Board and system level effects on plastic package thermal performance
Synopsys RTL Architect
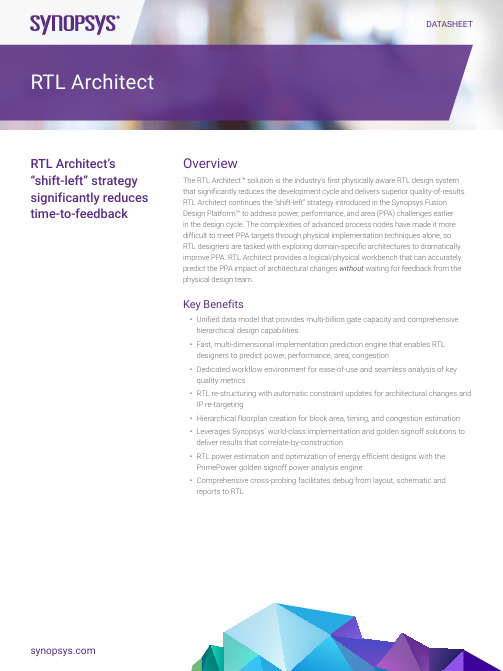
DATASHEET OverviewThe RTL Architect™ solution is the industry’s first physically aware RTL design system that significantly reduces the development cycle and delivers superior quality-of-results. RTL Architect continues the “shift-left” strategy introduced in the Synopsys Fusion Design Platform™ to address power, performance, and area (PPA) challenges earlierin the design cycle. The complexities of advanced process nodes have made it more difficult to meet PPA targets through physical implementation techniques alone, so RTL designers are tasked with exploring domain-specific architectures to dramatically improve PPA. RTL Architect provides a logical/physical workbench that can accurately predict the PPA impact of architectural changes without waiting for feedback from the physical design team.Key Benefits• Unified data model that provides multi-billion gate capacity and comprehensive hierarchical design capabilities• Fast, multi-dimensional implementation prediction engine that enables RTLdesigners to predict power, performance, area, congestion• Dedicated workflow environment for ease-of-use and seamless analysis of key quality metrics• RTL re-structuring with automatic constraint updates for architectural changes and IP re-targeting• Hierarchical floorplan creation for block area, timing, and congestion estimation • Leverages Synopsys’ world-class implementation and golden signoff solutions to deliver results that correlate-by-construction• RTL power estimation and optimization of energy efficient designs with thePrimePower golden signoff power analysis engine• Comprehensive cross-probing facilitates debug from layout, schematic andreports to RTLRTL Architect’s “shift-left” strategy significantly reduces time-to-feedback RTL Architect2Predictive ModelingRTL Architect’s new Predictive Engine (PE) is derived from Synopsys’ implementation environment and enables rapid multi-dimensional analysis and optimization of RTL to predict PPA of downstream implementation accurately. This Predictive Engine utilizes new correct-by-construction modeling, leveraging the proven and widely used core implementation algorithms and architectures of the Synopsys Fusion Design Platform. This ensures tight correlation to the best implementation.This also allows the RTL designers to experiment and tune their HDL code without multiple, back-and-forth, hand-offs to synthesis and to pinpoint timing bottlenecks in their source code to improve RTL quality.Design PlanningRTL Architect’s hierarchical, design planning, infrastructure automatically generates a physical implementation, with clock trees, to provide the RTL designer with accurate power, timing and area estimates. Additionally, the RTL block integrator can use the design planning capabilities to integrate in-house and third-party IP (as seen in Figure 1 Arteris ® IP FlexNoC ® Interconnect Integration) including bus and pipeline register planning. This fast and deep look-ahead allows the designers to not only predict but also drivephysical implementation.Figure 1: Arteris IP FlexNoC Interconnect IntegrationRTL Design ExperienceThe RTL Architect experience is built around the RTL designer. The PE maps leaf cells back to the RTL so that the designer can see the direct impact a code change has on PPA. Figure 2 RTL Cross-Probing, shows the cross-probing capability from various design views to RTL. Color coded reports indicate severity level.Layout viewRTL Architect Unified GUI EnvironmentRTL view view viewFigure 2: RTL Cross-Probing©2020 Synopsys, Inc. All rights reserved. Synopsys is a trademark of Synopsys, Inc. in the United States and other countries. A list of Synopsys trademarks isavailable at /copyright .html . All other names mentioned herein are trademarks or registered trademarks of their respective owners.02/28/20.CS469885535_RTL Architect_DS.For example, the designer can see how the logic is physically implemented by cross-probing from a report directly to the layout. This is useful for seeing the predicted congestion hotspots caused by RTL, so they can experiment with different architectures to reduce the congestion. Figure 3 shows the high degree of correlation between the place and route engines of RTL Architect and Fusion Compiler™.Fusion CompilerRTL Architect Figure 3: RTL Architect vs. Fusion Compiler CongestionAnother key concern for RTL designers is power usage. The interactive power summary report provides an overview of key power metrics, such as, switching and glitch power, leakage, and clock gating efficiency. The results are based on the PrimePower golden signoff power analysis engine. The report data can be sorted, filtered and cross-probed to RTL.Bridging the GapRTL Architect significantly improves the quality of RTL before handing off to implementation. It addresses the limitations of the existing solutions which are hampered by inaccuracies that impact productivity as downstream implementation tools compensate. The shift-left strategy identifies and corrects physical implementation issues early in the design cycle to achieve aggressive PPA targets at advanced nodes through better RTL.。
考研英语作文范文真题

考研英语作文范文真题The Graduate Record Examinations GRE is a standardized test widely used for graduate school admissions in various fields including business education and social sciences. The Analytical Writing section of the GRE assesses the testtakers ability to articulate and support complex ideas clearly and effectively. Below is a sample essay that addresses a GRE Analytical Writing prompt.Title The Role of Technology in Modern EducationIntroductionThe integration of technology in education has been a topic of debate for years. While some argue that it enhances learning experiences others believe it detracts from the value of traditional teaching methods. This essay will explore the various ways in which technology has transformed the educational landscape and evaluate its overall impact on modern education.Body Paragraph 1 Enhancing Learning ExperiencesTechnology has introduced a plethora of tools that have enriched the learning process. Interactive whiteboards for instance allow teachers to engage students in a more dynamic way making lessons more interactive and visually appealing. Moreover educational software and applications have made it possible for students to learn at their own pace catering to individual learning styles and needs.Body Paragraph 2 Access to Diverse Learning ResourcesThe internet has opened up a world of information to students providing them with access to a wealth of knowledge that was previously inaccessible. Online databases ebooks and academic journals are just