统计过程控制
统计过程控制(SPC)

11
控制图的选择
控制图的选定
计量值 数据性质
计数值
平均值
“n”=10~25 “n”是否较大
n≧1 样本大小 n≧2
Cl的性质
中位数 “n”=2~5
“n”=1
不良数
缺陷数
不良数或
缺陷数
不一定
一定
“n”是否一定
单位大小 是否一定 不一定 一定
X-s 图
X-R 图
X-R
X-Rm “p”
图
图图
“np” “c”
数据类别: 计数值数据:只以缺陷数和个数表示,不能连续取值的数据 计量值数据:以产品本身的特性来表示,可以连续取值的数据
2
两种变异
普通性(特定性)变异:不易避免的原因(普通 原因)造成的变异,如操作人员的熟练程度的 差异、设备精度与保养好坏的差异、同批原材 料本身的差异
特殊性(偶尔性)变异:可以避免也必须避免 的原因(特殊原因)造成的变异,如不同原材料 之间的差异、设备故障
“u”
图图
图
12
案例1(控制图的选择)
质量特性 长度 重量 乙醇比重 电灯亮/不亮 每一百平方米的 脏点
样本数 5 10 1
100 100平方米
选用什么图
13
答案1
质量特性 长度 重量 乙醇比重 电灯亮/不亮 每一百平方米的 脏点
样本数 5 10 1
100 100平方米
选用控制图 均值极差控制图
通常用来消除变差的普通原因 几乎总是要求管理措施,以便纠正 大约可纠正85%的过程问题
8
控制图的目的
控制图和一般的统计图不同,因其不仅能 将数值以曲线表示出来,以观其变异之趋 势,且能显示变异系属于机遇性或非机遇 性,以指示某种现象是否正常,而采取适 当之措施。
统计过程控制

统计过程控制
一、过程能力是指过程加工质量方面的能力, 它是衡量过程加工内在一致性的,也可称为 工序能力。而生产能力则指加工数量方面的 能力。过程能力确定于质量因素:人机料法 环,而与公差无关。
统计过程控制
二、过程能力指数 对具有双侧公差的过程来讲: 设规范要求特性值在LSL(TL) 与USL( TU)之间, 那么过程能力指数为:
Prediction
统计过程控制
Shift
Prediction
统计过程控制
Drift
Prediction
统计过程控制
统计过程控制
四、控制图在贯彻预防原则中的作用
➢及时告警 ➢发现异常执行“20字方针”
查出异因,采取措施,加以消除, 不再出现,纳入标准。
统计过程控制
五、统计控制状态 稳态 只有偶因 好处 全稳生产线
二、采用常规控制图应考虑的一些问题
1. 控制图用在何处?若所选的控制 对象的质量指标应能定量,则可选 用计量控制图,否则用计数控制图。 所控制的过程具有重复性。 2. 如何选择控制对象?应选用能代 表过程的主要质量指标作为控制对 象。可以选一个质量指标,也可能 要选几个质量指标。
统计过程控制
3. 如何选择控制图?应该根据所选指标 是定量的还是定性的来选,此外还要考 虑抽取样品、数据获得的难易等
CL p
UCL p 3 p(1 p) / n
LCL p 3 p(1 p) / n
当LCL<0时,取LCL=0
统计过程控制 (6) np图
CL np
UCL np 3 np(1 p)
LCL np 3 np(1 p)
当LCL<0时,取LCL=0
统计过程控制 (7) u图
统计过程控制(SPC)
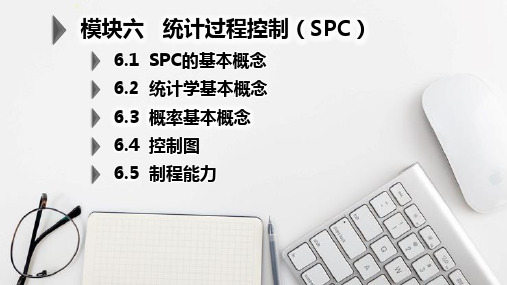
足公司管理需求作用。
6.2 统计学基本概念
6.2.1 统计学基础
母体指某家特定工厂所生
产的商品。
母体的子集代替研究母体
的每一笔资料,称做样本。
以某种经验设计实验所搜
集的样本叫做资料。
图6-4 统计学原理
利用推论统计学方法,将资料中的数据建模,计算它的机率并且做出对于母
常常是不经济的。
如果目前的产品不能满足顾客的要求,则有必要将所有的产品进行分类,
报废不合格品或返工。这种状态将持续到对过程采取必要的校正措施并验证,或
持续到产品更改为止。
在统计质量控制(SQC-Statistical Quality Control)过程中,引起质量波
