基于DOE的汽车碰撞优化分析_雷刚
汽车零部件结构性能分析及关键部件轻量化设计

汽车零部件结构性能分析及关键部件轻量化设计摘要:安全、节能、环保是当今汽车工业的三大主题,而汽车轻量化则是实现这三大诉求的重要途径。
部件结构作为车身的重要组成部分,其重量占到车身钣金件的比重达到20%左右,因此部件结构的轻量化对整车的轻量化具有重要意义。
关键词:汽车;零部件结构性能;关键部件;轻量化设计现代化的汽车工业中,为了降低成本,提高竞争力,模块化设计和平台化生产已经成为行业共识,前端框架的零件概念即由此产生。
部件结构将传统意义上汽车头部的散热器框架集成化,形成一个相对独立的模块连接到白车身。
汽车制造商因此解放出来,将各挂载组件的性能及尺寸控制交付给专业的零件供应商,从而更好地聚焦于整车性能表现以及尺寸匹配。
这种设计生产方式客观上加速了车型升级换代,使得汽车制造商在保持既有车型平台不变、多次复用的情况下,只需变更不同的模块设计(包括部件结构)就可以实现车型造型或功能升级,大大提升了迭代效率,同时节省了迭代成本。
1汽车零部件结构性能分析汽车开闭件在汽车整体系统中极为重要,其主要是指汽车上能够开闭的零部件,包括前后车门、前舱盖、后背门、顶棚总成等,多采取铰接方式连接。
开闭件对尺寸、公差要求较高,其制作工艺也极为复杂,安装时所需附件较多,且具有灵活、坚固、密封等多种安装要求,这些要求若无法得到保证,汽车的品质与性能都将受到严重影响。
前门作为汽车开闭件之一,其使用率极高,结构模态是影响车辆频率的重要因素,车门结构模态必须错开路面载荷激振频率与车辆频率,防止因车轮的不平衡导致激振频率的紊乱。
车门上部基本由玻璃组成,较为薄弱,而钣金件是汽车结构支撑的主要材料,它在车门门框的上部分较少,且门框相较车门其他部分更为薄弱,该处易导致门框外侧变形,引发车门密封性变差,使车门无法抵御风雨穿透,严重时易出现门框剧烈振动,导致玻璃无法正常升降。
窗沿处的前门内板腰线刚度在车门中的作用也是极为重要的,如若该处刚度不足,对于玻璃升降的平顺性可造成影响,易引发不必要的事故。
车辆碰撞模型的动力学分析与优化
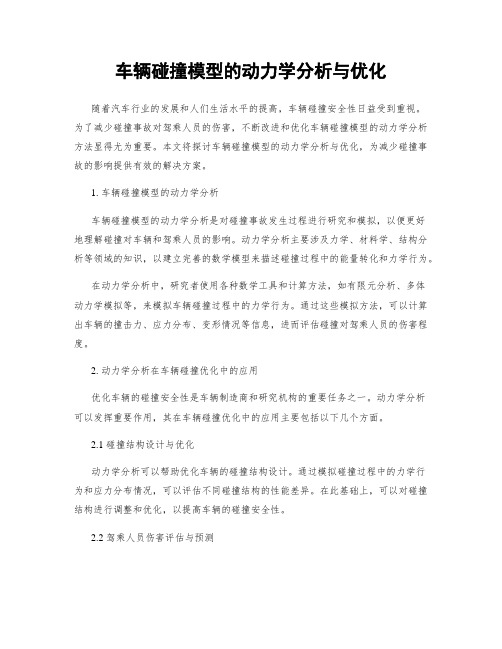
车辆碰撞模型的动力学分析与优化随着汽车行业的发展和人们生活水平的提高,车辆碰撞安全性日益受到重视。
为了减少碰撞事故对驾乘人员的伤害,不断改进和优化车辆碰撞模型的动力学分析方法显得尤为重要。
