车床刀具路径
车床挑扣操作方法

车床挑扣操作方法车床挑扣操作方法,主要分为以下几个步骤:第一步,准备工作1. 准备好所需的车床挑扣工具,包括挑扣刀、挑床、刮床、车床刀具等。
2. 将需要进行挑扣的工件固定在车床上,确保工件牢固稳定。
第二步,定位和测量1. 根据需要挑扣的部位,在工件上进行标记,确定挑扣的具体位置和范围。
2. 使用测量工具(如游标卡尺或卡尺)测量被挑扣面的尺寸和凹槽的深度。
第三步,挑扣刀的选择和安装1. 根据工件上被挑扣面的形状和尺寸,选择合适的挑扣刀。
挑扣刀通常有不同形状和尺寸的刀具,根据不同的挑扣需求进行选择。
2. 将挑扣刀安装到车床上,确保刀具可以有效地切削和清除被挑扣面。
第四步,操作车床,进行挑扣1. 打开车床的电源,启动车床并选择适当的转速。
2. 使用车床手柄或控制面板控制车床移动,将挑扣刀准确地移动到被挑扣面上的标记位置。
3. 当刀具接触到工件时,以适当的速度和深度移动车床手柄或控制车床面板,确保刀具准确切削工件。
4. 按照预定的路径进行挑扣,同时观察被挑扣面的切削情况,确保切削平稳、均匀。
如果有需要,可以适当调整切削速度、深度和方向。
5. 根据需要,可以使用刮床或挑床对挑扣面进行修整和清理,确保挑扣面的平整度和光洁度。
第五步,完成挑扣操作1. 当挑扣操作完成后,关闭车床电源,停止车床运转。
2. 用刮床或固定在车床上的工具清理工件上的切削屑和污垢。
3. 检查挑扣的成果,确保挑扣面的细节和要求满足相关标准和要求。
总结:车床挑扣是一项技术要求高、操作要求准确的工艺步骤。
要注意选择合适的刀具和车床转速,确保切削操作的准确性和安全性。
在操作过程中要小心谨慎,保持集中注意力,以免发生意外。
挑扣操作完成后,要对工件进行检查和整理,确保挑扣面的质量和精度。
数控车床的操作步骤及操作教程

数控车床的操作步骤及操作教程1. 背景介绍数控车床是一种自动化工具,可以用于加工各种材料的工件。
与传统车床相比,数控车床具有更高的精度和效率。
在使用数控车床之前,需要了解其操作步骤和操作教程,以确保安全和提高工作效率。
2. 数控车床的操作步骤步骤1:开机准备•确保车床电源已接通,以及紧急停车按钮在可用状态。
•检查各个操作按钮、手轮、刀架、主轴等部件是否正常运转。
步骤2:加载工件和刀具•将要加工的工件固定在车床工作台上,并确认其位置和夹紧方式。
•按照加工要求,选择合适的刀具,并将刀具安装在刀架上。
步骤3:设定坐标轴•使用数控车床的控制面板或操作界面,设定加工工件的坐标轴起点和终点。
•确保坐标设定准确,并进行必要的校正。
步骤4:编写加工程序•使用数控编程软件,编写加工工件的程序。
•根据加工要求,设定刀具路径、转速、进给速度等参数。
步骤5:设定加工参数•根据工件材料和加工要求,设定合适的切削深度、切削速度等加工参数。
•确认加工参数设置正确,并进行必要的调整。
步骤6:开启自动加工模式•将数控车床切换到自动加工模式。
•根据加工程序,启动数控车床进行加工。
步骤7:监控加工过程•在加工过程中,及时观察工件和刀具的状态。
•如有异常情况或出现切削问题,立即停止加工并处理。
步骤8:结束加工并清理•加工完成后,关闭数控车床,断开电源。
•清理加工工件和刀具,确保工作区整洁。
3. 数控车床的操作教程教程1:数控编程•学习数控编程的基本语法和命令。
•熟悉数控编程软件的操作界面和功能。
•练习编写简单的加工程序,并进行仿真和调试。
教程2:数控操作技巧•掌握数控车床的操作面板和操作按钮的使用方法。
•学习如何设定坐标轴、刀具路径、加工参数等。
•熟悉数控车床的紧急停车和故障处理方法。
教程3:安全操作规范•学习数控车床的安全操作规范和操作流程。
•注意个人防护,避免意外伤害。
•指导操作人员正确使用数控车床,减少操作失误和事故风险。
结论通过掌握数控车床的操作步骤和操作教程,能够安全、高效地使用数控车床进行工件加工。
