制氢工艺技术比较分析
常规的制氢方法及几种制氢技术的优劣势

常规的制氢方法及技术的优劣势1、工业上常用的制氢方法工业制氢方案很多,主要有以下几类:(1)煤制氢;(2)天然气制氢;(3)甲醇制氢:包括甲醇水蒸汽重整制氢、甲醇直裂制氢、甲醇部分氧化制氢;(4)水解制氢(5)富氢气体提纯制氢:各种富氢尾气(氯碱厂副产氢、炼油厂副产氢、合成氨厂副产氢、煤化工副产氢等)。
2、主流的工业制氢方案选择(1)煤制氢工艺流程复杂,环保问题也突出,目前中小型的煤制氢已经不再审批。
(2)富氢气体提纯制氢主要依托上游主装置,依赖性较强。
(3)在制氢领域,目前主要的是水电解制氢、甲醇制氢、天然气制氢,我们分别作详细介绍:3、主流的工业制氢方案介绍对比(1)电解水制氢原理是电解液(一般是含有30%左右氢氧化钾(KOH)的溶液),在接通直流电后,水分解为氢气和氧气。
该方法技术成熟、设备简单、运行可靠、管理方便、不产生污染、可制得氢气纯度高、杂质含量少,适用于各种应用场合,唯一缺点是耗能大,制氢成本高;目前商品化的水电解制氢装置的操作压力为0.8~3.0MPa,操作温度为80~90℃,制氢纯度可达99.7%,制氧纯度达99.5%。
(2)甲醇制氢原理是甲醇和水反应生成氢气和二氧化碳的合成气,再经过PSA提纯,得到高纯度的氢气。
该方法原料为甲醇和脱盐水,原料来源方便,在220~280℃下,专用催化剂上催化转化为组成为主要含氢和二氧化碳转化气;甲醇的单程转化率可达95%以上,氢气的选择性高于99.5%,再利用变压吸附技术,可得到纯度为99.999%的氢气,一氧化碳的含量低于1ppm。
(3)天然气制氢原理是天然气和水反应生成氢气和二氧化碳的合成气,再经过PSA提纯,得到高纯度的氢气。
该方法原料来源方便,不需要设置原料储罐,单系列能力较大, 原料费用较低。
反应温度在600-800℃,制氢过程需吸收大量的热,高温高压必然对设备的要求也比较高因此该装置投资高。
转化气经过变压吸附,可得到纯度为99.999%的氢气,4、主流的工业制氢方案选择4.1 小型制氢采用电解水方法(1)多年来,水电解制氢技术自开发以来一直进展不大,其主要原因是需要耗用大量的电能,电价的昂贵,用水电解制氢都不经济。
天然气制氢工艺技术
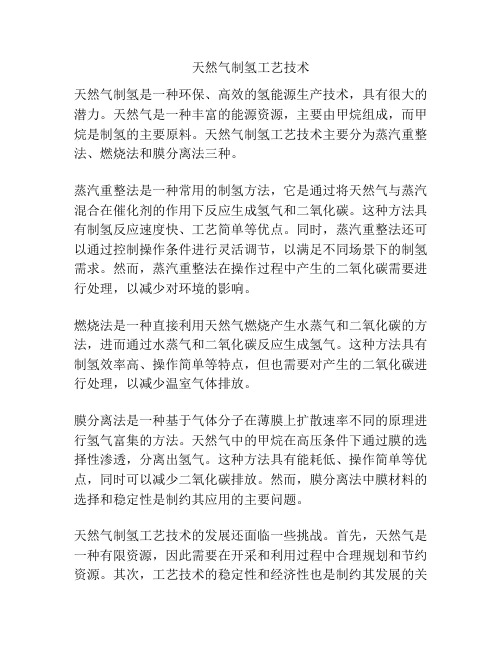
天然气制氢工艺技术天然气制氢是一种环保、高效的氢能源生产技术,具有很大的潜力。
天然气是一种丰富的能源资源,主要由甲烷组成,而甲烷是制氢的主要原料。
天然气制氢工艺技术主要分为蒸汽重整法、燃烧法和膜分离法三种。
蒸汽重整法是一种常用的制氢方法,它是通过将天然气与蒸汽混合在催化剂的作用下反应生成氢气和二氧化碳。
这种方法具有制氢反应速度快、工艺简单等优点。
同时,蒸汽重整法还可以通过控制操作条件进行灵活调节,以满足不同场景下的制氢需求。
