转子超音速喷涂工艺介绍
超音速喷涂原理

超音速喷涂原理超音速喷涂是一种先进的表面涂覆技术,它利用高速气流将粉末或液态材料喷涂到工件表面,形成坚固的涂层。
这种喷涂技术具有高效、高质、高精度的特点,被广泛应用于航空航天、汽车制造、电子设备等领域。
那么,超音速喷涂的原理是什么呢?超音速喷涂原理的核心是利用气体动力学效应,将材料颗粒加速到超音速,并喷射到工件表面。
首先,喷涂材料经过加速器加速,进入到高速气流中。
随着气流的加速,材料颗粒也跟随气流加速,最终达到超音速。
当材料颗粒以超音速喷射到工件表面时,会产生高温高压的冲击效应,使材料颗粒瞬间熔化或变形,然后迅速冷却凝固,形成坚固的涂层。
超音速喷涂原理的关键在于气体动力学效应的应用。
气体动力学是研究气体在动态条件下的运动规律的科学,它包括了气体的压缩、加速、膨胀等过程。
在超音速喷涂中,气体动力学效应被充分利用,通过设计合理的喷涂系统和喷嘴结构,使喷涂材料能够在高速气流中达到超音速,从而实现高效喷涂。
除了气体动力学效应,超音速喷涂原理还涉及到热力学和材料科学等多个领域的知识。
在喷涂过程中,高速气流的运动会产生大量的动能,同时也会带走大量的热能,使喷涂材料瞬间升温。
这种快速的加热和冷却过程,对于材料的变形和固化起到了至关重要的作用。
此外,超音速喷涂原理还需要考虑到喷涂材料的选择和粒度分布等因素。
不同的材料对于超音速喷涂的适用性不同,而材料颗粒的粒度分布也会影响到喷涂涂层的质量和性能。
因此,在实际应用中,需要根据具体的喷涂要求和工件材料的特性,选择合适的喷涂材料和工艺参数。
总的来说,超音速喷涂原理是一种复杂的物理过程,它涉及到气体动力学、热力学、材料科学等多个学科的知识。
通过合理设计喷涂系统和喷涂工艺,充分利用气体动力学效应,可以实现高效、高质的涂覆,为工件表面提供优良的保护和功能性涂层。
超音速喷涂技术的不断发展和应用,将为现代制造业带来更多的可能性和机遇。
超音速火焰喷涂原理

超音速火焰喷涂原理
超音速火焰喷涂是一种利用超音速气流将液态或粉状的火焰喷涂材料喷射到被涂表面的技术。
其原理可以概括为以下几点:
1. 喷涂材料的制备:将火焰喷涂材料以液态或粉状形式储存在高压容器中。
液态材料一般需要通过加热使其变为气态,而粉状材料则直接进入喷涂设备。
2. 气流产生:在喷涂设备中,利用压缩空气或氧气等气体通过高压喷嘴加速排出,形成超音速气流。
超音速气流具有非常高的动能和冲击力。
3. 火焰生成:喷涂设备中通过点火机构将气体与可燃物质混合,并点燃产生火焰。
火焰的燃烧产生高温、高能量的气体。
4. 喷涂作用:当火焰燃烧时,超音速气流通过喷嘴将火焰喷涂材料从喷射出,形成一个喷涂射流。
火焰的高温能使液体材料蒸发或粉状材料熔化,并将其析出到射流中。
5. 沉积:喷涂射流与被涂表面相碰撞,产生冲击和磨擦作用。
火焰喷涂材料将沉积在被涂表面上,与基材粘结。
6. 火焰喷涂层形成:随着火焰喷涂材料的沉积,一层薄的火焰喷涂层逐渐形成。
这层火焰喷涂层具有很高的致密性和附着力,能够提供保护和改良被涂表面的性能。
