驰腾CT3202中文说明
M03.0022_Chinese_2022-07说明书

操作说明控制器B500/B510C540/C550P570/P580M03.0022 CHINESISCH原版使用说明书 ◼ Made ◼ in ◼ GermanyCopyright© Copyright byNabertherm GmbH Bahnhofstrasse 2028865 LilienthalFederal Republic of Germany Reg: M03.0022 CHINESISCH Rev: 2022-07内容可能会修改,保留技术更改权利1引言 (7)2质保和责任 (8)2.1一般说明 (8)2.2环境条件 (9)2.3废料处理 (9)2.4产品说明 (9)2.5规定用途 (10)2.6符号说明 (10)3安全说明 (13)4运行 (14)4.1接通控制器/窑炉 (14)4.2关闭控制器/窑炉 (14)5控制器的构造 (15)5.1控制器的各个模块的布局 (15)5.2操作页面区域 (16)5.2.1“菜单栏”区域 (16)5.2.2“小区段播放器”区域 (17)5.2.3“大区段播放器”区域 (18)5.2.4“状态栏”区域 (19)6控制器性能特性 (20)7简要使用说明 B500/B510/C540/C550/P570/P580 (22)7.1基本功能 (22)7.2输入新程序 (程序表) (24)8概览图 (29)8.1“窑炉”概览(无程序处于活动状态) (29)8.2“窑炉”概览(程序处于活动状态) (29)9待机模式 (31)10显示、输入或更改程序 (31)10.1“程序”概览 (32)10.2显示并启动程序 (33)10.3分配并管理程序类别 (34)10.4输入程序 (36)10.5利用NTEdit在电脑上准备程序 (44)10.6管理程序(删除/复制) (44)10.7什么是Holdback? (45)10.8修改正在运行的程序 (46)10.9完成区段跳跃 (47)11设定参数 (48)11.1“设置”概览 (48)11.2校准量程 (48)11.3调节参数 (52)11.4调节性能 (54)11.4.1磨平 (54)11.4.2加热延迟 (55)11.4.3手动区段控制 (56)11.4.4在程序启动时将实际值作为额定值接受 (57)11.4.5受控冷却(选项) (58)11.4.6起动连接/功率限制 (60)11.4.7自优化 (61)11.4.8程序运行中的炉料控制 (63)11.4.9用于各个区间的额定值补偿 (65)11.4.10Holdback (66)11.5用户管理 (67)11.6控制器锁闭和操作禁用 (71)11.7连续锁闭(操作禁用) (71)11.7.1运行中的程序控制器锁闭 (71)11.8配置额外功能 (72)11.9收起或重命名附加功能 (73)11.9.1在一个加热程序运行期间人工操作额外功能 (73)11.9.2在一个加热程序之后人工操作额外功能 (74)11.10警报功能 (75)11.10.1警报 (1 和 6) (75)11.10.2可听报警(可选) (78)11.10.3监测梯度 (78)11.10.4警报配置举例 (80)11.11设定电网中断时的反应 (81)11.12系统设置 (82)11.12.1设定日期和钟点时间 (82)11.12.2设置日期和钟点时间格式 (82)11.12.3设定语种 (83)11.12.4调节显示屏亮度 (84)11.12.5调整温度单位 (°C/°F) (84)11.12.6设定数据接口 (85)11.12.7设置Wi-Fi端口 (88)11.13导入和导出过程数据、程序和参数 (90)11.14登录模块 (92)11.15对空气循环器的控制 (93)12信息菜单 (93)13过程记录 (95)13.1使用NTLog将数据保存到U盘 (95)13.2保存过程数据并使用VCD软件管理程序(可选) (99)14连接到MyNabertherm App (100)14.1故障排除 (104)15与控制器的通信 (104)15.1通过 Modbus-TCP 和上一级系统进行沟通 (104)15.2网络服务器 (105)15.3通信模块的补装 (107)15.3.1供货范围 (107)15.3.2安装一个通信模块 (107)16可设置关闭温度的温度选择限制器(附加配置) (109)17无电势触点用于开启外部设备以及接收监控信号(可选) (109)18故障消息或警告 (110)18.1控制器的故障消息 (110)18.2控制器警告 (112)18.3开关设备的故障 (114)18.4控制器的检查列表 (115)19技术数据 (117)19.1铭牌 (119)20清洁 (119)21维护和备件 (119)21.1更换一个控制器 (120)21.2调节器模块的拆卸 (120)21.3调节器模块的安装 (121)22电气连接 (121)22.1调节器模块 (121)22.2对电缆的要求 (122)22.3一般性连接 (122)22.4至 3.6 kW 的窑炉–用于 B130, B150, B180, C280, P330 的备件,截止 2008 年 12 月止 (123)22.5至 3.6 kW 的窑炉–用于 B130, B150, B180, C280, P330 的备件,从 2009 年 1 月起 (124)22.6窑炉,单区式> 3.6 k,带半导体继电器或接触器 (125)22.7窑炉> 3.6 kW,带 2 个加热回路 (126)23纳博热售后服务 (127)24您的备忘录......................................................................................................... Fehler! Textmarke nicht definiert.1 引言尊敬的客户:非常感谢您对纳博热有限公司产品的信任和支持。
Your Drive 运动跑步腿部训练设备说明书

Y our Drive brand product is warranted to be free of defects in materials and workmanship for the lifetime of the original consumer purchaser.This device was built to exacting standards and carefully inspected prior to shipment. This Lifetime Limited Warranty is an expression of our confidence in the materials and workmanship of our products and our assurance to the consumer of years of dependable service. In the event of a defect covered by this warranty, we will, at our option, repair or replace the device.This warranty does not cover device failure due to owner misuse or negligence, or normal wear and tear. The warranty does not extend to non-durable components, such as rubber accessories, casters, and grips, which are subject to normal wear and need periodic replacement. If you have a question about your Drive device or this warranty, please contact an authorized Drive dealer.maintaining your transport chair Proper care and maintenance is important in order to keep your Transport Chair in good working con-dition. Be sure that your chair is in proper working condition at all times. A qualified dealer or repair center (wheelchair rental dealer) should be con-sulted for periodic inspections and repairs.1. At least once a week, wipe off chrome using a clean soft cloth. If the chair is exposed to moisture, dry the chair immediately. The metal parts of the chair should be polished once a month with an auto wax.2. Clean the upholstery with a mild soap solution, rinse and wipe dry. Worn or torn upholstery should be replaced promptly as it may not support your body weight.3. Inspect the wheels at least once a month. Correct any side play by loosening the lock nut on the axle, then tighten the axle just enough to remove sideplay.4. Solid rubber tires require limited upkeep, but need to be cleaned periodically with a damp cloth. Solid rubber tires need to be replaced if they become cracked or severely worn.It is important for the attendant to be familiar withproper assisting procedures in anysituation that requires the use of the TransportChair. Safety is the Key consideration. Consultyour physician, nurse of physical therapist todetermine methods most suitable for yourindividual needs and abilities.Note: The transport chair does not conform toFederal Standards for automobile seating andshould not be used as a seat in a motor vehicle.Y our Transport Chair Dealer (Wheelchair rentalDealer) can assist you in making adjustments andprovide you with operational information.1. T o Open the chair, tilt to one side and push downon seat rails.2. Lift back support to upright position. The lock tosecure the back will engage automatically. T o folddown and store, pull up on locks simultaneously,and carefully fold down the back support.3. T o attach footrests, align the holes on thefootrest arm with the pegs on the frame of theTransport chair. (See Diagram)4. T o Adjust the length of the footrests, loosenthe bolt (or knob) on the telescoping tube shaft.Tighten securely after adjustment. The lowest partof the footrest should not be less than 2 1/2 inchesfrom the ground to permit proper clearance.operating tipshow to operate your transport chair:safety tips1. Before entering or leaving the chair, engage thedual wheel locks against the tires on both rearwheels. Make sure the front casters are in theforward position before transferring into or out ofthe chair.2. Always fasten the safety belt when