然而,蒸汽重整法在操作过程中产生的二氧化碳需要进行处理,以减少对环境的影响。
燃烧法是一种直接利用天然气燃烧产生水蒸气和二氧化碳的方法,进而通过水蒸气和二氧化碳反应生成氢气。
这种方法具有制氢效率高、操作简单等特点,但也需要对产生的二氧化碳进行处理,以减少温室气体排放。
膜分离法是一种基于气体分子在薄膜上扩散速率不同的原理进行氢气富集的方法。
天然气中的甲烷在高压条件下通过膜的选择性渗透,分离出氢气。
这种方法具有能耗低、操作简单等优点,同时可以减少二氧化碳排放。
然而,膜分离法中膜材料的选择和稳定性是制约其应用的主要问题。
天然气制氢工艺技术的发展还面临一些挑战。
首先,天然气是一种有限资源,因此需要在开采和利用过程中合理规划和节约资源。
其次,工艺技术的稳定性和经济性也是制约其发展的关键因素,需要继续进行研究和优化。
此外,二氧化碳的处理和排放问题也需要解决,以减少对环境的影响。
然而,天然气制氢工艺技术的优势仍然明显。
天然气资源丰富,可以为氢能源提供可靠的原料,使得制氢过程更加可持续。
同时,天然气制氢可以减少对传统能源的依赖,有利于改善能源结构和减少环境污染。
另外,天然气制氢技术的应用也能为氢能源的推广提供更多的途径和可能性。
综上所述,天然气制氢工艺技术是一种具有潜力和发展前景的氢能源生产技术。
蒸汽重整法、燃烧法和膜分离法是目前主要的制氢方法。
但是,工艺技术的稳定性、资源利用和环境管理仍然是需要解决的关键问题。
氢气生产工艺
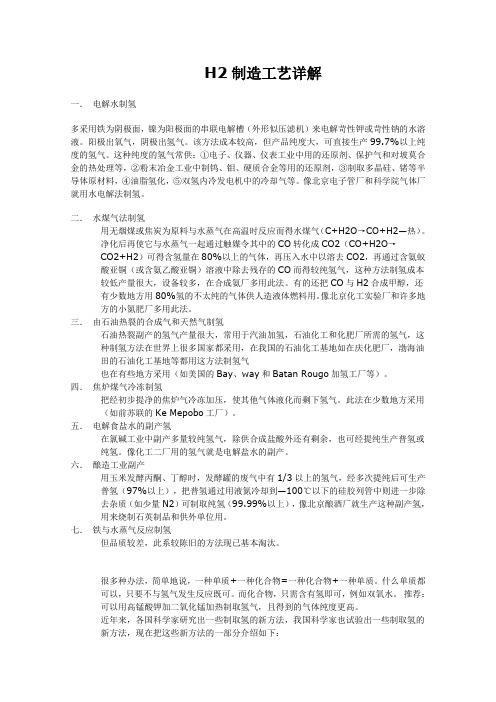
H2制造工艺详解一.电解水制氢多采用铁为阴极面,镍为阳极面的串联电解槽(外形似压滤机)来电解苛性钾或苛性钠的水溶液。
阳极出氧气,阴极出氢气。
该方法成本较高,但产品纯度大,可直接生产99.7%以上纯度的氢气。
这种纯度的氢气常供:①电子、仪器、仪表工业中用的还原剂、保护气和对坡莫合金的热处理等,②粉末冶金工业中制钨、钼、硬质合金等用的还原剂,③制取多晶硅、锗等半导体原材料,④油脂氢化,⑤双氢内冷发电机中的冷却气等。
像北京电子管厂和科学院气体厂就用水电解法制氢。
二.水煤气法制氢用无烟煤或焦炭为原料与水蒸气在高温时反应而得水煤气(C+H2O→CO+H2—热)。
净化后再使它与水蒸气一起通过触媒令其中的CO转化成CO2(CO+H2O→CO2+H2)可得含氢量在80%以上的气体,再压入水中以溶去CO2,再通过含氨蚁酸亚铜(或含氨乙酸亚铜)溶液中除去残存的CO而得较纯氢气,这种方法制氢成本较低产量很大,设备较多,在合成氨厂多用此法。
有的还把CO与H2合成甲醇,还有少数地方用80%氢的不太纯的气体供人造液体燃料用。
像北京化工实验厂和许多地方的小氮肥厂多用此法。
