复合材料性能试验方法选择和结果评价
复合材料拉伸试样

复合材料拉伸试样是一种用于评估材料力学性能的常见试验方法。
它通过施加拉伸载荷来测定材料的拉伸强度、弹性模量、屈服强度、延伸率等参数。
本文将介绍复合材料拉伸试样的基本原理、试验过程和结果分析。
一、引言复合材料是由两种或更多种不同材料组成的材料,具有优异的力学性能和物理化学性质。
复合材料广泛应用于航空航天、汽车、建筑和电子等领域。
了解复合材料的力学性能对于材料设计和工程应用至关重要。
拉伸试验是评估材料拉伸性能的重要手段之一。
二、试验原理复合材料拉伸试样通常采用标准矩形截面形状,长度为L,宽度为W,厚度为H。
试样两端固定在拉伸机上,施加拉伸载荷使试样产生拉伸变形。
根据试样的几何尺寸和加载情况,可以计算出试样的拉伸应力σ和应变ε。
三、试验过程1. 试样制备:根据标准要求,制备符合尺寸要求的试样。
确保试样表面光滑、无明显缺陷。
2. 试样安装:将试样两端固定在拉伸机上,确保试样的纵轴与拉伸机的加载方向一致。
3. 参数设置:根据试验要求,设置加载速率、试验温度等参数,并记录下来。
4. 施加载荷:开始拉伸试验,根据设定的加载速率逐渐施加拉伸载荷,直至试样断裂。
5. 数据记录:在试验过程中,实时记录试样的拉伸力和伸长量,并绘制应力-应变曲线。
6. 结果分析:根据试验数据,计算试样的拉伸强度、弹性模量、屈服强度和延伸率等力学性能参数。
四、结果分析1. 拉伸强度:试样断裂前所承受的最大拉伸应力,表示材料的抗拉强度。
2. 弹性模量:试样在弹性阶段的斜率,反映材料的刚度。
3. 屈服强度:试样开始产生塑性变形的应力,表示材料的抗变形能力。
4. 延伸率:试样断裂前的伸长量与初始长度的比值,表示材料的延展性能。
五、注意事项1. 试样制备要精细,确保尺寸准确,避免制备过程中引入缺陷。
2. 试验过程中应注意控制加载速率,避免过快或过慢导致结果误差。
3. 注意试验环境的温度和湿度对试验结果的影响,并进行相应的修正。
4. 在试验过程中,需注意安全操作,避免发生意外。
复合材料强度检测常用方法

复合材料强度检测常用方法一、引言复合材料广泛应用于航空、航天、汽车、建筑等领域,其性能与质量的检测是保证产品质量的重要环节之一。
其中,强度检测是复合材料性能检测的重要内容之一。
本文将介绍复合材料强度检测的常用方法,包括拉伸试验、剪切试验、弯曲试验、扭曲试验、压缩试验等。
二、拉伸试验拉伸试验是复合材料强度检测中最常用的方法之一,也是最基本的试验方法之一。
该试验方法通过施加拉伸荷载,使试样发生拉伸变形,从而获得试样的拉伸强度、弹性模量、屈服强度等力学性能参数。
1. 试样制备拉伸试验的试样形状为矩形条形,标准尺寸为25mm×250mm,以纤维方向为长度方向。
试样应当在同一工艺条件下制备,以保证试样的一致性。
2. 试验设备拉伸试验需要用到拉伸试验机,该设备能够施加稳定的拉伸荷载,同时具备高精度的位移测量系统,以便实时监测试样的变形情况。
3. 试验步骤(1)将试样安装在拉伸试验机上,并调整试验机的夹持装置,使试样处于合适的位置。
(2)设置试验机的拉伸速度和荷载范围。
(3)启动试验机,逐渐施加拉伸荷载,同时记录试样的变形情况和荷载变化情况。
(4)直至试样断裂,停止试验。
4. 试验结果分析拉伸试验得到的结果包括试样的最大拉伸强度、屈服强度、弹性模量等参数。