thetransport chair is in motion.3. Do not move forward on the seat while leaningforward out of the chair. If it isabsolutely necessary to do so, make sure the frontcasters are in the forward position. If you arepicking an object up from the floor, go past theobject, and then go backwards. Thecasters will then swing to the forward position.4. Leaning out of the transport chair withoutproper assistance could cause tipping.5. Do not step on the foot plates whentransferring, as this could cause tipping.Note: Y ou and your attendant should consult aqualified professional for correct techniques onramp negotiations.5. T o remove the Swing-away footrest, release thelock. Swing outward and rearward. Simply lift upand off to remove the footrest.6. The safety belt is already attached for use andshould not be removed from the Transport Chair.Note: The Transport Chair should not be operatedwithout the assistance of an attendant.please read carefully before using yourtransport chair.weight capacity 300 lbs。
EATON Series NRX NF 三路类型32电缆阻碍器安装和移除说明说明书

ContentsDescription P age General information . . . . . . . . . . . . . . . . . . . . . . . .2Installation of three-way cable interlock . . . . . . . .4Functional test of interlock assembly . . . . . . . . .10Installation and removal instructions for Series NRX NF fixed breaker three-way Type 32 cable interlock kitInstructions apply to:Series NRX T , Type NF frame, ANSI, UL T1066, UL 489 / IEC, IZMX162Instruction Leaflet IL0131081ENEffective August 2015Installation and removal instructionsSeries NRX NF fixed breakerthree-way T ype 32 cable interlock kitEATON m WARNING(1) ONLY QUALIFIED ELECTRICAL PERSONNEL SHOULD BE PERMITTED TO WORK ON THE EQUIPMENT.(2) ALWAYS DE-ENERGIZE PRIMARY AND SECONDARY CIRCUITS IF A CIRCUIT BREAKER CANNOT BE REMOVED TO A SAFE WORK LOCATION.(3) DRAWOUT CIRCUIT BREAKERS SHOULD BE LEVERED (RACKED) OUT TO THE DISCONNECT POSITION.(4) ALL CIRCUIT BREAKERS SHOULD BE SWITCHED TO THE OFF POSITION AND MECHANISM SPRINGS DISCHARGED.FAILURE TO FOLLOW THESE WARNINGS FOR ALL PROCEDURESDESCRIBED IN THIS INSTRUCTION LEAFLET COULD RESULT IN DEATH, BODILY INJURY, OR PROPERTY DAMAGE.m WARNINGTHE INSTRUCTIONS CONTAINED IN THIS IL AND ON PRODUCT LABELS HAVE TO BE FOLLOWED. OBSERVE THE FIVE SAFETY RULES: – DISCONNECTING– ENSURE THAT DEVICES CANNOT BE ACCIDENTALLY RESTARTED – VERIFY ISOLATION FROM THE SUPPLY – EARTHING AND SHORT-CIRCUITING– COVERING OR PROVIDING BARRIERS TO ADJACENT LIVE PARTSDISCONNECT THE EQUIPMENT FROM THE SUPPLY. USE ONLY AUTHORIZED SPARE PARTS IN THE REPAIR OF THE EQUIPMENT. THE SPECIFIEDMAINTENANCE INTERVALS AS WELL AS THE INSTRUCTIONS FOR REPAIR AND EXCHANGE MUST BE STRICTLY ADHERED TO PREVENT INJURY TO PERSONNEL AND DAMAGE TO THE SWITCHBOARD.m WARNINGMECHANICAL INTERLOCKS FOR SYSTEMS WITH ONE OR TWO SUPPLIES SWITCHED ON AT ALL TIMES. IN THE EVENT THAT BOTH SUPPLYSWITCHING DEVICES ARE IN THE OPEN POSITION, THERE IS A POSSIBILITY THAT A CLOSE SIGNAL TO ALL THREE SWITCHING DEVICES COULD CAUSE MOMENTARY PARALLELING. IF THIS IS UNDESIRABLE, THE USER MAY WANT TO INCLUDE A SEPARATE MECHANICAL AND/OR ELECTRICAL INTERLOCK TO PREVENT SIMULTANEOUS CLOSING COMMANDS BEING SENT TO BOTH OF THE NORMAL SUPPLY SWITCHING DEVICES (A AND C) AND THE TIE SWITCHING DEVICE (B) UNDER ALL CONDITIONS.General informationThis information leaflet provides detailed installation instructions for installing and interconnecting one fixed Type NF frame breaker to another type of low voltage circuit breaker (LVCB) in any position (see A, B, C in T able 1) for a Type 32 interlock configuration as shown in Figure 1 . When purchasing kits for a Type 32 interlock configuration setup, additional interlock kits (the types of interlock kits and the other breakers on which they can be installed that are compatible with this kit are listed in T able 2) are required for the other breaker as well as the interconnecting cable kits (three are required) .For Type 32 interlock configurations, the mechanical interlock holds one of the breakers tripped or open (prevents closure) when the other two are closed . A lever assembly is mounted on each breaker and interfaces with the poles haft and trip bar . The lever assemblies are interconnected with cables provided in interconnecting cable kits (listed in T able 3) that are compatible with this interlock kit . The cable kits, purchased separately, each contain two cables and can be used for any orientation of the breakers according to the installation recommendations in Step 9 .Refer to Figure 2 and Figure 3 for identification of interlock kit and interconnecting cable kit contents, respectively .Breaker ABreaker BBreaker CType 32 cable routingFigure 1. Cable routing for T ype 32 interlock configurations T able 1. T ype 32 interlock logicBreaker0 = open 1 = closed3Instruction Leaflet IL0131081ENEffective August 2015Installation and removal instructions Series NRX NF fixed breakerthree-way T ype 32 cable interlock kitEATON T able 2. Interlock assembly kits for interconnected breakersInterconnected breakerInterlock assembly kit for fixed breakerInterlock assembly kit for drawout breakerNRX Type RF frame IZMX-MIL32C-F16-2IZMX-MIL32C-W16-2NRX Type NF frame IZMX-MIL32C-F40-2IZMX-MIL32C-W40-2Magnum IZM97 or IZM99IZM-MCI32-F IZM-MCI32-W Magnum DS T or SB MCI3W32FX MCI3W32DOT able 3. Interconnecting cable kits (two cables per kit) aCable kit lengthCatalogue number1,5 m (5 ft)IZMX-MIL-CAB1520-21,8 m (6 ft)IZMX-MIL-CAB1830-22,4 m (8 ft)IZMX-MIL-CAB2440-23,0 m (10 ft)IZMX-MIL-CAB3050-2a Cable kits are purchased separately as needed.