本文将探讨车辆碰撞模型的动力学分析与优化,为减少碰撞事故的影响提供有效的解决方案。
1. 车辆碰撞模型的动力学分析车辆碰撞模型的动力学分析是对碰撞事故发生过程进行研究和模拟,以便更好地理解碰撞对车辆和驾乘人员的影响。
动力学分析主要涉及力学、材料学、结构分析等领域的知识,以建立完善的数学模型来描述碰撞过程中的能量转化和力学行为。
在动力学分析中,研究者使用各种数学工具和计算方法,如有限元分析、多体动力学模拟等,来模拟车辆碰撞过程中的力学行为。
通过这些模拟方法,可以计算出车辆的撞击力、应力分布、变形情况等信息,进而评估碰撞对驾乘人员的伤害程度。
2. 动力学分析在车辆碰撞优化中的应用优化车辆的碰撞安全性是车辆制造商和研究机构的重要任务之一。
动力学分析可以发挥重要作用,其在车辆碰撞优化中的应用主要包括以下几个方面。
2.1 碰撞结构设计与优化动力学分析可以帮助优化车辆的碰撞结构设计。
通过模拟碰撞过程中的力学行为和应力分布情况,可以评估不同碰撞结构的性能差异。
在此基础上,可以对碰撞结构进行调整和优化,以提高车辆的碰撞安全性。
2.2 驾乘人员伤害评估与预测在车辆碰撞优化过程中,了解驾乘人员的伤害情况是至关重要的。
动力学分析可以计算出碰撞过程中驾乘人员所受的力和加速度等信息,从而评估出伤害的程度。
这些信息可以用于优化车辆的安全设计,以减少碰撞事故对驾乘人员的伤害。
2.3 车辆主动安全系统的开发与改进动力学分析还可以用于开发和改进车辆的主动安全系统。
通过模拟不同碰撞情况下主动安全系统的响应,可以评估系统的效果和性能。
这些结果可以指导主动安全系统的设计和改进,提高车辆在碰撞中的安全性能。
3. 动力学分析方法的挑战与展望尽管动力学分析在车辆碰撞优化中的应用已经取得了一定的进展,但仍然存在一些挑战和待解决的问题。
基于DOE的汽车碰撞优化分析

基于DOE的汽车碰撞优化分析
雷刚;王希杰;张攀
【期刊名称】《重庆理工大学学报(自然科学版)》
【年(卷),期】2011(025)002
【摘要】建立了整车的有限元模型,对整车模型进行正面碰撞仿真分析,根据国标评价标准对车身加速度等参数进行了分析;在此基础上,提出了用实验设计的方法对汽车安全性进行直观分析、方差分析和显著性分析,得到最优的试验方案.优化结果表明,相比初始设计方案,优化后的方案明显降低了车身加速度,增强了汽车的耐撞性,为汽车正面碰撞安全设计与改进提供了依据.
