高钛烧结矿烧结试验研究
钛合金粉末注射成型烧结工艺对性能的影响

图 5 烧结后的 TC4 圆形件
(3)为掌握不同温度及持温时间与 TC4 烧结致密化的关系 我们选择 1240℃、1250℃及 1270℃进行如下图试验,烧结气氛 均为氩气环境。
图 6 烧结气氛均为氩气环境
图 3 圆形件烧结过程
由图 3 可以大致看出 TC4 持续 120min 情况下,在 1250℃可 以获得较高的致密化,随着温度升高密度略有下降,这是因为过 高的温度出现晶粒长大同时晶界之间空隙也变大,这样也导致 高温后标准拉伸件屈服强度会比 1250℃还低。
烧结,研究结果表明 , 在 1250℃(炉设定温度)持温 2 小时,工件获得较高的致密化和力学性能,在同样的烧结温度下持温时间
太短则工件无法获得高的致密化,持稳时间太久晶粒会有粗大现象随之力学性能略有下降。
关键词 :钛合金 ;分压烧结 ;晶界扩散
中图分类号 :TF124.39
文献标识码 :A
文章编号 :11-5004(2021)8-0122-2
收稿日期 :2021-04 作者简介 :张新房,男,生于 1980 年,重庆人,本科,研究方向 :粉末冶金。
122
Copyright©博看网 . All Rights Reserved.
S 科学技术 cience and technology
图 2 TC4 拉伸件烧结过程
2 数据处理及分析 依据烧结后的样品密度数据不难看出经过 1250℃持温 120-
180min 要比其他工艺获得之密度要高,根据图 3 及图 4 的关系 我们也得出致密化和屈服强度的一致性,故而在 1250℃持温 120min~180min 获得的致密化及力学性能是最高的 ;这是因为 过高的温度和过短的持温时间在钛合金烧结过程都没有让钛合 金晶体获得最佳致密化,同样低温和过长保温会因为晶界扩散 速度较慢而粉末表面驱动能在不断消耗,在晶界运动扩散过程 无法达到晶格较好的重叠和滑移,这样内部还有一定的空隙无 法消除从而无法达到较好的致密化。
威钢钒钛烧结试验研究

气 温 度 开 始下 降时 作 为 烧结 终 点 。将 烧结 饼 于 2 m 高 处 自由 落下 至 铁 板( 下 三次 1取 大 于 5 m 的百 落 , m
分 比作 为烧 结 成 品率 。 采用 12S /IO转鼓 测量 转鼓 指
烧结 杯实 验 主要研 究磁 铁矿 配 比 以及 焦粉 用量 对烧 结矿 产质 量 的影 响 。因此通 过钒 钛精 矿替 换 湖
从表 1可知 ,进 口矿 中 印度粉 的铁 品位 最高 为
6 .7 ,i 2 6 7 , 21 % SO 为 . % 而越 南 粉矿 T e为 5 . %, 5 F 50 2
SO 达 到 1 . %。国 内矿 湖北 高精 和平 川精 矿 品位 i 25 9
均 在 5 %左 右 , 钛磁 铁 精 矿较 低 . F 7 钒 T e为 5 .8 3 %, 9
实 验 所 用 的 原 燃 料 及 其 化 学 成 分 均 由威 钢 提