(A)(B)(C)(D)(E)(F)(H)(G)(I)M3 x 8 mm flathead screw2xLock washer 3xM6 x 12 mm hex bolt 3xInterlock assembly1xTrip pin 1xGrease tube1xCable bracket4xM6 x 10 mm thread-formingscrews 4x30,5 mm (1,2 inch) cable tube spacer1xDrive arm1x(J)Interlock mounting plate1x(K)M5 nut 1x(L)M5 x 12 mmscrew 3x(M)Figure 2. Interlock kit part identification, includes parts to install on a single fixed T ype NF frame breaker and cassette (does not include cables)Figure 3. Interconnecting cable kit part identification (includes cables)4Instruction Leaflet IL0131081ENEffective August 2015Installation and removal instructionsSeries NRX NF fixed breakerthree-way T ype 32 cable interlock kitEATON Installation of two-way cable interlockRequired tools• 10 mm hex socket• 11/16-inch open-end wrench • 3/8-inch open-end wrench • 3/8-inch hex socket • 2 mm Allen wrench • Drive extension • Adjustable wrench • T15 Torx driver • Ratchet•Measuring Instrument, in mmBefore proceeding with the following steps, ensure that all breakers are in the OPEN and DISCHARGED position .Step 1Remove the four screws holding the front cover in place (two on each side of the cover) as shown in Figure 4.Figure 4. Details for Step 1Step 2Remove the front cover as shown in Figure 5 . Pull down on thecharging handle to simplify removal .Figure 5. Details for Step 2Step 3Install the mounting feet . Refer to IL01301030E for detailed instructions .Step 4Install the drive arm (D) to the end of the pole shaft using one M3 x 8 mm flathead screw (C) as shown in Figure 6 and Figure 7 . Apply Loctite T Blue 242 to ensure that the screw cannot loosen during operation . The drive arm should be oriented as shown in Figure 6 and Figure 7 . Torque to 0,3–0,6 N·m (3–5 in-lb) .Step 5Install the trip pin (F) to the trip bar using an M3 x 8 mm flathead screw (C) while holding the trip bar with an adjustable wrench as shown in Figure 6 and Figure 7 . Apply Loctite Blue 242 to ensure that the screw cannot loosen during operation . Torque to 0,3–0,6 N·m (3–5 in-lb) .5Instruction Leaflet IL0131081ENEffective August 2015Installation and removal instructions Series NRX NF fixed breakerthree-way T ype 32 cable interlock kitEATON (F)(D)(C)(C)Figure 6. Details for Steps 4 and 5Figure 7. Details for Steps 4 and 5Step 6Fasten interlock assembly (E) to interlock mounting plate (K) using three M6 x 12 mm hex bolts (A) and lock washers (B) as shown in Figure 8 . Torque to 4,5–5,6 N·m (40–50 in-lb) . Then fasten interlock mounting plate (K) with attached interlock assembly to the right side of the breaker using three M5 x 12 mm screws (M) and one M5 square nut (L) as shown in Figure 8 . Torque to 7,3–9,6 N·m(65–85 in-lb) . Ensure that once attached to the breaker, the interlock assembly trip paddle is above the trip pin on the trip bar as shown in Figure 9 .(K)(M)(B)(A)Figure 8. Details for Step 6Interlock assembly trip paddle(A) Trip pin With all circuit breakers OPEN, the paddle is positioned above the trip pin as shown .Figure 9. Details for Step 6(E)6Instruction Leaflet IL0131081ENEffective August 2015Installation and removal instructionsSeries NRX NF fixed breakerthree-way T ype 32 cable interlock kitEATON Step 7Fasten four cable brackets (H) to interlock mounting plate (K) just below interlock assembly mounted in Step 6 using four M6 x 10 mm thread-forming screws (I) as shown in Figure 10 . Torque to 7,3–9,6 N·m (65–85 in-lb) .(I)(H)Figure 10. Details for Step 7Step 8Replace the front cover and secure it in place with the four mounting screws previously removed in Step 1 .Step 9This step contains cable routing and installation procedures .Make sure that cables move freely in their cable housings before installation . When attaching cables to swivel fittings, ensure that both ends of the cable are connected to pull swivel fittings (refer to Figure 12) . For example, a cable connected to the Drive Lever Pull Swivel Fitting on Breaker A must connect to the Driven Lever Pull Swivel Fitting on Breaker B .ATTENTIONFIGURE 11 SHOWS THE TYPICAL CABLE ROUTING FOR A TYPE 32INTERLOCK CONFIGURATION. NOTICE THAT DEPENDING ON THE POSITION OF THE BREAKER WITHIN THE INTERLOCK CONFIGURATION, THE CABLES WILL BE ATTACHED IN DIFFERENT LOCATIONS. THE CABLE MOUNTING ON BOTH POINTS OF THE DRIVE AND DRIVEN LEVERS ARE DESCRIBED BELOW. TABLE 4 SHOWS THE TYPE 32 INTERLOCK LOGIC DEPENDING ON POSITION.Breaker ABreaker BBreaker CType 32 cable routingFigure 11. Cable routing for T ype 32 interlock configurations7Instruction Leaflet IL0131081ENEffective August 2015Installation and removal instructions Series NRX NF fixed breakerthree-way T ype 32 cable interlock kitEATON T able 4. T ype 32 interlock logicBreaker0 = open 1 = closedInstallation recommendations• 4 inch (102 mm) minimum allowable cable housing bend radius •Use plastic wire ties / clamps to attach cable housing to structure after installation and adjustment • Do not compress cable housing •Recheck to ensure cables move freelyDriven ”And” leverDriven lever pull swivel fittingDrive lever push swivel fittingDriven lever push swivel fittingDrive lever pull swivel fitting Drive leverGapFigure 12. Push and pull swivel fitting identificationStep 10This step describes how to first attach the drive (short rod) end of a cable to its interlock assembly and cable bracket . See Figure 13 .To attach the drive (short rod) end of a cable to the drive lever pull swivel fitting (refer to Figure 12), follow the directions below .1. Remove upper nut, compression spring, and 38,1 mm (1,5 inch)tube spacer from end of rod of cable assembly .2. Slide rubber boot toward tip of rod .3. Unthread outer bulkhead nut and slide nut and lock washertoward tip .4. Insert threaded end of rod into swivel fitting .5. Slide smaller diameter portion of bulkhead fitting into cablebracket slot, keeping one of the two lock washers with each bulkhead nut .6. Raise the cable assembly until threaded portion of bulkheadfitting enters slotted hole in cable bracket (threads show above bracket) .7. Bring bulkhead washer and nut down to threads andhand tighten .8. Adjust two bulkhead nuts to approximately center the threadedsection of the bulkhead fitting on the cable mounting bracket . 