【总页数】5页(P8-12)
【作者】雷刚;王希杰;张攀
【作者单位】重庆理工大学汽车零部件制造及检测技术教育部重点实验室,重庆400054;重庆理工大学汽车零部件制造及检测技术教育部重点实验室,重庆400054;澳汰尔工程软件(上海)有限公司,上海,200082
【正文语种】中文
【中图分类】U491
【相关文献】
1.基于DOE的汽车碰撞优化分析 [J], 雷刚;王希杰;张攀
2.基于DOE的某车型无骨刮片优化分析 [J], 孔金超; 杨桂林; 梁刚
3.基于DOE与梯度优化的驱动条件多参数分析与优化 [J], 路昕;盛誉;陈雪凯
4.基于DOE实验设计的卤水中锂分析方法优化 [J], 李玲;乃学瑛;柴小丽;刘鑫;高丹丹;董亚萍
5.基于DOE及RSM的单线圈磁流变阻尼器优化设计及动力性能分析 [J], 胡国良;易锋;张佳伟;喻理梵
因版权原因,仅展示原文概要,查看原文内容请购买。
基于汽车正面碰撞的吸能盒设计及优化_雷刚
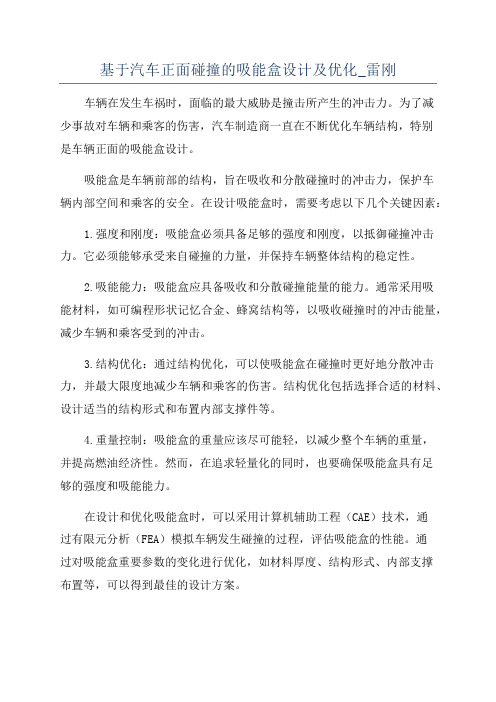
基于汽车正面碰撞的吸能盒设计及优化_雷刚车辆在发生车祸时,面临的最大威胁是撞击所产生的冲击力。
为了减少事故对车辆和乘客的伤害,汽车制造商一直在不断优化车辆结构,特别是车辆正面的吸能盒设计。
吸能盒是车辆前部的结构,旨在吸收和分散碰撞时的冲击力,保护车辆内部空间和乘客的安全。
在设计吸能盒时,需要考虑以下几个关键因素:1.强度和刚度:吸能盒必须具备足够的强度和刚度,以抵御碰撞冲击力。
它必须能够承受来自碰撞的力量,并保持车辆整体结构的稳定性。
2.吸能能力:吸能盒应具备吸收和分散碰撞能量的能力。
通常采用吸能材料,如可编程形状记忆合金、蜂窝结构等,以吸收碰撞时的冲击能量,减少车辆和乘客受到的冲击。
3.结构优化:通过结构优化,可以使吸能盒在碰撞时更好地分散冲击力,并最大限度地减少车辆和乘客的伤害。
结构优化包括选择合适的材料、设计适当的结构形式和布置内部支撑件等。
4.重量控制:吸能盒的重量应该尽可能轻,以减少整个车辆的重量,并提高燃油经济性。
然而,在追求轻量化的同时,也要确保吸能盒具有足够的强度和吸能能力。
在设计和优化吸能盒时,可以采用计算机辅助工程(CAE)技术,通过有限元分析(FEA)模拟车辆发生碰撞的过程,评估吸能盒的性能。
通过对吸能盒重要参数的变化进行优化,如材料厚度、结构形式、内部支撑布置等,可以得到最佳的设计方案。
另外,还可以利用仿生学原理进行吸能盒的设计和优化。
仿生学是一门研究生物体结构、形态和功能的学科,通过借鉴自然界的智慧,可以设计出更有效的吸能盒。
例如,可以通过仿生学原理设计出具有类似骨骼结构的吸能盒,以提高其强度和吸能能力。
总之,基于汽车正面碰撞的吸能盒设计及优化需要考虑多个关键因素,如强度、刚度、吸能能力、结构优化和重量控制。
通过采用CAE技术和仿生学原理,可以得到最佳的设计方案,提高车辆和乘客在碰撞事故中的安全性。
Hyperstudy在轿车正面碰撞优化分析中的应用
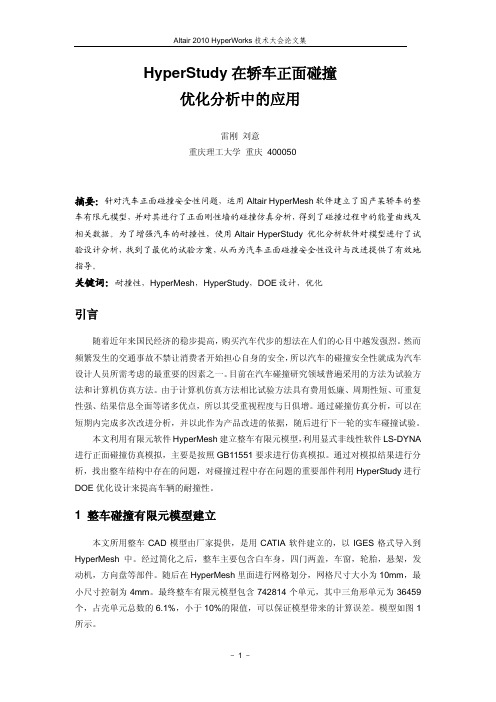
HyperStudy在轿车正面碰撞优化分析中的应用雷刚刘意重庆理工大学重庆400050摘要:针对汽车正面碰撞安全性问题,运用Altair HyperMesh软件建立了国产某轿车的整车有限元模型,并对其进行了正面刚性墙的碰撞仿真分析,得到了碰撞过程中的能量曲线及相关数据。
为了增强汽车的耐撞性,使用Altair HyperStudy 优化分析软件对模型进行了试验设计分析,找到了最优的试验方案,从而为汽车正面碰撞安全性设计与改进提供了有效地指导。