a few examples of the resources that students can now tap into to deepen their understanding of various subjects.Body Paragraph 3 Challenges and LimitationsDespite the numerous benefits the reliance on technology in education also presents certain challenges. One such challenge is the digital divide where students from underprivileged backgrounds may not have the same access to technological resources as their more affluent peers. Additionally an overreliance on technology can lead to a decrease in critical thinking skills as students may become overly dependent on searchengines and other digital shortcuts.Body Paragraph 4 Balancing Traditional and Modern MethodsTo maximize the benefits of technology in education it is crucial to strike a balance between traditional teaching methods and modern tools. Teachers should use technology as a supplement to their lessons rather than a replacement for direct instruction and facetoface interaction. This approach ensures that students not only benefit from the convenience and resources provided by technology but also develop essential skills such as critical thinking problemsolving and effective communication.ConclusionIn conclusion technology has undoubtedly revolutionized the field of education offering numerous advantages that enhance the learning experience. However it is important to recognize and address the challenges that come with this transformation. By integrating technology thoughtfully and purposefully we can ensure that it serves as a valuable tool in the pursuit of knowledge and personal growth.This sample essay provides a balanced view of the role of technology in education discussing both its benefits and potential drawbacks. It is structured with a clear introduction body paragraphs that explore different aspects of the topic and a conclusion that summarizes the main points. This structure is typical for GRE Analytical Writing essays which require a wellorganized and coherent response to the prompt.。
集成电路的通用单粒子效应测试系统设计

第19卷 第2期太赫兹科学与电子信息学报Vo1.19,No.2 2021年4月 Journal of Terahertz Science and Electronic Information Technology Apr.,2021 文章编号:2095-4980(2021)02-0347-06集成电路的通用单粒子效应测试系统设计杨婉婉1a,1b,刘海南1a,1b,高见头1a,1b,罗家俊1a,1b,滕瑞1a,1b,韩郑生1a,1b,2(1.中国科学院 a.微电子研究所;b.硅器件技术重点实验室,北京 100029;2.中国科学院大学微电子学院,北京 100029)摘 要:为满足种类繁多、功能复杂集成电路的单粒子效应评估需求,克服目前国内地面单粒子辐照实验环境机时紧张、物理空间有限等方面的限制,设计实现了一款高效通用的集成电路单粒子效应测试系统。
创新性地采用旋转立体垂直结构,包含一个多现场可编程门阵列(FPGA)电测试平台、运动控制分系统和被测器件装载板。
便携式箱体结构仅需3个DB9接口即可完成所有与外界连线;基于LabVIEW实现上位机交互界面,界面友好;基于多FPGA平台实现下位机测试程序,灵活可扩展,通用性强。
可实现8种300及以下管脚集成电路的一次安装、自动切换和10°~90°的角度辐射。
实时监控并后台记录翻转数据、翻转时间、电路状态等细节信息,测试频率可达100 MHz。
已通过专用集成电路(ASIC)、静态随机存取存储器(SRAM)、控制器局域网络(CAN)接口电路等集成电路的多次实测,验证了该系统的可靠性及其高效稳定、集成度高、安装调试方便等特点。
关键词:单粒子效应测试系统;旋转结构;角度辐射;虚拟仪器中图分类号:TN710 文献标志码:A doi:10.11805/TKYDA2019421Design of a general test system for integrated circuit Single Event EffectYANG Wanwan1a,1b,LIU Hainan1a,1b,GAO Jiantou1a,1b,LUO Jiajun1a,1b,TENG Rui1a,1b,HAN Zhengsheng1a,1b,2 (1a.Institute of Microelectronics;1b.Key Laboratory of Silicon Device Technology,Chinese Academy of Sciences,Beijing 100029,China;2.School of Microelectronics,University of Chinese Academy of Sciences,Beijing 100029,China)Abstract:In order to meet the requirements of Single Event Effect(SEE) evolution for a wide variety of integrated circuits with complex functions and overcome the limitations such as time constraints andlimited physical space in current domestic ground single event irradiation experimental environment, anefficient and universal single event effect test system is designed and implemented for integrated circuits,which innovatively adopts rotating solid vertical structure,including a multi-Field Programmable GateArray(FPGA) electrical test platform,a motion control subsystem and some loading boards of the DevicesUnder Test(DUT). The entire test system is packaged as a portable box, which only needs three DB9interfaces to complete all connections with the outside world. Therein the PC interface is achieved basedon LabVIEW, friendly to users. The lower computer test program is implemented based on the multi-FPGAplatform, which is flexible, extensible and versatile. It can realize one-time installation, automaticswitching and angle radiation test of 8 types of integrated circuits within 300 PINs, meanwhile monitor inreal-time and background record the detail information such as flip data, flip time, circuit status and so on,whose test frequency achieves 100 MHz. The reliability, efficiency, stability, high integration, andconvenient installation and debugging have been verified by multiple tests on Application SpecificIntegrated Circuit(ASIC), Static Random-Access Memory(SRAM), Controller Area Network(CAN) interfacecircuit and other integrated circuits.Keywords:Single Event Effect test system;rotating structure;angle radiation test;virtual instrument人类对于空间以及外太空的不断探索促进了国内外航天事业的迅速发展[1],但辐射环境中的高能粒子入射半导体材料引发的辐射效应,是影响航天器电子系统可靠性的主要问题之一[2],集成电路的抗单粒子效应能力 收稿日期:2019-10-17;修回日期:2019-12-24作者简介:杨婉婉(1989–),女,硕士,主要研究方向为辐照加固集成电路设计及辐照测试试验。
爱达顿力源系列PDU设备说明书
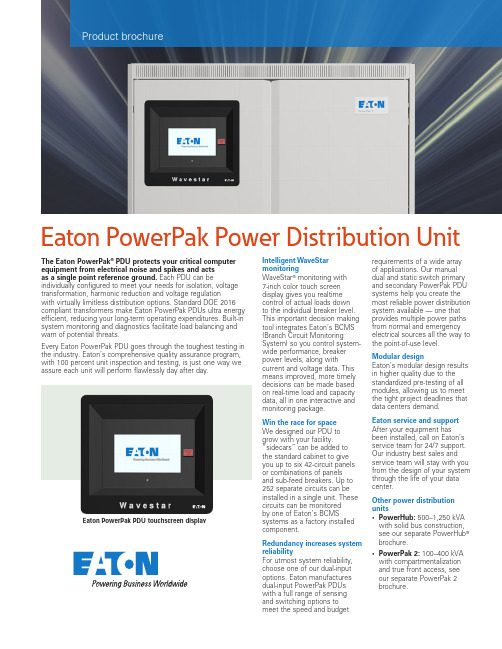
Eaton PowerPak Power Distribution UnitThe Eaton PowerPak® PDU protects your critical computer equipment from electrical noise and spikes and actsas a single point reference ground. Each PDU can be individually configured to meet your needs for isolation, voltage transformation, harmonic reduction and voltage regulationwith virtually limitless distribution options. Standard DOE 2016 compliant transformers make Eaton PowerPak PDUs ultra energy efficient, reducing your long-term operating expenditures. Built-in system monitoring and diagnostics facilitate load balancing and warn of potential threats.Every Eaton PowerPak PDU goes through the toughest testing in the industry. Eaton’s comprehensive quality assurance program, with 100 percent unit inspection and testing, is just one way we assure each unit will perform flawlessly day after day.Intelligent WaveStarmonitoringWaveStar® monitoring with7-inch color touch screendisplay gives you realtimecontrol of actual loads downto the individual breaker level.This important decision makingtool integrates Eaton’s BCMS(Branch Circuit MonitoringSystem) so you control system-wide performance, breakerpower levels, along withcurrent and voltage data. Thismeans improved, more timelydecisions can be made basedon real-time load and capacitydata, all in one interactive andmonitoring package.Win the race for spaceWe designed our PDU togrow with your facility.