连铸坯热送系统数学模型及综合效益分析
连铸坯热装热送系统的自动化控制策略优化技术改进
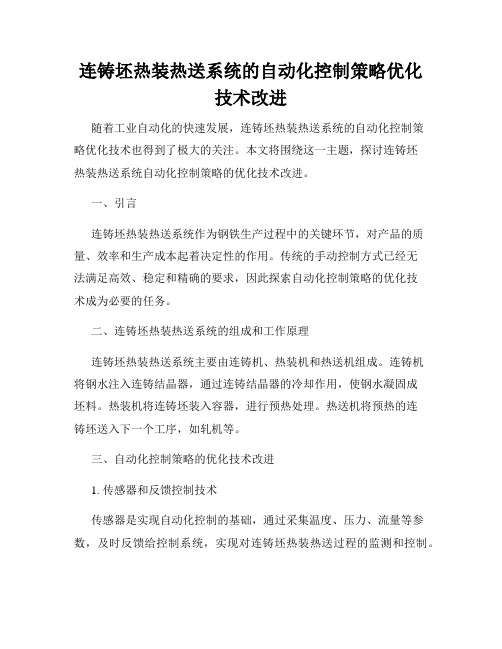
连铸坯热装热送系统的自动化控制策略优化技术改进随着工业自动化的快速发展,连铸坯热装热送系统的自动化控制策略优化技术也得到了极大的关注。
本文将围绕这一主题,探讨连铸坯热装热送系统自动化控制策略的优化技术改进。
一、引言连铸坯热装热送系统作为钢铁生产过程中的关键环节,对产品的质量、效率和生产成本起着决定性的作用。
传统的手动控制方式已经无法满足高效、稳定和精确的要求,因此探索自动化控制策略的优化技术成为必要的任务。
二、连铸坯热装热送系统的组成和工作原理连铸坯热装热送系统主要由连铸机、热装机和热送机组成。
连铸机将钢水注入连铸结晶器,通过连铸结晶器的冷却作用,使钢水凝固成坯料。
热装机将连铸坯装入容器,进行预热处理。
热送机将预热的连铸坯送入下一个工序,如轧机等。
三、自动化控制策略的优化技术改进1. 传感器和反馈控制技术传感器是实现自动化控制的基础,通过采集温度、压力、流量等参数,及时反馈给控制系统,实现对连铸坯热装热送过程的监测和控制。
优化技术改进的关键在于选择合适的传感器,并进行准确可靠的数据采集。
2. 模型预测控制技术模型预测控制技术是一种基于数学模型的优化控制方法,通过预测系统的状态和性能,优化控制策略的参数。
在连铸坯热装热送系统中,通过建立准确的数学模型,预测连铸坯的温度、形状和质量等参数,以实现系统的优化控制。
3. 协调控制技术连铸坯热装热送系统涉及多个子系统的协调工作,如连铸机、热装机和热送机的协调控制。
优化技术改进的关键在于建立系统仿真模型,通过协调控制策略,对不同子系统之间的关系进行优化调整,以提高系统的生产效率和质量。
4. 自适应控制技术自适应控制技术可以根据系统的实际运行状况和外部环境变化,自动调整控制策略的参数。
在连铸坯热装热送系统中,考虑到钢水的温度、浓度和流速等参数会发生变化,自适应控制技术可以根据实时数据,及时调整控制策略,确保系统的稳定性和可靠性。
四、总结连铸坯热装热送系统的自动化控制策略优化技术改进是钢铁生产过程中重要的研究方向。
连铸过程原理及数值模拟

连铸过程原理及数值模拟连铸是一种重要的金属成形工艺,广泛应用于钢铁、铝合金等金属材料的生产和加工中。
连铸过程原理及数值模拟是研究连铸工艺的关键内容,通过对连铸过程的原理分析和数值模拟,可以优化连铸工艺参数,提高产品质量和生产效率。
连铸过程是将熔融金属直接注入到连续运动的铸坯中,通过冷却和凝固过程,将熔融金属转化为固态铸坯。
连铸的基本原理是利用连续运动的铸坯带走热量,使熔融金属迅速凝固,形成连续的固态铸坯。
在连铸过程中,主要包括液相区、液固两相区和固相区三个区域。
在液相区,熔融金属通过连续浇注,填充到铸坯的空腔中。
熔融金属的温度高于固相线,处于液态状态。
随着熔融金属的注入,液相区的长度逐渐增加。
在液固两相区,熔融金属和正在凝固的铸坯同时存在。