关键词:耐撞性,HyperMesh,HyperStudy,DOE设计,优化引言随着近年来国民经济的稳步提高,购买汽车代步的想法在人们的心目中越发强烈。
然而频繁发生的交通事故不禁让消费者开始担心自身的安全,所以汽车的碰撞安全性就成为汽车设计人员所需考虑的最重要的因素之一。
目前在汽车碰撞研究领域普遍采用的方法为试验方法和计算机仿真方法。
由于计算机仿真方法相比试验方法具有费用低廉、周期性短、可重复性强、结果信息全面等诸多优点,所以其受重视程度与日俱增。
通过碰撞仿真分析,可以在短期内完成多次改进分析,并以此作为产品改进的依据,随后进行下一轮的实车碰撞试验。
本文利用有限元软件HyperMesh建立整车有限元模型,利用显式非线性软件LS-DYNA 进行正面碰撞仿真模拟,主要是按照GB11551要求进行仿真模拟。
通过对模拟结果进行分析,找出整车结构中存在的问题,对碰撞过程中存在问题的重要部件利用HyperStudy进行DOE优化设计来提高车辆的耐撞性。
1 整车碰撞有限元模型建立本文所用整车CAD模型由厂家提供,是用CATIA软件建立的,以IGES格式导入到HyperMesh中。
经过简化之后,整车主要包含白车身,四门两盖,车窗,轮胎,悬架,发动机,方向盘等部件。
随后在HyperMesh里面进行网格划分,网格尺寸大小为10mm,最小尺寸控制为4mm。
最终整车有限元模型包含742814个单元,其中三角形单元为36459个,占壳单元总数的6.1%,小于10%的限值,可以保证模型带来的计算误差。
基于碰撞模拟仿真的汽车车身刚性设计与优化

基于碰撞模拟仿真的汽车车身刚性设计与优化汽车在现代交通中扮演着重要的角色,而车身刚性是确保汽车乘员安全的重要因素之一。
随着科技的不断进步,碰撞模拟仿真成为了汽车行业中评估车辆安全性能的重要手段之一。
本文将讨论使用碰撞模拟仿真技术来进行汽车车身刚性设计与优化的方法。
1. 概述在汽车设计过程中,车身刚性是指汽车车身在受到碰撞或其他外力作用时的抗变形能力。
车身刚性的好坏直接影响车辆在碰撞事故中的安全性能。
因此,对车身刚性进行设计与优化是保障乘员安全的关键。
2. 碰撞模拟仿真简介碰撞模拟仿真是一种通过计算机模型对碰撞事故进行模拟的方法。
它可以通过预测车身在不同碰撞条件下的变形情况,帮助设计师评估车辆在不同碰撞事故中的安全性。
碰撞模拟仿真可以更好地理解和分析碰撞事故的物理过程,从而指导车身结构的刚性设计与优化。
3. 车身刚性设计与优化步骤3.1 初始车身结构设计在进行初始车身结构设计时,需要考虑到车身的骨架结构和各个构件之间的连接方式。
通过使用现代CAD软件,设计师可以快速绘制出车身的初始结构。
此时,需要注意车身的整体刚性布局和各个部件的布局。
3.2 建立碰撞仿真模型根据初始车身结构,需要将其转化为碰撞模拟仿真软件可识别的模型。
通常,采用有限元分析(FEA)技术将车身结构离散化为有限元网格。
在建模过程中,需要确保模型的准确性和精确性以保证仿真结果的可靠性。
3.3 定义碰撞边界条件及仿真方案定义碰撞边界条件是进行碰撞模拟的关键一步。
这包括定义碰撞速度、角度、区域等信息,以确保模拟的准确性。
在定义完碰撞边界条件后,还需选择合适的仿真方案,如选择撞击方向、撞击速度等参数。
3.4 执行碰撞仿真在定义好碰撞边界条件和仿真方案后,可以执行碰撞仿真。
这一过程由计算机对车身结构进行数值计算,模拟碰撞过程中发生的变形和应力分布情况。
仿真过程将模拟车身在碰撞事故中的响应,如变形程度、局部应力等。
3.5 优化车身结构通过对碰撞仿真结果的分析,可以获得车身在碰撞事故中的弱点和改进的方向。
轿车扭转梁悬架强度分析与疲劳寿命预测

