Mathematical Model for Mixing Reactants in a Capillary Microreactor by Transverse Diffusion
Advanced Mathematical Modeling Techniques
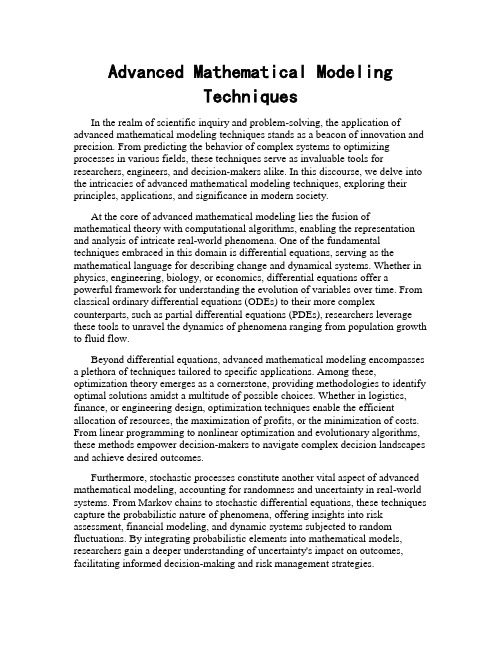
Advanced Mathematical ModelingTechniquesIn the realm of scientific inquiry and problem-solving, the application of advanced mathematical modeling techniques stands as a beacon of innovation and precision. From predicting the behavior of complex systems to optimizing processes in various fields, these techniques serve as invaluable tools for researchers, engineers, and decision-makers alike. In this discourse, we delve into the intricacies of advanced mathematical modeling techniques, exploring their principles, applications, and significance in modern society.At the core of advanced mathematical modeling lies the fusion of mathematical theory with computational algorithms, enabling the representation and analysis of intricate real-world phenomena. One of the fundamental techniques embraced in this domain is differential equations, serving as the mathematical language for describing change and dynamical systems. Whether in physics, engineering, biology, or economics, differential equations offer a powerful framework for understanding the evolution of variables over time. From classical ordinary differential equations (ODEs) to their more complex counterparts, such as partial differential equations (PDEs), researchers leverage these tools to unravel the dynamics of phenomena ranging from population growth to fluid flow.Beyond differential equations, advanced mathematical modeling encompasses a plethora of techniques tailored to specific applications. Among these, optimization theory emerges as a cornerstone, providing methodologies to identify optimal solutions amidst a multitude of possible choices. Whether in logistics, finance, or engineering design, optimization techniques enable the efficient allocation of resources, the maximization of profits, or the minimization of costs. From linear programming to nonlinear optimization and evolutionary algorithms, these methods empower decision-makers to navigate complex decision landscapes and achieve desired outcomes.Furthermore, stochastic processes constitute another vital aspect of advanced mathematical modeling, accounting for randomness and uncertainty in real-world systems. From Markov chains to stochastic differential equations, these techniques capture the probabilistic nature of phenomena, offering insights into risk assessment, financial modeling, and dynamic systems subjected to random fluctuations. By integrating probabilistic elements into mathematical models, researchers gain a deeper understanding of uncertainty's impact on outcomes, facilitating informed decision-making and risk management strategies.The advent of computational power has revolutionized the landscape of advanced mathematical modeling, enabling the simulation and analysis of increasingly complex systems. Numerical methods play a pivotal role in this paradigm, providing algorithms for approximating solutions to mathematical problems that defy analytical treatment. Finite element methods, finite difference methods, and Monte Carlo simulations are but a few examples of numerical techniques employed to tackle problems spanning from structural analysis to option pricing. Through iterative computation and algorithmic refinement, these methods empower researchers to explore phenomena with unprecedented depth and accuracy.Moreover, the interdisciplinary nature of advanced mathematical modeling fosters synergies across diverse fields, catalyzing innovation and breakthroughs. Machine learning and data-driven modeling, for instance, have emerged as formidable allies in deciphering complex patterns and extracting insights from vast datasets. Whether in predictive modeling, pattern recognition, or decision support systems, machine learning algorithms leverage statistical techniques to uncover hidden structures and relationships, driving advancements in fields as diverse as healthcare, finance, and autonomous systems.The application domains of advanced mathematical modeling techniques are as diverse as they are far-reaching. In the realm of healthcare, mathematical models underpin epidemiological studies, aiding in the understanding and mitigation of infectious diseases. From compartmental models like the SIR model to agent-based simulations, these tools inform public health policies and intervention strategies, guiding efforts to combat pandemics and safeguard populations.In the domain of climate science, mathematical models serve as indispensable tools for understanding Earth's complex climate system and projecting future trends. Coupling atmospheric, oceanic, and cryospheric models, researchers simulate the dynamics of climate variables, offering insights into phenomena such as global warming, sea-level rise, and extreme weather events. By integrating observational data and physical principles, these models enhance our understanding of climate dynamics, informing mitigation and adaptation strategies to address the challenges of climate change.Furthermore, in the realm of finance, mathematical modeling techniques underpin the pricing of financial instruments, the management of investment portfolios, and the assessment of risk. From option pricing models rooted in stochastic calculus to portfolio optimization techniques grounded in