供, 见表 1 。
表 1 原燃料化学成分( 量百分 比) 质 %
以提 高 烧 结 矿产 量 为 目标 ,需 要 摸 索 合 适 的 钒 钛
精 矿 配 比和 合 适 的工 艺参 数 , 展 试 验 研 究 工 作 . 开
结 矿 产 质 量 的影 响 。结 果 表 明 , 钛 矿 配 比 最合 适 的 比例 为 1% , 粉用 量 为 5 钒 5 焦 %。 关 键 词 : 钛烧 结 ; 粉 用 量 ; 结 矿产 钒 焦 烧
中 图分 类 号 : F 4 T 06 文 献 标 识 码 : A 文章 编号 :6 3 1 8 ( 0 ) 5 0 2 — 3 17 — 9 0 2 1 0 — 17 0 1
间 , 烧结 矿孔 隙率 提 高 , 种 矿物 之 间的粘 结 能力 使 各
钛粉烧结工艺
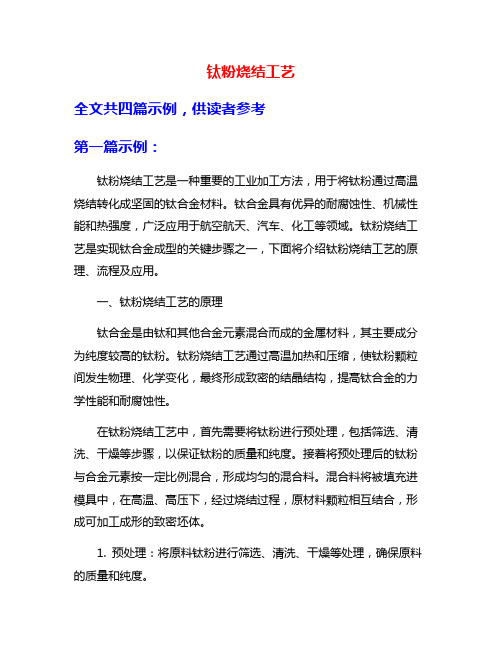
钛粉烧结工艺全文共四篇示例,供读者参考第一篇示例:钛粉烧结工艺是一种重要的工业加工方法,用于将钛粉通过高温烧结转化成坚固的钛合金材料。
钛合金具有优异的耐腐蚀性、机械性能和热强度,广泛应用于航空航天、汽车、化工等领域。
钛粉烧结工艺是实现钛合金成型的关键步骤之一,下面将介绍钛粉烧结工艺的原理、流程及应用。
一、钛粉烧结工艺的原理钛合金是由钛和其他合金元素混合而成的金属材料,其主要成分为纯度较高的钛粉。
钛粉烧结工艺通过高温加热和压缩,使钛粉颗粒间发生物理、化学变化,最终形成致密的结晶结构,提高钛合金的力学性能和耐腐蚀性。
在钛粉烧结工艺中,首先需要将钛粉进行预处理,包括筛选、清洗、干燥等步骤,以保证钛粉的质量和纯度。
接着将预处理后的钛粉与合金元素按一定比例混合,形成均匀的混合料。
混合料将被填充进模具中,在高温、高压下,经过烧结过程,原材料颗粒相互结合,形成可加工成形的致密坯体。
1. 预处理:将原料钛粉进行筛选、清洗、干燥等处理,确保原料的质量和纯度。
2. 混合:将预处理后的钛粉与合金元素按一定比例混合,形成混合料。
3. 压制:将混合料填充进模具中,进行压制成型,使原料颗粒紧密结合。
4. 烧结:将成型坯体置于高温烧结炉中,进行烧结处理,使原料颗粒经过高温加热相互结合,形成致密的结晶结构。
5. 热处理:对烧结后的钛合金进行适当的热处理,以调整合金的微观组织和性能。
6. 加工:将烧结后的钛合金坯体进行机械加工或热加工,得到所需形状和尺寸的钛合金制品。
1. 航空航天领域:钛合金具有优异的机械性能和耐高温性能,在航空航天发动机、航空器结构件等领域得到广泛应用。
2. 汽车工业:钛合金材料具有轻质、高强度和抗腐蚀性能,在汽车制造领域用于制造发动机零部件、排气系统等。
钛粉烧结工艺是一种重要的金属加工方法,通过高温烧结将钛粉转化成坚固的钛合金材料,具有广泛的应用前景和市场需求。
随着科技的不断发展和钛合金材料在各领域的应用增加,钛粉烧结工艺也将不断完善和发展,为促进产业发展和技术进步做出更大的贡献。