动的原因主要来自六个方面(5M1E):
体的推论。
这个推论可能以对/错问题的答案所呈现(假设检定),对数字特征量的估
计,对未来观察的预测,对关联性的预测(相关性),或是将关系模型化。
在统计学中,其基本要素包括:
1. 母体与样本的关系
母体和样本的概念不是固定不便的,随着研究的不同,母体和样本也会有所
不同。
2. 指标与标志的区别
指标是说明总体特征;而标志是说明总体单位特征的。标志可以分为不能用
以下几个阶段:
第一阶段:
SPC--统计过程控制,可判断过程的异常,及时告警;不能告知此异常是什
么因素引起的。
第二阶段:
SPCD--统计过程控制与诊断,SPCD既有告警功能,又有诊断功能。
第三阶段:
SPCDA--统计过程控制、诊断与调整,它能控制产品质量、发现异常并诊
断导致异常的原因、自动进行调整。
统计过程控制(SPC)

(三) x R 控制图的操作步骤
1. 确定控制对象(统计量) 2. 收集k组预备数据(一般K=25;每组数
据个数n ≥ 2;遵循合理子组原则) 3. 计算每一个样本的均值 X i 与极差 Ri 。 4. 计算 X与R 5. 计算R图控制限并作图 6. 用各样本点绘在图中,判断状态。
分析过程若失控或异常,找出原因, 进行纠正,防止再发生。
7. 计算 X 图控制限并作图,判断状态。 8. 计算过程能力指数验证是否符合要求 9. 延长控制限,作控制用控制图,进行日
常管理
四、 X S 图(掌握) 五、X-Rs图(了解)
六、Me-R图(了解)
七、P控制图
(一)P控制图的控制状态
P 常数
n
n
ˆp p di / ni
i1 i1
(二)P控制图的统计基础为二项分布,其
内容 (1)利用控制图分析过程的稳定性,对
过程存在的异常原因进行预警;
(2)计算过程能力指数分析稳定的过程 能力满足技术要求的程度,对过程质量进行 评价。
三、统计过程控制的特点 是一种预防性的方法 贯彻预防原则是现代质量管理的核心 强调全员参与
SPC的涵义
为了贯彻预防原则,应用统计技术对 过程各阶段评估和监控,建立并保持过程 处于可接受的并且稳定的水平从而保证产 品与服务符合规定的要求的一种质量管理 技术。
过程能力指数 过程性能指数
CP
TU TL 6ˆ ST
PP
TU TL 6ˆ LT
其中 ˆ St —— 短期波动的标准差估计,在稳态
下计算
ˆ St
R d2
或
S C4
ˆ Lt —— 长期波动的标准差估计,在实
际情况下计算 ˆ Lt S
统计过程控制知识
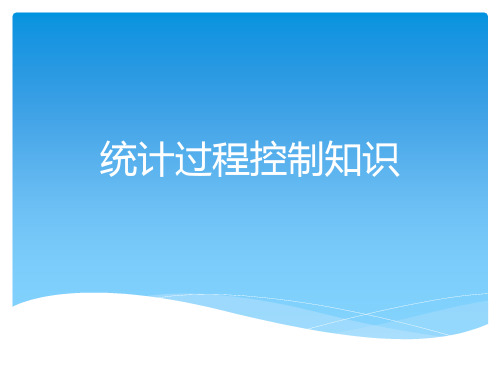
4
一、什麽是统计过程控制
2.预防与检测
1)事后检测——质量控制的最原始手段;
a.通过检查最终产品并剔除不符合规格产品, 保证不合格品不提交给顾客或下一工序;
1)直观方法(传统方法), 2)用统计控制方法;
二者之间有何区别呢?下面我们举例说明:
某公司是一家家电产品制造商,为了提高管理水平,导入了品质成 本管理体系,经过前期努力,其统计取得了前5个月的品质成本数据 如下表:
16
4.观察和处理过程变异的两种方法:
时间 星期一 星期二 星期三 星期四 星期五 平均
4.质量特性二重性: 绝对的波动性和相对的稳定性
1) 质量——是过程的结果,是顾客关注的 核心;
2) 波动性是绝对的,稳定性是相对的; a 波动就是过程变异的外在表现; b 过程控制就是有效限制波动,强化或 增强稳定
8
一、什麽是统计过程控制
5.统计过程控制的实质: 就是通过观察产品/过程波动;分析、鉴定产品/过程波 动的原因,将其控制在相对稳定的状态,从而保证过 程输出的稳定性。
16320 16534 17323 16231 17213 17574 17694 18101 17121 18752 16580 16989 17213 17029 16781 18123 17564 17856 16871 17549