optimization theory, these tools empower financial institutions to make informed decisions in a volatile and uncertain market environment. By quantifying risk and return profiles, mathematical models facilitate the allocation of capital, the hedging of riskexposures, and the management of investment strategies, thereby contributing to financial stability and resilience.In conclusion, advanced mathematical modeling techniques represent a cornerstone of modern science and engineering, providing powerful tools for understanding, predicting, and optimizing complex systems. From differential equations to optimization theory, from stochastic processes to machine learning, these techniques enable researchers and practitioners to tackle a myriad of challenges across diverse domains. As computational capabilities continue to advance and interdisciplinary collaborations flourish, the potential for innovation and discovery in the realm of mathematical modeling knows no bounds. By harnessing the power of mathematics, computation, and data, we embark on a journey of exploration and insight, unraveling the mysteries of the universe and shaping the world of tomorrow.。
Mathematical Modelling and Numerical Analysis Will be set by the publisher Modelisation Mat
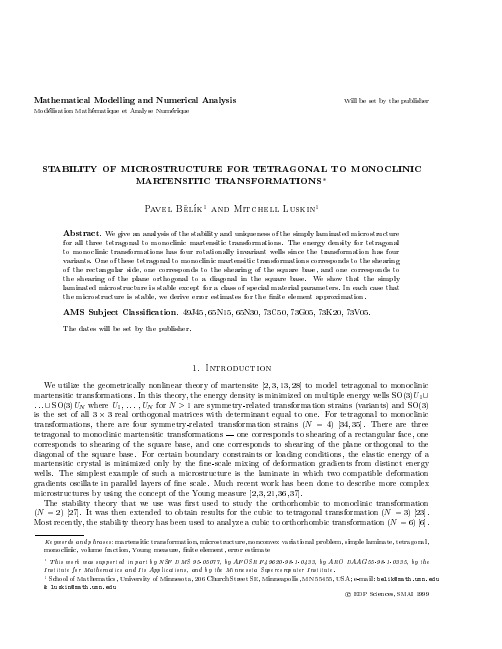
c EDP Sciences, SMAI 1999
2
PAVEL BEL K AND MITCHELL LUSKIN
In general, the analysis of stability is more di cult for transformations with N = 4 such as the tetragonal to monoclinic transformations studied in this paper and N = 6 since the additional wells give the crystal more freedom to deform without the cost of additional energy. In fact, we show here that there are special lattice constants for which the simply laminated microstructure for the tetragonal to monoclinic transformation is not stable. The stability theory can also be used to analyze laminates with varying volume fraction 24 and conforming and nonconforming nite element approximations 25, 27 . We also note that the stability theory was used to analyze the microstructure in ferromagnetic crystals 29 . Related results on the numerical analysis of nonconvex variational problems can be found, for example, in 7 12,14 16,18,19,22,26,30 33 . We give an analysis in this paper of the stability of a laminated microstructure with in nitesimal length scale that oscillates between two compatible variants. We show that for any other deformation satisfying the same boundary conditions as the laminate, we can bound the pertubation of the volume fractions of the variants by the pertubation of the bulk energy. This implies that the volume fractions of the variants for a deformation are close to the volume fractions of the laminate if the bulk energy of the deformation is close to the bulk energy of the laminate. This concept of stability can be applied directly to obtain results on the convergence of nite element approximations and guarantees that any nite element solution with su ciently small bulk energy gives reliable approximations of the stable quantities such as volume fraction. In Section 2, we describe the geometrically nonlinear theory of martensite. We refer the reader to 2,3 and to the introductory article 28 for a more detailed discussion of the geometrically nonlinear theory of martensite. We review the results given in 34, 35 on the transformation strains and possible interfaces for tetragonal to monoclinic transformations corresponding to the shearing of the square and rectangular faces, and we then give the transformation strain and possible interfaces corresponding to the shearing of the plane orthogonal to a diagonal in the square base. In Section 3, we give the main results of this paper which give bounds on the volume fraction of the crystal in which the deformation gradient is in energy wells that are not used in the laminate. These estimates are used in Section 4 to establish a series of error bounds in terms of the elastic energy of deformations for the L2 approximation of the directional derivative of the limiting macroscopic deformation in any direction tangential to the parallel layers of the laminate, for the L2 approximation of the limiting macroscopic deformation, for the approximation of volume fractions of the participating martensitic variants, and for the approximation of nonlinear integrals of deformation gradients. Finally, in Section 5 we give an application of the stability theory to the nite element approximation of the simply laminated microstructure.
MathematicalModeling理论建模及实际应用
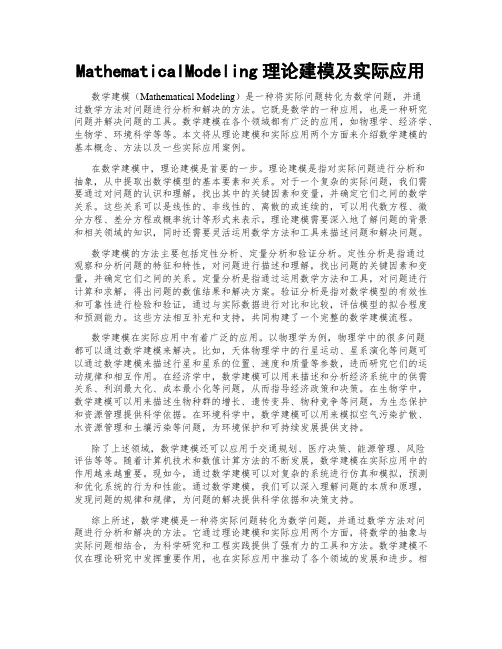
MathematicalModeling理论建模及实际应用数学建模(Mathematical Modeling)是一种将实际问题转化为数学问题,并通过数学方法对问题进行分析和解决的方法。
它既是数学的一种应用,也是一种研究问题并解决问题的工具。
数学建模在各个领域都有广泛的应用,如物理学、经济学、生物学、环境科学等等。
本文将从理论建模和实际应用两个方面来介绍数学建模的基本概念、方法以及一些实际应用案例。
在数学建模中,理论建模是首要的一步。
理论建模是指对实际问题进行分析和抽象,从中提取出数学模型的基本要素和关系。
对于一个复杂的实际问题,我们需要通过对问题的认识和理解,找出其中的关键因素和变量,并确定它们之间的数学关系。
这些关系可以是线性的、非线性的、离散的或连续的,可以用代数方程、微分方程、差分方程或概率统计等形式来表示。
理论建模需要深入地了解问题的背景和相关领域的知识,同时还需要灵活运用数学方法和工具来描述问题和解决问题。
数学建模的方法主要包括定性分析、定量分析和验证分析。
定性分析是指通过观察和分析问题的特征和特性,对问题进行描述和理解,找出问题的关键因素和变量,并确定它们之间的关系。
定量分析是指通过运用数学方法和工具,对问题进行计算和求解,得出问题的数值结果和解决方案。
验证分析是指对数学模型的有效性和可靠性进行检验和验证,通过与实际数据进行对比和比较,评估模型的拟合程度和预测能力。
这些方法相互补充和支持,共同构建了一个完整的数学建模流程。
数学建模在实际应用中有着广泛的应用。
以物理学为例,物理学中的很多问题都可以通过数学建模来解决。
比如,天体物理学中的行星运动、星系演化等问题可以通过数学建模来描述行星和星系的位置、速度和质量等参数,进而研究它们的运动规律和相互作用。
在经济学中,数学建模可以用来描述和分析经济系统中的供需关系、利润最大化、成本最小化等问题,从而指导经济政策和决策。
在生物学中,数学建模可以用来描述生物种群的增长、遗传变异、物种竞争等问题,为生态保护和资源管理提供科学依据。
