i 系列 FANUC - 30i / 31i / 32i 系列
总有一款PPT 适合您
【最新出品\精心整理\倾情奉献\敬请珍惜】
目前国内市场常见的FANUC 数控系统:
FANUC 0C / 0D 系列 FANUC 0i – A / B / C / D系列 FANUC – 21 / 21i 系列 FANUC – 16 / 16i 系列 FANUC – 18 / 18i 系列 FANUC - 15 / 15i 系列 FANUC - 30i / 31i / 32i 系列
FANUC – 16 / 16i 系列
FANUC – 18 / 18i 系列
FANUC - 15 / 15i 系列 FANUC - 30i / 31i / 32i 系列
·用于控制 2 轴的小型车床, 取代步进电机的伺服控制;
FANUC Power – Mate 系列
·也可与其它数控系统 通过 I/O Link连接,用于上下料、刀 库等非插补轴控制。
FANUC 0C / 0D 系列 FANUC 0i – A / B / C / D系列 FANUC – 21 / 21i 系列 FANUC – 16 / 16i 系列
FANUC 0i – TD 车床用系统
FANUC 0i – MD 加工中心 / 铣床用系统
FANUC – 18 / 18i 系列 FANUC - 15 / 15i 系列 FANUC - 30i / 31i / 32i 系列 FANUC Power – Mate 系列
FANUC系统简介

主轴模块报警表
6)报警号:09 报警含义:主轴模块温度过高 7)报警号:19、20 报警含义:电源接通时U相、V相电流检测过高 8)报警号:24 报警含义:主轴模块与CNC通信异常 9)报警号:31 报警含义:主轴不能按指令旋转,主轴停止转动或转速非常低 10)报警号:56 报警含义:主轴散热风扇故障
伺服系统主轴模块连接图
CX1A: AC 200 V输入 CX1B: AC 200 V输出 CX2A: DC 24 V输入及急停信号接口 CX2B: DC 24 V输出及急停信号接口 JX4:主轴伺服信号检测板接口 JX1A:模块之间的连接接口,接电源模块的JX1B JX1B:模块之间的连接接口,接驱动模块的JX1A JY1:外接主轴负载表和速度表接口 JA7B:串行主轴输入信号接口 JA7A:用于连接第二串行主轴接口 JY2:连接主轴电机内装传感器和热敏电阻装置 JY3:主轴位置1转信号接口(磁传感器) JY4:主轴独立编码器接口 JY5:使用主轴为回转轴控制时,作为反馈接口
FANUC 系统硬件简介
FANUC FANUC FANUC FANUC
0系统的硬件连接 0i系统的硬件连接 0i系统的改进及特点 伺服系统简介
FANUC系统简介
高性能数控系统:
FS15-B、FS15i系统:4-24轴联动控制、纳米级加工精度的复合机床
中档性能数控系统:
FS16-C、FS16i、FS18C、FS18i系统:3-8轴控制、可实现5轴联动、0.0001mm精度加工机床
伺服模块报警信息表
报警信息 显示的 ← 位置
电源模块报警表
1)报警号:01 报警含义:主回路检测到过载、过电流或控制电压过 低 2)报警号:02 报警含义:冷却风扇停止转动或控制电压衰减 3)报警号:03 报警含义:主回路温升异常 4)报警号:04 报警含义:主回路直流环电压低 5)报警号:05 报警含义:输入电压异常
- 1、下载文档前请自行甄别文档内容的完整性,平台不提供额外的编辑、内容补充、找答案等附加服务。
- 2、"仅部分预览"的文档,不可在线预览部分如存在完整性等问题,可反馈申请退款(可完整预览的文档不适用该条件!)。
- 3、如文档侵犯您的权益,请联系客服反馈,我们会尽快为您处理(人工客服工作时间:9:00-18:30)。
Automation Inc. ______________________________________________________________________________________Fanuc CNC Backup I nstruction Manual1 Table of ContentsTable of Contents (1)Procomm Plus® version 4.8 Configuration (3)Serial Cable Connection (6)Memory Card Usage (8)What Data Can be Archived (9)CNC Parameter settings for RS-232 communications (11)CNC Parameters Related to Memory Card Communications (13)How to Backup and Restore ALL Data in your CNC (14)Series 0 models A/B/C/D (14)Using the RS-232 interface (14)Series 16/18/21 models A/B/C, Powermate models D/H (16)Using the RS-232 interface (16)Series 15 models A/B (20)Using the memory card (20)Using the RS-232 interface (26)Series 16i/18i/21i/0i models A/B, Powermate i models D/H (29)Using the memory card (29)Using the RS-232 interface (34)Series 15i model A (38)Using the memory card (38)Using the RS-232 interface (43)How to Backup and Restore Programs in your CNC (47)Series 0 models A/B/C/D (47)Using the RS-232 interface (47)Series 16/18/21 models A/B/C, Powermate models D/H (47)Using the RS-232 interface (48)Series 15 models A/B (49)Using the RS-232 interface (49)Series 16i/18i/21i/0i models A/B, Powermate i models D/H (50)Using the memory card (50)Using the RS-232 interface (54)Series 15i model A (55)Using the RS-232 interface (55)How to Backup and Restore CNC Parameters in your CNC (57)Series 0 models A/B/C/D (57)Using the RS-232 interface (57)Series 16/18/21 models A/B/C, Powermate models D/H (58)Using the RS-232 interface (58)Series 15 models A/B (59)Using the RS-232 interface (59)Series 16i/18i/21i/0i models A/B, Powermate i models D/H (60)Using the memory card (60)Using the RS-232 interface (63)Series 15i model A (64)2Using the RS-232 interface (64)How to Backup and Restore PMC Parameters in your CNC (66)Series 16/18/21 models A/B/C, Powermate models D/H (66)Using the RS-232 interface (66)Series 15 models A/B (67)Using the RS-232 interface (67)Series 16i/18i/21i/0i models A/B, Powermate i models D/H (68)Using the memory card (68)Using the RS-232 interface (70)Series 15i model A (72)Using the RS-232 interface (72)Open Systems Backup and Restore using the Basic Operation Package (BOP) (74)References (75)3 Procomm Plus® version 4.8 ConfigurationThe following setup information applies to ProComm Plus 2.0® for Windows 95/98 through version 4.8 for Windows 95/98/2000/XP.NOTE:It