15698 16497 17301 17457 16545 17210 17230 16561 17543 18584 15991 15302 17530 17056 17234 17694 17011 16981 16594
03质量管理第3章 统计过程控制

上控制限
目 标 值
下控连制限续11个点中有10个点在中心线一侧;
点子呈现周期性变化
上控制限
目 标 值
下控制限
点子呈现周期性变化
六、控制图的应用程序和 作图方法
• 1、合理选择应用控制图的场合 • 2、选择控制对象 • 3、选择控制图 • 4、合理子组 • 5、绘制分析用控制图 • 6、确定控制标准 • 7、控制图的管理
1 k
k i 1
Ri
X 96.53 3.861 25
R 25.7 1.028 25
绘制 X R控制图步骤:
• 4、计算控制图的参数 • 查表得:A2=0.729,D4=2.282,D3=0
X图的控制界限
CLX X 3.861 UCLX X A2R 3.861 0.7291.028 4.610 LCLX X A2R 3.861 0.7291.028 3.112
X图的控制界限
CLX X 3.861 UCLX X A2R 3.861 0.7291.028 4.610 LCLX X A2R 3.861 0.7291.028 3.112
绘制X R 控制图步骤:
• 5、画控制图
4.8
UCL=4.610
4.6
4.4
3.9
4.10
0.6
4.2
3.62
1.0
3.0
3.5
1.2
3.7
3.62
0.6
12
3.1
4.4
4.8
4.2
4.05
1.4
13
3.4
3.7
3.8
3.9
3.70
SPC统计过程控制

SPC统计过程控制SPC(Statistical Process Control,统计过程控制)是一种基于统计原理和数据分析方法的质量管理工具,用于监控和控制生产过程中的变异性,以确保产品或服务的质量。
SPC是由质量概念的先驱沃尔特·A·谢温(Walter A. Shewhart)在20世纪20年代初首次引入的。
它的目的是通过使用统计技术来分析生产过程中的数据,从而减少产品或服务的变异性,提高整体质量水平。
SPC的基本原理是通过统计分析来了解生产过程中的变异性,以便及时采取措施来纠正和调整生产过程。
它主要包括以下步骤:1.确定控制指标:选择适当的指标来监控生产过程的变异性。
常用的指标包括尺寸、重量、硬度等。
2.收集数据:根据预定的采样计划和频率,定期收集生产过程中的数据。
数据可以通过各种手段收集,如直接测量、抽样检验等。
3.绘制控制图:使用统计方法将收集到的数据绘制成控制图。
控制图是一种图表,它显示了一个或多个过程指标的变化情况,以及上下限范围。
通过观察控制图,人们可以判断生产过程是否处于控制状态,是否存在异常情况。
4.分析控制图:根据控制图上的变化趋势和模式,进行统计分析,以确定生产过程的绩效。
常用的统计分析方法包括均值、标准差、极差等。
5.制定改进措施:根据分析的结果,确定需要改进的方面,并制定相应的措施。
改进措施可以包括修改生产过程参数、调整设备、培训员工等。
6.监控和调整:持续监控生产过程,并根据需要进行调整,以确保控制图保持在预定的限制范围内。
SPC的优势在于它能够提供实时和持续的监控生产过程的能力。
通过采集数据和绘制控制图,生产者可以及时发现生产过程中的变异,并采取措施进行纠正。
这样可以防止不良品的产生,并提高产品或服务的一致性和质量。
此外,SPC还具有以下几点优势:1.提高生产效率:通过控制和减少生产过程中的变异性,SPC可以提高生产效率。
它能够帮助生产者发现并消除生产过程中的浪费和不必要的变动,从而提高生产效率和资源利用率。
统计过程控制
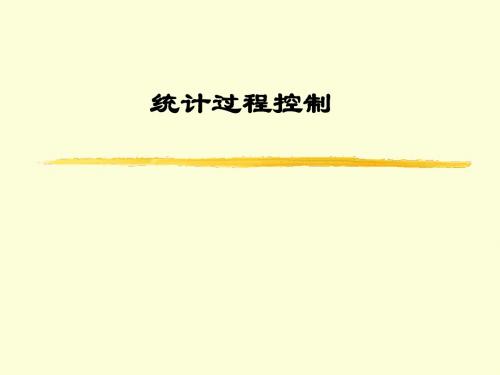
失去控制(有异因)
稳态图示
规格下限
技术稳态
规格上限
(偶因的变异减少)
年我国著名质量管理专家、北京科技大学张公绪教授提出选控图及两
种质量诊断理论,突破了休哈特的SPC理论,使SPC上升到SPD。 SPD不仅能预警, 而且能诊断, 为及时纠正提供了有利保障.