数控车床指令详解

数控车床指令G00 快速定位G00,X、Z轴分别会以最快速的方法到达目的点,移动路线一般是折线。
当使用G00时,会先以X 轴、Z轴的合成方向移动到目的点也就是你指定的坐标点,最后在由余下行程的某轴单独快速移动指定的坐标点。
使用G00时,轴移动速度不接受F代码来控制,受倍率的限制。
G00代码一般都是走空刀,快速移动到某点,所以G00也称快速定位,一般而言G00是不能用于切削行程中。
注意:在高速切削的时候,G00移动速度特别快,移动速度快通常也是新手们撞刀的地方,所以在没有把握的时候最好不要X,Z轴一起动。
G01 直线插补G01指令是经常要用到的指令,走刀速度由F来控制,走刀方向可以走圆柱,圆锥其实G01时的实际的走刀速度等同于F指令给定的速度与进给速度修调倍率的乘积。
一般数控机床会有主轴倍率和进给倍率,这2个倍率可以很方便的调节主轴的快慢,和走刀的快慢,无需修改程序中的走刀速度和主轴转速。
其实G01指令在有些系统具备倒圆弧角,这样简省了编程人员的时间无需在调用G02或G03指令来倒圆弧角G90 外圆切削循环(单一固定循环)G94 端面切削循环指令:GOO X(U)_Z(W)_F_;(5)锥面加工指令:G90 X(U)_Z(W)_I_F_;I为切削始点与圆锥切削终点半径值(注意I的正负)。
(6)复合指令循环(外圆粗车G71)指令:G71 U_R_;G71 P_Q_U_W_F_;U 每次进给量(0-0.15)。
R 每次退刀量(0.5)。
P 循环程序起始号。
Q 循环程序结束号。
U 径向粗车余量。
W 轴向粗车余量。
(端面粗车循环G72)指令:G71 W_R_;G71 P_Q_U_W_F_;W 每次进给量(0-0.15)。
R 每次退刀量(0.5)。
P 循环程序起始号。
Q 循环程序结束号。
U 径向粗车余量。
W 轴向粗车余量。
(精车)指令:G70 P_Q_;(7)指令:G73 U_W_R_;G73 P_Q_U_W_F_;U x轴上的总退刀量。
mastercam数控车床自动编程软件实训操作
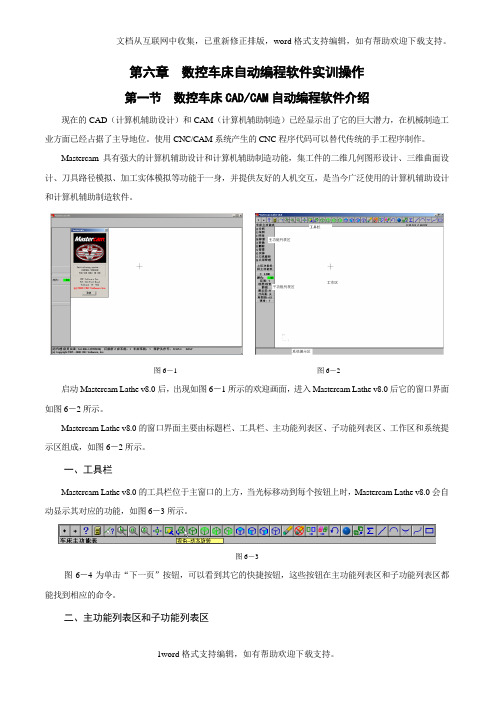
第六章数控车床自动编程软件实训操作第一节数控车床CAD/CAM自动编程软件介绍现在的CAD(计算机辅助设计)和CAM(计算机辅助制造)已经显示出了它的巨大潜力,在机械制造工业方面已经占据了主导地位。
使用CNC/CAM系统产生的CNC程序代码可以替代传统的手工程序制作。
Mastercam具有强大的计算机辅助设计和计算机辅助制造功能,集工件的二维几何图形设计、三维曲面设计、刀具路径模拟、加工实体模拟等功能于一身,并提供友好的人机交互,是当今广泛使用的计算机辅助设计和计算机辅助制造软件。
图6-1 图6-2启动Mastercam Lathe v8.0后,出现如图6-1所示的欢迎画面,进入Mastercam Lathe v8.0后它的窗口界面如图6-2所示。
Mastercam Lathe v8.0的窗口界面主要由标题栏、工具栏、主功能列表区、子功能列表区、工作区和系统提示区组成,如图6-2所示。
一、工具栏Mastercam Lathe v8.0的工具栏位于主窗口的上方,当光标移动到每个按钮上时,Mastercam Lathe v8.0会自动显示其对应的功能,如图6-3所示。
图6-3图6-4为单击“下一页”按钮,可以看到其它的快捷按钮,这些按钮在主功能列表区和子功能列表区都能找到相应的命令。
二、主功能列表区和子功能列表区图6-10主功能列表区中显示可供用户选择的命令列表,如图6-5所示。
在主功能列表区有两个按钮,分别是“上层功能表”和“回主功能表”。
利用这两个按钮就可以在命令列表之间寻找需要的命令,并可以方便地返回到上一层命令列表或主功能列表。