总结:超音速火焰喷涂利用超音速气流将火焰喷涂材料喷射到
被涂表面,通过火焰的燃烧以及超声速气流的动能和冲击力,将液态或粉状材料沉积到表面形成薄的火焰喷涂层。
这种技术可以实现高效、快速和高附着力的涂层制备。
超音速火焰喷涂工艺流程
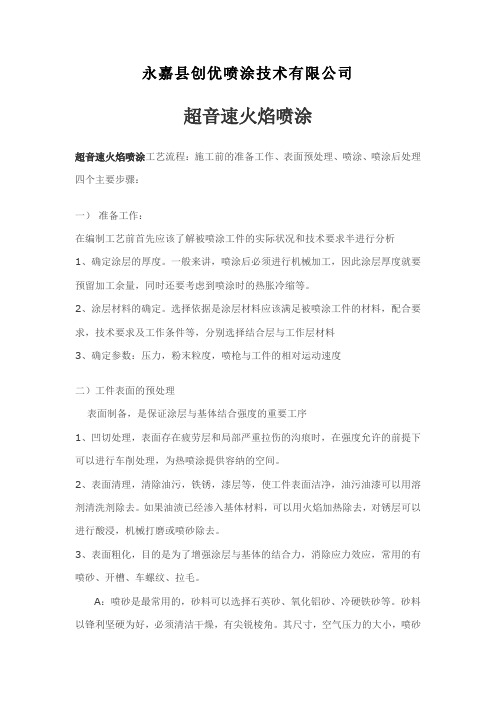
永嘉县创优喷涂技术有限公司超音速火焰喷涂超音速火焰喷涂工艺流程:施工前的准备工作、表面预处理、喷涂、喷涂后处理四个主要步骤:一)准备工作:在编制工艺前首先应该了解被喷涂工件的实际状况和技术要求半进行分析1、确定涂层的厚度。
一般来讲,喷涂后必须进行机械加工,因此涂层厚度就要预留加工余量,同时还要考虑到喷涂时的热胀冷缩等。
2、涂层材料的确定。
选择依据是涂层材料应该满足被喷涂工件的材料,配合要求,技术要求及工作条件等,分别选择结合层与工作层材料3、确定参数:压力,粉末粒度,喷枪与工件的相对运动速度二)工件表面的预处理表面制备,是保证涂层与基体结合强度的重要工序1、凹切处理,表面存在疲劳层和局部严重拉伤的沟痕时,在强度允许的前提下可以进行车削处理,为热喷涂提供容纳的空间。
2、表面清理,清除油污,铁锈,漆层等,使工件表面洁净,油污油漆可以用溶剂清洗剂除去。
如果油渍已经渗入基体材料,可以用火焰加热除去,对锈层可以进行酸浸,机械打磨或喷砂除去。
3、表面粗化,目的是为了增强涂层与基体的结合力,消除应力效应,常用的有喷砂、开槽、车螺纹、拉毛。
A:喷砂是最常用的,砂料可以选择石英砂、氧化铝砂、冷硬铁砂等。
砂料以锋利坚硬为好,必须清洁干燥,有尖锐棱角。
其尺寸,空气压力的大小,喷砂角度、距离和时间应该根据具体情况确定。
B:开槽、车螺纹、辊花。
对轴、套类零件表面的粗化处理,可采用开槽、车螺蚊处理,槽与螺纹表面粗糙度以Ra6.3—12.5为宜,加工过程中不加冷却液与滋润剂,也可以在表面滚花纹,但避免出现尖角。
C:硬度较高的工件可以进行电火花拉毛进行粗化处理,但薄涂层工件应慎用。
电火花拉毛法是将细的镍丝或铝丝作为电极,在电弧的作用下,电极材料与基体表面局部熔合,产生粗糙的表面。
表面粗化后呈现的新鲜表面,应该防止污染,严禁用手触摸,保存在清洁,干燥的环境中,粗化后尽快喷涂,一般喷涂时间不超过二个小时。
4、非喷涂部位的保护喷涂表面附近的非喷涂需要加以保护,可以用耐热的玻璃布或石棉而屏蔽起来。
超音速火焰喷涂
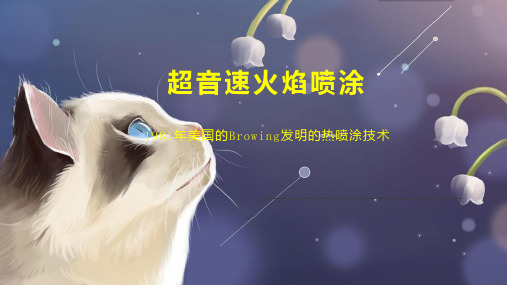
应用
超音速火焰是利用丙烷、丙烯等碳氢系燃气或氢气与高压氧气在燃烧室内,或在特殊的喷嘴中燃烧产生的高 温、高速燃烧焰流,燃烧焰流速度可达五马赫(1500m/s)以上。通常被称作HVOF(High-velocityoxygen-fuel)。 将粉末轴向送进该火焰,可以将喷涂粒子加热至熔化或半熔化状态,并加速到高达300-500m/s,甚至更高的速度, 从而获得结合强度高、致密的高质量的涂层。超音速火焰速度很高,但温度相对较低,对于WC-Co系硬质合金, 可以有效地抑制WC在喷涂过程中的分解,涂层不仅结合强度高,且致密,耐磨损性能优越,其耐磨损性能大幅度 超过等离子喷涂层,与爆炸喷涂层相当,也超过了电镀硬铬层、喷熔层,应用极其广泛 。
