吹塑模具生产技术要求
吹塑工艺技术要求
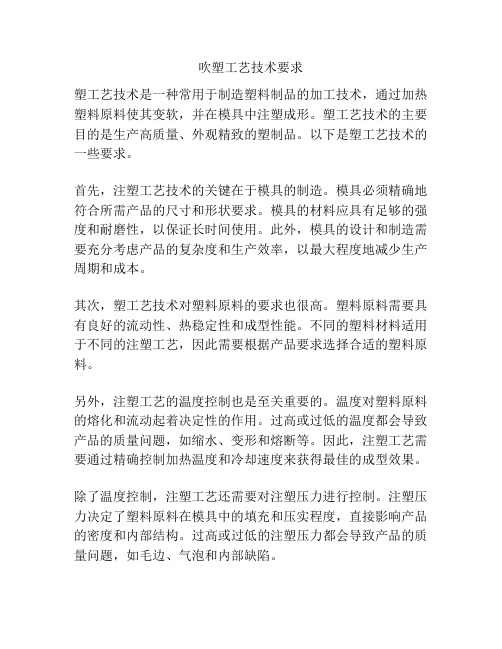
吹塑工艺技术要求塑工艺技术是一种常用于制造塑料制品的加工技术,通过加热塑料原料使其变软,并在模具中注塑成形。
塑工艺技术的主要目的是生产高质量、外观精致的塑制品。
以下是塑工艺技术的一些要求。
首先,注塑工艺技术的关键在于模具的制造。
模具必须精确地符合所需产品的尺寸和形状要求。
模具的材料应具有足够的强度和耐磨性,以保证长时间使用。
此外,模具的设计和制造需要充分考虑产品的复杂度和生产效率,以最大程度地减少生产周期和成本。
其次,塑工艺技术对塑料原料的要求也很高。
塑料原料需要具有良好的流动性、热稳定性和成型性能。
不同的塑料材料适用于不同的注塑工艺,因此需要根据产品要求选择合适的塑料原料。
另外,注塑工艺的温度控制也是至关重要的。
温度对塑料原料的熔化和流动起着决定性的作用。
过高或过低的温度都会导致产品的质量问题,如缩水、变形和熔断等。
因此,注塑工艺需要通过精确控制加热温度和冷却速度来获得最佳的成型效果。
除了温度控制,注塑工艺还需要对注塑压力进行控制。
注塑压力决定了塑料原料在模具中的填充和压实程度,直接影响产品的密度和内部结构。
过高或过低的注塑压力都会导致产品的质量问题,如毛边、气泡和内部缺陷。
此外,塑工艺技术还需要合理选择注塑周期和冷却时间。
注塑周期包括充填时间、保压时间和冷却时间。
充填时间是指塑料原料从进入模具到填充完成的时间,保压时间是指塑料原料在模具中保持压力的时间,冷却时间是指塑料原料在模具中冷却固化的时间。
合理控制注塑周期和冷却时间可以保证产品的成型完整性和稳定性。
最后,塑工艺技术还需要充分考虑产品的后续加工要求。
在注塑成型过程中,可以通过模具设计来直接实现产品的形状、表面效果和附加功能。
例如,在模具中设置凹槽、孔洞或纹理等,以减少后续加工工序,提高生产效率。
总之,塑工艺技术要求精确的模具制造、合适的塑料原料选择、恰当的温度和压力控制、合理的注塑周期和冷却时间,并充分考虑产品的后续加工要求。
通过满足这些技术要求,可以获得高质量的塑制品,提高生产效率和产品质量。
吹塑的工艺技术

吹塑的工艺技术吹塑是一种常见的塑料加工技术,也称为挤出吹塑,是利用吹塑机将加热熔融的塑料挤出成型,然后再通过气压吹气,使塑料膨胀成为中空的三维空心体。
吹塑工艺技术已广泛应用于食品包装、日用品、医疗器械以及工业制品等领域。
吹塑的工艺技术分为单层吹塑和多层吹塑两种。
单层吹塑是指通过挤出机将熔融的塑料挤出成型,并通过气压吹气使其膨胀成型。
这种技术适用于制作简单的塑料容器,如瓶子、罐子等。
多层吹塑则是在单层吹塑的基础上,通过多层挤出机、多层模头和多层模具,将不同材料的塑料层叠在一起形成多层结构,以达到更好的保温、保湿等效果。
