APS排程系统的生产模型
APS高级生产计划与生产排程-PPT
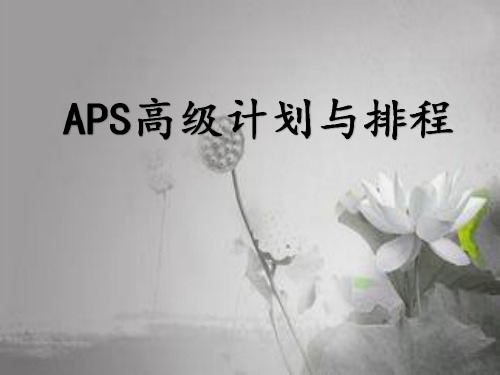
拉动计划-看板
传统MPS/MRP模式
APS精益混合管理模式
精益 传统 产模精
1、什么是APS? 2、APS在制造信息化位置与关系?
4、APS的难度与挑战
制造企业面临的困境
• 我们很多人身体长期都处于亚健康状态,忽视了三 高(高血糖、高血压、高血脂)。
• 制造企业存在长期亚健康状态,忽视“三高”:
当资源需要动态选择加工时,也就是对顺序规则从 新选择时, 如最小准备时间规则等。
4、资源组成员分配规则 当须选择多个资源,替代资源时,如最小
资源利用率资源等。
APS计划和排程
APS是一种新的计划方法
• 一个新的计划方法: “APS 在客户订单输入时, 能及时计划: .人力产能
.生产设备与工具产能排程 .物料需求计划
2,具体设备产能的、模具、物料、人员的约束计算,无论是按日、班次、 分钟计划非常重要,这影响到客户的精确交期。对插单、模拟调整是很多 企业非常重要的。产能是和多个产品、交期、需求同时变化的。尤其是瓶 颈产能,如有合理的排程顺序,产能是可以最有效利用的。(没必要那么
详细、尽量避免插单等)
3,MPS是主生产排程(Master production schedule),应该是具体指导生产 的,它应该受到产能、模具、物料、人员约束的可执行的主排程。但是。 可惜的是,MPS确实是无约束的手工调整来应对变化,品种一多,再变化 频繁,就力不从心了。如果MPS都是不可执行的计划排程,那么依据它的 MRP就更不准了。(MPS可以计划可以较粗,可以用RCCP分析来调整 MPS)
精益管理的两种方法
连续拉动 – 看板
– 丰田生产系统 – 零件超市系统 – 补充系统 – 订单点系统 – JIT (准时化) 主要消灭时间延迟 广播拉动 – APS – TOC(DBR)
先进规划与排程系统(APS)

先進規劃與排程系統(APS)企業的生產規劃與排程技術由早期的存貨規劃控制系統、物料需求規劃系統(MRP)、製造資源規劃系統(MRPⅡ),一直演變到今日的先進規劃與排程系統(Advanced Planning and Scheduling, APS),主要是過去的技術定了許多假設,但卻又不符合生產規劃及排程的需要,而先進規劃與排程系統則是可以克服那些不合理現象,因此已逐漸當今生產規劃的重要技術。
一、先進規劃與排程系統之簡介先進規劃與排程系統係利用許多進步的管理規劃技術,包括限制理論(Theory of Constraints, TOC)、作業研究(Operations Research, OR)、基因演算法(Genetic Algorithms, GA)、限制條件滿足技術(Constaint Satisfaction Technique,CST)等;在有限資源下,追求供給與需求間的平衡規劃;同時利用資訊的儲存與分析能力,以最短的時間,達到最有效的規劃。
(一) 傳統生產規劃與排程系統所面臨之問題傳統生產規劃與排程系統存在許多不易克服的問題,以致企業不得不重新發展更合適的生產規劃及排程技術,以解決實際上的問題。
以下就傳統生產規劃與排程系統面臨的問題說明如下:1. 系統假設不符合實際現況在實務上,企業的產能有限,而且經常有突發狀況的不定期出現,因此傳統的生產規劃與排程系統對產能有限、訂單交期做為演算依據,並不符合真實企業的生產需要,即使是MRP、MRPⅡ均無法解決上述的矛盾點。