超音速火焰喷涂
1981年美国的Browing发明的热喷涂技术
01 简介
03 工作原理
目录
02 工艺流程 04 应用
超音速火焰喷涂(high-velocity oxygen-fuel)是1981年美国的Browing发明了发明的一种新型热喷涂技术。 超音速火焰喷涂(HVOF)设备的核心为喷枪,喷枪由燃烧室(使喷涂材料粒子得到充分加热加速)、Laval喷嘴 (将焰流加速到超音速)和等截面长喷管(使喷涂材料粒子得到充分加热加速)三部分组成。
谢谢观看简介ຫໍສະໝຸດ 超音速火焰喷涂是在八十年代初期,由美国Browning公司研制成功,并且先以JET-KOTE为商品推出。经过几 年的应用开发,该方法的优点逐渐被认识和接受。由此,世界上发达国家,投入了大量的财力对HVOF进行研究开 发。于八十年代末九十年代初期,先后又有数种HVOF喷涂系统研制成功,井投入市场。如金刚石射流(Diamondjet),冲锋枪(Top-gun),连续爆炸喷涂(CDS,Continuous detonationspraying),射流枪(J-gun),高速空 气燃料系统(HVAF,High-velocity air-fuel)等 。
超音速喷涂原理
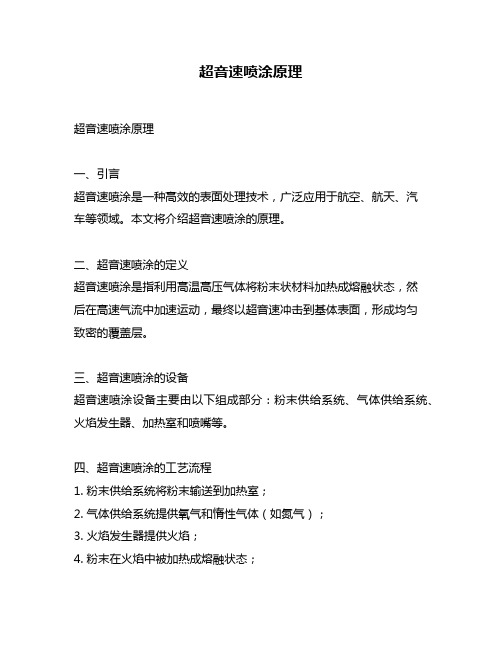
超音速喷涂原理超音速喷涂原理一、引言超音速喷涂是一种高效的表面处理技术,广泛应用于航空、航天、汽车等领域。
本文将介绍超音速喷涂的原理。
二、超音速喷涂的定义超音速喷涂是指利用高温高压气体将粉末状材料加热成熔融状态,然后在高速气流中加速运动,最终以超音速冲击到基体表面,形成均匀致密的覆盖层。
三、超音速喷涂的设备超音速喷涂设备主要由以下组成部分:粉末供给系统、气体供给系统、火焰发生器、加热室和喷嘴等。
四、超音速喷涂的工艺流程1. 粉末供给系统将粉末输送到加热室;2. 气体供给系统提供氧气和惰性气体(如氮气);3. 火焰发生器提供火焰;4. 粉末在火焰中被加热成熔融状态;5. 氧气和惰性气体混合后形成高温高压气流;6. 熔融的粉末在高速气流中加速运动;7. 熔融的粉末以超音速冲击到基体表面。
五、超音速喷涂的原理1. 粉末加热成熔融状态超音速喷涂的第一步是将粉末加热成熔融状态。
火焰发生器提供高温火焰,将粉末加热至熔点以上。
此时,粉末开始熔化,并形成一定的表面张力。
2. 气流加速运动氧气和惰性气体混合后形成高温高压气流。
这个气流在喷嘴中被加速,达到超音速。
同时,喷嘴内部的设计也能够使气流产生旋转运动,使得粉末在运动过程中更为均匀。
3. 粉末冲击基体表面经过以上两个步骤后,熔融的粉末已经被加速到了超音速。
它们以极高的能量冲击到基体表面,并迅速冷却凝固。
由于喷涂过程中使用的惰性气体可防止材料与空气发生反应,因此形成的覆盖层具有很高的致密性。