数学建模及仿真_1

Mathematical Modeling
主讲人:范瑾
Email: jinfan@ Office:信息学院(学院楼2号楼)216
考核方式
•平时成绩——作业,考勤10% •上机实践——实验报告30% • 考试 ——60%
<数学建模与数学实验>(第二版)赵
静 但琦, 高等教育出版社,2003年
4.模型求解。
应当借助 计算机 求出数值 解。
5.模型的分析与检验。
§1.3 数学模型的分类
分类标准
对某个实际问题了解 的深入程度
具体类别
白箱模型、灰箱模型、黑箱模型
模型中变量的特征
建模中所用的数学方 法 研究课题的实际范畴
连续型模型、离散型模型或确定性模型、随机
型模型等 初等模型、微分方程模型、差分方程模型、优 化模型等 人口模型、生 态系统模型 、交通 流模型、经 济模型、 基因模型等
x(t ) x0 e
rt
参数估计
根据最小二乘法,x0和r是以下函数的最小值:
E ( x0 , r ) ( x0e xi )
rti i 1
n
2
其中xi是ti时刻美国的人口数。 然后再代回函数计算新的时间t所对应的人口数:
x(t ) x0 e
rt
结果分析
人口将以指数规 律无限增长 1810-1870间的预 测人口数与实际 人口数吻合较好, 但1880年以后的 误差越来越大
• 通过直观观察, 猜测人口随时 间的变化规律 (即某种类型 的函数),再 用函数拟合的 方法确定其中 的未知参数。
指数增长模型
马尔萨斯提出 (1798)
基本假设 : 人口(相对)增长率 r 是常数
罗曼尼亚国防护卫舰T22号改装动力系统的自动化控制说明书
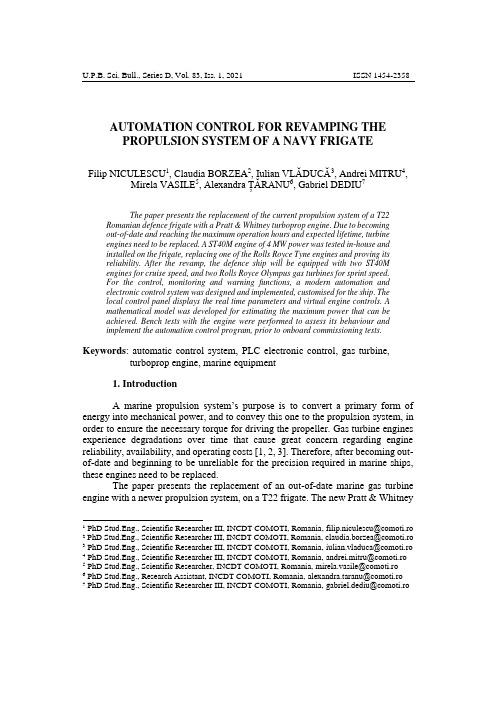
U.P.B. Sci. Bull., Series D, Vol. 83, Iss. 1, 2021 ISSN 1454-2358 AUTOMATION CONTROL FOR REVAMPING THE PROPULSION SYSTEM OF A NAVY FRIGATEFilip NICULESCU1, Claudia BORZEA2, Iulian VLĂDUCĂ3, Andrei MITRU4, Mirela VASILE5, Alexandra ȚĂRANU6, Gabriel DEDIU7The paper presents the replacement of the current propulsion system of a T22 Romanian defence frigate with a Pratt & Whitney turboprop engine. Due to becomingout-of-date and reaching the maximum operation hours and expected lifetime, turbineengines need to be replaced. A ST40M engine of 4 MW power was tested in-house andinstalled on the frigate, replacing one of the Rolls Royce Tyne engines and proving itsreliability. After the revamp, the defence ship will be equipped with two ST40Mengines for cruise speed, and two Rolls Royce Olympus gas turbines for sprint speed.For the control, monitoring and warning functions, a modern automation andelectronic control system was designed and implemented, customised for the ship. Thelocal control panel displays the real time parameters and virtual engine controls. Amathematical model was developed for estimating the maximum power that can beachieved. Bench tests with the engine were performed to assess its behaviour andimplement the automation control program, prior to onboard commissioning tests. Keywords: automatic control system, PLC electronic control, gas turbine, turboprop engine, marine equipment1. IntroductionA marine propulsion system’s purpose is to convert a primary form of energy into mechanical power, and to convey this one to the propulsion system, in order to ensure the necessary torque for driving the propeller. Gas turbine engines experience degradations over time that cause great concern regarding engine reliability, availability, and operating costs [1, 2, 3]. Therefore, after becoming out-of-date and beginning to be unreliable for the precision required in marine ships, these engines need to be replaced.The paper presents the replacement of an out-of-date marine gas turbine engine with a newer propulsion system, on a T22 frigate. The new Pratt & Whitney 1PhDStud.Eng.,ScientificResearcherIII,INCDTCOMOTI,Romania,************************* 2PhDStud.Eng.,ScientificResearcherIII,INCDTCOMOTI,Romania,************************ 3PhDStud.Eng.,ScientificResearcherIII,INCDTCOMOTI,Romania,************************ 4PhDStud.Eng.,ScientificResearcherIII,INCDTCOMOTI,Romania,********************** 5PhDStud.Eng.,ScientificResearcher,INCDTCOMOTI,Romania,***********************6PhDStud.Eng.,ResearchAssistant,INCDTCOMOTI,Romania,**************************7PhDStud.Eng.,ScientificResearcherIII,INCDTCOMOTI,Romania,***********************258 F. Niculescu, Claudia Borzea, I. Vlăducă, A. Mitru, Mirela Vasile, Alexandra Țăranu, G. Dediu ST40M is derived from the PW150A aviation turboprop engine [4]. Its power is the same as the one of the old engine, Rolls Royce Tyne [5], namely 4 MW. However, after the last capital revision of the Tyne engine, the maximum power obtained decreased to less than 3 MW.Fig. 1. T22 frigate to be revamped [6]ST40M is currently being used only on the series of Norwegian small superfast, stealth missile corvettes Skjold, powered by a Combined Gas-and-Gas (CoGaG) propulsion system consisting of four Pratt & Whitney gas turbine engines: two ST18M with output power of 2,000 kW gas turbines for cruise speed, and two larger ST40M turbines of 4,000 kW for sprint speed [7]. These gas turbines have been tailored for marine applications and offer high efficiency and low weight [8].Pratt & Whitney ST18 engines have been used for cogeneration purposes, at Suplacu de Barcău power plant, installed and commissioned by the Romanian Research and Development Institute for Gas Turbines COMOTI. The power plant was built with the aim of studying the efficiency in growing oil production with lower costs for the electrical and thermal energy used in oil field. Each line consists of an electrical generator powered by one aero derivative ST18 turbine engine, a heat recovery steam generator with afterburner, and linked installations. The ST18M proved its efficiency and reliability, with 32,000 hours between overhauls. Operating over 55,000 hours from 2004 to 2008, the two lines of the cogeneration plant provided an efficiency of 85% [9]. These gas turbines are tailored for marine applications, with high efficiency and low weight.2. Mathematical model regarding engine operationFrom energetic point of view, a marine propulsion system consists of the power source (main propulsion engine) and the energy consumer (thruster). Among currently used marine thrusters, propellers best cater for current