由于熔融金属的温度高于固相线,所以熔融金属仍然保持液态。
而铸坯由于受到液相的热量传递,开始逐渐凝固。
在这个区域中,液相区的长度逐渐减小,凝固铸坯的长度逐渐增加。
在固相区,整个铸坯都已经完全凝固。
熔融金属已经完全转化为固态,形成连续的固态铸坯。
在这个区域中,液相区的长度为零,凝固铸坯的长度为整个连铸过程的长度。
为了研究连铸过程的细节和优化连铸工艺参数,数值模拟成为一种重要的方法。
数值模拟是通过数学模型和计算机仿真技术,对连铸过程进行模拟和分析。
数值模拟可以准确地计算连铸过程中的温度场、流场和凝固结构等关键参数,为工艺优化提供科学依据。
在连铸过程的数值模拟中,需要考虑多个物理过程的相互作用。
首先是流体力学过程,包括熔融金属的流动和铸坯带走热量的过程。
其次是热传导过程,包括熔融金属的冷却和凝固过程。
最后是凝固结构演化过程,包括铸坯的晶粒生长和偏析等现象。
为了建立连铸过程的数值模型,需要考虑材料的物理性质、流体力学和热传导方程等方面的参数。
同时,还需要考虑边界条件和初始条件等参数。
通过数值模拟,可以预测连铸过程中的温度分布、流速分布和凝固结构等重要参数,为工艺优化提供指导。
连铸坯热装热送设备的能效评估与提升

连铸坯热装热送设备的能效评估与提升连铸坯热装热送设备在钢铁生产过程中扮演着至关重要的角色。
为了提高生产效率和降低能源消耗,评估和提升连铸坯热装热送设备的能效至关重要。
本文将从能效评估的角度讨论连铸坯热装热送设备,并提出一些建议来提升其能效。
一、能效评估方法评估连铸坯热装热送设备的能效可以采用多种方法,其中包括能耗对标法、传热模型法和能源利用率法等。
这些方法可以帮助我们全面了解设备的能源消耗情况,并定位问题所在。
例如,能耗对标法可以将不同制造工厂或设备进行比较,确定是否存在能源利用不佳的问题。
通过收集和分析能源消耗数据,可找出节能的潜力,并制定相应的改进措施。
传热模型法则借助数学模型来模拟设备的传热过程,通过分析热损失和能量流失,评估设备的热效率。
这种方法可以帮助我们确定热能损失的主要原因,并提出相应的改进建议。
另外,能源利用率法可以衡量设备在工作过程中对能量的利用程度。
通过比较能源投入和有用能量输出的比例,可以得出设备的能源利用率。
这可以帮助我们判断设备是否存在能量浪费的问题,并针对性地进行改进。
二、连铸坯热装热送设备能效提升建议1. 优化设备结构和布局:根据传热原理,合理设计设备结构和布局有助于提高传热效率。
通过优化流体动力学特性和流体通道的设计,可以减少能量损失和流体阻力,从而提升热装热送设备的能效。
2. 选用高效传热介质:合理选择传热介质可以显著提升连铸坯热装热送设备的能效。
例如,选用热导率高、对流传热能力强的介质,可以提高设备的传热效率,降低能源消耗。
3. 控制热损失:热损失是造成能效降低的主要原因之一。
采取合适的保温措施,如使用保温材料包覆设备、减少热辐射和对流散热等方法,可以有效降低能量的损失,提高热装热送设备的能效。