“sidecars” can be added tothe standard cabinet to giveyou up to six 42-circuit panelsor combinations of panelsand sub-feed breakers. Up to252 separate circuits can beinstalled in a single unit. Thesecircuits can be monitoredby one of Eaton’s BCMSsystems as a factory installedcomponent.Redundancy increases systemreliabilityFor utmost system reliability,choose one of our dual-inputoptions. Eaton manufacturesdual-input PowerPak PDUswith a full range of sensingand switching options tomeet the speed and budgetrequirements of a wide arrayof applications. Our manualdual and static switch primaryand secondary PowerPak PDUsystems help you create themost reliable power distributionsystem available — one thatprovides multiple power pathsfrom normal and emergencyelectrical sources all the way tothe point-of-use level.Modular designEaton’s modular design resultsin higher quality due to thestandardized pre-testing of allmodules, allowing us to meetthe tight project deadlines thatdata centers demand.Eaton service and supportAfter your equipment hasbeen installed, call on Eaton’sservice team for 24/7 support.Our industry best sales andservice team will stay with youfrom the design of your systemthrough the life of your datacenter.Other power distributionunits• P owerHub: 500–1,250 kVAwith solid bus construction,see our separate PowerHub®brochure.• P owerPak 2: 100–400 kVAwith compartmentalizationand true front access, seeour separate PowerPak 2brochure.Product brochureEaton PowerPak PDU touchscreen displayEaton 1000 Eaton Boulevard Cleveland, OH 44122 United States © 2021 Eaton All Rights Reserved Printed in USA Publication No. BR155041EN / GG March 2021Eaton is a registered trademark. All other trademarks are property of their respective owners.For more information, please visit: /powerpakpdu Follow us on social media to get the latest product and support information.Specifications Features • Copper or aluminum wound construction • D ual electrostatic shield—attenuates high frequency noise • O versized neutral conductor • C ommon mode noise protection • T ransverse mode noise protection • A ccurate kW, power factor and THD measurement • T rue RMS metering • O perating efficiency: 98% typical • L isted to UL 1950, CSA certified • M odbus RTU communications • B CMS available as factory installed option Enclosure • N EMA 1 enclosure with removable front side and rear panels • R emovable front, side and rear panels • I ntegrated two-point latch and vision panels • F lush-mounted door handle with integral locks • A dvanced door catch assures positive closure Operating conditions • O perating temperature: Ambient 0°C to 40°C per ANSI/IEEE C57.12.01—the temperature of the cooling air (ambient temperature) shall not exceed 40°C, and the average temperature of the cooling air for any 24-hour period shall not exceed 30°C • S torage temperature: Ambient -10°C to +40°C (for storage temperature outside the standard range contact Eaton)• A ltitude standard: 3300 ft., max:10,000 ft. (For altitudes greater than 10,000 ft please contact Eaton)• 50 Hz operating range: 47–53 Hz • 60 Hz operating range: 57–63 Hz Customization Eaton offers the most comprehensive designs in the industry.Let us help you create your own for your application.PowerPak PDU options Monitoring Standard monitor: Eaton WaveStar monitor with 7-inch color touchscreen display (input and output monitoring)Options: Dual transformer thermal switches Communications: Serial RS-485 Modbus; optional SNMP communications Thermal: Dual transformer thermal switches Quad-Wye ® technology Solves harmonic problems by canceling the destructive triplen and nontriplen current harmonics.T ransient Suppression Network (TSN)An integrated system engineered to meet ANSI/IEEE category C standards for transient voltages and surge currents.Lightning arrestor/surge suppressor Protects the insulation of the system magnetics.Distribution panelboards/sub-feed breakers Customized distribution configurations meet the demands of any facility.Redundant power distribution systems • W aveStar manual dualDual-input power distribution systems that allow for manual source selection to isolate upstream equipment and facilitate system maintenance and repair.• W aveStar primary and secondary static switch systemStatic switching, power conditioning and distribution system for transparent dual power source transfers. An integrated line up that offers primary, secondary and dual-cord configurations to help optimize your system solution. The Eaton static switch will sense and transfer between sources in 4 ms.T ransformersDOE 2016 compliant transformers are standard on all models.NEMA 1 enclosure ®。
piezoelectric effect 原理英文

piezoelectric effect 原理英文全文共3篇示例,供读者参考篇1Piezoelectric Effect PrincipleIntroductionThe piezoelectric effect is a phenomenon in which certain materials generate an electric charge in response to mechanical stress. This effect is widely used in various applications such as sensors, actuators, and energy harvesting devices. Understanding the principles behind the piezoelectric effect is crucial for optimizing the performance of these devices.Principle of Piezoelectric EffectThe piezoelectric effect is based on the unique properties of certain crystals, ceramics, and polymers that exhibit piezoelectric behavior. These materials have a crystalline structure that allows them to generate an electric charge when subjected to mechanical stress. This occurs because the application of stress causes the material's atoms to shift slightly from their equilibrium positions, creating a separation of positive and negative charges within the material.When a mechanical force is applied to a piezoelectric material, the material deforms and generates an electric charge as a result of the shift in atomic positions. This charge separation is known as the direct piezoelectric effect. Conversely, when an external electric field is applied to a piezoelectric material, it causes the material to deform, known as the inverse piezoelectric effect.Applications of Piezoelectric EffectThe piezoelectric effect has numerous applications across various industries due to its ability to convert mechanical energy into electrical energy and vice versa. Some common applications of the piezoelectric effect include:1. Sensors: Piezoelectric materials are used in sensors to detect pressure, force, acceleration, and vibration. These sensors are widely used in industrial, automotive, and medical applications.2. Actuators: Piezoelectric materials are also used in actuators to convert electrical energy into mechanical motion. These actuators are used in precision positioning systems, valves, and pumps.3. Energy Harvesting: The piezoelectric effect can be used to harvest energy from ambient vibrations and mechanical movements. This energy can be used to power small electronic devices and sensors.4. Medical Imaging: Piezoelectric materials are used in medical imaging devices such as ultrasound transducers. These transducers generate and receive ultrasound waves to create detailed images of internal body structures.5. Piezoelectric Fans: Piezoelectric fans use the piezoelectric effect to generate airflow without the need for rotating blades. These fans are quieter and more energy-efficient than traditional fans.ConclusionThe piezoelectric effect is a fascinating phenomenon that has revolutionized various industries with its ability to convert mechanical energy into electrical energy and vice versa. Understanding the principles behind the piezoelectric effect is essential for designing and optimizing devices that rely on this effect. As technology advances, the applications of the piezoelectric effect are expected to expand further, offering new opportunities for innovation and sustainability.