is possible that you may experience timeouts when uploading a program using drip feed to the CNC while using ProComm Plus Version 4.8. ProComm's default delay time is to wait 20 seconds after an XOFF command and then abort. Symantic has provided a solution to this on their web pages. For further explanation, please visit their Tech Support site at /techsupp/index.html, enter a search for that version of Procomm product and open the FAQ section for that product.1. After installing ProComm Plus®, launch the application by double clickingon the appropriate icon or selecting the appropriate item from the Startbutton. If you need any additional help on installing or launching theapplication, please refer to the ProComm documentation thataccompanied the software. This is the main screen of ProComm Plus®.Clicking the SETUP button will bring up the screens used to change thecommunications parameters.2. By clicking the SETUP button the following screen appears. Click on the“System" tab followed by the "Modem Connection" button. Next, select"direct connect – Com1" from the "Current Modem / Connection" dropdown box. To configure the Com1 port, click on the "Modem/ConnectionProperties…" button.43. After selecting the "Modem/Connection Properties…" button, youshould see the following screen. Set your PC to match the following:5 Click on "OK" to accept the settings and close the window4. Clicking on the "Data" tab of the Setup screen allows you to set the typeof transfer to be used. Click on the "Transfer Protocol" button. To communicate with the CNC, you should select ASCII from the "Current Transfer Protocol" drop down box. Set the remaining fields in this window to match those shown below.Click on "OK" to accept the settings and close the window6Serial Cable ConnectionThe GE Fanuc CNC controls have a minimum of one serial communication port available for communications. This port is designed to conform to the basic requirements of the EIA232C standard. Connection to an EIA232 or EIA574 compliant device can be accomplished using a null modem cable. Communication Cable DiagramsEIA232C Null Modem CableThis cable, utilizing a DB25P connector to a DB25S connector, uses Control Codes also known as Software Handshaking. Controls and PG systems use serial inter-face.NOTE:Pin #25 has 24 volts power supply on it. Do not use for normal interface connection or damage to the control may occur.EIA232C to EIA574 Null Modem CableThis cable can be used for interfacing between IBM-compatible computers and GE Fanuc controls. This cable uses a DB25P connector to a DB9S connector. This is the most commonly used cable for communications and is available from GE Fanuc or easily fabricated.7DB25P (male)RD SD SG RS CS CD ER DR RD SG RS CS DR CD ER SDFG: Frame ground SD: Send data RD:Receive data RS: Request to send CS: Clear to sendDR: Data set ready SG: Signal ground ER: Equipment readyCD: Received line signaldetector8Memory Card UsageThree types of memory cards can be used with our CNC and Power Matecontrols:1. ATA Flash Rom2. SRAM (Static Ram Access Memory), which are battery-backed.3. FlashROM (called FROM for the rest of this document), which do notrequire battery backup.Which type of memory card do you need? The Pros and Cons of each type ofcard are given below. We recommend SRAM or ATA Flash. The SRAM workswith a larger variety of controls, but requires a small battery on the card to retainits memory and should not be used as a permanent storage device. ATA Flashis lower cost and can be used for permanent storage of backup files, but is newertechnology and therefore works with a smaller number of controls.Memory Card Type ATA Flash SRAM FROMWorks with i series controls Yes Yes Yes Works with 15/16/18/21-B and 20/21-A controls No Yes YesWorks with PowerMate-C/D/E/F/H/I controls No Yes YesCan read/write from a PC Yes Yes NoFast Write Time Yes Yes NoPlug and Play for WIN95 and newer Yes No NoLow Cost Yes No YesRequires battery to retain backup data No Yes