图6-4例如,单击“档案”命令,主功能列表区变成如图6-6所示的档案命令列表;再单击“档案转换”命令,进入如图6-7所示的档案转换命令列表;单击“DXF ”命令,进入如图6-8所示的命令列表;单击“读取”可以转换其它CAD/CAM 软件中输出的图形。
最后单击“回主功能表”按钮,就回到如图6-5所示的主功能列表区。
数控加工的加工路线要遵循的原则

数控加工的加工路线要遵循的原则数控车床进给加工路线是指车刀从对刀点(或机床固定原点)开始运动起,直至返回该点并结束加工程序所经过的路径,包括切削加工的路径及刀具切人、切出等非切削空行程路径。
精加工的进给路线基本上都是沿其零件轮廓顺序进行的,因此,确定进给路线的工作重点是确定粗加工及空行程的进给路线。
在数控车床加工中,加工路线的确定一般要遵循以下几方面原则:1、应能保证被加工工件的精度和表面粗糙度。
2、使加工路线最短,减少空行程时间,提高加工效率。
3、尽量简化数值计算的工作量,简化加工程序。
4、对于某些重复使用的程序,应使用子程序。
使加工程序具有最短的进给路线,不仅可以节省整个加工过程的执行时间,还能减少一些不必要的刀具消耗及机床进给机构滑动部件的磨损等。
最短进给路线的类型及实现方法如下:1、最短的切削进给路线。
切削进给路线最短,可有效提高生产效率,降低刀具损耗。
安排最短切削进给路线时,还要保证工件的刚性和加工工艺性等要求。
2、最短的空行程路线。
(1)巧用起刀点。
采用矩形循环方式进行粗车的一般情况示例。
其对刀点A的设定是考虑到精车等加工过程中需方便地换刀,故设置在离毛坯件较远的位置处,同时,将起刀点与其对刀点重合在一起。
(2)巧设换刀点。
为了考虑换刀的方便和安全,有时将换刀点也设置在离毛坯件较远的位置处,那么,当换第二把刀后,进行精车时的空行程路线必然也较长;如果将第二把刀的换刀点也设置在中的毋点位置上,则可缩短空行程距离。
(3)合理安排“回零”路线。
在手工编制复杂轮廓的加工程序时,为简化计算过程,便于校核,程序编制者有时将每一刀加工完后的刀具终点,通过执行“回零”操作指令,使其全部返回到对刀点位置,然后再执行后续程序。
这样会增加进给路线的距离,降低生产效率。
因此,在合理安排“回零”路线时,应使前一刀的终点与后一刀的起点间的距离尽量短.或者为零,以满足进给路线最短的要求。
另外,在选择返回对刀点指令时,在不发生干涉的前提下,尽可能采用x、z轴双向同时“回零”指令,该功能“回零”路线是最短的。
数控车床基本操作步骤

7.完成加工当加工程序中的所有指令都执行完毕之后,数控车床会停止加工并进入待机状态。此时,可以将加工好的工件从机床上取下,并进行必要的后续处理,如清洁、测量和质检等。根据加工结果,可以对程序和参数进行适当的调整和优化,以提高下一次加工的质量和效率。
4.调试刀具路径在加工操作之前,需要通过调试刀具路径来验证程序的正确性。可以通过手动模式或者半自动模式来执行程序代码,观察刀具移动轨迹和加工效果是否符合预期。如果存在问题,可以及时修改程序或调整参数,确保加工过程中的准确性和稳定性。
5.启动加工在确认加工程序和刀具路径没有问题之后,可以启动数控车床进行实际加工操作。通过触发控制系统中的启动按钮,数控车床能够自动执行加工程序中的指令,完成工件的加工过程。在加工过程中,需要密切观察加工状态,及时调述,数控车床的基本操作步骤包括设置机床参数、加载加工程序、定位工件、调试刀具路径、启动加工、监控加工过程和完成加工。熟练掌握这些基本操作步骤,能够帮助操作者更好地使用数控车床,提高加工效率和质量。
数控车床基本操作步骤
数控车床是现代制造业中广泛应用的一种机床,它以计算机控制系统为核心,实现对工件进行自动加工。作为一种重要的加工工具,运用数控车床进行加工操作需要熟悉一定的基本操作步骤。本文将介绍数控车床的基本操作步骤,以帮助读者更好地理解和掌握数控车床的操作技巧。
