薄膜技术中pvd和cvd的区别详解
PVD与CVD
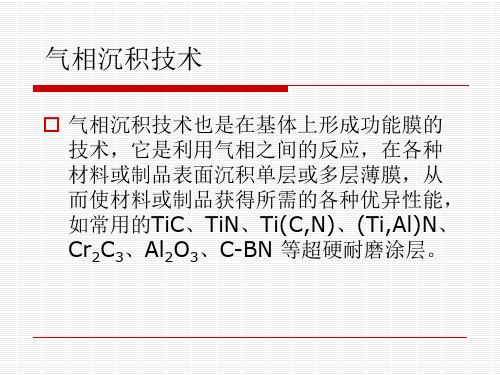
2.蒸发镀用途
蒸镀只适用于镀 制对结合强度要 求不高的某些功 能膜,例如用作 电极的导电膜, 光学透镜的反射 膜及装饰用的金 膜、银膜。
2.蒸发镀用途
蒸镀纯金属膜中90%是铝膜,铝膜有广泛的用 途。 目前在制镜工业中已经广泛采用蒸镀,以铝代 银,节约贵重金属。 集成电路是镀铝进行金属化,然后再刻蚀出导 线。在聚酯薄膜上镀铝具有多种用途,可制造 小体积的电容器;制作防止紫外线照射的食品 软包装袋等;经阳极氧化和着色后即得色彩鲜 艳的装饰膜。 双面蒸镀铝的薄钢板可代替镀锡的马口铁制造 罐头盒。
一、 蒸发镀
在真空条件下,用加热蒸发的方法使镀膜材 料转化为气相,然后凝聚在基体表面的方法 称为蒸发镀膜,简称蒸镀。 蒸发镀是PVD方法中最早用于工业生产的一 种方法,该方法工艺成熟,设备较完善,低 熔点金属蒸发效率高,可用于制备介质膜、 电阻、电容等,也可以在塑料薄膜和纸张上 连续蒸镀铝膜。
绕射性好。
基片的正面反面甚至内孔、凹槽、狭缝等,都能沉积上薄膜。
沉积速率快,镀层质量好 。
离子镀膜获得的镀层组织致密,针孔、气泡少。而且镀前对工件 ( 基片 )清洗处理较简单。成膜速度快,可达 75m/min ,可镀制厚 达30m的镀层,是制备厚膜的重要手段。
2 离子镀膜的特点
可镀材质广泛
真空蒸镀时,蒸发粒子动能为0.1~1.0eV,膜对 基体的附着力较弱,为了改进结合力,一般采 用: 在基板背面设臵一个加热器,加热基极,使基 板保持适当的温度,这既净化了基板,又使膜 和基体之间形成一薄的扩散层,增大了附着力。 对于蒸镀像Au这样附着力弱的金属,可以先蒸 镀像Cr,Al等结合力高的薄膜作底层。
1.基本原理
其中靶是一平板,由欲沉积的材料组成,一般 将它与电源的负极相连,故此法又常称为阴极 溅射镀膜。 固定装臵可以使工件接地、悬空、偏臵、加热、 冷却或同时兼有上述几种功能。真空室中需要 充入气体作为媒介,使辉光放电得以启动和维 持,最常用的气体是氩气。
PVD与CVD涂层工艺比较
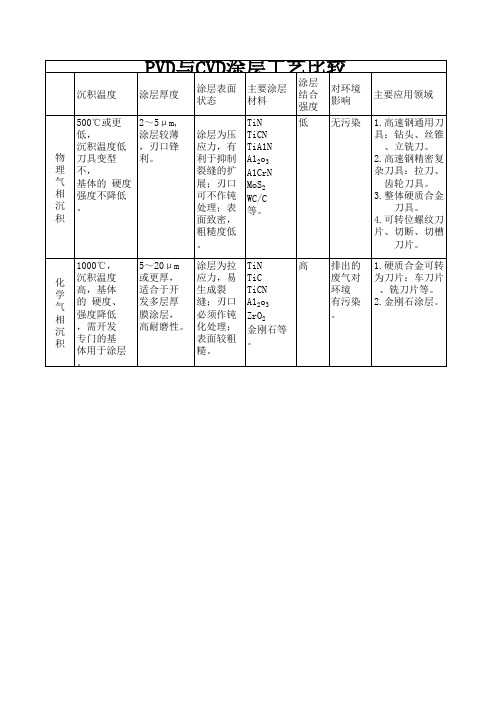
物 理 气 相 沉 积
化 学 气 相 沉 积
1000℃, 沉积温度 高,基体 的 硬度~20μ m 或更厚, 适合于开 发多层厚 膜涂层, 高耐磨性。
TiN TiC TiCN A12o3 ZrO2 金刚石等 。
高
排出的 废气对 环境 有污染 。
PVD与CVD涂层工艺比较
沉积温度 500℃或更 低, 沉积温度低 刀具变型 不, 基体的 硬度 强度不降低 。 涂层厚度 2~5μ m, 涂层较薄 ,刃口锋 利。 涂层表面 状态 涂层为压 应力,有 利于抑制 裂缝的扩 展;刃口 可不作钝 处理;表 面致密, 粗糙度低 。 涂层为拉 应力,易 生成裂 缝;刃口 必须作钝 化处理; 表面较粗 糙。 主要涂层 材料 TiN TiCN TiA1N A12o3 A1CrN MoS2 WC/C 等。 涂层 结合 强度 低 对环境 影响 无污染 主要应用领域 1.高速钢通用刀 具:钻头、丝锥 、立铣刀。 2.高速钢精密复 杂刀具:拉刀、 齿轮刀具。 3.整体硬质合金 刀具。 4.可转位螺纹刀 片、切断、切槽 刀片。 1.硬质合金可转 为刀片:车刀片 、铣刀片等。 2.金刚石涂层。