三.由石油热裂的合成气和天然气制氢石油热裂副产的氢气产量很大,常用于汽油加氢,石油化工和化肥厂所需的氢气,这种制氢方法在世界上很多国家都采用,在我国的石油化工基地如在庆化肥厂,渤海油田的石油化工基地等都用这方法制氢气也在有些地方采用(如美国的Bay、way和Batan Rougo加氢工厂等)。
四.焦炉煤气冷冻制氢把经初步提净的焦炉气冷冻加压,使其他气体液化而剩下氢气。
此法在少数地方采用(如前苏联的Ke Mepobo工厂)。
五.电解食盐水的副产氢在氯碱工业中副产多量较纯氢气,除供合成盐酸外还有剩余,也可经提纯生产普氢或纯氢。
像化工二厂用的氢气就是电解盐水的副产。
六.酿造工业副产用玉米发酵丙酮、丁醇时,发酵罐的废气中有1/3以上的氢气,经多次提纯后可生产普氢(97%以上),把普氢通过用液氮冷却到—100℃以下的硅胶列管中则进一步除去杂质(如少量N2)可制取纯氢(99.99%以上),像北京酿酒厂就生产这种副产氢,用来烧制石英制品和供外单位用。
制氢主要工艺

制氢主要工艺氢气是人类生活中不可或缺的能源之一,它可以作为燃料,也可以用于制造化学品。
制氢主要有三种工艺:热解法、电解法和化学反应法。
1. 热解法热解法是将天然气或其他烃类物质加热至高温,使其分解成氢气和碳。
这种方法可以通过两种不同的方式来实现:直接热解和间接热解。
直接热解是将天然气或烃类物质直接加热至高温,使其分解成氢气和碳。
这种方法需要高温和高压,通常在反应器内进行。
间接热解是通过热交换器将热能转移到反应器中,以实现分解反应。
这种方法可以减少反应器的磨损。
2. 电解法电解法是将水分解成氧气和氢气的方法,通常使用电解池来实现。
电解池由两个电极组成,分别是阴极和阳极。
在电解过程中,电子从阴极流入阳极,水分子被分解成氧气和氢气。
这种方法的优点是不需要使用化石燃料,因此不会产生二氧化碳等有害气体。
但是,电解法的缺点是成本较高,因为需要大量的电能。
3. 化学反应法化学反应法是将化学反应用于制氢的方法,通常使用天然气、煤或其他烃类物质作为原料。
这种方法通常需要使用催化剂来促进反应的进行。
化学反应法中最常用的是煤气化法。
这种方法将煤转化为合成气,然后使用催化剂将合成气转化为氢气和一些其他化学品。
这种方法的优点是可以利用廉价的煤作为原料,但缺点是会产生大量的二氧化碳等有害气体。
总结以上三种制氢主要工艺各有优缺点,具体应用要根据实际情况而定。
热解法和化学反应法适用于大规模的工业生产,而电解法则适用于小规模和分散的生产。
未来,随着技术的不断发展和能源环境的改变,制氢的工艺也将不断创新和改进。
不同制氢路径的成本比较
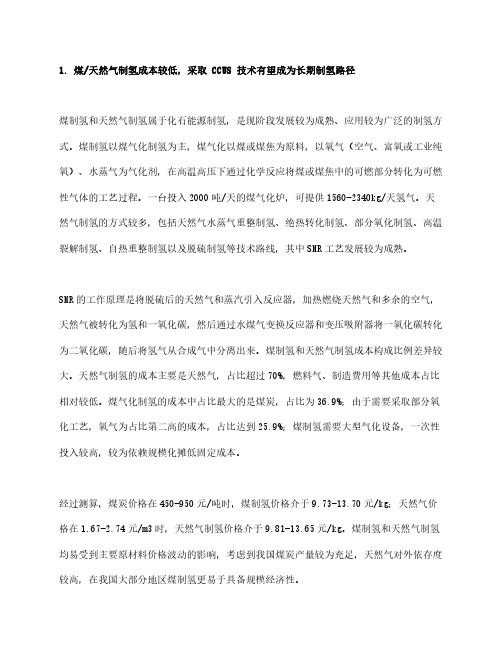
1.煤/天然气制氢成本较低,采取CCUS技术有望成为长期制氢路径煤制氢和天然气制氢属于化石能源制氢,是现阶段发展较为成熟、应用较为广泛的制氢方式。