doi:10. 3969 / j. issn. 1007-4554. 2012. 11. 05
0 引言
扭转梁悬架被广泛用于前轮驱动的中小型 家庭轿车的后悬架系统中。轿车悬架总成作为 轿 车 的 一 个 重 要 的 承 载 部 件 ,传 递 着 车 身 与 路 面 之 间 各 个 方 向 的 作 用 力 ,对 车 辆 的 安 全 性 和 可 靠 性有着重要影响。汽车行驶时有如下 3 种典型 的危险工况: 通过不平路面工况、紧急制动工况、 最小转向半径且不侧滑工况。这些典型危险工 况是汽车扭转梁悬架在使用过程中受力最大的 状态,因此有必要对其进 行 结 构 强 度 分 析,以 确 定扭转梁悬架是否会出现静力破坏的现象。轿 车 在 行 驶 过 程 中 ,扭 转 梁 悬 架 要 受 到 各 种 交 变 载 荷,这种交变载荷一般低 于 材 料 屈 服 极 限,在 这
表 1 悬架各部分材料厚度
部位 纵臂 厚度 /
4 mm
横梁 6
支架 加强板 减振器座 弹簧座 衬套座
13 2. 5
3. 5
3. 5 3
根据钢材的物理特性,其弹性模量 E = 210 GPa, 泊松比 μ = 0. 3,材料密度 ρ = 7 850 kg / m3。材料强 度要求: 屈服极限≥350 MPa; 极限强度≥550 MPa。对 网格单元赋予相应的材料属性,得到网格模型如图 1 所示。
上海汽车 2012. 11
·19·
设计研究
元。为了保 证 计 算 分 析 的 准 确 性,需 要 对 网 格 进 行质量检查,修改不合格的网格,最后得到合格的 网格模型。整个模型的网格数为 23 890 个,其中 quad 4 单元有 22 940 个,tria 3 单元有 950 个。该 扭转梁悬架 由 钢 材 加 工 而 成,各 部 分 材 料 厚 度 如 表 1 所示。
基于汽车正面碰撞的吸能盒设计及优化_雷刚

通过 11 次迭代计算, 得到了大管和小管的最 分别为 2. 15 mm 和 2. 24 mm。 优厚度,
, 因此, 将
波纹管作为吸能盒的最佳选择。 在大波纹管内部 增加一个直径和长度均较小、 材料强度较大、 波纹 管弱的 波 纹 管, 本文设计的吸能盒结构如图 9 所示。
图9
优化模型及吸能盒结构
吸能结构优化方法选择基于优化软件 Hyperstudy 的自适应响应面法。 自适应响应面法是将 响应面模型和试验设计相结合的一种试验方法, 它建立的响应面模型比之传统的响应面方法更精 确、 误差更小
[3 - 4 ]
。
在建立好的子模型中, 用圆形截面的吸能盒 将原吸能盒替换, 得到优化模型。 在此吸能结构 壁厚对整车的耐撞性能有重大的影响。 本文 中, 以大吸能盒厚度、 小吸能盒厚度作为设计变量。 综合整车左右纵梁碰撞过程中的碰撞力, 将 约束条件设为纵梁碰撞最大力小于 194 kN ( 整车 碰撞中纵梁出现的最大碰撞力 ) , 并且吸能盒所吸 收能量要不小于原设计左侧吸能盒所吸收的能量 ( 1. 58 kJ) , 该优化设计问题的数学表达式为 d2 } 设计变量: x = { d1 , 目标函数: max Energy( x) 约束条件: 碰撞力: F ( x) ≤194 000 N 吸能盒吸收能量: E ≥1. 58 kJ 1 . 5 ≤d2 ≤2 . 5 设计变量: 2 ≤d1 ≤3 , 迭代过程如图 10 所示。 将优化 得 到 的 吸 能 盒 结 构 替 换 原 吸 能 盒 结 计算吸能盒在碰撞过程中的吸收能量及纵梁 构, 碰撞力, 与原始结构仿真结果对比如表 1 所示。
doi: 10. 3969 / j. issn. 1674-8425( z) . 2013. 03. 001