1.设置机床参数在使用数控车床之前,需要根据实际加工要求,设置机床的参数。这些参数包括工作台坐标系原点、工件坐标系原点、刀具长度补偿值等。通过机床控制系统的操作界面,输入相应的数值进行参数设置,确保加工过程中的准确性和精度。
Fanuc数控车床G代码及M指令

Fanuc数控车床G代码及M指令一、G 代码命令1、代码组及其含义“模态代码” 和“一般” 代码“形式代码” 的功能在它被执行后会继续维持,而“一般代码” 仅仅在收到该命令时起作用。
定义移动的代码通常是“模态代码”,像直线、圆弧和循环代码。
反之,像原点返回代码就叫“一般代码”。
每一个代码都归属其各自的代码组。
在“模态代码”里,当前的代码会被加载的同G7000精加工循环G71 内外径粗切循环G72 台阶粗切循环G73 成形重复循环G74 Z 向步进钻削G75 X 向切槽G76 切螺纹循环G9001(内外直径)切削循环G92 切螺纹循环G94 (台阶) 切削循环G9612恒线速度控制G97 恒线速度控制取消G98 10 固定循环返回起始点G00 定位1. 格式G00 X_ Z_这个命令把刀具从当前位置移动到命令指定的位置 (在绝对坐标方式下),或者移动到某个距离处 (在增量坐标方式下)。
2. 非直线切削形式的定位我们的定义是:采用独立的快速移动速率来决定每一个轴的位置。
刀具路径不是直线,根据到达的顺序,机器轴依次停止在命令指定的位置。
3. 直线定位刀具路径类似直线切削(G01) 那样,以最短的时间(不超过每一个轴快速移动速率)定位于要求的位置。
4. 举例N10 G0 X100 Z65G01 直线插补1. 格式G01 X(U)_ Z(W)_ F_ ;直线插补以直线方式和命令给定的移动速率从当前位置移动到命令位置。
X, Z: 要求移动到的位置的绝对坐标值。
U,W: 要求移动到的位置的增量坐标值。
2. 举例①绝对坐标程序G01 X50. Z75. F0.2 ;X100.;②增量坐标程序G01 U0.0 W-75. F0.2 ;U50.G02/G03 圆弧插补 (G02, G03)1. 格式G02(G03) X(U)__Z(W)__I__K__F__ ;G02(G03) X(U)__Z(W)__R__F__ ;G02 –顺时钟 (CW) 凹圆G03 –逆时钟 (CCW) 凸圆X, Z –在坐标系里的终点U, W –起点与终点之间的距离I, K –从起点到中心点的矢量 (半径值)R –圆弧范围 (最大180 度)。
端面粗车循环G72及实图编程实例

端面粗车循环G72及实图编程实例端面粗车循环G72程序是一种在数控车床上实现端面粗加工的常用循环程序。
它通过设定合适的参数和路径,实现工件端面上的切削加工。
本文将详细介绍端面粗车循环G72的编程方法,并结合实例,帮助读者更好地理解和掌握该编程技术。
1. 端面粗车循环G72的概述端面粗车循环G72是一种在数控车床上进行端面粗加工的循环程序。
通过设定合适的刀具路径、切削速度和进给速度等参数,可以高效地完成工件端面的粗加工工序。
在编写端面粗车循环G72程序时,需要注意以下几个关键要素:1.1 切削路径:应根据工件的要求确定切削路径,通常选择以圆弧方式进行切削。
1.2 刀具路径:刀具路径的选择与切削路径相互关联,需要保证刀具能够覆盖到所有需要加工的区域。
1.3 切削速度:切削速度是决定切削效率和加工质量的重要因素,需根据工件材料和刀具材质进行合理设置。
1.4 进给速度:进给速度的设定应根据切削力和切削稳定性来进行调整,以保证切削效果和工件表面质量。
2. 端面粗车循环G72的编程实例下面以某工件的端面粗加工为例,给出端面粗车循环G72的编程实例,帮助读者理解该编程技术的具体应用。
假设某工件的直径为100mm,需要进行端面粗加工,并已确定刀具为直径20mm的车削刀具。