通过对试验结果的分析,可以评估复合材料的强度性能和应力-应变曲线的特征。
三、剪切试验剪切试验是复合材料强度检测中常用的试验方法之一,该试验方法通过施加剪切荷载,使试样发生剪切变形,从而获得试样的剪切强度、剪切模量等参数。
1. 试样制备剪切试验的试样形状为矩形条形,标准尺寸为25mm×250mm,以纤维方向为长度方向。
试样应当在同一工艺条件下制备,以保证试样的一致性。
2. 试验设备剪切试验需要用到剪切试验机,该设备能够施加稳定的剪切荷载,同时具备高精度的位移测量系统,以便实时监测试样的变形情况。
3. 试验步骤(1)将试样安装在剪切试验机上,并调整试验机的夹持装置,使试样处于合适的位置。
复合材料压缩实验报告总结

复合材料压缩实验报告总结复合材料是由两种或两种以上的材料组成的材料,具有轻质、高强度、耐腐蚀等优点,在航空航天、汽车制造、建筑等领域得到广泛应用。
为了研究复合材料在压缩载荷下的力学性能,本实验对不同类型的复合材料进行了压缩实验,并对实验结果进行了分析和总结。
一、实验目的本次实验旨在研究不同类型的复合材料在压缩载荷下的力学行为,探索其抗压性能和变形特点。
二、实验装置和方法1. 实验装置:采用万能试验机作为压缩装置,配备相应的夹具和传感器。
2. 实验方法:选取不同类型的复合材料样品,按照标准尺寸制备,并在试验机上进行压缩加载。
记录加载过程中的载荷-位移曲线,并测量样品断裂前后的尺寸。
三、实验结果与分析1. 载荷-位移曲线:通过对不同类型复合材料样品进行压缩加载,记录其载荷-位移曲线。
根据实验数据绘制曲线图,观察曲线的特点和变化趋势。
2. 抗压性能:根据载荷-位移曲线,可以得到复合材料的抗压强度和抗压模量。
比较不同类型复合材料的抗压性能,分析其差异原因。
3. 变形特点:观察样品在加载过程中的变形情况,包括临界载荷下的屈曲、破坏模式等。
分析不同类型复合材料的变形特点,并与传统材料进行对比。
四、实验结论1. 不同类型复合材料在压缩载荷下表现出不同的力学行为,其中某些类型的复合材料具有较高的抗压强度和抗压模量。
2. 复合材料在加载过程中呈现出一定的屈曲和破坏模式,这与其内部纤维排列、基体性质等因素有关。
3. 与传统材料相比,复合材料具有更好的抗压性能和变形特点,在工程应用中具有广阔前景。
五、实验总结通过本次实验,我们对不同类型复合材料在压缩载荷下的力学行为有了更深入的了解。
复合材料具有优异的力学性能和变形特点,对于提高工程结构的强度和轻量化具有重要意义。
然而,复合材料的制备工艺和性能预测仍然存在一定挑战,需要进一步研究和改进。
希望通过本次实验可以为相关领域的研究和应用提供一定参考。
复合材料结构的力学性能测试与分析

复合材料结构的力学性能测试与分析引言复合材料是由不同材料组合而成的一种新型材料,具有很多优异的机械性能,因此在航空、航天、汽车等领域得到广泛应用。
然而,复合材料的力学性能与其结构密切相关,因此对其进行力学性能测试与分析是十分关键的。
一、复合材料结构的力学性能测试方法1. 拉伸试验拉伸试验是评估复合材料材料强度和刚度的常用方法之一。
通过在拉伸机上施加一定的拉力,测量拉伸试样的应变和应力来分析材料的拉伸性能。
该方法能够得到材料的拉伸强度、弹性模量、屈服强度等参数。
2. 压缩试验压缩试验用于评估复合材料在受压状态下的抗压性能。
