硫化模设计橡胶加工工艺
橡胶硫化工艺流程

橡胶硫化工艺流程橡胶硫化是指将橡胶中的双键或多键化合物与硫或其它硫化剂反应生成交联结构的化学反应过程。
硫化是橡胶制品加工中必不可少的一道工艺,它可以提高橡胶制品的耐磨性、耐老化性和强度,使橡胶制品具有更好的物理性能。
橡胶硫化工艺流程是指橡胶硫化过程中所涉及到的各个环节和步骤,下面将详细介绍橡胶硫化工艺流程。
首先,橡胶硫化的原料准备。
在橡胶硫化工艺流程中,首先需要准备好橡胶和硫化剂。
橡胶可以是天然橡胶、合成橡胶或再生橡胶,而硫化剂主要是硫磺。
在一般情况下,还需要添加一些促进剂、活化剂和防老化剂等辅助原料,以提高硫化效果和橡胶制品的性能。
其次,橡胶混炼。
橡胶混炼是指将橡胶和各种硫化剂、促进剂等原料混合均匀的过程。
混炼的目的是使各种原料充分分散,以便硫化剂能够均匀地和橡胶发生化学反应。
混炼过程中需要控制好温度、时间和机械作用,以确保橡胶和各种原料充分混合。
然后,硫化成型。
混炼后的橡胶料需要进行硫化成型,即将橡胶料放入硫化模具中,加热使其发生硫化反应,并得到所需形状的橡胶制品。
硫化成型的温度、时间和压力等参数需要根据具体橡胶制品的要求来进行控制,以确保橡胶制品的质量。
最后,橡胶制品的后处理。
硫化成型后的橡胶制品需要进行后处理,包括去除模具、修整边角、清洗等工序。
有些橡胶制品还需要进行硫化后的热处理或冷却处理,以进一步提高其性能。
总之,橡胶硫化工艺流程是一个复杂的过程,需要严格控制各个环节和步骤,以确保橡胶制品的质量和性能。
只有在整个硫化工艺流程中严格执行标准操作规程,才能生产出优质的橡胶制品,满足不同行业的需求。
橡胶工艺----硫化篇
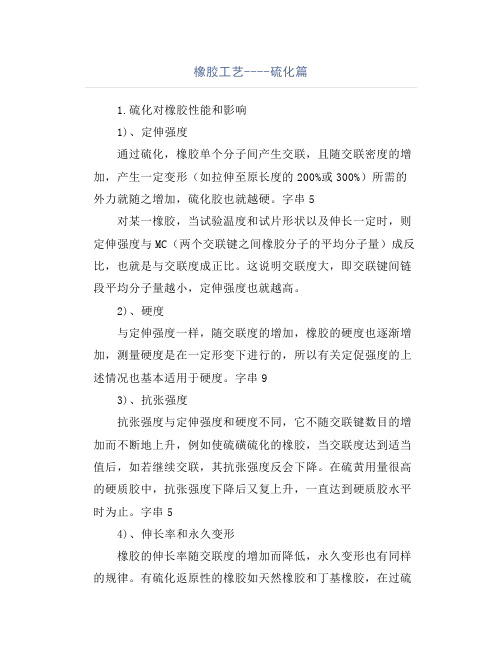
橡胶工艺----硫化篇1.硫化对橡胶性能和影响1)、定伸强度通过硫化,橡胶单个分子间产生交联,且随交联密度的增加,产生一定变形(如拉伸至原长度的200%或300%)所需的外力就随之增加,硫化胶也就越硬。
字串5对某一橡胶,当试验温度和试片形状以及伸长一定时,则定伸强度与MC(两个交联键之间橡胶分子的平均分子量)成反比,也就是与交联度成正比。
这说明交联度大,即交联键间链段平均分子量越小,定伸强度也就越高。
2)、硬度与定伸强度一样,随交联度的增加,橡胶的硬度也逐渐增加,测量硬度是在一定形变下进行的,所以有关定促强度的上述情况也基本适用于硬度。
字串93)、抗张强度抗张强度与定伸强度和硬度不同,它不随交联键数目的增加而不断地上升,例如使硫磺硫化的橡胶,当交联度达到适当值后,如若继续交联,其抗张强度反会下降。
在硫黄用量很高的硬质胶中,抗张强度下降后又复上升,一直达到硬质胶水平时为止。
字串54)、伸长率和永久变形橡胶的伸长率随交联度的增加而降低,永久变形也有同样的规律。
有硫化返原性的橡胶如天然橡胶和丁基橡胶,在过硫化以后由于交联度不断降低,其伸长率和永久变形又会逐渐增大。