9. Hand tighten the bulkhead nuts at this time .10. Slide rubber boot back into place over end of bulkhead fitting .11. Replace 38,1 mm (1,5 inch) tube spacer, compression spring,and upper nut on end of rod .12. Lower nuts should be against the stop at the end of threadand upper nut tightened against tube spacer .13. Hold lower nuts and torque upper nut to 3,3–4,5 N·m(30–40 in-lb) . To attach the drive (short rod) end of a cable to the drive lever push swivel fitting (refer to Figure 12), follow the directions below (see Figure 13) .1. Remove upper nut from end of rod of cable assembly .2. Slide rubber boot toward tip of rod .3. Unthread outer bulkhead nut and slide nut and lock washertoward tip .4. Insert threaded end of rod with 38,1 mm (1,5 inch) tube spacerinto swivel fitting ensuring that the compression spring remains between the lower nuts and the swivel .5. Slide smaller diameter portion of bulkhead fitting into cablebracket slot keeping one of the two lock washers with each bulkhead nut .6. Raise the cable assembly until threaded portion of bulkheadfitting enters slotted hole in cable bracket (threads show above bracket) .7. Bring bulkhead washer and nut down to threads andhand tighten .8. Adjust two bulkhead nuts to approximately center the threadedsection of the bulkhead fitting on the cable mounting bracket . 9. Hand tighten the bulkhead nuts at this time .10. Slide rubber boot back into place over end of bulkhead fitting .11. Lower nuts should be against the stop at the end of threadand upper nut tightened against tube spacer .12. Hold lower nuts and torque upper nut to 3,3–4,5 N·m(30–40 in-lb) .8Instruction Leaflet IL0131081ENEffective August 2015Installation and removal instructionsSeries NRX NF fixed breakerthree-way T ype 32 cable interlock kitEATON Figure 13. Details for Step 10: cable assembly drive (short rod) end mounting component identification, mounting cable assembly in cable bracket, and cable rod attachment to drive arm9Instruction Leaflet IL0131081ENEffective August 2015Installation and removal instructions Series NRX NF fixed breakerthree-way T ype 32 cable interlock kitEATON Step 11This step describes how to attach the driven (long rod) end of a cable attached to an interlock assembly on another breaker to the cable bracket and interlock assembly on this Type NF frame breaker . Refer to Figure 11 and Figure 12 for cable routing and correct swivel fittings to which the cables are connected .The driven (long rod) end of the cable is attached to thecorresponding push or pull swivel fitting on the driven lever on this cable interlock assembly similarly to Step 10 except the driven end does not utilize a compression spring between the swivel and nut . For the push cable, remove and discard the 22,2 mm (0,875 in) cable tube spacer (P) on the rod end of the cable assembly (N) and replace it with the 30,5 mm (1,2 in) cable tube spacer (J) . For the pull cable, retain the 22,2 mm (0,875 in) cable tube spacer (P) on the rod end of the cable assembly (N) . Install as shown in Figure 18 .Step 12This step describes how to adjust the cables to ensure proper functionality of the cable interlock setup . Cable adjustments are made with the large bulkhead nuts ONL Y and with all breakers OPEN . Nuts on the rod ends should not be moved .Begin by adjusting or verifying that the threaded section of allbulkhead fittings are approximately centered on the cable mounting brackets, allowing for room to adjust in either direction . Hand tighten the nuts at this time .Perform initial adjustments on the driven (long rod) end of cable until the gaps identified in Figure 14 through Figure 17 are as specified . Figure 14 through Figure 17 show the position of the interlock assembly driven “And” lever based on the state of the interconnected breakers .Lever plateGap 0Connected breaker openFigure 14. Driven “And” lever position with interconnected breakers openLever plateGap 0–4 mmConnected breaker closedConnected breaker openGap 0–2 mmFigure 15. Driven “And” lever position with interconnected push breaker open and pull breaker closedLever plateGap 0–4 mmConnected breaker openGap 0Connected breaker closed Figure 16. Driven “And” lever position with interconnected push breaker closed and pull breaker open10Instruction Leaflet IL0131081ENEffective August 2015Installation and removal instructionsSeries NRX NF fixed breakerthree-way T ype 32 cable interlock kitEATON Lever plateConnected breaker closedFigure 17. Driven “And” lever position with interconnected breakers closedIf there is too much clearance , adjust both bulkhead nuts to retract the cable housing (move threaded portion down) .If there is no clearance , advance the cable housing in the same manner (move threaded portion up) .If additional adjustment length is needed, the bulkhead nuts on the other (drive) end of cable can be used .When the proper clearance is attained on the driven end, torque both cable bulkhead nuts to 11–13 N·m (100–120 in-lb) without moving the bulkhead fittings .After the driven end has been adjusted and the bulkhead nuts have been tightened, perform adjustments on the drive (short rod) end of the cable . Adjust the bulkhead nuts up (move threaded portion down) such that the gap between the drive lever and the interlock assembly base shown on Figure 12 is less than 8 mm .When the gap is less than 8 mm, torque the cable bulkhead nuts on both ends to 11–13 N·m (100–120 in-lb) .Lower nutsUpper nutCable tube spacerDriven end (long rod)BulkheadRubber boot Outer bulkhead nut Lock washers (2)Pull swivel Upper nut22,2 mm (0,875 in) cable tube spacer Lower nutsDriven “And”leverPull swivel Upper nut30,5 mm (1,2 in) cable tube spacer Lower nutsDriven end cable bracketsFigure 18. Details for Step 11: driven (long rod) end mounting component identification and Step 12 driven (long rod) end after adjustments11Instruction Leaflet IL0131081EN Effective August 2015Installation and removal instructions Series NRX NF fixed breaker three-way T ype 32 cable interlock kitEATON Functional test of interlock assembly Refer to T able 1 and Figure 1 for breaker position in the interlock configuration . Begin test sequence with all breakers OPEN . For Breaker A , verify that the interlock assembly is positioned as shown in Figure 19 while in the various states required by the steps below . For Breakers B and C , use the figure included in the information leaflet for the interlock kit installed on those breakers .T ype 32Six-cable interlock assembly test . Refer to T able 1 for logic details .