PVD与CVD表面处理技术
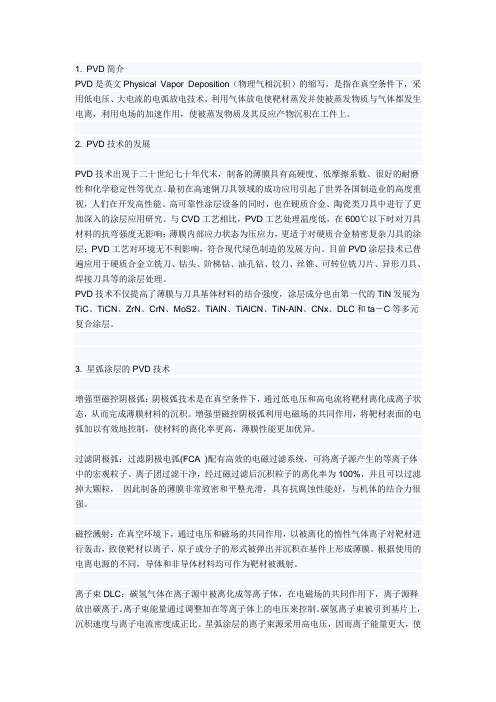
1. PVD简介PVD是英文Physical Vapor Deposition(物理气相沉积)的缩写,是指在真空条件下,采用低电压、大电流的电弧放电技术,利用气体放电使靶材蒸发并使被蒸发物质与气体都发生电离,利用电场的加速作用,使被蒸发物质及其反应产物沉积在工件上。
2. PVD技术的发展PVD技术出现于二十世纪七十年代末,制备的薄膜具有高硬度、低摩擦系数、很好的耐磨性和化学稳定性等优点。
最初在高速钢刀具领域的成功应用引起了世界各国制造业的高度重视,人们在开发高性能、高可靠性涂层设备的同时,也在硬质合金、陶瓷类刀具中进行了更加深入的涂层应用研究。
与CVD工艺相比,PVD工艺处理温度低,在600℃以下时对刀具材料的抗弯强度无影响;薄膜内部应力状态为压应力,更适于对硬质合金精密复杂刀具的涂层;PVD工艺对环境无不利影响,符合现代绿色制造的发展方向。
目前PVD涂层技术已普遍应用于硬质合金立铣刀、钻头、阶梯钻、油孔钻、铰刀、丝锥、可转位铣刀片、异形刀具、焊接刀具等的涂层处理。
PVD技术不仅提高了薄膜与刀具基体材料的结合强度,涂层成分也由第一代的TiN发展为TiC、TiCN、ZrN、CrN、MoS2、TiAlN、TiAlCN、TiN-AlN、CNx、DLC和ta-C等多元复合涂层。
3. 星弧涂层的PVD技术增强型磁控阴极弧:阴极弧技术是在真空条件下,通过低电压和高电流将靶材离化成离子状态,从而完成薄膜材料的沉积。
增强型磁控阴极弧利用电磁场的共同作用,将靶材表面的电弧加以有效地控制,使材料的离化率更高,薄膜性能更加优异。
过滤阴极弧:过滤阴极电弧(FCA )配有高效的电磁过滤系统,可将离子源产生的等离子体中的宏观粒子、离子团过滤干净,经过磁过滤后沉积粒子的离化率为100%,并且可以过滤掉大颗粒,因此制备的薄膜非常致密和平整光滑,具有抗腐蚀性能好,与机体的结合力很强。
磁控溅射:在真空环境下,通过电压和磁场的共同作用,以被离化的惰性气体离子对靶材进行轰击,致使靶材以离子、原子或分子的形式被弹出并沉积在基件上形成薄膜。
pvd和cvd是有区别的

CVD与PVD的区别及比较2009年03月06日 17:17 www.elecfans.co 作者:本站用户评论(0)关键字:CVD与PVD的区别及比较(一)选材:化学蒸镀-装饰品、超硬合金、陶瓷物理蒸镀-高温回火之工、模具钢(二)蒸镀温度、时间及膜厚比较:化学蒸镀-1000℃附近,2~8小时,1~30μm(通常5~10μm)物理蒸镀-400~600℃,1~3小时,1~10μm (三) 物性比较:化学蒸镀皮膜之结合性良好,较复杂之形状及小孔隙都能蒸镀;唯若用于工、模具钢,因其蒸镀温度高于钢料之回火温度,故蒸镀后需重施予淬火-回火,不适用于具精密尺寸要求之工、模具。