naval technology, most frequently used, and generally most efficient type of marine propulsion [10].Automation control for revamping the propulsion system of a navy frigate 259 Pratt & Whitney delivers ST40M power prop engine (Figure 2), without the control electronics. For functioning as cruise engine, this one has to be adapted to the specific type of ship.Fig. 2. Section through the 3D CAD model of ST40M gas turbine engine The characteristic curve of ST40M gas turbine, given in the specifications [11] for natural gas fuel operation, shows the relation between the output power at shaft and the exhaust fuel gas flow. Relying on specified characteristic for power in relation with the fuel gas discharge flow, we extracted the data in Table 1, using the exhaust gas flow (G gT), calculated with the relation:G gT=G c∙(α∙L0+1)(1) where: G c–fuel flow in kg/s; α – air excess; L0 – stoichiometric coefficient iterated determining the excess air α used to calculate the power (3728 kW) from Table 1, using natural gas fuel, for which the stoichiometric coefficient L0 is 17.16.Table 1In Table 2 we determined Q cn (exhaust gas flow injected in the combustion chamber of the turboprop engine) and the maximum shaft power in relation to the experimental fuel flow.260 F. Niculescu, Claudia Borzea, I. Vlăducă, A. Mitru, Mirela Vasile, Alexandra Țăranu, G. DediuTable 2cnAt a fuel flow Q cn of 19 l/min, a maximum exhaust gas flow of 13.6 kg/s at a power of 3728.7 kW was calculated iteratively using relation (1). For this shaft power, we also determined the acceleration percentage and the fuel flow. Table 3 shows experimental data acquired, the bolded values being used for computations.Table 3Depending on the propulsion turbine speed NTL, the parabolic variation curves for acceleration (Throttle [%]), and fuel flow Q cn) were determined, which allowed to calculate the acceleration percentage at 9900 rpm, namely 81.8%. The values of the free turbine speed and fuel flow required for acceleration of 81.8% and 100% respectively were determined using the universal characteristic of the turbine given by relation (2) hereinafter.W̅̅̅TP=f(G gT,N TP)(2) where: G gT is the exhaust gas flow and N TP is the propulsion turbine speed.Automation control for revamping the propulsion system of a navy frigate 261The variation curves and their polynomial approximation equations for propulsion turbine speed and fuel flow in relation with throttle opening percentage are represented on the graphs below.a) b) Fig. 3. a) Propulsion turbine speed and b) Fuel flow, depending on throttle opening percentageHaving the temperatures before and after the propulsion turbine, using the actual diesel fuel flow Q cn in (kg/s), we can obtain the free turbine power W TP :W TP =G gT ∙(H ITT −H 6)∙ηT (3)where: H ITT and H 6 are the exhaust gas enthalpies before and after turbine, depending on exhaust gas temperatures and excess air α, consider ed constant.G gt was determined, considering the stoichiometric coefficient of diesel fuel, L 0 = 14.7. The enthalpies were calculated according to the thermodynamic tables for exhaust gases using the excess air coefficient α = 2.991 [12]. Considering turbine efficiency ηT = 0.86, we obtain the real shaft power, W TP-cor in Table 4, along with the enthalpies for ITT and T 6M , with respect to the temperatures from Table 3. The shaft power is also given according to these parameters.Table 4y = 0.0258x 2+ 70.036x + 3921.2020004000600080001000012000020*********N T P [R P M ]THROTTLE OPENING [%]Propulsion turbine speed vs. throttle opening Throttle vs. NTP y = 0.0006x2 + 0.1408x + 3.2733051015202530020406080100F U E L F L O W [L /M I N ]THROTTLE OPENING [%]Fuel flow vs. throttle opening Throttle vs. fuel flow262 F. Niculescu, Claudia Borzea, I. Vlăducă, A. Mitru, Mirela Vasile, Alexandra Țăranu, G. DediuThe subsequent graphs show the power variation with throttle opening and with exhaust gas flow respectively, in the experimental data domain.a) b) Fig. 4. Shaft power variation with: a) throttle opening and b) exhaust gas flowFrom the ST40M data [11], the maximum power is 4040 kW, for fuel flow at 100% operation, at a gas flow of 13.88 kg/s (30.6 lb/s). Thus, at an acceleration of 81.8% we would have a theoretical axis power of 3304.72 kW. The difference between the two power values is:δcalculation =(P theoretical@81.8% − W TP−corrected )Ptheoretical@81.8%∙100 =19.1% (4)It has been demonstrated that changing the fuel from natural gas to diesel can modify the parameters with 2-4%, at the same shaft power [13]. Therefore, since the ship uses diesel, the total maximum difference from the theoretical power would be about 21-22%.The propulsion turbine rotation speed NTP at maximum power would be below 12000 rpm (Figure 3), while the theoretical rotation speed is ~14000 rpm[11]. To sum up, because the lifetime of Tyne turboprop engine has shortened, both the acquired data and computations show that we would have a decrease in the maximum theoretical power with ~20%, down to 3100-3200 kW.3. Automation and electronic control system designChoosing a propulsion system for maritime applications supposes the integration of a large number of elements into a limited functional space, choosing its components (propulsion engine, gear transmission and thruster), and adjusting them according to the imposed constraints and available space, as well as arranging the