在压力机上施加一定的压力,测量压缩试样的应变和应力来分析材料的抗压性能。
该方法能够得到材料的压缩强度、弹性模量、破坏形态等参数。
3. 剪切试验剪切试验用于评估复合材料在受剪切状态下的抗剪性能。
通过施加剪切力,测量试样剪切区域的切应变和切应力来分析材料的抗剪切性能。
该方法能够得到材料的剪切强度、剪切模量等参数。
4. 冲击试验冲击试验用于评估复合材料在受冲击载荷下的性能表现。
通过施加冲击载荷,测量试样的冲击吸收能力和冲击强度来分析材料的抗冲击性能。
该方法能够得到材料的冲击韧性、断裂能量等参数。
二、复合材料结构力学性能分析1. 有限元分析有限元分析是一种常用的力学性能分析方法,通过将结构离散化为有限个单元,在每个单元内建立方程组,最终求解整个结构的力学行为。
通过有限元分析,可以得到复合材料结构在不同载荷条件下的应力和应变分布,并可以进行累积疲劳分析、刚度分析等。
2. 弹性力学分析弹性力学分析可以用来研究复合材料的静力响应。
通过应变-应力关系和材料的力学参数,可以计算出复合材料在受力作用下的应变和应力分布。
弹性力学分析可用于优化设计和评估复合材料结构的强度。
3. 疲劳寿命评估复合材料结构在长期受到变化载荷作用下会发生疲劳破坏。
通过进行疲劳寿命评估,可以预测结构在特定载荷下的寿命。
疲劳寿命评估可以使用实验方法和数值模拟方法,如基于有限元分析的疲劳分析。
复合材料的力学性能测试与分析

复合材料的力学性能测试与分析引言:复合材料是由两个或多个成分组合而成的材料,通常包括纤维增强材料和基体材料。
由于其独特的结构和组分,复合材料具有优良的力学性能和广泛的应用领域。
在设计和制造复合材料制品时,力学性能的测试与分析非常重要,可以评估材料的强度、刚度和韧性等关键指标,指导工程应用中的设计和生产。
本文将深入探讨复合材料的力学性能测试方法和分析技术。
力学性能测试方法:1. 张力测试:张力测试用于测量材料在施加纵向拉力时的承载能力。
一种常用的方法是单轴拉伸测试,其中样品被拉伸直至断裂,通过测量施加的力与应变之间的关系,获得材料的应力-应变曲线。
这个曲线可以提供材料的强度和刚度等信息。
2. 压力测试:压力测试旨在测量材料的抗压能力。
常见的方法是将样品置于压力机之间,逐渐施加压力直至样品破裂。
通过测量施加的压力与应变之间的关系,可以评估材料的抗压强度和变形能力。
3. 剪切测试:剪切测试用于测量材料在剪切加载下的表现。
通常使用剪切试验机在两个表面之间施加剪切力,测量材料的剪切应力与应变关系。
这个关系提供材料的剪切强度和剪切刚度等参数。
力学性能分析技术:1. 杨氏模量:杨氏模量是描述材料刚度的指标,表示材料在受力时的应变响应。
通过施加小应力并测量产生的应变,可以计算出材料的杨氏模量。
杨氏模量越大,材料的刚度越高。
2. 弯曲强度:弯曲强度是评估复合材料抵抗在横向加载下发生弯曲的能力。
通过施加弯矩并测量产生的应力,可以计算出材料的弯曲强度。
弯曲强度高的材料在横向应力下更为耐用。
3. 破坏韧性:破坏韧性是评估复合材料耐受冲击或断裂的能力。
常用的测试方法是冲击测试,通过施加冲击力并测量导致的破损面积,可以评估材料的破坏韧性。
高韧性材料能够吸收能量并减缓破坏过程。
实例分析:以碳纤维增强复合材料为例,进行实例分析。
碳纤维增强复合材料由碳纤维作为纤维增强材料,环氧树脂作为基体材料组成。
