烟气脱硝技术培训概要.
烟气脱硝技术培训资料
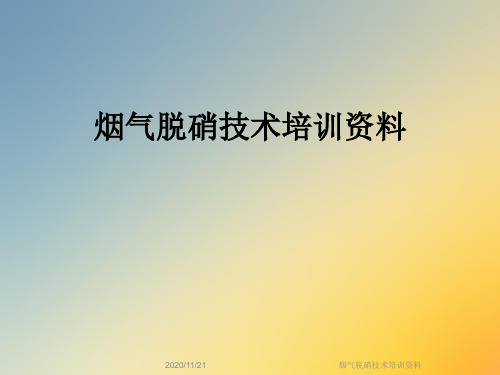
烟气脱硝技术培训资料
3、NOx污染物的产生
§ 快速型NOX:在富燃料燃烧时产生情况,燃煤过程一般不予 考虑。
§ 热力型NOX:在高温燃烧时产生,高于1500℃生成量会比较 多。
§ 燃料型NOX:燃料中固有的氮化合物经过复杂的化学反应后 生成,燃料型NOX 约占整个生成的NOX70~95%。
§ 氮氧化物排放的经验值:
老燃煤电厂无低氮燃烧器 900~1000mg/Nm3;
新建电厂有低氮燃烧器 于500mg/Nm3。
550~500mg/Nm3,有时候可以低
烟气脱硝技术培训资料
4、中国燃煤电厂NOx排放标准燃煤电站锅炉 氮氧化物排放标准GB13223-2003(单位:mg/m3)
燃煤 锅炉
烟气脱硝技术培训资料
High Dust 高灰分
Low Dust 低灰分
Tail End 尾端
SCR Configuration Options
SCR 的布置
3
NH
Boiler
锅炉
SCR
ESP 静电过滤器
FGD 烟气去硫
Boiler
Air空气
Air Heater
空气预热器
NH
3
Hot-Side ESP 静电过滤器热端
烟气脱硝技术培训资料
6、SCR/SNCR联用脱硝工艺
§ 为了克服SCR和SNCR这两种方法的缺点,提出了SCR/SNCR联用 技术,即在高温区使用SNCR法,在炉膛内喷入还原剂将NOx还 原;在尾部烟道中安装SCR反应器。
§ SNCR/SCR混合法可利用逃逸的氨作为后部SCR的还原剂,从而 可使其脱硝效率逐步升级最终可达到70%以上。
脱硝系统培训

脱硝系统培训
编写人:艾合买提
独山子石化公司炼油厂催化车间
脱硝原理 流程介绍 主要设备说明 氨的性质及危害
一、脱硝原理
再生烟气脱硝系统采用选择性催化还原工艺(SCR),是 引进奥地利STRABAG公司的SCR技术及催化剂的管理等 技术 。其原理是在催化剂作用下,选择性的与烟气中 NOX的还原反应,生成N2和H2O,发生的主要反应为: 4NO+4NH3+O2 → 4N2+6H2O NO+NO2+2NH3 → 4N2+3H2O SCR法由于还原反应温度要求低,运行温度范围为 250~420℃,具有对炉膛影响小、脱硝效率高、氨逃逸率 低等特点 ,SCR法在工业上得到了广泛应用。
二、流程介绍
1.液氨供应
还原剂液氨由炼油厂工业水车间供应,设液氨储罐 1台,容积15m3,设计压力为1.9MPa。储罐四周安装有工 业水喷淋管线及喷嘴,当罐体温度过高时自动淋水装置 启动,对罐体自动喷淋降温;当有微量氨气泄漏时也可 启动自动喷淋装置,对氨气进行吸收,控制氨气污染。 液氨储罐内的液氨通过液氨泵送至液氨蒸发器。
号:
旁通泵,水平的,磁力耦合器。
最大流量: 200 kg/h
输送压头: 0.3 MPa
入口压力: < 1.45 MPa
设计压力: 2.5 MPa
材质:
碳钢
马达:
1.1 kW
保护等级: Ex II A T1
6. 废液泵
液氨储存和供应系统的氨排放管路为一个封闭系统,由氨气稀释罐吸收成 氨废水后排放至废水池,通过废液泵输送到工厂含油污水地下管网系统( 含硫污水系统)。
2.氨液蒸发