煤制氢以煤气化制氢为主,煤气化以煤或煤焦为原料,以氧气(空气、富氧或工业纯氧)、水蒸气为气化剂,在高温高压下通过化学反应将煤或煤焦中的可燃部分转化为可燃性气体的工艺过程。
一台投入2000吨/天的煤气化炉,可提供1560-2340kg/天氢气。
天然气制氢的方式较多,包括天然气水蒸气重整制氢、绝热转化制氢、部分氧化制氢、高温裂解制氢、自热重整制氢以及脱硫制氢等技术路线,其中SMR工艺发展较为成熟。
SMR的工作原理是将脱硫后的天然气和蒸汽引入反应器,加热燃烧天然气和多余的空气,天然气被转化为氢和一氧化碳,然后通过水煤气变换反应器和变压吸附器将一氧化碳转化为二氧化碳,随后将氢气从合成气中分离出来。
煤制氢和天然气制氢成本构成比例差异较大。
天然气制氢的成本主要是天然气,占比超过70%,燃料气、制造费用等其他成本占比相对较低。
煤气化制氢的成本中占比最大的是煤炭,占比为36.9%;由于需要采取部分氧化工艺,氧气为占比第二高的成本,占比达到25.9%;煤制氢需要大型气化设备,一次性投入较高,较为依赖规模化摊低固定成本。
经过测算,煤炭价格在450-950元/吨时,煤制氢价格介于9.73-13.70元/kg;天然气价格在1.67-2.74元/m3时,天然气制氢价格介于9.81-13.65元/kg。
煤制氢和天然气制氢均易受到主要原材料价格波动的影响,考虑到我国煤炭产量较为充足,天然气对外依存度较高,在我国大部分地区煤制氢更易于具备规模经济性。
CCUS技术长期降本空间足,煤制氢/天然气制氢配套CCUS有望成为长期制氢的路线。
煤制氢和天然气制氢的碳排放均较大,利用二氧化碳捕集、封存和利用(CCUS)技术可以有效降低生产过程的碳排放水平,减排比例可达到90%以上。
采用CCS和CCU技术后,煤制氢的成本分别增加10%和38%,即煤炭价格为450元/吨时,氢气成本约上升至约14.4元/kg,若考虑到碳税,采用CCS和CCU技术的煤制氢的生产成本可能会具有优势。
制氢 方法
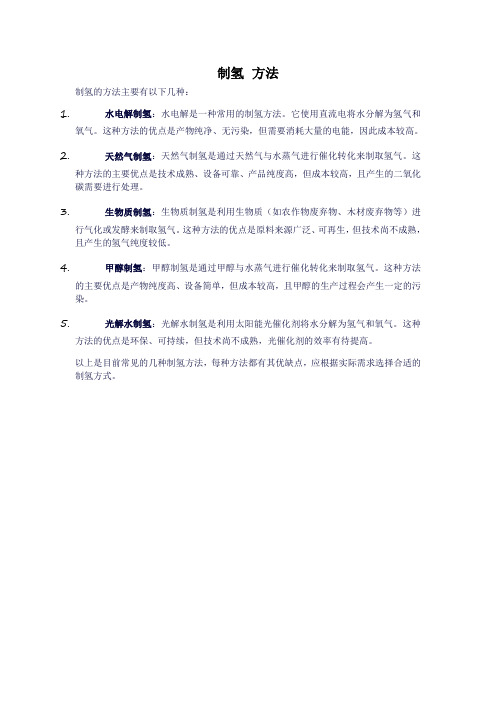
制氢方法
制氢的方法主要有以下几种:
1.水电解制氢:水电解是一种常用的制氢方法。
它使用直流电将水分解为氢气和
氧气。
这种方法的优点是产物纯净、无污染,但需要消耗大量的电能,因此成本较高。
2.天然气制氢:天然气制氢是通过天然气与水蒸气进行催化转化来制取氢气。
这
种方法的主要优点是技术成熟、设备可靠、产品纯度高,但成本较高,且产生的二氧化碳需要进行处理。
3.生物质制氢:生物质制氢是利用生物质(如农作物废弃物、木材废弃物等)进
行气化或发酵来制取氢气。
这种方法的优点是原料来源广泛、可再生,但技术尚不成熟,且产生的氢气纯度较低。
4.甲醇制氢:甲醇制氢是通过甲醇与水蒸气进行催化转化来制取氢气。
这种方法
的主要优点是产物纯度高、设备简单,但成本较高,且甲醇的生产过程会产生一定的污染。