六、超音速喷涂的优点1. 覆盖层致密由于超音速喷涂过程中使用的惰性气体可防止材料与空气发生反应,因此形成的覆盖层具有很高的致密性,能够有效防止基体受到外界环境的腐蚀和磨损。
2. 生产效率高超音速喷涂是一种高效的表面处理技术,可以在短时间内完成大面积覆盖。
同时,由于喷涂过程中使用的是粉末材料,因此可以根据需要进行不同材料之间的混合。
3. 可适用于多种材料超音速喷涂可以适用于多种不同类型和形状的材料,包括金属、陶瓷、塑料等。
超音速火焰喷涂工艺流程

超音速火焰喷涂工艺流程:施工前的准备工作、表面预处理、喷涂、喷涂后处理四个主要步骤:一)准备工作:在编制工艺前首先应该了解被喷涂工件的实际状况和技术要求并进行分析1、确定涂层的厚度。
一般来讲,喷涂后必须进行机械加工,因此涂层厚度就要预留加工余量,同时还要考虑到喷涂时的热胀冷缩等。
2、涂层材料的确定。
选择依据是涂层材料应该满足被喷涂工件的材料,配合要求,技术要求及工作条件等,分别选择结合层与工作层材料。
3、确定参数:压力,粉末粒度,喷枪与工件的相对运动速度。
二)工件表面的预处理表面制备,是保证涂层与基体结合强度的重要工序1、凹切处理,表面存在疲劳层和局部严重拉伤的沟痕时,在强度允许的前提下可以进行车削处理,为热喷涂提供容纳的空间。
2、表面清理,清除油污,铁锈,漆层等,使工件表面洁净,油污油漆可以用溶剂清洗剂除去。
如果油渍已经渗入基体材料,可以用火焰加热除去,对锈层可以进行酸浸,机械打磨或喷砂除去。
3、表面粗化,目的是为了增强涂层与基体的结合力,消除应力效应,常用的有喷砂、开槽、车螺纹、拉毛等。
A:喷砂是最常用的,砂料可以选择石英砂、氧化铝砂、冷硬铁砂等。
砂料以锋利坚硬为好,必须清洁干燥,有尖锐棱角。
其尺寸,空气压力的大小,喷砂角度、距离和时间应该根据具体情况确定。
B:开槽、车螺纹、辊花。
对轴、套类零件表面的粗化处理,可采用开槽、车螺蚊处理,槽与螺纹表面粗糙度以RA6.3—12.5为宜,加工过程中不加冷却液与滋润剂,也可以在表面滚花纹,但避免出现尖角。
C:硬度较高的工件可以进行电火花拉毛进行粗化处理,但薄涂层工件应慎用。
电火花拉毛法是将细的镍丝或铝丝作为电极,在电弧的作用下,电极材料与基体表面局部熔合,产生粗糙的表面。
表面粗化后呈现的新鲜表面,应该防止污染,严禁用手触摸,保存在清洁,干燥的环境中,粗化后尽快喷涂,一般喷涂时间不超过二个小时。
4、非喷涂部位的保护喷涂表面附近的非喷涂需要加以保护,可以用耐热的玻璃布或石棉来屏蔽起来。
超音速电弧喷涂技术

防磨防腐新材料超音速电弧喷涂技术一、超音速电弧喷涂的原理电弧喷涂原理是利用两根连续送进的金属丝作为自耗电极,在其端部产生电弧作为热源,用压缩空气将熔化了的丝材雾化,并以超音速喷向工作件形成一种结合强度高、孔隙率低、表面粗糙度低的涂层的热喷涂方法。
其工作原理与普通电弧喷涂(亚音速雾化)一样,超音速电弧喷涂是一个不断连续进行的熔化-雾化-沉积的过程。