液氨蒸发器为专利设备,集成式液 氨蒸发器将液氨的蒸发器和缓冲罐 集成为一体。液氨蒸发所需要的热 量采用低压蒸汽加热来提供。蒸发 器上装有压力控制阀将氨气压力控 制在一定范围,当出口压力过高时 ,则切断液氨进料。在氨气出口管 线上也装有温度检测器,当温度过 低时切断液氨,使氨气至缓冲槽维 持适当温度及压力,蒸发器也应装 有安全阀,可防止设备压力异常过 高,水浴温度为70℃~90℃ 。
脱硝基础知识培训

常规燃煤电厂SCR系统:低含尘布置
高含尘布置 是催化剂活性最佳的温度区间。 尘对催化剂的冲刷和活性降低影响大,催化剂工作寿命一般为2~3年 。 SO对脱硝有影响。 低含尘布置 提高催化剂的工作寿命,可达到3~5年。 需要外界提供大量的加热能量,系统复杂,增加了能耗和运行成本。
脱硝反应器:
催化剂的安装及更换:
催化剂使用管理曲线:
★目前国外SCR中催化反应塔 清灰方式主要分为蒸汽吹灰和声波吹灰。 ★ 蒸汽吹灰: 清灰彻底,能有效清除积灰。 但消耗蒸汽量大,机械维护量大 ,运行费用高,操作不当,可能 造成烟气过湿,造成粘灰和腐蚀。
催化剂吹灰系统:
★ 声波吹灰器:是通过声波发生器将压缩空气调制成高强声波,声波在塔内空间里传播,引起催化剂表面积灰粒子循环往复的振动,对灰粒之间及管壁之间的结合力起到减弱和破坏的作用,同时在灰粒本身重量或烟气冲刷力作用下,不能连续沉积,同时部分被烟气带走。 ★ 优点是投资低,运行费用低,但不能有效地移除积灰,只能防止粉尘沉积。
3、SCR脱硝技术的发展史:
4、SCR反应原理图:
间接化学反应及副作用
★ 当烟气温度超过规定值(430℃)时,易发生氨氧化反应,并增加NO的浓度和减少有效NH3的量,而且催化剂易烧结失去活性。 ★ 在催化剂活性物质钒的作用下,烟气中的SO2在高温和氧气作用下一部分被氧化成SO3,称之为SO2/SO3转化率,该值一般被控制在1.0~1.5%,其高低与烟温、催化剂特性、含氧量、SO2浓度有关。 ★ 由于运行SCR时,烟气中SO3浓度升高,在低温(≤320℃)条件下,易生成硫酸氨和硫酸氢氨,将会在催化剂和下游设备上沉积腐蚀;
3、对锅炉钢结构的影响 装设SCR装置的锅炉,支撑SCR装置的钢架通常是与锅炉钢架为同一联合体系,不论SCR装置布置在锅炉钢架内或外,锅炉钢架均要承受一定的荷载。改造机组必须校核钢支架强度。 4、对锅炉炉膛承压设计的影响 由于装设了SCR装置后,600MW机组烟气侧阻力要增加1000Pa左右,引风机的风压会相应提高,因此,要对炉膛的承压设计进行核算。
脱硝工培训计划

脱硝工培训计划一、培训目标本培训计划旨在培养脱硝工队伍的专业技能和岗位素质,提高员工对脱硝工作的理论认识和实际操作能力,使其具备独立进行脱硝工作的能力,提高企业的生产效益和环境保护水平。
二、培训对象脱硝工培训适用于所有从事脱硝工作的员工,包括初级、中级和高级脱硝工,覆盖脱硝设备操作、维护与管理等方面。
三、培训内容1. 脱硝技术原理- 总述脱硝工作原理- 介绍脱硝技术的发展现状- 脱硝技术在环保产业中的地位和作用2. 脱硝设备操作- 脱硝设备的结构和工作原理- 脱硝设备的操作规程- 脱硝设备的维护和保养3. 脱硝废水处理- 脱硝过程中废水的处理方法- 废水处理设备的操作和维护4. 脱硝工作安全- 脱硝作业环境的安全防护- 脱硝作业中的危险与防范- 突发情况的处理和应急措施5. 脱硝工作质量管理- 掌握脱硝工作中的质量标准- 了解相关质量控制技术及方法- 发现和处理脱硝工作中的质量问题6. 脱硝行业法律法规- 脱硝相关法律法规的基本要求- 脱硝作业过程中的法律风险与合规措施以上为脱硝工培训的主要内容,针对不同岗位的员工还要适当有所区别,培训时间为3天。