5.光解水制氢:光解水制氢是利用太阳能光催化剂将水分解为氢气和氧气。
这种
方法的优点是环保、可持续,但技术尚不成熟,光催化剂的效率有待提高。
以上是目前常见的几种制氢方法,每种方法都有其优缺点,应根据实际需求选择合适的制氢方式。
不同制氢路径的工艺特点及成本比较

不同制氢路径的工艺特点及成本比较制氢是一种广泛应用的工业过程,用于生产氢气的不同路径有很多种。
这些路径包括煤炭气化、天然气重整、电解水、生物质转化等。
本文将分析这些不同制氢路径的工艺特点及成本比较。
首先,煤炭气化是一种常见的制氢方法,工艺特点如下:1.建设成本较高:煤炭气化厂的建设成本较高,主要是因为煤炭气化设备和相关气体净化设备的投资较大。
2.高效能转换:煤炭气化可以将煤炭转化为氮气和甲烷等气体,然后通过气体净化设备去除杂质,得到高纯度的氢气。
3.二氧化碳排放:煤炭气化过程会产生大量的二氧化碳排放,对环境造成一定的影响。
其次,天然气重整是另一种常见的制氢方法,其工艺特点如下:1.低成本:相比于煤炭气化,天然气重整的建设成本较低,主要是因为天然气作为原料更加便宜且易于获取。
2.产气质量高:天然气重整可以生产高纯度的氢气,并且能够调节氢气的产量和纯度。
3.二氧化碳排放:与煤炭气化相比,天然气重整的二氧化碳排放量较低。
接下来,电解水是制氢的一种绿色路径,其工艺特点如下:1.能源消耗:电解水是通过电流将水分解为氢气和氧气,相比于煤炭气化和天然气重整,电解水具有较低的能源消耗。
2.可再生能源:使用可再生能源如太阳能和风能作为电力源是电解水制氢的一种可行方法,能够实现零排放。
3.生产纯度高:电解水制氢可以生产高纯度的氢气,但是该方法的氢气产量相对较低。
最后,生物质转化是一种潜力巨大的制氢方法,其工艺特点如下:1.可持续性:生物质转化使用农作物秸秆、木材废弃物等生物质作为原料,具有良好的可持续性。
2.温室气体排放:生物质转化可以将生物质中的有机物转化为氢气,产生的副产品包括水和二氧化碳等,而二氧化碳可以用于植被生长,有利于减少温室气体排放。
3.技术成熟度低:尽管生物质转化具有潜力,但是目前该技术的成熟度较低,需要进一步的研发和测试。
综上所述,不同制氢路径的工艺特点及成本比较如下:煤炭气化成本较高,但能够高效能转换;天然气重整成本较低,产气质量高;电解水能源消耗低,但氢气产量相对较低;生物质转化可持续性好,但技术成熟度较低。
天然气制氢技术的不同方法
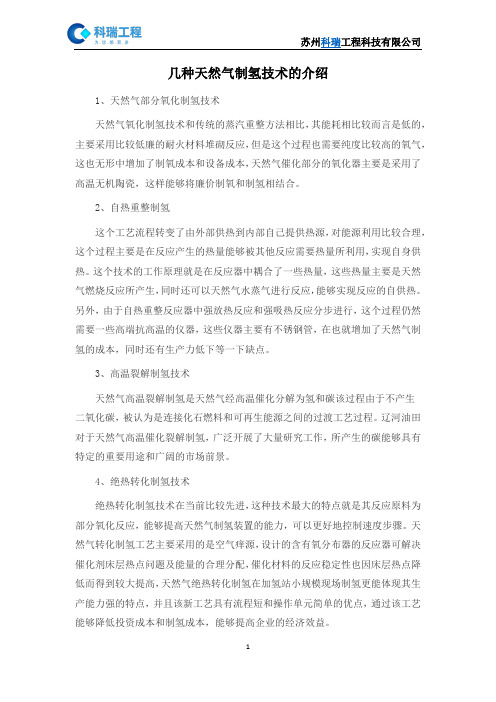
几种天然气制氢技术的介绍1、天然气部分氧化制氢技术天然气氧化制氢技术和传统的蒸汽重整方法相比,其能耗相比较而言是低的,主要采用比较低廉的耐火材料堆砌反应,但是这个过程也需要纯度比较高的氧气,这也无形中增加了制氧成本和设备成本,天然气催化部分的氧化器主要是采用了高温无机陶瓷,这样能够将廉价制氧和制氢相结合。