2. 供需規劃並不能溝通協調傳統的生產規劃及排程系統係將需求規劃系統與供給規劃系統分別看待,然而,實務上若不將兩者一併整合來分析,則此種生產規劃及排程系統是無效率的,因為不是供過於需,便是供給不足於因應需求,造成服務品質不佳或成本過高的結果。
3. 未能考量上下層資源整合的問題生產規劃及排程的工作通常包括生產規劃、主排程規劃、物料需求規劃、產能需求規劃、詳細作業排程等階段。
基于APS的制丝智能化自适应排产系统模型设计与应用

基于APS的制丝智能化自适应排产系统模型设计与应用摘要:本文通过研究建立基于APS技术的自适应排产系统模型,可以制定合理优化的生产资源规划策略,并且还可以将实际与计划结合,及时修正因为异常及故障原因造成的计划执行偏差,从而彻底解决工序生产计划与生产资源调配难做的问题。
本文提出的模型与应用方案在卷烟厂进行了大量卓有成效的实践,取得了良好的生产管理效果。
关键字:APS;自适应;排产;资源规划;生产调度作为生产组织和管理的关键,对提高企业的生产效率、设备利用率等有着重要的作用。
但是由于烟草企业生产中约束条件的限制,各个企业的生产调度方案多依靠计划员凭借经验手工完成。
制丝车间之前的生产组织模式,是在调度生产计划的指导下,依据生产管理人员的经验对生产资源进行调配和组织,这种模式容易造成对生产计划和生产状况的误判,做出不适合的生产决策,影响生产进度。
为了更高效、更智能的对生产组织进行管理和控制,制丝车间结合APS(高级计划排程)技术推行以自适应排产系统为基础的智能化生产组织模式。
APS技术主要解决“在有限产能条件下,交期产能精确预测、工序生产与物料供应最优详细计划”的问题。
通过建立基于APS技术的自适应排产系统,可以制定合理优化的生产资源规划策略,并且还可以将实际与计划结合,及时修正因为异常及故障原因造成的计划执行偏差,从而彻底解决工序生产计划与生产资源调配难做的问题。
1.制丝自适应排产系统规划如图1所示,规划系统是在每班生产前,外部输入调度生产计划,根据相关算法,进行智能化运算,产生最佳制丝排产方案。
系统能够自动采集物料消耗量、实际烟丝库存和制丝线产能、储柜留存、设备保养、异常停机等信息数据,能够导入制丝生产规则、批次优先级策略等约束条件,然后根据效率最优化原则安排出各工序生产的最佳方案,以保证各工序进行正常衔接且不超出工艺要求的时间。
在建立策略模型的基础上,同时根据配方要求来演算对梗丝、膨化烟丝、糖香料的需求和生产计划,保证制丝车间的生产顺畅和卷包车间的烟丝及时供给。
APS计划系统和生产排程系统的基本原理和排程步骤

APS计划系统和⽣产排程系统的基本原理和排程步骤APS⾼级计划与排程系统作为ERP和MES之间的桥梁,是承上启下的作⽤,⽤于协调物流、开发瓶颈资源和保证交货⽇期。
APS系统包括需求和供应计划、运输和⽣产计划排程等各种供应链计划模块,下⾯主要介绍APS中⽣产计划排程模块的基本原理。
⼀、APS系统基本原理和排程步骤APS⾼级计划排程是实时的、动态集成的、基于内存计算,主要⽤于车间订单⼯序的排程。
是基于事件的有限约束排程,意味是实时的考虑⽬前的负荷和能⼒和材料供应等多因素。
可以⽀持不同的优化⽅法,考虑基于规则的资源和⼯序选择如最少换装时间、最⼩闲散时间和尽可能的迟考虑排序的相关性等。
APS⾼级计划排程系统⼀般分三步:预见性排程,可以给⼀组订单预先准备优化的排程。
响应性排程,可以在多变的环境中适应变化以维护可⾏的排程。
交互性排程,可以⽤⽢特图触摸屏⼿⼯拖拉⼯序排程调度。