首先进行张力测试,测量样品在单轴拉伸下的强度和应变。
复合材料力学性能表征
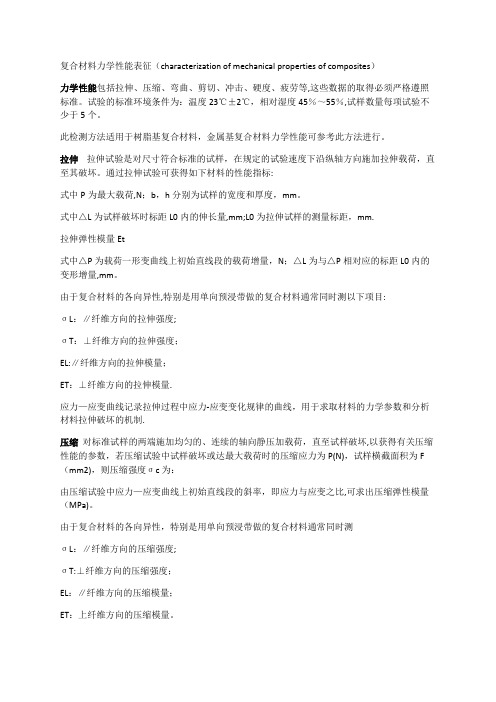
复合材料力学性能表征(characterization of mechanical properties of composites)力学性能包括拉伸、压缩、弯曲、剪切、冲击、硬度、疲劳等,这些数据的取得必须严格遵照标准。
试验的标准环境条件为:温度23℃±2℃,相对湿度45%~55%,试样数量每项试验不少于5个。
此检测方法适用于树脂基复合材料,金属基复合材料力学性能可参考此方法进行。
拉伸拉伸试验是对尺寸符合标准的试样,在规定的试验速度下沿纵轴方向施加拉伸载荷,直至其破坏。
通过拉伸试验可获得如下材料的性能指标:式中P为最大载荷,N;b,h分别为试样的宽度和厚度,mm。
式中△L为试样破坏时标距L0内的伸长量,mm;L0为拉伸试样的测量标距,mm.拉伸弹性模量Et式中△P为载荷一形变曲线上初始直线段的载荷增量,N;△L为与△P相对应的标距L0内的变形增量,mm。
由于复合材料的各向异性,特别是用单向预浸带做的复合材料通常同时测以下项目:σL:∥纤维方向的拉伸强度;σT:⊥纤维方向的拉伸强度;EL:∥纤维方向的拉伸模量;ET:⊥纤维方向的拉伸模量.应力—应变曲线记录拉伸过程中应力-应变变化规律的曲线,用于求取材料的力学参数和分析材料拉伸破坏的机制.压缩对标准试样的两端施加均匀的、连续的轴向静压加载荷,直至试样破坏,以获得有关压缩性能的参数,若压缩试验中试样破坏或达最大载荷时的压缩应力为P(N),试样横截面积为F (mm2),则压缩强度σc为:由压缩试验中应力—应变曲线上初始直线段的斜率,即应力与应变之比,可求出压缩弹性模量(MPa)。
由于复合材料的各向异性,特别是用单向预浸带做的复合材料通常同时测σL:∥纤维方向的压缩强度;σT:⊥纤维方向的压缩强度;EL:∥纤维方向的压缩模量;ET:上纤维方向的压缩模量。
弯曲复合材料在弯曲试验中受力状态比较复杂,拉、压、剪、挤压等力同时对试样作用,因而对成型工艺配方,试验条件等因素的敏感性较大。
6-复合材料试验方法总结

(六) 复合材料试验方法总结
杨胜春 2015-06-25
(一)拉伸试验 (二)压缩试验 (三)弯曲/短梁剪切试验 (四)疲劳试验 (五)环境试验
(一六)拉总伸试结验
单向板( 0°、 90°)拉伸 多向层压板拉伸 ±45°拉伸(面内剪切) 螺栓(拉伸)挤压 开孔拉伸 充填孔拉伸
(三)弯曲五、短总梁剪结切试验
三点弯曲 四点弯曲 短梁剪切
注意事项
与压缩试验一样,弯曲试验都通过夹具对试件加载,因此,试 验前必须调整好夹具的跨距,正确选择压头和支座的尺寸。 必须保证试验夹具压头的中心线与试验机的加载中心线保持一 致。
(四)复合五材料总疲劳结试验
几个试验参数:
(二)五压缩总试验结
(二)五压缩总试验结
(二五)压总缩试结验
(二)五压缩总试验结
压缩试验注意事项
压缩试验与拉伸不同,都需要压缩夹具,因此,试件安装时必须小心, 以保证试件与夹具的良好配合(包括夹具螺栓拧紧力矩的要求)。
通过压缩试验夹具保证试件的中心线与试验机的加载中心线保持一致。 压缩试验应尽量选择带有万向球绞压缩平台的试验机。
试验能力
试验机——20 余台(静力、疲劳、 动态);