但在雾化方式上,超音速电弧喷涂与普通电弧喷涂有根本的区别,即超音速电弧喷涂是采用超音速雾化。
其优点是:雾化效果好,雾化后的粒子细小均匀,速度高,有利于获得高质量的涂层。
超音速电弧喷涂采用拉伐尔喷嘴,将气流的速度从亚音速提高到超音速,加强了气流对粒子的加速效果,从而提高了粒子速度。
粒子速度对涂层的性能有很大的影响。
粒子速度高,粒子沉积时对基体的撞击作用就强,粒子变形就充分。
有利于粒子与基体、粒子与粒子之间的结合,从而提高涂层的结合强度和内聚强度;粒子速度高,粒子沉积前在空气中的飞行时间短,飞行中产生的氧化物就少,有利于粒子的结合,从而提高涂层的内聚强度,降低涂层的孔隙率。
粒子速度越高,越有利于获得高质量的涂层。
随着热喷涂设备的更新换代,粒子速度在不断提高,涂层的质量也不断得到改善。
超音速雾化减小了粒子的粒度,降低了涂层的粗糙度。
粗糙度是涂层的一项重要性能指标,它取决于雾化后粒子的粒度。
超音速雾化加强了气流对丝材端部熔化金属间的作用,雾化的粒子细小均匀,大大降低了涂层的粗糙度。
同时,粒子粒度的减小,也降低了粒子扁平化过程中的飞溅,有利于降低涂层的孔隙率。
超音速雾化是超音速电弧喷涂的出发点,是其与普通电弧喷涂的根本区别。
超音速电弧喷涂设备包括电源、喷枪、送丝机构及其附件,关键设备是超音速电弧喷枪。
我公司采用进口喷嘴,并且喷涂电流稳定,能在保证丝材雾化效果、涂层质量的前提下,一天的喷涂面积达到20m2。
电弧喷涂时,弧区的温度高达5000-6000℃,用气冷的方式对喷嘴进行冷却。
超音速火焰喷涂工艺流程
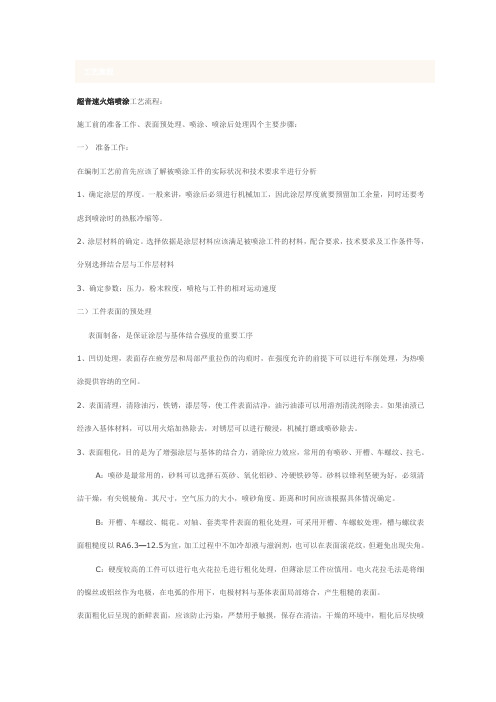
超音速火焰喷涂工艺流程:施工前的准备工作、表面预处理、喷涂、喷涂后处理四个主要步骤:一)准备工作:在编制工艺前首先应该了解被喷涂工件的实际状况和技术要求半进行分析1、确定涂层的厚度。
一般来讲,喷涂后必须进行机械加工,因此涂层厚度就要预留加工余量,同时还要考虑到喷涂时的热胀冷缩等。
2、涂层材料的确定。
选择依据是涂层材料应该满足被喷涂工件的材料,配合要求,技术要求及工作条件等,分别选择结合层与工作层材料3、确定参数:压力,粉末粒度,喷枪与工件的相对运动速度二)工件表面的预处理表面制备,是保证涂层与基体结合强度的重要工序1、凹切处理,表面存在疲劳层和局部严重拉伤的沟痕时,在强度允许的前提下可以进行车削处理,为热喷涂提供容纳的空间。
2、表面清理,清除油污,铁锈,漆层等,使工件表面洁净,油污油漆可以用溶剂清洗剂除去。
如果油渍已经渗入基体材料,可以用火焰加热除去,对锈层可以进行酸浸,机械打磨或喷砂除去。
3、表面粗化,目的是为了增强涂层与基体的结合力,消除应力效应,常用的有喷砂、开槽、车螺纹、拉毛。
A:喷砂是最常用的,砂料可以选择石英砂、氧化铝砂、冷硬铁砂等。
砂料以锋利坚硬为好,必须清洁干燥,有尖锐棱角。
其尺寸,空气压力的大小,喷砂角度、距离和时间应该根据具体情况确定。
B:开槽、车螺纹、辊花。