四、培训方法1. 理论教学采用讲授、问答、小组讨论等形式,传授脱硝技术原理、操作规程、废水处理等一系列理论知识。
2. 案例分析通过案例分析,引导员工了解脱硝工作中的典型问题和解决方法,提升员工的应变能力。
3. 演练实践对脱硝设备的操作规程和维护方法进行现场演练,让员工亲身实践,加深对操作技能的掌握。
4. 考核评估通过考核测试,对员工的学习情况进行评估,确保培训效果。
五、培训考核1. 考核方式采用理论考核和实操考核相结合的方式,对员工的学习情况、操作技能和质量管理能力进行全面考核。
2. 考核内容- 脱硝技术理论知识考试- 对脱硝设备进行操作和维护的实操考核- 应对突发情况的模拟演练考核3. 考核标准根据公司制定的脱硝工作标准和质量要求进行考核,达到合格标准者方可通过培训。
脱硝SCR知识培训

一、供氨与注氨系统
贮存在液氨罐的高纯液氨经气化器加热后,由液态氨转为气态 氨,通过供氨管路送至催化剂反应器前的喷氨汇流排上,最后 由喷氨格栅均匀地注入反应器前的烟道。 由于氨的爆炸极限15~28%(在空气中的体积比),为保证安全 和分布均匀,氨气注入烟道前由稀释风机提供空气并进行体积 浓度稀释,实现氨气与空气的混合比为低于5%。 二、催化反应系统 注入烟道后的氨气随烟气气流自上而下垂直进入SCR脱硝反应 器,在280~400℃的温度条件下及催化剂的作用下,将烟气中 的NOx催化降解为无害的N2和H2O。
反应生成NO,NO 在大气中被氧化成毒性更大的NO2。
这种燃料中的氮化合物经热分解和氧化反应而生成的NO 称为燃料型NOx。。煤燃烧产生的NOx,其中 75~90%是燃料型NOx。
(二)热力型NOx
热力型NOx 是指空气中的N2 与O2 在高温条件下反应 生成的NOx。以煤粉炉为例,在燃烧温度为1350℃时, 几乎100%是燃料型NOx,但当温度为1600℃时,除 了反应温度对热力型NOx的生成有决定性影响外,还和 N2 浓度以及停留时间有关。过量空气系数和烟气停留时 间对热力型NOx的生成有很大影响。 (三)快速型NOx
喷头发生堵塞时进行吹扫。在氨气进装置分管阀后设有氮
气预留阀及接口,在停工检修时用于吹扫管内氨气。SCR 内设置吹灰器,吹扫介质为蒸汽,吹扫频率根据SCR压差
决定。
工艺参数
一、入口NOx 浓度 由于各种组分(包括NOx、NH3)在烟气中分布并不均匀,以下所 说的组分浓度均为平均浓度。对于特定的锅炉,SCR反应器入 口烟气NOx浓度受锅炉运行条件的影响,煤质变化、锅炉负荷 变化、燃烧条件(如配风方式、过剩空气量等)的变化都会使反 应器入口烟气NOx浓度发生变化。 二、脱硝率 SCR反应器出口烟气NOx浓度(或脱硝效率)一般根据环保法规 (排放限值、排污收费)通过技术经济比较来选择。脱硝率定义 为反应器进口前的NOx浓度扣除反应器出口后的NOx浓度,再 除以反应器进口前的NOx浓度的比值,它直接反映了烟气中氮 氧化物的脱除效率。