环境试验箱——20 余台(高温、 低温、高低温循环、盐雾、紫外 老化等);
标准/非标准试验夹具 无损检测等
试验夹具研制
力学性能试验夹具研制
GB、HB试验夹具 ASTM 试验夹具 SACMA 试验夹具
压缩夹具(SACMA 1) 压缩夹具(ASTM D 6641)
(一六)拉总伸试结验
(六一)总拉伸结试验
(一六)拉总伸试结验
拉伸试验注意事项:
复合材料界面粘接性能的监测与分析

复合材料界面粘接性能的监测与分析复合材料在工程领域中得到广泛应用,其独特的物理性质使其成为制造飞机、汽车和结构材料的理想选择。
然而,复合材料的性能很大程度上取决于其界面粘接性能。
因此,监测和分析复合材料界面粘接性能对于确保产品质量和使用寿命具有重要意义。
为了监测复合材料界面粘接性能,一种常用的方法是通过力学试验来评估粘接强度。
拉伸、剪切和剥离试验是常见的评估技术。
在拉伸试验中,施加纵向的压力来测试界面强度。
剪切试验则通过在两个相邻表面上施加剪切力来评估界面黏结强度。
剥离试验则是通过施加拉力来测试粘接层的强度。
这些试验方法能够提供一些关于复合材料粘接性能的基本信息,但是缺乏深入的分析。
为了更好地理解界面胶粘剂的性能,还可以进行界面形态分析。
电镜技术(如扫描电镜和透射电镜)能够提供关于复合材料界面形态的详细信息。
通过观察界面微观结构,可以评估胶粘剂的分布、界面的亲和性以及粘接层的完整性。
此外,原子力显微镜也可以用来研究表面的纳米级别特征,以便更好地理解复合材料界面的性能。
除了力学试验和界面形态分析外,热分析技术也可以用于评估复合材料界面粘接性能。
差示扫描量热法(DSC)可以用来分析胶粘剂的玻璃化转变温度,这对于界面黏结的稳定性和长期使用寿命非常重要。
动态热机械分析(DMA)则可以评估界面的弹性和黏弹性特性,从而了解胶粘剂对于应力和温度变化的响应。
在监测和分析复合材料界面粘接性能的过程中,还需要考虑界面预处理和环境因素。
界面预处理包括清洗、脱脂和粗糙化等步骤,以确保胶粘剂可以牢固地附着在基材上。
此外,湿度、温度和化学环境等因素也会对界面粘接性能产生影响。
因此,在测试和分析过程中,需要保持恒定的环境条件,以获得准确可靠的结果。
总之,复合材料界面粘接性能的监测与分析对于确保产品质量和使用寿命至关重要。
通过力学试验、界面形态分析和热分析等多种方法,可以全面了解胶粘剂的性能特征和界面的质量状况。
此外,还需要考虑界面预处理和环境因素对粘接性能的影响。
- 1、下载文档前请自行甄别文档内容的完整性,平台不提供额外的编辑、内容补充、找答案等附加服务。
- 2、"仅部分预览"的文档,不可在线预览部分如存在完整性等问题,可反馈申请退款(可完整预览的文档不适用该条件!)。
- 3、如文档侵犯您的权益,请联系客服反馈,我们会尽快为您处理(人工客服工作时间:9:00-18:30)。
复合材料性能试验方法选择和结果评价张汝光(上海玻璃钢研究院 200126)摘要:由于复合材料性能的多样性和性能机理的复杂性,其试验方法也同样多样、复杂。
应该根据试验目的和考虑材料的性能机理,正确选择试验方法或制订试验方案,以确保试验结果的可靠性。
对试验方法和试验结果都要作科学的评价。
关键词:复合材料性能试验 多样性 复杂性 可靠性1 概 述要用好材料,首先就要认识材料。
认识材料的最重要途径就是通过材料的性能试验。