对轴、套类零件表面的粗化处理,可采用开槽、车螺蚊处理,槽与螺纹表面粗糙度以RA6.3—12.5为宜,加工过程中不加冷却液与滋润剂,也可以在表面滚花纹,但避免出现尖角。
C:硬度较高的工件可以进行电火花拉毛进行粗化处理,但薄涂层工件应慎用。
电火花拉毛法是将细的镍丝或铝丝作为电极,在电弧的作用下,电极材料与基体表面局部熔合,产生粗糙的表面。
表面粗化后呈现的新鲜表面,应该防止污染,严禁用手触摸,保存在清洁,干燥的环境中,粗化后尽快喷涂,一般喷涂时间不超过二个小时。
4、非喷涂部位的保护喷涂表面附近的非喷涂需要加以保护,可以用耐热的玻璃布或石棉而屏蔽起来。
- 1、下载文档前请自行甄别文档内容的完整性,平台不提供额外的编辑、内容补充、找答案等附加服务。
- 2、"仅部分预览"的文档,不可在线预览部分如存在完整性等问题,可反馈申请退款(可完整预览的文档不适用该条件!)。
- 3、如文档侵犯您的权益,请联系客服反馈,我们会尽快为您处理(人工客服工作时间:9:00-18:30)。
汽轮机低压转子末级叶片水蚀部位Jet-Kote®超音速喷涂保护项目介绍
第一章概述
第一节末级叶片水蚀部位JK超音速喷涂保护简介
现役机组中,低压转子末级叶片处于特殊湿蒸汽区,在小流量、低真空工况下,叶片水蚀损伤或多或少存在。
叶片水蚀后,轻者增加叶片表面粗糙程度,蒸汽效能减弱;重者在叶片水蚀部位缺损处产生裂纹,经长期运行后会导致叶片断裂,引发事故。
通过多家火力发电厂多台次、不同类型机组现场超音速喷涂保护应用效果来看,JK135超音速保护涂层,能够阻止叶片水蚀或减缓水蚀速度,有效延长叶片使用寿命,降低机组检修费用,并提高机组运行的安全性。
第二节 JK超音速喷涂发展史
现代工业的发展对各类机械零件的性能提出了更高的要求,与之对应,对材料的研制及其加工工艺提出了挑战。
基于对工件综合性能及性能价格比的考虑,单一材料显然无法满足要求。
在这种情况下,各类硬面技术(Hardfacing)、喷涂工艺应运而生,并获得长足发展。
早在上世纪70年代,美国的Browning工程公司发明了JK超音速喷涂,1983年获得美国专利。
1986年该专利转到了美国Deloro Stellite (集团)公司,由美国Deloro Stellite (集团)公司统一开发、销售,并提供技术服务。
1987年上海司太立有限公司从美国Deloro Stellite (集团)公司引进了这种国际上最先进的设备及相关专利技术,使之服务于中国经济。
经过十几年的不懈努力,上海司太立有限公司已熟练地使用
此工艺,并在航空航天、石油、电力、造纸、化工等行业广泛应用。
第二章末级叶片水蚀部位JK超音速喷涂
保护介绍
第一节 JK超音速喷涂保护工艺原理
JK超音速喷涂保护是美国DELORO STELLITE(集团)公司专利工艺。
其原理是采用干净、蒸汽压高、热焓值大的丙烯气体和高压氧气,使两者通过特殊设计的喷枪,以4~5马赫的速度产生高速燃气流。
在氮气引导保护下,涂层材料粒子被注入燃气流内加速,从而形成高动能粒子束。
粒子与工件表面接触后实现机械嵌合,进而形成保护层。