统计本身不能提高制程能力,消除 异常因素! 它是我们的工具。
第二节
控制图原理
一、控制图的结构
控制图(Control Chart)是对过程质量特性值进行测定、记录、
评估,从而监察过程是否处于控制状态的一种用统计方法设计的图。
样 本 统 计 量 数 值 描点序列 上控制限(UCL) 中心线(CL)
下控制限(LCL)
控制图示例
时间或样本号
控制图组成包括中心线、上下控制限以及按时间顺序抽取的样本 统计量数值的描点序列。
二、控制图的重要性
控制图是贯彻预防原则的SPC的重要工具,可用以直接对产品生 产过程的控制与诊断,是质量管理(老)七个工具的重要组成部分。
LCL为下控制限。
控制图虽然由正态分布转化而来,由于二项分布、泊松分布当样本量较 大时近似正态分布,因此,控制图对典型分布均适用。
(二)控制图原理的第一种解释 (1)若过程正常,即分布不变,则出现点子超过上或下控制限情
况的概率只有1‰左右。( 0.27%÷2 = 1.35‰ )
(2)若过程异常,发生这种情况的可能性很大,其概率可能为 1‰的几十乃至几百倍。 例如:当正态分布的均值偏移1.5σ 的情况 不合格品率 p=1-Φ(1.5 ) + Φ(-4.5 ) =2- Φ(1.5 ) - Φ(4.5 ) =0.06681 根据小概率事件原理:即小概率事件在一次试验中几乎不可能发 生,因此,若发生即可判断异常。
- 1、下载文档前请自行甄别文档内容的完整性,平台不提供额外的编辑、内容补充、找答案等附加服务。
- 2、"仅部分预览"的文档,不可在线预览部分如存在完整性等问题,可反馈申请退款(可完整预览的文档不适用该条件!)。
- 3、如文档侵犯您的权益,请联系客服反馈,我们会尽快为您处理(人工客服工作时间:9:00-18:30)。
第一章 SPC简介第一节什么是SPC一、 定义:SPC是英文Statistical Process Control的字首缩写,即统计过程控制。
SPC就是应用统计技术对过程中的各个阶段进行监控,从而达到改进与保证质量的目的。
SPC强调全过程的预防。
二、 SPC的特点:1)SPC是全系统的,全过程的,要求全员参与,人人有责;2)SPC强调用科学方法(主要是统计技术,尤其是控制图)来保证全过程的预防;3)SPC不仅用于生产过程,而且可用于服务过程和一切管理过程。
三、 为什么要推行SPC?优质企业平均有73%(用SPC方法的)的过程Cpk超过1.33,低质企业只有45%过程达到Cpk=1.33。
Cpk>1.67的企业,平均销售收入增长率为11%以上,而其它企业的数据为4.4%。
一家企业用了三年的时间使废品率降低58%,其使用的方法:将使用SPC的过程比例由52%增加到68%。
1)时代的要求:PPM管理、6σ管理;2)科学的要求;3)认证的要求;4)外贸的要求。
四、推行SPC的目标A.达到统计受控状态;B.维持统计受控状态;C.改进过程能力。
第二节 SPC发展简史过程控制的概念与实施监控的方法早在20世纪20年代就由美国的休哈特(W.A.Shewhart)提出。
今天的SPC与当年休哈特的方法并无根本的区别。
SPC迄今为止经历了三个发展阶段,即:SPC,SPCD及SPCDA。
1)第一阶段为SPC:SPC是美国休哈特在20世纪二、三十年代所创造的理论,它科学地区分出生产过程中产品质量的偶然波动与异常波动,从而对过程的异常及时告警,以便采取措施,消除异常,恢复过程的稳定。
这就是所谓统计过程控制;2)第二阶段为SPCD:SPCD是英文Statistical Process Control and Diagnosis的缩写,即统计过程控制与诊断。
SPCD是SPC的进一步发展,1982年我国张公绪首创两种质量诊断理论,突破了传统的美国休哈特质量控制理论,开辟了统计质量诊断的新方向。
目前SPCD已进入实用性阶段;3)第三阶段为SPCDA:SPCDA是英文Statistical Process Control,Diagnosis and Adjustment的缩写,即统计过程控制、诊断与调整。