• OPEN all breakers• CHARGE and CLOSE Breaker A —Breakers B and C should not be interlocked (not held OPEN and able to CLOSE, one at a time)• OPEN Breaker A• CHARGE and CLOSE Breaker B —Breakers C and A should not be interlocked (not held OPEN and able to CLOSE, one at a time)• OPEN Breaker B• CHARGE and CLOSE Breaker C —Breakers A and B should not be interlocked (not held OPEN and able to CLOSE, one at a time)• OPEN Breaker C• CHARGE and CLOSE Breakers A and B —Breaker C should be interlocked (held OPEN, not able to CLOSE)• CHARGE and attempt to CLOSE Breaker C —it should not respond to CLOSE attempt (no noise, spring discharge, or contact motion)• OPEN Breakers A and B• CHARGE and CLOSE Breakers B and C —Breaker A should be interlocked (held OPEN, not able to CLOSE)• CHARGE and attempt to CLOSE Breaker A —it should not respond to CLOSE attempt (no noise, spring discharge, or contact motion)• OPEN Breakers B and C• CHARGE and CLOSE Breakers C and A —Breaker B should be interlocked (held OPEN, not able to CLOSE)• CHARGE and attempt to CLOSE Breaker B —it should not respond to CLOSE attempt (no noise, spring discharge, or contact motion)• OPEN Breakers C and AThe mechanical interlock is now properly installed and adjusted . Use a light amount of supplied lubricant (G) if any interlock parts are sticky or do not fully reset . This is only recommended if needed .Type RF frame breaker interlock assembly in OPEN state (not interlocked, able to close) .Type RF frame breaker interlock assembly in interlocked state (open and unable to close) .Type RF frame breaker interlock assembly in CLOSED state (not interlocked) .Figure 19. Position of interlock based on breaker stateEaton1000 Eaton Boulevard Cleveland, OH 44122 United StatesEaton .com© 2015 EatonAll Rights ReservedPrinted in USAPublication No . IL0131081EN / Z16896 Part Number: IL0131081ENH01 August 2015Eaton is a registered trademark.All other trademarks are propertyof their respective owners. Installation and removal instructions Series NRX NF fixed breaker three-way T ype 32 cable interlock kitInstruction Leaflet IL0131081ENEffective August 2015Disclaimer of warranties and limitationof liabilityThe information, recommendations, descriptions, and safety notations in this document are based on Eaton’s experience and judgment, and may not cover all contingencies . If further information is required, an Eaton sales office should be consulted .Sale of the product shown in this literature is subject to the terms and conditions outlined in appropriate Eaton selling policies or other contractual agreement between Eaton and the purchaser .THERE ARE NO UNDERSTANDINGS, AGREEMENTS, WARRANTIES, EXPRESSED OR IMPLIED, INCLUDING WARRANTIES OF FITNESS FOR A PARTICULAR PURPOSE OR MERCHANTABILITY, OTHER THAN THOSE SPECIFICALL Y SET OUT IN ANY EXISTING CONTRACT BETWEEN THE PARTIES . ANY SUCH CONTRACT STATES THE ENTIRE OBLIGATION OF EATON . THE CONTENTS OF THIS DOCUMENT SHALL NOT BECOME PART OF OR MODIFY ANY CONTRACT BETWEEN THE PARTIES .In no event will Eaton be responsible to the purchaser or user in contract, in tort (including negligence), strict liability or otherwisefor any special, indirect, incidental or consequential damage or loss whatsoever, including but not limited to damage or loss of use of equipment, plant or power system, cost of capital, loss of power, additional expenses in the use of existing power facilities, or claims against the purchaser or user by its customers resulting fromthe use of the information, recommendations and description contained herein .The information contained in this manual is subject to change without notice .。
驰腾ct930R一维说明书完整版

VC-SZSC-1DR02.C111免责声明请您在使用本手册描述的产品前仔细阅读手册的所有内容,以保障产品的安全有效地使妥善保存以备下次使用时查询。
请勿自行拆卸终端或撕毁终端上的封标,否则东莞市万酷电子科技有限公司不承担保修或更换终端的责任。
本手册中的图片仅供参考,如有个别图片与实际产品不符,请以实际产品为准。
对于本产品的改良更新,东莞市万酷电子科技有限公司保留随时修改文档而不另行通知的权利。
本手册包含的所有信息受版权的保护,东莞市万酷电子科技有限公司保留所有权利,未经书面单位及个人不得以任何方式或理由对本文档全部或部分内容进行任何形式的摘抄、复制或与其它产销售。
本手册中描述的产品中可能包括东莞市万酷电子科技有限公司或第三方享有版权的软件,除非获得相关权利人的许可,否则任何单位或者个人不能以任何形式对前述软件进行复制、分发、修改、摘录、反编、解密、反相工程、出租、转让、分许可以及其它侵犯软件版权的行为。
东莞市万酷电子科技有限公司对本声明拥有最终解释权。
版本记录版本更新及说明目录第一章系统设置 (6)简介 (6)恢复默认值 (7)查看版本号 (7)启动关闭设置码 (8)发送设置码 (9)识读模式选择 (10)解码声音设置 (13)声音增大/减小 (13)声音频率 (13)数据传输速度 (14)图像识别方式 (15)第二章通讯设置 (16)简介 (16)USB-KBW模式 (16)PS2键盘口模式 (20)USB-COM虚拟串口模式 (20)TTL/RS232串口通讯模式 (20)第三章数据编辑 (22)简介 (22)Code ID设置 (23)自定义前缀 (24)自定义后缀 (25)退出添加前后缀 (26)隐藏字符 (27)结束符设置 (31)字符转换 (32)第四章条码参数设置 (33)简介 (33)UPC-A (33)UPC-E (35)EAN-8 (37)EAN-13 (38)Code 128 (40)Code 39 (40)Code 93 (41)Code 11 (42)Interleaved 2 of 5 (43)Matrix 2 of 5 (43)Industrial 2 of 5 (43)Standard 2 of 5(IATA) (44)Codabar(NW-7) (44)Plessey (45)MSI Plessey (45)GS1 DataBar Limited(RSS Limited) (46)GS1 DataBar Omnidirectional(RSS Omnidirectional) (46)China Post(Datalogic 2 of 5) (46)附加位设置 (47)第五章串口通信指令 (48)简介 (48)帧格式结构 (48)指令解析 (49)指令保存 (49)指令反馈设置 (50)声音反馈设置 (50)触发指令 (50)实例分析 (51)指令发送示例 (53)第六章附录 (54)附录-默认设置表 (54)附录-Code ID (58)附录-指令集 (59)附录-字符表(用于添加前后缀) (66)附录-ASCII码表 (72)第一章系统设置简介用户可通过扫描一个或多个设置条码对条码器进行功能设置。
Hypertherm Powermax G3 Series Plasma Cutter 产品说明书