5)、弹性未硫化胶受到较长时间的外力作用时,主要发生塑性流动,橡胶分子基本上没有回到原来的位置的倾向。
橡胶硫化后,交联使分子或链段固定,形变受到网络的约束,外力作用消除后,分子或链段力图回复原来构象和位置,所以硫化后橡胶表现出很大的弹性。
交联度的适当增加,这种可逆的弹性回复表现得更为显著。
2.硫化过程的四个阶段胶料在硫化时,其性能随硫化时间变化而变化的曲线,称为硫化曲线。
从硫化时间影响胶料定伸强度的过程来看,可以将整个硫化时间分为四个阶段:硫化起步阶段、欠硫阶段、正硫阶段和过硫阶段。
1)、硫化起步阶段(又称焦烧期或硫化诱导期)硫化起步的意思是指硫化时间胶料开始变硬而后不能进行热塑性流动那一点的时间。
硫起步阶段即此点以前的硫化时间。
在这一阶段内,交联尚未开始,胶料在模型内有良好的流动性。
橡胶硫化工艺部分流程表

已经混炼好的胶板。
(600-B型)橡胶切条机 一台,小型手动压力油壶 一只,6~12寸活动扳手各 一只。
18 19
炼胶
一般橡胶生产加工工艺流程
加工制作阶段 工作环境要求 专业 工种 操作步骤一 操作步骤二 1首先把胀杆互相撞击一 下,目的是把胀杆加工时的 铁屑除去,特别是大规格的 1操作工应该防止皮肤接触 胀杆要这样处理一次。2把 液体。2必须戴好手套,口 已经按照浓度要求勾兑好的 罩,穿工作服。3操作工必 熟练 磷酸液装在桶内。3磷酸液 按照时间把浸泡后的胀 须站立在上风口进行操作 工 在桶内的深度应该是胀杆长 杆提起淋干液体待用。 。4手套以及工作台必须无 度的1.3倍 ,3把胀杆竖立 油迹灰尘, 在提蓝内,放入磷酸液桶 内,按照时间要求浸泡。大 件25~30分钟,小件20~25分 钟 1操作工应该防止皮肤接触 液体。2必须戴好手套, 1 把碱溶液加热到70~100度 穿工作服。3操作工必须站 熟练 。2把胀杆浸泡在液体中不 立在上风口进行操作。4防 工 得露出液体水面,3~5分钟 止明火引燃其他物体,造 后,捞出来晾干, 成火灾。5手套以及工作台 必须无油迹灰尘,
段 操作步骤三 专业工种
成品下线修理装箱 操作步骤一 操作步骤二 操作步骤三
1不锈钢圆形提蓝应该架在 磷酸液桶的上口,使磷酸液 淋滴在桶内,防止漏滴在地 面或其他物体上造成腐蚀性 污染。
熟练工
将磷酸液桶 半成品转移到 加盖,防止 碱液脱脂工作 杂物漏入桶 区 内。
装到提蓝内待用,
熟练工
1将碱溶液桶 加盖,防止 半成品转移到 杂物漏入桶 喷砂工作区 内。
16
15硫化工 艺2
熟练 工
相关的硫化模具一副,鸭 嘴撬棒一根,约30~40公 硫化机械一套(生产主 分长,撬棒头宽度约1.6 管或者机械专业人员对 公分,扁头子,用于上下 机械进行跟踪维护保 模具撬开的自制工具。 养,) (生产主管或者机械专业 人员对机械进行跟踪维护 保养,)
硫化成型工艺文件

硫化成型工艺文件硫化成型工艺是一种常用的加工方法,用于制造橡胶制品。
它是将橡胶材料加热并与硫化剂一起混合,然后通过加压和加热使其变硬和耐磨。