这种技术适用于制作保温瓶、冷藏箱等需要特殊性能的产品。
在吹塑的工艺过程中,首先需要将塑料颗粒加入挤出机中进行熔融。
挤出机通过加热和搅拌将塑料颗粒熔化并形成熔融状态,然后将熔融的塑料挤出成型。
挤出成型过程中,需要根据产品的尺寸和形状来调整模具的大小和形状,以获得合适的产品形态。
挤出后的塑料形状必须与模具的孔口一致,以保证产品的准确性和一致性。
在挤出成型后,需要立即通过气压将塑料膨胀成型。
一般情况下,需要通过机械手将挤出的塑料制品转移到吹气模上,然后再进行吹气。
通过调整气压和吹气时间,可以控制产品的膨胀程度和厚度,以满足不同产品的要求。
吹塑工艺技术具有成本低、生产效率高、产品品质稳定等优点。
同时,吹塑也具有一定的局限性,如产品尺寸和形状的限制,对塑料材料的要求等。
为了提高吹塑产品的品质和效率,可以通过改善模具和模具装置的设计,提高挤出机的精度和稳定性,改进挤出和吹气工艺参数等手段来优化工艺。
总之,吹塑工艺技术是一种常见的塑料加工技术,通过挤出和吹气使塑料膨胀成型。
它具有成本低、生产效率高、产品品质稳定等优点,在食品包装、日用品、医疗器械和工业制品等领域得到广泛应用。
随着科技的进步和工艺技术的不断改进,吹塑工艺技术将有更广阔的应用前景。
吹塑成型工艺及吹塑制品设计
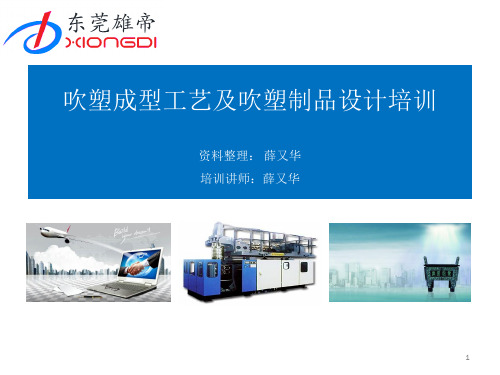
03 吹塑成型工艺材料的选择
其它小众材料的应用:
聚碳酸脂(PC) 可吹塑成高透明度的硬质容器,可直接热罐装和蒸煮,但其耐化学腐蚀性和阻渗透性能较差。
聚甲醛(POM) 用料吹塑耐高温又有刚性要求的小制件。
聚酰胺(PA) 有较高的力学性能,耐磨性及阻渗透性能较好,常用来吹塑工业制件和多层容器的阻渗透层。
吹塑成型工艺及吹塑制品设计培训
资料整理: 薛又华 培训讲师:薛又华
1
01:吹塑工艺概述 02:吹塑工艺应用领域 03:吹塑工艺材料的选择 04:吹塑制品的结构设计 05:吹塑工艺的优缺点 06:吹塑工艺的品质缺陷
吹塑工艺介绍
01 吹塑成型工艺概述
吹塑成型:即中空吹塑成型,是将从挤出机挤出的熔融热塑性胚料,夹入模具, 然后向原料内吹入空气,熔融的原料在空气压力的作用下膨胀,向模具型腔壁面 贴合,最后冷却固化成为所需产品形状的方法。 这种成型方法可生产口径不同、容量不同的瓶、壶、桶等各种包装容器,日常用 品和儿童玩具等。
(4) 热塑性聚酯(PET) 热塑性聚酯中适合吹塑成型中空制品的树脂是聚对苯二甲酸乙二醇酯(PET)。这种材料吹塑成型的中空制品 具有阻隔性、防渗透能力强,耐冲击、耐化学药品及耐压性高,有良好的透明度和光泽性好等优点,在容器 包装领域中得到了广泛应用,大量用于饮料瓶的吹塑。
(4)丙烯腈-丁二烯-苯乙烯(ABS) 适合吹塑成型中空制品的ABS,具有良好的延展性、抗冲击平衡性、耐高温、加工成型性好、翘曲变形小等特 点,大大提高了吹塑制品的尺寸稳定性,在最近的汽车部件广泛应用。 。