⽣产计划排程的⽬的是为车间⽣成⼀个详细的⽣产计划,⽣产排产计划明确给出了计划范围内的每⼀个订单在所需资源上的加⼯开始时间和结束时间,也给出了在所需资源上订单的加⼯⼯序,⽣产排产计划可以通过⽢特图和数据报表可视化查看。
⼆、排产计划⽣成由车间模型⽣成排产计划的⼀般程序可简单地描述为下⾯6个步骤:▊建模车间模型必须详细地配置⽣产⼯艺、BOM物料构成和相应的资源约束,以便以最⼩的成本⽣成可⾏的⽣产计划。
由于⼯⼚制造产品的能⼒只受潜在瓶颈资源的限制,因此,我们只需对车间现有全部资源的⼀部分,也就是将可能成为瓶颈的资源,建⽴⼀个清晰的模型。
关于建模⽅法的细节我们将在后⾯进⼀步阐述。
▊提取需要的数据⽣产计划排程使⽤的数据来⾃ERP系统导⼊、EXCEL导⼊或者APS系统⼿⼯录⼊,数据主要包含物料、销售订单、主⽣产计划和需求计划等。
⽣产计划排程仅利⽤这些模块中可⽤数据的⼀个⼦集,因此,在建⽴⼀个⽣产单元的模型时,必须指明它实际需要哪些数据。
▊⽣成⼀组假定(⽣产状况)除了上述数据源中接收的数据之外,车间或⽣产单位的决策者或许对车间当前或未来的状况会有更进⼀步的预测和判定,这些信息在其它地⽅(如软件模块中)是不能得到的。
金蝶APS排程系统介绍

1系统定义生产排程:基于约束对生产任务进行有限能力优化排序,确定生产任务在相应资源上的加工顺序及占用时间片段与产能比例,并通过丰富的、交互友好的图形界面将结果展示给用户。
在多种小量、短交期日益成为主流生产模式的今天,生产排程系统通过优化排序,快速、直观、有效的信息传递帮助用户快速、及时、低成本交付产品与服务,具体价值有:图中黄色块代表将来要扩展的内容。
“主计划排程”与“作业排程”共用基础数据、核心算法和大部分的业务功能,主要区别在于排程粒度,交期承诺使用“主计划排程”逻辑。
“主计划排程”计算出各资源(车间、生产单元)日生产计划,考虑产能、工序前后关系,精度到天;“作业排程”计算各资源(设备)在什么时间段做什么做多少,精度到分(秒),考虑产能、工序前后关系、资源任务排序。
新模块在K/3 WISE系统中的位置如下图所示:1.4角色分析间内部设备众多且专业化、产能主要受设备限制,工序产能较稳定;由于工序产能由设备决定,不确定性较小,且工厂现场管控能力较高,排程应该排到具体设备,并进行准确排序,但由于工艺流程过长,涉及多个车间,直接排到设备后,计划的优化性是提高了,但可执行性降低了,因而需先进行主计划排程,对生产任务进行初步分解,到车间(生产单元)日计划,再对车间(生产单元)日计划进行精确作业排程,如此既保证了计划可执行,又有局部的优化,不失为最可接受的方案。
宁波勋辉资源结构如下图,其中车间级为计划资源,设备级为调度资源,计划资源包含调度资源!鹤山市雅瑶隔朗五金实业有限公司主要生产铁线、铁皮、藤编工艺品,塑料、珠子编织工艺品,产品主要有下料、弯管、点焊、喷涂、包装等工序;工序定义范围较宽,产能受人工影响较大,现场精细管控能力不是很强,适合仅使用“主计划排程”做初步排程,使生产可视化,计划合理化。
其资源结构如下图,全部为计划资源。
隔朗五金下料单元弯管单元点焊单元喷涂线包装车间。
APS高级生产计划与生产排程培训讲义

APS高级生产计划与生产排程培训讲义1. 引言高级生产计划与生产排程(Advanced Planning and Scheduling,APS)是一种用于优化生产计划和排程的先进技术。
通过APS系统,企业可以更好地管理生产计划和资源,提高生产效率,降低成本,提供更好的客户服务。