篇2The piezoelectric effect is a phenomenon in which certain materials generate an electric charge when subjected to mechanical stress. This effect was first discovered by the Curie brothers, Pierre and Jacques Curie, in 1880. It has since been widely studied and utilized in various fields, including physics, engineering, and materials science.At the heart of the piezoelectric effect is the concept of polarized ions within a crystalline structure. In a piezoelectric material, such as quartz or lead zirconate titanate (PZT), the atoms are arranged in a symmetric pattern with positive and negative charges balanced. When an external force is applied to the material, it causes the lattice structure to deform, which in turn displaces the polarized ions. This displacement of charges creates an electric field within the material, resulting in the generation of an electric voltage.The piezoelectric effect can be categorized into two types: direct and inverse. In the direct piezoelectric effect, mechanical stress leads to the production of electrical charge within the material. This effect is commonly used in sensors, actuators, and transducers. For example, piezoelectric sensors are oftenemployed in pressure sensing applications, while piezoelectric actuators are utilized in precision positioning systems.Conversely, the inverse piezoelectric effect involves the application of an electric field to induce mechanical strain in the material. This effect is commonly utilized in piezoelectric motors, ultrasonic transducers, and acoustic devices. For instance, ultrasound imaging systems rely on the inverse piezoelectric effect to generate high-frequency sound waves for imaging purposes.The practical applications of the piezoelectric effect are vast and diverse. In the field of energy harvesting, piezoelectric materials are used to convert mechanical vibrations into electrical energy. This technology can be employed in wearable devices, wireless sensors, and self-powered electronics. Piezoelectric materials are also utilized in medical devices, such as ultrasound probes and bone-conduction hearing aids.In conclusion, the piezoelectric effect is a fundamental principle that has revolutionized various industries. Its ability to convert mechanical energy into electrical energy, and vice versa, has paved the way for innovative technologies and advancements in science. As research in piezoelectric materialscontinues to progress, we can expect to see even more exciting developments in the future.篇3The piezoelectric effect is a fascinating phenomenon that has been studied and utilized in various fields of science and technology. In this document, we will discuss the principles behind the piezoelectric effect and its applications in different industries.Piezoelectric materials are substances that have the ability to generate an electric charge in response to mechanical stress. This effect was first discovered by French physicists Jacques and Pierre Curie in 1880 when they observed that certain crystals, such as quartz, produced an electric charge when subjected to pressure. This discovery led to the development of the piezoelectric effect, which has since been studied extensively and applied in various devices and technologies.The piezoelectric effect is based on the concept of polarization, which is the separation of positive and negative charges within a material. When a piezoelectric material is deformed or compressed, the crystal lattice structure of the material is disturbed, causing the positive and negative chargesto separate and generate an electric charge. This electric charge can be harnessed and used to power devices or sensors.One of the most common applications of the piezoelectric effect is in sensors and transducers. Piezoelectric sensors are widely used in industries such as automotive, aerospace, and healthcare to measure pressure, force, acceleration, and vibration. For example, piezoelectric sensors can be used in accelerometers to detect changes in speed and direction, or in ultrasound devices to generate and receive sound waves for medical imaging.Piezoelectric materials are also used in actuators, which are devices that convert electrical energy into mechanical motion. Piezoelectric actuators can be found in devices such as inkjet printers, where they are used to control the movement of the printer nozzle and dispense ink onto the paper. They are also used in precision positioning systems, microscopy, and robotics.Another area where the piezoelectric effect is utilized is in energy harvesting. Piezoelectric materials can convert mechanical energy from sources such as vibration, motion, or pressure into electrical energy, which can be stored and used to power electronic devices. This technology is particularly useful inremote or inaccessible locations where traditional power sources are not available.In addition to these practical applications, the piezoelectric effect has also been studied in research and development for its potential in other areas. For example, researchers are exploring the use of piezoelectric materials in energy-efficient buildings, where they can be used to generate electricity from ambient vibrations and movements in the structure. They are also investigating the use of piezoelectric materials in biomedical devices, such as implants and medical sensors.Overall, the piezoelectric effect is a powerful phenomenon that has revolutionized various industries and technologies. Its ability to convert mechanical energy into electrical energy makes it a valuable tool in sensors, actuators, energy harvesting, and many other applications. As researchers continue to explore and develop new uses for piezoelectric materials, the potential for innovation and advancement in this field is limitless.。
How to Order Glenair Circular Connector Backshells