components in such a configuration so as to comply with the required performance [10, 14]. The advantages of electronic control in terms of accuracy and 020406080100050010001500200025003000T h r o t t l e [%]Power [kW]Power vs. throttle opening02468101214050010001500200025003000F l o w [k g /s ]Power [kW]Power vs. Exhaust gas flowAutomation control for revamping the propulsion system of a navy frigate 263 adaptability to various differing requirements are renowned for a long time. Among the available control systems [15], electronic control currently offers the highest reliability and adaptability, and can easily and rapidly be custom tailored for any arising situation or parameter change [16]. An automated electronic control system with programmable logic controller (PLC) was designed, built, installed and tested together with the ST40 engine for the replacement of the old propulsion system.The gas turbine control is performed from the engines room of the ship, situated on the deck above the hull, where the four propulsion engines of the frigate are installed. The gas turbines control is realized from the Panel PC on the local control cabinet (LCP) interfacing the PLC. This one receives the operator’s command, analyses the cruise mode of the ship, the regimes of the other propulsion systems, and conveys the electronic command to the PLC, which triggers the actuation elements for driving the engines. The PLC also monitors and acquires the parameters for operation in optimum conditions, setting thresholds for a safe and secure operation. The Panel PC offers all the functionalities of a computer, enabling the software program modification on-site, with all sequences and parameter limits.The PLC assembly located in the local control cabinet is connected to the current adapters located in the junction boxes (temperatures – TJB, pressures – PJB, speeds and vibrations– VJB), in close proximity of the engine. The PLC’s central processing unit (CPU) communicates over Ethernet with the Panel PC on the local control cabinet in engines room, and with the control panel and tests computer in the engines control room. Bench tests (Figure 5a) of the engine with the automation system were conducted according to the ones recommended by manufacturer, after which this one was installed in the place of a Tyne on the frigate (Figure 5b).a) b)Fig. 5. ST40M gas turbine: a) on test bench, and b) installed on the ship The block diagram of the automation system hardware physical components is presented in Figure 6 hereinafter. Placing the transducers configuration considered the distance from measured parameter, ease of debugging, and minimizing the environmental influences on the devices (such as a potential salt water penetration inside the ship, humidity, ambient temperature and pressure, etc.).264 F. Niculescu, Claudia Borzea, I. Vlăducă, A. Mitru, Mirela Vasile, Alexandra Țăranu, G. DediuFig. 6. Block diagram of the automation control systemThe designed automation system enables an integrated engine control and monitoring with programmable logic controller. The programmed sequences implemented in Proficy Machine Edition, the software for VersaMax PLCs, are presented hereinafter.•START-UP. The conditions that must be met for the start-up sequence to begin are: Cool engine (inter turbine temperature ITT<150°C); Fuel pressure >0.8 bar; Engine speed <1000 rpm; Deactivated stop valves (stop valves bypass the fuel tray so that it does not get into the engine); An override button is provided, allowing engine start-up overseeing the above two temperature and pressure conditions. There are three start-up possibilities, presented hereinafter.a)Cold start-up– is performed without fuel ignition, only by gradually opening the air inlet valve and, depending on the pressure attained, it is tried to maintain the engine at a speed of 6000 rpm. During in house tests, we obtained an 8 bar pressure, rendering a speed of ~5000 rpm.b)Deco start-up– when it was just taken out of the warehouse (the fuel valve is opened at 15% and the fuel is cleaned of impurities).Automation control for revamping the propulsion system of a navy frigate 265 In cold and deco start-up modes, the engine functions for 45 s and then stops.c)Hot start-up–begins with opening the air inlet valve. When the engine reaches 3200 rpm, the speed is maintained constant by controlling the air valve. When reaching this speed, the spark plugs are ignited. The fuel valve is opened progressively. If 15 seconds after it has reached 3200 rpm, the inter-turbine temperature ITT does not increase over 150°C, the engine is automatically shut down, since not reaching this temperature means that the spark plugs did not ignite.If ITT > 150°C, the opening of the fuel valve is continued and, at 1600 rpm, the spark plugs are turned off and the air valve is closed. The opening of the air valve is being carried on. If within 50 seconds after reaching 3200 rpm, from the moment fuel supply has started, the speed has not reached 19000 rpm, the engine is emergency shut down and the bypass valves are opened. The threshold speed between start-up and normal regime operation is 19700 rpm.