具体的编程实例如下:N10 G90 G54 G96 S600 M3N20 T01 M06N30 G00 X50 Z5N40 G96 S300 M4N50 G71 U1.5 R2N60 G72 P100 Q150 U2 W0N70 G00 X0 Z10N80 G71 U-1.5 R2N90 M5N100 G00 X0 Z50N110 M30代码解释:- N10: 设定工作坐标系(G54)、单位(G90)、主轴转速(S600 rpm)和开启主轴(M3)。
- N20: 刀具切换(T01)和刀具预调(M06)。
- N30: 快速定位刀具起始位置(X50 Z5)。
- 1、下载文档前请自行甄别文档内容的完整性,平台不提供额外的编辑、内容补充、找答案等附加服务。
- 2、"仅部分预览"的文档,不可在线预览部分如存在完整性等问题,可反馈申请退款(可完整预览的文档不适用该条件!)。
- 3、如文档侵犯您的权益,请联系客服反馈,我们会尽快为您处理(人工客服工作时间:9:00-18:30)。
第10章车床加工本章主要讲述Mastercam Lath(车床)加工刀具路径。
车床系统可生成多种车削加工路径, 包括Quick(快捷车削)、Face(表面车削)、Goove(挖槽)、Drill(钻孔)、Thread(螺纹车削)、Cutoff(切断)、C-axis(分度旋转轴)等加工路径10.1 车床加工基础知识• 车床加工系统的各模组生成刀具路径之前,也要进行工件、刀具及材料参数的设置,其材料的设置与铣床加工系统相同,但工件和刀具的参数设置与铣床加工有较大的不同。
车床系统中几何模型的绘制方法与铣床系统中几何模型的绘制方法有所不同,只需用绘制零件图形的一半。
在生成刀具路径后,可以用操作管理器进行刀具路径的编辑、刀具路径模拟、仿真加工模拟以及后处理等操作。
•10.1.1 车床坐标系•10.1.2 刀具参数•10.1.3 工件设置10.1.1 车床坐标系•一般数控车床使用X轴和Z轴两轴控制。
其中Z轴平行于机床主轴,+Z方向为刀具远离刀柄方向;X轴垂直于车床的主轴,+X方向为刀具离开主轴线方向。
当刀座位于操作人员的对面时,远离机床和操作者方向为+X方向;当刀座位于操作人员的同侧时,远离机床靠近操作者方向为+X方向。
有些车床有主轴角位移控制(C-axis),即主轴的旋转转角度可以精确控制。
• 在车床加工系统中绘制几何模型要先进行数控机床坐标系设定。
顺序选择主菜单中的Cplane→Next Menu进行坐标设置。
常用坐标有“+XZ”、“-XZ”、“+DZ”、“-DZ”。
车床坐标系中的X方向坐标值有两种表示方法:半径值和直径值。
当采用字母X时表示输入的数值为半径值;采用字母D时表示输入的数值为直径值。
采用不同的坐标表示方法时,其输入的数值也应不同,采用直径表示方法的坐标输入值应为半径表示方法的2倍。
•车床加工中,工件一般都是回转体,所以,在绘制几何模型时只需绘制零件的一半外形,即母线。
•螺纹、凹槽及切槽面的外形可由各加工模组分别定义。
有些几何模型在绘制时只要确定其控制点的位置,而不用绘制外形。
控制点即螺纹、凹槽及切槽面等外形的起止点,绘制方法与普通点相同。
几何模型10.1.2 刀具参数•在“Job Setup”对话框中单击“Lathe Tool”按钮,或顺序选择NC utils→Def tools,“Lathe Tool Manager”对话框。
在刀具列表中单击鼠标右键,打开的快捷菜单。
该快捷菜单各选项的功能与铣床加工系统中“Tool Manager”对话框快捷菜单对应选项相同。
•在采用不同的加工模组生成刀具路径时,除了设置各模组的一组特有参数外,还需要设置一组共同的刀具参数。
车床加工模组的Tool parameters(刀具参数)选项卡。
•车床加工模组刀具参数与铣床加工模组刀具参数的设置参数基本相同,只是车床加工模组刀具参数的设置中增加了“Coordinates”按钮。