由于复合材料本身就是个结构,在进行复合材料产品设计时,不能简单地选择材料,而是要同时设计复合材料。
因此认识材料就不单单是了解材料的性能数值范围,而还要了解复合材料的性能机理。
复合材料性能试验变得更加重要。
复合材料的性能试验一般有三种不同的目的。
一是揭示复合材料的材料性能机理;二是取得用于产品设计的材料性能参数;三是取得供材料质量评定用的材料性能参数。
试验目的的不同,对试验方法的要求,就有各自不同的侧重点,自然就会有不同的试验方法或方案。
复合材料细观不均匀结构的本质,使其性能不但具有各向异性的特点,在许多情况下,还具有各种耦合效应。
这就使得复合材料的性能试验相对于常规材料,要多样、复杂,同时也具有更多的影响材料性能的因素。
在制订试验方案或选择试验方法时,这些方面都应该加以考虑,做认真、细致的分析。
对试验方法和试验结果都要作科学的评价。
2复合材料性能试验的目的制订试验方案或选择试验方法,首先要根据自己的试验目的。
即使是对同一个性能,目的不同,对试验方案或方法也会有不同的考虑和选择。
2.1为揭示材料性能机理的性能试验揭示材料性能机理,就是揭示在一定条件下材料作出响应的全过程及其原因,揭示各种因素是如何影响这一过程。
显然,以揭示材料性能机理为目的的材料性能试验,要强调的是试验所得到的性能规律首先必须是定性上准确。
因此,在考虑试验方法时,首先要确保这一点。
例如,当我们要揭示某一因素对某一性能的影响规律时,在试验条件中要特别注意严格排除其他影响因素同时发生变化,否则试验结果就无法说明是哪一因素的影响规律,测试数据再准确也毫无用处。
2.2 为取得用于产品设计性能参数的性能试验要取得用于产品设计性能参数,对其性能试验要求,自然是试验结果的可靠性。
例如,试样工作区内要确保材料是处在试验所要求的条件状态下,试验中所测数据,必须取自试样工作区或是与工作区内数值相同。
除此之外,可靠性还要求试验要有一定的试样个数,对试验结果除要计算平均值外,还需要计算离散系数。
在产品设计中,仅有性能参数的平均值而没有离散系数,就无法确定该性能的离散程度,就将无法确定在一定置信度要求下,如何使用这一平均值参数。
2.3为取得供质量评定性能参数的性能试验质量评定,可以是在生产过程中的质量检验,也可以是对产品的质量检验。
进行质量评定,往往都预先设定一个合格的材料性能标准,将试验结果与这一标准相比较,以评定其质量是否合格。
这种其结果用于对比的材料性能试验,应该强调的是:试验必须严格按照同一标准试验方法进行。
因为任何试验方法都只有具有相对的理想或合理性(第5节中进一步说明),不同的试验方法往往会得出不同的结果,它们之间常常不具有可对比性,最具权威的试验方法自然是国家标准试验方法。
作为产品性能指标的性能数据,必须按照国家标准试验方法测得。
3复合材料性能的特点复合材料性能试验方法与复合材料性能特点密切相关。
要正确制订试验方案或选择试验方法,还必须对复合材料性能特点有所了解。
3.1 复合材料性能的多样性由于复合材料细观上是结构,它的材料性能参数与常规材料相比要多很多。
例如,根据平面受力方向的不同,拉伸性能就有纵向拉伸、横向拉伸和偏轴拉伸性能等之分;剪切性能除了有平面方向不同之分外,根据空间方向的不同又有平面剪切、层间剪切和断纹剪切性能等之分。
因此,即使同是拉伸性能或同是剪切性能,它们的性能试验方法也不完全相同,甚至还会完全不同。