•NORMAL REGIME OPERATION. Hereinafter, if the hot start-up sequence finished successfully and all conditions are met, after reaching 20000 rpm, no action is taken for the next 3 minutes, as it is an interval reserved for thermal stabilization. In emergency situations that can arise during frigate operation on sea, this condition can be overridden. After these 3 minutes, the speed can be modified both from the power control lever (PCL) situated in engines control room, as well as by pressing the virtual arrows on the touchscreen panel. The only difference is that propeller angle cannot modified from the operator panel. Initially, the angle is 0°, the blades being in the same plane, perpendicular on the engine shaft. From the lever, the angle can be modified, for allowing ship advancing.The command of ST40M gas turbine engine can thus be performed from the local control panel or from the engine control room. The so-called remote control from engines room is realised by means of the power control lever situated on the ship control board. ST40M also has two surge valves after the second compressor stage, namely valve 2.2 and valve 2.7. Valve 2.2 is gradually closed from the fully opened position at 20900 rpm, to completely closed at 23200 rpm. Valve 2.7 is closed at 21500 rpm, being an all or nothing flow control valve.In the speed domain from 20000 rpm to 29500 rpm, the ship is in normal operation, being ab le to be controlled according to captain’s orders.•SHUTDOWNa)Normal shutdown– can be activated either automatically by exceeding the set limits of less important parameters (such as fuel pressure, oil pressure, oil temperature, vibrations etc.), or manually by pushing the shutdown button (usually for the sprint engines to enter regime or for accosting. The engine is decelerated until reaching 20000 rpm, maintaining it at this idle speed for 5 minutes. During this time, while the engine cools down, in case it was shutdown due to exceeding a parameter limit, there is another override button that cancels the shutdown sequence (for unexpected situations during frigate operations on sea). If the engine shutdown266 F. Niculescu, Claudia Borzea, I. Vlăducă, A. Mitru, Mirela Vasile, Alexandra Țăranu, G. Dediu has not been cancelled during these 5 minutes, the stop valve is opened and the fuel valve is closed, the engine stopping completely in about 1 minute (speed 0).b)Emergency shutdown– occurs when one of the important parameters (such as turbines speeds or ITT exceed the prescribed limits. The fuel is cut, the air valves and surge valves are opened, the air valve is closed, and the spark plugs are closed. It is realised by pushing either of the two emergency shutdown (ESD) buttons – one placed on the local control panel near the engine, and one on the remote control box upstairs in engine control room. In this room where the engines control is performed, there is a switch for controls commutation on deck to the ship’s captain.The tests performed on the ship involved a minimal intervention in the automatic control of engines and propellers. The throttle controlling the power of the old engine was used for the new engine so that this signal is acquired, and depending on it, the engine provides the necessary power to the ship (up to around3.5 MW). The high-pressure compressor signal (throttle position) is converted intoa unified 4-20mA signal by the pressure transducer. Its value is converted, by the implemented software program of the PLC, into the corresponding speed of the high-pressure compressor required for the ST40M gas turbine. Relying on this signal, the position or opening of the fuel valve is regulated automatically, for setting the desired speed of the ship. The main screen with ST40M diagram and real time parameter values displayed on the LCP is presented in Figure 7.Fig. 7. Main screen with gas turbine and important parameters during operationAutomation control for revamping the propulsion system of a navy frigate 267The graph in Figure 8, represented with acquired parameters, shows that during tests the engine reached a speed between ~22,000÷28,800 rpm. By using solely this engine, the ship was driven up to a cruise speed of 8 knots (~22 km/h).Fig. 8. Evolution of the acquired values for the speed of the high-pressure compressorThe inter turbine temperature is considered to be at least 800°C by fuel flow decrease condition (ITT lim = 800°C). At every time increment Δt = 0.4 s, this condition is verified.4. ConclusionsThe evolution of the essential parameters recorded and acquired for ST40M gas turbine engine shows the stability of the engine in every functioning regime (idle and loaded). The implemented automated electronic control system has proved reliable, accomplishing the optimum control of the gas turbine, with the functions of monitoring, displaying and acquiring of the values of operation parameters. The operation was performed in good conditions and a safe and smooth engine characteristic was achieved by setting the temperature limiting protection. The touch screen control panels interfacing the PLC provide an easily and safely controlled operation, facilitating the revamp of the frigates by replacing the out-of-date Rolls Royce Tyne engine with Pratt & Whitney ST40M marine gas turbine engine, together with developing and implementing the afferent electronics tailored for this specific application. The chosen configuration of the system has proved its compatibility with the given naval requirements, also being easily adaptable.AcknowledgementThe work presented herein was funded by the Operational Programme Human Capital of the Ministry of European Funds through the Financial Agreement 51675/09.07.2019, SMIS code 125125.S p e e d [r p m ]Time [s]268 F. Niculescu, Claudia Borzea, I. Vlăducă, A. Mitru, Mirela Vasile, Alexandra Țăranu, G. Dediu We would like to thank our colleague Adrian Săvescu, for his essential contribution of elaborating and implementing the PLC software embedding the operation sequences, and for providing important information for the present paper.R E F E R E N C E S[1]Y.G. Li and P. Nilkitsaranont, "Gas Turbine Performance Prognostic for Condition-BasedMaintenance", Applied Energy 86, no. 10 (2009).