4. 定期维护和检修:连铸坯热装热送设备在长时间运行后往往存在磨损和结垢等问题,导致能效下降。
定期进行维护和检修,清除结垢,更换磨损部件,可以保持设备的正常运行和高效工作。
连铸坯热装热送过程中的传质特性研究与模拟优化改进

连铸坯热装热送过程中的传质特性研究与模拟优化改进连铸坯热装热送是钢铁工业中重要的生产过程,涉及到钢水的传质特性、温度分布以及坯料质量等诸多问题。
为了提高连铸坯的质量和生产效率,研究人员不断探索和改进相关技术,本文旨在探讨连铸坯热装热送过程中的传质特性,并提出模拟优化改进方案。
1. 传质特性研究连铸坯热装热送过程中的传质特性是影响钢水质量和坯料性能的重要因素之一。
在传质过程中,钢水与周围环境之间的质量交换起着关键作用。
传质过程中的传热、传质速率、温度分布等参数都会影响坯料的结晶行为和内部组织结构。
因此,深入研究传质特性对于提高连铸坯质量非常重要。
2. 温度分布模拟在连铸坯热装热送过程中,温度分布对于铸坯的质量具有重要影响。
通过建立数学模型,可以对温度分布进行模拟,以便了解钢水在装入和运输过程中的温度变化情况。
模拟结果可以指导实际生产中的工艺优化和质量控制,提高坯料的结晶性能和整体质量。
3. 优化改进方案基于传质特性研究和温度分布模拟的结果,我们可以提出一些优化改进方案,以进一步提高连铸坯的质量和生产效率。
其中一项可能的改进方案是优化钢水的注入方式,以确保坯料内部温度分布更为均匀,减少板坯内部的温度梯度。
另外,可以通过改变连铸坯的凝固过程,控制结晶方式,调整浇注温度和浇注速度等参数,以提高连铸坯的结晶结构和性能。
4. 模拟优化方法为了对连铸坯热装热送过程进行优化,模拟方法是一种有效的工具。
基于数值模拟,可以对连铸坯的传质特性和温度分布进行精确预测,并基于模拟结果进行进一步的优化设计。
常用的模拟方法包括计算流体力学(CFD)和有限元分析(FEA)等技术。
这些方法可以帮助我们更好地理解热装热送过程的规律,并提供指导生产的依据。
5. 结论连铸坯热装热送过程中的传质特性对于钢铁行业的发展具有重要意义。
研究连铸坯的传质特性、温度分布以及优化改进方案,可以提高坯料的质量和生产效率。
通过模拟方法,可以预测和优化连铸坯热装热送过程中的各项参数,为实际生产提供有力的技术支持。
连铸坯热装热送攻关方案的实验与验证

连铸坯热装热送攻关方案的实验与验证随着现代工业的发展,连铸技术在钢铁行业中扮演着重要的角色。
连铸坯热装热送是一种提高连铸坯质量、减少能耗的技术手段。
本文旨在介绍连铸坯热装热送攻关方案的设计,并对其进行实验与验证。
1. 背景连铸技术是指通过连续铸造技术将钢液直接连续铸造成坯料。
连铸坯热装热送是将连铸坯在连铸机上直接进行预热,并通过热运输设备将坯料送入热轧生产线,以达到提高产品质量和能源利用效率的目的。
因此,研究连铸坯热装热送的方案具有重要的实际意义。
2. 设计方案(1)连铸坯热装热送系统设计根据连铸坯的特点和热装热送的需求,设计了连铸坯热装热送系统。