The performance st andard for air plasma cuttingISO 90013⁄4"(19mm )1"(25mm )11⁄4"(32mm )Maximum capacitySeverance capacityRecommended capacityHyper therm – the world leader in plasma cutting technologyW hen you do only one thing, you’d better do it better than anyone else. As the only major manufacturer to focus exclusively on plasma cutting technology, Hypertherm is committed to providing the highest quality systems in the world: improving the performance, reliability and value of our systems, and serving and supporting Hypertherm users. This commitment to technology leadership, quality and support makes Hypertherm the first choice of the true cutting professional.Superior performance by hand or machineT he Powermax1000 is the latest addition to the Powermax G3 Series. With advanced technologies in both power supply and torch,The third generation of plasma cutting has a second great product!The power supply:the heart of the machineAdvanced, intelligent tec hnology gives the Powermax1000 the power to cut with greater speed, quality and efficiency.60-amp, 8.4-kilowatt output provides ample power for clean, quick cutting.Auto-voltage runs on voltages from 200 to 600 volts, 1- or 3-phase, (CE 230 to 400 V 3-phase only) without the need for manual rewiring.New Boost Conditioner ™circuitcompensates for input voltage variation. Advanced, digitally-controlled inverter design delivers continuously adjustable, constant current output from 20 to 60 amps, permitting high-quality cuts over a wide range of metal thicknesses.An active electronic pilot arc controller for cutting expanded metal or grating. New gouging setting for easier operation and faster metal removal.CNC/robotic machine interface is standard on all units, allowing automated control and rapid changeover to mechanized operation.Hypertherm G3 products cut faster and more economically than any system available today.The Powermax1000’s Auto-voltage ™circuit provides automatic adjustment to any input voltage from 200 to 600 volts, 1- or 3-phase (CE 230 to 400 V 3-phase only). A state-of-the-art, microprocessor-based architecture assures optimum system reliability. Add to this Hypertherm’s advanced torch technology and easy-to-read controls, and you have the most advanced plasma cutter money can buy.Recommended capacity: metals to 3⁄4inc h (19 mm) at cutting speeds of 22 inches (559 mm) per minute.Maximum capacity:metals to 1 inc h (25 mm) at cutting speeds of 12 inches (304 mm) per minute.Severance capacity:rough cut on metals up to 11⁄4inc hes (32 mm) at low speed.The cut capacities above are on mild steel.Some metals, such as aluminum and stainless steel, may require up to 20% reduction in cut speed and capacity.Mac hine torch operationRecommended capacity:Up to 3⁄8inc h (10 mm).Maximum capacity: Up to 1⁄2inc h (12 mm).Cutting above requires an edge start.withCoaxial-assistWorkpiecePowermax1000Competitor ACompetitor BCompetitor CHypertherm, P owermax, G3 Series, HyLife, Boost Conditioner, Dual-threshold, Auto-voltage, Coaxial-assist, ETR (Easy Torch Removal) and FineCut are trademarks of Hypertherm, Inc. and may be registered in the United States and/or other countries.© Copyright 6/05 Hypertherm, Inc. Revision 4 860240 North AmericanHyper therm, Inc. U **********************************************************Hyper therm Automation, LLC U *************************************************************Hyper therm Plasmatechnik, GmbH D eutschland 49 6181 58 2100 Tel 49 6181 58 2134 Fax *********************************Hyper therm (S) Pte Ltd. Singapore 65 6 841 2489 Tel 65 6 841 2490 Fax *******************************Hyper therm Branc h of Hypertherm UK, LLC England 00 800 3324 9737 Tel 00 800 4973 7329 Fax ************************Fr ance 00 80033249737Té*********************************************Hyper therm S.r.l. Italia 3*********************************************************Hyper therm Europe B.V. Nederland 31 165 596907 Tel 31 165 596901 Fax ****************************Japan 810 559757387 Tel 810 55975**********************************H YPERTHERM BRASIL LTDA. 5*********************************************************Input volt ages 200 – 600 V, 1/3-PH, 50 - 60 Hz, CSA 230 – 400 V, 3-PH, 50 - 60 Hz, CEInput current @8.4 kW200/208/230/240/480 V, 1-PH: 50/48/44/42/22 A 200/208/230/240/400/480/600 V, 3-PH: 30/29/26/24/15/12/11 A Output voltage 140 VDCDuty cycle @ 40˚ C 50% @ 60 A, 230 – 600 V, 3-PH (104˚ F)50% @ 60 A, 230 – 480 V, 1-PH 40% @ 60 A, 200 – 208 V, 3-PH 40% @ 60 A, 200 – 208 V, 1-PH Maximum OCV 300 VDCDimensions 23.1" (586 mm) D; 10.7" (271 mm) W; 19.6" (498 mm) H Weight with torch 83 lbs (37 kg)Gas supply Clean, dry, oil-free air or nitrogenFlow rate 400 scfh; 6.7 cfm (189 l/min) at 90 psi (6.2 bar)Flow pressure70 psi (4.8 bar) flowing, 25' leads 75 psi (5.1 bar) flowing, 50' leadsPowerma x1000 G3 Series standard system componentsP ower supplyT60 or T60M torch Spare consumables Work cable with clamp 15 feet (4.5 m)Primary power cableOptions - (P art number)Circle cutting guide - 027668Wheel kit - 128646Leather cable covers - 024548Air filtration kit - 128647Extended work cable - 128717Hand heat shield - 128658Ordering informationSpecificationsG F IJH Maximum Material Thickness Current travel speed*(inches)(mm)(amps)(ipm)(mm/min.)Mild steel26 GA.0.5256381620510 GA.3.44015138351⁄4 6.46013233533⁄810606316001⁄212604210675⁄81660317873⁄4196022559A luminum1⁄320.825610154941⁄8 3.24020451821⁄4 6.46014536833⁄810607418801⁄212605112955⁄8166033838Stainless 26 GA.0.52563116027steel 14 GA.1.94022156131⁄4 6.46011027943⁄810605313461⁄21260358895⁄81660266603⁄4196018457*Maximum travel speeds are the results of Hypertherm's laboratory testing. For optimum cut performance, actual cutting speeds may vary based on different cutting applications. Refer to the operator's manual for more details.S IP23CSSystems part numbersWith 25' With 50' With 75'(7.5 m) torch(15 m) torch (23 m) torch200 – 600 V, 1/3-PH, CSA Hand system 083178083179083210Machine system083182083183083212230 – 400 V, 3-PH, CE Hand system 083192083193083211Machine system083194083195083213(where indicated)High -performance portable plasma cutting systemOper ating dataHand torc h Machine torch Recommended capacity 3⁄4" (19 mm)3⁄8" (10 mm)Maximum capacity 1" (25 mm)1⁄2" (12 mm)Severance capacity11⁄4" (32 mm)–E。
驰腾CT3200A使用说明