H t o O The Working EnvironmentThe broad range of backshell types available to-day makes it critical for interconnect engineers, and others tasked with the responsibility of specifying connector accessories to become adept at building backshell part numbers. For the most part, the pro-cess entails selecting options from the part number development trees found on each catalog page.But experience shows it is equally important to consider the working environment of the target ap-plication before completing the backshell selection process. There are many electrical, mechanical and environmental considerations which, when properly addressed, will ensure a long functional life for the interconnect system. So before you start building part numbers, please consider the following:(1) What are the material/finish specifications of the mating connector?(2) What level of environmental protection is re-quired in the system—from full water immersion, to splash proof and/or moisture resistance?(3) What level of EMI shielding is required, and is any particular style or type of shield termination generally specified in the target assembly?(4) What level or amount of strain-relief, from light duty to gorilla proof, is required to protect shield and conductor terminations from damage?(5) What is the temperature range of the appli-cation environment? Is it so hot that stainless steel is called for, or so cold that an elastomeric seal might potentially fail?(6) Is repairability a design requirement? Some split shell designs make field repair a snap, while solid shell models make accessing contact termi-nations more difficult.(7) Are there size or shape constraints which need to be considered? Is working room so impor-tant that an extender needs to be designed in? Or is available space so tight that an ultra low profile backshell design is called for? Does cable routing dictate 45o , 90o or straight cable entries?(8) Is a metal shell required or is saving weight and preventing corrosion with composite thermo-plastic materials an option?(9) Does the application require conformance to AS85049 or another specification?Cable Make-upOther questions in backshell selection cannot be answered without an understanding of the overall make-up of the cable and harness. Basic dimen-sional decisions on cable entry size cannot be specified without accurate descriptions and mea-surements of the cable or wire bundle. A basic analysis of the cable should include:• Wire Numbers and Types: twisted shielded pairs, coaxial power, signal, fiber optic, etc.• Shield Material Gauge, Number and Type:tin, nickel, silver plated copper wire, and so on.• Jacket Material and Thickness.The table on the following page will assist you in calculating wire bundle diameter for use in choos-ing the correct backshell cable entry diameter.An accurate estimate of the cable diameter is required to select the right backshell cable entry diameter. Com-plete the cable analysis before selecting the backshell.Backshell Part Number DevelopmentGlenair follows a standardized format for the de-velopment of accessory part numbers, so mastering the process once will enable you to build valid part numbers from any connector accessory product family—circular, rectangular, composite, fiber op-tic, and so on. Some differences are of course to be found from one product series to the next be-cause of the range of available options. If in doubt,QwikCreate, The Glenair Part Number Builder , is now available on our website and takes all the pain and suffering out of backshell specification. For catalog users, the following steps will serve as gen-eral guide to the process.(1) Select the Product Series: Do you want a dust cap, a banding adapter, an environmental back-shell or some other type of connector accessory?Use the graphical product selection guide at the be-ginning of the catalog for help in getting to the right section.Typical backshell part number development or "How to Order" treeSteps (1a) Determine average wire diameter whenall wires are the same diameter; or(1b) Determine average wire diameter when wires are different diameters.(2) Multiply average wire diameter by factor from Table I below(3) Add thickness of any shielding or jacketing to core wire bundle diameter (for example,add .025 for braided sleeving)Given 30 Wires @ .045 DIA Avg. Wire DIA = .045Given 15 Wires @ .045 and 15 Wires @ .13515 x .045 = .6815 x .135 = 2.03(1a) .045 x 6.7 = .3015 Core Wire Bundle DIA (1b) .090 x 6.7 = .603 Core Wire Bundle DIA (1a) .3015 + .025 = .3265 Wire Bundle Outside DIA (1b) .603 + .025 = .628 Wire Bundle Outside DIA2.71+302.71= .090 Avg. Wire DIA =H t o O (2) Select the Connector Designator: This al-phabetic symbol or "designator" is used to match each standardized connector family with the cor-rect backshell thread and interface dimensions.Tables listing all the connector designators used by Glenair can be found beginning on page 15. MIL-DTL-5015 connector users must use an additional manufacturer symbol when ordering backshells.Please see pages 18 and 19 for more information.(3) Select the Basic Part Number: This num-ber fine-tunes your selection within the productStrain-ReliefsTypical Mil-Aero cable assemblies often have over a hundred wires terminated to a single connector. Preventing the wires from pulling on the contacts and damaging the termination is critical, and is usually accomplished with a strain-relief cable clamp that serves to isolate the pulling strain applied to the cable. Strain relief on electrical connectors can be accom-plished in other ways, such as with a wire service loop that allows the wire to move be-tween the clamping device and the contactwithout over-stressing the termination. However the basic method of clamping the wire bundle or cable jacket with saddle bars has historically been the most common method of protectingcontact terminations.• Straight and Angled Strain Reliefs• Light, Medium and Heavy-Duty Saddle Bars• Qwik-Ty ®• QwikClamp ®series. For example, for Series 39 EMI/RFI Cable Sealing Backshells, your Basic Part Number selec-tion will tell the factory what style of shield termination technology you prefer and the level of environmen-tal sealing desired. The Basic Part Number also selects for other attributes such as rotatable or di-rect coupling.(4) Select the Angle and Profile: Choose 45o ,90o or straight backshells in either standard, low or full radius profiles. Selected parts are also avail-able in Ultra Low Profile Split Shell versions.Angle and ProfileThe art of successful backshell selection includes specifying the most appropriate shape and cable entry for each connector accessory.This selection determines working room,repairability, cable routing and the elimination of acute angles. In addition to straight backshells,the range of angles and profiles offered byGlenair include:• 45° Elbow - Standard Profile • 45° Elbow - Low Profile • 45° Elbow - Full Radius Profile • 45° Elbow - Low Profile Split Shell• 90° Elbow - Standard Profile • 90° Elbow - Low Profile • 90° Elbow - Full Radius Profile • 90° Elbow - Low Profile Split Shell• 90° Elbow - Ultra Low Profile Split Shell "Cobra"45o90oStraightBand-It Termination SystemGlenair TAG Ring BackshellsConical Ring Style Backshells(5) Select the Finish Symbol: This symbol, se-lected from the table on page 14 or from the same table inside the back cover, tells the factory what surface finish or plating should be applied to the product. In almost all cases this selection should match the material finish of your connector.