2、自热重整制氢这个工艺流程转变了由外部供热到内部自己提供热源,对能源利用比较合理,这个过程主要是在反应产生的热量能够被其他反应需要热量所利用,实现自身供热。
这个技术的工作原理就是在反应器中耦合了一些热量,这些热量主要是天然气燃烧反应所产生,同时还可以天然气水蒸气进行反应,能够实现反应的自供热。
另外,由于自热重整反应器中强放热反应和强吸热反应分步进行,这个过程仍然需要一些高端抗高温的仪器,这些仪器主要有不锈钢管,在也就增加了天然气制氢的成本,同时还有生产力低下等一下缺点。
3、高温裂解制氢技术天然气高温裂解制氢是天然气经高温催化分解为氢和碳该过程由于不产生二氧化碳,被认为是连接化石燃料和可再生能源之间的过渡工艺过程。
辽河油田对于天然气高温催化裂解制氢,广泛开展了大量研究工作,所产生的碳能够具有特定的重要用途和广阔的市场前景。
4、绝热转化制氢技术绝热转化制氢技术在当前比较先进,这种技术最大的特点就是其反应原料为部分氧化反应,能够提高天然气制氢装置的能力,可以更好地控制速度步骤。
天然气转化制氢工艺主要采用的是空气痒源,设计的含有氧分布器的反应器可解决催化剂床层热点问题及能量的合理分配,催化材料的反应稳定性也因床层热点降低而得到较大提高,天然气绝热转化制氢在加氢站小规模现场制氢更能体现其生产能力强的特点,并且该新工艺具有流程短和操作单元简单的优点,通过该工艺能够降低投资成本和制氢成本,能够提高企业的经济效益。
5、传统天然气制氢工艺传统的天然气制氢的工艺流程由原料气处理、蒸汽转化、CO变换和氢气提纯四大单元组成。
- 1、下载文档前请自行甄别文档内容的完整性,平台不提供额外的编辑、内容补充、找答案等附加服务。
- 2、"仅部分预览"的文档,不可在线预览部分如存在完整性等问题,可反馈申请退款(可完整预览的文档不适用该条件!)。
- 3、如文档侵犯您的权益,请联系客服反馈,我们会尽快为您处理(人工客服工作时间:9:00-18:30)。
制氢工艺技术比较分析
发表时间:2018-12-05T20:54:23.827Z 来源:《电力设备》2018年第22期作者:艾腾筐[导读] 摘要:随着国家的发展,制氢工艺技术的应用受到广泛关注,但是,由于制氢工艺技术种类很多,应用效果与效益存在差异,因此,在应用之前应重视各类工艺技术之间的对比分析,并采用科学化与合理化的方式开展综合研究工作,探索新时期的主要制氢工艺技术方式,为产业化的发展夯实基础。
(新疆美克化工股份有限公司新疆维吾尔自治区巴音郭楞蒙古自治州 841000)摘要:随着国家的发展,制氢工艺技术的应用受到广泛关注,但是,由于制氢工艺技术种类很多,应用效果与效益存在差异,因此,在应用之前应重视各类工艺技术之间的对比分析,并采用科学化与合理化的方式开展综合研究工作,探索新时期的主要制氢工艺技术方式,为产业化的发展夯实基础。