在整个硫化成型过程中,需要严格控制时间、温度和压力等参数,以确保最终产品的质量。
为了实现硫化成型,我们需要准备橡胶材料和硫化剂。
橡胶材料可以是天然橡胶或合成橡胶,而硫化剂则是用于促进橡胶材料硫化反应的化学物质。
这两种原材料需按照一定比例进行混合,以确保硫化反应的有效进行。
接下来,混合好的橡胶材料和硫化剂会被放入硫化机中进行加热。
硫化机通常由加热系统、压力系统和控制系统组成。
加热系统会提供足够的温度,以使橡胶材料与硫化剂发生硫化反应。
压力系统则会施加适当的压力,将橡胶材料充分填充到模具中,并确保形状的准确性和一致性。
控制系统则用于监控和调节加热、压力和时间等参数,以确保硫化成型过程的稳定性和可控性。
在硫化成型过程中,温度是一个至关重要的因素。
橡胶材料需要在适当的温度下进行硫化反应,以确保其硫化程度和物理性能的稳定。
不同的橡胶材料和硫化剂会有不同的硫化温度范围,因此需要根据具体情况来确定最佳的硫化温度。
硫化时间也需要仔细控制。
过短的硫化时间可能导致橡胶制品硫化不完全,从而影响其物理性能和使用寿命。
而过长的硫化时间则可能造成橡胶制品过度硫化,导致其变脆和易碎。
因此,在硫化成型过程中,需要根据橡胶材料和硫化剂的特性来确定最佳的硫化时间。
总的来说,硫化成型工艺是一项关键的橡胶加工方法,它能够将橡胶材料加工成各种形状和尺寸的制品。
通过准确控制温度、压力和时间等参数,可以确保最终产品的质量和性能。
硫化成型工艺在各个领域都有广泛的应用,例如汽车制造、电子设备、医疗器械等。
它不仅提高了产品的耐磨性和耐候性,还能够为用户提供更好的使用体验和安全保障。
硫化工艺简介
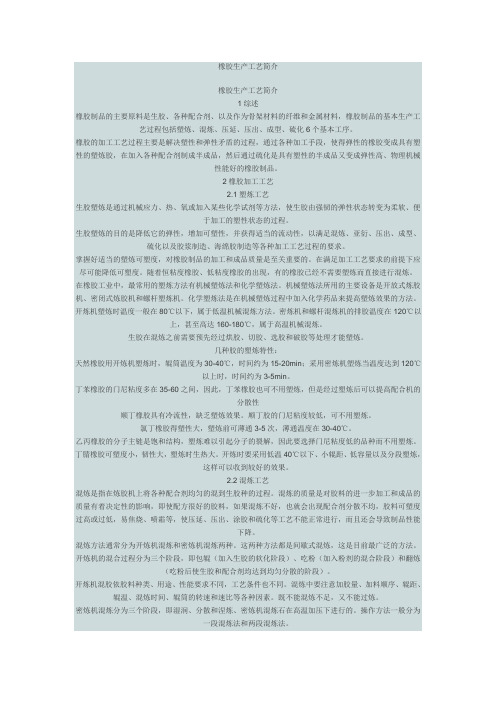
橡胶生产工艺简介橡胶生产工艺简介1综述橡胶制品的主要原料是生胶、各种配合剂、以及作为骨架材料的纤维和金属材料,橡胶制品的基本生产工艺过程包括塑炼、混炼、压延、压出、成型、硫化6个基本工序。
橡胶的加工工艺过程主要是解决塑性和弹性矛盾的过程,通过各种加工手段,使得弹性的橡胶变成具有塑性的塑炼胶,在加入各种配合剂制成半成品,然后通过硫化是具有塑性的半成品又变成弹性高、物理机械性能好的橡胶制品。
2橡胶加工工艺2.1塑炼工艺生胶塑炼是通过机械应力、热、氧或加入某些化学试剂等方法,使生胶由强韧的弹性状态转变为柔软、便于加工的塑性状态的过程。
生胶塑炼的目的是降低它的弹性,增加可塑性,并获得适当的流动性,以满足混炼、亚衍、压出、成型、硫化以及胶浆制造、海绵胶制造等各种加工工艺过程的要求。
掌握好适当的塑炼可塑度,对橡胶制品的加工和成品质量是至关重要的。
在满足加工工艺要求的前提下应尽可能降低可塑度。
随着恒粘度橡胶、低粘度橡胶的出现,有的橡胶已经不需要塑炼而直接进行混炼。
在橡胶工业中,最常用的塑炼方法有机械塑炼法和化学塑炼法。
机械塑炼法所用的主要设备是开放式炼胶机、密闭式炼胶机和螺杆塑炼机。
化学塑炼法是在机械塑炼过程中加入化学药品来提高塑炼效果的方法。