NoFiles can be deleted individually Yes Yes NoCan be formatted on PC Yes Yes NoRequires special drivers No No YesGE Fanuc Part Numbers 44A725977-G09 (8MB) 44A725977-G01 (2MB) 44A725977-G02 (4MB)44A725977-G10 (16MB)44A725977-G03 (4MB)What Data Can be ArchivedThe system software that operates GE Fanuc CNC controls is stored in EPROM. They are essentially fixed and unchangeable. The CNC is shipped from GE Fanuc ready for the machine builder to customize for his application. The files needed for final operation are contained in non-volatile RAM, or battery backed-up RAM. The data stored here can be lost for a variety of reasons and therefore must be saved externally on permanent media. It is recommended that all user data be kept both on a computer diskette or CD-ROM as well as on paper to ensure that it will be available in time of need.User FilesLong term archival:1. CNC Parameters (including servo parameters)2. Pitch Error Compensation (if used)3. PMC Parameters (or Diagnostic Data on FS-0 Controls)This data seldom changes after installation of the machine tool. However, the archive must be updated whenever changes are madeData that changes regularly.1. Tool Offsets2. Work Offsets3. Dynamic Tool Offsets4. Macro Variables5. Tool Form Data6. CAP Tool Data7. CNC Part ProgramsThis data should be backed up any time maintenance is performed that might cause a memory loss.Data normally stored in EPROM but may be stored in RAM format:1. PMC ladder program2. Macro executor programsFile NamingWhen user data is saved to a diskette, it should be remembered that in an average plant there may possibly be multiple machines and controls of the same model. This means that there will be multiple versions of this data. There should be a complete set for each machine on which a GE Fanuc control is applied. It is important to realize that even identical machines may have different parameter data based on any number of factors. The existence of so much similar data can easily cause problems if not addressed from the beginning, so some type ofsystem for naming and archiving files must be created. For example, when backing up the data, you will be asked what to name the resulting data file on disk. GE Fanuc recommends that you use a unique name such as the machine serial number, brass tag or asset number, combined with an extension that helps label the type of data being backed up. By using the first eight (8) characters to identify the machine and the extension to identify the file type, much confusion can be avoided. For example, the filename C could be used to name the CNC parameter file for machine BT156679.CNC Parameter settings for RS-232 communicationsThe parameter tables on the following page can be used as a reference when setting up the various models of CNC control for RS-232 communications. These parameters tell the control which port to use and the device type (in this case, RS-232). These parameters also determine that the number of data bits will be “8”, the number of stop bits “2”, that “EVEN” parity will be used as well as a baud rate of 4800bps set. These settings coincide with the ProComm configuration explained earlier in this manual.Additionally, these parameters also unlock the custom macro protection, allowing the download of the macro programs. When setting CNC parameters ensure that the Parameter Write Enable (PWE) setting is set to “1” on the control settings screen.PWEPWE Setting from series 16i-MA controlControl Series 10/11/12/15A/15B/15i Parameters Port 1 Port 2 P 0000 ****1010****1010 P 0020 12 P 0021 12 P 0011 ******00******00 P 2201 ******00******00 P 5001 1P 5002 2 P 5110 8P 5111 2P 5112 10P 5120 8 P 5121 2 P 5122 10 Control Series 0A/0B/0C/0DParameter Port 1 Port 2 P 0000 1******1P 0010 ***0*******0****P 0038 01******P 0050 1******1P 0250 10P 0251 10P 0552 10P 0553 10TVON 00ISO 0,12I/O 11PWE 11TAPEF 00Control Series 16/18/20/21-ABCi / 0iParameter Port 1 Port 2P 0000 ******10******10P 0020 0,12P 0101 1***0**1P 