该系统包括连铸机、预热炉和热运输设备三个部分。
其中,连铸机负责将钢液进行连续铸造,预热炉用于对连铸坯进行预热,热运输设备则负责将预热坯料送到热轧生产线。
(2)能源利用方案设计在连铸坯热装热送过程中,能源的利用对于提高能耗效率至关重要。
设计了采用工业余热回收方式,对预热炉的废气进行回收利用。
通过对废气进行余热交换,提高能源的利用效率,减少能源的浪费。
(3)工艺参数设计为了实现连铸坯热装热送的效果,设计了合适的工艺参数。
包括预热炉的温度控制、热运输设备的速度调节等。
通过对工艺参数的精确控制,实现了连铸坯在短时间内达到预定的温度要求,并顺利送入热轧生产线。
3. 实验与验证(1)实验设计为了验证连铸坯热装热送方案的可行性和效果,进行了一系列实验。
在实验中,选择不同规格的连铸坯进行热装热送,记录下温度、速度等相关参数。
通过实验数据的分析,验证方案的有效性。
(2)实验结果与分析通过实验,得到了一系列数据。
根据数据分析,验证了连铸坯热装热送方案的可行性和有效性。
实验证明,在连铸坯通过预热炉预热后,坯温均匀、温度适宜,符合热轧工艺要求。
4. 结论与展望通过实验与验证,验证了连铸坯热装热送方案的可行性和有效性。
该方案在提高产品质量、减少能耗方面具有重要的意义。
在未来的工业生产中,可以进一步优化连铸坯热装热送的方案,并结合实际情况进行推广应用。
连铸坯热装热送设备的能源消耗分析与改进

连铸坯热装热送设备的能源消耗分析与改进近年来,随着工业发展的不断推进,连铸技术在钢铁生产中的应用越来越广泛。
而作为连铸生产线的重要组成部分,连铸坯热装热送设备在钢铁生产过程中起着至关重要的作用。
然而,由于设备结构和运行方式等方面存在一些问题,导致了能源消耗较高的情况。
因此,本文将就连铸坯热装热送设备的能源消耗进行分析,并提出相应的改进措施。
一、能源消耗分析连铸坯热装热送设备在钢铁生产中的能源消耗可以分为电力消耗、水消耗、燃料消耗三个方面。
1. 电力消耗连铸坯热装热送设备中的各种电动机、电加热设备、液压站等设备的用电量占据了总耗电量的主要部分。
这些设备在工作过程中需要大量的电能来驱动,由于设备数量和规模的不同,耗电量也会有所差异。
因此,在改进连铸坯热装热送设备的能源消耗时,着重考虑合理控制电动机的使用以及优化电加热设备的工作方式等措施是非常必要的。
2. 水消耗连铸坯热装热送设备在工作过程中需要大量的水来进行冷却和清洗等操作。
设备中的循环水、冷却水、诱导水等流体对钢坯进行冷却,但同时也造成了大量的水消耗。
因此,降低设备对水的需求以及合理循环利用水资源是改进能源消耗的关键之一。
3. 燃料消耗连铸坯热装热送设备中的加热炉、燃烧器等设备需要燃料进行加热操作。
这些燃料消耗不仅耗费大量的能源,同时也产生了大量的废气排放,对环境造成了一定影响。
因此,在改进连铸坯热装热送设备的能源消耗方面,燃料的选择、燃烧效率的提高等都需要引起重视。