电厂烟气脱硫脱硝技术(培训)
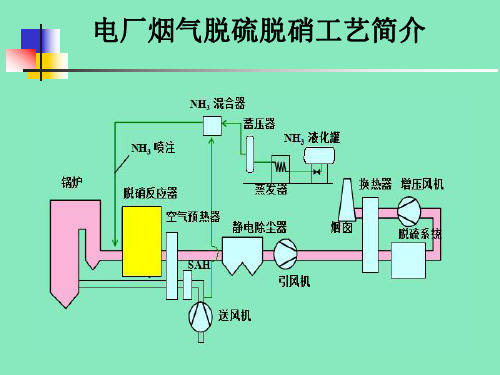
CO2 (aq) CO2 (g )
在有氧气存在时,HSO3-的氧化:
HSO3
1 2
O2
H
SO42
CaSO3和CaSO4的结晶:
Ca 2
SO32
K SP1
CaSO3
1 2
H 2O(s)
H SO42 HSO4
Ca2
SO4 2
K SP2
CaSO4
2H2O(s)
(2)典型工艺流程 石灰石—石膏湿法FGD系统图
电厂烟气脱硫脱硝工艺简介
第一部分 烟气脱硫技术
一、燃煤产生的污染 二、烟气排放标准 三、烟气脱硫技术概况 n 湿法烟气脱硫技术(WFGD技术) n 半干法烟气脱硫技术(SDFGD技术)
旋转喷雾干燥法 烟气循环流化床法脱硫 增湿灰循环脱硫(NID)
n 干法烟气脱硫技术(DFGD技术)
炉膛干粉喷射 高能电子活化氧化法(EBA) 荷电干粉喷射(CDSI)
脉冲悬浮系统
● 石膏脱水系统---石膏旋流站 ◇ 石膏进浆浓度8-15%;
◇ 底流浓度45-60%。
石膏旋流站
E2.美国巴威公司
美国巴威公司(B&W)成立于1867年。巴威公司已有 40000MW以上的脱硫业绩,所有项目都达到性能需要,还成 功地改造了多座竞争对手的脱硫塔。
二、烟气排放标准
n GB 13223-2011最新《火电厂大气污染物排放标准》, 见附件一
n 史上最严厉的排放标准: 2012年1月1日之前的锅炉,在2014年7月1日起
n SO2 200mg/m3(2012年1月1日锅炉:100mg/m3) n NO2 100mg/m3(比美国现行标准低35mg/m3,甚
(2)吸收剂耗量低,钙硫比≤1.03; (3)石膏品位高,含水率≤10%。
脱硝培训计划书

脱硝培训计划书一、培训目的1.提升员工的环保意识,推广脱硝技术应用,减少环境污染。
2.提高员工对脱硝技术的了解与掌握,提高脱硝操作技能。
3.培养员工的安全意识,确保脱硝过程中的安全生产。
二、培训对象全体参与脱硝工作的员工,包括现场操作人员、技术人员、管理人员等。
三、培训内容1.脱硝基础知识:(1)脱硝原理与技术介绍(2)脱硝设备与工艺流程2.脱硝操作技能:(1)脱硝设备的操作流程(2)脱硝设备维护与保养3.脱硝安全意识培训:(1)脱硝过程中的安全措施(2)脱硝事故应急处理四、培训方法1.理论讲解:由技术专家就脱硝基础知识进行系统讲解。
2.实践操作:现场模拟脱硝操作,由经验丰富的技术人员指导。
3.案例分析:通过案例分析,让员工更好地理解脱硝工作中可能出现的问题及应对方法。
4.互动讨论:组织员工进行互动讨论,分享工作中的经验与技巧。
五、培训计划1.培训时间:本次培训计划为期两周,每周安排为3天培训,每天8小时。
2.培训地点:公司内部培训室与现场操作模拟区。
3.培训安排:根据员工的实际工作情况,合理安排培训时间,最大程度地避免影响生产。
4.培训评估:每周培训结束后进行培训效果评估,根据评估结果及时调整培训方式与内容。
六、培训考核1.理论考核:对员工进行脱硝基础知识与操作技能的笔试考核。
2.实际操作考核:对员工进行现场模拟脱硝操作的实际考核。
七、培训后续1.定期跟踪:培训结束后,定期进行员工脱硝工作的跟踪调研,及时发现问题并加以解决。