不需强度要求之装饰品、超硬合金、陶瓷等则无上述顾虑,故能适用。
物理蒸镀皮膜之结合性较差,且背对金属蒸发源之处理组件会产生蒸镀不良现象;但其蒸镀温度可低于工、模具钢的高温回火温度,且其蒸镀后之变形甚微,故适用于经高温回火之精密工具、模具。
(4) 半导体制程概要-离子布植郑硕贤4.1前言在半导体组件工业中,常在半导体晶体中加入杂质以控制带电载子数目,来增加导电性。
这种加入杂质的方法称为掺入杂质(Doping) 。
一般来说,掺入杂质的方法有两种:1. 化学蒸镀法2. 扩散法3. 离子布植法其中1、3两项在微电子组件工业中已普遍使用,这两种方法虽简易实用,但却牺牲了完整晶型的要求。
如化学蒸镀法在较低温度下进行,则蒸镀层常为非晶质或是多晶质。
离子布植则造成许多表面有许多点缺陷,甚至使表面层变成非晶质;因此一般均须经一道恢复完整晶格的退火处理,使表面层能回复晶型的样子。
4.2原理离子布植是将高能量带电粒子射入硅基晶中。
离子进入硅靶材后,会和硅原子发生碰撞而逐渐损失能量;直到能量耗损殆尽,即停止在该深度。
在与硅原子碰撞过程中,离子会传递部份能量给硅原子,若此能量大于硅和硅间的键结能量,则可使其产生位移而产生新的入射粒子;这新获得动能的粒子,也会与其它硅原子产生碰撞。
薄膜技术中PVD和CVD的区别详解

Page 24
Page 14
溅射法
直流溅射沉积装置
真空系统中,靶材
是需要溅射的材料, 它作为阴极。相对于 作为阳极的衬底加有 数千伏的电压。在对 系统预抽真空以后, 充入适当压力的惰性 气体。
Page 15
溅射法
溅射法分类
(1)直流溅射; (2)高频溅射; (3)磁控溅射; (4)反应溅射; (5)离子镀。
Page 16
Page 10
真空蒸镀
蒸发源分类
(一)电阻加热蒸发 (二)电子束加热蒸发 (三)电弧加热蒸发 (四)激光加热蒸发
Page 11
真空蒸镀
真空蒸发的影响因素
1.物质的蒸发速度 2.元素的蒸汽压 3.薄膜沉积的均匀性 4.薄膜沉积的纯度
Page 12
真空蒸镀
薄膜沉积的纯度
蒸发源的纯度; 加热装置、坩埚可能造成的污染; 真空系统中的残留气体。
物理气相沉积(PVD)
物理气相沉积法过程的三个阶段: 1,从原材料中发射出粒子; 2,粒子运输到基片; 3,粒子在基片上凝结、成核、长大、成膜。
Page 6
物理气相沉积(PVD)
PVD
物理气相沉积技术中最为基本的两种方法就 是蒸发法和溅射法,另外还有离子束和离子助等 等方法。
蒸发法相对溅射法具有一些明显的优点,包 括较高的沉积速度,相对较高的真空度,以及由 此导致的较高的薄膜质址等。
薄膜制备
张洋洋
薄膜制备工艺包括:薄膜制备方法的 选择,基体材料的选择及表面处理, 薄膜制备条件的选择和薄膜结构、性 能与工艺参数的关系等。