二、改进措施为了降低连铸坯热装热送设备的能源消耗,提高设备的工作效率和节能程度,以下是一些可行的改进措施:1. 优化设备结构通过对连铸坯热装热送设备的结构进行优化,减少设备的阻力和能量损失,提高设备的工作效率。
例如优化管道设计、改进流体动力学特性等措施,可以减少管道系统中的能源损耗。
2. 引入节能设备在连铸坯热装热送设备中引入节能设备,如高效换热器、节能电机等,以降低电力消耗。
此外,可以考虑采用节能燃烧器、余热回收等技术,减少燃料消耗和废气排放。
莱钢板坯连铸机凝固传热模型
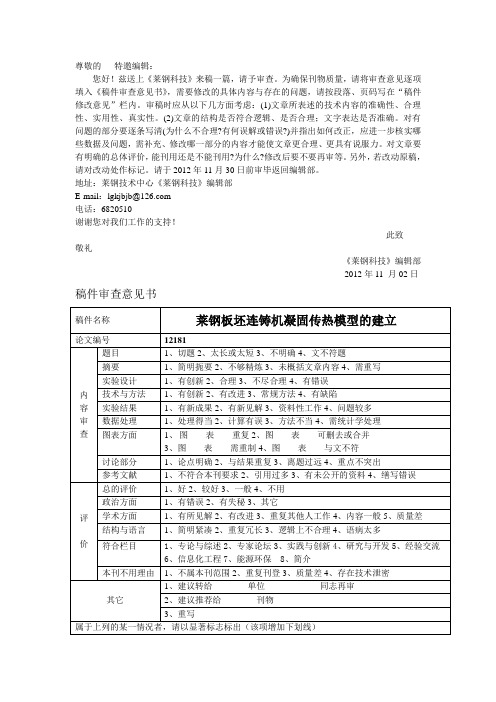
尊敬的特邀编辑:您好!兹送上《莱钢科技》来稿一篇,请予审查。
为确保刊物质量,请将审查意见逐项填入《稿件审查意见书》,需要修改的具体内容与存在的问题,请按段落、页码写在“稿件修改意见”栏内。
审稿时应从以下几方面考虑:(1)文章所表述的技术内容的准确性、合理性、实用性、真实性。
(2)文章的结构是否符合逻辑、是否合理;文字表达是否准确。
对有问题的部分要逐条写清(为什么不合理?有何误解或错误?)并指出如何改正,应进一步核实哪些数据及问题,需补充、修改哪一部分的内容才能使文章更合理、更具有说服力。
对文章要有明确的总体评价,能刊用还是不能刊用?为什么?修改后要不要再审等。
另外,若改动原稿,请对改动处作标记。
请于2012年11月30日前审毕返回编辑部。
地址:莱钢技术中心《莱钢科技》编辑部E-mail:lgkjbjb@电话:6820510谢谢您对我们工作的支持!此致敬礼《莱钢科技》编辑部2012年11 月02日稿件审查意见书需要修改的具体内容与存在问题莱钢连铸板坯凝固传热模型的建立吴会亮1,李生根1,陈永生2,肖强2(1.莱钢技术中心;2.莱钢型钢炼钢厂,莱芜 271104)摘要:连铸坯凝固传热数学模型研究的基本思路是基于凝固传热理论,根据能量守恒定律,建立二维非稳态传热模型,建立模型的内容包括:基本假设、凝固传热方程、边界条件以及初始条件的确定、连铸坯凝固传热数学模型的求解(边界条件、物性参数的确定等),然后进行程序编制。
本研究中,根据莱钢型钢炼钢厂4#连铸机现场实际条件,建立了中碳钢的宽板坯凝固传热模型。
关键词:边界条件;固相分率;导热系数;传热模型0 前言连铸二冷水工艺是连铸的三大核心工艺之一,对连铸生产和铸坯质量有着重要影响。
二冷控制模型主要是通过计算铸流方向上的凝固坯壳厚度与表面温度,并根据与生产工艺温度的比较差异来调节水量,其核心是连铸坯凝固传热数学模型。
铸坯沿拉坯方向被分成若干小切片,依据铸坯从结晶器移动开始贯穿整个铸流,对于每一个切片的实际铸坯生长期进行跟踪并且对坯壳厚度按周期计算,一维时间的温度曲线描述了铸坯表面直到中心各点处的温度情况。
连铸坯热装热送系统的自动化控制策略优化方案

连铸坯热装热送系统的自动化控制策略优化方案随着工业技术的不断发展,连铸工艺在钢铁行业中的应用越来越广泛。
连铸坯热装热送系统作为整个连铸流程中的关键环节,其自动化控制策略的优化对于提高生产效率、降低能耗具有重要意义。