开炼机塑炼时温度一般在80℃以下,属于低温机械混炼方法。
密炼机和螺杆混炼机的排胶温度在120℃以上,甚至高达160-180℃,属于高温机械混炼。
生胶在混炼之前需要预先经过烘胶、切胶、选胶和破胶等处理才能塑炼。
几种胶的塑炼特性:天然橡胶用开炼机塑炼时,辊筒温度为30-40℃,时间约为15-20min;采用密炼机塑炼当温度达到120℃以上时,时间约为3-5min。
丁苯橡胶的门尼粘度多在35-60之间,因此,丁苯橡胶也可不用塑炼,但是经过塑炼后可以提高配合机的分散性顺丁橡胶具有冷流性,缺乏塑炼效果。
顺丁胶的门尼粘度较低,可不用塑炼。
氯丁橡胶得塑性大,塑炼前可薄通3-5次,薄通温度在30-40℃。
橡胶硫化工艺流程
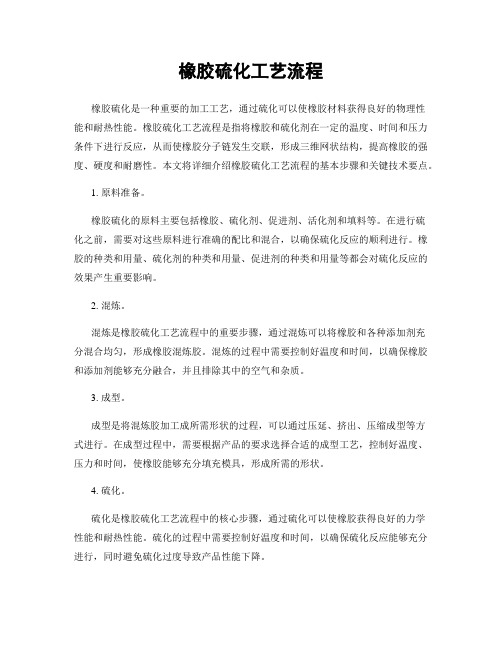
橡胶硫化工艺流程橡胶硫化是一种重要的加工工艺,通过硫化可以使橡胶材料获得良好的物理性能和耐热性能。
橡胶硫化工艺流程是指将橡胶和硫化剂在一定的温度、时间和压力条件下进行反应,从而使橡胶分子链发生交联,形成三维网状结构,提高橡胶的强度、硬度和耐磨性。
本文将详细介绍橡胶硫化工艺流程的基本步骤和关键技术要点。
1. 原料准备。
橡胶硫化的原料主要包括橡胶、硫化剂、促进剂、活化剂和填料等。
在进行硫化之前,需要对这些原料进行准确的配比和混合,以确保硫化反应的顺利进行。
橡胶的种类和用量、硫化剂的种类和用量、促进剂的种类和用量等都会对硫化反应的效果产生重要影响。
2. 混炼。
混炼是橡胶硫化工艺流程中的重要步骤,通过混炼可以将橡胶和各种添加剂充分混合均匀,形成橡胶混炼胶。
混炼的过程中需要控制好温度和时间,以确保橡胶和添加剂能够充分融合,并且排除其中的空气和杂质。
3. 成型。
成型是将混炼胶加工成所需形状的过程,可以通过压延、挤出、压缩成型等方式进行。
在成型过程中,需要根据产品的要求选择合适的成型工艺,控制好温度、压力和时间,使橡胶能够充分填充模具,形成所需的形状。
4. 硫化。
硫化是橡胶硫化工艺流程中的核心步骤,通过硫化可以使橡胶获得良好的力学性能和耐热性能。
硫化的过程中需要控制好温度和时间,以确保硫化反应能够充分进行,同时避免硫化过度导致产品性能下降。
5. 后处理。
硫化完成后,还需要进行后处理工艺,如冷却、清洗、修整等,以确保产品的质量和外观。
同时还需要进行产品的检验和包装,最终将产品送往市场。
总之,橡胶硫化工艺流程是一个复杂而精细的加工过程,需要严格控制各个环节,以确保产品的质量和性能。
只有在每个步骤中严格执行工艺要求,才能生产出符合要求的橡胶制品。
希望本文对橡胶硫化工艺流程有所帮助,谢谢阅读。
橡胶波纹管硫化模具设计

没辊轴颈处使用 的机械密封 中的橡胶波纹管就是一个 补偿 机构 ,通过压缩波纹 管利用橡胶 的回弹性 ,向密 封环提供弹力。
1 橡胶 波纹管的结构特点
橡胶波纹管 的结构如 图 1 所示 。产品一端安装 密
2 橡胶波 纹管的模具设计