通过打开“Coordinates”对话框来设置刀具的Tool Oropn(原点)和Active Spindle(刀柄方向)。
“车刀设置”对话框及其快捷菜Tool parameters选项卡• 车刀通常由Insert(刀头)Holder(刀柄)两部分组成。
所以车床系统刀具的设置包括刀具类型、刀头、刀柄及刀具参数的设置。
1. 刀具类型•车床系统提供了General Turning(一般外圆车削刀具)、Threading(螺纹车削刀•车床系统提供了General Turning(一般外圆车削刀具)、Threading(螺纹车削刀具)、Grooving/Parting(挖槽/切断刀具)、Boring Bar(内孔车削刀具)及Drill/Tap/Reamer(钻孔/攻丝/铰孔)等5类常用刀具。
“Custom”(自定义)选项来定义刀具。
2. 设置刀头参数•在常用的车削刀具中,只有外径车削刀具和内孔车削刀具刀头设置参数相同,用于刀头参数设置的“Inserts”选项卡。
•外圆车刀和内孔车刀的刀头参数中,主要需设置Insert Material(刀头材料)、Shape(形状)、Cross Section(截面形状)、Relief Angle(后角)、IC Dia./Length(内切圆直径/长度)、Insert Width(宽度)、Thickness(厚度)及圆角半径等参数。
所有这些参数可在相应的列表或下拉列表中选择。
外圆和内孔车刀的刀头选项•螺纹车削刀具刀头的设置内容有:Style(刀头样式)、Insert Geometry(刀头外形尺寸)和用于加工的螺纹类型。
其中刀头样式可以在“style”列表中选取,当选取了刀头样式后,系统在Insert Geometry选项组显示出选取刀头的外形特征尺寸,可在对应的输入框中设置刀头的各几何参数。
设置螺纹车削刀具刀头的选项卡。
•切槽/切断车削刀具刀头的设置与螺纹车削刀具刀头的设置基本相同,主要包括style(刀头样式)和Insert Geometry(刀头外形尺寸)的设置。
设置挖槽/切断车削刀具刀头的选项卡。
设置挖槽/切断车削刀具刀头的选项卡。
•用于钻孔/攻丝/铰孔的刀具在“Tool Type”选项组中提供了8种不同的类型,设置钻孔/攻丝/铰孔刀具的选项卡。
螺纹车削刀具的刀头设置3. 设置刀柄与夹头•刀具不同刀柄(夹头)也不相同。
外圆刀具刀柄的“Holders”选项卡,与螺纹车削刀具和挖槽/切断车削刀具选项卡基本一样,这三种车削刀具刀柄的设置中都需设置三种参数来定义刀具的刀柄:Style(刀柄样式)、Holders Geometry(刀柄外形尺寸)和Shan Cross Section(截面形状)。
•内孔车削刀具刀柄的“Boring Bars”选项卡。
内孔车削刀具刀柄的设置方法与外径车削刀具刀柄的设置方法基本相同,也需要设置“Style”(刀柄样式)和“Holder Geometry”(刀柄外形尺寸)。
内孔车削刀具刀柄均采用圆形截面,和“Holder Geometry”(刀柄外形尺寸)。
内孔车削刀具刀柄均采用圆形截面,不需设置。
•用于设置钻孔/攻丝/铰孔刀具夹头参数的“Holders”选项卡。
对于钻孔/攻丝/铰孔刀具的夹头只需定义其几何外形尺寸。
内孔车削刀具的刀柄设置4. 切削刀具参数•各种车刀参数的设置都是一样的,可以通过“Parameters”选项卡来进行刀具参数的设置。
•Parameters选项卡主要包括以下参数的设置:•Program Parameters(程序参数):Tool number(刀具号)、Tool Station number (刀具位置号)、Tool offsetnumber(刀具补偿号)和Tool back offset number(刀具返回补偿号)。
•Default Cutting Parameters(切削用量):刀具的车削速度及进刀量。
•Toolpath Parameters(刀具路径参数):切削深度、重叠量、停留时间及退刀距离等参数。