本文将从控制系统结构、控制策略优化等方面来讨论连铸坯热装热送系统的自动化控制策略优化方案。
一、控制系统结构连铸坯热装热送系统的自动化控制系统一般包括数据采集、数据传输、控制单元、执行单元等模块。
其中,数据采集模块负责采集温度、压力等关键参数的数据;数据传输模块将采集到的数据传输给控制单元;控制单元根据传输过来的数据进行处理,并输出合适的控制指令;执行单元接收控制指令并对系统进行相应的运行控制。
为了提高控制系统的稳定性和可靠性,可以考虑引入分布式控制结构,将控制单元和执行单元分离,以降低控制信号传输的时延。
二、控制策略优化1. 基于模型预测控制模型预测控制(MPC)是一种基于数学模型对系统进行优化控制的策略。
通过对连铸过程中各个环节的温度、压力和流量等参数进行建模,并结合系统约束条件,可以在保证连铸坯质量的前提下,实现热装热送过程中能耗的最小化。
MPC可以有效地克服传统控制策略中的滞后性和非线性问题,提高系统的动态响应速度和控制精度。
2. 优化控制算法针对连铸坯热装热送系统的特点,可以引入一些优化控制算法,如遗传算法、神经网络等。
这些算法可以在控制过程中实时调整控制参数,以适应系统动态的变化。
通过优化控制算法的运用,可以提高连铸坯的质量稳定性和产品的均匀性。
3. 开关控制策略在连铸坯热装热送系统中,往往存在多个阀门、泵和加热设备等执行元件,开关控制策略可以使这些元件在适当的时刻开启和关闭,以达到系统的自动化调节。
通过合理设置控制逻辑和参数,可以实现连铸坯在整个过程中的温度和流量的平稳控制。
4. 自适应控制策略连铸坯热装热送过程中,受到环境温度、气氛控制等外部因素的影响较大。
为了稳定系统的控制效果,可以引入自适应控制策略。
- 1、下载文档前请自行甄别文档内容的完整性,平台不提供额外的编辑、内容补充、找答案等附加服务。
- 2、"仅部分预览"的文档,不可在线预览部分如存在完整性等问题,可反馈申请退款(可完整预览的文档不适用该条件!)。
- 3、如文档侵犯您的权益,请联系客服反馈,我们会尽快为您处理(人工客服工作时间:9:00-18:30)。
连铸坯热送系统数学模型及综合效益分析 高仲龙 蒋杨虎 董补全 温 治 张欣欣 (北京科技大学) 刘铁树 解 雯 庄国伟 (宝山钢铁(集团)公司)
摘 要 概要地介绍了连铸坯热送系统的工艺、热送过程的数学模型以及连铸坯热送的综合效益。 关键词 连铸坯 热送 数学模型
MATHEMATICAL MODEL OF HOT CHARGING OF CONTINUOUS CASTING SLAB AND ANALYSIS OF COMPREHENSIVE BENEFIT GAO Zhonglong JIANG Yanghu DONG Buquan WEN Zhi ZHANG Xinxin (University of Science and Technology Beijing) LIU Tieshu XIE Wen ZHUANG Guowei (Baoshan Iron and Steel Corp.)