本讲义将介绍APS 的基本概念、原理和实践方法,帮助学员了解和掌握这一重要领域的知识。
2. APS的基本概念2.1 生产计划与生产排程的定义和区别生产计划是指制定一个生产计划以满足特定的需求或目标,它包括决定什么时候制造什么产品,预测产量和资源需求等。
生产排程则是在给定的生产计划下,决定每个生产任务在何时进行、使用哪些资源、以及如何安排等问题。
APS系统旨在同时实现高效的生产计划和排程。
2.2 APS的特点和优势• 2.2.1 高度自动化:APS系统大量使用先进的算法和模型,自动化生成生产计划和排程,减少人工干预的需求。
• 2.2.2 实时性:APS系统具备实时监控和调整生产计划和排程的能力,能够快速应对变化的需求和资源状况。
• 2.2.3 优化性:APS系统能够自动优化生产计划和排程,以实现最佳的资源利用率、生产效率和客户服务水平。
• 2.2.4 可视化:APS系统通过直观的图形化界面,展示生产计划和排程的情况,便于管理者和操作人员进行决策和执行。
3. APS的实施流程3.1 项目准备阶段在实施APS系统之前,需要进行一些前期准备工作,包括明确项目目标、确定项目团队、收集数据等。
3.2 数据准备阶段数据是APS系统的重要输入,包括产品结构、工艺路线、库存状况、客户订单等信息。
在数据准备阶段,需要对这些数据进行收集、清洗和整理。
3.3 模型建立阶段在模型建立阶段,需要根据具体的业务需求和规则,建立适合企业的模型和算法。
这包括产品结构模型、工艺模型、资源模型等。
3.4 系统实施阶段在系统实施阶段,需要根据模型和算法,开发和部署APS系统。
APS高级生产排程系统
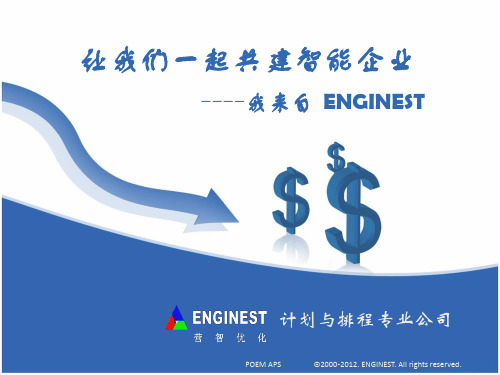
生产排程的约束及目标(1)
Simpler • Smarter • Swifter
资源约束: 资源生产能力 资源并行加工能力 资源使用方式 日工作模式 资源工作日历 日工作时间段(多班次) 资源损耗上限 外协资源约束...
订单级约束: 订单多批次执行 最早开工时间 最晚完工时间 不同订单的资源耦合 不同订单间的执行间隔 订单间后继关系 订单的调度次序 订单相互间的次序关系 订单的优先级...
• POEM APS是基于NCL语言进行应用化研发。NCL语言是一门基于常 规数理逻辑、求解约束满足问题的描述型语言。NCL语言与其它声明 型语言不同:它基于一阶逻辑(量词、布尔逻辑、数值约束、集合运 算和逻辑函数)自然地对问题建模;它在实数、整数、布尔、日期/时 间、指针及集合的混合域上以混合集合规划(Mixed Set Programming)算法对问题求解。它适用于逻辑规划、约束规划、优 化、建模、运筹学及人工智能等领域的研发人员
POEM APS
© 2000-2012. ENGINEST. All rights reserved.
ENGINEST的知识产权保护
国际保护: • 国际知识产权OMPI登记 • 欧盟OHMI登记 • 美国专利与商标局登记 • 欧盟IDDN软件登记证书
Simpler • Smarter • Swifter
POEM APS
© 2000-2012. ENGINEST. All rights reserved.
对大规模生产的排程与再排程
Simpler • Smarter • Swifter
可求解数千资源、10万工序级规模的生产排程问题
POEM APS
© 2000-2012. ENGINEST. All rights reserved.