2 . 1 橡 胶 波纹 管 的模 具 结构
封环 ,一端 通过螺栓 与设 备腔体 紧密接触 ,形成静密
2 0 1 3年 5月
润滑 与密封
I BRI CAT I ON ENGI NEERI NG
Ma v 2 01 3 Vo 1 . 3 8 No . 5
第3 8卷 第 5期
DOI :1 0 . 3 9 6 9 / j . i s s n . 0 2 5 4—01 5 0 . 2 0 1 3 . 0 5 . 0 2 6
p a r t o f t h e r u b b e r b i l l o ws mo l d, a nd t h e s t uc r t u r e o f c o mb i n a t i o n l a mo u n t b l o c k s wa s a d o p t e d or f t h e mo l d c o r e . Ma c h i n i n g a b i l i t y a n d o p e r a t i o n a b i l i t y o f v u l c a n i z e d t e c h n o l o g y or f p r o d u c t s we r e t a k e n i n t o c o n s i d e r a t i o n d u in r g t h e d e s i g n . Th e mo l d h a s r e a s o n a b l e s t uc r t u r e, wh i c h c a n p r o d u c e q u a l i f i e d ub r be r b i l l o ws s t a b l y . Ke y wo r d s :r ub b e r b e l l o ws ;c u in r g mo l d;me c h a n i c a l s e a l
橡胶硫化工艺

橡胶硫化工艺(总5页) -CAL-FENGHAI.-(YICAI)-Company One1-CAL-本页仅作为文档封面,使用请直接删除一、传统橡胶硫化工艺1、影响硫化工艺过程的主要因素:硫磺用量。
其用量越大,硫化速度越快,可以达到的硫化程度也越高。
硫磺在橡胶中的溶解度是有限的,过量的硫磺会由胶料表面析出,俗称“喷硫”。
为了减少喷硫现象,要求在尽可能低的温度下,或者至少在硫磺的熔点以下加硫。
根据橡胶制品的使用要求,硫磺在软质橡胶中的用量一般不超过3%,在半硬质胶中用量一般为20%左右,在硬质胶中的用量可高达40%以上。
硫化温度。
若温度高10℃,硫化时间约缩短一半。
由于橡胶是不良导热体,制品的硫化进程由于其各部位温度的差异而不同。
为了保证比较均匀的硫化程度,厚橡胶制品一般采用逐步升温、低温长时间硫化。
2、硫化时间:这是硫化工艺的重要环节,时间过短,硫化程度不足(亦称欠硫)。
时间过长,硫化程度过高(俗称过硫)。