Page 2
薄
膜
物理气相沉积(PVD)
制
化学气相沉积 ( CVD)
PVD和CVD涂层方法
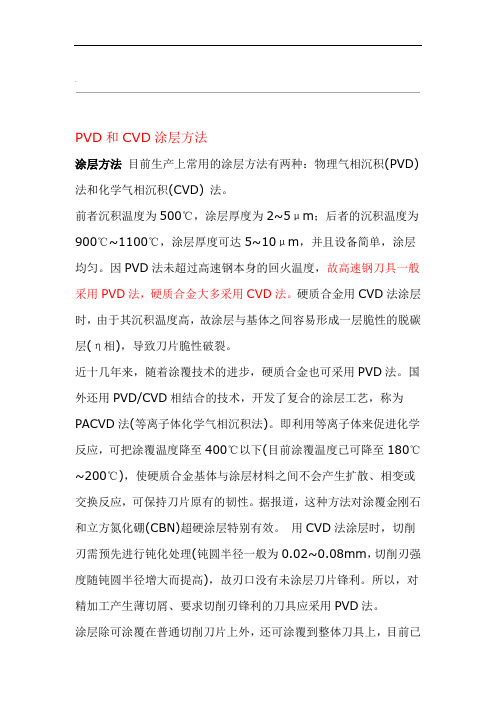
.PVD和CVD涂层方法涂层方法目前生产上常用的涂层方法有两种:物理气相沉积(PVD) 法和化学气相沉积(CVD) 法。
前者沉积温度为500℃,涂层厚度为2~5μm;后者的沉积温度为900℃~1100℃,涂层厚度可达5~10μm,并且设备简单,涂层均匀。
因PVD法未超过高速钢本身的回火温度,故高速钢刀具一般采用PVD法,硬质合金大多采用CVD法。
硬质合金用CVD法涂层时,由于其沉积温度高,故涂层与基体之间容易形成一层脆性的脱碳层(η相),导致刀片脆性破裂。
近十几年来,随着涂覆技术的进步,硬质合金也可采用PVD法。
国外还用PVD/CVD相结合的技术,开发了复合的涂层工艺,称为PACVD法(等离子体化学气相沉积法)。
即利用等离子体来促进化学反应,可把涂覆温度降至400℃以下(目前涂覆温度已可降至180℃~200℃),使硬质合金基体与涂层材料之间不会产生扩散、相变或交换反应,可保持刀片原有的韧性。
据报道,这种方法对涂覆金刚石和立方氮化硼(CBN)超硬涂层特别有效。
用CVD法涂层时,切削刃需预先进行钝化处理(钝圆半径一般为0.02~0.08mm,切削刃强度随钝圆半径增大而提高),故刃口没有未涂层刀片锋利。
所以,对精加工产生薄切屑、要求切削刃锋利的刀具应采用PVD法。
涂层除可涂覆在普通切削刀片上外,还可涂覆到整体刀具上,目前已发展到涂覆在焊的硬质合金刀具上。
据报道,国外某公司在焊接;..式的硬质合金钻头上采用了PCVD法,结果使加工钢料时的钻头寿命比高速钢钻头长10倍,效率提高5倍。
涂层成份又有哪些呢?各自的区别在哪里,应用面怎样。
通常使用的涂层有:TiC、TiN、Ti(C.N)、Gr7O3、Al2O3等。
以上几种CVD的硬质涂层基本具备低的滑动摩擦系数,高的抗磨能力,高的抗接触疲劳能力,高的表面强度,保证表面具有足够的尺寸稳定性与基体之间有高的粘附强度。
PVD与CVD涂层工艺比较;..PVD与CVD涂层工艺比较涂层涂层表面主要涂层对环境主要应用领域结合强沉积温度涂层厚度状态材料影响度1.高速钢通用刀具:TiN钻头、丝锥、物立铣刀。
CVD和PVD工艺比较

VII. 最后一个比较因素是操作运行安全问题 操作运行安全问题。PVD 操作运行安全问题 是一种完全没有污染的工序,有人称它为“绿色工 程”。而CVD的反应气体、反应尾气都可能具有一 定的腐蚀性,可燃性及毒性,反应尾气中还可能有 粉末状以及碎片状的物质,因此对设备、环境、操 作人员都必须采取一定的措施加以防范。