0102 3P 0103 10P 0111 1***0**1P 0112 3P 0113 10P 3202 ***0***0***0***0CNC Parameters Related to Memory Card Communications1. Select the MDI mode on the operator panel for the CNC.2. Go to the Offset/Setting screen.3. Set I/O channel =4.or1. Select the MDI mode on the operator panel for the CNC.2. Place the CNC into an Emergency Stop condition.3. Set your control so that Parameter Write is enabled.4. For series 18i set parameter 20 = 4, series 15i set 20=4.These settings will let you upload and download files to the cards the same as you would to a PC and there is also an additional menu called all IO with additional I/O functionality.IO Channel SettingIO Channel Setting from series 16i-MA controlHow to Backup and Restore ALL Data in your CNCOne of the most common procedures on CNC controls during maintenance is to backup all of the data possible before working on a CNC system. In this manner, a maintenance person can easily restore the control to the original state should a problem be encountered during the maintenance activity.Series 0 models A/B/C/DThis series of controls is restricted to using the RS-232 interface for all data backup and restore operations.Using the RS-232 interfaceTo Transfer Programs from CNC to PCFrom the CNC Side, do the following:1. Select EDIT mode.2. Select the PROGRAM screen.3. Depress I/O key.4. Prepare the PC to receive file (See appropriate section on ProComm forreceiving a file on the PC).5. To output an individual program, enter the Letter O and the part programnumber OR to output all programs enter –9999.To Transfer Program from PC to CNCFrom the CNC side, do the following:1. Select EDIT mode.2. Select the PROGRAM screen.3. Depress I/O softkey.4. Depress READ softkey.5. Send file from PC (See appropriate section on ProComm for sending fromPC).To Transfer Parameters from CNC to PCFrom the CNC side, do the following:1. Select EDIT mode.2. Select the PARAMETER menu.3. Prepare PC to receive the file (See appropriate section on ProCommfor receiving a file on the PC).4. Hold down EOB key and simultaneously depress OUTPUT STARTkey.NOTE:Failure to press the EOB key and OUTPUT START will result in an incomplete parameter file being downloaded.Transfer Parameters from PC to CNCFrom the CNC side, do the following:1. Set Parameter Write Enable (PWE) to 1.2. Select EDIT mode.3. Select the PARAMETER menu.4. Depress INPUT key.5. Send the parameter file from the PC (See appropriate section onProComm for sending from PC).6. When the transfer is complete, turn CNC OFF and back ON to use thenew parameter set. Also verify that PWE is set to 0.NOTE:To upload and download PMC parameters (Diagnostics) and offsets, the procedures are the same as for the system parameters. The only difference is that you must be on the CNC Diagnostic Page for transferring PMC parameters and the Offset Page for transferring offsets.Series 16/18/21 models A/B/C, Powermate models D/HThe primary method for archiving data from this series of control is through the RS-232 port. Newer models B/C controls may have PCMCIA memory card slots located in the control rack and are accessible through the boot mode. For instructions on using the boot mode backup procedures for the model A/B controls, see the section for 16i/18i/21i/0i controls.Using the RS-232 interfaceFirst set the CNC parameters as per the settings in the section labeled “CNC Parameter Settings for RS-232 Communications”Punching CNC Parameters (CNC --> PC)Connect the cable to the computer and the serial port on the CNC.Set up the computer in accordance with "Procomm Plus® Version 4.8configuration."Set up the CNC for communications as per “CNC Parameter Settingfor RS-232 Communication.”Perform the following steps on the PC and CNC as follows:PC Launch Procomm Plus 4.8PC Select File Receive from the toolbarPC Designate a name and directory for the saved dataCNC Select EDIT mode.CNC Press SYSTEM key.CNC Hit softkeys [PARAM], [OPRT], [+], [PUNCH],[EXEC].(You will see the parameters scroll up on the PC screen.)