催化助燃剂试验报告

烧结配加催化助燃剂实验室试验总结攀枝花新钢钒股份有限公司炼铁厂二○○一年四月1.前言攀枝花高钛型钒钛磁铁精矿具有粒度粗亲水性差,TiO2、Al2O3含量高,SiO2含量低,烧结液相量少,同时,烧结速度慢,烧结机利用系数低,是一种难烧矿石。
提高烧结矿强度和利用系数,需要增加烧结液相量和提高垂直烧结速度。
国内从八十年代就开始研究通过配加催化助燃剂,改善烧结过程,目前许多厂家已成功地研制出多种催化助燃剂并应用于生产。
在燃料中配加1~2%的催化助燃剂后,烧结矿产量提高4~8%,固体燃料消耗降低8~12%。
为了探索在钒钛磁铁矿烧结条件下配加催化助燃剂的试验效果,在实验室进行了一系列试验,分析了配加催化助燃剂后,对烧结过程参数和烧结矿性能的影响。
2.试验条件和试验方法2.1.试验条件1)试验所用原燃料取自生产现场。
2)烧结矿品位控制在48.0%,Ro控制在1.76(倍),返矿取自生产现场,按10~5mm,-5mm以3:7塔配使用,返矿外配50%,混合料水分控制在7.1%,焦粉烘干后加入混合料。
2.2试验方法烧结试验在(250(600mm烧结杯中进行,点火负压控制在600×9.8Pa,烧结负压控在1200×9.8Pa,点火时间2min。
烧结杯铺底料粒度10~20mm,铺底料厚20mm。
生石灰加水40%,消化时间3min,混合料经人工混均后加入消化好的石灰,补充加水,再人工混均,装入(600(1200mm的圆筒混合机内制粒4min,混合机转速为16.77rpm。
烧结矿烧好后到出进行自然冷却,然后经2米高落下两次,进行筛分,+10mm粒级含量计成品率,10~40mm粒级取7.5kg 进行1/2ISO转鼓,最后用6.3mm和0.5mm标准筛进行筛分,+6.3mm粒级含量计转鼓指数,-0.5mm粒极含量计抗磨指数。
原燃料化学成分见表1,试验设置见表2、3。
通过正交试验表明,1#催化剂的效果较好,燃料配比4.5%,料层500mm为优选参数,设置了对比试验,见表4。
w(MgO)对含钒、钛烧结矿强度和烧结过程的影响
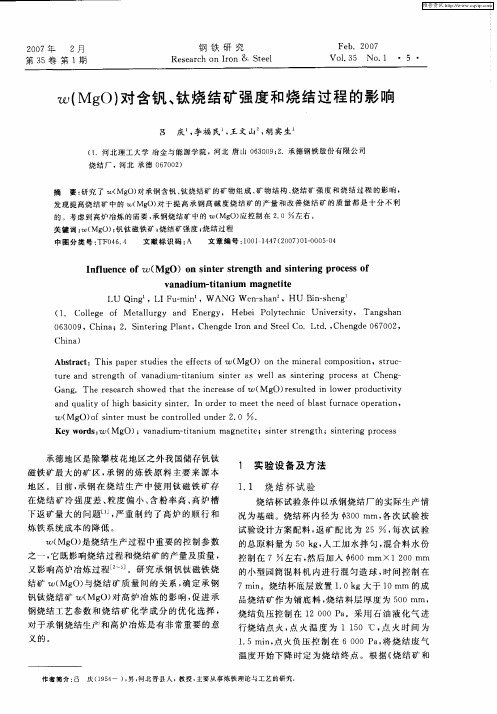
吕 庆 ’李福 民 王文 山 胡宾 生 , , ,
(.河 北 理 工 大 学 冶 金 与 能 源 学 院 ,河北 唐 山 0 3 0 ;.承德 钢 铁 股份 有 限公 司 1 6092
烧结厂 , 河北 承德 0 7 0 ) 6 0 2
摘 要 : 究 了 ( O) 承 钢 含 钒 、 烧 结 矿 的 矿 物 组 成 、 物 结 构 、 结 矿 强 度 和 烧 结 过 程 的 影 响 , 研 Mg 对 钛 矿 烧
维普资讯
20 0 7年 2月
钢 铁 研 究
Re e rh 0 r n & S e l s a c n Io t e
F b 0 7 e .2 0
第 3 5卷 第 1 期
Vo . 5 NO 1 ・ 5 ・ 13 .