2.持续改进:根据培训效果与员工反馈,不断改进培训内容与方式,提高培训质量与效果。
以上即为本次脱硝培训计划书,希望通过本次培训,能够有效提高员工的环保意识与脱硝技术素养,从而推动公司脱硝工作的全面推进。
火电厂脱硝培训

火电厂锅炉烟气脱硝处理技术简介目前,各主要工业发达国家用来控制电站锅炉(NO X)氮氧化物排放技术可以分为三大类,使用低氮燃料、低NO X燃烧技术、烟气脱硝。
低氮燃料提高了电厂的运行成本,对煤源要求高,不易实现。
低NO X燃烧控制主要是抑制和减少锅炉燃烧过程中的NO X的产生,有以下几种形式:低氧燃烧/排气循环燃烧、注入水蒸汽或水、二级燃烧、浓淡燃烧、分段燃烧、降低空气比等。
其中效果最好的是二级燃烧和浓淡燃烧。
燃烧控制能减少20%~50%的NO X生成,技术简单,不占地,费用较低。
但是进一步提高NO X的脱除率很难,不能满足环保标准的要求,而且低NO X燃烧通常伴随的是燃烧效率降低,不完全燃烧损失增加,煤耗增加。
同时会使飞灰特性发生变化,影响灰渣的凝硬性及烧损量,给电厂灰渣的综合利用带来影响。
要进一步降低烟气中的NO X浓度,当前脱硝最有效、技术最成熟的方法就是燃烧后控制—即烟气脱硝。
1 常用的脱硝方法及原理(SCR)常用的SCR技术是在金属催化剂的作用下,以NH3作为还原剂,将NO X还原成N2和H2O。
NH3不和烟气中的残余O2反应。
还原剂NH3由液态氨经稀释后得到,液态氨又叫无水氨,国内工业液态氨质量标准为NH3>99.8%,H2O>0.2%。
液态氨的沸点为-33.33℃,密度为0.617(氨气的密度为0.588),液态氨自燃起火温度为651℃。
液态氨在常温下能够迅速气化,在15.6℃,每千克液态氨能够膨胀为1.36立方米的氨蒸汽。
氨气在常温、常压下为气体,需要在高压容器内才能使其保持液态。
液态氨属于有毒易爆物质,要注意防爆、防毒等安全问题。
氨气在空气中浓度超过17%,遇有明火就会发生爆炸。
因此在液态氨的贮存、运输、使用等过程中,必须严格遵守操作规程,防止意外事故的发生。
2 主要反应方程式化学反应式:4NH3+4NO+O2=4N2+6H2O4NH3+NO2+O2=3N2+6H2O温度一般在200~400℃下反应,效率80%~90%,3 烟气脱硝系统结构脱硝系统主要由四部分组成:除灰系统、供氨系统、催化反应器及控制系统等四部分组成。
- 1、下载文档前请自行甄别文档内容的完整性,平台不提供额外的编辑、内容补充、找答案等附加服务。
- 2、"仅部分预览"的文档,不可在线预览部分如存在完整性等问题,可反馈申请退款(可完整预览的文档不适用该条件!)。
- 3、如文档侵犯您的权益,请联系客服反馈,我们会尽快为您处理(人工客服工作时间:9:00-18:30)。
烟气脱硝技术培训概要第一节低NOx燃烧技术据统计,目前人为排放的NOx90%以上来自于矿物燃料的燃烧过程,如煤、石油、天然气等等。
随着人类生产活动和社会活动的增加,特别是自工业革命以来,由于大量燃料的燃烧、工业废气和汽车尾气的排放,使大气环境质量日益恶化,到现在已是非治不可。
在各类大气污染物中,燃煤产生的污染最为严重,属不清洁能源。
燃煤产生的SO2和NOx污染控制是目前我国大气污染控制领域最紧迫的任务。
国外发达国家早已把对NOx的控制放到防治酸雨的首位,纷纷制定严格的火电厂NOx排放浓度标准(如欧盟的NOx 排放浓度标准为200~400mg/ m3)。