1二维扫描引擎2D Scan Engine用户使用手册User’s Guide带接口板二维扫描引擎外观图 2D Scan Engine with Interface board1.RJ45接口2.串口二维扫描引擎外观图 2D Scan Engine扫描引擎接口 Scan Engine Interface●解码板 Decoder board●引擎头 Image Engine引擎头板 image board包括支架●规格参数传感器Sensor CMOS sensor, pixels: 640*480,30 fpsWhite LED624nm Red LED扫描视角Field of view Angle40*30 degree旋转 / 倾斜 / 偏转Roll / Pitch / Yaw angle360 / ±60 / ±61 degree电源 / 电流Voltage / Current3.3VDC±5% / 390mA(Max.),300mA(Typical)基本码制 Default code1D: Code 39 (Code 32), Code 128, UPC/EAN/JAN, Code 93, Interleaved 2 of 5, Codabar, Matrix2 of 5, Industrial 25(Straight 2 of 5 Industrial)2D: QR Code, Data Matrix, PDF417可选码制 Optional code1D: China Post(Hong Kong 2 of 5), NEC 2 of 5, Code 11, MSI Plessey, GS1 Databar(RSS), Korea Post, Trioptic code39, GS1 Composite Code, Telepen2D: MicroPDF417, Aztec Code, Codablock, MaxiCode, 汉信(Chinese Sensible Code)典型性能Typical Performance 13mil UPC (25-210mm)13mil Code39 (95-160mm)5mil Code39 (50-80mm)20mil Code39 (100-310mm(5chars)) 6.7mil PDF417 (25-120mm)10mil PDF417 (25-190mm)10mil Data Matrix (20-70mm)20mil QR (30-210mm)环境参数 Environment工作温度Operating temperature-20°C ~ +60°C储存温度Storage temperature-40°C ~ +85°C工作湿度Humidity5% ~ 95%(non-condensing)●出厂设置Factory default settings:接口Interface USB HID打开码制Enabled Codes1D: Code 39, Code 128, UPC/EAN/JAN2D: QR Code, Data Matrix, PDF417常用设置基本码制设置 Code settings:码制属性设置Codabar:命令 Programming command syntax串口缺省配置:115200bps,8数据位+1停止位Series default setting: 115200bps, 8 data bit + 1 stop bit格式 format:前缀 Prefix:设置参数命令前缀:<SYN>M<CR> (ASCII: 0x16,0x4d,0x0D)。
MIC3202 MIC3202-1 LED驱动器评估板说明书
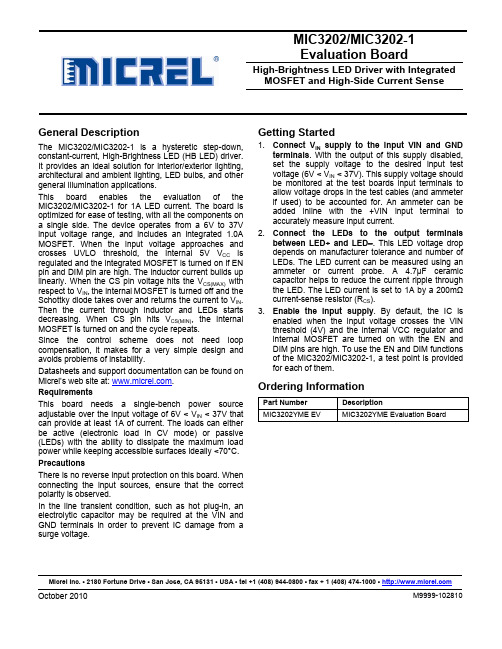
MIC3202/MIC3202-1Evaluation BoardHigh-Brightness LED Driver with IntegratedMOSFET and High-Side Current Sense Micrel Inc. • 2180 Fortune Drive • San Jose, CA 95131 • USA • tel +1 (408) 944-0800 • fax + 1 (408) 474-1000 • General DescriptionThe MIC3202/MIC3202-1 is a hysteretic step-down,constant-current, High-Brightness LED (HB LED) driver.It provides an ideal solution for interior/exterior lighting,architectural and ambient lighting, LED bulbs, and othergeneral illumination applications.This board enables the evaluation of theMIC3202/MIC3202-1 for 1A LED current. The board isoptimized for ease of testing, with all the components ona single side. The device operates from a 6V to 37Vinput voltage range, and includes an integrated 1.0AMOSFET. When the input voltage approaches andcrosses UVLO threshold, the internal 5V V CC isregulated and the integrated MOSFET is turned on if ENpin and DIM pin are high. The inductor current builds uplinearly. When the CS pin voltage hits the V CS(MAX) withrespect to V IN,the internal MOSFET is turned off and theSchottky diode takes over and returns the current to V IN.Then the current through inductor and LEDs startsdecreasing. When CS pin hits V CS(MIN), the internalMOSFET is turned on and the cycle repeats.Since the control scheme does not need loopcompensation, it makes for a very simple design andavoids problems of instability.Datasheets and support documentation can be found onMicrel’s web site at: .RequirementsThis board needs a single-bench power sourceadjustable over the input voltage of 6V < V IN < 37V thatcan provide at least 1A of current. The loads can eitherbe active (electronic load in CV mode) or passive(LEDs) with the ability to dissipate the maximum loadpower while keeping accessible surfaces ideally <70°C.PrecautionsThere is no reverse input protection on this board. Whenconnecting the input sources, ensure that the correctpolarity is observed.In the line transient condition, such as hot plug-in, anelectrolytic capacitor may be required at the VIN andGND terminals in order to prevent IC damage from asurge voltage.Getting Started1. Connect V IN supply to the input VIN and GNDterminals. With the output of this supply disabled,set the supply voltage to the desired input testvoltage (6V < V IN < 37V). This supply voltage shouldbe monitored at the test boards input terminals toallow voltage drops in the test cables (and ammeterif used) to be accounted for. An ammeter can beadded inline with the +VIN input terminal toaccurately measure input current.2. Connect the LEDs to the output terminalsbetween LED+ and LED−. This LED voltage dropdepends on manufacturer tolerance and number ofLEDs. The LED current can be measured using anammeter or current probe. A 4.7µF ceramiccapacitor helps to reduce the current ripple throughthe LED. The LED current is set to 1A by a 200mΩcurrent-sense resistor (R CS).3. Enable the input supply. By default, the IC isenabled when the input voltage crosses the VINthreshold (4V) and the internal VCC regulator andinternal MOSFET are turned on with the EN andDIM pins are high. To use the EN and DIM functionsof the MIC3202/MIC3202-1, a test point is providedfor each of them.Ordering InformationPart Number DescriptionMIC3202YME EV MIC3202YME Evaluation BoardOther FeaturesEN InputThe EN pin provides a logic level control of the output and the voltage has to be 2.0V or higher to enable the current regulator. The output stage is gated by the DIM pin. When the EN pin is pulled low, the regulator goes to off-state and the supply current of the device is reduced to below 1µA. Do not drive the EN pin above the supply voltage. DIM InputThe DIM pin provides a logic level control for brightness of the LED. A PWM input can be used to control the brightness of LED. DIM high enables the output and its voltage has to be 2.0V or higher. DIM low disables the output, regardless of EN high-state. Current-Sense InputThe CS pin provides the high-side current sense to set the LED current with an external sense resistor.A sense resistor R CS is placed between V IN and LED+ terminals.The current through LED is sensed by the sense resistor (R CS ). The sensed voltage is fed back to the MIC3202 to regulate the LED current R CS is given by:)I V +V (x 21=R LED)MIN (CS )MAX (CS CS Error!Bookmark not defined.I LED is LED current required to set.R CS (Ω) I LED (A)I 2R (W)Size (SMD)1.33 0.15 0.03 0603 0.56 0.35 0.07 0805 0.4 0.5 0.1 0805 0.28 0.7 0.137 0805 0.2 1.0 0.2 1206For V CS(MAX) and V CS(MIN) refers to the Electrical Characteristics table. Frequency of OperationTo calculate the frequency spread across input supply:)V +V (×I Δ×L )V R ×I V (×)V +R ×I +V (=F IN D L LED CS LED IN LED CS LED D SW --CS)MIN (CS )MAX (CS L R