由于JK超音速喷涂系统产生的燃气流温度适中;粒子加速过程中吸收热量很少;粒子的飞行速度很高;尺寸微小,因此形成的保护层具有结合强度高、致密度高、均一性好等特点。
第二节 JK超音速喷涂保护设备构成
JK超音速喷涂保护使用美国DELORO STELLITE(集团)公司原装进口JET-KOTE®超音速喷涂系统及JK3000®型喷枪。
美国DELORO STELLITE(集团)公司作为超音速喷涂的创始人,其工艺、设备、材料经过多年不断完善,制备的超音速保护涂层,性能达到国际领先水平。
其JK135超音速保护涂层经美国最大的航空发
动机制造商–通用飞机公司系统评估,其结合强度达到65MPa以上,致密度超过99%,具有优越的耐高温氧化、耐冲蚀、耐磨料磨损性能。
通用飞机公司现全部采用该涂层对生产的涡轮发动机主要部件(叶片、燃料喷嘴、发动机密封面等)进行保护处理。
JK超音速喷涂保护设备构成如下图:
第三节末级叶片水蚀部位JK超音速喷涂保护使用材料1)气体材料
●燃料气●导燃气:氧气(O2)
主燃料气:丙烯(C3H6)●载粉气:氮气(N2)
导向燃料气:氢气(H2)
2)喷砂毛化材料:A级棕刚玉砂, 颗粒规格为A f 36~46。
3)涂层材料
针对汽轮机低压转子末级叶片水蚀机理及特点,选用美国DELORO STELLITE(集团)公司原装进口JKl35金属陶瓷材料。
JKl35为质地高度均匀的碳化物-镍铬钴合金复合粉末,尺寸规格为325目/D。
第四节末级叶片水蚀部位JK超音速喷涂保护施工流程1)在施工现场组装自备喷涂工作棚。
2)确定末级叶片喷涂保护部位。
3)制作喷涂挡板。
4) 设备管路连接、检漏及调试。
5) 喷涂保护部位毛化处理。
6) 清洗喷涂保护部位。
7) 设备试运行,喷涂涂层试样。
8) 正式喷涂保护作业。
第五节 JK超音速喷涂保护质量保证及验收
1)JK超音速喷涂保护质量保证
在国内表面工程行业中,上海司太立有限公司是唯一一家由百余年历史的美国DELORO STELLITE(集团)公司控股的外资企业,其产品曾获得过多个国家、国际组织和国际知名企业(ISO—9001、GTS、TÜV、ROLLS-ROYCE)高等级质量认证。
JK超音速喷涂系统制备的JKl35保护涂层,除经美国最大的航空发动机制造商–通用飞机公司系统评估,又经国内最大的航空发动机制造商–西安航
空发动机(集团)有限公司的国家双认证“理化检测中心”检测,并经原国家电力工业部“热力发电设备及材料质量检验测试中心”确认,其质量不低于美国通用公司合格涂层性能。
经过近几年的不懈努力,国内多家火力发电厂多台次、不同类型机组(上汽、北汽、哈汽、东汽)应用了JK超音速喷涂现场保护或预保护叶片技术,实践证明JK135保护涂层质量可靠,提高叶片使用寿命效果明显。
2)JK超音速喷涂保护质量验收
在ISO9001质量认证体系中,JK超音速喷涂保护,属于一种特殊工艺,不能通过传统的检验方法进行质量评定。
即涂层性能是靠设备、材料的选用,过程控制及作业人员的规范化操作来保证的。