吹塑成型工艺介绍---拉伸中空吹塑
拉伸吹塑工艺流程
两步法生产,第一步制备型坯,型坯经 冷却后成为一种待加工的半成品,具有专门 化生产的特性。第二步将冷型坯提供另一企 业或另一车间进行再加热、拉伸和吹塑,又 称为冷型坏法。两步法的产量、工艺条件控 制是一步加工法无可比拟的,适宜大批量生 产,但能耗较多。
吹塑成型剖析
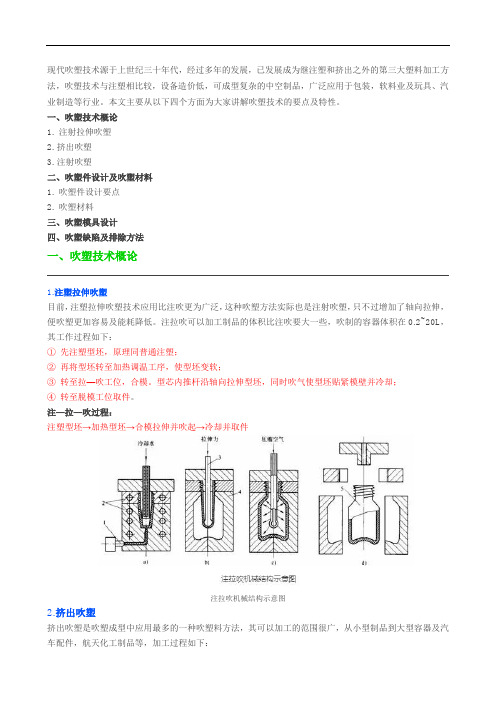
现代吹塑技术源于上世纪三十年代,经过多年的发展,已发展成为继注塑和挤出之外的第三大塑料加工方法,吹塑技术与注塑相比较,设备造价低,可成型复杂的中空制品,广泛应用于包装,软料业及玩具、汽业制造等行业。
本文主要从以下四个方面为大家讲解吹塑技术的要点及特性。
一、吹塑技术概论1. 注射拉伸吹塑2. 挤出吹塑3. 注射吹塑二、吹塑件设计及吹塑材料1. 吹塑件设计要点2. 吹塑材料三、吹塑模具设计四、吹塑缺陷及排除方法一、吹塑技术概论1.注塑拉伸吹塑目前,注塑拉伸吹塑技术应用比注吹更为广泛,这种吹塑方法实际也是注射吹塑,只不过增加了轴向拉伸,便吹塑更加容易及能耗降低。
注拉吹可以加工制品的体积比注吹要大一些,吹制的容器体积在0.2~20L,其工作过程如下:①先注塑型坯,原理同普通注塑;②再将型坯转至加热调温工序,使型坯变软;③转至拉—吹工位,合模。
型芯内推杆沿轴向拉伸型坯,同时吹气使型坯贴紧模壁并冷却;④转至脱模工位取件。
注—拉—吹过程:注塑型坯→加热型坯→合模拉伸并吹起→冷却并取件注拉吹机械结构示意图2.挤出吹塑挤出吹塑是吹塑成型中应用最多的一种吹塑料方法,其可以加工的范围很广,从小型制品到大型容器及汽车配件,航天化工制品等,加工过程如下:①先将胶料熔融,混炼,熔体进入机头成为管况型坯;②型坯达到预定长度后,吹塑模具闭合,将型坯夹在两半模具之间;③吹气,将空气吹入型坯内,将型坯吹胀,便之贴紧模具型腔成型;④冷却制品;⑤开模,取走已冷硬的制品。
挤出吹塑加工过程:熔料→挤出型坯→合模吹塑→开模取件挤出吹塑原理示意图(1—挤出机头; 2—吹塑模; 3—型坯; 4—压缩空气吹管; 5—塑件)3.注射吹塑注塑吹塑是综合了注射成型与吹塑特性的成型方法,目前主要应用于吹制精度要求较高的饮料瓶及药瓶及一些小型的结构零件等。
①在注塑工位,先注塑出型胚,加工方法同普通注塑。
②注塑模开模后,芯棒连同型坯移动到吹塑工位。
③芯棒把型坯置于吹塑模之间,合模。
中空吹塑模具设计资料文档
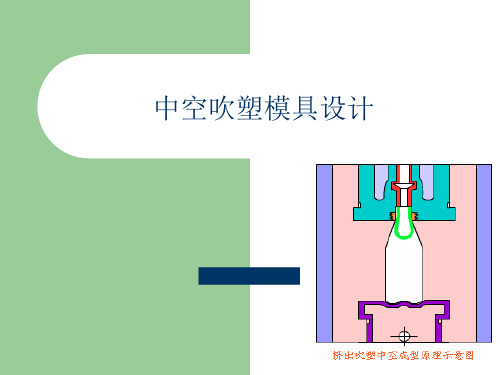
中空吹塑模具设计
4、圆角:
如果不是厚壁制品,不要将制品设计成尖角或尖边的形 状。 对圆柱形制品,边缘的圆弧半径应不小于制品直径的 1/10。 对矩形制品,圆弧半径大于0.15倍的模具型腔深度.