ABSTRACT This paper briefly introduces the technology of hot charging of continuous casting slab,the mathematical model of hot charging process and the comprehensive benefit of hot charging of continuous casting slab. KEY WORDS continuous casting slab,hot charging,mathematical model
1 前言
钢铁联合企业从钢到材的生产中有大量炉料余热。据统计,炉料余热占炉子余热总资源的40 %以上,炉料余热中也包括连铸坯的载热资源,应尽可能地加以利用。 连铸坯热送,从而实现热装炉,是连铸技术的一项重大突破,可以取得节能、降耗、高产等综合经济效益,而且对改革传统的钢铁工业结构具有深远的意义。
2 热送工艺 2.1 热装 该工艺连铸坯的热装温度为400~700 ℃,在工艺流程上连铸和热轧可以各自独立地编制生产计划,可在连铸机和加热炉之间设置保温设备(如保温坑、保温车等),保温设备在其间起着生产的缓冲和协调作用。 2.2 直接热装 该工艺连铸坯装炉温度为700~1 000 ℃,连铸坯生产的序号与装炉序号要一致,这就要求连铸与热轧生产一体化。直接热装的综合经济效益比热装还好,但组织生产的难度较大,直接热装是热送工艺的进一步发展。 2.3 直接轧制 该工艺连铸坯在1 100 ℃条件下不经加热炉,在输送过程中通过边角补热装置直送轧机轧制。直接轧制工艺对连铸与热轧一体化生产的要求更高,由于取消了加热炉这道工序,其综合经济效益最高,而实现的难度就更大。 生产中可根据当时的坯温条件组织不同的工艺,其优先顺序是:首先力争直接轧制,条件不够时则争取直接热装,条件再不够则采用热装,当然连热装条件都不够时只好冷装。 生产中采用哪种热送工艺取决于连铸坯的热状态,即连铸坯在任意时刻(任意地点)的温度场、凝固场、载热量等,为此要用数学模型来确定连铸坯在热送系统全部过程的热状态参数。再根据热送工艺特点合理地控制炉子的供热(能耗)和生产节奏(生产率),以取得节能、降耗和高产的综合经济效益。
3 数学模型 3.1 连铸坯凝固过程数学模型 计算不同连铸工艺条件下不同钢种连铸坯的温度分布,从而为后面的铸坯输送过程计算提供准确的初始条件。模型计算涉及的区域包括:结晶器、二冷区以及二冷区终了到切割点为止的空冷区。描述连铸坯凝固过程的导热方程为
(1) 式中 ρ——密度; c——比热容; θ——温度; t——时间; λ——导热系数; F——相变热源的分布特征函数; x、y、z——空间坐标。 如连铸坯为矩形断面,式(1)可以表达为二维问题,相变潜热用等效热容方式处理后,导热方程(适用于连铸坯热送全过程)表达为
(2) 式中 ce——等效比热容, (3) 式中cl——液相比热容; cs——固相比热容; θl——液相线温度; θs——固相线温度; L——凝固潜热; fs——固相率。 计算的初始条件用钢液的浇注温度。边界条件在结晶器和二冷区的表面热流密度用牛顿冷却定律计算
q=h(θ-θ′) (4) 式中 q——表面热流密度; h——对流换热系数; θ(T)——连铸坯表面温度(绝对温度); θ′(T′)——冷却水温度(绝对温度)。 在空冷区连铸坯表面热流密度包括对空间的辐射换热和对流换热。
q=εsσo(T4-T4a)+hc(θ-θa) (5) 式中 εs——连铸坯表面黑度; σo——黑体辐射常数; hc——连铸坯表面与周围空间的自然对流换热系数; θa(Ta)——周围介质的温度(绝对温度)。 3.2 连铸坯辊道输送冷却过程数学模型 计算的初始条件为连铸坯在切割点处的温度场。边界条件分两种情况。 (1) 辊道上面加盖保温罩。连铸坯上表面热流密度包括与罩内表面的辐射换热以及罩内空气对连铸坯上表面的自然对流换热。