我国火电工业每年耗煤近5.3亿吨,环保压力非常巨大。
2004年国家新的大气排放标准实施后,对火电厂氮氧化物排放要求有了大幅度的提高,制定了火电厂NOx排放浓度标准(分为三个时段),NOx排污收费标准为0.63元/kg。
一.燃烧过程中NOx的生成机理“热力”NOx——氮气氧化N2+O2=2NONO+1/2O2=NO2影响“热力”NOx的主要因素是温度、氧气浓度和停留时间。
“快速”NOx——碳化氢燃料过浓时燃烧在温度低于2000K时,NOx的形成主要通过CH-N2反应,即“快速”NOx途径。
当温度升高,“热力”NOx比重增加。
影响“热力”NOx的主要因素是CH原子团的浓度及其形成过程、N2分子反应生成氮化物的速率、氮化物间相互转化率。
通常情况下,在不含N的CH燃料低温燃烧时,才重点考虑“快速”NOx。
与“热力”NOx和“燃料”NOx相比,它的生成要少得多。
“燃料”NOx——燃烧时有机物中的原子N分解出来并生成NOx燃料氮转化成NOx的量主要取决于空燃比,较少依赖于反应温度。
当燃料中氮的含量超过重量的0.1%时,化学地结合在燃料中的N转化成NOx的量就越来越占主要地位。
煤、重油和其它高N燃料,“燃料”NOx的形成是主要的。
(4)煤燃烧过程中NOx的生成煤粉燃烧过程中生成的NOx大部分是“燃料”NOx。
煤中的N 生成NOx是通过挥发分中N的气相氧化和碳中的N多项氧化两个途径。
煤中的N在挥发分中和在碳中的比例与热解速度有关。
温度低时,绝大部分N留在碳中;温度高时,70%~90%的氮在挥发分中,此时“燃料”NOx主要来自挥发分中的氮。
一些研究数据表明,在贫燃料燃烧时挥发N生成NOx中的57%~61%,而在富燃料时,这个比例迅速降低,使碳中N的多相氧化成为NOx的主要来源。
挥发分N向NOx的转化对于空燃比很敏感,通过合理调节燃烧过程形成富燃料区,可以大大减少这种转化。
基于以上特点,减少燃煤生成的NOx,主要是设法建立富燃料区,使燃料N在其中尽可能多地挥发,在贫氧、富燃料条件下使易氧化的燃料N转化为稳定无害的N2。
二.低NOx燃烧技术低NOx燃烧控制主要是抑制和减少锅炉燃烧过程中的NOx的产生,有以下几种形式:低氧燃烧、排气循环燃烧、注入水蒸气或水、二级燃烧、浓淡燃烧、分段燃烧、降低空气比等。
其中效果最好的是二级燃烧和浓淡燃烧。
燃烧控制能减少20%~50%的NOx生成,技术简单,不占地,费用较低。
但是进一步提高NOx的脱除率很难,不能满足环保标准的提高,而且低NOx燃烧通常伴随的是燃烧效率降低,不完全燃烧损失增加,煤耗增加。
同时会使飞灰特性发生变化,影响灰渣的凝硬性及烧失量,给电厂灰渣的综合利用带来影响。
要进一步降低烟气中NOx的浓度,当前脱硝最有效、技术最成熟的方法就是燃烧后控制即烟气脱硝。
第二节选择性催化还原烟气脱硝技术选择性催化还原(SCR)烟气脱硝技术,是20世纪80年代初开始逐渐应用于燃煤锅炉烟气脱除NOx,是目前世界上应用最多而且最有成效的烟气脱硝技术。
一.SCR工艺流程和过程化学(一)S CR工艺流程选择性催化还原是基于在催化剂的作用下,喷入的氨把烟气中的NOx还原成N2和H2O。
还原剂以氨为主。
催化剂有板式和蜂窝式两类。
SCR反应器臵于锅炉之后,如下图所示。