[2]P. Laskowski, "Damages to Turbine Engine Components", in Scientific Journal of SilesianUniversity of Technology. Series Transport 94 (2017).[3] D. Burnes, A. Camou, "Impact of Fuel Composition on Gas Turbine Engine Performance", inJournal of Engineering for Gas Turbines and Power 141, no. 10 (2019).[4]"PW100-150 - Pratt & Whitney", Pwc.ca, https://www.pwc.ca/en/products-and-services/products/regional-aviation-engines/pw100-150 [Accessed: 28.04.2020]. [5]"Rolls-Royce Engines: Tyne - Graces Guide", , 2019,https:///Rolls-Royce_Engines:_Tyne. [Accessed 29.04.2020].[6] E. Pascu, "Fregata …Regina Maria”, de 15 ani în serviciul Forțelor Navale Român e",Defenseromania.ro, 2020, https://www.defenseromania.ro/fregata-regina-maria-de-15-ani-in-serviciul-for-elor-navale-romane_602768.html. [Accessed 03.05.2020].[7]"Skjold Class" (Archived report), pdf, 2018, , 2013,https:///archive/disp_pdf.cfm?DACH_RECNO=1014. [8]"P&W to Power Norwegian Navy “Skjold” Patrol Boats", , 2019,/articles-view/release/3/32064/p%26w-turbines-for-%E2%80%98skjold%E2%80%99-boats-(jan.-20).html. [Accessed 30.04.2020].[9]M. Borzea, G. Fetea, R. Codoban, "Implementation and Operation of a Cogeneration Plant forSteam Injection in Oil Field", in Volume 7: Education; Industrial and Cogeneration; Marine;Oil and Gas Applications, 2008.[10]G. Samoilescu, D. Iorgulescu, R. Mitrea, L.D. Cizer, "Propulsion Systems in MarineNavigation", in International Conference Knowledge-based Organization 24, no. 3 (2018). [11]"PW Power Systems ST18/ST40"(Archived report), pdf, 2018, ,2020, https:///archive/disp_pdf.cfm?DACH_RECNO=1327 [Accessed: 28.04.2020].[12]H. Kayadelen, Y. Ust, "Thermodynamic Properties of Engine Exhaust Gas for Different Kindof Fuels", Lecture Notes in Electrical Engineering 307, pp. 247-259, 2014. DOI: 10.1007/978-3-319-03967-1_19.[13]M. Elgohary, I. Seddiek, "Comparison between Natural Gas and Diesel Fuel Oil Onboard GasTurbine Powered Ships", Journal of King Abdulaziz University, vol. 23, no. 2, pp. 109-127, 2012. DOI: 10.4197/mar.23-2.7.[14]C.G. Hodge, "The Integration of Electrical Marine Propulsion Systems", in InternationalConference on Power Electronics Machines and Drives, 2002.[15]B. MacIsaac, R. Langton, "Marine Propulsion Systems", in Gas Turbine Propulsion Systems,2011.[16]F. Niculescu, A. Savescu, "Aspects Regarding the Control and Regulation of an IndustrialTurbine", 11th International Symposium on Advanced Topics in Electrical Engineering, 2019.。
常用数学软件介绍Maple、Mathematica、Matlab、_MathCAD、_SAS、SPSS、LINDO、LINGO
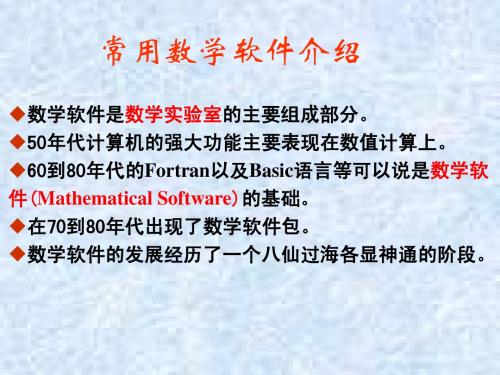
世界上应用最广泛的专业统计软件。在国际学术界有 条不成文的规定,即在国际学术交流中,凡是用SPSS软 件完成的计算和统计分析,可以不必说明算法 。
和SAS相同,SPSS也由多个模块构成,在最新的11版 中,SPSS一共由十个模块组成,其中SPSS Base为基本 模块,其余九个模块分别用于完成某一方面的统计分析 功能,他们均需要挂接在Base上运行。除此之外, SPSS 11完全版还包括SPSS Smart Viewer和SPSS Report Writer两个软件,他们并未整合进来,但功能 上完全是SPSS的辅助软件。 SPSS最突出的特点就是操作界面极为友好,输出结果 美观漂亮(从国外的角度看),他使用Windows的窗口 方式展示各种管理和分析数据方法的功能,使用对话框 展示出各种功能选择项。 是非专业统计人员的首选统计软件。
Matlab的功能和特点
1.功能强大
(1) 运算功能强大
Matlab的数值运算要素不是单个数据,而是矩阵, 每个元素都可看作复数,运算包括加、减、乘、除、 函数运算等; 通过Matlab的符号工具箱,可以解决在数学、应用
科学和工程计算领域中常常遇到的符号计算问题。
(2) 功能丰富的工具箱
Matlab主要由主程序和功能各异的各种工具箱组成,其
主要特点是使用操作简单,输入格式与人们习惯的 数学书写格式很近似,采用所见即所得界面。 对于数值精度要求很严格的情形,或者是对于计算 方法有特殊要求的情况,MathCAD不适合。
四种软件的比较
如果同时要求计算精度、符号计算和编程的话,最好同
时使用Maple和Mathematica ,它们在符号处理方面各具
Introduction to Mathematical Modeling in Mathematica

Bruce E. Shapiro
Department of Biomathematics UCLA School of Medicine and Jet Propulsion Laboratory California Institute of Technology bshapiro@ 3 June 1998 Presented as part of Medical Informatics: A Course for Health Professionals Sponsored by the National Library of Medicine and Marine Biology Laboratory Water Street Woods Hole, MA 02543
Starting Mathematica............................12
An Example Population Biology...........23 Mathematica Reference Outline............24
Numerical Computation.........................24 Numerical Evaluation.........................24 Equation Solving..............................24 Sums and Products............................24 Integration.......................................25 Optimization....................................25 Data Manipulation.............................25 Curve Fitting...............................25 Fourier Transform.........................26 Selection of special elements...........26 Set Manipulation..........................26 Matrices and Vectors..........................27 Matrix Operations.........................27 Systems of Linear Equations...........27 Matrix Decompositions..................27 Complex Numbers............................28 Number Representation......................28 Heads..........................................28 Digits, Exponents, and Mantissas.....28 Change of Representation...............29 Infinity........................................29 Numerical Precision...........................29 Evaluation Accuracy and Precision....29 Intervals......................................29 Machine Accuracy and Precision.......30 Options...........................................30 Algebraic Computation..........................30 Basic Algebra...................................30 Formula Manipulation.......................31 Simplification..............................31 Expansion....................................31 Rearrangement..............................31 Parts of an Expression....................32 Numerators and Denominators.........32 Trigonometric Function Manipulation ..................................................32 Root and Radical Manipulation........32 Other Manipulations......................32 Bruce E. Shapiro Woods Hole, 1998