q=εswσo(T4-T4w)φsw+hc(θ-θa) (6) 式中 εsw——连铸坯上表面对保温罩内壁辐射换 热系统黑度; φsw——连铸坯上表面对保温罩内壁辐射角系数; θw(Tw)——保温罩内表面温度(绝对温度)。 罩的内表面温度与罩的散热有关,罩的导热可处理为厚度方向的一维问题,因为罩的厚度比其长宽尺寸小很多。
(7) 式中 ρw、cw、λw——罩的密度、比热容、导热系数。
罩外表面的散热热流密度包括对空间的辐射换热和对流换热,计算式的形式与式(5)相同。 (2) 辊道上面无保温罩。连铸坯上表面裸露在大气空间,其上表面热流密度为对空间的辐射换热与对流换热之和,计算式的形式与式(5)相同。 连铸坯下表面面向辊道和地坑,与辊道接触的瞬间属接触导热冷却,考虑到瞬间热流仅作用到铸坯和辊道的表层,故可作为半无限厚物体的导热问题处理。
(8) 式中θj为连铸坯下表面与辊道接触处温度。
非接触处为连铸坯下表面对辊道、地坑的辐射换热以及坑内空气的自然对流换热,计算式的形式与式(5)相同。 辊道输送冷却过程数学模型适用于生产流程中的如下两段: (1) 连铸坯从切割点到入保温设备之前; (2) 连铸坯从出保温设备到入加热炉之前。 实际生产中不可避免地要有连铸坯从生产线上掉队而落地放置,如下线坯数量多应码垛放置,这样既减少车间占地又可减少连铸坯的散热,下线坯散热的表面热流密度计算式与式(5)相同。 3.3 连铸坯保温过程数学模型 连铸坯在保温设备(保温坑或保温车等)中表面热流密度计算式的形式与式(6)相同。连铸坯在保温设备中均叠落成垛放置,垛内各坯均用式(2)计算。保温设备墙壁导热以及对外散热的计算式形式与式(7)、(5)相同。 3.4 连铸坯在加热炉内加热过程数学模型 应用该模型得出不同情况下炉子的优化加热制度,即温度制度和供热制度,为在线优化控制提供依据,连铸坯在炉内的表面热流密度为
q=ησo(T4f-T4)+hf(θf-θ) (9) 式中 η——炉膛内总括吸收率; hf——炉内对流换热系数; θf(Tf)——炉温(绝对温度)。 关于炉墙导热及对外散热的计算式形式与式(7)及式(5)相同。由于炉内结构复杂,如炉顶曲线变化及压下、炉底水管结构以及炉温不均等情况将使炉膛内辐射换热、连铸坯内温度场计算复杂化,增加了计算难度,计算应细化的程度视工程需要而定。 炉子的供热制度要通过炉膛热平衡数学模型来确定。通过炉膛各段的区域热平衡计算各炉区的燃料供给量,进一步算出燃料总消耗量、炉膛热效率、废气出炉温度以及炉子燃耗、产量等技术经济指标。 上述各个子过程数学模型构成了连铸坯热送系统全过程数学模型,各个子过程数学模型均结合具体生产情况进行离线仿真运算,所得计算结果经生产实测数据验证表明,数学模型可用 。 为了满足生产运行的需要,可以用热送系统数学模型离线仿真所得的一系列数据进行回归处理,从而建立在线控制用数学模型,在线数学模型的突出特点是算式简单,运算速度快。 热送系统数学模型还可用于分析设备和工艺过程,提出改进和完善措施。
4 综合效益分析 以连铸板坯(尺寸为0.25 m×1.25 m×12 m)为例进行热送效果的综合分析。 4.1 辊道加罩保温 数学模型计算和实测表明:随环境和钢种不同,板坯在裸露的辊道上冷却,温降为4~6.5 ℃/min。而辊道上加盖保温罩后,板坯温降为2.5 ~5.5 ℃/min,即加罩后板坯温降减少1~1.5 ℃/min,说明加罩是有保温效果的。 4.2 保温设备保温 将热板坯码垛在保温坑内保温,保温坑壁用厚为65 mm粘土砖和厚为230 mm硅藻土砖砌成。数学模型计算和实测表明:板坯垛在坑内的温降为0.2~0.4 ℃/min,仅为裸露放置的板坯温降的6 %左右,说明保温设备的保温效果非常显著。 4.3 节能 根据数模计算和实测: (1) 连铸坯装炉温度小于500 ℃时,热装温度每提高10 ℃,炉子节能约7 MJ/t; (2) 连铸坯装炉温度大于500 ℃时,热装温度每提高10 ℃,炉子节能约10 MJ/t。 当连铸坯热装温度为500 ℃时,比冷装时炉子节能约30 %。