只有适宜的硫化程度(俗称正硫化),才能保证最佳的综合性能二、橡胶硫化工艺方法按硫化条件可分为冷硫化、室温硫化和热硫化三类。
1、冷硫化可用于薄膜制品的硫化,制品在含有2%~5%氯化硫的二硫化碳溶液中浸渍,然后洗净干燥即可。
2、室温硫化时,硫化过程在室温和常压下进行,如使用室温硫化胶浆(混炼胶溶液)进行自行车内胎接头、修补等。
3、热硫化是橡胶制品硫化的主要方法。
根据硫化介质及硫化方式的不同,热硫化又可分为直接硫化、间接硫化和混气硫化三种方法。
①直接硫化,将制品直接置入热水或蒸汽介质中硫化。
②间接硫化,制品置于热空气中硫化,此法一般用于某些外观要求严格的制品,如胶鞋等。
③混气硫化,先采用空气硫化,而后再改用直接蒸汽硫化。
此法既可以克服蒸汽硫化影响制品外观的缺点,也可以克服由于热空气传热慢,而硫化时间长和易老化的缺点。
三、橡胶硫化工艺:橡胶在未硫化之前,分子之间没有产生交联,因此缺乏良好的物理机械性能,实用价值不大。
- 1、下载文档前请自行甄别文档内容的完整性,平台不提供额外的编辑、内容补充、找答案等附加服务。
- 2、"仅部分预览"的文档,不可在线预览部分如存在完整性等问题,可反馈申请退款(可完整预览的文档不适用该条件!)。
- 3、如文档侵犯您的权益,请联系客服反馈,我们会尽快为您处理(人工客服工作时间:9:00-18:30)。
橡胶硫化模设计基础知识
1对橡胶硫化模的要求
1.1切实有效:设计的橡胶硫化模必须保证压制出的橡胶
制品在尺寸、形状、表面外观质量等方面符合图纸要
求。
1.2方便操作:包括以下几个方面
●装料方便
●取零件方便
●装卸模具方便
●搬动模具方便
●模具轻便
1.3制造简便:模具结构的机械加工工艺性要好。
1.4经久耐用
1.5造价低廉
2橡胶硫化模主要构成
2.1成型结构:包括上模、中模、下模、型芯、哈夫块等。
2.2定位结构:包括定位销定位、本体定位等。
2.3排气结构:包括硫胶槽等。
2.4启模结构:包括启模槽、卸模架等。
2.5测温结构:包括测温孔。
2.6标识结构:包括对模倒角、防错销、防错孔、文字标
识等。
2.7加料结构:包括加料室、注压缸、浇注孔等。
3分模面选择与胶料收缩率确定
分模面选择应以方便制件取出和不影响制件外观为原
则,一般选在最大外园处并且是棱角部位。
橡胶制件是在高温下成型的,由于橡胶的热膨胀系数
比模具材料(钢)大的多,所以橡胶制件冷却后尺寸
要比型腔尺寸小。
型腔尺寸与橡胶制件冷却后尺寸之
比叫胶料收缩率,丁腈橡胶收缩率为1.5%,硅橡胶为
2.5%,氟橡胶为3%。
4常用模具结构
●上下模中心定位
●上下模本体定位
●上下模双销定位
●上中下中心定位
●上中下本体定位
●上中下双销定位
●上下模型芯定位
●上中下型芯定位
●普通复合模结构
●合页式复合模结构
橡胶模压工艺
1.模压工艺综述
1.1 模压工艺流程图
1.2 模压工艺各工步操作要点
1.2.1 下料:将胶料制成与橡胶制品的形状与大小相适应的毛坯,根据不同制品的要求,可采取不同的下料方法,如冲切下料、挤出下料和手工下料。