为此,我们可为用户提供JK135保护涂层试样,供用户进行涂层性能检测。
相关标准:《热喷涂涂层结合强度测试标准》 ASTM.C-633 《热喷涂涂层耐磨料磨损性能测试标准》ASTM.G-99
《热喷涂涂层耐腐蚀性能测试标准》 ASTM.G-90
《热喷涂涂层盐喷试验测试标准》 ASTM.B-117
第六节相关情况
1)汽轮机低压转子末级叶片水蚀机理及特点
汽轮机低压转子末级叶片处于特殊湿蒸汽区,该区域内汽流含有一定量大小不同的液滴。
液滴直径不同,其流速也不同,它们以不同的速度、角度,撞击叶片的叶顶进汽边背弧不同宽度及
高度处。
其撞击叶片表面有两个运动过程,初始阶段在表面形成很高压力,然后沿叶片表面向四周飞速扩散并伴随产生激波阵面。
激波阵面随之形成对叶片表面的冲击波,使叶片表面逐渐变形和硬化,从而导致疲劳裂纹产生并逐渐扩散,形成碎片导致剥落,叶片表面呈现锯齿状及凹坑,随之应力在该处集中,严重的还导致叶片断裂。
另外,末级叶片在小流量、低真空工况下,叶片底部负反动度会变得很大,使叶片出口边下半部形成大范围的回流区。
回流的蒸汽携带着液滴撞击叶片下半部出汽边背弧,使其产生0.5~1.5mm深的齿状小缺口,水蚀宽度一般为5~10mm,高度为200~400mm。
根据对680、700型叶片的应力计算和测量显示,叶片底部出汽边0~300mm范围内承受着巨大的离心拉应力和较大的振动应力。
相关部门对多地区不同类型汽轮机70多组末级叶片水蚀导致叶片断裂事故的统计分析,叶根出汽边背弧事故率占到80%以上。
因而叶片型线底部出汽边背弧的水蚀比叶顶进汽边背弧的水蚀有更大的安全危害性。
2)汽轮机低压转子末级叶片采取的防水蚀措施现状
功率为50MW及大于50MW以上的汽轮机低压转子末级叶片,出现叶顶进汽边背弧及叶根出汽边背弧的水蚀损伤,是普遍存在的问题。
就损伤程度而言,叶顶进汽边背弧水蚀损伤明显大于叶根出汽边背弧;从叶片受力状态来分析,叶根出汽边背弧水蚀损
伤对叶片运行的安全危险性远大于叶顶进汽边背弧。
因此对叶根出汽边背弧与叶顶进汽边背弧采取保护措施同等重要。
国内现役机组中,汽轮机制造厂除在低压转子末级叶片叶顶进汽边背弧采取防水蚀保护措施(钎焊司太立合金片、电火花强化、高温表面淬火硬化、表面渗氮)外, 叶根出汽边背弧并未采取防水蚀保护措施。
而且对于运行10~15年以上的末级叶片叶顶进汽边背弧,除钎焊司太立合金片的部位,还保留部分合金片外,其它防水蚀处理工艺的硬化层已被水蚀殆尽。
JK超音速喷涂保护,可在汽轮机大修现场,对叶根出汽边背弧和叶顶进汽边背弧都进行保护处理。
由于其喷涂设备及材料先进、操作工艺及过程控制严格,涂层具有极佳的抗水蚀、耐磨损、耐高温氧化性能。
通过多家火力发电厂多台次、不同类型机组现场超音速喷涂保护应用效果来看,其能够阻止叶片水蚀或减缓水蚀速度,有效延长叶片使用寿命,降低机组检修费用,并提高机组运行的安全性。
JK超音速喷涂保护是一颗耀眼的明星,让我们共同携起手来,真诚合作,为电力行业汽轮机组的安全、经济运行作出贡献。