(6) Select the Connector Shell Size Number:The connector shell size number is taken from Table 1, located on page 13 and repeated again on the inside back cover. The connector shell size num-ber ensures the backshell thread and interface dimensions will fit the chosen size connector. Find the shell size number in the appropriate column ac-cording to your connector designator. In certain cases, such as MIL-DTL 38999 Series I and II Con-nectors (designator F), we have combined both series under a single choice. Simply find your odd connector number or letter in the [brackets] and enter the adjacent number in your part number.(7) Select the Cable Entry Diameter: This en-try specifies the minimum and maximum diameter of cable the backshell accessory can accommo-date. Cable entry selection tables are generally found right there on the page. If in doubt, err on the big side, as cables may always be enlarged with tape or a grommet.(8) Select the Strain Relief Style: Most acces-sories that are able to accept saddle bar cable clamps offer a range of choices. The selection is usually based on the level or duty of strain-relief that is required, and design drawings of applicable options are featured right there on the catalog page.(9) Select Unique Options: Other available op-tions, such as drain holes, bands, wire attachment lengths, special material designators, and so on,are tacked on to the end of the part number. In some cases you will be asked to omit the code for a particular option if you do not want it included with the part.Shield Termination DevicesSelecting the most appropriate shield terminat-ing backshell for a particular application requires a detailed analysis of the cable and the application environment in which the assembly will be used.H t o O There is no single shield termination technology or methodology that will meet every customer require-ment. For this reason, Glenair supports every popu-lar shield termination method with the full range of shell sizes, materials, platings and tooling, including:• Single and Multiple Conical Rings • Crimp Rings• Banding Terminations• Castellated or Splined Rings • Lampbase Thread Rings • Radial Compression Springs • Integrated Shield Socks • Magnaforming • Tinel ™ Lock-RingsCustomer selection depends on many factors,including cost, repairability, shield type and construc-tion, cable diameter and type, cable jacket thick-ness, weight, shock and vibration, strain-relief, cor-rosion resistance and so on. The primary factor is cable construction: what type of shield is being ter-minated, where the shield or combination of shields is located within the cable or wire bundle, and how difficult the outer jacket is to work with. Customer preference, established methods and practices, tra-dition, manual skill levels and inspection procedures must also be considered.The relative effectiveness of each style can be measured using a transfer impedance test. The transfer impedance test is the most widely accepted absolute measure of a shield's performance. It is used to evaluate cable shield performance against electrostatic discharge and radiated emissions cou-pling at frequency ranges up to 1 GHz. This testing method is recommended by the International Electrotechnical Commission as well as the military.T est reports for most standard termination technolo-gies are available upon request from the factory.Corrosion Protection in Electromagnetic Interconnect SystemsGlenair has a responsibility to deliver intercon-nect systems and hardware to its customers with-out "built-in" corrosion problems. As part of this ef-fort we have pioneered the use of composite ther-Submersible BackshellsThis Cable Sealing Backshell provides a resil-Splash-Proof BackshellsFor applications requiring only moisture resis-moplastic materials as an alternative to conductive metal materials and finishes. Composite products can eliminate corrosion problems completely in in-terconnect systems and should be considered for all harsh application environments.The problems associated with corrosion are compounded by the need to produce parts which are electrically conductive. To prevent EMI from permeating into system electronics, conductive cable shielding is grounded to plated backshells and connectors to take the unwelcome EMI to earth. The challange is to produce conductive,plated products which both prevent EMI and resist corrosion in harsh application environments. At Glenair this work takes place in three areas:1. Strict attention to dissimilar metal combinations;2. The specification of corrosion-resistant mate-rials such as stainless steels and composites in se-vere environments wherever possible; and3. The use of surface coatings such as nickel,zinc or gold plating to isolate base metals from re-active electrolytes.The selection of compatible (non-galvanic)surface finishes is a critical step in backshell speci-fication. To prevent dissimilar metal corrosion,customers should note material and finish specifi-cations for connectors and cable shields before selecting connector accessory hardware. As a general rule, the backshell material and finish should match that of the chosen connector.Electroless nickel plating (code M) provides a low resistance conductive finish appropriate for most H (magnetic) and E (electrical) field EMI ap-plications, and is ideally suited for benign environ-ments not exposed to salt-spray. For environmen-tal applications, a sacrificial overplating, such as cadmium plate over electroless nickel (code NF),is recommended. Glenair zinc-nickel over electro-less nickel (code ZN) may also be specified for en-vironmental applications which require ASTMB 841-91 approval but are prohibited from using cadmium.Non-EMI applications may utilize nonconductive fin-ishes such as Black Anodize (Code C). See T able II for other standard finish options.Positive-Lock, Non-Detent CouplingSelf-Locking, Rotatable CouplingDirect couplers thread directly onto the connector by rotating the entire part. A separate toothed follower pro-pling nut for easier installation.Rotatable Self-Lockers add a ratcheted detent "clicker"to prevent de-coupling due to extreme vibration and shock.Glenair Mod Code -445 ("NESTOR") coupling mecha-nism corresponds to AS85049 style "N" non-detent, rotat-。