关键词:制氢;工艺技术;比较
氢气属于我国重要工业产品之一,广泛应用在石油领域、化工领域、建材领域、冶金领域、电子领域、医药领域、电力领域、轻工业领域、气象领域与交通领域,在不同领域应用中对氢气的纯度与杂质含量要求不同。
因此,为了结合各个领域的氢气需求,应筛选效率较高的制氢工艺与相关配套装置,提升经济效益并保证生产工作灵活性,满足安全管理需求,加大新工艺技术的应用力度。
一、制氢工艺技术方式分析
第一,电解水制氢工艺技术。
对于此类工艺技术而言,属于我国常用且发展成熟的制氢方法,主要将水作为原材料,形成氢气与氧燃料生成水的逆过程,达到制氢的目的。
因此,在实际制作的过程中,需要提供一定能量,并促进水分解,例如:提供电能,可以促进水分解,制氢效率为86%左右,工艺的应用较为简单,没有污染问题,且经济效益较高,但是,在实际应用过程中,对配电功率的要求很大,单套装置难以完成任务,因此,在很多区域中受到限制。
第二,天然气转化制氢工艺技术。
此类方式就是在催化剂的作用之下,使得水蒸气转化成为氢气,通常反应温度为810摄氏度左右。
此类工艺技术所制成的氢气含量在74%左右,很多大型加工厂中都在使用天然气作为燃料,对蒸汽进行催化,制取氢气。
但是,此类工艺技术在实际应用期间,流程较为繁琐,需要投入的成本很高,消耗的能源也很多,对生态环境会产生一定影响。
因此,我国已经开始针对此类工艺技术进行整改,开发间歇式的天然气蒸汽制作工艺技术,在小型设备的支持下,降低制取成本。
但是,由于原材料的分布不均匀,导致此类方式的应用受到一定限制。
第三,没碳化制氢工艺技术。
此类技术将煤设置在与空气相互隔绝的环境中,温度为950摄氏度左右,制取焦炭,副品就是焦虑煤气,其中含有60%左右的氢气。
对于焦炉煤气而言,在去除杂质之后,可以进行氢气的提取,但是,此类工艺技术的应用流程较为复杂,需要投入的资金量较高,存在制约。
第四,煤气化制氢工艺技术。
此类技术就是创建固定床类型的汽化炉设备,所制取的煤气中含有40%氢气。
在煤气杂质处理之后,可以使用相关装置进行氢气的制取,且费用很低,氢气的提取效率较高,可以应用在生产中。
第五,甲醇水蒸气转化制氢工艺技术。
通常情况下,在甲醇与脱盐水蒸汽相互混合之后,将其放置在加压加热的的容器中,可以形成催化与转化作用,生成75%的氢气。
在变压吸附的过程中,应使用吸附剂,根据压力变化对吸附剂的剂量进行动态化调整,在高压环境中对原料中杂质进行吸附,在低压环境中对杂质进行脱附处理,保证吸附剂的再生应用。
此类技术的使用可以进行脱盐水与循环液缓冲罐中的甲醇、水等混合在一起,在循环液体升压泵的支持下,进行加压处理,将其与甲醇冲关升压泵加压之后的甲醇原料混合在一起,然后设置在换热器设备中,形成自转化器的转化作用,完成第一次热交换。