中空吹塑模具设计
5、螺纹:
(1)螺纹的精度一般不超过3级精度; (2)螺距一般不小于0.75mm,螺距大对模具制造及产品
横向、纵向收缩率的比较:
聚乙烯 聚氯乙烯
纵向 横向
2.1±0.1 1.9±0.2
0.36±0.0 4
0.13±0.0 5
中空吹塑模具设计
三、模具设计(以挤出吹塑为例) 1、夹坯口
1、夹坯口
1、夹坯口
hmin=0.38 通常:0.51~2.5mm; 大型容器:2~3mm。 (美)Norman C.Lee 《吹塑成型技术 》
均有好处; (3)长度一般为直径的2倍,需长螺纹时壁厚应增加,且
要计算收缩量。
6、支承面:
中空吹塑模具设计
7、收缩率:
材料
聚甲醛
尼龙
低压聚乙烯
高压聚乙烯
聚丙烯
聚苯乙烯
聚氯乙烯
收缩率 2.5~3.5 10~20 1.5~3.0 3.0~4.0 2.0~3.5 0.3~0.3 0.3~1.0
中空吹塑模具设计
W t BR
W:口模厚度; t :塑件壁厚; BR :吹胀比;
:修正系数,常取1 ~ 1.5。
中空吹塑模具设计
2、延伸比:
塑件的长度与型坯之比,SR。 为保证制品的强度、壁厚,一般SR× BR = 4 ~ 6。
中空吹塑模具设计
3、制品的斜度:
一般原则,最小斜度: 1°/边;推荐斜度:2 °/边。
吹塑的工艺技术

吹塑的工艺技术
吹塑是一种塑料加工的方法,它通过加热塑料颗粒使其熔化,然后将熔化的塑料吹入模具中,最终形成所需的产品。
吹塑工艺技术在现代工业生产中应用广泛,为生产各种塑料制品提供了便利和效率。
吹塑工艺技术的过程可以简单分为以下几个步骤:首先是原料的准备,将塑料颗粒放入吹塑机中进行加热熔化;然后是模具的制备,根据产品的设计要求选择合适的模具;接着是吹塑成型,将熔化的塑料吹入模具中,并利用气压使其充满模具,最终形成产品的外形;最后是冷却和脱模,待产品冷却固化后从模具中取出,即可得到成品。
吹塑工艺技术具有以下几个显著的优点:首先是生产效率高,可以快速大批量生产塑料制品;其次是成本低,吹塑设备简单、模具制作成本低廉;再者是产品的形状复杂多样,可以满足不同客户的需求;最后是原料可塑性强,可以用各种塑料原料进行加工,适用范围广泛。
然而,吹塑工艺技术也存在一些不足之处,比如产品的厚度不易控制、表面光洁度不高等问题。
为了解决这些问题,现代工艺技术不断进行创新和改进,引入了先进的控制系统和模具设计,提高了产品质量和生产效率。
总的来说,吹塑工艺技术在塑料加工行业中扮演着重要的角色,为
生产各种塑料制品提供了有效的解决方案。
随着科技的不断进步,吹塑工艺技术必将不断完善和发展,为塑料加工行业带来更多的机遇和挑战。
希望吹塑工艺技术能够在未来发展中发挥更大的作用,为人类社会的进步做出更大的贡献。
关于吹塑工艺介绍

关于吹塑工艺介绍关键信息项:1、吹塑工艺的定义和原理2、吹塑工艺的分类3、吹塑工艺的材料选择4、吹塑模具的设计与制造5、吹塑工艺的生产流程6、吹塑产品的质量控制7、吹塑工艺的应用领域8、吹塑工艺的优缺点9、吹塑工艺的发展趋势1、吹塑工艺的定义和原理11 吹塑是一种将塑料型坯通过压缩空气吹胀成中空制品的成型方法。
111 其原理是将处于粘流态的塑料型坯置于模具内,通过压缩空气将型坯吹胀,使其紧贴模具内壁,冷却定型后得到中空制品。
2、吹塑工艺的分类21 挤出吹塑211 挤出机将熔融的塑料挤出形成型坯,然后将型坯放入模具中进行吹塑成型。
212 适用于生产大型中空制品,如塑料桶、水箱等。
22 注射吹塑221 先用注塑机将塑料制成有底型坯,然后将型坯转移到吹塑模具中进行吹塑成型。
222 主要用于生产高精度、高透明度的中空制品,如药瓶、化妆品瓶等。
23 拉伸吹塑231 型坯经过拉伸后再进行吹塑,可提高制品的机械性能和透明度。
232 分为一步法和两步法拉伸吹塑。
3、吹塑工艺的材料选择31 常用的吹塑材料包括聚乙烯(PE)、聚丙烯(PP)、聚氯乙烯(PVC)等。