( O) 含 钒 、 烧 结矿 强度 和烧 结 过 程 的影 响 Mg 对 钛
(hj ) na
Ab ta t sr c :Th sp p rsu ist eefcsO M g i a e t d e h fe t fw( O)o h n r l o o iin,s r t n t emi e a mp sto c tu —
t e a s r ngt o v n d u -ia i ur nd t e h f a a i m— t n um snt r a we l s i e i pr c s a Che g— t i e S l a snt rng o es t n‘
(完整word版)烧结、高炉、转底炉对比

烧结Sintering烧结是为高炉冶炼提供“精料”的一种加工方法,其实质是将准备好的各种原料(精矿、矿粉、燃料、熔剂、返矿及含铁生产废料等),按一定比例经过配料,混合与制粒,得到符合要求的烧结料,烧结料经点火借助碳的燃烧和铁矿物的氧化而产生高温,使烧结料中的部分组份软化和熔化,发生化学反应生成一定数量的液相,冷却时相互粘结成块。
其过程的产品叫烧结矿。
烧结是不能直接加入高炉的铁(精)矿粉造块的主要方法之一。
烧结厂将贫铁矿经过选矿得到的铁精矿,富铁矿在破碎、筛分过程中得到的粉矿和生产中回收的含铁粉料、熔剂以及燃料等,按要求比例配合,加水制成颗粒状的烧结混合料,平铺在烧结机上,经点火抽风烧结成块,形成烧结矿。
可充分利用粉状原料,扩大矿源;产品具有较均粒度、高气孔率和足够强度,良好的还原和造渣性能有利于强化高炉炼铁。
烧结也应用于有色金属冶炼过程。
有色金属硫化物精矿的烧结,除造块外,还有脱硫的作用。
烧结厂生产烧结矿,以前用过烧结盘、回转窑和悬浮烧结等方法,现在都用带式烧结机。
后者单机产量高,产品质量好。
高炉Blast furnace横断面为圆形的炼铁竖炉。
用钢板作炉壳,壳内砌耐火砖内衬。
高炉本体自上而下分为炉喉、炉身、炉腰、炉腹、炉缸5部分。
由于高炉炼铁技术经济指标良好,工艺简单,生产量大,劳动生产效率高,能耗低等优点,故这种方法生产的铁占世界铁总产量的绝大部分。
高炉生产时从炉顶装入铁矿石、焦炭、造渣用熔剂(石灰石),从位于炉子下部沿炉周的风口吹入经预热的空气。
在高温下焦炭(有的高炉也喷吹煤粉、重油、天然气等辅助燃料)中的碳同鼓入空气中的氧燃烧生成的一氧化碳,在炉内上升过程中除去铁矿石中的氧、硫、磷,还原得到铁。
炼出的铁水从铁口放出。
铁矿石中未还原的杂质(主要为脉石SiO2)和石灰石等熔剂结合生成炉渣(主要为CaSiO3等),从渣口排出。
产生的煤气从炉顶排出,经除尘后,作为热风炉、加热炉、焦炉、锅炉等的燃料。
高负压大风量高钛型钒钛磁铁精矿烧结生产实践

攀枝花钒钛 磁铁精 矿 由于粒度 粗成球 性差 , 且在烧 结 的干燥阶段 受 机械挤压 和强热气 流作用 , 矿从核粒 上脱落 , 透气性更加 恶化 , 精 使 鉴 于钒钛磁铁 精矿 的原 料特点 , 根据烧结 负压与风量对 烧结指标 的影 响规律 , 获得较 高的产质量 , 要 必然要求采 取高负压 大风量烧 结 , 而且 其 高负压水平 与烧结机 单位面积 的风量亦 有别于普通 矿烧结 , 其负压 水 平与单位 面积 的风量 远高于普 通矿烧结 , 其主风机 的设计水平 远高 于普 通矿烧结 , 同时采取一 整套的配套技术及改进 , 发挥 高负压大风量 烧结 的作用 与效 果。 2现状 与存在 的主 要问题 . 攀枝 花钒钛磁铁矿属于世 界上 难烧 矿石之一 , 其精矿粒度粗 ,2 0 <0 目粒 级仅 5 %左 右 , 5 呈较 规则 的圆球 状 , 比表 面积仅 4 11c , 9 . m/ 其在 7 g 核粒 上的粘附力弱 , 成球性极差 ; 在烧结的干燥 阶段受机 械挤压和强热 气 流作用 , 矿从核粒 上脱落 , 透气性更 加恶化 ; 精 使 严重 影响制粒 与烧 绪 性能。