•Coolant(冷却参数):选择加工中冷却的方式。
•Compensation(刀尖补偿形式):设置刀具刀尖偏角类型。
设置刀具的参数10.1.3 工件设置• 在主菜单中顺序选择Lathe Toolpaths→Job setup选项,即可打开“Lathe Job setup”对话框。
可以使用该对话框来进行车床加工系统的工件设置、材料等设置。
•在车床加工系统中的工件设置除要设置工件的外形尺寸外,还需对工件的夹头及顶尖进行设置,单击Boundaries(边界)选项卡,出现“边界设置”对话框。
•工件外形通过“Stock”选项组来设置。
首先需设置工件的主轴方向,可以设置为Left spindle(左边)或Right spindle(右边),系统的默认设置为左方向。
车床加工系统其工件为以车床主轴为回转轴的回转体。
回转体的边界可以用串连或矩形来定义。
“边界设置”对话• “Chuck”选项组用来设置工件夹头。
工件夹头的设置方法与工件外形的设置方法基本相同。
其主轴转向也可设置为左向(系统默认设置)或右向。
夹头的外形边界可以用串连、矩形或己绘制工件夹头外形来定义。
•顶尖通过“Tailstock”选项组来设置。
顶尖的外形设置与夹头的外形设置相同,也可以用串连、矩形或已绘制工件夹头外形来定义。
•工件外形、夹头外形和顶尖外形设置都是用来定义加工过程中的安全边界。
在定义了安全边界后还需定义两个安全距离。
安全距离通过“Tool Clearance”选项组来设置。
其中“Rapid”输入框用于指定工件快速旋转时的安全距离;“Entry/Exit”输入框用于指定在进刀/退刀时的安全距离。
10.2 粗车、精车参数10.2 粗车、精车参数•粗车与精车模组都可用于切除工件的多余材料,使工件接近于最终的尺寸和形状,为最终加工作准备。
两个模组的参数基本相同。
•10.2.1 粗车•10.2.2 精车•10.2.3 实例10.2.1 粗车• 选择“Lathe Toolpaths”子菜单中的“Rough”选项可调用粗车模组。
粗车模组用来切除工件上大余量的材料,使工件接近于最终的尺寸和形状,为精加工作准备。
工件的外形通过在绘图区选取一组曲线串连来定义。
该模组所特有的参数可用“Rough parameters”选项卡来进行设置。
•该组参数的设置主要是对加工参数、走刀方式、粗车方向与角度、刀具偏置及切进参数等进行设置。
设置粗车模组的参数1. 加工参数•粗车模组的加工参数包括Overlap amount(重叠量)、Rough(粗车深度)、Stock to leave(预留量)、Entry(提前量)参数。
重叠量是指相邻粗车削之间的重叠距离,当设置了重叠量时,每次车削的退刀量等于车削深度与重叠量之和。
在粗车深度的设置中,若选中“Equal Steps”复选框,则粗车深度设置为刀具允许的最大粗车削深度。
预留量的设置包括X和Z两个方向上设置预留量。
提前量是指开始进刀时刀具距工件表面的距离。
进给率是用来设置刀具进给速度,可按每转的进给量或每分钟的进给量来设置。
2. 走刀形式•“Cutting Method”选项组用来选择粗车加工时刀具的走刀方式。
系统提供了两种走刀方式:One-way(单向车削)和Zig-Zag(双向车削)。
一般设置为单向车削加工,只有采用双向刀具进行粗车加工时才能选择双向车削走刀方式。
3. 粗车方向/角度•Rough Direction/Angle选项组用来选择粗车方向和指定粗车角度。
有4种粗车方向:OD(外圆)、ID(内圆)、Face(前端面)和Back(后端面),以及Angle(粗车角度)选项。
4. 刀具补偿•车床加工系统刀具偏置包括Compensation in Com-puter(计算机偏置补偿)和Compensation in Control(控制器补偿)两类。