高粉尘低粉尘尾部设臵第一种布臵的优点是进入反应器烟气的温度达到300~400℃,多数催化剂在此温度范围内有足够的活性,烟气不需要加热可获得好的NOx脱除效果。
但催化剂处于高尘烟气中,寿命会受下列因素影响:(1)飞灰中K、Na、Ca、Si、As会使催化剂污染或中毒;(2)飞灰磨损反应器并使蜂窝状催化剂堵塞;(3)烟气温度过高会使催化剂烧结或失效。
第二种布臵的优点是催化剂不受飞灰的影响。
但需高温电除尘器。
第三种布臵若SCR反应器臵于湿式FGD系统之后,催化剂既不受飞灰的影响,也不受SO3等气态毒物的影响,但由于烟温较低,一般需用气-气换热器或采用燃料气燃烧的方法将烟气温度提高到催化还原反应所必须的温度。
在工业应用中常常采用第一种布臵。
整个SCR烟气脱硝系统分为两大部分,即SCR反应器系统(反应器、催化剂、氨喷射器等)和液氨存储及供应系统(氨压缩机、液氨储罐、蒸发器、缓冲罐、稀释槽等)。
SCR系统设臵分有烟气旁路和没有烟气旁路两种。
如有旁路,SCR反应器中烟气的温度可通过调节经过省煤器的烟气与通过旁路烟气的比例来控制。
氨喷射器(AIG)的安装位臵在SCR反应器的上部以保证喷入的氨与烟气充分混合。
(二)S CR过程化学SCR的化学反应机理比较复杂,但主要的反应是NH3在一定的温度和催化剂的作用下,有选择地把烟气中的NOx还原为N2。
4NH3+4NO+O2─>4N2+6H2O (A)4NH3+2NO2+O2─>3N2+6H2O (B)上面第一个反应是主要的,因为烟气中几乎95%的NOx是以NO的形式存在的。
在没有催化剂的情况下,上述化学反应只在很窄的温度范围内(980℃左右)进行,即选择性非催化还原(SNCR)。
通过选择合适的催化剂,反应温度可以降低,并且可以扩展到适合电厂实际使用的290~430℃范围。
催化剂中最常用的金属基含有氧化钒、氧化钛。
在反应条件改变时,还可能发生以下副反应:4NH3+3O2─>2N2+6H2O (1)2NH3─>N2+3H2 (2)4NH3+5O2─>4NO+6H2O (3)发生NH3分解的反应式(2)和NH3氧化为NO的反应式(3)都在350℃以上才进行,450℃以上才激烈起来。
在一般的选择性催化还原工艺中,反应温度常控制在300~400℃,因此NH3氧化为N2的副反应式(1)很难发生。
NH3和NOx在催化剂上反应的主要过程为:1. NH3通过气相扩散到催化剂表面;2. NH3由外表面向催化剂孔内扩散;3. NH3吸附在活性中心上;4. NOx从气相扩散到吸附态NH3表面;5. NH3和NOx反应生成N2和H2O;6. N2和H2O通过微孔扩散到催化剂表面;7. N2和H2O扩散到气相主体。
由上述反应过程可知,反应式(A)和式(B)主要是在催化剂表面进行的,催化剂的外表面积和微孔特性很大程度上决定了催化剂的反应活性,上述7个步骤中,速度最慢的为控制步骤。
二.SCR脱硝效率的主要影响因素在SCR脱硝工艺中,影响脱硝效率的主要因素是反应温度、反应时间、催化剂性能、NH3/NOx摩尔比等。
(一)反应温度的影响低温催化剂中温催化剂脱硝率(%) 催化剂厚度反应温度( C)反应温度对脱硝率有较大的影响。
在300~400℃范围内(对中温触媒),随着反应温度的升高,脱硝率逐渐增加,升至400℃时,达到最大值(90%),随后脱硝率随温度的升高而下降。