- 1、下载文档前请自行甄别文档内容的完整性,平台不提供额外的编辑、内容补充、找答案等附加服务。
- 2、"仅部分预览"的文档,不可在线预览部分如存在完整性等问题,可反馈申请退款(可完整预览的文档不适用该条件!)。
- 3、如文档侵犯您的权益,请联系客服反馈,我们会尽快为您处理(人工客服工作时间:9:00-18:30)。
第25卷 第2期V o l .25 N o .2重庆理工大学学报(自然科学)J o u r n a l o f C h o n g q i n g U n i v e r s i t y o f T e c h n o l o g y (N a t u r a l S c i e n c e )2011年2月F e b .2011 收稿日期:2011-11-20作者简介:雷刚(1968—),男,博士,教授,主要从事计算力学、C A D /C A E 方面研究。
基于D O E 的汽车碰撞优化分析雷 刚1,王希杰1,张 攀2(1.重庆理工大学汽车零部件制造及检测技术教育部重点实验室,重庆 400054;2.澳汰尔工程软件(上海)有限公司,上海 200082)摘 要:建立了整车的有限元模型,对整车模型进行正面碰撞仿真分析,根据国标评价标准对车身加速度等参数进行了分析;在此基础上,提出了用实验设计的方法对汽车安全性进行直观分析、方差分析和显著性分析,得到最优的试验方案。
优化结果表明,相比初始设计方案,优化后的方案明显降低了车身加速度,增强了汽车的耐撞性,为汽车正面碰撞安全设计与改进提供了依据。
关 键 词:汽车正面碰撞;有限元分析;D O E 分析;耐撞性中图分类号:U 491 文献标识码:A文章编号:1674-8425(2011)02-0008-05O p t i m a l A n a l y s i s o f V e h i c l e C r a s hB a s e do nD O EL E I G a n g 1,W A N GX i -j i e 1,Z H A N GP a n2(1.K e y L a b O f M a n u f a c t u r e &T e s t T e c h n i q u e s o f M i n i s t r y o f E d u c a t i o n ,C h o n g q i n g U n i v e r s i t y o f T e c h n o l o g y ,C h o n g q i n g 400054,C h i n a ;2.A l t a i r E n g i n e e r i n g I n c .,S h a n g h a i 200082,C h i n a )A b s t r a c t :I n t h i s p a p e r ,t h e C A Em o d e l o f t h e c a r w a s e s t a b l i s h e d ,a n d t h e f r o n t a l c r a s h s i m u l a t i o n a n a l y s i s a s t h e n a t i o n a l e v a l u a t i o n c r i t e r i o n w a s c o m p l e t e d .T h e s e p a r a m e t e r s i n c r a s h c o u r s e f o r e v a l -u a t i n g s a f e o f v e h i c l e ,s u c h a s a