同时精矿 TO含量高达 l . 1 . A , i 2 — 3 %, 1 高达4 5 烧结产生 5 2 0 — %, 的液 相量少 , 影响烧结矿质 量 , 对烧结和炼铁都不利 。用 这种钒钛磁铁 精 矿烧结 由于透 气性 差 , 结风量 不足 , 烧 在没有 采取 有效 的强化措 施 下, 采用一般负压 l0 0 a O0 P 左右进行烧结 , 烧结机利用系数不 到 1  ̄  ̄。 . m2h O 转鼓 强度仅 6 %左右 , 5 成品率 5 %左右 。由于钒 钛精矿烧结透气性 差 , 0 烧结 阻力 大 , 采用低负压小风量 , 以满足钒钛精矿烧结 , 难 利用 系数 、 成 品率 、 转鼓强度 等低 。 3高负压烧结对产量影响 的理论分 析 . 31 . 负压与产量 的关 系模 型 根据烧结理论 与气 体力学推导出的公式 :
钛粉烧结温度

钛粉烧结温度一、介绍钛粉烧结温度是指将钛粉经过一定的压制和热处理工艺,使其颗粒互相结合,形成一定形状和尺寸的块状材料的温度。
烧结是钛粉冶金中的重要工艺之一,对于提高钛合金的力学性能、改善耐腐蚀性以及实现钛粉的成型具有重要作用。
本文将从烧结温度的选择、烧结机理以及烧结温度对钛粉烧结的影响等方面进行探讨。
二、烧结温度的选择2.1 温度范围钛粉烧结的温度范围一般在1200℃到1450℃之间,具体选择还需考虑钛粉的种类、烧结机器的类型以及所需产品的性能要求等因素。
2.2 烧结速率烧结温度的选择应使得烧结速率能够得到控制,过低的温度会导致烧结速率过慢,从而增加生产周期和成本;而过高的烧结温度则可能引起颗粒的过度生长,导致孔隙度增加,影响材料的力学性能。
2.3 材料相变钛合金在烧结过程中存在相变现象,合理选择烧结温度有助于控制相变规律,确保最终材料的结构和性能。
三、烧结机理3.1 颗粒初接触烧结开始时,钛粉颗粒之间的初接触是烧结过程的第一步。
通过加热,钛粉颗粒表面氧化物在颗粒之间形成,从而促进颗粒粘结。
3.2 表面扩散随着温度的升高,表面氧化物在颗粒表面扩散,进一步增加颗粒之间的粘结力,颗粒开始团聚。
3.3 颗粒扩散随着温度的继续升高,颗粒松散的氧化物层渐渐融化,颗粒之间发生扩散,出现颗粒与颗粒之间的物质交换。
3.4 界面弛豫在烧结过程的后期,材料表面能的减小使得颗粒之间形成块状物质,并逐渐达到表面能的最小化。
四、烧结温度对钛粉烧结的影响4.1 烧结致密度烧结温度的升高有利于增加颗粒之间的粘结力和扩散速率,从而提高烧结体的致密度。
但过高的烧结温度会导致颗粒过度烧结,增加孔隙度,降低材料的致密度。
4.2 颗粒尺寸烧结温度的选择对于颗粒尺寸的控制起重要作用。
合适的烧结温度可以促使颗粒逐渐聚集并增长,从而得到较大的颗粒尺寸。
4.3 晶粒长大过高的烧结温度会导致晶粒长大速率加快,晶界能量的降低,从而影响材料的晶界结构和力学性能。
- 1、下载文档前请自行甄别文档内容的完整性,平台不提供额外的编辑、内容补充、找答案等附加服务。
- 2、"仅部分预览"的文档,不可在线预览部分如存在完整性等问题,可反馈申请退款(可完整预览的文档不适用该条件!)。
- 3、如文档侵犯您的权益,请联系客服反馈,我们会尽快为您处理(人工客服工作时间:9:00-18:30)。
高钛烧结矿烧结试验研究
赵佐军李荣玲刘福泉黄晓东邱学先
((宣钢炼铁厂)
摘要:随着低钛精粉资源的紧缺,烧结生产中需要使用一部分高钛精粉,使得烧结矿的钛含量升高,而钛会对烧结各项指标产生影响。
本文介绍了在实验室进行烧结杯实验,研究烧结矿二氧化钛,对烧结指标的影响。