板级测试指南

板级测试指南[英]Printedcircuit boards used to be works of art,and the PCB designer was an artist as well as a ponents had many different shapes,sizes,and colors,and the traces connecting them were graceful arcs in beautiful patterns.在过去,一块印刷电路板就是一份艺术品,印刷电路板的设计人员不仅仅是一名技术人员还是一位艺术家。
器件有不同的形状、大小和颜色,而且连接器件的导线形式优美。
Today’s boards,by contrast,are boring.On a typical modern digital PCB assembly,for example,the parts are all squat rectangular components,and the traces are laid out with a precision only a computer could love.相比之下,现在的电路板令人厌烦。
例如,在一块标准的数字印刷电路板上,所有的器件都是有棱有角的,布线的精度也只有计算机才可以完成。
Test methods for PCB assemblies have changed as well.In the past,nearly all testing was functional testing,and it was performed with bench top instruments or a custom tester.T oday,the test engineer has many more options,including incircuit testers, manufacturing defects analyzers,and several types of functional testers.对印刷电路板装配的测试方法也已经改变了。
暴露生物标志物--英文解释

/pesticides/science/biomarker.html#exposureDefining BiomarkersBiomarkers are measurable substances or characteristics in the hum an body that can be used to m onitor the presence of a chemical in the body, biological responses, or adverse health effects. The use of biom arkers will help us evaluate potential exposures to pesticides as well as predict effects that m ay result, allowing us to make decisions that are m ore protective of hum an health. Biomarkers are commonly grouped into biomarkers of exposure, effect, and susceptibility. This Web page describes these groups of biomarkers and provides examples.On this page:Biomarkers of ExposureBiomarkers of exposure are used to assess the amount of a chemical that is present within the body. Many chemicals can be m easured in urine, blood, saliva, and, if they are fat soluble, in body fat and breast m ilk (e.g., DDT). Biomarkers of exposure provide information on∙chemical exposures in individua ls,∙changes in levels over tim e, and∙variability am ong different populations.They m ay also provide information on the relative importance of different exposure pathways and associated risk. It is important to note that the m easurement of a chemical in som eone’s body does not by itself m ean that chemical has caused adverse health effects.Additionally, there are a number of uses related to the interpretation of biomarkers of exposure. For example, the m easurement of 3-phenoxybenzioc acid (3-PBA) in urine is considered a non-specific biom arker of exposure because 3-PBA is a common m etabolite of several pyrethroid pesticides. Therefore, additional information is needed to resolve which pyrethroid was the parent chemical.Top of pageBiomarkers of Exposure Categories∙Chemical–The m ost specific exposure biomarker is direct m easurement of the chem ical of interest in the body. Typically, m easurement of thechemical is made in an accessible biological matrix (e.g., blood, urine).While some pesticides can be directly m easured in the body, it is generallymore common to m easure m etabolites of pesticides.∙Metabolite– Many chem icals are rapidly m etabolized or difficult to m easure.In these cases, a m ore stable breakdown product (m etabolite) of thechemical m ay be m easured to estim ate exposure to the chemical. When ametabolite m ay derive from a number of different chem icals (as in the3-PBA example above), additional information is needed to resolve towhich chemical the person was exposed.∙Endogenous surrogate– In som e cases, a chemical or class of chem icals may result in an endogenous response (response within the body) that ishighly characteristic of that chemical or class. Measures of that responsecan be used as a surrogate in lieu of direct m easurement of the chemical ormetabolite concentration when sufficient additional information is available.Since there are m any factors that can influence endogenous responses,this type of exposure biomarker is accom panied by m any uncertainties thatshould be identified and discussed.See examples in Table 1Top of pageBiomarkers of EffectBiomarkers of effect are indicators of a change in biologic function in response to a chemical exposure 1. Thus, they m ore directly relate to insight into the potential for adverse health effects com pared with biomarkers of exposure.One example of a biomarker of effect is blood cholinesterase, which can becom e depressed following exposure to organophosphate and N-m ethyl carbamate pesticides. Measuring cholinesterase levels can be a useful tool for m onitoringagricultural workers and identifying workers that m ay potentially be overexposed to pesticides.Top of pageBiomarkers of Effect Categories∙Bioindicator– An ideal biomarker of effect has an explicitly known mechanism that links the marker and an adverse outcom e. In most cases,this is achieved by a sufficient understanding of the adverse outcom epathway or m ode of action of the chemical, and the causal or correlativerelationship of biological events between the m arker and the adverseoutcom e.Bioindicators provide a high degree of confidence in predicting thepotential for adverse effects in an individual or population based on markerlevels. An understanding of the adverse outcom e pathway also supportsdevelopment of a variety of bioindicators for different key events oroutcom es of interest (e.g., m arkers for precursor event s leading to aclinically detectable adverse outcom e to support early detection andprevention).When cellular or molecular initiating events can be identified as criticalsteps in an adverse outcom e pathway, bioindicators can be developed inconjunction with high throughput screening assays to provide a rapid andefficient m eans for early detection of adverse outcom es in targetpopulation. EPA researchers are actively developing this class ofbiomarkers of effects in support of Toxicity Testing in the 21st Century.∙Undetermined consequence– This subgroup of biomarkers provides more limited and uncertain indication of the potential for adverse effects,because the events or deterministic linkages in an adverse outcom epathway are less well known. An example would be markers of oxidativestress where elevations have been associated with a variety of adverseoutcom es, but the explicit relationships have yet to be defined. As the roleof oxidative stress in different disease processes (and adverse outcom epathways) becom es more clearly defined, there will be increasing certaintyin the use of oxidative stress biomarkers to predict the potential fororganism/population-level effects. Meanwhile, these biomarkers can beused in conjunction with other biomarkers in this or other subgroups toimprove the specificity and sensitivity of the overall set of m arkers fordevelopment of an adverse outcom e.