(The CNC will flash OUTPUT on the lower section of the CRT.)Reading CNC Parameters (CNC <-- PC)Connect the cable to the computer and the serial port on the CNC.Set up the computer in accordance with "Procomm Plus® Version 4.8configuration."Set up the CNC for communications as per “CNC Parameter Setting forRS-232 Communication.”Perform the following steps on the PC and CNC as follows:PC Launch Procomm Plus 4.8CNC Select MDI mode and press ESTOPCNC Set PWE to 1.CNC Press SYSTEM key.CNC Hit softkeys [PARAM], [OPRT], [+], [READ], [EXEC].PC Select File Send from the toolbarPC Designate the name and directory for the file to send(You will see the parameters scroll up on the PC screen.)(The CNC will flash INPUT on the lower section of the CRT.) CNC Power the CNC off then on to have the new parameters takeeffect.Punching CNC Part Programs (CNC --> PC)Connect the cable to the computer and the serial port on the CNC.Set up the computer in accordance with "Procomm Plus® Version 4.8configuration."Set up the CNC for communications as per “CNC Parameter Settingfor RS-232 Communication.”Perform the following steps on the PC and CNC as followPC Launch Procomm Plus 4.8PC Select File Receive from the toolbarPC Designate a name and directory for the saved dataCNC Select EDIT mode.CNC Press PROG keyCNC To output current program hit softkeys [PRGRM], [OPRT], [+],[PUNCH],[EXEC]CNC To output all programs input O-9999 and hit [+],[PUNCH], [EXEC].(You will see the program scroll up on the PC screen.)( The CNC will flash OUTPUT on the lower section of theCRT.)Reading CNC Part Programs (CNC <-- PC)Connect the cable to the computer and the serial port on the CNC.Set up the computer in accordance with "Procomm Plus® Version 4.8configuration."Set up the CNC for communications as per “CNC Parameter Settingfor RS-232 Communication.”Perform the following steps on the PC and CNC as follows:PC Launch Procomm Plus 4.8CNC Select EDIT mode and turn program protect key off.CNC Press PROGRAM key.CNC Hit softkeys [PRGRM],[OPRT], [+], [READ], [EXEC].PC Select File Send from the toolbarPC Designate the name and directory for the file to send(You will see the parameters scroll up on the PC screen.)(The CNC will flash INPUT on the lower section of the CRT.) Punching PMC Data (CNC --> PC)Connect the cable to the computer and the serial port on the CNC.Set up the computer in accordance with "Procomm Plus® Version 4.8configuration."Perform the following steps on the PC and CNC as follows:PC Launch Procomm Plus 4.8PC Select File Receive from the toolbarPC Designate a name and directory for the saved dataCNC Select EDIT mode.CNC Go to the PMC side and select I/O.CNC Select Channel 1 for Port 1 and Channel 2 for Port 2.CNC Set Device to OTHERSCNC Set Data kind to type desired --- ALL/LADDER/PARAM. SetFunction to WRITE.CNC Press the SPEED softkey.CNC Select 4800 Baud (depending on computer setup).CNC Select Parity 0, Stop bits 1, Write code ASCII.CNC Press < and EXEC softkeys to initiate download.(The CNC screen will flash executing and count up untilcomplete.)Reading PMC Data (CNC <-- PC)Connect the cable to the computer and the serial port on the CNC.Set up the computer in accordance with "Procomm Plus® Version 4.8configuration."PC Launch Procomm Plus 4.8CNC Select MDI mode and press ESTOPCNC Set PWE to 1.CNC Go to the PMC side and select I/O.CNC Select Channel 1 for Port 1 and Channel 2 for Port 2CNC Set Device to OTHERS.CNC Set Function to READ.CNC Press the SPEED softkeyCNC Select 4800 Baud.CNC Select Parity 0, Stop bits 1.CNC Press < and EXEC softkeys. (Executing should flash)PC Select File Send from the toolbarPC Designate the name and directory for the file to send (You will see the parameters scroll up on the PC screen.)