在此之后,将原料液体放置在汽化塔设备中,然后在沸腾器与导热油的作用之下实现二次加热,进行汽化处理。
在转化之后进入到脱碳的程度中,在八塔七次均压环境之下,进行真空变压吸附处理,制取出相关气体,将杂质排放在大气中。
对于半成品气体而言,还需进入到PSA制氢工艺环节中,实现提纯处理目的,此时的氢气纯度甚至可以达到99.99%。
在使用甲醇水蒸气转化制氢工艺技术的过程中,工艺流程较为简单,需要支付的成本很少,且操作灵活性很高,制氢规模在8000nm3/小时左右,有利于进行精细化生产与制作,因此,在实际生产的过程中,应合理使用此类工艺技术,遵循科学化与合理化的工作原则,编制完善的计划方案,在提升整体工作质量与制氢工艺技术应用水平的基础上,更好的完成当前任务,达到预期的工作目的。
二、制氢工艺技术比较
对于电解水制氢工艺技术而言,主要使用的原材料为水,制取规模为300nm3/小时,装置在使用过程中规模很小,建设的周期很多,使用便利性高,操作灵活,但是存在耗电量大的缺点[1]。
天然气转化制氢工艺技术的应用原材料为天然气与水,制取规模为4000nm3/小时左右,工艺流程较为复杂,配套装置的安装与建设时间长,需要支付较高投资成本。
煤焦化制氢工艺技术在应用期间,原材料为煤与水,制取规模为10000nm3/小时左右,但是,煤炭的资源分布不均匀,煤焦化的工艺流程会受到一定影响[2]。
煤气化制取技术在应用过程中,原材料为煤与水,制取规模为10000nm3/小时左右,工艺流程较为复杂,对生态环境会产生污染[3]。
甲醇水蒸气转化技术的原材料为甲醇与水,制取规模为8000nm3/小时左右。
在生产过程中,甲醇原材料容易获取,运输与存储便利性高,需要投入的资金成本很低,且基础设施的建设时间很短,能耗较少。
同时,此类技术在应用期间的工艺流程很简单,灵活性符合要求[4]。
综合对比分析可以发现,甲醇水蒸气转化制氢工艺技术的应用效果较高,能够打破传统工艺技术局限性,降低成本提升制氢工艺技术应用效果,因此,需予以足够重视,广泛进行推广应用[5]。
结语:
综上所述,对比分析各类制氢工艺技术,甲醇水蒸气转化制氢技术的应用效果较为良好,因此,在实际生产期间应总结丰富经验,合理应用此类工艺技术开展工作,确保满足当前的时代发展需求。
参考文献:
[1]杨小彦,陈刚,殷海龙,等.不同原料制氢工艺技术方案分析及探讨[J].煤化工,2017(6):40-43.
[2]刘晓丽.制氢工艺技术比较[J].当代化工研究,2016(5):78-79.
[3]张兴,袁飞.轻烃蒸汽转化制氢HYSYS软件全流程模拟[J].当代化工,2017(3):546-549.
[4]刘莹.异丁烷脱氢制异丁烯技术的现状与发展趋势[J].石油化工,2016(5):630-635.
[5]孙启梅,王崇辉,王领民,等.生物柴油副产物粗甘油的综合利用[J].化工进展,2017(z1):161-166.。