311 PE 具有良好的柔韧性和耐冲击性,广泛用于各类中空制品。
312 PP 硬度较高,耐热性好,适用于食品包装等领域。
32 材料的选择取决于制品的性能要求、使用环境和成本等因素。
4、吹塑模具的设计与制造41 模具设计要考虑制品的形状、尺寸、壁厚分布等因素。
411 合理的模具结构有助于提高制品的质量和生产效率。
42 模具制造通常采用数控加工、电火花加工等技术。
421 模具的表面质量和精度对制品的外观和尺寸精度有重要影响。
5、吹塑工艺的生产流程51 型坯制备511 通过挤出或注塑等方法制备塑料型坯。
512 控制型坯的温度、长度和壁厚等参数。
52 型坯置入模具521 将型坯准确地放入吹塑模具中。
522 确保型坯与模具的贴合度。
53 吹气成型531 向型坯内通入压缩空气,使其膨胀贴合模具内壁。
吹塑工艺注意事项

吹塑工艺是一种常用的塑料制造方法,以下是一些注意事项:
1.安全防护:在进行吹塑工艺时,需要戴上适当的个人防护装备,如手套、护目镜和口罩,
以确保自身安全。
2.材料选择:选择适合吹塑工艺的塑料材料,考虑其熔点、流动性和可塑性等特性,以获
得最佳的成型效果。
3.温度控制:严格控制加热区域和模具温度,确保塑料可以均匀且适宜地熔化和流动。
4.压力控制:根据所需产品的形状和尺寸,调整吹塑压力,使塑料能够填充模具,并保持
一定的厚度和强度。
5.模具设计:合理设计模具结构,确保塑料在充分膨胀的同时不会过度拉伸或受损。
6.冷却过程:控制好冷却时间和速度,以便让塑料在模具中固化和稳定,避免变形或开裂
的问题。
7.机器维护:定期检查和维护吹塑机械设备,确保其正常运行和高效工作。
8.质量检测:对吹塑成品进行质量检测,包括尺寸、外观和物理性能等方面,以确保产品
符合要求。
9.环境保护:妥善处理和回收废弃的塑料材料,遵守相关环保法规和政策。
10.持续改进:不断学习和改进吹塑工艺技术,提高生产效率和产品质量,追求更好的结果。
- 1、下载文档前请自行甄别文档内容的完整性,平台不提供额外的编辑、内容补充、找答案等附加服务。
- 2、"仅部分预览"的文档,不可在线预览部分如存在完整性等问题,可反馈申请退款(可完整预览的文档不适用该条件!)。
- 3、如文档侵犯您的权益,请联系客服反馈,我们会尽快为您处理(人工客服工作时间:9:00-18:30)。
吹塑模具生产技术要求
吹塑模具是塑料制品生产中必不可少的工具,它的制造技术要求非常高。
本文将从模具材料、设计要求、加工工艺等方面介绍吹塑模具的生产技术要求。
吹塑模具的材料要求具有一定的硬度和耐磨性。
常见的模具材料有工具钢、合金钢等。
这些材料具有良好的耐磨性和耐腐蚀性,能够在长时间的使用中保持模具的准确度和稳定性。
吹塑模具的设计要求非常重要。
模具设计应根据产品的形状和尺寸来确定,确保产品能够在模具中得到准确的成型。
设计时应考虑产品的收缩率、壁厚均匀性、结构强度等因素,以确保产品的质量和稳定性。
吹塑模具的加工工艺也是关键。
模具加工应采用精密的数控机床进行,以保证模具的精度和表面质量。
加工过程中还需要经过多道工序,如车削、铣削、磨削等,以确保模具的精度和表面光洁度。
吹塑模具生产技术的要求还包括模具的维护和保养。
模具在使用过程中会受到磨损和腐蚀,需要定期进行维修和保养,以延长模具的使用寿命。
维护工作包括清洁模具表面、修复损坏部分、涂覆防锈剂等。
吹塑模具生产技术还需要注意模具的冷却系统。
模具的冷却系统应
设计合理,确保在模具制造过程中能够有效地冷却模具,并在使用过程中能够快速冷却产品,以提高生产效率和产品质量。
吹塑模具生产技术要求非常严格,涉及到材料选择、设计要求、加工工艺等多个方面。
只有按照这些要求进行生产,才能制造出高质量的吹塑模具,满足塑料制品生产的需求。
希望本文的介绍能够对吹塑模具生产技术有所帮助。