(The CNC will flash INPUT on the lower section of the CRT.)Series 15 models A/BThe series 15 model A control is restricted to using the RS-232 interface whereas the series 15 model B control additionally offers a PCMCIA memory card slot in the control rack. For more information refer to GE Fanuc Manual GFZ-62075 Series 15/150 Model-B Maintenance Manual.Using the memory card(Not available on series 15 model a)The table below lists the functions and corresponding memory card types that can be used. Cards must be of TYPE 1 or 2 as defined in the Personal Computer Memory Card International Association (PCMCIA) standard, version 2.0 or later, or the Japan Electronic Industry Development Association (JEIDA) standard, version 4.1 or later. The format conforms to the DOS FAT file system. The memory card has a maximum storage capacity of 32M bytes.Accessing the Boot SystemInsert the SRAM Memory card into the PCMCIA slot in the control rack.Turn the power on while holding down the page up/down keysNote: If you are using a 9” small MDI unit, turn the power on while holding down cursor keys up and down keys instead of the page up/down keys.SYSTEM DATA SAVEThe SYSTEM DATA SAVE screen enables the saving of user files, such as PMC ladder files. System files, such as executive software cannot be saved. To save SYSTEM DATA use the following procedure.Press a cursor up/down key to choose the desired function.Position the cursor to a desired function, then press the INPUT/INSERT key.The ROM files in flash memory are listed together with the number of management units (128KB management units) in each file.Use the cursor keys to position the cursor to the file to be saved to the memory card. Then, press the INPUT/INSERT key.The INPUT FILE NAME (CAN: RESET) message appears in the message field. Enter the name of the desired file on the memory card, then press the INPUT/INSERT key.To abandon saving, press the RESET key. To end the processing, position the cursor to END, then press the INPUT/INSERT key. The main menu appears again.SRAM DATA BACKUPTo save a complete image of the data stored in SRAM memory, select FILE DATA BACKUP from the System Monitor screen (selection 4).From the File Data Backup screen, select STORE FILE. To execute batch restoration, select LOAD FILE. To terminate the processing, select END. To select the processing, press a cursor key to position the cursor, then press the INPUT/INSERT key.When the batch saving or restoration of a file is selected, the size of the system’s backup RAM is displayed on the screen. To execute the selected processing, press the INPUT/INSERT key. To cancel the processing, press the CAN key. (See the detailed description given below.)NOTEThe backup data is saved to file FILEx.BAK, where x is a value of 1 to 4. The original data can be saved in up to four files. If a single memory card cannot hold all the original data, the data can be saved using up to four memory cards. Existing FILEx.BAK files on a memory card may be overwritten if a file of thesame name is stored. The names of the files already on the memory card can be listed in the FILE DIRECTORY field of the SYSTEM DATA LOADING screen.To execute the batch saving of backup data, perform the following steps:1. Select the STORE FILE function on the initial screen.2. When the SET IC CARD NO.1 & HIT INPUT KEY message appears inthe message field, mount the first memory card. Then, press theINPUT/INSERT key. To cancel the processing, press the RESET key.The initial screen appears again.3. While data is being saved, the STORE TO IC–CARD message blinks.Once saving has been completed, the STORE FILE COMPLETE andHIT INPUT KEY messages appear in the message field. When theINPUT/INSERT key is pressed, the initial screen appears again. If thefirst memory card cannot hold all the data to be saved, the SETIC/CARD NO.2 & HIT INPUT KEY message appears in the messagefield. Mount the second memory card without turning the power off,then press the INPUT/INSERT KEY.4. The backup data can be saved using up to four memory cards byperforming step (3) repeatedly. If four memory cards cannot hold allthe data, the FILE DATA SIZE ERROR and HIT INPUT KEYmessages appear in the message