毛坯的好坏直接影响橡胶制品质量,主要影响因素有毛坯的重量、形状和尺寸。
1.2.2 装料:将毛坯装入模具中,装料位置要准确。
对于金属橡胶件,要注意金属件的安装方向和位置。
1.2.3 合模:合模时要注意:①方向不要搞错②定位销要确实进入定位孔内③不要碰伤模具④多套模具压制时模具之间的零件不要搞混。
1.2.4 预压:加压前要检查定位销是否确实进入定位孔内并且根据制品的具体情况确定预压的速度和次数。
1.2.5 硫化:硫化期间注意检查温度、时间、压力三要素的情况。
1.2.6 启模:启模时注意不要碰伤模具。
1.2.7 脱模:不要划伤制品,不要碰伤模具。
1.2.8 清模:硫化后,胶料中一些有害物质粘附在型腔表面,影响模具的光度和寿命,多余的毛边留在模具上,影响下次硫化制品的质量。
因此,每次硫化后,都必须对模具进行清理,确保制品的质量,延长模具的寿命。
1.3 生产中制品常见缺陷分析
1.3.1 产生缺陷的主要因素:①毛坯②操作方法③工艺参数④材料⑤工装设备⑥环境
1.3.2 闷气:①装料过多②装料方法不当③预压速度不当④胶料挥发物太多⑤模具结构不合理
1.3.3 杂质:①模具未清理干净②带手套装料③环境不好④胶料本身有杂质1.3.4 撕裂:①脱模时操作不当②胶料过脆
1.3.5 错位或偏心:①模具搞错②定位销磨损
O 型圈(45度分型)操作要点
4.O 型圈(45度分型)操作要点
4.1 准确下料:一般用挤出条,公差要求严格的用下料模冲切下料,尽量避免手工下料。
4.2 校正平板:平板的平行度对O 型圈截径尺寸影响很大,因此每次硫化前都必须对平板进行校正。
4.3 调整压力:压力大小对O 型圈截径尺寸也有一定影响,对于截径尺寸轻微超差的,适当调整压力有可能解决问题。
4.4 清理毛边:模具加压后,马上启开模具,将多余的毛边清理掉,再加压硫化(启二遍)。
对于必须手工下料,而截面尺寸又较严的O 型圈来说,这一措施往往很见效。
1.O 型圈(45度分型)生产中常见缺陷分析
5.1 截径局部尺寸不合格:
原因:硫化时多余的橡胶覆盖于45度分模面上形成厚薄不均匀的毛边。
这就造成上下模在水平方向不同心、在垂直方向倾斜的现象。
表现在截径尺寸上就是一边尺寸大一边尺寸小。
对策1:尽可能减小毛边厚度。
措施包括减少用料、加大压力、清理毛边、模具开流胶槽等。
对策2:尽可能使毛边厚度保持均匀。
措施包括校正平板、调整模具位置、准确下料、在模具上增加定位销定位等。
5.2 错牙:造成错牙有两种原因,一种是模具本身制造问题,另一种是由于操作不当引起的。
两种不同原因引起的错牙,分别具有不同的特点。
由模具引起的错牙,沿圆周错牙的程度是均匀的,错牙的方向都是相同的。
由操作不当引起的错牙,沿圆周错牙的程度是不均匀的,错牙的方向往往是不相同的。
如果是模具问题,应更换模具。
如果是操作问题,则应按照《减小毛边厚度、使毛边厚度保持均匀》〉这两项原则改进操作。