这方面国外刚刚起步,他们称为ASPC(AlgorithmicStatistical Process Control,算法的统计过程控制),目前尚无实用性的成果。
第三节 SPC应用领域及与QS9000的关系一、SPC应用领域原则上,SPC应该用于有数量性和持续性的所有工艺过程;SPC研究的前提是测量系统受控且其变差占过程总变差的比例很小;SPC使用的领域是大规模生产;多数企业,SPC用于生产阶段;在强调预防的企业,在开发阶段也使用SPC。
二、SPC与QS9000 名称条款内容举例持续改进 4.2.5 “供方必须制定优先化的措施计划,以持续改进那些表明稳定,具有可接受的能力和性能的过程”过程控制 4.9 “---,确保这些过程在受控状态下进行”过程检验和试验4.10.3“针对防止缺陷发生的直接过程活动,例如,统计过程控制,---,而不是找出缺陷”统计技术 4.20 SPC即一种统计技术产品和过程确认APQP 输出要素之一:“初始过程能力研究” 生产件批准要求PPAP “---并提供支持数据,如控制图。
”第二章 过程控制系统第一节 预备知识一、概率A .什么是随机现象?→ 每次观察或试验,结果不确定。
→大量重复观察或试验,结果呈现某种统计规律B .概率NN A P A =)(二、两类随机变量三、标准正态分布曲线及分布概率 A .标准正态分布曲线B .正态分布的概率μ——均值 σ ——方差σ——标准差 ± 3σ——常用来表示变差的大小2四、二项式分布与泊松分布A.二项式分布——“0-1”分布。
如对,错、男,女、合格不合格等;B.泊松分布——“单位产品上的缺点数”。
随机变量X=c 0 1 2 …… 出现的概率P(A) P0P1P2……P0 +P1+P2 +P3+……=1五、抽样实验A.术语母体:指某次统计分析中,所研究的对象全体;个体:所研究对象的一个单位;样本:部分个体用于测量;样本容量:样本中所含个体的数目;抽样频率:抽取样本的频次。
B.正态分布参数C.产品质量的统计观点z产品质量具有变异性;z产品质量的变异具有统计规律性。
第二节两种不同的过程控制模型一、过程的定义:所谓过程指的是共同工作以产生输出的供方、生产者、人、设备、输入材料、方法和环境以及使用输出的顾客之集合(见图一)。
ISO9000:2000中“过程”----使用资源将输入转化为输出的活动的系统。
两种过程控制模型的比较稳定一般产品质量避免浪费 容忍浪费经济性预防 检测方法 过程 输出控制点 反馈模型 检测模型第三节 两种变差原因及相应的两种控制措施一、变差的普通与特殊原因没有两件产品是完全相同的,因为任何过程都存在许多引起变差的原因。
产品间的差距也许很大,也许小得无法测量,但差距总是存在。
例如影响一个电池得高度的因素有设备(磨损率、速率)、原材料本身特性差异、操作人员及环境(温度、动力供应)等。
零件变差位于公司规定的公差范围内是可接受的,超出公差范围是不可接受的;按时完成报告是可接受的,迟缓的报告是不可接受的。
而管理任何一个过程减少变差时,都必须追究造成变差的原因。
首先要区分普通原因和特殊原因。
普通原因指造成随着时间的推移具有稳定的且可重复的分布过程中的许多变差的原因,我们称之为:“处于统计控制状态”、“受统计控制”,或有时简称“受控”。
特殊原因(可查明原因)指的是造成不是始终作用于过程的变差的原因,即当它们出现时将造成(整个)过程的分布改变。
由于特殊原因造成的过程分布的改变有些有害,有些有利。
有害时应识别出来并消除它,有利时可识别出来并使其成为过程恒定的一部分。
(见图4)如果仅存在变差的普通原因,随着时间的推移,过程的输出形成一个稳定的分布并可预测如果存在变差的特殊原因,随着时间的推移,过程的输出不稳定二、两种控制措施À系统措施9通常用来减少变差的普通原因9通常要求管理层的支持9工业经验,约占过程措施的第四节过程控制与过程能力一、 过程控制要点À收集数据并用统计方法来解释它们并不是最终目标,最终目标是加深对过程的理解,以持续改进为目的;À研究变差和应用统计知识来改进性能的基本概念适用于任何领域,包括行政管理;À属于系统的问题不要去责难现场人员,要由系统采取措施(理解什么是“控制不足”);À属于局部的问题也不要轻易采取系统措施(理解什么是“过度控制”);À有用的特殊原因变差,应该保留。