高级计划排产( APS)的概念和内容

高级计划排产(APS)的概念和内容高级方案排产(advanced planningand scheduling, APS)是一个方案排产软体包,主要解决「在有限产能条件下,交期产能精确猜测、工序生产与物料供应最优具体方案」的问题。
APS(高级方案排产)系统制订合理优化的具体生产方案,并且还可以将实际与方案结合,接收MES制造执行系统或者其他工序完工反馈资讯,从而彻底地解决工序生产方案与物料需求方案难做的问题。
APS(高级方案排产)系统是企业实施JIT精益制造系统的最有效工具。
APS(高级方案排产)方案可以依据公司目标建立一个资源力量与生产设备力量模型。
一旦完成模型的设定,就可以选择通过高级算法或模拟方案规章,自动地调配资源,达到优化方案排程的目标。
它可以通过生产的工艺路径、订单、力量等简单状况自动地生成一个优化的、符合实际的具体的生产方案。
它能检查、评估量划的表现。
假如需要可准时调整约束条件,产生动态的目标方案。
1.APS所包括的内容APS内容主要有以下几点:(1)基于订单任务(job-based)的订单优先挨次方案;(2)基于大事(event-based)的资源利用率最大化方案;(3)基于资源(resource-based)的瓶颈约束方案;(4)基于物料约束的可行的方案;(5)基于历史、现在、将来的需求方案;(6)基于供应资源优化的分销配置方案;(7)基于运输资源的优化运输方案。
2.APS为制造业供应的解决方案APS为制造业的四类制造模型供应的解决方案:(1)流程式模型,APS主要是解决挨次优化问题;(2)离散式模型,APS主要是解决多工序、多资源的优化调度问题;(3)流程和离散的混合模型,APS同时解决挨次和调度的优化问题;(4)项目管理模型,APS主要解决关键链(资源约束)和成本时间最小化问题。
3.APS考虑不同行业的解决方案APS的主要着眼点是工序规律约束和资源力量约束,物料和工序流程紧密联接,各种优化规章,计算最早可能开头时间和最迟可能开头时间。
- 1、下载文档前请自行甄别文档内容的完整性,平台不提供额外的编辑、内容补充、找答案等附加服务。
- 2、"仅部分预览"的文档,不可在线预览部分如存在完整性等问题,可反馈申请退款(可完整预览的文档不适用该条件!)。
- 3、如文档侵犯您的权益,请联系客服反馈,我们会尽快为您处理(人工客服工作时间:9:00-18:30)。
APS排程系统的生产模型
建立生产模型,让软件接受企业的详细生产过程,这的确很麻烦,但并非是无法完成的,真正的难点在于下一步:根据模型和生产请求得到详细的作业计划,也就是详细生产排程。
ERP的真正技术瓶颈就发生在这里。
详细生产排程的结果是‘生产作业计划’,是针对每个人员每个设备的生产资源的工作计划。
作业计划必须满足在生产工艺上不能有半点差错。
首先,工序之间必须满足特定的逻辑关系,以及要求某些工序必须连续、同时、或者间隔进行等等,这是对作业计划最基本的要求。
其次,作业计划必须满足资源能力限制,一个资源在一个时间内只能干一件事情,生产作业计划中不能有资源冲突;最后,作业计划必须满足物料供应的限制,没有原材料不能开始生产。
也就是说:作业计划必须同时满足多种复杂的约束条件。
TOC约束理论早已有之,只是需要比较高级的算法和数学理论,在这方面需要进行长期投入才会有所收获。
因此国内理论界对此的研究还很少。
有了按照TOC理论计算出来的计划,满足企业生产工艺要求是不是就行了?很遗憾,这还是差的很远。
现在我们以一个假想例子来说明。
一个ERP生产调度系统,很顺利接受了某企业的全部生产细节,并计算出了一套生产作业计划,打印成一份给所有生产资源安排工作的作业计划。
现在,由一个有经验的老调度师来决断这个ERP计划系统是不是可以用的,他将如何做?