V. 在CVD工艺过程中,要严格控制工艺条件 控制工艺条件,否 控制工艺条件 则,系统中的反应气体或反应产物的腐蚀作用会使 基体脆化。 VI. 比较CVD和PVD这两种工艺的成本 成本比较困难, 成本 有人认为最初的设备投资PVD是CVD的3一4倍,而 PVD工艺的生产周期是CVD的1/10。在CVD的一个 操作循环中,可以对各式各样的工件进行处理,而 PVD就受到很大限制。综合比较可以看出,在两种 工艺都可用的范围内,采用PVD要比CVD代价高。
厚度上的区别正好可以弥补 PVD阶梯覆盖性能的不足 阶梯覆盖性能的不足
III. CVD镀层往往比各种PVD镀层略厚一些,前者厚 厚 度在7.5µm左右,后者通常不到2.5µm厚。CVD镀层的 表面略比基体的表面粗糙些。相反,PVD镀膜如实地 反映材料的表面,不用研磨就具有很好的金属光泽, 这在装饰镀膜方面十分重要。
I. 工艺温度高低 CVD 和 PVD 之间的主要区别。 工艺温度高低是 温度对于高速钢镀膜具有重大意义。 CVD 法的工艺 温度超过了高速钢的回火温度,用 CVD 法镀制的高 速钢工件,必须进行镀膜后的真空热处理,以恢复硬 度。镀后热处理会产生不容许的变形。 II. CVD 工艺对进人反应器工件的清洁 要求 PVD 清洁要求 清洁 要求比 工艺低一些,因为工件表面的一些脏东西很容易在高 温下烧掉。此外,高温下得到的镀层结合强度要更好 些。
薄膜技术中PVD和CVD的区别详解
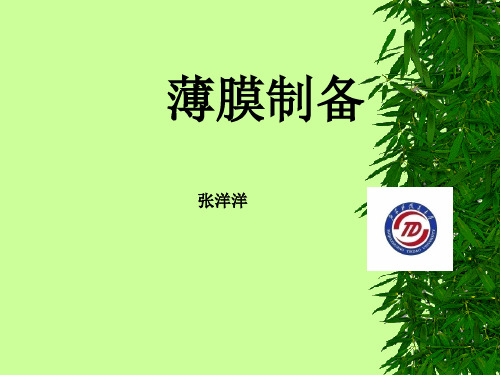
薄膜的化学气相沉积(CVD)
最基本的CVD装置 高温和低温CVD装置 低压CVD (LPCVD)装置 等离子体增强CVD(PECVD)装置 激光辅助CVD装置 金属有机化合物CVD (MOCVD)装置
场中加速后具有一定动能的特点,将 离子引向欲被溅射的靶电极。在离子 能量合适的情况下,入射的离子将在 与靶表面的原子的碰撞过程中使后者 溅射出来。这些被溅射出来的原子将 带有一定的动能,并且会沿着一定的 方向射向衬底,从而实现在衬底上薄 膜的沉积。
溅直射流溅法射沉积装置
真空系统中,靶材 是需要溅射的材料, 它作为阴极。相对于 作为阳极的衬底加有 数千伏的电压。在对 系统预抽真空以后, 充入适当压力的惰性 气体。
物理气相沉积法过程的三个阶段:
1,从原材料中发射出粒子; 2,粒子运输到基片; 3,粒子在基片上凝结、成核、长大、成膜。
物理气相沉积P(VDPVD)
物理气相沉积技术中最为基本的两种方法就 是蒸发法和溅射法,另外还有离子束和离子助等 等方法。
蒸发法相对溅射法具有一些明显的优点,包 括较高的沉积速度,相对较高的真空度,以及由 此导致的较高的薄膜质址等。
特别值得一提的是,在高质量的半导体晶 体外延技术以及各种绝缘材料薄膜的制备 中大量使用了化学气相沉积技术。比如, 在MOS场效应管中,应用化学气相方法沉 积的薄膜就包括多晶Si、 SiO2、SiN等。
薄膜的化学气相沉积(CVD)
CVD所涉及的化学反应类型
1.热解反应 2.还原反应 3.氧化反应 4.化合反应 5.歧化反应 6.可逆反应
蒸发源分类
(一)电阻加热蒸发 (二)电子束加热蒸发 (三)电弧加热蒸发 (四)激光加热蒸发