二、过程能力A.什么是过程能力过程在统计受控状态下的变差大小;过程能力是由造成变差的普通原因确定的;特性分布服从正态分布;过程能力通常代表过程本身的最佳性能;过程能力与技术规范无关。
B.如何计算过程能力在正态分布的情况下,过程能力用分布的±3σ宽度来描述。
C.四类过程按过程是否受控及过程特性是否满足技术规范要求(即是否可接受),分为四类:I.理想过程,过程受控又满足技术规范要求;II. 过程受控,不满足技术规范要求,必须降低普通原因造成的过大的变差;III. 过程可接受,但存在特殊原因的变差,要找出特殊原因并消除,只有在个别情况下,如特殊原因已查明,并具有一定的稳定性,消除措施成本过大,顾客特允时可以保留;IV.即不受控又不可接受,应采取措施,消除变差的特殊原因和降低普通原因的变差。
D .过程控制与过程能力图示A .)?PK P C ,规范中心值规范上限规范下限为两者较小值PKPLPUCLSL CUSLC ⎪⎪⎭⎪⎪⎬⎫−=−=σμσμ332/)(3PLPUP CCLSLUSLC+=±−=σC P 、C PK 表示过程能力满足技术规范的程度;C PK 值与σ,技术规范宽度,分布和技术规范的相对位置有关; 当过程均值与规范中心值重合时,C PK =C P 。
B .典型的能力指数Cpk 与PPM 关系一、两种不同的质量观第五节 持续改进由图大家可以看出,第一种观点是除去坏的全部是好的,第二种观点是尽量往目标值靠拢保证产品的损失最小。
三、持续改进过程循环的各个阶段A.分析过程¾本过程应做些什么?¾会出现什么问题?¾本过程正在做什么?¾确定能力。
B.维护(控制)过程¾监控过程性能;¾查找变差的特殊原因并采取措施。
C.改进过程¾改变过程从而更好地理解普通原因变差;¾减少普通原因变差。
第三章了解控制图第一节 概述一、控制图的作用A.什么是控制图B .控制图的的益处À 现场人员了解过程变差并使之达到统计受控状态的有效工具; À 有助于过程在质量上和成本上持续地,可预测地保持下去;À 对已达到统计受控的过程采取措施,不断减少普通原因变差,以达到提高质量,降低成本和提高生产率的改进目标;À 现场人员、支持人员、设计人员、顾客等提供有关过程性能的共同语言; À 区分变差的特殊原因和普通原因,作为采取局部措施或对系统采取措施的依据。
二、应用控制的准备工作→建立适用于实施的环境;→定义过程;→确定待管理的特性 考虑到:________顾客的需求;________当前及潜在的问题区域; ________特性间的相互关系; →定义测量系统,使之具有可操作性;→使不必要的变差最小。
三、控制图的制作步骤(1)收集数据 (7)修正数据或重新采集数据 (2)画图 (8)重新画图和计算控制限 (3)计算试验控制限 (9)计算过程能力性能和指数 (4)将试验控制限及中心线画在图上 (10)分析过程能力(5)分析控制图 (11)保持过程、改进过程(6)分析特殊原因,采取措施消除 (12)控制图制作及应用程序图图R X −四、控制图的类别计量型数据控制图,有均值和极差图()、均值与标准差图(R x −~图s X −)、中位数图(图)、单值和移动差图(X-MR 图)等;B. 计数型数据控制图,有不合格品率的p 图、不合格品数的np 图、不合格数的c 图、单位产品不合格数的u 图等。
图R X −)第二节 均值和极差图(一、收集数据A.选择子组大小、频率和数据A.1子组大小——计量型控制图的第一关键步骤就是“合理子组”的确定,这一点将决定控制图的效果及效率。
选择子组应使得一个子组内在该单元中的各样本之间出现变差的机会小。
在过程初期研究中,子组一般由4到5件连续生产的产品组合,这样子组内的零件都是在很短的时间间隔内及非常相似的生产条件下生产出来的,子组内的变差主要是普通原因造成的。