关键词高钛烧结矿烧结矿强度利用系数
1 前言
随着低钛精粉资源的紧缺,使用一部分当地高钛精粉。
烧结矿的钛含量升高,通过试验摸索二氧化钛对烧结指标的影响,为日后使用高钛精粉,进行高钛烧结矿生产提供技术准备。
2试验条件及方法2.1试验条件
试验所用精粉化学成分
表1 精粉化学成分
矿粉种类TFe SiO2 CaO MgO FeO TiO2Al2O3烧损高钛精粉62.52 5.050 1.526.05 6.53 4.250.75 低钛酸精65.37 5.450 1.1428.010.52 1.56 1.2
2.2试验方法
烧结杯内径:300 mm
料层高度:500mm
点火时间:90s
点火温度:1150±50℃
点火负压6000Pa
烧结负压9600Pa
总秤量70kg,混合料水分以满足制粒条件为主,一混为人工混合,二混为滚筒混合4min。
用大于10mm的成品烧结矿铺底料,铺底料2 kg,铺底料高度20mm,采取人工布料,计算机自动控制烧结过程。
烧结结束后,将烧结矿从2m高处自由落下三次,装入振动筛筛300s,大于6.3mm的烧结矿为成品矿,按标准取7.5 kg做强度指标检测。
3. 试验方案与试验结果
试验烧结矿碱度为2.2倍,MgO3.1%,FeO8~10%。
入烧进口粉配比20%,根据理论测算烧结矿TiO2含量为0.5%、1.0%、1.5%、1.6%、2.0%。
原料结构见表2
表2 原料结构
编号烧结杯编号
低钛
酸精
高钛精
粉
64
印
粉
60
印
粉
FMG钢渣
瓦斯
灰
铁鳞
除尘
灰
高返钙灰镁灰燃料
1 SG8221(Ti0.5)35.7001055 2.150.43 3.44 2.5819.358.55 3.59 4.30
2 SG8131(Ti1.0)25.639.351055 2.150.4
3 3.4
4 2.5819.359.2
5 3.52 4.30
3 SG8202(Ti1.5)17.9317.961055 2.150.43 3.4
4 2.5819.358.39 3.47 4.30
4 SG9042(Ti1.6) 16.3
5 19.68 1055 2.150.43 3.44 2.5819.358.39 3.33 4.30
5 SG8261(Ti2.0)9.4426.68 1055 2.150.43 3.44 2.5819.358.39 3.47 4.30
实验数据见表2~5。
表3 烧结试验结果
编号烧结杯编号
混合料
水分(%)
垂直烧结速度
(mm/min)
利用系数
(t/m2.h)
强度
(%)
抗磨
(%)
成品率
(%)
1 SG8221(Ti0.5)818.39 1.50568.67 4.6786.37
2 SG8131(Ti1.0)8.318.18 1.42269.3
3 4.6784.03
3 SG8202(Ti1.5)8.419.28 1.50462.67 6.6781.97
4 SG9042(Ti1.6) 8.1 16.16 1.3264683.15
5 SG8261(Ti2.0)8.616.9 1.31964 4.00 82.89
表4烧结矿化学分析
编号烧结杯编号TFe SiO2 CaO MgO FeO TiO2 Al2O3 R2
1 SG8221(Ti0.5) 52.93 6.0413.41 2.94 9.690.53 1.98 2.22
2 SG8131(Ti1.0)52.7
3 6.0413.57 2.46 9.79 1.0
4 1.46 2.25
3 SG8202(Ti1.5) 52.3
4 6.0813.32 3 10.17 1.38 2.4 2.19