3.2 复合材料性能机理的复杂性复合材料性能机理的复杂性,笔者归结主要有三个方面:第一,各个性能往往都有独特的性能机理。
例如,同样是拉伸性能,纵向拉伸性能和横向拉伸性能机理完全不同;又如,平面剪切、层间剪切和断纹剪切,虽然宏观上都是受剪力,但从细观上它们的受力状态完全不同,自然也有完全不同的性能机理。
第二,性能机理中影响因素很多。
不但组分性能(纤维、基体和界面性能)、含胶量的多少、细观结构形式(如不同的角铺设或不同的编织形式等)对复合材料性能会有很大影响,这些因素之间的相对不同组合,也将会对性能有很大的影响。
例如,单向板的纵向拉伸强度一般说来是由纤维(强度和含量)所控制。
但高强脆性纤维若增强脆性基体,而又遇较强界面,则受拉时将发生脆性断裂的破坏形式,得到很低的纵向拉伸强度,完全没有发挥出高强纤维的作用。
反之,高强脆性纤维若增强韧性基体,又有适中的界面强度,受纵向拉伸时将发生损伤积累形式的破坏,得到很高的纵向拉伸强度,高强纤维的作用得到超(平均强度)水平发挥。
由于复合材料性能的影响因素比较多,在制订试验方案或选择试验方法时,需要根据试验目的,在试验条件中正确控制各种影响因素。
对于探索材料性能机理为目的的性能试验尤为重要。
第三,许多复合材料都具有这样或那样的耦合效应特性。
例如,材料在受拉时,不单会产生拉伸变形,还会产生剪切变形或弯曲变形等;反之,受剪力吋,不单会发生剪切变形,还会产生拉伸变形等。
这些耦合效应的存在,往往很难在试样工作区内形成一个均匀的单向应力场,或者会造成在试样夹持端产生较为复杂的应力状态而容易在这一区域首先发生破坏。
上述两种情况将会影响到试验结果的可靠性,因此在制订试验方案吋需要特别注意。
4 复合材料性能试验方案制订或方法选择本节以具体事例说明在制订复合材料性能试验方案或选择试验方法时应考虑的有关问题。
4.1注意对影响因素的控制这一问题在进行材料性能机理研究的性能试验中尤为重要。
(1)对水扩散系数的测定对水扩散系数是复合材料乎板一维水扩散(水只从板面垂直向板内扩散)理论模型中提出的材料吸水性能参数。
因此,在测定水扩散系数的吸水试验中,必须确保水只从试样两表面内扩散人板內,而将试样侧面的吸水降到最小的程度。
如,采用相对板面尺寸厚度很薄的试样或采用四个侧面封边的措施等。
曾见到采用短梁弯曲试件测定水扩散系数的试验,显然其结果是可疑的。
由于有较大量的水是从侧面吸人,所得数据已不代表真正的水扩散系数。
(2)厚度对性能影响的试验曾见到一些探索厚度对性能影响的试验,试验中没有注意其它影响因素的确保不变,因此所测得的性能变化情况不能说明是由厚度变化引起的。
例如,在一个厚度对复合材料单向板剪切模量影响的试验研究中,不同厚度试样的含胶量同时有较大波动,因此测得剪切模量的变化实际上是由含胶量变化所引起,并非厚度所影响。
又如,在做厚度对相对饱和吸水率影响时,也要确保不同厚度试样含胶量必须相同。
因为含胶量对饱和吸水率也有很大影响。
(3)界面对弯曲性能影响的试验曾见到探索芳纶纤维增强铝层板界面对弯曲性能影响的试验,试验中没有注意到不同界面处理的层板中,它们的铺层顺序以及对应层的厚度都必须确保相同。
由于铺层情况对弯曲性能的影响很大,这一试验结果实际已无法说明界面的影响。
4.2注意确保试验结果的可靠性这一问题对取得产品设计性能参数的试验尤为重要。