c c e l e r a t i o n s o f c a r b o d y ,w e r e a n a l y z e d .T h e D O Em e t h o d w a s p r o -p o s e d t o s t u d y a u t o m o t i v e s a f e t y b y i n t u i t i v e a n a l y s i s ,a n a l y s i s o f v a r i a n c e a n d s i g n i f i c a n c e a n a l y s i s ,i n o r d e r t o g e t t h e m o s t o p t i m a l t e s t p r o g r a m .T h e r e s u l t s s h o wt h a t t h e a c c e l e r a t i o n o f b o d y h a d b e e n r e d u c e d o b v i o u s l y ,v e h i c l e 's c r a s h w o r t h i n e s s h a d b e e n s t r e n g t h e n e d ,a n d v e h i c l e 's s a f e t y h a d b e e n e n h a n c e d c o m p a r e d w i t h o r i g i n a l p r o g r a m .T h e e f f e c t i v e i n s t r u c t i o n f o r t h e a u t o m o b i l e f r o n t c r a s h s a f e d e s i g n a n d i m p r o v e m e n t h a d b e e n p r o v i d e d .K e y w o r d s :c a r h e a d -o n c o l l i s i o n ;C A Ea n a l y s i s ;D O Ea n a l y s i s ;c r a s h w o r t h i n e s s 汽车碰撞是汽车被动安全研究的主要内容之一,目前在汽车碰撞研究领域中普遍采用的方法为试验方法和计算机仿真方法。
试验方法是一种直接而又客观的设计与验证方法,但试验周期长、费用高、重复性差,并且也不可能采集到足够多的数据,特别是用于产品改进所需的详细数据;计算机仿真具有费用低、周期短、重复性好、结果信息全面等优点。
通过碰撞仿真分析,可以在短期内完成多次改进,为真车碰撞试验提供充分的技术准备[1]。
本文利用有限元软件H y p e r M e s h 建立了整车有限元模型,依照国标G B 11551要求,利用L S -D Y N A 进行了碰撞仿真模拟。
通过模拟分析,对碰撞过程中存在问题的重要部件进行D O E 优化来提高车辆的耐撞性。
1 有限元模型的建立在有限元分析过程中,模型的准确及合理简化具有极其重要的意义。
根据有限元计算的需要和要求,在H y p e r M e s h 中对整车的几何模型进行必要的简化。
最后建立的整车有限元模型如图1所示。
图1 整车有限元模型 整车有限元模型共有37万个单元,其中三角形单元的数量占壳单元总数的4.5%,可以保证模型的计算精度。
2 汽车正面碰撞数值仿真依照G B 11551—2003《乘用车正面碰撞的乘员保护》的要求,对整车施加边界条件[2],用L S -D Y N A 提交求解,求解时间为120m s 。