首先,他会逐一检查每个工序的时间安排,看它们之间的次序和逻辑关系是不是符合企业生产工艺的逻辑关系要求;其次,他会观察这个计划中对每个资源的安排是不是合理,有没有一个时间干两个活这种冲突的情况发生;最后他要看在计划时间内物料能不能供应的上。
这些都没有问题了,他必须承认:这个计划已经是一个‘可行’的计划了,也就是说,照此计划一定可以完成生产任务。
但是,还有一个关键的事情,老调度师根据自己习惯的做法,也手工制定了一个作业计划,他把这两个计划一对E比,发现问题了。
手工的计划可以8个小时完成全部工作,而计算机的计划需要9个小时。
或者手工计划可以在8:00完成而计算机的计划要在9:00点完成。
原因在于:计算机对某几个工序的顺序安排虽然可行但是不合理,而老调度师根据长期经验早已清楚此时安排工序应该哪个先、哪个后、哪些并行比较好,结果可以得到更短时间完成的计划。
这是一种优化安排,而计算机没有找到这种安排方法,所以计算机给出的是一个‘可行’的,但是‘不好’的计划!理想中计算机应自动计算出一个比手工计划更好更优化的排产方案结果,指导人如何工作。
这样的软件才能体现出‘企业资源计划’的威力。
否则,不能满足最优化排程的ERP在企业生产中还是无法代替手工。
这隔例子凸现出了一个世界性的关键技术瓶颈:一个生产过程可能有无穷多种‘可行’的安排方式,但是必须从其中找出一个‘最优’的计划,即使不能达到最优,起码要比人的手工计划更优,这才是一套可用的生产排程软件,否则企业还是用不起来。
找出‘可行’计划的难度已经很大,找出‘优化’计划的难度更大。
不仅要处理错综复杂的约束条件,还要从几乎无穷多种满足约束的可行方案中找到优化排程方案。
怎样才能找到这种优化的计划?这是ERP系统共同面对的真正瓶颈问题,是世界性的技术难题。
其中的关键在于算法,算法的基础是数学模型,特别是高级图论、离散数学与线性代数中的矢量矩阵技术。
对此,国外已经作出了
很多年的努力,其研究成果已形成了多个‘APS先进生产排程’产品,发展出了几十种先进生产排程算法,比较常用的如:启发式图搜索法、禁忌搜索法、神经网络优化、遗传算法等,这些算法各有优劣,可用在不同场合。
目前不同的新的算法仍正在蓬勃发展中。
用一句话来形容APS的主要功能:可以自动给出满足多种约束条件、手工排程无法找到的、优化的排产方案。
其实关键就是…可行‟和…优化‟这两个概念。
这个说起来很简单的功能意义十分重大,主要体现在它可以给传统ERP带来以下几个关键的变化:
1)对企业来说,在不增加生产资源的情况下,通过最大限度发挥当前资源能力的方式实现了提高企业生产能力的目标。
2) APS排程的结果给出了精确的物料使用和产出的时间、品种、数量信息,用这些信息可以把很多相关企业或者分厂、车间联合在一起组成一个…SC M供应链‟系统,最大限度减少每个企业的库存量。
3) APS可以用来做为生产决策的依据,它的排程计算结果不光可以作为生产计划,还可以通过不断what if的…试算‟的方式为企业提供生产决策依据。
4)根据自动生成的作业计划还可以自动生成质检、成本、库存、采购、设备维护、销售、运输等计划。
带动企业各个不同管理模块围绕生产运转,改进这些模块的运转方式,大大提高这些模块的运转效率,提升企业整体管理水平。
但是,APS系统的开发难度很大,需要融合最前沿数学理论和最先进管理理论,专业人才很少,投资见效很慢,在国外的价格非常昂贵。
即使是世界性大ERP公司也很少独立投入力量研发,都是采购外插件直接引入相应功能。
国内对这方面的研究除了个别公司外,基本停留在大学院校的实验室中。
永凯软件作为一家全资美资的企业信息化解决方案与服务供应商,亚太区总部位于狮城新加坡,在中国设立上海总部并成立永凯软件技术(上海)有限公司。
公司自成立以来一直致力于为制造业提供领先的APS、WMS产品,制定解决方案及咨询等信息化整体解决方案。
公司拥有一批技术全面的研发人员和经验丰富的管理人员,其中多位已获得博士、硕士学历,在规范化管理过程中形成了永凯独有的开发管理模式。
逐渐发展成具有一定规模的现代化软件公司。
多年来积累了大量的成功案例,“他山之石,可以攻玉”,借鉴他人的智慧,成就自己的梦想!。