(1)单向板剪切性能试验方法选择曾见到选择45°偏轴拉伸试验方法测试单向板的剪切性能。
这一试验方法测得的剪切模量偏差不大,但测得的剪切强度将显著偏低。
这是因为单向板受45°偏轴拉伸时,在材料坐标系下,除了有剪切应力分量外还会有同等大小的纵向和横向拉伸应力分量。
由于单向板的横向拉伸强度很低,因此破坏往往就由横向拉伸应力引起,至少也会对破坏的产生起较大的拉伸试验方法(GB3355-82)测作用。
这样测出的剪切强度自然是不可靠的。
国标采用[±45°]s,它有较高的纵向试剪切性能,虽然应力状态与45°偏轴拉伸相似,但此时的层板为[0°/90°]s和横向强度,保证了破坏还是由最薄弱的环节,剪切破坏所控制,所以测得的剪切强度是合理的。
(2)非均匀铺设层合板的弯曲试验非均匀铺设层合板是指层合板中并非每层都相同的层合板。
如不同角铺设的层合板,织物、单向布或毡等单层混合组成的层合板等。
经常见到此类层合板(实际应用中很常见)采用国标GBl449-83试验方法测定弯曲性能,计算弯曲强度和模量时仍然采用方法中所提供的计算公式,这是不正确的。
上述公式仅适用于均匀层合板的情况,对于非均匀层合板,应采用组合梁的计算方法计算弯曲模量和弯曲强度。
(3)非均匀铺设层合板的短梁层间剪切试验非均匀铺设层合板的短梁层间剪切试验与前一小节一样,存在不同铺层对层间应力影响的问题,不能简单套用均匀层板层间剪切强度的计算公式(CB3357-82)。
(4)不对称层合板的薄板压缩试验曾见到采用国标GB5258-85试验方法测定不对称层合板的压缩试验,测得显著偏高的压缩强度。
这可能是由于非对称层合板有较强的拉弯耦合效应,在试样受压缩应力作用时,除了产生压缩变形外,还将发生弯曲变形,这将对支撑试样侧面的夹具施加更大的侧向压力,会使试样的弯曲变形受到更大的约束,增大试样变形的阻力,产生偏高的压缩性能。
(5)纤维增强热塑性层板的层间剪切性能试验曾见到采用国标CB3357-82试验方法测定玻璃纤维增强热塑性塑料层板层间剪切性能试验,测得的载荷—挠度曲线呈现出显著的材料“强化”现象,并得到很高的“层间剪切强度”其实上述结果是不真实的。
实际情况是由于纤维增强热塑性塑料板材柔性较大,而该试验的试样厚度较薄(仅2.5mm左右),因而跨距较小(仅12.5mm)。
试验时由于变形较大,压头相对更深地压入两支座之间,造成压头和支座之间对试样相当大的挤压应力,这种受力状态下自然不可能测得可靠的层间剪切性能。
发生这种情况时,正确的做法是提高层板厚度以增大层板刚度,减少挠度,避免压头与支座之间相互挤压,确保试样始终处在层间剪切应力的控制下的应力状态。
4.3 要根据试验目的正确选择试验方法前面已提到,试验目的不同对试验会有不同的侧重方面和要求,而不同的试验方法常常是不具有可比性,因此就需要根据试验目的,正确选择对应的试验方法。
(1)内压试验方法的选择国标GB5351-85试验方法中,对管子的内压试验给出两种端部的密封形式,一种是自由端密封形式,密封端所承受的压力将直接传递到管壁,使之承受轴向拉伸应力;另一种是约束端密封形式,密封端所承受的压力由连接两密封端的金属连杆的拉力来平衡,管壁轴向受力为零。
两种密封形式的结果显然是不同比的。
给出两种形式决不意味着试验方法使用者可以任意选择其中的一种,而是根据实际情况的不同,给出对应两种不同的合理试验方法。