V V =I Δ-where:V D is Schottky diode forward drop V LED is total LEDs voltage drop V IN is input voltageI LED is average LED currentAccording to the above equation, choose the inductor to make the operating frequency no higher than 1MHz.Refer to the datasheet Application Information for more information on components selection guidelines. Frequency DitheringThe MIC3202 is designed to modulate the V CS(MAX) with amplitude ±6mV by a pseudo random generator to generate the ±12% of the switching frequency dithering. This spreads the frequency spectrum over a wider range and reduce the EMI noise peaks.The MIC3202-1 is non-dithering version of the MIC3202.Notes:1. If bulk capacitor on input rail is away (4 inches or more) from the MIC3202/MIC3202-1, install the 100µF bulk capacitor near V IN.2. Source impedance should be as low as 10mΩ.Bill of MaterialsItem Part Number Manufacturer DescriptionQty. 12105C475KAZ2A AVX (1) C1, C2, C8GRM32ER71H475KA88L Murata (2) 4.7µF/50V, Ceramic Capacitor, X7R, Size 1210 2 08053D105KAT2A AVX (1)1µF/25V, Ceramic Capacitor, X5R, Size 0805 1 GRM21BR71E105KA99L Murata (2) C3, C9C2012X7R1E105K TDK (3)1µF/25V, Ceramic Capacitor, X7R, Size 0805 1 06035C271KAT2A AVX (1)C4, C7GRM188R71H271KA01D Murata (2)270pF/50V, Ceramic Capacitor NPO, Size 0603206035C104MAT AVX (1)GRM188R71H104KA93D Murata (2) C5, C6C1608X7R1H104K TDK (3)0.1µF/50V, Ceramic Capacitor, X7R, Size 06032SS24-TP MCC (4) D1 SS24 Fairchild (5) 60V, 2A, SMA, Schottky Diode 1 D2, D3B0530WS-TPMCC (4) 30V, 200mA, Schottky diode, SOD-323 2 L1 SLF10145T-470M1R4 TDK (3) 47µH, 1.4A, SMT, Power Inductor 1 R1 CSR 1/2 0.2 1% I Stackpole Electronics,Inc (7)0.2Ω Resistor, 1/2W, 1%, Size 12061 R2, R3CRCW06031003FKEAVishay (8) 100k Ω Resistor, 1%, Size 06032 R4 CRCW08052R20FKEA Vishay (8) 2.2Ω Resistor, 1%, Size 0805 1 R5 CRCW080510R0FKEA Vishay (8) 10Ω Resistor, 1%, Size 0805 1 R6 CRCW060310K0FKEA Vishay (8) 10k Ω Resistor, 1%, Size 0603 1 R7, R8CRCW06030000FKEAVishay (8)0Ω Resistor, 1%, Size 06032 R9 CRCW060349R9FKEA Vishay (8)49.9Ω Resistor, 1%, Size 0603 1RV1 3386P-1-104TLF Bourns (9) POT 100k Ω 3/8" SQ CERM SL ST1U1 MIC3202YME Micrel, Inc.(10)High Brightness LED Driver with High-SideCurrent Sense 1 U2 MIC1557YM5Micrel, Inc.(10) RC Time/Oscillator (SOT-23-5)1Notes:1. AVX: .2. Murata: .3. TDK: .4. MCC: .5. Fairchild: .6.Diodes Inc. : .7. Stackpole Electronics: . 8. Vishay: . 9.Bourns Inc : . 10. Micrel, Inc.: .PCB Layout RecommendationsTop AssemblyTop LayerPCB Layout Recommendations (Continued)Bottom Layer。
M3202C M3702C 用户手册说明书
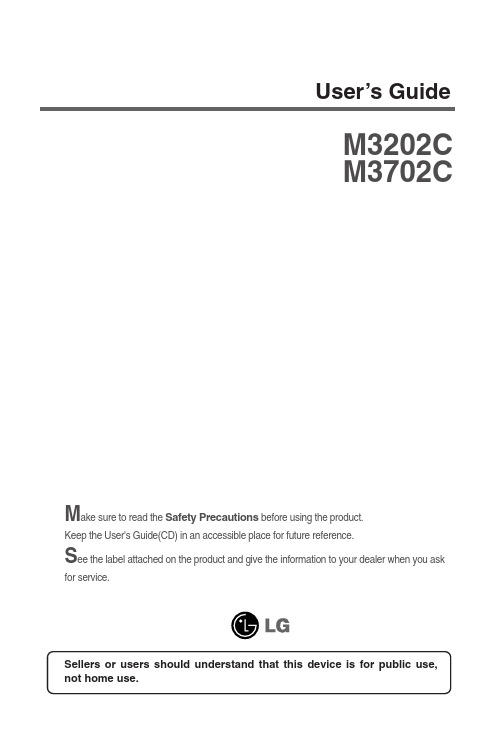
AV Component1 Component2 RGB PC HDMI/DVIPC Rear side of the product.Component2RGB PC HDMI/DVI RGB PC HDMI/DVIRGB INRGB OUTRGB IN RGB OUT RGB IN RGB OUT RGB IN RGB OUTAVComponent1Component2RGB PCHDMI/DVIWhen the BNC cable is connected simultaneously with S-Video cable, S-Video input has a priority.Component1Component2RGB PC HDMI/DVIAVComponent1Component2RGB PC HDMI/DVIConnect the video/audio cable as shown in the below figure and then connect the power cord (See page 9).RCA-PC Audio CableProductVCR/DVD/Set-top BoxHDMI to DVI Signal Cable (not included)HDMI Input (480p/576p/720p/1080i/1080p)VCR/DVD/Set-top BoxProductSelect an input signal.Press the INPUT button on the remote control to select the input signal.Or, press the INPUT botton on the bottom of the product.INPUT SETINPUTAUTO/SETHDMI Signal Cable (not included)When connecting with a HDMI to DVI signal input cable.When connecting with a HDMI signal input cable.• Select HDMI/DVI-HDMI Supports High Definition input and HDCP (High-bandwidth Digital Content Protection). Some devices require HDCP in order to display HD signals.Note : Dolby Digital is not supported.Input AVComponent1Component2RGB PC HDMI/DVIAVComponent1Component2RGB PC This is where the unit receives signals from the remote control.VividStandardMENUToggles between screen presets.: Select this option to display with a sharp image.Standard: The most general and natural screen display status.MENUBacklight: To control the brightness of the screen,adjust the brightness of LCD panel.Contrast : Adjust the difference between the light and dark levels in the picture.CoolMediumWarmUser Color Settings: Slightly purplish white. Medium: Slightly bluish white.Red / Green / BlueSet your own color levels.Gamma: Set your own gamma value. : -50/0/50On the monitor, high gamma values display whitish images and low gammavalues display high contrast images.16:9Original Widescreen mode.Adjust the screen video.PictureAuto Config. (RGB PC input only) : This button is for the automatic adjustment of the screen position, clock and phase. This function is available for analog signals only.If the picture isn't clear after auto adjustment and characters are stillClear VoiceStandardMusicClear Voice: By differentiating the human sound range from others,it helps users listen to human voices better.Standard: The most commanding and natural audio.To adjust uneven sound volumes across all channels or signals automatically to the mostIf the current time is incorrect, reset the clock manually.1) Press the MENU2) Press the button and then useIn the event of power interruption (disconnection or power failure), the clock must be reset. Once the on or off time is set, these functions operate daily at the preset time.Off time function overrides On time function if they are set to the same time.When On time is operated, input screen is turned on as it was turned off.To choose the language in which the control names are displayed. Use the buttons to selectTile mode and choose Tile alignment and set the ID of the current product to set location.Tile ModeID 1ID 2ID 3ID 4Tile mode (product 1 ~ 4) : r(2) x c(2)rowID 1ID 2ID 1ID 2ID 3ID 4ID 5ID 6ID 7ID 8ID 9ID 1ID 5ID 9ID 13ID 2ID 6ID10ID 14ID 3ID 7ID 11ID 15ID 4ID 8ID 12ID 16Adjust the horizontal size of the screen taking into account the size of the bezel.You can assign a uniqueproducts are connected for display. Specify the number (1~99) using the button。