field. When the INPUT INSERT keyis pressed, the initial screen appears again.NOTEOnce batch saving starts, requests to replace the memory card are repeated until all the backup data has been normally saved (using up to four memory cards). To stop the processing, press the RESET key while the SET IC CARD NO.x & HIT INPUT KEY message is displayed.Data is stored on the memory cards under the following file names:First memory card: FILE1.BAKSecond memory card: FILE2.BAKThird memory card: FILE3.BAKFourth memory card: FILE4.BAKNote that a file on a memory card can be overwritten. If the specified name of a file to be saved duplicates that of a file already on the card, the old data will be overwritten.To execute the batch restoration of backup data, perform the following steps:1. On the initial screen, select the LOAD FILE function.2. The SET FILE1.BAK & HIT INPUT KEY message appears in themessage field. Mount the first memory card containing FILE1.BAK,then press the INPUT/INSERT key. To cancel the processing, pressthe RESET key. The initial screen appears again.3. While data is being restored, the LOADING FROM IC–CARD messageblinks. Once data restoration has been completed, the LOAD FILECOMPLETE and HIT INPUT KEY messages appear in the messagefield. When the INPUT/INSERT key is pressed, the initial screenappears again.4. Backup data stored using up to four memory cards can be restored byperforming step (3) repeatedly. If all the required data cannot berestored from all of the four memory cards, the FILE DATA SIZEERROR and HIT INPUT KEY messages appear in the message field.When the INPUT/INSERT key is pressed, the initial screen appearsagain.NOTE:The function for saving or restoring a file in batch mode of the boot system assumes that the backup RAM (file SRAM) used for saving and that used for restoration are of the same size. So, this function should be used in the following cases:1. To restore a file when file all clear must be executed (the file SRAMmodule is not replaced)2. To restore a file when the file SRAM module must be replaced andwhen the size of the new backup RAM is the same.If this function is used for any other purpose, such as restoring SRAM into a module of a different size after an upgrade, file restoration may not be performed correctly. In the case of a memory upgrade, use the RS-232 option to backup and restore the control. Similarly, if an error (a RAM parity error, for example) is found in the contents of the backup RAM during batch saving, file restoration may not be performed correctly and the RS-232 method must be used.Using the RS-232 interfacePUNCHING CNC PARAMETERS (CNC --> PC)Connect the cable to the computer and the serial port on the CNCSet up the computer in accordance with "Procomm Plus® Version 4.8configuration."Set up the CNC for communications as per “CNC Parameter Settingfor RS-232 Communication.”Perform the following steps on the PC and CNC as follows:PC Launch Procomm Plus 4.8PC Select File Receive from the toolbarPC Designate a name and directory for the saved dataCNC Go into EDIT mode.CNC Press the <, SERVICE, CHAPTER, PARAMETER, >, PUNCH,ALL keys.( The CNC will flash PNCH on the lower portion of the CRT. )( The PC will display the text and count lines until finished.) READING CNC PARAMETERS (PC --> CNC)Connect the cable to the computer and the serial port on the CNC.Set up the computer in accordance with "Procomm Plus® Version 4.8configuration."Set up the CNC for communications as per “CNC Parameter Settingfor RS-232 Communication.”Perform the following steps on the PC and CNC as follows:PC Launch Procomm Plus 4.8CNC Go into EDIT mode.CNC Press ESTOP.CNC Press the <, SERVICE, CHAPTER, PARAMETER, >, READ,ALL keys.PC Select File Send from the toolbarPC Designate the name and directory for the file to send(You will see the parameters scroll up on the PC screen.)(The CNC will flash INPUT on the lower section of the CRT.) CNC Power the CNC off and then on to have the new parameterstake effect.。