汽车正面碰撞在80m s 时的变形如图2所示,从图2中可以看出,本车正面变形分布合理,车体保持了较好的完整性,没有出现不合理的变形。
图2 80m s 时的变形 碰撞过程中的总能量曲线变化平稳,基本为一个恒定值。
在沙漏过程中产生的沙漏能很少,沙漏能与内能的比值远小于5%,证明碰撞模拟的结果具有一定的精确性[3]。
车身加速度曲线如图3所示,由图3可知,加速度曲线平滑、没有突变,在34m s 时加速度达到最大值68.9g ,相比同类车型偏大,乘员在碰撞过程中会受到较大伤害,甚至死亡。
图3 车身加速度曲线 G B 115511—2003《乘用车正面碰撞的乘员保护》规定:“碰撞试验后,不使用工具,车门应能开启。
”[2]图4为车门框测点分布,共有10个测点,测点分布均匀且包含了整个车门的几何信息,能完整描述车身变形。
分析图4可知,前门框测点B 、E 间的距离在87m s 时变形最大,为28.52m m ,其他测点间的变形均未超过5m m ,前门框的变形率为9雷 刚,等:基于D O E 的汽车碰撞优化分析28.52/993.7=2.87%,因此前车门在碰撞时能够打开。
由图5可知:车身侧围变形均匀,没有出现畸变的情况,因此车门不会出现卡死的情况[2]。
3 正面碰撞优化分析碰撞中影响乘员响应的主要因素是车体加速度。
加速度越高,乘员头部加速度也会越大,从而H I C 值(乘员头部伤害指标)也越大。
根据分析结果可以看出,汽车正面碰撞时车身加速度峰值达到了68.9g ,相对同类车型明显偏大,必须在不显著增加驾驶室的侵入量的条件下,采取可行的优化方法对车身的结构参数进行调整,以此降低车身的加速度。
综合考虑计算时间和优化效果,本文选用试验设计方法(D O E )对车身的结构参数进行优化调整。
3.1 主要变形吸能结构分析汽车车身结构在正面碰撞中的载荷传递路径较多,如图6,外载荷从汽车前部通过多条路径传递到车身整体。
图6 正面碰撞载荷传递路径 在汽车正面碰撞中,主要的变形吸能结构能否稳定变形、吸收能量,决定了整车的碰撞性能和乘员保护效果。
从图7可以看出,变形截止线以前是设计变形区,要求汽车正面碰撞时变形最好完全发生在该区域,变形截止线以后是乘员舱,是非设计变形区,不允许发生较大变形,否则乘员会因为金属件侵入乘员舱而危害乘员生命[1]。
从图7可以看出,在设计变形区内前保险杠、前纵梁是主要的吸能结构,本文把前保险杠、前纵梁、前纵梁竖直板和前保险杠的结构作为试验设计的4个因素。
图7 汽车前纵梁设计区域3.2 因素水平的选取基于工程实际需要,材料、板厚、结构等都可以被选为设计因素。
考虑到制造成本和实际可行性,选择板厚作为设计水平比较经济适用,同时在不改变整车结构的条件下增加局部部件也是可取的。
在板厚因素水平选择中,最佳水平应该与实际生产中的常用板厚相一致,反之得到的试验结果就没有实际应用价值。
在本次D O E 分析过程中共选择了4个因素,每个因素取3个水平,设计因素水平如表1所示[4]。
10重庆理工大学学报表1 设计因数水平表m m水平因素水平1水平2水平3前纵梁1.21.52前纵梁竖直板11.52保险杠1.21.52保险杠结构无加强件加强板 本次D O E分析工作分2步:首先建立正交试验矩阵L9(34),通过有限元计算分析,找出最佳因素水平组合;对最佳因素水平进行有限元计算,验证D O E分析结果。
3.3 试验分析计算设计一个4因素3水平的标准正交矩阵L9(34),如表2所示,由正交表得到9个试验方案,根据这9个不同水平组合下的设计参数,利用L S-D Y N A依次进行分析,计算得到每个试验的车身加速度。