∙Exogenous surrogate– Som e chemicals have well known adverse effects, which are accompanied by other effects that can be used as surrogateindicators of the m ain adverse effect of interest. A common example isparanitrophenol , a m etabolite of m ethyl parathion. Measurement inhumans of paranitrophenol in the urine has been used as an exogenoussurrogate biomarker of exposure to m ethyl parathion, and as an indicatorof the potential for toxicity due to m ethyl parathion-inducedacetylcholinesterase inhibition.Exogenous surrogate biomarkers are suboptimal as effects m arkersbecause they do not directly capture the contribution of additional factors(intrinsic and extrinsic) that m ay influence the incidence or severity of anadverse outcom e. Given these limitations, use of exogenous surrogates asbiomarkers is mostly limited to m easurement of those effects that arepredominantly due to the chemical of interest (i.e., to reduce the num berof potentially confounding effects, and to decrease uncertainty associatedwith the m easured surrogate biomarker).See examples in Table 2Top of pageBiomarkers of SusceptibilityBiomarkers of susceptibility are factors that m ay make certain individuals more sensitive to chem ical exposure. Biomarkers of susceptibility include:∙genetic factors that m ay influence how the body interacts with a chemical ∙other biological factors related to nutritional status, health status, lifestyle, and life stage that m ay affect an individual’s susceptibility to chemicalexposure.Top of pageTable 1: Examples of Biomarkers of Exposure from Different CategoriesTable 2: Examples of Biomarkers of Effects from Different CategoriesAbbreviations:3-PBA: 3-phenoxybenzioc acid8-OHdG: 8-hydroxy-2'-deoxyguanosineAcetylcholinesterase: AChEDiPap: Polyfluoroalkyl phosphate esterPFOA: Perfluorooctanoic acidT4: thyroxine (a thyroid hormone)1 Biomarkers of effect correspond to biomarkers as defined by the FDA: Biomarkers Definitions Working Group (2001). Clinical Pharmacology and Therapeutics, 69, p.89 – 95.。
- 1、下载文档前请自行甄别文档内容的完整性,平台不提供额外的编辑、内容补充、找答案等附加服务。
- 2、"仅部分预览"的文档,不可在线预览部分如存在完整性等问题,可反馈申请退款(可完整预览的文档不适用该条件!)。
- 3、如文档侵犯您的权益,请联系客服反馈,我们会尽快为您处理(人工客服工作时间:9:00-18:30)。
0-7803-3286-5/96 $4.00 01996 IEEE
91 1
1996 Electronic Components and Technology Conference
( 3 ) The percentage of heat conducted to the PCB is
Board and System Level Effects on Plastic Package Thermal Performance
Tiao Zhou, Michael Hundt SGS-Thomson Microelectronics
ABSTRACT
The objective of this work is to understand the effect of the boardsystem environment on package thermal performance. It is found that for most plastic packages and in typical application environment, the majority of heat is conducted to the board. The junction to ambient thermal resistance can be obtained by the package thermal resistance and board thermal resistance. For a particular package, as the board and system environment changes, the package thermal resistance does not change, what changes is the board resistance. Thermal enhancement can be achieved in board and system level in additional to package level. The board and system act as the system heat sink. The thermal resistance of this heat sink is represented by the board to ambient thermal resistance. In this study, the sensitivity of the board thermal resistance to different parameters is examined by simulation. These parameters include: package size and placement, board construction and mounted, and the component interaction. It is suggested that by carefully designing the board and system, the optimal thermal performance can be reached.
2. PACKAGE THERMALto understand how the heat is dissipated from the chip to outside the package. For a plastic package mounted on a PCB, the heat is dissipated through three paths: (1) IC => package surfaces => ambient; (2) IC => leads => PCB; and (3) IC => package bottom => air gap => PCB. The first path involves convection and radiation. The heat dissipations through the second and the third paths are by conductive heat transfer. In this section, the efficiency of the thermal paths is studied by analyzing the percentage of heat dissipated through each path. Two PQFP packages are considered for the thermal path analysis. The first one is a small package: the 10x10 mm power TQFP. The second package is a big one: the 28x28 mm PQFP. PCB's with different sizes and copper layers are employed. These models cover situations with small package and thermally effective PCB (for which maximum heat is conducted to PCB) to big package and thermally less effective PCB. The common conclusions will be valid for most plastic packages. The models are described in Table 1. The percentages of heat dissipated from the IC to outside the package through different thermal paths are also listed in this table.
extensively. The PCB effect has been assessed with board temperature ([2], [3] & [SI). In this study, a new approach is taken to look at the board and system level effects. Thermal path analysis is presented first to illustrate the roles of the package, PCB and the system in the overall thermal resistance. Board and system level effects are investigated next followed by conclusions and discussions.
approximately constant for a package, regardless of the board construction. (4) The percentage of heat dissipated through the first path increases when the package size increases, board size decreases, board thermal conductivity decreases or the Alloy42 lead frame is used.
1. INTRODUCTION
The primary goal of the thermal management is to maintain the integrated circuit (IC) junction temperatures (Tj) below a certain limit to ensure the required reliability. It is essential to be able to estimate the Tj of the key IC components. The junction temperature is usually estimated based on the junction to ambient thermal resistance e,, for the IC package. This seems to be straight forward. Unfortunately, the e,, is not a constant. It depends on the PCB and environment. Directly applying the thermal resistance value obtained in standard package characterization process to predict the thermal performance of the package in the application environment can cause significant errors ([l] - [4]). The purpose of this study is to understand the board and system level effects on plastic package thermal performance. This will help to achieve more realistic junction temperature estimate and thermal performance optimization in application environment. This work is limited to the applications where no discrete heat sink is attached to the package top. In these situations, the primary thermal path is the conduction to the board. The factors which govern the junction to ambient thermal resistance are package construction, PCB and environment (system). The effect of package construction has been studied