基于大数据的数学建模方法融入高职数学教学实践探究
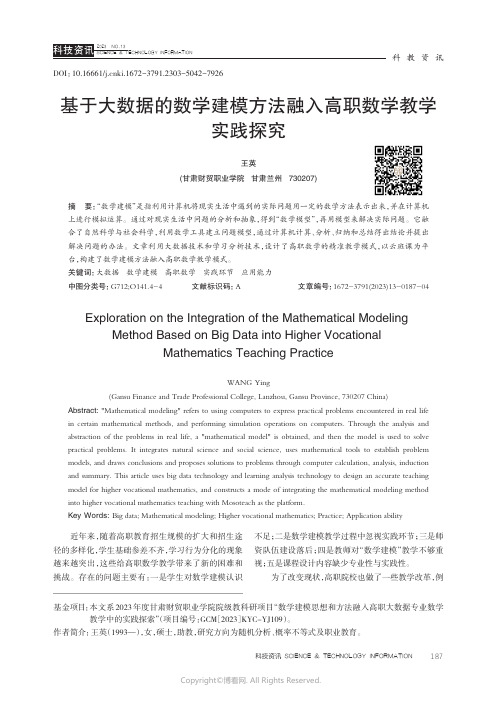
基于大数据的数学建模方法融入高职数学教学实践探究王英(甘肃财贸职业学院 甘肃兰州 730207)摘要:“数学建模”是指利用计算机将现实生活中遇到的实际问题用一定的数学方法表示出来,并在计算机上进行模拟运算。
通过对现实生活中问题的分析和抽象,得到“数学模型”,再用模型来解决实际问题。
它融合了自然科学与社会科学,利用数学工具建立问题模型,通过计算机计算、分析、归纳和总结得出结论并提出解决问题的办法。
文章利用大数据技术和学习分析技术,设计了高职数学的精准教学模式,以云班课为平台,构建了数学建模方法融入高职数学教学模式。
关键词:大数据 数学建模 高职数学 实践环节 应用能力中图分类号:G712;O141.4-4文献标识码:A 文章编号:1672-3791(2023)13-0187-04Exploration on the Integration of the Mathematical Modeling Method Based on Big Data into Higher VocationalMathematics Teaching PracticeWANG Ying(Gansu Finance and Trade Professional College, Lanzhou, Gansu Province, 730207 China)Abstract: "Mathematical modeling" refers to using computers to express practical problems encountered in real life in certain mathematical methods, and performing simulation operations on computers. Through the analysis and abstraction of the problems in real life, a "mathematical model" is obtained, and then the model is used to solve practical problems. It integrates natural science and social science, uses mathematical tools to establish problem models, and draws conclusions and proposes solutions to problems through computer calculation, analysis, induction and summary. This article uses big data technology and learning analysis technology to design an accurate teaching model for higher vocational mathematics, and constructs a mode of integrating the mathematical modeling method into higher vocational mathematics teaching with Mosoteach as the platform.Key Words: Big data; Mathematical modeling; Higher vocational mathematics; Practice; Application ability近年来,随着高职教育招生规模的扩大和招生途径的多样化,学生基础参差不齐,学习行为分化的现象越来越突出,这些给高职数学教学带来了新的困难和挑战。
- 1、下载文档前请自行甄别文档内容的完整性,平台不提供额外的编辑、内容补充、找答案等附加服务。
- 2、"仅部分预览"的文档,不可在线预览部分如存在完整性等问题,可反馈申请退款(可完整预览的文档不适用该条件!)。
- 3、如文档侵犯您的权益,请联系客服反馈,我们会尽快为您处理(人工客服工作时间:9:00-18:30)。
ห้องสมุดไป่ตู้
Mathematical Model for Mixing Reactants in a Capillary Microreactor by Transverse Diffusion of Laminar Flow Profiles
Victor Okhonin, Edmund Wong, and Sergey N. Krylov* Department of Chemistry, York University, Toronto, Ontario M3J 1P3, Canada Transverse diffusion of laminar flow profiles (TDLFP) was recently suggested as a generic approach for mixing reactants inside a capillary microreactor. Conceptually, solutions of reactants are injected inside the capillary by high pressure as a series of consecutive plugs. Because of the laminar nature of the flow inside the capillary, the nondiffused plugs have parabolic profiles with predominantly longitudinal interfaces between the plugs. After the injection, the reactants are mixed by transverse diffusion across the longitudinal interfaces. TDLFP-based mixing is still in its infancy as only the principle was proved. Here, we develop the theory of TDLFP and introduce a dimensionless parameter, York number, which can be used in predicting the quality of TDLFP-based mixing. The theory uses a single simplifying assumption that the longitudinal diffusion is negligible; this assumption is readily satisfied. We then develop a numerical model of TDLFP and use it to simulate the concentration profiles of three reactants mixed by TDLFP in the capillary. The correlation between the York number and quality of mixing is analyzed. Two ways of improving the quality of TDLFP-based mixing are suggested and studied: (i) increasing the longitudinal interface between the plugs by a long last plug of a solvent and (ii) “shaking” the injected reactants by a series of alternating negative and positive pressure pulses. The developed theory and computational simulation of TDLFP will stimulate the practical use of capillary microreactors.
Microreactors, which facilitate the conduction of chemical processes in nanoliter and subnanoliter volumes, are highly attractive for a variety of applications including high-throughput screening,1 multiplexed bioanalyses,2 studies of single molecules,3 and analyses of chemical contents of single cells.4 The major requirements for microreactors include (i) easy and reproducible mixing, (ii) negligible evaporation, and (iii) simple interfacing with sensitive and informative analytical tools. These requirements can be met by confining the nanoliter-volume reaction mixture in a
* To whom correspondence should be addressed. E-mail: skrylov@yorku.ca. (1) Steger, R.; Bohl, B.; Zengerle, R.; Koltay, P. JALA 2004, 9, 291–299. (2) Moser, C.; Mayr, T.; Klimant, I. Anal. Chim. Acta 2006, 558, 102–109. (3) Lee, J.-Y.; Li, H.-W.; Yeung, E. S. J. Chromatogr., A 2004, 1053, 173–179. (4) Hellmich, W.; Pelargus, C.; Leffhalm, K.; Ros, A.; Anselmetti, D. Electrophoresis 2005, 26, 3689–3696.