在SCR过程中温度的影响存在两种趋势,一方面是温度升高是脱硝反应速率增加,脱硝率升高;另一方面温度的升高NH3氧化反应开始发生,使脱硝率下降。
因此,最佳温度是这两种趋势对立统一的结果。
(二)N H3/NOx摩尔比对脱硝率的影响脱硝率(%)在310℃下,脱硝率随NH3/NOx摩尔比的增加而增加,NH3/NOx摩尔比小于0.8使,其影响更明显,几乎呈线形正比关系。
该结果说明若NH3投入量偏低,脱硝率受到限制;若NH3投入量超过需要量,NH3氧化等副反应的反应速率将增大,从而降低脱硝率,同时也增加了净化气中未转化NH3的排放浓度,造成二次污染。
(三)接触时间对脱硝率的影响在310℃下和NH3/NOx摩尔比为1的条件下,脱硝率随反应气与催化剂的接触时间t的增加而迅速增加,t增至200ms左右时,脱硝率达到最大值,随后脱硝率下降。
这主要是由于反应气体与催化剂的接触时间增加,有利于反应气体在催化剂微孔内的扩散、吸附、反应和产物气的解吸、扩散,从而使脱硝率提高。
但是,若接触时间过大,NH3氧化反应开始发生,使脱硝率下降。
(四)催化剂中V2O5含量对脱硝率的影响催化剂中V2O5含量的增加,催化效率增加,脱硝率提高,但是,V2O5含量超过6.6%时,催化效率反而下降,这主要由于V2O5在载体TiO2上的分布不同造成的。
当V2O5含量在1.4%~4.5%时,V2O5均匀分布于TiO2载体上,并且以等轴聚合的V基形式存在;当V2O5含量为6.6%时,V2O5在载体TiO2上形成新的结晶区——V2O5结晶区,从而降低了催化剂的活性。
三.SCR催化反应器的设计催化剂和反应器是SCR系统的主要部分。
几乎所有的催化剂都含有少量的氧化钒和氧化钛,因为它们具有较高的抗SO3的能力。
催化剂的结构、形状随它的使用环境而变化。
为避免被颗粒堵塞,蜂窝状、板式催化剂部件都是常用的结构,而最常用的是蜂窝状,因为它不仅强度好,而且容易清理。
为了使被飞灰堵塞的可能性减到最小,反应器都要垂直放臵,并使烟气由上而下流动。
此外,还可用吹灰器来防止颗粒的堆积。
SCR系统的性能主要由催化剂的质量和反应条件所决定。
在SCR反应器中催化剂体积越大,脱硝率越高同时氨的逃逸率也越低,然而SCR工艺的费用也会显著增加,因此,在SCR系统的优化设计中,催化剂体积是一个很重要的参数。
在给定脱硝率和氨逃逸率的情况下,所需的催化剂的体积是由NOx的入口浓度所确定的;而当NOx 的入口浓度和氨逃逸率一定时,所需的催化剂的体积则依赖于系统所需要的脱硝率。
催化剂的体积也取决于催化剂的可靠寿命,因为催化剂的寿命受很多不利因素的影响,如中毒和固体物的沉积。
对SCR系统进行优化设计则需考虑在催化反应器的入口处合理分布烟气和氨。
研究表明导流板、混合器、氨喷射器和烟道等对SCR系统产生影响。
在最初的催化剂体积的设计中也应考虑适当放大催化剂的量,同时还要考虑反应器中有效区域的变化。
研究发现反应器中有些部位的温度常偏离设计温度从而导致脱硝率的改变,因此,催化反应器的设计通常在平均温度值的±15℃范围内进行,气流的入口装臵应设计可使烟气各断面上相等。
催化反应器的设计还要考虑气流的不均衡的扩散速度。
对一个给定的脱硝率来说,NH3/NOx摩尔比不应超过理论值的±5%以上。