4 SG9042(Ti1.6) 53.02 5.62 12.69 2.97 9.12 1.62 2.4 2.26
5 SG8261(Ti2.0)52.33 5.7612.29 2.859.03 1.87 1.5
6 2.13
由数据可知,烧结矿TiO2为0.5%、1%时,烧结矿强度、利用系数以及成品率等烧结指标较好;烧结矿TiO2为1.5%,较TiO20.5%相比,强度下降6个百分点,成品率降低4.39个百分点;当烧结矿TiO2为1.6%和2.0%时,降低混合料水分后,利用系数下降,强度和成品率较烧结矿TiO21.5%时有所提高。
在以上试验数据基础上,将烧结矿TiO2控制在 1.2%和 1.3%两个因素水平进行了试验。
原料结构见表5,试验结果见表6,化学分析见表7
表5 原料结构
编号烧结杯编号
低钛酸
精
高钛精
粉
64
印粉
60
印粉
FMG钢渣
瓦斯
灰
铁鳞
除尘
灰
高返钙灰镁灰燃料
6
SG-
Ti1.2-8.323.23 12.69 1055 2.150.43 3.44 2.5819.358.44 3.39 4.30
7 SG-Ti1.2
-8.023.23 12.69 1055 2.150.43 3.44 2.5819.358.44 3.39 4.30
8
SG-
Ti1.2-8.2 23.23 12.69 1055 2.150.43 3.44 2.5819.358.44 3.39 4.30
9 SG-Ti1.321.40 14.52 1055 2.150.43 3.44 2.5819.358.44 3.39 4.30
表6 烧结试验结果
编号烧结杯编号
混合料
水分(%)
垂直烧结速度
(mm/min)
利用系数
(t/m2.h)
强度
(%)
抗磨
(%)
成品率
(%)
6 SG-Ti1.2-8.38.3 18.68 1.47764682.17
7 SG-Ti1.2-
8.0
8 14.04 1.14571.33 6.6784.28
8
SG-
Ti1.2-8.2
8.2 16.84 1.402
67.334
86.01
9 SG-Ti1.38.2 17.98 1.47762.67682.95
表7烧结矿化学分析
编号烧结杯编号TFe SiO2 CaO MgO FeO TiO2 Al2O3 R2
6 SG-Ti1.2-8.352.76 5.6712.5 2.9
7 9.69 1.15 2.20 2.20
7 SG-Ti1.2-8.053.22 5.712.4 2.91 8.41 1.21 2.08 2.18
8 SG-Ti1.2-8.2 52.83 5.7512.89 2.85 9.31 1.17 2.34 2.24
9 SG-Ti1.353.12 5.8612.84 2.88 9.41 1.34 1.15 2.19
烧结矿TiO2在1.2%时,分别按混合料水分8.3%、8.0%、8.2%进行三杯试验,试验结果表明,烧结矿TiO2在1.2%时,利用系数、烧结矿强度和成品率仍能保持较好指标。
烧结矿TiO2在1.3%时,提高利用系数情况下,强度下降。
四、实验结论
1、烧结矿TiO2为0.5%、1%时,烧结矿强度、利用系数以及成品率等烧结指标较好。
2、烧结矿TiO2为1.5%,烧结矿强度和成品率呈下降趋势。
3、烧结矿TiO2为 1.2%时,利用系数在1.145 t/m2.h、1.402 t/m2.h、1.477 t/m2.h,烧结矿强度分别为71.33%、67.33%和64%,由此可知,控制好利用系数,烧结矿强度和成品率等烧结指标较优,提高利用系数,强度和成品率呈下降趋势。
烧结矿TiO2为 1.3%时,利用系数为1.477 t/m2.h,烧结矿强度为62.67%,烧结矿TiO2≥1.3%时,烧结矿各项指标呈下降趋势。